Open Access
ARTICLE
Wood Gasification in Catastrophes: Electricity Production from Light-Duty Vehicles
1 Department of Mechanical Engineering, University of Canterbury, Christchurch, 8041, New Zealand
2Alliance to Feed the Earth in Disasters (ALLFED), Lafayette, CO 80026, USA
3 Department of Electrical & Computer Engineering, Western University, London, ON N6A 5B9, Canada
4 Ivey Business School, Western University, London, ON N6A 5B9, Canada
* Corresponding Authors: Baxter L. M. Williams. Email: ; David Denkenberger. Email:
Energy Engineering 2025, 122(4), 1265-1285. https://doi.org/10.32604/ee.2025.063276
Received 10 January 2025; Accepted 17 February 2025; Issue published 31 March 2025
Abstract
Following global catastrophic infrastructure loss (GCIL), traditional electricity networks would be damaged and unavailable for energy supply, necessitating alternative solutions to sustain critical services. These alternative solutions would need to run without damaged infrastructure and would likely need to be located at the point of use, such as decentralized electricity generation from wood gas. This study explores the feasibility of using modified light duty vehicles to self-sustain electricity generation by producing wood chips for wood gasification. A 2004 Ford Falcon Fairmont was modified to power a woodchipper and an electrical generator. The vehicle successfully produced wood chips suitable for gasification with an energy return on investment (EROI) of 3.7 and sustained a stable output of 20 kW electrical power. Scalability analyses suggest such solutions could provide electricity to the critical water sanitation sector, equivalent to 4% of global electricity demand, if production of woodchippers was increased post-catastrophe. Future research could investigate the long-term durability of modified vehicles and alternative electricity generation, and quantify the scalability of wood gasification in GCIL scenarios. This work provides a foundation for developing resilient, decentralized energy systems to ensure the continuity of critical services during catastrophic events, leveraging existing vehicle infrastructure to enhance disaster preparedness.Keywords
In the aftermath of global catastrophic infrastructure loss (GCIL) caused by events such as large-scale solar storms, cyber-attacks, high-altitude electromagnetic pulses (HEMPs), or pandemics, the disruption of electricity and fossil fuel networks poses a threat to modern civilization [1]. While small-scale disruptions are undesirable but manageable [2–4], catastrophic infrastructure loss could cause cascading failures across critical sectors, including the most important of food and water provision. Severe disruptions could lead to an irreversible societal collapse, which would threaten human survival by hindering the recovery of essential systems and services [5]. Electricity is fundamental to the operation of all infrastructure critical for modern civilization [6,7], including healthcare [8], water treatment [9], and communication systems [10]. With the loss of electricity supply, essential services would be severely compromised, exacerbating the risk of further system failures and increasing the likelihood of an irreversible collapse of industrial society [11].
The vulnerability of current electricity infrastructure has precipitated recommendations for increased resilience, such as through distributed energy resources (DERs) [12–15], self-supporting microgrids [16–18], and flexible electricity demand [19–22]. Currently, DER technologies have advanced sufficiently for off-grid [23,24], DC nano-grids [25–27], and captive power [28–30] to become economically viable [31]. Such localized electricity generation and flexible energy systems could help to maintain essential services during some disruptions to centralized systems [32,33]. However, energy system resilience requires not only mitigation of supply and network shocks but also the ability to recover rapidly following disruptions [34,35]. Such needs would become critical during catastrophic events, where decentralized, flexible energy sources would be indispensable for essential services [36].
Extreme events, such as HEMP detonation, could also cause the loss of conventional DERs [37,38]. In such scenarios, restoration of electricity to critical services would require alternative generation sources [39]. Light duty vehicles are ubiquitous around the world, so vehicle-based electricity generation could provide such an alternative, mitigating the severe impacts of prolonged electricity network outages by restoring electrical infrastructure in the absence of conventional, centralized systems [40].
The loss of electricity networks could, however, disrupt supply chains for other energy sources, such as reducing or eliminating the ability to drill and refine crude oil. Thus, resilient solutions should not rely on the combustion of refined fossil fuels for decentralized electricity generation. Instead, wood gasification could provide an alternative energy supply for combustion in light-duty vehicles. Wood gasification, a controlled process of heating wood in an oxygen-limited environment, produces syngas, a mixture of carbon monoxide, hydrogen, and methane which can serve as an alternative fuel for combustion in light-duty vehicle petrol engines [41]. Gasification is best achieved with wood chips smaller than a 3 cm cube [42,43] and previous work has developed low-cost open-source technologies, which could be rapidly fabricated and used for such wood chipping [44]. Wood gasification has been used to fuel personal vehicles during fossil fuel supply shocks, such as in Sweden during World War II [45], and could be used to fuel other combustion engines, such as generators and power tools.
Previous research has explored various methods of energy generation in post-disaster scenarios, particularly with the production of food [46], and water [47]. While grid recovery from short-term disruptions could be managed through the distribution of stored food [48], longer-term grid failures, such as those resulting from a HEMP event, could precipitate widespread famine in several regions [49]. Prolonged infrastructure collapse could lead to severe resource scarcity, potentially driving widespread famine across vulnerable regions, as essential systems for food, water, and heating would be severely impacted [46,50].
Previous research has shown wood gasification could extend diesel fuel reserves in a GCIL scenario by up to 290% (and petrol indefinitely) [49], indicating the production of syngas to power internal combustion engines could be a key component of global responses to a catastrophe of this kind. The feasibility of generating electricity for critical services with decentralized wood gasification, however, has not been assessed.
This research explores the feasibility of using light duty petrol (gasoline)-powered internal combustion vehicles to generate electricity in a GCIL scenario. The drivetrain of a light-duty vehicle is modified to power an electrical generator to supply electricity and a woodchipper to chip the wood required for gasification, and assessments of the scalability of such solutions in a catastrophe. As such, this work shows both the feasibility of wood gasification for decentralized electricity generation and a roadmap for scaling decentralized electricity generation with wood gasification to meet critical energy needs following a GCIL event.
A light-duty vehicle was modified, allowing a power take-off (PTO) to attach to its drivetrain. The PTO was connected to a woodchipper and an electrical generator (collectively referred to as “external machinery” in this work), and both were tested separately. Results from these tests were used to inform calculations on the scalability of such systems in a GCIL scenario.
The vehicle chosen for modification was a 2004 Ford Falcon Fairmont. The car was stock (no prior modifications) before testing, thus requiring modification to power external machinery. The vehicle’s drivetrain featured an open differential to distribute power through the path of least resistance [51]. The following modifications were performed:
• Disconnected parking brake (handbrake) on the rear right wheel (“driving wheel”) and activated the handbrake to prevent rotation of all non-driving wheels, as only one was required to power external machinery
• Removed rear bumper and towbar to access towbar mounting points, which were used to mount an external frame to balance the rotational moment created by external machinery.
• Removed the front grill to increase airflow over the radiator and allow installation of an auxiliary cooling system.
All design files used in the vehicle conversion are available on the Open Science Framework repository [52].
To dissipate heat during machinery operation, an auxiliary cooling system was designed, which sprayed atomized water on the radiator. This cooling system used atomizing nozzles connected to a 12 V diaphragm pump, which supplied water from a reservoir. The nozzles produced a water mist, which evaporated as it passed over the radiator fins. This method was predicted to dissipate up to 11 kW of heat per nozzle, with a potential flow rate of 0.3 L per min. Two nozzles were placed at opposite acute angles, with a third facing directly upwards to maximize surface area coverage. The nozzle assembly was connected using 16 mm hosing from the water reservoir to the pump, as shown in Fig. 1.
Figure 1: Cooling system setup in the engine compartment of the vehicle. Water flowed from a high-density polyethylene (HDPE) water reservoir into a diaphragm pump, which pumped it through the nozzle, out through atomizing nozzles, and onto the vehicle’s radiator
2.3 Experimental Testing Setup
The vehicle’s rear end was lifted by car jacks and supported by jackstands at the rear axle, engaging the vehicle’s suspension to minimize vibrations. The rear wheels were removed to allow connection to the PTO, which was attached to the driving wheel with the spline adapter shown in Fig. 2. The adapter had the appropriate pitch circle diameter (PCD) (5 × 114.3 mm) of the wheel’s studs and center bore (70.5 mm) to keep the mounting concentric. The spline on the adapter hub was a standard Class I PTO spline (6 spline, 1 3/8” (34.9 mm)), to which a PTO shaft could connect. To ensure the torque would not overturn external machinery, a moment-restricting frame was constructed from a welded hollow square steel section, shown in Fig. 3, which connected external machinery to the vehicle’s towbar with rigid members and provided stabilizing contact with the ground.
Figure 2: Spline adapter to connect external machinery to the vehicle’s driving wheel via a power take-off (PTO)
Figure 3: Moment-restricting frame (blue steel bars) to stabilize external machinery, shown here connected to the PTO by standard pins
To evaluate the effectiveness of the cooling system, a constant engine speed of 3750 revolutions per minute (RPM) was maintained while the vehicle remained in neutral gear, to heat the engine and ensure additional load would require more cooling than could be provided by the unassisted radiator. Coolant temperature was monitored by the vehicle’s internal coolant temperature gauge. Temperatures on the gauge were unmarked, so the 1/4–3/4 span was assumed to be between 90°C, and 105°C, as is standard for similar vehicles [53,54].
2.3.2 Mechanical Work: Wood Chipping
A Hanmey WCX5 PTO woodchipper, rated for chipping wood up to 5 inches (125 mm) in diameter, was connected by the PTO shaft to the driving wheel’s hub, as shown in Fig. 4. The moment-restricting frame was bolted to the vehicle’s towbar and mounted to the woodchipper by the standard pins.
Figure 4: Hub spline adapter mounted to PTO shaft for connecting vehicle’s driving wheel to external machinery
The woodchipper shaft’s stated operating speed was 430 RPM, corresponding to a vehicle engine speed of approximately 2000 RPM in first gear. This operating RPM was maintained by a driver, who adjusted the throttle according to load. Before chipping, wood volume and mass were measured. During operation, the woodchipper was spun to 430 RPM, then the wood was fed in with the thickest end first. The following wood types were tested: (i) wet wood, diameter 1–3.5 inches (25–90 mm); (ii) wet wood, diameter 4 inches (100 mm); (iii) dry wood, diameter 5 inches (125 mm). The volume of wood, chipping time, instantaneous fuel consumption, and engine rotational velocity were recorded during operation.
An Agriquip GP33 PTO generator with a 30 kVA synchronous alternator was connected by the PTO shaft to the driving wheel’s hub, using the same mechanism shown in Fig. 4. The generator was equipped with an automatic voltage regulator (AVR) to maintain constant output voltage. The generator was connected by a New Zealand-standard 60-Amp three-phase plug to a load bank with variable resistance. To generate three-phase 400 V 50 Hz electricity, the generator required a rotational velocity of 1500 RPM, corresponding to 430 RPM at the PTO, and an engine speed of ~2000 RPM with the vehicle in first gear. During operation, the electrical load of the load bank was increased in increments of 2.5 kW, to a maximum of 20 kW. Power, current, frequency, and voltage were measured at the load bank and generator, and engine rotational velocity and instantaneous fuel consumption were measured at the vehicle.
The feasibility of light-duty vehicles to self-sustain electricity generation for the critical water sanitation sector was assessed. Best estimates were calculated for the availability of key components for vehicle-based wood chipping and electricity generation, and potential limitations to scalability were identified. Calculations were for aggregate global energy production, assuming sufficient labor availability and materials and components could be transported to the required location.
The modified vehicle is shown in Fig. 5, with the rear wheels removed, the PTO drive shaft connected to the woodchipper, and the moment-restricting frame supporting the vehicle and external machinery. Not shown is the auxiliary cooling system on the engine radiator, located at the front of the vehicle, which is shown in Fig. 1.
Figure 5: Photograph of the modified vehicle on jackstands and with rear wheels removed, connected to the red woodchipper by the black PTO. The blue steel sections are the moment-restricting frame
For all tests, the moment-restricting frame and PTO hub connection successfully transferred power from the vehicle’s driving wheel to external machinery, without destabilizing the vehicle or machinery. The average speed of the driving wheel’s hub during the operation of external machinery was equivalent to approximately 30 km/h.
All three wood types were chipped successfully. Although the test for dry wood (type iii) was interrupted by a knot in the wood causing the woodchipper to jam, the vehicle remained running, and chipping was restarted, allowing successful completion of the test. The dry wood produced 0.00152 m3 of wood chips, with a total mass of 700 g, and required 0.0299 L of petrol. Assuming a petrol energy content of 32 MJ/L [55] and wood chip energy content of 10 MJ/kg [56], the wood chipping process used 0.96 MJ of energy from petrol to produce 7 MJ of energy from wood chips, of which 3.5 MJ (conservatively) would likely be used to produce syngas [57,58]. Thus, the modified vehicle’s energy returns on energy investment (EROI, the amount of usable energy output for a given amount of energy input [55]) is 3.7. An example of engine speed and fuel consumption during the chipping of dry wood, before restarting, is shown in Fig. 6.
Figure 6: Vehicle engine speed and fuel consumption during chipping of 5-inch (125 mm) diameter dry wood, showing changes in vehicle operation from idle to chipping, and from chipping to jamming. Dashed lines correspond to the onset of chipping and wood jamming
Electricity generation of up to 20 kW was sustained, with voltage fluctuations within the limits of the New Zealand Electricity Regulations [59]. Minimal vibrations were observed in the vehicle, and the electrical power output variation was under 1 kW. Electrical frequency varied when the load changed, as the vehicle RPM was managed by manual control of the engine throttle, which typically overcompensated for load increases. Engine speed and power at the load and generator during electricity generation are shown in Fig. 7. Engine speed and power frequency at the load and generator are shown in Fig. 8.
Figure 7: Vehicle engine speed, and power at load and generator during electricity generation
Figure 8: Vehicle engine speed and power frequency at load and generator during electricity generation
3.2.3 Auxiliary Cooling System
The radiator coolant temperature reached 105°C after 10 min of engine operation at 3750 RPM in neutral gear. Auxiliary cooling for two minutes reduced coolant temperature to 90°C.
With simple modifications, a 2004 Ford Falcon Fairmont was capable of powering external machinery, producing wood chips and electricity. The modified vehicle successfully chipped wet and dry wood with diameters up to the woodchipper’s rated capacity, producing wood chips of a suitable size for wood gasification, with an EROI of 3.7. Chipping was possible in the straight sections of a dry log with a diameter of 5 inches (125 mm), but a knot in the wood caused the woodchipper to jam and the vehicle’s engine to stall (Fig. 6). While chipping was restarted after the stall and completed successfully, chipping of larger logs should be reserved for vehicles with higher power delivery capacities, to minimize stalling. Wet wood was found to be easier to chip, as is typical for woodchippers [60], which could be an advantage in a catastrophe, as wet wood is more common than dry. Wood with a high moisture content would need to be dried before gasification, which could require additional energy or could be achieved passively, aided by the increased surface area of the wood chips.
Operation of the electrical generator with the modified vehicle sustained an output of 20 kW of regulated electrical power without overheating. The frequency of produced electricity was directly proportional to the rotation speed of the synchronous alternator. Thus, variation in driving wheel rotational speed resulted in a proportionally equivalent variation in electricity frequency. The alternator’s AVR effectively decoupled electricity frequency from rotational speed within an operational speed range, however, with the magnitude of generator torque proportional to electrical power. This versatility in frequency and ability to match power requirements means decentralized generation with modified wood gas-powered vehicles could replace electricity supply in a range of critical applications following a GCIL event.
Electrical frequency varied by up to 1 Hz with unchanging load, as shown in Fig. 8. The peak variation of approximately 3 Hz occurred when the electrical load changed, as the vehicle throttle was managed manually by a driver, whose responses to load changes were imperfect. Automated throttle control could be implemented to reduce the number of required operators and reduce the risk of large frequency variations, which could damage connected electronic devices [61,62]. As cruise control could be difficult to implement for stationary vehicles and is not ubiquitous, particularly in older vehicles, operator training could reduce the risk of damaging frequency variations. Additionally, the vehicle throttle could be set at a constant point for electrical loads with no variability, reducing operator requirements.
Electricity demand subject to human behavior is inherently variable [63,64]. Thus, any automated control of electricity generation should account for such changes in demand. Demand timing issues could, however, be partially mitigated by integrating the system into a local microgrid, where other sources of generation, storage, and dispatchable loads could enable a steady operation. For wood chipping, which is less frequency-sensitive but has large load variations, throttle control would need to respond sufficiently quickly for the engine to prevent stalling with load increases. Thus, throttle control for wood chipping is likely best achieved by a human operator.
Water sanitation constitutes 4% of global electricity demand [65,66], equivalent to 1200 TWh in 2023 [67]. As critical facilities, water sanitation facilities often have backup electrical supplies and limited fuel to power these supplies for several days. While new fossil fuel extraction would likely be crippled in a GCIL scenario, some fossil fuel would already be above ground and could be used to fuel critical services, such as water sanitation facilities. However, the backup generators in these facilities typically have lifetimes of around 3000 h of continuous use [68], and portable electricity generators’ lifetimes are typically between 1000–2000 h of continuous use [69]. Thus, even with emergency provision of fossil fuel, these methods would be insufficient to outlast a GCIL event [70].
However, wood gasification capacity could be increased at a rate of approximately 6.1 GW per day [49]. Generating the electricity required for water sanitation, and producing the wood chips required for gasification with an EROI of 3.7, is expected to require 1.3 TW of continuous engine power. Thus, gasifier scale-up is expected to take approximately 210 days (approximately 7 months). Materials and other requirements for replacing the electricity supply for water sanitation with wood gas-powered generation from light-duty vehicles are calculated in this section.
With light-duty vehicles generating 20 kW of electricity for an average of 120 h per week (accounting for 30% downtime [71]), equivalent to 124,800 kWh per year, 9.6 million vehicles would be required to produce electricity equivalent to the demand of the water sanitation sector. With an EROI of 3.7 from wood chipping for gasification, 3.5 million vehicles would be required to chip wood for gasification to power electricity generation, for a total requirement of 13.2 million vehicles. Older vehicles are expected to be better suited to modification than newer vehicles, given their limited internal electronics and thus lower likelihood of damage in an HEMP event, but newer vehicles are still typically unplugged and would likely survive. Approximately 830 million light-duty vehicles were produced between 1990–2005 [72], of which approximately 5% are operational [73], leaving roughly 41 million suitable vehicles expected to be operational. Thus, the supply of light-duty vehicles is expected to exceed requirements.
When not connected to an electrical grid to induce a magnetic field in their rotor, induction motors require self-exciting capacitors, which use the reactive power of the spinning motor [74]. The annual global capacitor market is valued at USD 25 billion [75], with aluminum electrolytic capacitors accounting for 22% (USD 5.5 billion) [75]. Of these, approximately 6% (34 million capacitors per year, assuming an average price of 10 USD [75]) are within the required 50–500 μF range and rated about 400 V [75]. Assuming an average lifespan of 10 years, 330 million suitable capacitors are expected to be currently operational. To fulfill the capacitor requirement for electricity generation, 9.6 million would be required, indicating even a very low survival rate of capacitors to HEMP (anything greater than 3%) would be sufficient.
The PTO used in this work included an integrated gearbox with a 3.49:1 ratio, to meet the required 1500 RPM of the generator. Most continuously variable transmissions (CVTs) could meet this gearing requirement and be used instead in a catastrophe [76]. With a market size of 22.1 billion USD [77] and an average price of around 5000–10,000 USD [78], approximately 2.2–4.4 million CVTs are produced annually. Assuming each lasts for 15 years, approximately 33–66 million would be operational at the time of a GCIL event. Some gearboxes with the appropriate gear ratio could be manufactured or salvaged from other applications, so this supply is likely to be sufficient for the 13.1 million required.
4.1.4 Auxiliary Cooling Systems
Recreational vehicles and residential boats both have water pumps of sufficient sizes for auxiliary cooling systems. With an annual market of 55 billion USD [79] and an average cost of 50,000 USD [80], approximately 1.1 million recreational vehicles are produced annually. Assuming all have usable pumps and an average lifetime of 15 years, 16.5 million pumps could be sourced from recreational vehicles. Residential boats have an annual market of 34 billion USD [81] and average cost of 100,000 USD [82]. Assuming an average lifetime of 15 years and 75% with sufficiently large pumps, 3.8 million pumps could be sourced from residential boats. Neither recreational vehicles nor residential boats are typically connected to electricity grids. Thus, both are expected to survive a HEMP or electrical storm, so could provide pumps for auxiliary cooling systems. Combined, recreational vehicles and residential boats are expected to provide up to 20.3 million pumps, more than the 9.6 million required to produce 1200 TWh per year. However, in a catastrophe affecting the availability of transport, boat pumps may only be available near coastal areas where the boats are located. As only 14% of the global population lives within 10 km of coastal areas [83], transportation limitations could necessitate alternative solutions for cooling system pumps. Additionally, future work could consider developing open-source water pump designs for such emergencies, using distributed manufacturing methods, such as those used in the COVID-19 pandemic [84].
Other components for auxiliary cooling systems are expected to be sourced without difficulty in a catastrophe. A single nozzle supplier can produce up to 2.5 million nozzles per year [85]; assuming an average lifetime of 10 years, demand could thus be met even by the 25 million nozzles available from a single supplier. Other components, such as tubing and reservoirs, could be adapted from common polymer components and are expected to be sufficiently ubiquitous in a GCIL scenario.
While vehicles with larger engines have higher-capacity cooling systems and are unlikely to require auxiliary cooling systems to produce 20 kW of electrical power, these vehicles could be used to generate higher loads and could thus still require auxiliary cooling. Alternatively, the production of electrical power from each vehicle could be scaled according to their cooling capacity, removing the need for auxiliary cooling systems altogether. Furthermore, salvaged auxiliary radiators could obviate water cooling.
Synchronous generators, particularly those with AVRs, can provide stable electricity generation with high efficiency [86]. While large-scale commercial synchronous generators (2–50 MW) have an annual market of ~6 billion USD [87], data on smaller systems (1 kW–2 MW) are not readily available. Diesel gensets pair a synchronous motor with AVR to a diesel engine, and the market for small (<100 kVA) gensets is approximately 7 billion USD [88]. Assuming an average cost, power, and power factor of 10,000 USD, 50 kVA, and 0.8 [89], respectively, approximately 24 GW of genset capacity is produced annually. Assuming an average lifetime of 10–15 years and a 30% survival rate from an EMP, 72–108 GW of installed capacity is expected to be operational, which is less than the required 192 GW.
Induction motors, while providing less stable electricity generation than synchronous generators, are widely available and have long lifetimes [86]. Induction motors have an annual market of 21 billion USD [90], and more than half are estimated to be of appropriate sizes (in the range of 1–75 kW) [91]. With an average price of approximately 1000 USD [92], an average lifetime of around 15 years, 158 million suitably sized induction motors. Assuming an average size of 3 kW and an HEMP survival rate of 30%, 142 GW of induction motor capacity is expected to be operational.
Hybrid electric vehicles (EVs) contain integrated motor generators (IMGs), which generate electricity to store in the vehicle’s battery or power the drivetrain [93]. If the availability of gensets and induction motors is insufficient, these IMGs could be used in a catastrophe for electricity supply. The total number of EVs (including hybrids) is estimated to be 40 million, of which hybrids constitute approximately 30% [94], so approximately 12 million hybrid EVs are expected to be operational. The average electrical output of an IMG is between 20–90 kW [93], so the total generation capacity from hybrid EVs is expected to be approximately 240–1080 GW. Assuming a HEMP survival rate of 30% to account for some hybrid EVs being plugged in, 72–324 GW of generation capacity is expected to be available from hybrid EVs. Additionally, the number of hybrid EVs is increasing globally [95], so the total generation capacity from IMGs is likely to increase.
Combined available generation capacity from gensets, induction motors, and hybrid EVs is expected to be 285–573 GW, which exceeds the 192 GW demand for water sanitation. Alternatively, future work could assess the feasibility of directly powering hybrid EVs with wood gas to directly generate electricity from their IMGs, with no modifications.
The annual woodchipper market size is approximately 430 million USD [96], and average costs are approximately 2000 USD per unit [97]. Assuming an average lifetime of 15 years, approximately 3.2 million woodchippers are expected to be available in a catastrophe, which is just under the required 3.5 million. Furthermore, the size of the chips is smaller than the chunks ideal for gasifiers.
With 120 h of engine operation per week and an average wheel speed equivalent to 30 km/h, each vehicle would cover an annual equivalent distance of 187,200 km. With oil changes for light duty vehicles (~6.5 L per vehicle) recommended every 7000–10,000 km [98], each vehicle would require 18–26 oil changes per year. With 33 million vehicles required, total annual requirements are expected to be 4.0–5.7 billion L. While other consumables, such as transmission fluid, would also be required, these consumables typically have much longer replacement intervals than engine oil, so are not expected to limit scalability while vehicles use the consumables already in their systems. However, while the stockpiles of these consumables are unknown, they could likely be salvaged from non-operational vehicles post-catastrophe.
Annual engine oil consumption in the USA is approximately 2.1 billion L [99]. Assuming engine oil consumption is proportional to contribution to gross world product (GWP), of which the USA contributes 25% [100], global annual engine oil consumption is estimated to be 8.4 billion L. Assuming one month’s worth of consumption is available at a given time in warehouses and in transit, approximately 700 million L of engine oil would be available at the time of a GCIL event, equivalent to 3–5 months of required consumption. Although the availability of new engine oil would be low after production ceased in a GCIL event, engine oil could likely be salvaged from other vehicles. The total number of light-duty vehicles in the world is approximately 1.4 billion [101]. Assuming engine oil tanks are an average of 40% full, approximately 3.8 billion L of engine oil could be salvaged from existing vehicles, equivalent to 20–28 months of required consumption. Together with oil in the supply chain, the total available engine oil is expected to be between 23–33 months of required consumption. Additionally, some research has shown oil change intervals can be extended up to 2–3 times those typically recommended by vehicle manufacturers, without incurring mechanical damage or impairing engine operation [102,103]. Thus, available engine oil could likely be extended up to 47–100 months of required consumption.
Decentralized wood gasification could mitigate the effects of electricity loss on the critical water sanitation sector following a GCIL event. Supplies of vehicles, capacitors, gearboxes, and electrical generators could be sufficient to provide equivalent electricity to the demand for water sanitation facilities. While pump supply could be a limiting factor for auxiliary cooling systems, the required number of these could be reduced by pairing external machinery loads with vehicles with sufficient cooling capacity.
The supply of woodchippers could be a limiting factor for scalability. Production of woodchippers could potentially be increased following a GCIL event, as many factories are expected to be capable of producing woodchippers, which are simple machines, consisting essentially of a single cutting wheel in a housing to direct logs towards, and wood chips away from, the wheel. Fabrication capacity, however, may be limited following a catastrophe and could be constrained by other requirements, so further research is required to assess the scalability of woodchipper production in a GCIL scenario. Although plans have also been developed for bicycle-based wood chipping [104], this method is best suited to chipping small-diameter wood, so the supply of wood would be limited. Additional work is needed to investigate alternatives, such as the industrial woodchippers used for paper production (which also produce chips, not chunks), wood splitters, chainsaws, band saws, table saws, circular saws, and splitting by hand.
Engine oil could also be a limiting factor for scalability. Current engine oil stores are expected to last 3–5 months of continuous wood chipping and electricity generation but could be extended up to 47–100 months with longer oil change intervals and/or salvaged engine oil, which may be sufficient to allow repair of power plants, although the time required for this work is unknown. Alternative methods of supplying conventional engine lubricants, or alternative lubricants, such as bio-lubricants [105,106], could potentially replace conventional engine oil if production was increased. For example, an open-source controlled pyrolysis system can convert waste plastics to oil-based lubricants [107,108], so could potentially be produced quickly in a catastrophe. While the production of bio-lubricants could be decentralized, the potential for global production to increase is unknown and could be the subject of future research.
Current supplies of wood gasifiers are negligible, so the scalability of wood gasification to produce electricity for critical needs would depend on post-GCIL production. Wood gasifiers can be built with simple tools and supplies from open-source plans [109,110] and thus could potentially be produced quickly in a catastrophe, particularly with simple pre-planning [49]. Thus, the supply of wood gasifiers may not be a limiting factor for scalability.
4.2 Limitations and Future Work
The results of this work are from tests conducted on one vehicle (a 2004 Ford Falcon Fairmont) with one type of woodchipper and electricity generator. While these tests showed simple modifications allowed the vehicle to operate both types of external machinery, budget, and time constraints did not allow for the testing of more vehicle or machinery types. Additionally, time constraints restricted total testing durations; while no degradation was observed during testing, the degradation caused by operating external machinery for long periods is unknown. Thus, while these results are expected to be indicative of real performance following a catastrophe, further research could assess the impacts of other vehicle, woodchipper, and generator models, and quantify degradation and other impediments to long-term use.
To provide power to only the driving wheel, the handbrake was engaged on all other wheels. While sufficient at these loads, the handbrake could be insufficient to constrain the rotation of non-driving wheels in higher-torque operating conditions, such as with more powerful vehicles. Welding of the vehicle’s differential could mitigate these effects and remove mechanical losses from the differential, thus increasing EROI, but would increase labor costs and could reduce the safety and legality of driving the vehicle at a later time. Additionally, other methods of reducing mechanical losses, and thus increasing the EROI of vehicle-based wood chipping and electricity generation, could be investigated, including more efficient power transmission systems, such as increasing the transmission efficiency of gears and/or PTOs. Future work should also assess the full-system EROI However, these investigations are outside the scope of this work.
In a GCIL scenario, wood chipping is expected to be required as an initial step to gasification. While the wood chips produced by the modified vehicle in this work were not used for gasification themselves, they were of a size potentially appropriate for gasification, with all dimensions under 3 cm [42,43]. The scalability analyses presented in this work used the EROI of 3.7 calculated from real-world testing of the modified vehicle, but the transferability of this EROI to large-scale electricity production, which would require additional models of vehicles and external machinery, was not assessed. Future work could assess the real-world EROI of producing syngas from these wood chips, and the differences resulting from alternative equipment, which would reduce uncertainty on the whole-system EROI for producing electricity from wood gas-powered modified vehicles.
Syngas has a lower energy content than petrol, so internal combustion engines can require petrol combustion when first operating until engine temperature reaches a steady state [111], so some petrol may still be required for this solution. However, using stationary engines, particularly when operated continuously, or the use of a blower to increase engine airflow, can reduce these petrol requirements or eliminate them [112]. Thus, future work should quantify the ongoing petrol requirements for the methods presented in this work and investigate the feasibility of reducing these requirements.
While this work assessed the ability of light-duty vehicles to power external machinery to generate electricity and chip wood, vehicles could also be used to operate other processes requiring driving power. For example, the same methods presented in this work could use light-duty vehicles to power industrial processes, such as pumps or milling equipment, which could directly replace damaged equipment in critical industries and increase resilience to GCIL. Such analyses are not conducted in this work and could be the subject of future research.
Some diesel gensets and induction motors are plugged into the electricity supply, so their control systems would be vulnerable to HEMP. While many are unplugged and would thus survive, further work could assess the feasibility of installing substitute control systems in affected generators. While control systems would be unaffected in GCIL scenarios with non-HEMP causes, a better understanding of potential substitutes for critical components would increase the robustness of vehicle-based electricity generation.
This work assessed the feasibility of replacing electricity supply to water sanitation with wood gas-powered modified vehicles. Other critical sectors require electricity, however, such as food production and space conditioning. In some of these cases, energy demand could be met without electricity, such as wood combustion for emergency space heating [70]. In other cases, such as food processing, electricity is likely to be the most useful energy source. While some energy sources could be scaled up following a catastrophe [113] and other methods could meet some critical needs, such as consolidation of housing for shelter and wind power for transportation, total electricity demand for critical needs is expected to be much higher than what could be produced using the methods presented in this work. Thus, future work could investigate other methods of increasing electricity supply in a GCIL scenario.
In this work, the availability of light-duty vehicles to produce electricity was determined with the assumption older vehicles would be preferable, as they do not contain complex electrical control systems vulnerable to HEMPs. However, engines and other critical components of older vehicles are typically more worn than those of newer vehicles, so some newer vehicles would likely be required, particularly if the proposed electricity generation solution was required to operate for many months or years. Additionally, the number of operational older vehicles is declining, so newer vehicles would likely be required if this solution is required many years in the future. Thus, future work could assess the vulnerability of all types of light-duty vehicles to HEMP, and investigate replacements or substitutes for damaged components.
The scalability analyses presented in this work included only the major components required for large-scale decentralized electricity generation from light-duty vehicles, such as vehicles, generators, and engine oil. Other components would also be required, such as advanced control and power quality equipment to ensure the electricity generated was fit-for-purpose in sensitive applications, and other consumables and mechanical parts, such as spark plugs and other lubricants. However, these other consumables have longer replacement intervals than engine oil, so are unlikely to be a limiting factor. Future work could investigate the potential for these factors to limit the scalability of the methods presented in this research and could include testing a range of vehicles, external machinery, and wood gasifiers, and assessment of the vulnerability of components to HEMP.
Additionally, the scalability analyses assumed sufficient materials and labor would be available where required, implicitly assuming global trade systems would be functioning. Global trade is expected to be affected by catastrophic scenarios [114], whether directly, such as through loss of electronics resulting from a HEMP, or indirectly, from factors such as resource scarcity or political action. Thus, the results of these scalability analyses would require large-scale coordination, cooperation, and possibly pre-planning to achieve in a worst-case GCIL scenario, particularly if transport were limited, which indicates two things: (i) the importance of maintaining global trade and cooperation in a catastrophe, the likelihood of which could be strengthened by measures such as national and international planning for a range of disaster scenarios, and increased pre-catastrophe international cooperation; and (ii) a direction for potential future work to assess the magnitude and impacts of global trade disruptions following catastrophic events.
However, scale-up of wood gasification and electricity production could mutually benefit transportation, facilitating international trade. By providing electricity and syngas to supplement existing fossil fuel reserves, the decentralized methods presented in this work could provide the necessary energy to rebuild other energy supply chains damaged in a GCIL event. Thus, although disruptions to global supply chains and limitations on international trade may initially limit the scalability of these methods, the methods themselves could help to restart those supply chains. These effects are outside the scope of this work but could be assessed in future research.
This work demonstrates the feasibility of using modified light-duty vehicles to generate electricity and produce wood chips for gasification in the event of global catastrophic infrastructure loss. A 2004 Ford Falcon Fairmont with simple modifications successfully powered external machinery, including a woodchipper and an electrical generator, highlighting the potential for decentralized energy supply in post-catastrophe scenarios. The vehicle modifications allowed for effective wood chipping, producing chips with an EROI of 3.7. Additionally, the vehicle-powered generator sustained a stable output of 20 kW electrical power, sufficient for some critical applications, such as water sanitation. Scalability analyses indicated potential limitations, particularly in the availability of woodchippers and engine oil. While increases in the production of woodchippers and lubricant recycling could mitigate these issues, further research is required to quantify the feasibility of such production in a GCIL scenario. Future research should also explore the long-term durability of modified vehicles and alternative methods for increasing electricity supply in GCIL scenarios. Additionally, the impact of global trade disruptions on material and labor availability should be assessed to ensure robust disaster preparedness. This work provides a foundation for developing resilient, decentralized energy systems capable of maintaining essential services during catastrophic events. By leveraging existing vehicle infrastructure and simple modifications, preparedness for future global challenges can be enhanced, ensuring the continuity of critical services.
Acknowledgement: The authors thank the University of Canterbury Mechanical Engineering Department workshop staff, particularly Tony Doyle, and Agriquip New Zealand for discounting the electricity generator.
Funding Statement: This work was funded in part by the Alliance to Feed the Earth in Disasters (ALLFED).
Author Contributions: Conceptualization: Joshua M. Pearce and David Denkenberger; Formal analysis: Henri Croft, James Hunt, Josh Viloria, Nathan Sherman, James Oliver, Brody Green, and Alexey Turchin; Investigation: Henri Croft, James Hunt, Josh Viloria, Nathan Sherman, James Oliver, and Brody Green; Methodology: Baxter L. M. Williams, Henri Croft, James Hunt, Josh Viloria, Nathan Sherman, James Oliver, Brody Green, Alexey Turchin, Juan B. García Martínez, and David Denkenberger; Project administration: David Denkenberger; Resources: Joshua M. Pearce, Juan B. García Martínez, and David Denkenberger; Supervision: Baxter L. M. Williams and David Denkenberger; Visualization: Baxter L. M. Williams; Writing—original draft: Baxter L. M. Williams, Henri Croft, James Hunt, Josh Viloria, Nathan Sherman, and James Oliver; Writing—review & editing: Baxter L. M. Williams, Joshua M. Pearce, Juan B. García Martínez, and David Denkenberger. All authors reviewed the results and approved the final version of the manuscript.
Availability of Data and Materials: All design files are available on the Open Science Framework: https://osf.io/k6v4f/ (DOI 10.17605/OSF.IO/K6V4F (accessed on 1 January 2025)). The raw data supporting the conclusions of this article will be made available by the authors on request.
Ethics Approval: Not applicable.
Conflicts of Interest: The authors declare no conflicts of interest to report regarding the present study.
Abbreviations
ASRS | Abrupt sunlight reduction scenario |
AVR | Automatic voltage regulator |
CVT | Continuously variable transmission |
DER | Distributed energy resource |
EROI | Energy return on investment |
GCIL | Global catastrophic infrastructure loss |
GCR | Global catastrophic risk |
GDP | Gross domestic product |
HEMP | High-altitude electromagnetic pulse |
OSF | Open science framework |
PCD | Pitch circle diameter |
PTO | Power take-off |
RPM | Revolutions per minute |
USD | United States dollar |
References
1. Ord T. The precipice: existential risk and the future of humanity. New York, NY, USA: Grand Central Publishing; 2020. [Google Scholar]
2. Anuat E, Van Bossuyt DL, Pollman A. Energy resilience impact of supply chain network disruption to military microgrids. Infrastructures. 2022;7(1):4. doi:10.3390/infrastructures7010004. [Google Scholar] [CrossRef]
3. Aitken C, Ersoy E. War in Ukraine: the options for Europe’s energy supply. World Econ. 2023;46(4):887–96. doi:10.1111/twec.13354. [Google Scholar] [CrossRef]
4. Cui L, Yue S, Nghiem XH, Duan M. Exploring the risk and economic vulnerability of global energy supply chain interruption in the context of Russo-Ukrainian war. Resour Policy. 2023;81(2):103373. doi:10.1016/j.resourpol.2023.103373. [Google Scholar] [CrossRef]
5. Bostrom N, Cirkovic MM. Global catastrophic risks. Oxford, UK: Oxford University Press; 2011. [Google Scholar]
6. Masters CD, Root DH, Attanasi ED. Energy: the basis of modern civilization. In: Challenged Earth: an overview of humanity’s stewardship of Earth. London, UK: Imperial College Press; 2006. 355 p. [Google Scholar]
7. Kjølle GH, Utne IB, Gjerde O. Risk analysis of critical infrastructures emphasizing electricity supply and interdependencies. Reliab Eng Syst Saf. 2012;105(6):80–9. doi:10.1016/j.ress.2012.02.006. [Google Scholar] [CrossRef]
8. Mechtenberg A, McLaughlin B, DiGaetano M, Awodele A, Omeeboh L, Etwalu E, et al. Health care during electricity failure: the hidden costs. PLoS One. 2020;15(11):e0235760. doi:10.1371/journal.pone.0235760. [Google Scholar] [PubMed] [CrossRef]
9. Plappally AK, Lienhard VJH. Energy requirements for water production, treatment, end use, reclamation, and disposal. Renew Sustain Energy Rev. 2012;16(7):4818–48. doi:10.1016/j.rser.2012.05.022. [Google Scholar] [CrossRef]
10. Lambert S, Van Heddeghem W, Vereecken W, Lannoo B, Colle D, Pickavet M. Worldwide electricity consumption of communication networks. Opt Express. 2012;20(26):B513–24. doi:10.1364/OE.20.00B513. [Google Scholar] [PubMed] [CrossRef]
11. Bostrom N. Existential risks: analyzing human extinction scenarios and related hazards. J Evol Technol. 2002;9:1–37. [Google Scholar]
12. Rickerson W, Gillis J, Bulkeley M. The value of resilience for distributed energy resources: an overview of current analytical practices. Golden, CO, USA: National Renewable Energy Laboratory; 2024. [Google Scholar]
13. Gilani MA, Kazemi A, Ghasemi M. Distribution system resilience enhancement by microgrid formation considering distributed energy resources. Energy. 2020;191(2):116442. doi:10.1016/j.energy.2019.116442. [Google Scholar] [CrossRef]
14. Wang F, Ge X, Yang P, Li K, Mi Z, Siano P, et al. Day-ahead optimal bidding and scheduling strategies for DER aggregator considering responsive uncertainty under real-time pricing. Energy. 2020;213(2):118765. doi:10.1016/j.energy.2020.118765. [Google Scholar] [CrossRef]
15. Moon JY, Park J. Smart production scheduling with time-dependent and machine-dependent electricity cost by considering distributed energy resources and energy storage. Int J Prod Res. 2014;52(13):3922–39. doi:10.1080/00207543.2013.860251. [Google Scholar] [CrossRef]
16. Hamidieh M, Ghassemi M. Microgrids and resilience: a review. IEEE Access. 2022;10:106059–80. doi:10.1109/ACCESS.2022.3211511. [Google Scholar] [CrossRef]
17. Mengelkamp E, Gärttner J, Rock K, Kessler S, Orsini L, Weinhardt C. Designing microgrid energy markets a case study: the Brooklyn Microgrid. Appl Energy. 2018;210(6):870–80. doi:10.1016/j.apenergy.2017.06.054. [Google Scholar] [CrossRef]
18. Aybar-Mejía M, Villanueva J, Mariano-Hernández D, Santos F, Molina-García A. A review of low-voltage renewable microgrids: generation forecasting and demand-side management strategies. Electronics. 2021;10(17):2093. [Google Scholar]
19. Guo Z, Li G, Zhou M, Feng W. Resilient configuration approach of integrated community energy system considering integrated demand response under uncertainty. IEEE Access. 2019;7:87513–33. doi:10.1109/ACCESS.2019.2924828. [Google Scholar] [CrossRef]
20. Williams B, Bishop D, Hooper G, Chase JG. Driving change: electric vehicle charging behavior and peak loading. Renew Sustain Energy Rev. 2024;189(5):113953. doi:10.1016/j.rser.2023.113953. [Google Scholar] [CrossRef]
21. Williams B, Bishop D, Docherty P. Assessing the energy storage potential of electric hot water cylinders with stochastic model-based control. J R Soc N Z. 2023;54(2):240–56. [Google Scholar] [PubMed]
22. Bishop D, Nankivell T, Williams B. Peak loads vs. cold showers: the impact of existing and emerging hot water controllers on load management. J R Soc N Z. 2023;221:1–26. doi:10.1080/03036758.2023.2286988. [Google Scholar] [CrossRef]
23. Pal P, Mukherjee V. Off-grid solar photovoltaic/hydrogen fuel cell system for renewable energy generation: an investigation based on techno-economic feasibility assessment for the application of end-user load demand in North-East India. Renew Sustain Energy Rev. 2021;149:111421. [Google Scholar]
24. Vaziri Rad MA, Kasaeian A, Niu X, Zhang K, Mahian O. Excess electricity problem in off-grid hybrid renewable energy systems: a comprehensive review from challenges to prevalent solutions. Renew Energy. 2023;212:538–60. [Google Scholar]
25. Turan O, Durusu A, Yumurtaci R. Driving urban energy sustainability: a techno-economic perspective on nanogrid solutions. Energies. 2023;16(24):8084. doi:10.3390/en16248084. [Google Scholar] [CrossRef]
26. Jamal S, Tan NML, Pasupuleti J. A review of energy management and power management systems for microgrid and nanogrid applications. Sustainability. 2021;13(18):10331. doi:10.3390/su131810331. [Google Scholar] [CrossRef]
27. Burmester D, Rayudu R, Seah W, Akinyele D. A review of nanogrid topologies and technologies. Renew Sustain Energy Rev. 2017;67:760–75. doi:10.1016/j.rser.2016.09.073. [Google Scholar] [CrossRef]
28. Amin S, Jamasb T, Llorca M, Marsiliani L, Renström TI, Sarkar A. Captive power, market access and macroeconomic performance: reforming the Bangladesh electricity sector. Energy Econ. 2021;102(3):105468. doi:10.1016/j.eneco.2021.105468. [Google Scholar] [CrossRef]
29. Ghosh R, Kathuria V. The transaction costs driving captive power generation: evidence from India. Energy Policy. 2014;75(150):179–88. doi:10.1016/j.enpol.2014.10.003. [Google Scholar] [CrossRef]
30. Abdul-Majeed MA, Al-Hadhrami LM, Al-Soufi KY, Ahmad F, Rehman S. Captive power generation in Saudi Arabia—overview and recommendations on policies. Energy Policy. 2013;62(5):379–85. doi:10.1016/j.enpol.2013.07.101. [Google Scholar] [CrossRef]
31. Ali Sadat S, Pearce JM. The threat of economic grid defection in the U.S. with solar photovoltaic, battery and generator hybrid systems. Sol Energy. 2024;282:112910. doi:10.1016/j.solener.2024.112910. [Google Scholar] [CrossRef]
32. Panteli M, Mancarella P. Influence of extreme weather and climate change on the resilience of power systems: impacts and possible mitigation strategies. Electr Power Syst Res. 2015;127:259–70. doi:10.1016/j.epsr.2015.06.012. [Google Scholar] [CrossRef]
33. Kahnamouei AS, Lotfifard S. Enhancing resilience of distribution networks by coordinating microgrids and demand response programs in service restoration. IEEE Syst J. 2022;16(2):3048–59. doi:10.1109/JSYST.2021.3097263. [Google Scholar] [CrossRef]
34. Kyriakidis M, Lustenberger P, Burgherr P, Dang VN, Hirschberg S. Quantifying energy systems resilience—a simulation approach to assess recovery. Energy Tech. 2018;6(9):1700–6. doi:10.1002/ente.201700841. [Google Scholar] [CrossRef]
35. Jasiūnas J, Lund PD, Mikkola J. Energy system resilience—a review. Renew Sustain Energy Rev. 2021;150:111476. doi:10.1016/j.rser.2021.111476. [Google Scholar] [CrossRef]
36. Zafeiropoulou M, Sijakovic N, Zarkovic M, Ristic V, Terzic A, Makrygiorgou D, et al. A flexibility platform for managing outages and ensuring the power system’s resilience during extreme weather conditions. Processes. 2023;11(12):3432. doi:10.3390/pr11123432. [Google Scholar] [CrossRef]
37. Savage E, Gilbert J, Radasky W. The early-time (E1) High-altitude electromagnetic pulse (HEMP) and its impact on the us power grid. Goleta, CA, USA: Metatech Corporation; 2010. [Google Scholar]
38. Hoad R, Radasky WA. Progress in high-altitude electromagnetic pulse (HEMP) standardization. IEEE Trans Electromagn Compat. 2013;55(3):532–8. doi:10.1109/TEMC.2012.2234753. [Google Scholar] [CrossRef]
39. Pennington HM, Hanley CJ, Rogers JD. Toward an electromagnetic event resilient grid. Proc IEEE. 2021;109(4):315–9. doi:10.1109/JPROC.2021.3062297. [Google Scholar] [CrossRef]
40. IEEE. 1366:2022. Guide for electric power distribution reliability indices. Piscataway, NJ, USA: IEEE Standards Association; 2022. [Google Scholar]
41. Skov NA, Papworth ML. Driving on wood: the lost art of driving without gasoline. Golden, CO, USA: Biomass Energy Foundation Press; 2006. [Google Scholar]
42. Janajreh I, Al Shrah M. Numerical and experimental investigation of downdraft gasification of wood chips. Energy Convers Manag. 2013;65(1):783–92. doi:10.1016/j.enconman.2012.03.009. [Google Scholar] [CrossRef]
43. Brynda J, Skoblia S, Pohořelý M, Beňo Z, Soukup K, Jeremiáš M, et al. Wood chips gasification in a fixed-bed multi-stage gasifier for decentralized high-efficiency CHP and biochar production: long-term commercial operation. Fuel. 2020;281(4):118637. doi:10.1016/j.fuel.2020.118637. [Google Scholar] [CrossRef]
44. Vennard H, Pearce JM, Denkenberger D. Wood chipper design for biofuel production in a global catastrophic loss of infrastructure scenario. Hardware. 2024;2(2):154–72. doi:10.3390/hardware2020008. [Google Scholar] [CrossRef]
45. Ingneiorsvetenskapsakademien, Biomass Energy Foundation. Generator gas: the swedish experience [with Wood]-gas 1939–1945. Golden, CO, USA: Biomass Energy Foundation; 1998. [Google Scholar]
46. Moersdorf J, Rivers M, Denkenberger D, Breuer L, Jehn FU. The fragile state of industrial agriculture: Estimating crop yield reductions in a global catastrophic infrastructure loss scenario. Glob Chall. 2024;8(1):2300206. doi:10.1002/gch2.202300206. [Google Scholar] [PubMed] [CrossRef]
47. Denkenberger DC, Cole DD, Abdelkhaliq M, Griswold M, Hundley AB, Pearce JM. Feeding everyone if the Sun is obscured and industry is disabled. Int J Disaster Risk Reduct. 2017;21:284–90. doi:10.1016/j.ijdrr.2016.12.018. [Google Scholar] [CrossRef]
48. Fraser EDG, Legwegoh A, Kc K. Food stocks and grain reserves: evaluating whether storing food creates resilient food systems. J Environ Stud Sci. 2015;5(3):445–58. doi:10.1007/s13412-015-0276-2. [Google Scholar] [CrossRef]
49. Nelson D, Turchin A, Denkenberger D. Wood gasification: a promising strategy to extend fuel reserves after global catastrophic electricity loss. Biomass. 2024;4(2):610–24. doi:10.3390/biomass4020033. [Google Scholar] [CrossRef]
50. Zheng G, Bu W. Review of heating methods for rural houses in China. Energies. 2018;11(12):3402. doi:10.3390/en11123402. [Google Scholar] [CrossRef]
51. Sellen M. What’s the difference between a limited-slip and an open differential? [cited 2024 Nov 23]. Available from: https://mechanicbase.com/transmission/open-vs-limited-slip-differential-differences/. [Google Scholar]
52. Pearce JM. CAD for vehicle conversion to power a woodchipper and an electrical generator. [cited 2024 Nov 22]. Available from: https://osf.io/k6v4f/. [Google Scholar]
53. Carfect. Car temperature gauge: what you need to know about your vehicle. [cited 2024 Nov 13]. Available from: https://carfect.com/need-know-car-temperature-gauge. [Google Scholar]
54. Chevrolet. A guide to your car’s temperature gauge: what’s normal and what’s not. [cited 2024 Nov 13]. Available from: https://www.vanchevrolet.com/blog/2017/june/19/a-guide-to-your-cars-temperature-gauge-whats-normal-and-whats-not.htm. [Google Scholar]
55. Smil V. Energy and civilization: a history. Cambridge, MA, USA: MIT Press; 2017. [Google Scholar]
56. Xia Z. Wood energy: basic knowledge. Rome, Italy: Food and Agriculture Organization of the United Nations; 2017. [Google Scholar]
57. Sadaka S. Gasification, producer gas and syngas. [cited 2024 Nov 18]. Available from: https://www.uaex.uada.edu/publications/PDF/FSA-1051.pdf. [Google Scholar]
58. Gao Y, Wang M, Raheem A, Wang F, Wei J, Xu D, et al. Syngas production from biomass gasification: influences of feedstock properties, reactor type, and reaction parameters. ACS Omega. 2023;8(35):31620–31. doi:10.1021/acsomega.3c03050. [Google Scholar] [PubMed] [CrossRef]
59. Satyanand A. Electricity (Safety) regulations 2010. Wellington, New Zealand: New Zealand Legislation; 2022. [Google Scholar]
60. Gard Timmerfors J, Salehi H, Larsson SH, Sjölund T, Jönsson LJ. The impact of using different wood qualities and wood species on chips produced using a novel type of pilot drum chipper. Nord Pulp Pap Res J. 2021;36(2):214–26. doi:10.1515/npprj-2019-0096. [Google Scholar] [CrossRef]
61. Méndez-González LC, Ambrosio-Lazaro R, Rodríguez-Borbon I, Alvarado-Iniesta A. Failure mode and effects analysis of power quality issues and their influence in the reliability of electronic products. Electr Eng. 2017;99(1):93–105. doi:10.1007/s00202-016-0399-9. [Google Scholar] [CrossRef]
62. Caicedo JE, Agudelo-Martínez D, Rivas-Trujillo E, Meyer J. A systematic review of real-time detection and classification of power quality disturbances. Prot Control Mod Power Syst. 2023;8(1):3. doi:10.1186/s41601-023-00277-y. [Google Scholar] [CrossRef]
63. Williams B, Bishop D, Gallardo P, Chase JG. Demand side management in industrial, commercial, and residential sectors: a review of constraints and considerations. Energies. 2023;16(13):5155. doi:10.3390/en16135155. [Google Scholar] [CrossRef]
64. Williams B, Bishop D. Flexible futures: the potential for electrical energy demand response in New Zealand. Energy Policy. 2024;195:114387. doi:10.1016/j.enpol.2024.114387. [Google Scholar] [CrossRef]
65. Walton M. The energy sector should care about wastewater. Paris, France: International Energy Agency [cited 2024 Nov 13]. Available from: https://www.iea.org/commentaries/the-energy-sector-should-care-about-wastewater. [Google Scholar]
66. World Health Organization. Electricity in health-care facilities. Geneva, Switzerland: World Health Organization [cited 2024 Nov 13]. Available from: https://www.who.int/news-room/fact-sheets/detail/electricity-in-health-care-facilities. [Google Scholar]
67. Statista. Statista electricity generation worldwide from 1990 to 2023. [cited 2024 Nov 13]. Available from: https://www.statista.com/statistics/270281/electricity-generation-worldwide/. [Google Scholar]
68. Toner R. How long does a generator last? [cited 2024 Dec 12]. Available from: https://timbersill.com/electrical/how-long-does-generator-last/. [Google Scholar]
69. Generator Hero. How long will a generator last? [cited 2024 Dec 12]. Available from: https://www.generatorhero.com/how-long-will-a-generator-last/. [Google Scholar]
70. Jose L, Raxworthy M, Williams BLM, Denkenberger D. Be Clever or be cold: repurposed ovens for space heating following global catastrophic infrastructure loss. EarthArXiv. 2024. doi:10.31223/X5P693. [Google Scholar] [CrossRef]
71. Hollingdale AC, Breag GR, Pearce D. Producer gas fuelling of a 20 kW output engine by gasification of solid biomass (ODNRI Bulletin No. 17). London, UK: Overseas Development Natural Resources Institute; 1988. [Google Scholar]
72. Statista. Worldwide automobile production since 2000. [cited 2024 Nov 13]. Available from: https://www.statista.com/topics/1487/automotive-industry/. [Google Scholar]
73. Motor and Wheels. How long does each car last? [cited 2024 Nov 13]. Available from: https://motorandwheels.com/how-long-car-models-last/. [Google Scholar]
74. Ma D. Self-excited induction generator: a study based on nonlinear dynamic methods [dissertation]. Newcastle upon Tyne, UK: Newcastle University; 2012. [Google Scholar]
75. Global Market Insights. Electric capacitor market size, share and industry analysis report. [cited 2024 Nov 13]. Available from: https://www.gminsights.com/industry-analysis/electric-capacitor-market. [Google Scholar]
76. Kluger MA, Long DM. An overview of current automatic, manual and continuously variable transmission efficiencies and their projected future improvements. SAE Trans. 1999;108(2):1–6. doi:10.4271/1999-01-1259. [Google Scholar] [CrossRef]
77. IMARC Group. Continuously variable transmission systems market report by vehicle type, type, fuel, end user, and region. [cited 2024 Nov 13]. Available from: https://www.imarcgroup.com/continuously-variable-transmission-systems-market. [Google Scholar]
78. Shadetree Automotive. Honda CVT reliability: what you should know. [cited 2024 Nov 13]. Available from: https://www.shadetreeautomotive.net/honda-cvt-reliability-need-to-know/. [Google Scholar]
79. Market Research Future. Recreational vehicles market research report. [cited 2024 Nov 2]. Available from: https://www.marketresearchfuture.com/reports/recreational-vehicles-market-7537. [Google Scholar]
80. Farmer T, Carlson J, Cramer K. How much does an RV cost? [cited 2024 Nov 13]. Available from: https://homeguide.com/costs/rv-cost. [Google Scholar]
81. Fortune Business Insights. Boats market size, share & industry analysis, By type, by size, by end-user, by propulsion, by hull, by application, and regional forecasts, 2024–2032. [cited 2024 Nov 13]. Available from: https://www.fortunebusinessinsights.com/boats-market-103854. [Google Scholar]
82. Storgaard M, Presgraves A. Average boat prices: 15 types explained. [cited 2024 Nov 13]. Available from: https://www.godownsize.com/average-boat-prices/. [Google Scholar]
83. Cosby AG, Lebakula V, Smith CN, Wanik DW, Bergene K, Rose AN, et al. Accelerating growth of human coastal populations at the global and continent levels: 2000–2018. Sci Rep. 2024;14(1):22489. doi:10.1038/s41598-024-73287-x. [Google Scholar] [PubMed] [CrossRef]
84. Pearce JM. Distributed manufacturing of open source medical hardware for pandemics. J Manuf Mater Process. 2020;4(2):49. doi:10.3390/jmmp4020049. [Google Scholar] [CrossRef]
85. Hsu J. Supplier assessment report [personal communication]; 2024. [Google Scholar]
86. Smith N. Motors as generators for micro-hydro power. Rugby, UK: Practical Action Publishing; 2007. [Google Scholar]
87. Markets and Markets. Synchronous generator market by prime mover, speed, power rating, end user & region—global forecast to 2028. [cited 2024 Nov 13]. Available from: https://www.marketsandmarkets.com/Market-Reports/synchronous-generator-market-183822134.html. [Google Scholar]
88. Grand View Research. Diesel generator market size, share & trends analysis report by power rating, by application, by region, and segment forecasts, 2024–2030. [cited 2024 Nov 13]. Available from: https://www.grandviewresearch.com/industry-analysis/diesel-gensets-industry. [Google Scholar]
89. Able Sales. 50kVA 415V 69Amps per phase diesel generator. [cited 2024 Nov 13]. Available from: https://www.ablesales.com.au/industrial-diesel-generators/21kva-to-55kva-single-and-3-phase/able-50kva-415v-diesel-generator.html. [Google Scholar]
90. Market Research Future. Induction motors market research report by product type, by type, by end-use and by region. [cited 2024 Nov 13]. Available from: https://www.marketresearchfuture.com/reports/induction-motors-market-1603. [Google Scholar]
91. Data INTELO. Three-phase induction motor market. [cited 2024 Nov 13]. Available from: https://dataintelo.com/report/three-phase-induction-motor-market. [Google Scholar]
92. Parker O. How much does an electric motor cost. [cited 2024 Nov 13]. Available from: https://storables.com/articles/how-much-does-an-electric-motor-cost/. [Google Scholar]
93. Bosch Mobility. Integrated motor-generator: electric drive system for plug-in hybrid vehicles. [cited 2024 Nov 1]. Available from: https://www.bosch-mobility.com/en/solutions/electric-motors/integrated-motor-generator/. [Google Scholar]
94. IEA. Global EV outlook 2024. [cited 2024 Nov 1]. Available from: https://www.iea.org/reports/global-ev-outlook-2024. [Google Scholar]
95. Ritchie H. Tracking global data on electric vehicles. [cited 2024 Nov 1]. Available from: https://ourworldindata.org/electric-car-sales. [Google Scholar]
96. Future Market Insights. Wood chipper market outlook (2022 to 2032). [cited 2024 Nov 13]. Available from: https://www.futuremarketinsights.com/reports/wood-chipper-market. [Google Scholar]
97. Haugh J. Woodchipper 2023 Buyer’s guide: all you need to know. [cited 2024 Nov 13]. Available from: https://www.forestryjournal.co.uk/features/forestry-journal-features/23602731.woodchipper-2023-buyers-guide-need-know/. [Google Scholar]
98. Youngk RD. Automobile engine reliability, maintainability and oil maintenance. In: Proceedings of the Annual Reliability and Maintainability Symposium. 2000 Proceedings. International Symposium on Product Quality and Integrity (Cat. No.00CH37055); 2000 Jan 24–27; Los Angeles, CA, USA. p. 94–9. [Google Scholar]
99. Statista. Private sector motor oil consumption in the United States from 2013 to 2024. [cited 2024 Nov 13]. Available from: https://www.statista.com/statistics/993731/private-sector-motor-oil-consumption-us/. [Google Scholar]
100. Worldometer. GDP by Country. [cited 2024 Nov 13]. Available from: https://www.worldometers.info/gdp/gdp-by-country/. [Google Scholar]
101. Hedges & Company. Automotive market research. [cited 2024 Dec 6]. Available from: https://hedgescompany.com/blog/2021/06/how-many-cars-are-there-in-the-world/. [Google Scholar]
102. Younggren PJ, Schwartz SE. The effects of trip length and oil type (synthetic versus mineral oil) on engine damage and engine-oil degradation in a driving test of a vehicle with a 5.7L V-8 engine. SAE Tech Pap. 1993;1:1–15. doi:10.4271/932838. [Google Scholar] [CrossRef]
103. Thorn R, Kollmann K, Warnecke W, Frend M. Extended oil drain intervals: conservation of resources or reduction of engine life. SAE Trans. 1995;104(4):706–18. doi:10.4271/951035. [Google Scholar] [CrossRef]
104. Sonde VM, Warnekar PN, Ashtankar PP, Ghutke VS. An approach to form manual power generalized experimental model for wood chipping process. In: Advances in Lightweight Materials and Structures: Select Proceedings of ICALMS 2020; 2020; Berlin/Heidelberg, Germany: Springer. p. 461–8. [Google Scholar]
105. Gili F, Igartua A, Luther R, Woydt M. The impact of biofuels on engine oil performance. Lubr Sci. 2011;23(7):313–30. doi:10.1002/ls.158. [Google Scholar] [CrossRef]
106. Cecilia JA, Ballesteros Plata D, Alves Saboya RM, Tavares de Luna FM, Cavalcante CL JrJr, Rodríguez-Castellón E. An overview of the biolubricant production process: challenges and future perspectives. Processes. 2020;8(3):257. doi:10.3390/pr8030257. [Google Scholar] [CrossRef]
107. Hafting FK, Kulas D, Michels E, Chipkar S, Wisniewski S, Shonnard D, et al. Modular open-source design of pyrolysis reactor monitoring and control electronics. Electronics. 2023;12(24):4893. doi:10.3390/electronics12244893. [Google Scholar] [CrossRef]
108. Chipkar S, Kulas D, Taylor T, Leverance E, Shonnard D. Upcycled group IV base oil lubricants generated from pyrolysis of military waste polyethylene and polypropylene plastics. In: Proceedings of the 2024 AIChE Annual Meeting; 2024 Oct 27–31; San Diego, CA, USA. [Google Scholar]
109. Kornelius G, Kruger S, Fouchee R, Van Wyk H. A wood gasification stove for domestic use: design, performance and emission factors. Clean Air J. 2012;22(2):14–6. doi:10.17159/caj/2012/22/2.7078. [Google Scholar] [CrossRef]
110. Manguiat NAS, Marco OC, Miranda CMN, Moren KO, Magnaye RLRRC. Design and development of a wood-fired gasifier prototype for synthesis gas production and analysis. Asia Pac J Multidiscip Res. 2015;3(5):160–6. [Google Scholar]
111. Bates R, Dölle K. Syngas use in internal combustion engines—a review. Adv Res. 2017;10(1):1–8. doi:10.9734/AIR/2017/32896. [Google Scholar] [CrossRef]
112. Fiore M, Magi V, Viggiano A. Internal combustion engines powered by syngas: a review. Appl Energy. 2020;276(3):115415. doi:10.1016/j.apenergy.2020.115415. [Google Scholar] [CrossRef]
113. Varne AR, Blouin S, Williams BLM, Denkenberger D. The impact of abrupt sunlight reduction scenarios on renewable energy production. Energies. 2024;17(20):5147. doi:10.3390/en17205147. [Google Scholar] [CrossRef]
114. Jehn F, Gajewski Ł, Hedlund J, Arnscheidt C, Xia L, Wunderling N, et al. Food trade disruption after global catastrophes. EarthArXiv. 2024. doi: 10.31223/X5MQ4R. [Google Scholar] [CrossRef]
Cite This Article
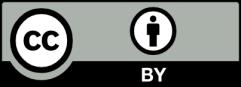
This work is licensed under a Creative Commons Attribution 4.0 International License , which permits unrestricted use, distribution, and reproduction in any medium, provided the original work is properly cited.