Open Access
ARTICLE
Production of Light Fraction-Based Pyrolytic Fuel from Spirulina platensis Microalgae Using Various Low-Cost Natural Catalysts and Insertion
1 Energy Conversion and Conservation Laboratory, Department of Chemical Engineering, Faculty of Technology and Vocational Education, Universitas Pendidikan Indonesia, Bandung, 40154, Indonesia
2 Center of Energy Research and Application (CERAP), Faculty of Technology and Vocational Education, Universitas Pendidikan Indonesia, Bandung, 40154, Indonesia
3 Center for Renewable Fuels Research (CRFR), Department of Mechanical and Industrial Engineering, Universitas Negeri Malang, Malang, 65145, Indonesia
4 Center of Advanced Materials for Renewable Energy (CAMRY), Universitas Negeri Malang, Malang, 65145, Indonesias
5 Department of Mechanical Engineering, Universitas Brawijaya, Malang, 65145, Indonesia
6 School of Chemical Engineering and Energy, Universiti Teknologi Malaysia, Johor Bahru, 81310, Malaysia
7 Department of Mechanical Engineering Education, Faculty of Teacher Training and Education, Universitas Sebelas Maret, Surakarta, 57126, Indonesia
* Corresponding Authors: Indra Mamad Gandidi. Email: ; Nugroho Agung Pambudi. Email:
Energy Engineering 2024, 121(12), 3635-3648. https://doi.org/10.32604/ee.2024.054943
Received 12 June 2024; Accepted 09 August 2024; Issue published 22 November 2024
Abstract
The use of catalysts has significantly enhanced the yield and quality of in-situ pyrolysis products. However, there is a lack of understanding regarding pyrolysis approaches that utilize several low-cost natural catalysts (LCC) and their placement within the reactor. Therefore, this study aims to examine the effects of various LCC on the in-situ pyrolysis of spirulina platensis microalgae (SPM) and investigate the impact of different types of catalysts. We employed LCC such as zeolite, dolomite, kaolin, and activated carbon, with both layered and uniformly mixed LCC-SPM placements. Each experiment was conducted at a constant temperature of 500°C for 60 min. The resulting pyrolytic liquids (bio-oil) and syngas were analyzed using a Gas Chromatography Mass Spectrometry (GC-MS) analyzer to determine the distribution of hydrocarbon compounds. The experimental results indicated that the presence of catalysts significantly influenced the mass yield productivity of liquid fuels and syngas. Activated carbon and zeolite were preferred among the four catalysts for producing liquid fuels (22.4 and 18.6 wt%) when layered and uniformly mixed, respectively. Kaolin with a layered mixture with SPM was more suitable for the production of light fractions (C5–C12), achieving approximately 95.7% peak area, while zeolite with a uniform mixture produced the highest light fraction at about 86.3% peak area. All catalysts except kaolin significantly increased the aromatic compounds in the liquid fuels. Although the amount of oxygenated hydrocarbons in the bio-oil remained relatively high, the final hydrocarbon composition was highly comparable to conventional fuels such as gasoline-88, which has a C5–C12 hydrocarbon distribution of approximately 88.1% peak area. Regarding the syngas products, all catalysts except activated carbon successfully converted nitromethane compounds into tetranitromethane hydrocarbons, with activated carbon predominantly yielding nitromethane compounds.Graphic Abstract
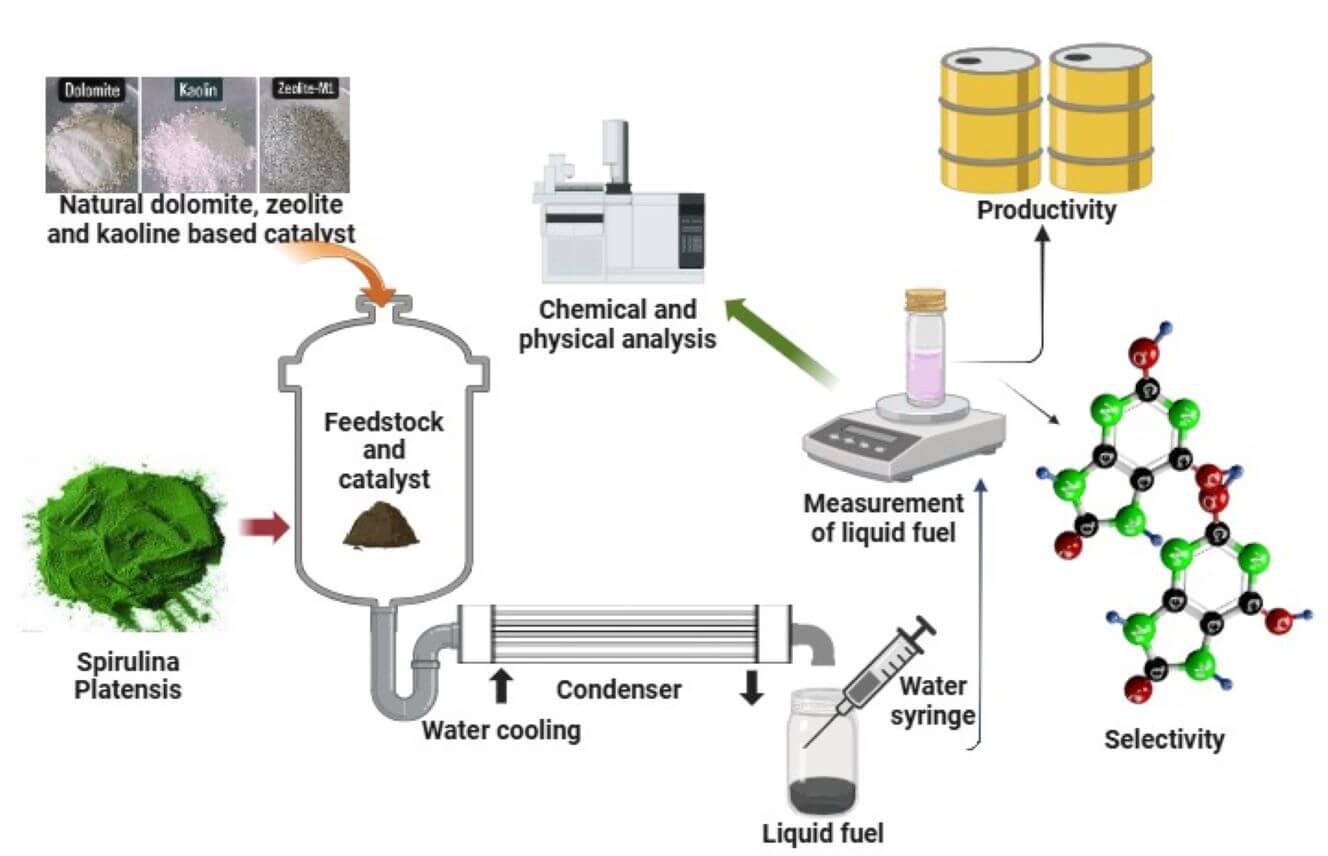
Keywords
Nomenclature
ASTM | American Standard Testing and Material |
C5–C12 | Range of gasoline hydrocarbon fraction |
C13–C20 | Range of diesel hydrocarbon fraction |
GC-MS | Gas Chromatography Mass Spectrometry |
HHV | Higher heating value |
LCC | Low-cost natural catalysts |
SPM | Spirulina platensis microalgae |
XRF | X-Ray Fluorescence |
CH | Hydrocarbon |
Subscript | |
m | Number of carbon |
n | Number of hydrogen |
Recently, global anxiety and concern about worsening global warming and the depletion of fossil fuel reserves have resonated across communities worldwide. This underscores the need for everyone to engage in mitigation actions aimed at minimizing CO2 and CH4 production, which are the primary sources of increased greenhouse gases. Consequently, the industrial sector is encouraged to reduce the use of coal as boiler fuel, the transportation sector to use electric or gas vehicles, and the residential sector to use gas fuels or electric appliances. Moreover, governments worldwide have actively engaged in significant efforts to manage and process municipal solid waste with the primary goal of preventing methane gas pollution [1]. However, current mitigation measures are unable to keep pace with the increasing fuel demand across various sectors. Therefore, a more practical approach is to create energy from sources other than fossil fuels, such as biomass, municipal solid waste, and other hydrocarbon resources [2].
Algal biomass is rich in proteins, lipids, and carbohydrates, making it a valuable source for biofuel production. These plants can be easily cultivated in diverse environments on a large scale with relatively short harvesting times and various types. Based on these characteristics, they have great potential and promise as an environmentally friendly energy source in the future, capable of replacing non-renewable resources [3]. Furthermore, due to its simplicity, short pathways, and minimal technological involvement, the pyrolysis process has emerged as a more favourable option compared to conventional thermochemical processes for creating biofuels from algal biomass [4]. Pyrolysis, also known as thermal degradation, is the process of breaking the chemical bonds of a feedstock composed of long-chain hydrocarbons in an oxygen-free reactor, resulting in the production of short-chain hydrocarbon compounds [5]. In a study conducted by Du et al., the pyrolysis of microalgae was carried out in a microwave oven reactor to produce bio-oil [6,7]. At a microwave power of 750 watts, the maximum bio-oil yield was approximately 28.6 wt%, with bio-oil properties such as a density of 0.98 kg/L, viscosity of 6.12 mm2/s, and HHV of 30.7 MJ/kg, with quality comparable to standard diesel fuel. Additionally, when using a fixed-bed tubular reactor at 500°C for slow pyrolysis of microalgae, a bio-oil yield of 43 v/v% can be achieved [8]. In terms of bio-oil productivity, the performance of the fixed-bed tubular reactor appears superior to that of the microwave oven reactor.
The liquid products from this process contain a very high number of nitrogen and oxygen molecules, significantly lowering their calorific value [9]. Conversely, the pyrolysis process shows inefficiency in energy utilization, especially at high temperatures and high electrical power input. Therefore, the use of catalysts to mitigate these challenges is highly recommended. Direct catalytic cracking (in-situ pyrolysis) techniques have the potential to reduce the pyrolysis operating temperature while enhancing the quality or selectivity of the bio-oil [10]. For instance, when activated carbon catalysts were used at 500°C in a fixed-bed reactor, they produced 50.2 wt% bio-oil with properties including a density of 0.88 kg/m3 and viscosity of 5.79 mm2/s [11]. The application of HZSM-5-based catalysts at a pyrolysis temperature of 500°C resulted in increased mass yield and decreased oxygen content in the bio-oil [12]. Moreover, the use of silica-alumina catalysts can reduce activation energy and reaction time [13], and there are several similar studies with consistent results on the presenceof catalysts.
Unfortunately, there is almost no information on the use of low-cost natural catalysts (approximately USD 0.04/kg) and their placement in the pyrolysis process of SPM. Uniform and layered mixing of catalysts will significantly contribute to the production of fuel from SPM. The reported results are mostly based on expensive synthetic catalysts. From an economic and business perspective, the high price of these catalysts will increase operational and production costs, resulting in costly pyrolysis products. Additionally, if synthetic catalysts are required, they must be imported from abroad. The cost and time considerations for importing synthetic catalysts are significant. Therefore, this study conducts in-situ pyrolysis experiments using various natural catalysts such as dolomite, zeolite, kaolin, and activated carbon. This step is necessary because natural catalysts are abundantly available and easy to obtain. Furthermore, studying the use of natural catalysts for promising liquid fuel production from SPM is essential given the increasing demand for green fuels.
In this study, SPM as the raw material was sourced from a local vendor located in Jepara, Central Java Province, with a moisture content of 6.11 wt%. Natural catalysts such as zeolite, dolomite, kaolin, and activated carbon were obtained from a local supplier located in Bandung City. The SPM underwent proximate, ultimate, and bomb calorimeter analyses to assess its initial properties before undergoing pyrolysis treatment. Before data collection through experimentation, all catalysts used were activated at a temperature of 150°C for 120 min by oven to minimize their moisture content and remove impurities present in the catalyst pores. The activated catalysts were then subjected to XRF analysis to determine the chemical characteristics of all catalysts. This was done because the characteristics of a solid catalyst are key parameters in breaking long hydrocarbon chains into shorter chains. After that, all SPM and catalysts were stored in tightly sealed containers before being used in pyrolysis experiments. Table 1 shows the chemical composition of SPM, while Tables 2 and 3 show the chemical composition of the catalysts.
Series of experiments were conducted within the energy conversion and conservation laboratory at the Indonesian University of Education, using a fixed-bed reactor to collect the necessary data. The reactor was constructed from a stainless-steel cylinder with an inner diameter of 50 mm and a height of 300 mm. At the upper end of the reactor, a sequential connection was established to link it with Condenser-1 and Condenser-2, serving as the refrigerator, for the separation of pyrolytic liquid fuel from permanent gases such as H2, CH4, CO, and CO2. To maintain oxygen-free conditions, nitrogen gas was introduced into the reactor before the experiment. In this study, an electric furnace with a heating rate of 20–23°C/min was used as a reactor heater to achieve a maximum reactor temperature of 600°C (Fig. 1).
Figure 1: Experimental setup of layered catalytic pyrolysis for Spirulina platensis microalgae
Regarding the experimental performance, a quantity of 100 grams of Spirulina platensis microalgae (without the presence of a catalyst) was introduced into the reactor. Subsequently, the electrical furnace was activated to serve as a heating device. Initially, the pyrolysis process took place under pressure by closing the flow valve leading to the condenser. After reaching the designated experimental temperature of 500°C, the valve was then opened to initiate the reaction, which was allowed to proceed for 40 min. The valve of the pyrolysis reactor was unsealed to facilitate the direct passage of the thermally degraded gas through condenser-1, operating at a temperature range of 25°C–30°C, and condenser-2, operating at a temperature range of 5°C–10°C. The pyrolytic liquid fuel was collected within a sample vial, while any non-condensable or permanent gas (referred to as pyrolytic gaseous fuel) was confined within a Tedlar sampling bag. After a 30-min cooling period in the pyrolysis reactor, the solid residue from the pyrolysis process, namely left over, was separated. The bio-oil and left over were later measured in terms of weight.
The thermal-catalytic pyrolysis (in-situ) process was conducted by combining the catalyst and microalgae in a ratio of approximately 1:1 (w/w). Before introduction into the reactor, the catalyst and microalga were meticulously mixed in an external setting. In this study, the second method used was the establishment of a multilayer interface between microalgae and catalysts. The microalga was introduced into the lower section of the reactor, while the catalyst was positioned above, thereby enveloping the microalga. The subsequent procedure included establishing the temperature and reaction duration in a manner that is analogous to pyrolysis in the absence of a catalyst.
This study was focused on evaluating the performance of a catalyst in the pyrolysis process by examining the quantity of biofuel produced and the composition of hydrocarbon compounds present in the resulting liquid fuel. To calculate the weight percentage of bio-oil, left-over, and syngas products can be calculated using Eqs. (1) to (3). Meanwhile, to calculate the distribution of gasoline and diesel fractions, Eq. (4) can be used.
Bio−oil(wt% )=mass of weighted Bio−oilmass of spirulina×100%(1)
Charcoal(wt% )=mass of weighted charcoalmass of spirulina×100%(2)
Syngas(wt% )=100% −(wt% bio−oil+wt% charcoal)(3)
Hydrocarbon range(% peak area)=fraction of CmHnTotal CmHn×100% (4)
where: m = 1, 2, 3, …, n = 1, 2, 3, ….
The SF-400 digital scale was used to measure the mass yield of liquid fuel and left over. To analyze the chemical composition of the liquid fuel, GC-MS analysis was used, and this analysis included the use of a mass spectrometer (MS, QP 2010 Ultra) and a gas chromatography (GC, Shimadzu 2010 Plus) system. Helium was used as the carrier gas at a rate of 1 mL/min, and the GC was equipped with a Rxi-5ms column (30 m, 0.25 mm, 0.5 m). The oven was preheated to 70°C and held at this temperature for one minute. After one minute, the temperature was increased to 300°C at a heating rate of 9°C per minute. Additionally, a separation ratio of 1:200 and a mass spectrum scanning range of 35–500 m/z were utilized. The GC-MS analysis was carried out using the Wiley 7 library to identify the chemical characteristics and quantify the distribution of hydrocarbon compounds.
This section covers the discussion on the potential impact of using natural catalysts in a fixed-bed reactor, as well as examining the effects of various types and insertions of low-cost natural catalysts. The primary emphasis of this research focuses on the selectivity and productivity of liquid and gaseous pyrolytic fuels, with special attention given to their correlation with mass yields and chemical properties.
3.1 Effect of Different Catalysts and Insertion on the Mass Yield Productivity
The effectiveness of the pyrolysis process is significantly influenced by the properties of the catalyst and the heat used, as both play crucial roles in breaking down long hydrocarbon chains into smaller fragments. On the other hand, catalyst characteristics have a high impact on selectivity, as this is related to the uniformity of hydrocarbon molecules in the liquid fuel. The mass yield for various types of catalysts mixed evenly with SPM biomass is shown in Fig. 2. Fig. 2 below illustrates the mass yields associated with each type of catalyst and without a catalyst. Additionally, catalytic pyrolysis demonstrates superior performance and produces a much higher volume of liquid fuel compared to when no catalyst is used.
Figure 2: Mass yield of Spirulina platensis pyrolyzed with uniform blended of LCC-SPM
The effectiveness of zeolite and dolomite catalysts in producing liquid fuel surpasses that of the other two catalysts, as shown in Fig. 2. The utilization of kaolin and activated carbon catalysts potentially facilitates the production of syngas fractions. This indicates that activated carbon and kaolin catalysts have lower reactivity levels compared to zeolite and dolomite catalysts. The significant reactivity and cracking tendencies exhibited by the catalysts are primarily due to their low Si/Al ratios and/or high Si-Al values. These characteristics lead to an increase in syngas production from the pyrolysis process [14–16].
However, these findings differ from the results documented by previous studies [17–20]. The differences in mass yields and liquid fuel properties can be attributed to the characteristics of the catalysts used and the duration of the reaction time. In addition to the catalyst properties and reaction time, the placement of the catalyst also has a significant impact on the quantity of liquid fuel produced. When the catalyst is mixed with the feedstock through layering or stacking on top, a noticeable decrease in the mass yield of liquid fuel occurs. This phenomenon indicates that when the catalyst is separated from the SPM, the freedom of the catalyst and active sites to perform cracking is reduced. Consequently, there is an increase in the solid residue products. However, the reduction in mass yield can be mitigated by implementing activated carbon, as shown in Fig. 3. This observation indicates that the layered arrangement of the catalyst has led to reduced cracking of the SPM material, related to the reduction in activation energy from the catalyst, and increased solid residue products at the end of the process.
Figure 3: Mass yield of Spirulina platensis pyrolyzed with a layered blend of LCC-SPM
Furthermore, the high silica-alumina content in kaolin and zeolite catalysts significantly influences the fragmentation of hydrocarbon molecules in the SPM, as opposed to using activated carbon. This is evidenced by the use of kaolin catalyst, which reduces solid products and increases syngas production [21–23]. On the other hand, dolomite catalyst shows minimal influence and increases the fraction of solid residue, primarily due to its very low silica and alumina concentration. Nevertheless, the advantage of layered mixing between SPM and the catalyst is the reduced impurities in the liquid fuel due to the entrainment of solid particles from SPM and the catalyst into the liquid fuel, as experienced in the mixed process between the catalyst and SPM.
3.2 Effect of Different Catalysts and Insertion to the Selectivity
The concept of carbon number distribution relates to the classification of various forms of liquid fuels. Furthermore, liquid fuels can be categorized into three distinct categories based on their carbon number distribution. These types include the gasoline fraction, which typically consists of carbon numbers ranging from C4 to C12; the diesel fraction, which consists of carbon numbers from C13 to C20; and finally, the heavy oil fraction (>C20) [24–26].
The distribution of carbon numbers in liquid fuels is greatly influenced by the specifications of the catalyst used. The surface texture and pore size of the catalyst play a crucial role in catalytic pyrolysis as they have the ability to guide reaction pathways and determine the selectivity of the products formed. Therefore, the addition of a catalyst has the potential to alter the overall composition and enhance the quality of the final products [27–29]. There is a positive correlation between the characteristics of the catalyst and the increase in catalytic activity [30–32]. Moreover, the application of this approach is expected to improve productivity and selectivity in producing pyrolysis products, which will reduce the amount of solid residue from the pyrolysis process.
The range of carbon numbers produced from the pyrolysis process using a homogeneous mixture of catalysts and SPM is shown in Fig. 4. Based on their high silica and alumina content, zeolite and kaolin catalysts have better cracking abilities compared to other catalysts [33–35]. This indicates that these two catalysts will yield the highest proportion of light fractions in the pyrolysis products. In fact, the zeolite catalyst produced 86.3% peak area in the gasoline light fraction, while the kaolin catalyst produced 58.4% peak area. The lower light fraction produced when using the kaolin catalyst reveals that kaolin is less reactive than zeolite and more dominant in diesel products. The very low Si-Al content characterizes that the acidity level of the kaolin catalyst is lower than that of zeolite. Meanwhile, the relatively low Si/Al ratio of activated carbon is quite promising in producing a better light fraction, although the mass of the fuel produced is relatively less. The dolomite catalyst, which also has very low Si and Al content, yields a higher product in the diesel fraction. The low Na and K content in dolomite also reduces the catalyst’s cracking ability [36,37].
Figure 4: Carbon number distribution in pyrolytic liquid fuel with uniform blended of LCC-SPM
Furthermore, the kaolin catalyst demonstrates superior performance when applied on top of SPM biomass, unlike the other catalysts, which show lower efficiency. This observed phenomenon can be explained by considering the chemical properties exhibited by each catalyst. Information in Table 2 and Fig. 5 show that the kaolin catalyst has a low Si/Al ratio and contains a significant amount of silica and alumina. These inherent characteristics make the kaolin catalyst highly reactive compared to other natural catalysts in a layered position. Conversely, the dolomite and activated carbon catalysts show much lower chemical compositions of Si and Al. While zeolite shows a very high composition of silica (Si) and alumina (Al), the silica-alumina (Si/Al) ratio is slightly high. These features make zeolite superior to dolomite and activated carbon in terms of selectivity and productivity performance.
Figure 5: Carbon number distribution in pyrolytic liquid fuel with a layered blend of LCC-SPM
Based on the GC-MS analysis results, the pyrolytic liquid fuel predominantly contains alkene and alkyne compounds (Table 4). The placement and type of catalyst significantly determine the chemical composition of the pyrolytic liquid fuel. Even mixing of SPM and LCC results in a predominance of alkene hydrocarbons in the pyrolytic liquid fuel. Meanwhile, layered mixing has shifted some alkenes into aromatic and alkane compounds [19,38]. The shift in alkene compounds heavily depends on the chemical composition of the LCC. Dolomite and activated carbon catalysts, with their low Al-Mg content and Si/Al ratio (Table 2), tend to convert alkenes into aromatic hydrocarbons. Conversely, the kaolin catalyst, with high Al-Mg content and a low Si/Al ratio, converts alkenes into alkane hydrocarbons. Zeolite, with high Al-Mg content and a high Si/Al ratio, converts alkenes into aromatic-rich fuels. Therefore, in terms of catalyst placement, layered mixing is advantageous for the production of aromatic-rich liquid fuels from SPM, supported by zeolite and activated carbon catalysts [39,40]. Unfortunately, pyrolytic liquid fuel from SPM still contains relatively high oxygen andnitrogen components.
Table 5 shows the chemical composition of syngas produced by pyrolysis. The main components of syngas consist of nitromethane or tetranitromethane. The syngas product from the pyrolysis of Spirulina without a catalyst predominantly yields tetranitromethane, propene, and pentanenitrile. The presence of natural catalysts has altered this composition. An even mixture of catalysts and Spirulina biomass has increased the tetranitromethane content and shifted propene and pentanenitrile to cyclobutene, except for the natural dolomite catalyst. On the other hand, the layered catalyst mixture has increased the nitromethane content with zeolite and activated carbon catalysts. Differences in Si-Al content and Si/Al ratio can be considered the cause of this variation. Tetranitromethane is a highly explosive chemical used as an oxidizer in rocket propellants, an additive in diesel fuel, in the manufacture of liquid explosives, and is highly hazardous to health. Meanwhile, nitromethane is a colorless, oily liquid with an unpleasant odor, highly flammable, and often used in various industrial applications as a solvent, and is easily soluble in water, alcohol, ether, acetone, and dimethylformamide [41,42]. Among the characteristics of these two chemical compounds, nitromethane is preferred as a fuel due to its lower carcinogenicity [43]. Thus, the pyrolysis process with layered mixtures of zeolite and activated carbon catalysts is more recommended.
As a feedstock for the catalyzed pyrolysis process that produces liquid fuel, SPM shows significant potential for development. Using a layered mixture model, activated carbon catalyst is highly recommended for the synthesis of liquid fuel from Spirulina platensis. However, to obtain liquid fuel dominated by light hydrocarbon fractions, the use of kaolin catalyst presents a great opportunity. Meanwhile, a layered mixture of kaolin and dolomite catalysts performs well in producing syngas from SPM. In terms of liquid fuel quality and catalyst longevity, the layered mixture concept is more advantageous compared to a uniform mixture. Zeolite catalyst is highly recommended in the catalytic process when mixed, as it yields a high mass fraction of light liquid fuel. This study strongly suggests employing numerous pyrolysis reactors in a two- or multi-stage pyrolysis method. Furthermore, it is advised to carry out a co-pyrolysis process using SPM and additional materials like coal, waste plastic, and other materials in order to boost the mass yield.
Acknowledgement: We extend our heartfelt thanks to Universitas Pendidikan Indonesia through DAPT-LPDP Program for their financial support. Finally, we thank our families and friends for their unwavering support and encouragement.
Funding Statement: This study was funded by Universitas Pendidikan Indonesia and the Ministry of Education, Culture, Research, and Technology through an Indonesian Research Collaboration of PTNBH Universities.
Author Contributions: Indra Mamad Gandidi: Conceptualization, Methodology, Analysis; Sukarni Sukarni: Data curation, Writing—original draft preparation; Avita Ayu Permanasari: Visualization, Investigation; Nugroho Agung Pambudi: Supervision; Purnami Purnami: Software, Validation, Writing—reviewing and editing; Tuan Amran Tuan Abdullah: Supervision; Anwar Johari: Supervision. All authors reviewed the results and approved the final version of the manuscript.
Availability of Data and Materials: As the lead researcher and responsible party for the study, I affirm that the data supporting the findings of this research are available from the corresponding author upon reasonable request. We acknowledge the importance of transparency and reproducibility in research and are committed to sharing our data with the scientific community. Researchers interested in accessing the data are encouraged to contact the corresponding author to discuss the details and terms of data sharing. For further inquiries or to request the data, please contact: Assoc. Prof. Dr. Indra Mamad Gandidi, with email address: indra.gandidi@upi.edu.
Ethics Approval: Not applicable.
Conflicts of Interest: This study is a partnership between Universitas Pendidikan Indonesia, Universitas Negeri Malang, Universitas Brawijaya and Universiti Teknologi Malaysia and all of the authors declare that there is no conflict of interest.
References
1. S. Nanda and F. Berruti, “Municipal solid waste management and landfilling technologies: A review,” Environ. Chem. Lett., vol. 19, no. 2, pp. 1433–1456, Apr. 2021. doi: 10.1007/s10311-020-01100-y. [Google Scholar] [CrossRef]
2. K. Alper, K. Tekin, S. Karagöz, and A. J. Ragauskas, “Sustainable energy and fuels from biomass: A review focusing on hydrothermal biomass processing,” Sustain. Energy Fuels, vol. 4, no. 9, pp. 4390–4414, 2020. doi: 10.1039/D0SE00784F. [Google Scholar] [CrossRef]
3. S. Pourkarimi, A. Hallajisani, A. Alizadehdakhel, and A. Nouralishahi, “Biofuel production through micro- and macroalgae pyrolysis–A review of pyrolysis methods and process parameters,” J. Anal. Appl. Pyrolysis, vol. 142, Sep. 2019, Art. no. 104599. doi: 10.1016/j.jaap.2019.04.015. [Google Scholar] [CrossRef]
4. S. Aravind, P. S. Kumar, N. S. Kumar, and N. Siddarth, “Conversion of green algal biomass into bioenergy by pyrolysis. A review,” Environ. Chem. Lett., vol. 18, no. 3, pp. 829–849, May 2020. doi: 10.1007/s10311-020-00990-2. [Google Scholar] [CrossRef]
5. N. Toscano Miranda, I. Lopes Motta, R. Maciel Filho, and M. R. Wolf Maciel, “Sugarcane bagasse pyrolysis: A review of operating conditions and products properties,” Renew. Sustain. Energ. Rev., vol. 149, no. 2, Oct. 2021, Art. no. 111394. doi: 10.1016/j.rser.2021.111394. [Google Scholar] [CrossRef]
6. Z. Du et al., “Microwave-assisted pyrolysis of microalgae for biofuel production,” Bioresour. Technol., vol. 102, no. 7, pp. 4890–4896, Apr. 2011. doi: 10.1016/j.biortech.2011.01.055. [Google Scholar] [PubMed] [CrossRef]
7. B. Sardi, H. Rachmawati, T. F. Maulana, E. Setiawati, N. Indrawan and M. Mahfud, “Advanced bio-oil production from a mixture of microalgae and low rank coal using microwave assisted pyrolysis,” Bioresour. Technol. Rep., vol. 21, Feb. 2023, Art. no. 101367. doi: 10.1016/j.biteb.2023.101367. [Google Scholar] [CrossRef]
8. F. Li, S. C. Srivatsa, and S. Bhattacharya, “A review on catalytic pyrolysis of microalgae to high-quality bio-oil with low oxygeneous and nitrogenous compounds,” Renew. Sustain. Energ. Rev., vol. 108, no. 23, pp. 481–497, Jul. 2019. doi: 10.1016/j.rser.2019.03.026. [Google Scholar] [CrossRef]
9. M. A. Babatabar, F. Yousefian, M. V. Mousavi, M. Hosseini, and A. Tavasoli, “Pyrolysis of lignocellulosic and algal biomasses in a fixed-bed reactor: A comparative study on the composition and application potential of bioproducts,” Int. J. Energy Res., vol. 46, no. 7, pp. 9836–9850, Jun. 2022. doi: 10.1002/er.7855. [Google Scholar] [CrossRef]
10. Q. T. Trinh et al., “Upgrading of bio-oil from biomass pyrolysis: Current status and future development,” in Bioref. Altern. Res.: Target. Green Fuels Platform Chem., Singapore: Springer Singapore, 2020, pp. 317–353. doi: 10.1007/978-981-15-1804-1_14. [Google Scholar] [CrossRef]
11. V. Aswie, L. Qadariyah, and M. Mahfud, “Pyrolysis of microalgae chlorella sp. using activated carbon as catalyst for biofuel production,” Bull. Chem. React. Eng. Catal., vol. 16, no. 1, pp. 205–213, Mar. 2021. doi: 10.9767/bcrec.16.1.10316.205-213. [Google Scholar] [CrossRef]
12. N. Chaihad et al., “Preparation of various hierarchical HZSM-5 based catalysts for in-situ fast upgrading of bio-oil,” Renew. Energy, vol. 169, pp. 283–292, May 2021. doi: 10.1016/j.renene.2021.01.013. [Google Scholar] [CrossRef]
13. S. Jamilatun et al., “Catalytic pyrolysis of spirulina platensis residue (SPRThermochemical behavior and kinetics,” Int. J. Technol., vol. 11, no. 3, pp. 522–531, Jul. 2020. doi: 10.14716/ijtech.v11i3.2967. [Google Scholar] [CrossRef]
14. A. A. Bianasari, M. S. Khaled, T. -D. Hoang, M. S. Reza, M. S. A. Bakar and A. K. Azad, “Influence of combined catalysts on the catalytic pyrolysis process of biomass: A systematic literature review,” Energy Convers. Manag., vol. 309, Jun. 2024, Art. no. 118437. doi: 10.1016/j.enconman.2024.118437. [Google Scholar] [CrossRef]
15. Q. Li, A. Faramarzi, S. Zhang, Y. Wang, X. Hu and M. Gholizadeh, “Progress in catalytic pyrolysis of municipal solid waste,” Energy Convers. Manag., vol. 226, no. Suppl 1, Dec. 2020, Art. no. 113525. doi: 10.1016/j.enconman.2020.113525. [Google Scholar] [CrossRef]
16. M. Abou Rjeily, C. Gennequin, H. Pron, E. Abi-Aad, and J. H. Randrianalisoa, “Pyrolysis-catalytic upgrading of bio-oil and pyrolysis-catalytic steam reforming of biogas: A review,” Environ. Chem. Lett., vol. 19, no. 4, pp. 2825–2872, Aug. 2021. doi: 10.1007/s10311-021-01190-2. [Google Scholar] [CrossRef]
17. L. A. Andrade, J. M. Barbosa, M. A. S. Barrozo, and L. G. M. Vieira, “A comparative study of the behavior of Chlamydomonas reinhardtii and Spirulina platensis in solar catalytic pyrolysis,” Int. J. Energy Res., vol. 44, no. 7, pp. 5397–5411, Jun. 2020. doi: 10.1002/er.5289. [Google Scholar] [CrossRef]
18. S. F. A. et al., “Pyrolysis-GCMS of Spirulina platensis: Evaluation of biomasses cultivated under autotrophic and mixotrophic conditions,” PLoS One, vol. 17, no. 10, Oct. 2022, Art. no. e0276317. doi: 10.1371/journal.pone.0276317. [Google Scholar] [PubMed] [CrossRef]
19. S. Jamilatun, R. Mahardhika, I. E. Nurshinta, and L. M. Sithopyta, “In-situ catalytic pyrolysis of spirulina platensis residue (SPREffect of temperature and amount of C12-4 catalyst on product yield,” Jurnal Rekayasa Proses, vol. 15, no. 1, p. 14, Jun. 2021. doi: 10.22146/jrekpros.60477. [Google Scholar] [CrossRef]
20. U. Jena and K. C. Das, “Comparative evaluation of thermochemical liquefaction and pyrolysis for bio-oil production from microalgae,” Energy Fuels, vol. 25, no. 11, pp. 5472–5482, Nov. 2011. doi: 10.1021/ef201373m. [Google Scholar] [CrossRef]
21. I. S. Golubev et al., “The effect of Si/Al ratio of zeolite Y in NiW catalyst for second stage hydrocracking,” Catal. Today, vol. 378, pp. 65–74, Oct. 2021. doi: 10.1016/j.cattod.2021.01.014. [Google Scholar] [CrossRef]
22. P. Kasar and Md. Ahmaruzzaman, “Characterization of liquid products obtained from catalytic binary co-cracking of residual fuel oil with various waste plastics,” Sci Rep., vol. 12, no. 1, Jun. 2022, Art. no. 10987. doi: 10.1038/s41598-022-15371-8. [Google Scholar] [PubMed] [CrossRef]
23. A. I. Eldahshory, K. Emara, M. S. Abd-Elhady, and M. A. Ismail, “Catalytic pyrolysis of waste polypropylene using low-cost natural catalysts,” Sci. Rep., vol. 13, no. 1, Jul. 2023, Art. no. 11766. doi: 10.1038/s41598-023-37769-8. [Google Scholar] [PubMed] [CrossRef]
24. Y. Nakagawa, M. Tamura, and K. Tomishige, “Recent development of production technology of diesel- and jet-fuel-range hydrocarbons from inedible biomass,” Fuel Process. Technol., vol. 193, pp. 404–422, Oct. 2019. doi: 10.1016/j.fuproc.2019.05.028. [Google Scholar] [CrossRef]
25. A. Matuszewska, M. Owczuk, and K. Biernat, “Current trends in waste plastics’ liquefaction into fuel fraction: A review,” Energies, vol. 15, no. 8, Apr. 2022, Art. no. 2719. doi: 10.3390/en15082719. [Google Scholar] [CrossRef]
26. J. T. Edwards, “Reference jet fuels for combustion testing,” in 55th AIAA Aerosp. Sci. Meet., Reston, Virginia, American Institute of Aeronautics and Astronautics, Jan. 2017. doi: 10.2514/6.2017-0146. [Google Scholar] [CrossRef]
27. K. W. Cheah, M. J. Taylor, G. Evans, A. Samson, and V. Skoulou, “Overview of biomass conversion to biofuels,” in Value-Chain of Biofuels. Elsevier, 2022, pp. 1–48. doi: 10.1016/B978-0-12-824388-6.00007-5. [Google Scholar] [CrossRef]
28. P. R. Bhoi, A. S. Ouedraogo, V. Soloiu, and R. Quirino, “Recent advances on catalysts for improving hydrocarbon compounds in bio-oil of biomass catalytic pyrolysis,” Renew. Sustain. Energ. Rev., vol. 121, Apr. 2020, Art. no. 109676. doi: 10.1016/j.rser.2019.109676. [Google Scholar] [CrossRef]
29. E. Yaman et al., “Catalytic upgrading of pyrolysis vapours: Effect of catalyst support and metal type on phenolic content of bio-oil,” J. Clean. Prod., vol. 185, no. 1, pp. 52–61, Jun. 2018. doi: 10.1016/j.jclepro.2018.03.033. [Google Scholar] [CrossRef]
30. Q. Che et al., “Influence of physicochemical properties of metal modified ZSM-5 catalyst on benzene, toluene and xylene production from biomass catalytic pyrolysis,” Bioresour. Technol., vol. 278, no. 1, pp. 248–254, Apr. 2019. doi: 10.1016/j.biortech.2019.01.081. [Google Scholar] [PubMed] [CrossRef]
31. H. Yang, Z. Chen, W. Chen, Y. Chen, X. Wang and H. Chen, “Role of porous structure and active O-containing groups of activated biochar catalyst during biomass catalytic pyrolysis,” Energy, vol. 210, Nov. 2020, Art. no. 118646. doi: 10.1016/j.energy.2020.118646. [Google Scholar] [CrossRef]
32. W. Chen et al., “Bamboo wastes catalytic pyrolysis with N-doped biochar catalyst for phenols products,” Appl. Energy, vol. 260, Feb. 2020, Art. no. 114242. doi: 10.1016/j.apenergy.2019.114242. [Google Scholar] [CrossRef]
33. S. Jafarian and A. Tavasoli, “A comparative study on the quality of bioproducts derived from catalytic pyrolysis of green microalgae Spirulina (Arthrospira) plantensis over transition metals supported on HMS-ZSM5 composite,” Int. J. Hydrogen Energy, vol. 43, no. 43, pp. 19902–19917, Oct. 2018. doi: 10.1016/j.ijhydene.2018.08.171. [Google Scholar] [CrossRef]
34. Z. Gong et al., “Catalytic pyrolysis of chemical extraction residue from microalgae biomass,” Renew. Energy, vol. 148, no. 31, pp. 712–719, Apr. 2020. doi: 10.1016/j.renene.2019.10.158. [Google Scholar] [CrossRef]
35. R. He et al., “Effects of Si and Al elements in coal on Fe-catalyzed brown coal pyrolysis,” Fuel, vol. 315, no. 9, May 2022, Art. no. 123170. doi: 10.1016/j.fuel.2022.123170. [Google Scholar] [CrossRef]
36. M. Safar et al., “Catalytic effects of potassium on biomass pyrolysis, combustion and torrefaction,” Appl. Energy, vol. 235, pp. 346–355, Feb. 2019. doi: 10.1016/j.apenergy.2018.10.065. [Google Scholar] [CrossRef]
37. W. Wang, R. Lemaire, A. Bensakhria, and D. Luart, “Review on the catalytic effects of alkali and alkaline earth metals (AAEMs) including sodium, potassium, calcium and magnesium on the pyrolysis of lignocellulosic biomass and on the co-pyrolysis of coal with biomass,” J. Anal. Appl. Pyrolysis, vol. 163, no. 1, May 2022, Art. no. 105479. doi: 10.1016/j.jaap.2022.105479. [Google Scholar] [CrossRef]
38. M. Dai, Z. Yu, S. Fang, and X. Ma, “Behaviors, product characteristics and kinetics of catalytic co-pyrolysis spirulina and oil shale,” Energy Convers. Manag., vol. 192, pp. 1–10, Jul. 2019. doi: 10.1016/j.enconman.2019.04.032. [Google Scholar] [CrossRef]
39. G. Yildiz, F. Ronsse, R. van Duren, and W. Prins, “Challenges in the design and operation of processes for catalytic fast pyrolysis of woody biomass,” Renew. Sustain. Energ. Rev., vol. 57, no. 2, pp. 1596–1610, May 2016. doi: 10.1016/j.rser.2015.12.202. [Google Scholar] [CrossRef]
40. Y. Xue, P. Johnston, and X. Bai, “Effect of catalyst contact mode and gas atmosphere during catalytic pyrolysis of waste plastics,” Energy Convers. Manag., vol. 142, pp. 441–451, Jun. 2017. doi: 10.1016/j.enconman.2017.03.071. [Google Scholar] [CrossRef]
41. S. Mohammadi and A. Foroumadi, “Nitromethane,” in Reference Module in Biomedical Sciences, Elsevier, 2023. doi: 10.1016/B978-0-12-824315-2.01096-4. [Google Scholar] [CrossRef]
42. L. Sánchez-Montero, M. Pérez-López, and F. Soler-Rodríguez, “Tetranitromethane,” in Reference Module in Biomedical Sciences, Elsevier, 2022. doi: 10.1016/B978-0-12-824315-2.00100-7. [Google Scholar] [CrossRef]
43. Z. R. Ismagilov and M. A. Kerzhentsev, “Catalytic fuel combustion—A way of reducing emission of nitrogen oxides,” Catal. Rev., vol. 32, no. 1–2, pp. 51–103, Feb. 1990. doi: 10.1080/01614949009349940. [Google Scholar] [CrossRef]
Cite This Article
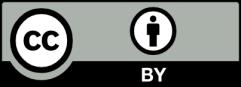
This work is licensed under a Creative Commons Attribution 4.0 International License , which permits unrestricted use, distribution, and reproduction in any medium, provided the original work is properly cited.