Open Access
REVIEW
Parametric Analysis and Design Considerations for Micro Wind Turbines: A Comprehensive Review
Department of Mechanical Engineering, Amrutvahini College of Engineering, Sangamner, 422608, India
* Corresponding Author: Dattu Ghane. Email:
Energy Engineering 2024, 121(11), 3199-3220. https://doi.org/10.32604/ee.2024.050952
Received 23 February 2024; Accepted 26 August 2024; Issue published 21 October 2024
Abstract
Wind energy provides a sustainable solution to the ever-increasing demand for energy. Micro-wind turbines offer a promising solution for low-wind speed, decentralized power generation in urban and remote areas. Earlier researchers have explored the design, development, and performance analysis of a micro-wind turbine system tailored for small-scale renewable energy generation. Researchers have investigated various aspects such as aerodynamic considerations, structural integrity, efficiency optimization to ensure reliable and cost-effective operation, blade design, generator selection, and control strategies to enhance the overall performance of the system. The objective of this paper is to provide a comprehensive design and performance review of horizontal and vertical micro-wind turbines. The study begins with an overview of the current landscape of wind energy across the globe and India in particular, highlighting key challenges and opportunities. Numerical and experimental studies were used to validate the designs. Horizontal Axis Wind Turbines (HAWTs) with ducts or shrouds are suitable for microscale and low-speed applications. Researchers investigated the position and location of the turbines to enhance their performance in urban settings. Airflow and airfoil noise produce aerodynamic noise, which is the most significant disadvantage of wind turbines. The findings provide valuable insights for stakeholders interested in advancing micro-wind turbine technology. The highlighted research opportunities may be pursued further to improve the efficiency, reliability, and overall performance of micro-wind turbines.Keywords
Wind energy, along with other renewable energy sources, plays a significant role in contributing to global sustainability goals. Its continuous expansion is imperative for fostering a sustainable and prosperous future worldwide. Wind energy plays a critical role in the global transition to renewable sources, reducing reliance on fossil fuels.
Mitigating climate change is a key function of wind energy, as it decreases carbon dioxide and other greenhouse gas emissions associated with electricity generation, assisting nations in meeting their emissions reduction targets. Wind power diversifies the energy mix, enhances energy security by utilizing indigenous wind resources, and boosts resilience to supply disruptions and geopolitical tensions. The growth of wind energy signifies a broader shift towards a more sustainable and resilient energy system, showcasing the feasibility and scalability of renewable technologies and inspiring global transition efforts.
Wind, an inexhaustible resource, is harnessed by wind turbines to generate electricity without burning fuel or polluting the air [1,2]. Renewable energy accounted for 13% of India’s electricity production and 25% of total installed capacity by March 2022, with a target of 40% by 2030 under the Paris Agreement [3]. There are many types of horizontal axis wind turbines, but only a few are really made to work well on small scales. This has made people more interested in designing and improving micro wind turbines, especially for areas with low wind speeds or in cities [4]. This study aims to review previous works in the wind energy sector and develop micro wind turbines suitable for such environments.
1.1 Global Energy Distribution Scenario
Demand for energy is growing across many countries in the world. In the case of wind energy, the use of renewable energy technologies is growing because of things like rising population and changing energy needs. Wealth may play a part, but it’s more important to look at bigger picture factors like energy demand, technological progress, and policy frameworks that encourage the use of wind energy. The global wind energy industry has witnessed remarkable growth over the years. In 2022, it was the third-best year ever for new wind energy capacity, with 78 GW added globally. The total installed global capacity reached 906 GW, representing a 9% year-on-year growth. In 2023, it is projected to be the very first to exceed 100 GW of new capacity added globally, with a forecasted year-on-year growth of 15%. 680 GW of new capacity is expected in the next five years (2023–2027), averaging 136 GW per year. However, trends documented in the Global Wind Report 2022 from the Global Wind Energy Council (GWEC) indicate that growth must quadruple by the end of the decade if the world is to stay on course for a 1.5°C pathway and net zero by 2050 [5].
From 1800 to 2022, there has been a significant and rapid growth in global energy consumption. Initially, traditional biomass was the primary source of energy until the early 20th century. The Industrial Revolution heralded the ascendancy of coal as a primary energy source, which was subsequently succeeded by the prominence of oil and natural gas in the mid-20th century [2]. Over the past few decades, there has been a substantial increase in the use of renewable energy sources such as wind, solar, and contemporary biofuels. Additionally, nuclear power has consistently played a role in the global energy mix, indicating a broader range of energy options.
1.2 Energy Distribution Scenario of India
Energy demand and consumption in India have experienced significant growth over the past few decades due to factors such as population growth, urbanization, industrialization, and economic development. The country’s energy sector is characterized by a diverse mix of energy sources, including fossil fuels (coal, oil, and natural gas) and renewables (solar, wind, hydroelectric, and biomass). Coal has historically been the dominant source of energy in India, primarily used for electricity generation. Oil and natural gas also play significant roles, particularly in transportation and industry. The demand for electricity in India has been growing steadily. This has put pressure on the country’s power infrastructure, leading to efforts to improve energy efficiency and expand electricity generation capacity. The government’s commitment to increasing access to electricity, improving energy efficiency, and reducing reliance on fossil fuels is reflected in initiatives, including the promotion of renewable energy. Wind energy holds immense potential for India’s sustainable development, contributing to environmental protection, economic growth, energy access, and energy security. Wind energy diversifies India’s energy mix, reducing reliance on conventional fossil fuels like coal and natural gas. This diversification contributes to a more balanced and sustainable energy portfolio. India has vast wind resources, especially in regions like Gujarat, Rajasthan, Tamil Nadu, and Maharashtra, making it one of the most suitable countries for wind energy development. Wind energy is renewable and clean, contributing to India’s efforts to reduce greenhouse gas emissions and combat climate change. It aligns with the country’s commitments under international agreements like the Paris Agreement. The cost of wind energy has become increasingly competitive with conventional sources of energy, especially as technology advances and economies of scale are achieved. This makes wind energy an attractive option for meeting India’s growing electricity demand. Wind energy can play a crucial role in electrifying remote and off-grid areas where extending conventional grid infrastructure is economically unviable. Off-grid wind power systems can provide reliable electricity access to remote communities.
As per the World Energy Outlook 2019 by the International Energy Agency, coal continues to be the primary source of worldwide energy consumption, accounting for 45% of the total. Petroleum and other liquids constitute 25% of the total, while biomass and garbage make up 20%. Natural gas accounts for 6% of the total contribution, whereas hydroelectricity, nuclear power, and other renewable sources each for 1%. This distribution highlights the ongoing worldwide dependence on fossil fuels, specifically coal and petroleum [2].
By the end of 2021, the country had the fourth-largest wind power capacity globally, totaling 40 GW, which was a 4% increase from the 38.62 GW generation in 2020. India is seeking to increase its green energy portfolio by utilizing the untapped coastal wind energy potential along its 7600 km shoreline. There has been a growing emphasis on offshore activities in recent years. The Ministry of Renewable Energy has established a goal of installing 30 gigawatts of offshore wind power by the year 2030. The Indian Wind Atlas indicates that the potential capacity for wind energy installation is approximately 102.79 GW at 80 m above ground level and 302.25 GW at 100 m above ground level. India’s offshore wind power business is in its early stages, with a potential capacity of approximately 60 GW. The coastal wind energy operational capacity grew from 25,088 MW in 2015 to 41.93 GW in 2022, as reported by IRENA. The trend is anticipated to rise in the upcoming years, contributing to the market’s expansion. The market is anticipated to be driven by the rising use of onshore wind energy, fueled by the expanding domestic wind sector.
As a result of increasing affluence and adapting to new ways of life, India has become the 3rd biggest global consumer of energy [6]. India will soon be the most populous nation on earth. India will need to add a power system the size of the European Union to its existing infrastructure in order to satisfy the rise in demand for electricity that is expected to occur over the course of the next two decades [7].
1.3 Installed Renewable Energy Capacity in India
As of April 2022, the installed renewable energy capacity in India was 158.12 GW, which represents 39.43% of the country’s total installed power capacity. When compared to the previous fiscal year’s first eight months, the addition of 8.2 GW of capacity for renewable energy sources occurred during the first eight months of the FY22 fiscal year. Solar energy’s installed capacity has expanded by a factor of 18 since March 2014, when it stood at 2.63 gigawatts (GW), to its projected level of 49.3 GW by the end of 2021. When compared to the 1.73 GW of solar power capacity that was built in FY21, India’s addition of 7.4 GW of solar power capacity in FY22 through December 2021 is a 335% increase. It is anticipated that 392,000 off-grid solar goods would be sold in India during the first half of the year 2021, suggesting a rapid increase in the utilisation of this renewable energy source. The amount of energy that was generated from renewable sources (other than hydro) in May 2022 was 19.31 billion units (BU), which is an increase from the 17.87 billion units (BU) that were generated in May 2021. In the period from April 2021 to March 2022, renewable energy sources generated 170.91 billion units (BU), which is an increase from the previous year’s production of 147.24 billion units (BU). When it comes to the overall wind power capacity built, the nation holds the fifth spot on the global list. When compared to the 1.73 GW of solar power capacity that was built in FY21, India’s addition of 7.4 GW of solar power capacity in FY22 through December 2021 is a 335% increase [8].
The domestic wind power business in India has shown steady expansion over the past few years, making it the leader in India’s wind energy industry. The growth of the wind sector has resulted in the development of a thriving ecosystem, the capacity to successfully operate projects, and a yearly manufacturing base of around 10,000 MW. By the end of March 2021, the country had the fourth highest amount of installed wind capacity in the world, totaling 39.25 gigawatts (GW). During the year of 2020–2021, it generated around 60.149 billion units [9].
1.3.1 Government Involvement in Favor of Wind Energy
The national government offers fiscal and financial incentives to the private sector in order to support the establishment of wind generating projects over the entirety of the country. This is accomplished through private sector investment. These incentives consist of a sped-up depreciation schedule as well as exemptions from having to pay customs duty on wind power generator components. In order to qualify for participation in the Generation Based Incentive (GBI) Scheme, wind energy projects have to have already been authorized by 31 March 2017, in order to be eligible. The administration of this country has taken the following steps, in addition to providing financial and other kinds of incentives, in order to encourage the development of wind power: The National Institute of Wind Energy in Chennai provides services including both wind resource assessment and site appraisal for potential wind farm locations. The issuance of these guidelines was done with the purpose of establishing a framework for the acquisition of wind power. These rules are intended to provide assistance to Distribution Licensees in the process of procuring wind energy at prices that are comparable to other sources [10].
Previous review papers have given useful information about micro wind turbine technology. This review paper is different because it focuses on the newest developments and innovations in design and parametric studies. While earlier reviews have been helpful, this paper fills a gap in the research by focusing on the design and parametric study aspects and giving a full analysis of recent developments. While many reviews have given broad overviews of different aspects of wind energy technology, not many have gone into specific detail about the design and parametric studies of micro wind turbines. This review paper carefully looks at the newest research results and compares them to previous research. The goal is to fill in any gaps in our knowledge and give a full picture of the latest developments in micro wind turbine technology.
Micro-wind generation employs wind turbines that are significantly more compact than those used in conventional wind generation, making them well-suited to domestic power generation. Micro-wind generating is a type of micro-generation that harnesses the natural energy of the wind to power a single building or an entire farm [11]. It is possible to set up either a horizontal axis wind turbine or a vertical axis wind turbine. The turbine and an inverter are the two main components of a typical micro wind turbine installation [12]. Mechanical energy is produced as the wind turns the blades of the wind turbine. The mechanical energy of spinning is transformed by the turbine into Direct Current (DC), and then by the inverter into Alternative Current (AC). The inverter’s output is wired to the home’s breaker panel, from which the electricity is fed to the various electrical devices throughout the dwelling. A bidirectional metre allows for the export of excess electricity from a home to the electrical grid, with the retailer issuing credits based on the electricity current tariff [13].
2.1 Classification Based on Axis of Rotation
2.1.1 Vertical Axis Wind Turbines (VAWTs)
Verticle axis wind turbines (VAWTs) may generate electricity in any wind direction and need only a low “cut-in” wind speed to function [14]. These turbines offer a significant improvement over traditional Horizontal Axis Wind Turbines (HAWTs) in terms of noise levels, weight, and ease of incorporation into preexisting buildings. They were considered practical for use in cities with varying wind conditions. Classifying VAWT layouts can be done in two ways, the Savonius and the Darrieus [15,16].
Savonius rotor
The Savonius rotor is made up of a number of hollow cylinders in the shape of a half cup, all of which are fastened to a central shaft that spins. The drag force acting on the halves of the cylinders generates torque. Savonius rotors use up less of the flow energy (only 20%) than Darrieus rotors. Therefore, this type of turbine is more commonly used for wind velocimetry than for producing significant amounts of electricity. In comparison to other ‘Lift type’ VAWTs, the Savonius rotor’s ability to kick itself into gear is its biggest selling point. The possibility of achieving commercial profitability in power generation is present with this configuration, subject to the advancement of efficient turbine designs [17].
Darrieus type wind turbine
Darrieus originally filed for a patent on his wind turbine ideas in 1931. The highest efficiency ratings among VAWTs go to these turbines, however their low starting torque and poor building integration are commonplace. Darrieus-type wind turbines function exclusively as lift-type turbines, with the rotor rotating and the generator being powered by the lift forces acting on the turbine blades [18].
2.1.2 Horizontal Axis Wind Turbines (HAWTs)
Wind turbines with a horizontal axis can yaw and spin on their own, unlike their vertically oriented counterparts. These turbines are more sensitive to wind direction than VAWTs, hence they are often placed at higher altitudes. Between 50% to 60% efficiency [19] is the sweet spot for these turbines.
2.2 Classification Based on Aerodynamic Force
Another way to classify wind turbines is by the type of aerodynamic force they generate, either lift or drag, at the blade’s surface. As the name implies, lift-type machines exert a force perpendicular to the direction that the wind is blowing, whereas drag-based Wind Turbines (WTs) use aerodynamics to push in the same direction as the air flow. Unlike HAWTs and Darrieus turbines, which rely purely on lift forces, Savonius turbines and other innovative types of VAWT are based on the drag forces. The drag-based turbines are simple in design but perform poorly overall. However, lift-based turbines capture more of the wind’s potential energy per square foot of swept area [15], despite their complexity. Table 1 summarizes of the research work on various blade profiles used and parameters for small scale wind turbine.
2.3 Classification Based on Rotor Diameter and Power Rating
There are several types of wind turbines that can create different amounts of energy based on the diameter of their rotors. Classification of HAWT based on rotor diameter and power rating were given in Table 2. Segmentations of wind turbines are used to categorise them, although there are no agreed-upon boundaries for these types of turbines. Small wind turbines typically have a rotor diameter of 0.5–10 metres with a power output of 50 watts to 15 kilowatts. They are used for low-power applications (battery charging, domestic consumption, cottages, etc.). Commercial applications typically require the design, installation, and connection to the grid of wind turbines with capacity of 15 kW or above (rotor diameters of 10 m or higher). A smaller wind turbine’s COE per unit of swept area is much more than that of a larger wind turbine.
2.4 Horizontal Axis Wind Turbines (HAWTs)
The turbine is located inside of a duct that has been specially constructed to look like an annular wing, with the suction side of the wing pointing inward. Ducted turbines, in comparison to turbines without ducts, are able to sustain lower pressure levels than the ambient air pressure. This leads to enhanced airflow and higher energy generation capabilities [33]. The current design of wind turbines makes use of a mechanism known as passive yawing, and it has been recommended that the shroud be self-stabilizing in order to lessen the stress that is placed on the control system [34]. The fundamental advantage of the shrouded wind turbine is its great efficiency, but there are several other reasons why it beats horizontal axis wind turbines of comparable diameter. It is not necessary to have a yaw control system while using the shroud for yaw angles that fall within the stall range, which is around +30 degrees. The enclosure that is established by the shroud helps to reduce the losses that occur at the tip of the turbine, and it also helps to eliminate the negative effects that are caused by the tower wake on the turbine. Because of the flow field that exists within the shroud, it is possible to use an axial flow turbine, which ultimately results in increased energy production. In addition, the cost of the tower for a shrouded wind turbine is considerably less than the cost of a normal horizontal-axis wind turbine [33].
In comparison to the performance of the naked turbine, the installation of a simple conical diffuser increased the micro wind turbine’s coefficient of performance by around 60%. The coefficient of performance increased by 63% after the addition of a conical diffuser shroud for the nozzle. The ideal tip speed ratio for the diffuser and nozzle-diffuser advancements was determined to be 33% greater when compared to the bare turbine. The study revealed that the nozzle-diffuser enhancement yielded a minimal increase compared to the diffuser enhancement. The difference between the two was only 1.7% in favor of the turbine using diffuser augmentation [35].
2.5 Performance of Micro Scale HAWT
Numerous research was undertaken to optimise the design parameters in order to increase performance, and a number of methods for estimating the aerodynamic characteristics of wind turbines were published. The aerodynamic performance of wind turbine is largely influenced by blade profile, the different types of blade profiles used for the study are as shown in Fig. 1. On the aerodynamic performance of tiny turbines, additional characteristics, such as rotor solidity and blade number, have also been explored [36,37].
Figure 1: Different blade profiles used for small scale wind turbines
Wind tunnel experiments and the Lattice Boltzmann Method (LBM) were used to examine the performance and interaction of two-stage rotors in micro–Counter Rotating Wind Turbines (CRWTs) [22]. The counter-rotating method improves the wind power coefficient of HAWT, whereas micro CRWT has two schemes that achieve the same result. National Renewable Energy Laboratory (NREL) Phase VI’s numerical study on the effect of pitch angle on HAWT performance led to the following conclusions. The Shear-Stress Transport (SST) k-model predicts thrust and power well. Most of the time, the SST turbulence model is used to simulate turbulent flow phenomena in Computational Fluid Dynamics (CFD). It takes the best parts of two well-known turbulence models and puts them together: the k-ω (k-omega) model near the walls and the k-ε (k-epsilon) model in the flow regions on the outside. The SST model can accurately represent both near-wall and far-from-wall turbulent flow behavior thanks to this hybrid approach. This makes it useful for many situations, such as those with complex geometries and boundary layer flows. Because micro turbines are smaller and have lower Reynolds numbers than utility-scale turbines, they often have different flow characteristics, such as being more sensitive to turbulence and boundary layer effects. For a given wind speed, there is an optimal pitch angle that maximizes turbine power. Wind speed determines the optimal angle. As air velocity increases, momentum transfer increases, increasing thrust. Increased pitch angle reduces blade frontal area and drag, reducing thrust [38,39].
The capacity of a wind turbine to convert wind energy into electricity is its efficiency. Using the National Advisory Committee for Aeronautics (NACAs) data and Qblade airfoil modelling, the efficiency and power of new airfoils were studied in the past [39]. According to NREL, the choice of airfoil should maximise lift. The National Aeronautics and Space Administration preferred lift-based airfoils over lift-to-drag ratio. Three high-lift airfoils are being modelled in Qblade. A NACA 23012 5-digit airfoil is utilised in power generation [40]. According to Qblade, the addition of turbine blades boosts power. New airfoils and an optimised pitch were used to test this notion. The end product of the project is a portable turbine with four sets of blades capable of producing 10 watts of power in various conditions. The modular hub and blades make wind blade replacement simple. The 5-blade model cut 3.35 m/s. Reduced power increases efficiency. The 7-blade type provides the highest power between 3 and 4 m per second. Six-blade designs operate best over 5 m/s. The Alpha model generates 10 watts in winds greater than 10 m per second and is advised for safety [40].
Ronit et al. developed a low Reynolds number airfoil for use in tiny horizontal axis wind turbines to improve start-up and operational efficiency in low wind speeds. Tests were conducted on the upgraded airfoil (AF300) in an open circuit wind tunnel at Reynolds numbers of 38,000, 75,000, 128,000, and 205,000. Pressure variations were collected throughout the airfoil’s surface, and lift and drag forces were quantified using a dynamometer at various angles of attack, α. Particle Image Velocimetry (PIV) and smoke flow visualization were employed to analyze the airflow around the airfoil. Maximum lift coefficients of 1.72, 1.81, and 1.86 were achieved at Reynolds numbers of 75,000, 128,000, and 205,000, respectively, with a stall angle of 140 degrees. The lift coefficient rose from 0.41 to 1.05 at Re = 38,000 within the α range of 0–180, with no stalling observed [21].
The results from particle image velocimetry and smoke flow visualization showed that the flow stayed fully attached to the airfoil surface from Re as low as 56,000 at an angle of attack of 80 and maintained a fully attached flow up to 140 angle of attack for Re as low as 75,000.
The typical lifespan of a modern wind turbine is estimated to be twenty years, and the comparable number of rotations is somewhere between 108 and 109. The choice of material and the shape that it takes are the two most important aspects of the design of a rotor blade. The material that is chosen needs to be able to withstand wear and tear while also being relatively lightweight [41–43].
In the study, a computerized model was suggested for determining the amount of ice load that would be placed on wind turbine wing portions that were 80% of their span. Calculating the torque coefficient for four clear and iced rotors at different Angles of Attack (α) allows one to analyse how the buildup of ice affects the efficiency of a HAWT by measuring the influence of lower lift and greater drag brought on by the formation of ice. A rotor blade with a radius of 40 m is used in the calculation of the angle of relative wind; thus, rotor blades with a radius of 32 m are used in the calculation of the torque coefficient. In addition to that, a Tip Speed Ratio (TSR) of 6 and a wind speed of 15.3 m/s are presumed [44].
Stereoscopic Particle Image Velocimetry (PIV) was used to analyze the near-end transition-wake of a 0.6 m horizontal-axis wind turbine model [45]. The tip speed ratio impacts the structures and mixing qualities of the wake flow. Analysis of the structure of vortices reveals that wake instability relies on rotor tip speed ratio. Experimental work performed on small scale horizontal axis wind turbines presented in Table 3. As evidenced by unconditioned and phase-lock average velocity fields, wake instability influences flow characteristics [45].
The research shows that a powerful root vortex that is released from the maximum chord results in an outboard radial motion at the root region and a similar inboard motion at the maximum chord area (at r/R = 0.3). Both of these movements can happen at the identical radial point in relation to the turbine radius (r/R). This process results in a rise in axial velocity [55]. The effect of yaw angle on blade power with respect to different rpm speeds. Abu Dhabi’s accumulated wind hours are used to compare micro wind turbine performance and economics. The study says ATT’s payback is 1.83 years. ATT micro wind turbines could replace commercial wind turbines. Using the same swept area produces more energy, according to the study [56]. Salih N. et al. introduced an innovative design of a micro wind turbine optimized for low wind speed areas including the Arabian Peninsula, Jordan Desert, and United Arab Emirates (UAE). The experimental validation confirms the accuracy of the theoretical design’s performance analysis, demonstrating a high level of agreement between the two results. The theoretical power coefficient is 0.38, while the experimental power coefficient is 0.34 [22]. A prototype is created using a 3D printer to validate the simulation. The ATT prototype blades are tested in an open-air environment to achieve more realistic results. A methodology for designing ATT blades that incorporates Reynolds Number as a design parameter has been created and applied. The operational Reynolds number is taken into account together with the Blade Element Momentum (BEM) theory specifications since the lift and drag coefficients of the airfoils depend on it. The Reynolds number significantly impacts the performance of turbine blades. Reynolds number sensitivity research indicates that the ATT turbine blade airfoil SG6043 outperforms the NACA 4412 and SG6042 airfoils, as illustrated in Fig. 2. The Reynolds number is determined by the average chord length of the blade, while maintaining a constant wind speed of 5 m/s as the primary goal for designing micro turbine blades. The Reynolds number is estimated relatively high at first as 120000, and after three iterations for NACA 4412 and SG6042, it settles down to about 25000. Nonetheless, Airfoil SG6043 continues to oscillate in proximity to Reynolds number 25000.
Figure 2: Illustration of SG6042, SG6043 and NACA4412 Airfoil Profiles in dimensionless format with respect to the chord length
It has been shown that neuro fuzzy control is a very reliable and secure method for managing established boundaries, and it can operate with steady-state, sinusoidal, and random wind profiles. In light of the fact that it was difficult to construct either a linear or a nonlinear plant, a database was utilised in order to fit the control. The control unit showed some encouraging capabilities, including being able to deter overload and reduce the amount of time required to overcome inertia. By preventing unnecessary wear and tear caused by low wind speed, an automatic timer that calculates the mean wind speed could be of great use. Training for the controller can be done with the neuro fuzzy tool, or it can be done manually if necessary. By providing the data set following the definition of the control rules, this tool made the process of designing the rules much simpler [57].
Simple passive controllers can be found on very small horizontal-axis wind turbines. These systems comprise tilt-up structures, gravity-operated furling tails, side-vanes, and spring-loaded tails. Microturbines that have a flexible tail that shifts as well as an off-center pivot offer a greater controlling ability and a more straightforward construction. This strategy is non-invasive, low-risk, dependable, and easy to execute [58].
France’s Georges Darrieus is credited with developing the first aerodynamic vertical-axis wind turbine, which was initially patented in 1931. Its operating principle relies on the fact that the speed of its blades is a multiple of wind speed. This results in an apparent wind blowing from behind the turbine all through the entire cycle, with minimal fluctuation in the angle of attack. Summary of wind turbine configurations with capacity and different features were been presented in Table 4. When combined to the actual wind, this headwind produces the perceived wind. If the angle of attack of this observed wind on the blade is larger than zero [59], the lift force contains a forward component that propels the turbine.
Wind tunnel testing and Particle Image Velocimetry (PIV) are the primary experimental techniques used for studying Darrieus Vertical Axis Wind Turbines (VAWTs) [74]. Summary of experimental work on vertical axis wind turbine given in Table 5. The trial results indicate that the conventional practice of adjusting upstream velocity in wind tunnels to account for blockage effects may not be directly suitable for Vertical Axis Wind Turbines (VAWTs) [74]. These most likely results in underestimation of the correction rates for all of the cases considered. Moreover, according to the results of tests, the significance of upstream velocity adjustments decreases as the thrust coefficient increases [75].
There are differences between the computed and measured force coefficients and wake characteristics in validation scenarios. Summary of numerical work performed on small scale Darrius wind turbine given in Table 6. The anticipated power gains and trends lend credibility to the ideas. This research demonstrates the ability to regulate and use wake zones in VAWT arrays to attain high wind farm efficiency.
3.1.3 Savonius Type Wind Turbine
The Savonius rotor is a wind turbine with a vertical axis that operates mostly due to wind drag forces acting on its buckets. However, lifting forces also contribute to the transmission of mechanical power to the turbine shaft [94,95]. The structural solution for the Savonius rotor comprises of two or more blades positioned along the rotor’s central axis to capture a portion of the main air stream. There are numerous sorts of blades, each with a unique section form and each positioned at a unique distance from the rotor’s centre axis. This separation is known as the blade gap [96].
As mentioned earlier, small-scale wind turbines can efficiently fulfill the energy requirements of homes. However, the placement of these turbines is also vital in order to achieve maximum efficiency. Small-scale wind turbines have become a practical option for fulfilling the energy requirements of residential properties. Nevertheless, the strategic placement of these turbines is crucial in order to attain optimal efficiency. Multiple experiments have been carried out to determine the optimal locations for the placement of wind turbines. Topographical characteristics, such as elevations, depressions, and plant life, can greatly impact the movement of air currents. Multiple experiments have been conducted to determine the optimal location for placing wind turbines [97]. The topography, barriers, and adjacent constructions in the vicinity can affect the direction and intensity of wind currents, leading to turbulent conditions that may affect the efficiency of small wind turbines. Optimization techniques are employed to ascertain the optimal arrangement and design of turbines for a specific location. This entails employing mathematical modeling, computer simulations, and iterative design processes to determine the most advantageous placement of turbines in relation to one another and nearby obstacles. In order to tackle these challenges, optimization techniques are utilized to ascertain the most efficient arrangement and setup of turbines for a specific location [98]. This procedure frequently entails the utilization of advanced mathematical modeling, computer simulations, and iterative design processes. By employing these techniques, engineers and researchers can examine wind flow patterns, turbulence impacts, and wake interactions to determine the most advantageous placement of turbines in relation to one another and nearby obstacles. This article provides a comprehensive account of the planning, building, and overseeing of El Alumbre’s inaugural wind energy project, aimed at providing electricity to rural areas in Peru. The project is designed to generate power on a community-wide scale.
3.3 Aeroacoustics of Wind Turbines
Wind turbine noise limits widespread wind energy adoption. Assuming that mechanical noise is well-controlled, aerodynamic noise from the blades dominating current large wind turbines. Aerodynamic noise is caused by airflow and airfoil noise. Low-frequency noise from upwind turbines is unimportant (i.e., with the rotor upstream of the tower). The leading edge of the blade and upstream turbulence generate inflow noise. On a three-bladed, 58-m-diameter wind turbine, acoustic field measurements were undertaken to identify noise sources and determine if trailing edge noise was predominant. Blade roughness was evaluated using untreated, cleaned, and scuffed blades. A broad horizontal microphone array assessed the rotor plane and blades for noise. The results of the array indicate that nearly all noise (emitted to the ground) is generated during blade fall. Convective amplification and trailing edge noise result in an asymmetric source pattern. The blades’ loudness was proportional to the flow speed. The slashed blade was more audible. The narrowband noise spectrum of a blade revealed that trailing edge bluntness noise was unimportant. According to tests [99], trailing edge noise dominates wind turbine noise.
3.4 Performance Assessment of Micro Wind Turbines Installed on Site
The issue of wind turbine noise is a substantial concern that can have an effect on the widespread acceptance of wind energy. Although wind turbines generally have effective measures to minimize mechanical noise, the main source of noise in modern large wind turbines is aerodynamic noise, specifically from the blades. Aerodynamic noise is primarily caused by the interactions between airflow and airfoils. This study compares and contrasts the findings of the estimated annual energy production and cost-benefit evaluations conducted using actual wind speed data from various locations in the United Kingdom. The evaluations were performed under both steady state and dynamic conditions. The obtained results were derived from actual wind speed measurements. Therefore, to evaluate the performance in a stable condition, the wind power input is determined by employing Weibull distributions, with the user having the flexibility to choose the shape factors and mean wind speeds. The study utilized acoustic field measurements with a wide horizontal microphone array to evaluate noise levels at the rotor plane and on the blades. The evaluation of blade roughness involved comparing untreated, cleaned, and scuffed blades to determine the effect it has on noise production. The payback period for micro-wind turbines (micro-WTs) with rated powers of 1.5 kW or less is the most extended, and it may surpass the initially intended lifespan of these turbines. These micro-wind turbines make up 84% of all small and micro-wind turbines that have been installed in urban areas of the United Kingdom. The results unveiled various significant revelations regarding wind turbine noise. Initially, it was noted that the predominant amount of noise produced towards the ground happens when the blades descend, which is commonly referred to as blade fall. This indicates that phenomena such as convective amplification and trailing edge noise have a substantial impact on the production of noise. According to a study, micro-wind turbines with a maximum power output of 1.5 kW or less account for 84% of all small-scale wind turbines installed in urban areas of the United Kingdom [100].
4 Summary of Research Work on Micro Wind Turbine
Scientific and industrial research is needed to develop and optimize microwind turbine rotors. Global research focuses on designing and building large-scale wind turbines that generate electricity and supply grid connections. Smaller wind turbines contribute much less kW than larger ones. Miniature wind turbines on homes are feasible. Micro wind turbines reduce fossil fuel emissions, boosting renewable energy production. Their compact size makes these turbines cost-effective. Several scholars have proposed diffuser-equipped wind turbines. Over time, diffusers have evolved, and the flanged diffuser can increase power by four to five times. In contrast, a diffuser makes the wind turbine larger. This increases aerodynamic drag, requiring a strong attachment. Micro wind turbines have been extensively studied, but low-speed, ground-mounted wind turbines have received little attention. The literature has little research on improving wind turbine performance. Therefore, there are many research opportunities to analyze and optimize low-speed micro wind turbine performance parameters.
It is known that large-scale wind turbines have an effect on global climates. Although large-scale wind farms are unsustainable, small-scale wind turbines offer a tremendous deal of potential for generating valuable energy that can be sufficient for home requirements. Following are the outcomes of the analysis:
• By the first half of 2022, India’s installed renewable energy capacity (including hydro) had reached 158.12 GW, or 39.43% of the country’s total installed power capacity.
• For the most part, the BEM theory was utilized to design HAWT blades, which involved establishing the best distributions of pitch angle and chord length in each segment under the design point.
• Enhancing design parameters such as tip speed ratio, blade twist angle, number of blades, chord length, and Reynolds number improved WT performance.
• Numerical and experimental studies were used to validate the designs. HAWTs with ducts or shrouds are suitable for microscale and low-speed applications. The flow rate through a shroud-mounted turbine is much higher than that of equivalent unducted turbines. As a result, this process generates more electricity.
• To provide stronger control of the turbine, sophisticated computational approaches such as neurofuzzy control have been developed, which have proven to have a promising capacity to prevent overpowering and shorten the time required to overcome inertia.
• Researchers studied the position and location of the turbines to improve their performance in urban settings. Airflow and airfoil noise produce aerodynamic noise, which is the most significant disadvantage of wind turbines. This has hindered WT adaptation in urban environments. Efforts are underway to reduce the noise, but progress is slow.
The literature has reported ample research, but here are some research opportunities related to micro-wind turbines to enhance their efficiency, reliability, and overall performance:
1. Investigate advanced aerodynamic designs and materials for turbine blades to improve energy capture and efficiency in low-speed conditions. Explore the use of variable pitch or adaptive blade technologies for optimal performance across a range of wind speeds.
2. Develop and implement smart control algorithms that enable real-time adjustments to turbine operation based on changing wind conditions, ensuring maximum energy extraction with integrated energy storage technologies such as batteries or flywheels. Investigate remote monitoring systems that allow real-time performance tracking and diagnostics for early detection of issues, ensuring a reduction in downtime and operational costs.
3. Investigate innovative noise reduction technologies to address concerns about the acoustic impact of small wind turbines in residential and urban settings. Explore aerodynamic modifications, materials, or structural changes to minimize turbine noise without compromising performance.
4. Address small wind turbine operation challenges in cold climates by developing technologies that prevent ice accumulation on blades and ensure reliable functioning in freezing conditions.
5. Investigate cost-effective manufacturing methods, such as advanced molding, 3D printing, or modular designs, to reduce the overall production costs of small wind turbines. Explore materials that balance cost-effectiveness with performance and durability.
Acknowledgement: None.
Funding Statement: The authors received no specific funding for this study.
Author Contributions: The authors confirm contribution to the paper as follows: Study conception and design: Dattu Ghane and Vishnu Wakchaure; data collection: Dattu Ghane and Vishnu Wakchaure; analysis and interpretation of results: Dattu Ghane and Vishnu Wakchaure; draft manuscript preparation: Dattu Ghane. All authors reviewed the results and approved the final version of the manuscript.
Availability of Data and Materials: No new data has been generated during the study, all the available data has been included within the manuscript.
Ethics Approval: Not applicable.
Conflicts of Interest: The authors declare that they have no conflicts of interest to report regarding the present study.
References
1. A. V. Satpute and E. V. Kumar, “Current scenario of wind power in India, government policies, initiatives, status and challenges,” Int. J. Energy Sect. Manag., vol. 15, no. 1, pp. 209–226, 2021. doi: 10.1108/IJESM-03-2020-0007. [Google Scholar] [CrossRef]
2. U. S. Energy Information Administration (EIA), “International-U.S. Energy Information Administration (EIA),” 2022. Accessed: Aug. 24, 2022. [Online]. Available: https://www.eia.gov/international/analysis/country/IND [Google Scholar]
3. The Economic Times, “Renewable energy: India’s renewable energy journey: Two steps forward, one step back,” 2022. Accessed: Aug. 23, 2022. [Online]. Available: https://economictimes.indiatimes.com/industry/renewables/indias-renewable-energy-journey-two-steps-forward-one-step-back/articleshow/91790588.cms [Google Scholar]
4. M. Bourhis, M. Pereira, F. Ravelet, and I. Dobrev, “Innovative design method and experimental investigation of a small-scale and very low tip-speed ratio wind turbine,” Exp. Therm. Fluid Sci., vol. 130, 2022, Art. no. 110504. doi: 10.1016/J.EXPTHERMFLUSCI.2021.110504. [Google Scholar] [CrossRef]
5. Energy Institute, “Statistical review of world energy,” Smil, 2017. Accessed: Nov. 23, 2023. [Online]. Available: https://ourworldindata.org/grapher/global-energy-substitution?time=earliest.1985 [Google Scholar]
6. S. V. Tyagi and M. K. Singhal, “A comprehensive review of sizing and uncertainty modeling methodologies for the optimal design of hybrid energy systems,” Int. J. Green Energy, vol. 1–46, 2023. doi: 10.1080/15435075.2023.2253885. [Google Scholar] [CrossRef]
7. IEA, “India energy outlook 2021–analysis,” 2022. Accessed: Aug. 24, 2022. [Online]. Available: https://www.iea.org/reports/india-energy-outlook-2021 [Google Scholar]
8. IBEF, “Renewable energy industry, solar energy companies in India,” 2022. Accessed: Aug. 24, 2022. [Online]. Available: https://www.ibef.org/industry/renewable-energy [Google Scholar]
9. T. Lu, P. Sherman, X. Chen, S. Chen, X. Lu and M. McElroy, “India’s potential for integrating solar and on- and offshore wind power into its energy system,” Nat. Commun., vol. 11, no. 1, 2020, Art. no. 4750. doi: 10.1038/s41467-020-18318-7. [Google Scholar] [PubMed] [CrossRef]
10. R. Aghamolaei and M. Fallahpour, “Strategies towards reducing carbon emission in university campuses: A comprehensive review of both global and local scales,” J. Build. Eng., 2023, Art. no. 107183. doi: 10.1016/j.jobe.2023.107183. [Google Scholar] [CrossRef]
11. I. V. Saradhi, G. G. Pandit, and V. D. Puranik, “Energy supply, demand and environmental analysis—a case study of indian energy scenario,” Int. J. Civ. Environ. Eng., vol. 1, no. 3, pp. 115–120, 2009. [Google Scholar]
12. U. Singh, M. Rizwan, H. Malik, and F. P. García Márquez, “Wind energy scenario, success and initiatives towards renewable energy in India—A review,” Energies, vol. 15, no. 6, 2022, Art. no. 2291. doi: 10.3390/EN15062291. [Google Scholar] [CrossRef]
13. J. M. K. C. Donev et al., “Micro-wind turbine,” Energy Educ., 2020. Accessed: Nov. 27, 2023. https://energyeducation.ca/encyclopedia/Micro-wind_turbine [Google Scholar]
14. Project Drawdown, “Micro wind turbines,” 2022. Accessed: Aug. 23, 2022. [Online]. Available: https://drawdown.org/solutions/micro-wind-turbines [Google Scholar]
15. M. Ahmad, A. Shahzad, and M. N. M. Qadri, “An overview of aerodynamic performance analysis of vertical axis wind turbines,” Energy Environ., vol. 34, no. 7, pp. 2815–2857, 2022. doi: 10.1177/0958305X221121281. [Google Scholar] [CrossRef]
16. R. S. Amano, “Review of wind turbine research in 21st century,” J. Energy Resour. Technol. Trans. ASME, vol. 139, no. 5, pp. 0508011–0508018, 2017. doi: 10.1115/1.4037757. [Google Scholar] [CrossRef]
17. M. Ahmad, A. Shahzad, F. Akram, and M. N. M. Qadri, “Determination of efficient configurations of vertical axis wind turbine using design of experiments,” Proc. Inst. Mech. Eng., Part A: J. Power Energy, vol. 236, no. 8, pp. 1558–1581, 2022. doi: 10.1177/09576509221095347. [Google Scholar] [CrossRef]
18. H. K. Kelele, L. Froyd, M. Kahsay, and T. Nielsen, “Characterization of aerodynamics of small wind turbine blade for enhanced performance and low cost of energy,” Energies, vol. 15, no. 21, 2022, Art. no. 8111. doi: 10.3390/en15218111. [Google Scholar] [CrossRef]
19. R. A. Kishore, T. Coudron, and S. Priya, “Small-scale wind energy portable turbine (SWEPT),” J. Wind Eng. Ind. Aerodyn., vol. 116, no. 2, pp. 21–31, 2013. doi: 10.1016/j.jweia.2013.01.010. [Google Scholar] [CrossRef]
20. H. Matsumiya, R. Ito, M. Kawakami, D. Matsushita, M. Iida and C. Arakawa, “Field operation and track tests of 1-kW small wind turbine under high wind conditions,” J. Sol. Energy Eng., vol. 132, no. 1, 2010, Art. no. 011002. doi: 10.1115/1.4000330. [Google Scholar] [CrossRef]
21. M. Kumar, P. Palanisamy, K. Sivalingam, T. C. Lim, S. Ramakrishna and H. Wei, “Strategies for enhancing the low wind speed performance of H-Darrieus wind turbine—Part 1,” Clean Technol., vol. 1, no. 10, pp. 185–204, 2019. doi: 10.3390/cleantechnol1010013. [Google Scholar] [CrossRef]
22. C. Mayer, M. E. Bechly, M. Hampsey, and D. H. Wood, “The starting behaviour of a small horizontal-axis wind turbine,” Renew. Energy, vol. 22, no. 1–3, pp. 411–417, 2001. doi: 10.1016/S0960-1481(00)00066-5. [Google Scholar] [CrossRef]
23. P. Giguere and M. S. Selig, “Low Reynolds number airfoils for small horizontal axis wind turbines,” Wind Eng., pp. 367–380, 1997. Accessed: Dec. 1, 2023. https://www.jstor.org/stable/43749658 [Google Scholar]
24. M. S. Selig and B. D. McGranahan, “Wind tunnel aerodynamic tests of six airfoils for use on small wind turbines,” J. Sol. Energy Eng., vol. 126, no. 4, pp. 986–1001, 2004. doi: 10.1115/1.1793208. [Google Scholar] [CrossRef]
25. R. K. Singh, M. R. Ahmed, M. A. Zullah, and Y. H. Lee, “Design of a low Reynolds number airfoil for small horizontal axis wind turbines,” Renew. Energy, vol. 42, no. 2–3, pp. 66–76, 2012. doi: 10.1016/j.renene.2011.09.014. [Google Scholar] [CrossRef]
26. Q. Song and W. David Lubitz, “Design and testing of a new small wind turbine blade,” J. Sol. Energy Eng., vol. 136, no. 3, 2014, Art. no. 034502. doi: 10.1115/1.4026464. [Google Scholar] [CrossRef]
27. M. Takao et al., “A straight-bladed vertical axis wind turbine with a directed guide vane row—Effect of guide vane geometry on the performance,” J. Therm. Sci., vol. 18, no. 1, pp. 54–57, 2009. doi: 10.1007/s11630-009-0054-0. [Google Scholar] [CrossRef]
28. R. C. Maydew and P. C. Klimas, “Aerodynamic performance of vertical and horizontal axis wind turbines,” J. Energy, vol. 5, no. 3, pp. 189–190, 1981. doi: 10.2514/3.48033. [Google Scholar] [CrossRef]
29. K. McLaren, S. Tullis, and S. Ziada, “Measurement of high solidity vertical axis wind turbine aerodynamic loads under high vibration response conditions,” J. Fluids Struct., vol. 32, pp. 12–26, 2012. doi: 10.1016/j.jfluidstructs.2012.01.001. [Google Scholar] [CrossRef]
30. J. J. Miau et al., “Design and test of a vertical-axis wind turbine with pitch control,” in Applied Mechanics and Materials. Switzerland: Trans. Tech. Publications Ltd., 2012, vol. 225, pp. 338–343. doi: 10.4028/www.scientific.net/AMM.225.338. [Google Scholar] [CrossRef]
31. S. Armstrong, A. Fiedler, and S. Tullis, “Flow separation on a high Reynolds number, high solidity vertical axis wind turbine with straight and canted blades and canted blades with fences,” Renew. Energy, vol. 41, no. 3, pp. 13–22, 2012. doi: 10.1016/j.renene.2011.09.002. [Google Scholar] [CrossRef]
32. A. Tummala, R. K. Velamati, D. K. Sinha, V. Indraja, and V. H. Krishna, “A review on small scale wind turbines,” Renew. Sustain. Energy Rev., vol. 56, no. 4, pp. 1351–1371, 2016. doi: 10.1016/j.rser.2015.12.027. [Google Scholar] [CrossRef]
33. S. Leloudas, G. Lygidakis, A. Eskantar, and I. Nikolos, “A robust methodology for the design optimization of diffuser augmented wind turbine shrouds,” Renew. Energy, vol. 150, pp. 722–742, 2020. doi: 10.1016/j.renene.2019.12.098. [Google Scholar] [CrossRef]
34. H. Zhu, M. Sueyoshi, C. Hu, and S. Yoshida, “A study on a floating type shrouded wind turbine: Design, modeling and analysis,” Renew. Energy, vol. 134, no. 3, pp. 1099–1113, 2019. doi: 10.1016/j.renene.2018.09.028. [Google Scholar] [CrossRef]
35. N. Siavash, G. Najafi, T. Hashjin, B. Ghobadian, and E. Mahmoodi, “An innovative variable shroud for micro wind turbines,” Renew. Energy, vol. 145, no. 1, pp. 1061–1072, 2020. doi: 10.1016/j.renene.2019.06.098. [Google Scholar] [CrossRef]
36. V. Kouloumpis, R. Sobolewski, and X. Yan, “Performance and life cycle assessment of a small scale vertical axis wind turbine,” J. Clean. Prod., vol. 247, 2020, Art. no. 119520. doi: 10.1016/j.jclepro.2019.119520. [Google Scholar] [CrossRef]
37. G. Y. Huang, Y. C. Shiah, C. J. Bai, and W. T. Chong, “Experimental study of the protuberance effect on the blade performance of a small horizontal axis wind turbine,” J. Wind Eng. Ind. Aerodyn., vol. 147, pp. 202–211, 2015. doi: 10.1016/j.jweia.2015.10.005. [Google Scholar] [CrossRef]
38. T. Sant et al., “Development and performance testing of a small, multi-bladed wind turbine,” Wind Eng., vol. 44, no. 1, pp. 20–23, 2019. doi: 10.1177/0309524X19849845. [Google Scholar] [CrossRef]
39. M. Refan and H. Hangan, “Aerodynamic performance of a small horizontal axis wind turbine,” J. Sol. Energy Eng., Trans. ASME, vol. 134, no. 2, 2012. doi: 10.1115/1.4005751. [Google Scholar] [CrossRef]
40. B. Aljafari, D. Samithas, P. Balachandran, S. Anandan, and T. S. Babu, “Performance analysis of PLA material based micro-turbines for low wind speed applications,” Polymers, vol. 14, no. 19, 2022, Art. no. 4180. doi: 10.3390/polym14194180. [Google Scholar] [PubMed] [CrossRef]
41. S. Y. Araújo de Falani, M. González, F. de Melo Barreto, J. C. Toledo, and A. L. Vitale Torkomian, “Trends in the technological development of wind energy generation,” Int. J. Technol. Manag. Sustain. Dev., vol. 19, no. 1, pp. 43–68, 2020. doi: 10.1386/tmsd_00015_1. [Google Scholar] [CrossRef]
42. M. Ramezani, D. E. Choe, K. Heydarpour, and B. Koo, “Uncertainty models for the structural design of floating offshore wind turbines: A review,” Renew Sustain. Energy Rev., vol. 185, 2023, Art. no. 113610. doi: 10.1016/j.rser.2023.113610. [Google Scholar] [CrossRef]
43. S. Younoussi and A. Ettaouil, “Numerical study of a small horizontal-axis wind turbine aerodynamics operating at low wind speed,” Fluids, vol. 8, no. 7, 2023, Art. no. 192. doi: 10.3390/fluids8070192. [Google Scholar] [CrossRef]
44. G. M. Ibrahim, K. Pope, and Y. S. Muzychka, “Effects of blade design on ice accretion for horizontal axis wind turbines,” J. Wind Eng. Ind. Aerodyn., vol. 173, no. 1, pp. 39–52, 2018. doi: 10.1016/j.jweia.2017.11.024. [Google Scholar] [CrossRef]
45. C. Sun, T. Tian, X. Zhu, O. Hua, and Z. Du, “Investigation of the near wake of a horizontal-axis wind turbine model by dynamic mode decomposition,” Energy, vol. 227, 2021, Art. no. 120418. doi: 10.1016/j.energy.2021.120418. [Google Scholar] [CrossRef]
46. Y. Nishizawa, H. Tokuyama, Y. Nakajo, and I. Ushiyama, “Yaw behavior of horizontal-axis small wind turbines in an urban area,” Wind Eng., vol. 33, no. 1, pp. 19–30, 2009. doi: 10.1260/0309-524X.33.1.19. [Google Scholar] [CrossRef]
47. S. Ladge and Y. Modarres-Sadeghi, “Supercritical and subcritical dynamic flow-induced instabilities of a small-scale wind turbine blade placed in uniform flow,” J. Fluids Struct., vol. 54, pp. 936–946, 2015. doi: 10.1016/j.jfluidstructs.2015.02.008. [Google Scholar] [CrossRef]
48. W. D. Lubitz, “Impact of ambient turbulence on performance of a small wind turbine,” Renew. Energy, vol. 61, no. 1, pp. 69–73, 2014. doi: 10.1016/j.renene.2012.08.015. [Google Scholar] [CrossRef]
49. L. C. Pagnini, M. Burlando, and M. P. Repetto, “Experimental power curve of small-size wind turbines in turbulent urban environment,” Appl. Energy., vol. 154, no. 1, pp. 112–121, 2015. doi: 10.1016/j.apenergy.2015.04.117. [Google Scholar] [CrossRef]
50. X. Shen, H. Yang, J. Chen, X. Zhu, and Z. Du, “Aerodynamic shape optimization of non-straight small wind turbine blades,” Energy Convers. Manag., vol. 119, no. 6, pp. 266–278, 2016. doi: 10.1016/j.enconman.2016.04.008. [Google Scholar] [CrossRef]
51. S. Jugsujinda, P. Jugsujinda, and T. Seetawan, “The derivation of efficiency equation of the prototype of pico wind turbine produces the electricity,” Procedia Eng., vol. 32, pp. 994–999, 2012. doi: 10.1016/j.proeng.2012.02.044. [Google Scholar] [CrossRef]
52. L. M. Al-Hadhrami, “Performance evaluation of small wind turbines for off grid applications in Saudi Arabia,” Energy Convers. Manag., vol. 81, no. 11, pp. 19–29, 2014. doi: 10.1016/j.enconman.2014.01.064. [Google Scholar] [CrossRef]
53. S. W. Hong, I. B. Lee, I. H. Seo, and K. S. Kwon, “The design and testing of a small-scale wind turbine fitted to the ventilation fan for a livestock building,” Comput. Electron. Agric., vol. 99, no. 4, pp. 65–76, 2013. doi: 10.1016/j.compag.2013.08.020. [Google Scholar] [CrossRef]
54. Y. Nishi, Y. Yamashita, and T. Inagaki, “Study on the rotor design method for a small propeller-type wind turbine,” J. Therm. Sci., vol. 25, no. 4, pp. 355–362, 2016. doi: 10.1007/s11630-016-0871-x. [Google Scholar] [CrossRef]
55. A. Eltayesh et al., “Experimental and numerical investigation of the effect of blade number on the aerodynamic performance of a small-scale horizontal axis wind turbine,” Alex. Eng. J., vol. 60, no. 4, pp. 3931–3944, 2021. doi: 10.1016/j.aej.2021.02.048. [Google Scholar] [CrossRef]
56. V. Akbari, N. Mohammad, K. Ramin, and Y. Wahiba, “Comparative study of the blade number and airfoil profile impacts on the twist/chord distribution of a small wind turbine blade,” Int. J. Energy Res., vol. 1, 2023, Art. no. 8164273. doi: 10.1155/2023/8164273. [Google Scholar] [CrossRef]
57. W. B. Lenz, A. M. Tusset, M. A. Ribeiro, and J. M. Balthazar, “Neuro fuzzy control on horizontal axis wind turbine,” Meccanica, vol. 55, no. 1, pp. 87–101, 2020. doi: 10.1007/s11012-019-01118-9. [Google Scholar] [CrossRef]
58. M. Zhao, T. Posenauer, and E. L. Tan, “Effect of yaw angle on large scale three-blade horizontal axis wind turbines,” Hydro. Sci. Mar. Eng., vol. 4, no. 1, pp. 8–15, 2022. doi: 10.30564/hsme.v4i1.4489. [Google Scholar] [CrossRef]
59. V. Sharma, “Vertical axis wind turbine,” University of Illinois at Urbana-Champaign, 1993. Accessed: Dec. 3, 2023. [Online]. Available: https://www.academia.edu/3163517/Vertical_axis_wind_turbine [Google Scholar]
60. M. Islam, D. S. K. Ting, and A. Fartaj, “Aerodynamic models for Darrieus-type straight-bladed vertical axis wind turbines,” Renew Sustain. Energy Rev., vol. 12, no. 4, pp. 1087–1109, 2008. doi: 10.1016/j.rser.2006.10.023. [Google Scholar] [CrossRef]
61. D. N. Gorelov and V. P. Krivospitsky, “Prospects for development of wind turbines with orthogonal rotor,” Thermophys. Aeromech., vol. 15, no. 1, pp. 153–157, 2008. doi: 10.1134/S0869864308010149. [Google Scholar] [CrossRef]
62. S. Eriksson, H. Bernhoff, and M. Leijon, “Evaluation of different turbine concepts for wind power,” Renew Sustain. Energy Rev., vol. 12, no. 5, pp. 1419–1434, 2008. doi: 10.1016/j.rser.2006.05.017. [Google Scholar] [CrossRef]
63. T. Brahimi and I. Paraschivoiu, “Darrieus rotor aerodynamics in turbulent wind,” J. Sol. Energy Eng., vol. 117, no. 2, pp. 128–136, 1995. doi: 10.1115/1.2870839. [Google Scholar] [CrossRef]
64. A. Rosen and H. Abramovich, “Investigation of the structural behavior of the blades of a Darrieus wind turbine,” J. Sound Vib., vol. 100, no. 4, pp. 493–509, 1985. doi: 10.1016/S0022-460X(85)80003-1. [Google Scholar] [CrossRef]
65. G. Bergeles, A. Michos, and N. Athanassiadis, “Velocity vector and turbulence in the symmetry plane of a Darrieus wind generator,” J. Wind Eng. Ind. Aerodyn., vol. 37, no. 1, pp. 87–101, 1991. doi: 10.1016/0167-6105(91)90007-J. [Google Scholar] [CrossRef]
66. M. Marini, A. Massardo, and A. Satta, “Performance of vertical axis wind turbines with different shapes,” J. Wind Eng. Ind. Aerodyn., vol. 39, no. 1–3, pp. 83–93, 1992. doi: 10.1016/0167-6105(92)90535-I. [Google Scholar] [CrossRef]
67. T. Wakui et al., “Optimum method of operating the wind turbine-generator systems matching the wind condition and wind turbine type,” in World Renewable Energy Congress VI, 2000, pp. 2348–2351. doi: 10.1016/B978-008043865-8/50509-2. [Google Scholar] [CrossRef]
68. Y. Staelens, F. Saeed, and I. Paraschivoiu, “A straight-bladed variable-pitch VAWT concept for improved power generation,” in ASME 2003 Wind Energy Symp., Reno, NV, USA, 2003, pp. 146–154. doi: 10.1115/WIND2003-524. [Google Scholar] [CrossRef]
69. L. A. Schienbein and D. J. Malcolm, “Design, performance, and economics of 50-kW and 500-kW vertical axis wind turbines,” J. Sol. Energy Eng., vol. 105, no. 1, 1983. doi: 10.1115/1.3266402. [Google Scholar] [CrossRef]
70. D. Vandenberghe and E. Dick, “A free vortex simulation method for the straight bladed vertical axis wind turbine,” J. Wind Eng. Ind. Aerodyn., vol. 26, no. 3, pp. 307–324, 1987. doi: 10.1016/0167-6105(87)90002-X. [Google Scholar] [CrossRef]
71. H. Z. Graham IV, C. Panther, M. Hubbell, J. P. Wilhelm, G. M. Angle II and J. E. Smith, “Airfoil selection for a straight bladed circulation controlled vertical axis wind turbine,” in ASME 2009 3rd Int. Conf. Energy Sustain., San Francisco, CA, USA, 2009, pp. 579–584. doi: 10.1115/ES2009-90343. [Google Scholar] [CrossRef]
72. J. P. Wilhelm et al., “Momentum analytical model of a circulation controlled vertical axis wind turbine,” in ASME 2009 3rd Int. Conf. Energy Sustain., San Francisco, CA, USA, 2009, pp. 1009–1017. doi: 10.1115/ES2009-90352. [Google Scholar] [CrossRef]
73. T. Siota et al., “Matching between straight-wing nonarticulated vertical axis wind turbine and a new wind turbine generator,” Electr Eng. Jpn., vol. 174, no. 2, pp. 26–35, 2011. doi: 10.1002/eej.21036. [Google Scholar] [CrossRef]
74. S. M. H. Karimian and A. Abdolahifar, “Performance investigation of a new Darrieus vertical axis wind turbine,” Energy, vol. 191, no. 1, 2020, Art. no. 116551. doi: 10.1016/j.energy.2019.116551. [Google Scholar] [CrossRef]
75. L. Battisti et al., “Aerodynamic measurements on a vertical axis wind turbine in a large scale wind tunnel,” J. Energy Resour. Technol. Trans. ASME, vol. 133, no. 3, 2011. doi: 10.1115/1.4004360. [Google Scholar] [CrossRef]
76. A. Ali et al., “Experimental and computational study of a micro vertical axis wind turbine,” Procedia Eng., vol. 49, pp. 254–262, 2012. doi: 10.1016/j.proeng.2012.10.135. [Google Scholar] [CrossRef]
77. A. Damak, Z. Driss, and M. S. Abid, “Experimental investigation of helical Savonius rotor with a twist of 180,” Renew. Energy, vol. 52, no. 1, pp. 136–142, 2013. doi: 10.1016/j.renene.2012.10.043. [Google Scholar] [CrossRef]
78. U. K. Saha and M. J. Rajkumar, “On the performance analysis of Savonius rotor with twisted blades,” Renew. Energy, vol. 31, no. 11, pp. 1776–1788, 2006. doi: 10.1016/j.renene.2005.08.030. [Google Scholar] [CrossRef]
79. R. E. Sheldahl, L. V. Feltz, and B. F. Blackwell, “Wind tunnel performance data for two-and three-bucket Savonius rotors,” J. Energy, vol. 2, no. 3, pp. 160–164, 1978. doi: 10.2514/3.47966. [Google Scholar] [CrossRef]
80. B. Loganathan, I. Mustary, H. Chowdhury, and F. Alam, “Effect of sizing of a Savonius type vertical axis micro wind turbine,” Energy Proc., vol. 110, no. 7, pp. 555–560, 2017. doi: 10.1016/j.egypro.2017.03.184. [Google Scholar] [CrossRef]
81. J. Yen and N. Ahmed, “Improving safety and performance of small-scale vertical axis wind turbines,” Procedia Eng., vol. 49, pp. 99–106, 2012. doi: 10.1016/j.proeng.2012.10.117. [Google Scholar] [CrossRef]
82. R. Howell, N. Qin, J. Edwards, and N. Durrani, “Wind tunnel and numerical study of a small vertical axis wind turbine,” Renew. Energy, vol. 35, no. 2, pp. 412–422, 2010. doi: 10.1016/j.renene.2009.07.025. [Google Scholar] [CrossRef]
83. C. Li, S. Zhu, Y. L. Xu, and Y. Xiao, “2.5D large eddy simulation of vertical axis wind turbine in consideration of high angle of attack flow,” Renew. Energy, vol. 51, no. 4, pp. 317–330, 2013. doi: 10.1016/j.renene.2012.09.011. [Google Scholar] [CrossRef]
84. L. A. Danao, N. Qin, and R. Howell, “A numerical study of blade thickness and camber effects on vertical axis wind turbines,” Proc Inst. Mech. Eng. A J. Power Energy, vol. 226, no. 7, pp. 867–881, 2012. doi: 10.1177/0957650912454403. [Google Scholar] [CrossRef]
85. M. R. Castelli, A. Englaro, and E. Benini, “The Darrieus wind turbine: Proposal for a new performance prediction model based on CFD,” Energy, vol. 36, no. 8, pp. 4919–4934, 2011. doi: 10.1016/j.energy.2011.05.036. [Google Scholar] [CrossRef]
86. K. M. Almohammadi, D. B. Ingham, L. Ma, and M. Pourkashanian, “Computational fluid dynamics (CFD) mesh independency techniques for a straight blade vertical axis wind turbine,” Energy, vol. 58, no. 1, pp. 483–493, 2013. doi: 10.1016/j.energy.2013.06.012. [Google Scholar] [CrossRef]
87. K. M. Almohammadi, D. B. Ingham, L. Ma, and M. Pourkashanian, “Effect of transitional turbulence modelling on a straight blade vertical axis wind turbine,” in Alternative Energies, Berlin, Heidelberg: Springer, 2013, pp. 93–112. doi: 10.1007/978-3-642-40680-5_5. [Google Scholar] [CrossRef]
88. M. H. Mohamed, “Impacts of solidity and hybrid system in small wind turbines performance,” Energy, vol. 57, no. 11, pp. 495–504, 2013. doi: 10.1016/j.energy.2013.06.004. [Google Scholar] [CrossRef]
89. M. H. Mohamed, “Performance investigation of H-rotor Darrieus turbine with new airfoil shapes,” Energy, vol. 47, no. 1, pp. 522–530, 2012. doi: 10.1016/j.energy.2012.08.044. [Google Scholar] [CrossRef]
90. A. M. Chowdhury, H. Akimoto, and Y. Hara, “Comparative CFD analysis of Vertical Axis Wind Turbine in upright and tilted configuration,” Renew. Energy, vol. 85, no. 1, pp. 327–337, 2016. doi: 10.1016/j.renene.2015.06.037. [Google Scholar] [CrossRef]
91. M. Elkhoury, T. Kiwata, and E. Aoun, “Experimental and numerical investigation of a three-dimensional vertical-axis wind turbine with variable-pitch,” J. Wind Eng. Ind. Aerodyn., vol. 139, no. 7, pp. 111–123, 2015. doi: 10.1016/j.jweia.2015.01.004. [Google Scholar] [CrossRef]
92. D. W. Wekesa, C. Wang, Y. Wei, and L. A. M. Danao, “Influence of operating conditions on unsteady wind performance of vertical axis wind turbines operating within a fluctuating free-stream: A numerical study,” J. Wind Eng. Ind. Aerodyn., vol. 135, pp. 76–89, 2014. doi: 10.1016/j.jweia.2014.10.016. [Google Scholar] [CrossRef]
93. D. W. Wekesa, C. Wang, Y. Wei, J. N. Kamau, and L. A. M. Danao, “A numerical analysis of unsteady inflow wind for site specific vertical axis wind turbine: A case study for Marsabit and Garissa in Kenya,” Renew. Energy, vol. 76, pp. 648–661, 2015. doi: 10.1016/j.renene.2014.11.074. [Google Scholar] [CrossRef]
94. P. G. Regodeseves and C. S. Morros, “Numerical study on the aerodynamics of an experimental wind turbine: Influence of nacelle and tower on the blades and near-wake,” Energy Convers. Manag., vol. 237, no. 6–7, 2021, Art. no. 114110. doi: 10.1016/j.enconman.2021.114110. [Google Scholar] [CrossRef]
95. J. V. Akwa, H. A. Vielmo, and A. P. Petry, “A review on the performance of Savonius wind turbines,” Renew. Sustain. Energy Rev., vol. 16, no. 5, pp. 3054–3064, 2012. doi: 10.1016/j.rser.2012.02.056. [Google Scholar] [CrossRef]
96. S. F. Dorel, G. A. Mihai, and D. Nicusor, “Review of specific performance parameters of vertical wind turbine rotors based on the SAVONIUS type,” Energies, vol. 14, no. 7, 2021, Art. no. 1962. doi: 10.3390/en14071962. [Google Scholar] [CrossRef]
97. L. Ferrer-Martí, A. Garwood, J. Chiroque, R. Escobar, J. Coello and M. Castro, “A community small-scale wind generation project in Peru,” Wind Eng., vol. 34, no. 3, pp. 277–288, 2010. doi: 10.1260/0309-524X.34.3.277. [Google Scholar] [CrossRef]
98. P. A. B. James and A. B. S. Bahaj, “Small-scale wind turbines,” in Wind Energy Engineering: A Handbook for Onshore and Offshore Wind Turbines, 2017, pp. 389–418. doi: 10.1016/B978-0-12-809451-8.00019-9. [Google Scholar] [CrossRef]
99. S. Oerlemans, P. Sijtsma, and B. Mendez Lopez, “Location and quantification of noise sources on a wind turbine,” J. Sound Vib., vol. 299, no. 4–5, pp. 869–883, 2007. doi: 10.1016/j.jsv.2006.07.032. [Google Scholar] [CrossRef]
100. J. L. Acosta et al., “Performance assessment of micro and small-scale wind turbines in urban areas,” IEEE Syst. J., vol. 6, no. 1, pp. 152–163, 2012. doi: 10.1109/JSYST.2011.2163025. [Google Scholar] [CrossRef]
Cite This Article
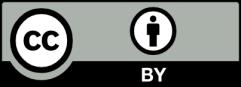
This work is licensed under a Creative Commons Attribution 4.0 International License , which permits unrestricted use, distribution, and reproduction in any medium, provided the original work is properly cited.