Open Access
ARTICLE
Reliability-Based Model for Incomplete Preventive Replacement Maintenance of Photovoltaic Power Systems
School of Electrical Engineering and Information Engineering, Lanzhou University of Technology, Lanzhou, 730050, China
* Corresponding Author: Ming Li. Email:
Energy Engineering 2024, 121(1), 125-144. https://doi.org/10.32604/ee.2023.042812
Received 13 June 2023; Accepted 26 July 2023; Issue published 27 December 2023
Abstract
At present, the operation and maintenance of photovoltaic power generation systems mainly comprise regular maintenance, breakdown maintenance, and condition-based maintenance, which is very likely to lead to over- or under-repair of equipment. Therefore, a preventive maintenance and replacement strategy for PV power generation systems based on reliability as a constraint is proposed. First, a hybrid failure function with a decreasing service age factor and an increasing failure rate factor is introduced to describe the deterioration of PV power generation equipment, and the equipment is replaced when its reliability drops to the replacement threshold in the last cycle. Then, based on the reliability as a constraint, the average maintenance cost and availability of the equipment are considered, and the non-periodic incomplete maintenance model of the PV power generation system is established to obtain the optimal number of repairs, each maintenance cycle and the replacement cycle of the PV power generation system components. Next, the inverter of a PV power plant is used as a research object. The model in this paper is compared and analyzed with the equal cycle maintenance model without considering reliability and the maintenance model without considering the equipment replacement threshold, Through model comparison, when the optimal maintenance strategy is (0.80, 4), the average maintenance cost of this paper’s model are decreased by 20.3% and 5.54% and the availability is increased by 0.2395% and 0.0337%, respectively, compared with the equal-cycle maintenance model without considering the reliability constraint and the maintenance model without considering the equipment replacement threshold. Therefore, this maintenance model can ensure the high reliability of PV plant operation while increasing the equipment availability to improve the system economy.Keywords
With the construction of a large number of photovoltaic power plants, the installed capacity of photovoltaics has increased significantly. However, because photovoltaic power plants are generally established in open areas with sufficient light and are affected by the environment, with characteristics such as large fluctuations and poor controllability, it is important to reasonably develop operation and maintenance strategies for photovoltaic power plants.
At present, in the operation and maintenance of photovoltaic power plants, the main focus is on regular maintenance, breakdown maintenance, and condition-based maintenance as appropriate [1–3]. Regular maintenance of PV power plants means that the system or components are regularly repaired at a predetermined time to prevent component failure and avoid downtime losses, but there are cases of over- or under-repair in regular maintenance [1]. Breakdown maintenance of a PV power plant refers to the method of repairing the system or component after it fails, and thus breakdown maintenance causes component or system failure downtime, which will reduce the reliability of the PV power generation system [2]. PV plant condition-based maintenance refers to the collection and evaluation of real-time information on the operation of the PV system to determine the maintenance strategy, which requires monitoring the real-time operational data of the PV system components and monitoring data with a high degree of accuracy [3]. At present, the research on the maintenance strategy of PV power plants is still in its initial stage and needs to be improved. The photovoltaic power station is scattered, the number is large, and the installed capacity is small, which makes the photovoltaic operation and maintenance difficult and high cost. To reduce operation and maintenance costs and improve service quality, the current distributed photovoltaic operation and maintenance technology development gradually tends to be intelligent. Current research at home and abroad mainly focuses on the information monitoring technology of photovoltaic power stations. Reference [4] proposed a photovoltaic array fault detection method based on particle swarm optimization wavelet neural network (PSOWNN). The output characteristic of the PV array is analyzed, the input characteristic parameters of the fault detection model are determined, and the fault detection model of the PV array based on PSOWNN is established. To better diagnose the photovoltaic array fault under the condition of maximum power point tracking, Reference [5] analyzed the temporal transient sequence data under the fault and took it as the input fault feature. The model can automatically extract the appropriate feature representation from the original electrical time series graph without using artificial data features, and the proposed method can be effectively used in photovoltaic fault diagnosis. There are many types of research on dynamic scheduling of distributed photovoltaic operation and maintenance resources [6], and many kinds of research on traditional maximum power point tracking technology are mature [7,8]. Reference [7] aimed to propose new optimization technologies to reduce how to track global maximum power point (GMPP) under partial shadows and proposes gray Wolf optimization, moth flame optimization, and moth flame optimization. Compared with the hybrid particle swarm optimization algorithm, the ability of the best algorithm to track MPPT accurately under the condition of partial shadow (PS) is verified. Reference [9] applied two IncCond MPPT techniques to the proposed single-stage three-phase differential flyback inverter (DFI). In addition, the negative sequence harmonic compensation (NSHC) of three-phase DFI is also analyzed. The voltage boost characteristics of MPPT and DC-AC inverters of PV systems are effectively provided. In addition, the average efficiency of the traditional MPPT technology and the improved IncCond MPPT technology is also verified by computer-based simulation. The main function of the newly proposed computer program in reference [10] is to determine the optimal ratio of each component of a hybrid energy system to produce the lowest KWH price and the best probability of load loss with the highest reliability. Using the actual data of the Saudi site together with the computer program has proved its feasibility and superiority, and many valuable results can be extracted from the computer program, which can help researchers and decision-makers. However, at present, there are few maintenance studies on various components of photovoltaic power generation systems, and it is easy to cause problems such as over-repair or under-repair and poor reliability. References [11,12] have proposed that the changing trend of the failure rate before and after equipment maintenance satisfies the law and characteristics of increasing equivalent service age and failure rate of the equipment, and thus provides a theoretical basis for establishing a single-equipment preventive maintenance model. Reference [13] recursively derived the relationship between the evolution of the equipment failure rate and revealed the dynamic law between the equipment failure rate and preventive maintenance. A preventive maintenance model centered on equipment reliability was developed using the mixed failure rate evolution rule of equipment [14]. A Markovian state maintenance model was developed with reliability as a constraint and verified to improve equipment availability [15]. Reference [16] segmented the equipment degradation process and developed a phased isocyclic maintenance model with the lowest average maintenance cost rate. A three-stage equal-cycle maintenance model with reliability as a constraint was developed to derive the optimal number of repairs and maintenance cycles for the equipment [17]. A phased sequential maintenance model was developed using a hybrid failure rate function to describe the deterioration process of the equipment and segmentation [18]. By comparing the effect of different numbers of failed component strings on the maintenance cost, it was demonstrated that the maintenance cost is proportional to the number of failed component strings [19]. A PV intelligent O&M model with the lowest O&M cost as the optimization objective function was established and solved by the particle swarm algorithm [20]. Reference [21] analyzed the relationship between maintenance cost and maintenance cycle and concluded that the shorter the maintenance cycle, the higher the cost, and the longer the maintenance cycle, the lower the cost. A preventive maintenance strategy for PV modules in PV power generation systems was proposed to determine the optimal maintenance cycle and the number of PV panels to be replaced with the minimum overall operating cost [22]. One study in reference [23] considered the method for determining the optimal O&M cycle for distributed PV plants under different scenarios. Currently, studies on the development of maintenance strategies with equipment reliability as a constraint have achieved some success [24–27]. In references [28,29], condition prediction is performed using the collected operational data, and then the maintenance interval of the equipment is determined. Among the studies on equipment for preventive replacement, the main focus is on the direct replacement of the equipment when it fails; in references [30,31], the equipment is replaced when its reliability drops to the preventive maintenance threshold in the last operating cycle.
The maintenance strategies determined by the above research methods can ensure reliability and reduce the maintenance cost of the equipment, but they fail to make full use value of the equipment and ignore the availability of equipment. To improve the highly reliable and safe operation of the PV power generation system while giving full play to the use value of PV power generation equipment, in this paper, we propose a preventive maintenance and replacement strategy for PV power generation systems based on reliability as a constraint. In the last pre-repair cycle, the equipment is replaced only when its reliability drops to the replacement threshold. With the reliability of the equipment as the constraint, the dynamic maintenance cost and availability of the equipment are considered, and an off-cycle incomplete replacement maintenance model of the PV power generation system is established to calculate the optimal number of repairs, each maintenance cycle, and the replacement cycles of the components. Based on the simulation analysis and model comparison, it was verified that the model can save maintenance costs as well as improve equipment availability under the premise of ensuring high reliability, which provides a certain theoretical basis for the preventive maintenance of PV power plants.
The remainder of this paper is structured as follows. Section 1 describes the structure of a photovoltaic power plant and description of maintenance strategies and assumptions, Section 2 the incomplete maintenance model is established and analyzed, Section 3 takes the inverter of photovoltaic power generation system as an example to verify, Section 4 concludes that this paper proposes a preventive maintenance and replacement strategy for photovoltaic power generation systems based on reliability as a constraint, and conclusions can be drawn from the arithmetic analysis.
2 Description of Maintenance Strategies and Assumptions
2.1 Incomplete Preventive Maintenance Strategy
The structure of a photovoltaic power plant is shown in Fig. 1. Multiple PV modules are connected in series and parallel to form a PV array A. They are connected in series with DC sink box C and inverter I to form a power unit, and multiple units are connected to the system through a grid connection.
Figure 1: Structure diagram of a photovoltaic power plant
To maintain the highly reliable and continuous operation of the PV power system, this paper uses the reliability of the equipment as a constraint to develop a maintenance strategy for the equipment, which is determined by replacement thresholds to decide when to replace the PV plant components. As shown in Fig. 2, during the service life of equipment, as the life cycle continues to extend, the equipment is bound to age, and wear severely, the failure rate increases, and the reliability of the equipment used is greatly reduced. In the first n−1 maintenance cycle, if the reliability of the components drops to Rp, the components are subject to incomplete preventive maintenance, and the reliability of the equipment becomes Rn(t) after the first n−1maintenance. In the last operation cycle when the reliability of the components drops to Rc, only then are the components subject to replacement maintenance, which also effectively maintains the use value of the equipment itself. After performing the replacement maintenance, the components are in a new condition and the reliability is restored to 1 again.
Figure 2: Imperfect maintenance strategy diagram
(1) The failure law of each component of the PV power system obeys the two-parameter Weibull distribution.
(2) In the minor repair state, the failure rate of the equipment before and after the repair does not change, and the minor repair time is constant.
(3) During the preventive maintenance interval, once the system fails, it needs to be repaired immediately. After the repair is completed, it only enables the system to partially recover its function, and although the failure rate is reduced to some extent, it will grow at a faster rate.
(4) When a failed component cannot be repaired, it will be replaced to complete the repair.
(5) After replacement and repair, the parts are brand new, and the reliability is 1.
3 Preventive Maintenance Interval Optimization Model
3.1 Failure Rate Evolution Rules
The failure law of PV power generation equipment obeys the Weibull distribution. Then, its failure rate expression is:
λ(t)=βγ(tγ)β−1(1)
where γ is the scale parameter and β is the shape parameter.
Photovoltaic power plants are built in open areas with sufficient light, making them subject to additional external influencing factors and complex working conditions. During operation, the components experience wear and aging, increasing the failure rate of PV plant components and decreasing their service life. Therefore, this model uses the decreasing service age factor and the increasing failure rate factor to describe the change in the PV plant component failure rate after incomplete preventive maintenance. The failure rate of a component after the first i repair is given by [32]:
λi(t)=bi−1λi−1(t+ai−1Ti−1)(2)
where λi(t) and λi−1(t+ai−1Ti−1) are the failure rate distribution functions for the i and i−1 cycles, respectively; bi−1 is the failure rate increment factor; and ai−1 is the service age decrement factor.
From Eqs. (1) and (2), it can be derived that the mixed failure rate function of the equipment during the ith incomplete preventive maintenance interval Ti is:
λ1(t)=λ(t)λ2(t)=b1λ1(t+a1T1)λ3(t)=b2λ2(t+a2T2)=b1b2λ(t+a1T1+a2T2)λi(t)=(i−1∏k=1bk)λ(t+i−1∑k=1akTk)(3)
To ensure the highly reliable and safe operation of PV power plants, when the reliability of the components decreases while reaching the set threshold value of incomplete preventive maintenance, incomplete maintenance of the components is needed, and thus:
exp[−∫T10λ1(t)dt]=exp[−∫T20λ2(t)dt]=…=exp[−∫Ti0λi(t)dt]=Rp(4)
Eq. (4) can be transformed into
∫T10λ1(t)dt=∫T20λ2(t)dt=…=∫Ti0λi(t)dt=−lnRp(5)
From Eq. (5), it is known that the probability of failure of components is −lnRp, and Eqs. (3) and (5) can be used to deduce that the interval of the i repair is:
Ti=β√(i−1∑k=1akTk)β−lnRp×γβ∏i−1k=1bk−i−1∑k=1akTk(6)
The reliability of the system after the i−1th and ith incomplete repairs can be expressed as:
Ri(t)=exp[−∫Ti0λi(t)dt](7)
For the reliability of the components, after n−1 incomplete preventive maintenance, a certain degree of improvement is obtained. With the frequent maintenance of the components, the failure rate of the system increases, and the reliability Rn(t) begins to decrease at a faster rate to Rc. At this time, it cannot meet the working performance of the system, and thus the components need to be replaced.
Rn(t)=exp[−∫Tn0λn(t)dt]=Rc(8)
where Tn is the first n operation cycle of the part. According to Eqs. (3) and (8), the expression of Tn is:
Tn=β√(n−1∑k=1akTk)β−lnRc×γβ∏n−1k=1bk−n−1∑k=1akTk(9)
To optimize the economic benefits of maintenance, it is necessary to consider the costs of carrying out maintenance of the equipment while ensuring high operational reliability. These comprise the cost of minor repairs during the maintenance period Cm, the cost of incomplete repairs Cp, the cost of replacement Cf, and the loss due to downtime Closs.
3.3.1 Sudden Failure Minor Repair Costs
Each component in the PV power system will age with the operating time, and sudden failures will occur in actual operation. Minor repairs to the components will be performed to restore the normal operation of the system, assuming that the cost of a single minor repair of the component is Cm, the minor repair time is tm, and the minimum maintenance cost for the whole cycle is:
TCm=Cm(n−1∑i=1∫Ti0λi(t)dt+∫Tn0λn(t)dt)(10)
The total minor repair time for the entire cycle is:
Tm=tm(n−1∑i=1∫Ti0λi(t)dt+∫Tn0λn(t)dt)(11)
3.3.2 Incomplete Preventive Maintenance Costs
As the service life of the equipment increases and the equipment undergoes frequent maintenance, the cost of incomplete maintenance will gradually increase, and the cost of incomplete maintenance in the first i can be expressed as:
Cpi=Cg+iCv(12)
where Cg is the fixed cost of incomplete repairs and Cv is the variable cost.
Then, the cost of incomplete preventive maintenance of the equipment throughout the maintenance cycle can be expressed as:
TCP=n−1∑i=1(Cg+iCv)(13)
The total time for incomplete preventive maintenance of the equipment throughout the maintenance cycle is:
TP=(n−1)τ(14)
where τ is the length of time it takes to perform an incomplete repair.
3.3.3 Replacement Cost of Equipment
The cost of a replacement unit is Cf, and the time required is Tf.
From Eq. (11) for the minor repair time, Eq. (14) for the incomplete preventive maintenance time, and the equipment replacement time Tf, the total maintenance time of the equipment can be derived as:
Tall=tm(n−1∑i=1∫Ti0λi(t)dt+∫Tn0λn(t)dt)+(n−1)τ+Tf(15)
Then, the total downtime loss of the equipment is:
TCloss=Cd(Tm+Tp+Tf)=Cd[(n−1)τ+Tf]+Cd[tm(n−1∑i=1∫Ti0λi(t)dt+∫Tn0λn(t)dt)](16)
The total maintenance cost of the equipment is:
CT=TCm+TCp+TCloss+Cf(17)
The entire life cycle of the component, including normal operation and downtime for maintenance, is expressed as follows:
T=n−1∑i=1Ti+Tn+Tall(18)
3.4 Component Availability Model
Availability measures the availability of a component and refers to the property of a component that is available at any given time. In the field of reliability research, availability is measured in various ways depending on the environment in which it is used. Among them, the achievable availability takes into account the working time and the repair time and is generally used for the trade-off of preventive maintenance programs. The expression of availability A is:
A=MUTMUT+MDT(19)
where MUT is the normal operating time and MDT is the downtime for the maintenance. Eqs. (6) and (15) can be derived from the availability expression when not considering the equipment replacement threshold Rc, as shown in Eq. (20).
A(T)=n∑i=1Tin∑i=1Ti+Tm+Tp+Tf=n∑i=1Tin∑i=1Ti+tm(−lnRP)n+(n−1)τ+Tf(20)
From Eqs. (6), (9) and (15), an expression for the availability when considering the equipment replacement threshold Rc can be derived, as shown in Eq. (21).
A(T)=n−1∑i=1Ti+Tnn−1∑i=1Ti+Tn+Tm+Tp+Tf=n−1∑i=1Ti+Tnn−1∑i=1Ti+Tn+tm[(−lnRP)(n−1)−lnRC]+(n−1)τ+Tf(21)
3.5 Dynamic Maintenance Cost Model
Taking the reliability of the equipment as a constraint, the equipment operates with high reliability while saving maintenance cost, and thus Eqs. (5), (8), (17) and (18) can be combined to minimize the average maintenance cost of the components as an objective function, through which the elastic maintenance cycle of the equipment Ti and the optimal number of pre-repairs n are determined. If the replacement threshold of the equipment Rc is not considered, the average maintenance cost is as shown in Eq. (22).
Ccost(n,Ti)=(Cm+Cdtm)(−lnRp)n+n−1∑i=1(Cg+iCv)+Cf+TClossn∑i=1Ti+tm(−lnRp)n+(n−1)τ+Tf(22)
When considering the replacement threshold of the equipment Rc, the average maintenance cost is shown in Eq. (23).
Ccost(n,Ti)=(Cm+Cdtm)[(−lnRp)(n−1)−ln(Rc)]+n−1∑i=1(Cg+iCv)+Cf+TClossn−1∑i=1Ti+Tn+tm[(−lnRp)(n−1)−ln(Rc)]+(n−1)τ+Tf(23)
where n is the optimal number of incomplete preventive maintenance instances and Ti is the maintenance interval. n and Ti should satisfy the following constraints:
s.t.
Ri(t)≥Rp,i=1,2,…,n−1(24)
Rn(t)≥Rc(25)
n−1∑i=1Ti+Tn+tm(n−1∑i=1∫Ti0λi(t)dt+∫Tn0λn(t)dt)+(n−1)τ+Tf≤TL(26)
tm(−lnRp)+τ≤Ti(27)
tm(−lnRP)+Tf≤Tn(28)
4 Photovoltaic Power Generation System Inverter Is Verified by an Example
4.1 Background of the Algorithm and Maintenance Optimization
4.1.1 Background of the Algorithm
In this paper, the inverter of a 10 MW PV plant is used as the research object [33]. To verify the feasibility and validity of the maintenance model, assume the failure rate parameters of the inverter β=2, γ=2000; the time to perform minor repairs on its tm=2d, the time to perform incomplete repairs τ=3d; and the time to replace it Tf=10d. The repair costs of the inverter of the PV power plant are shown in Table 1.
For photovoltaic power generation equipment, the reliability interval is set to Rp∈[0.80,0.95] for incomplete maintenance and R=0.70 for the lowest reliability that can operate safely. ai and bi are obtained, and it is necessary to statistically fit the past maintenance data of the equipment, which is not easy to derive in this paper.
{ai=i5i+9bi=13i+112i+1(29)
4.1.2 Selection of Replacement Thresholds
The replacement threshold determines the length of the last operating cycle and whether the value of the component can be fully utilized. Therefore, it is important to reasonably choose the replacement threshold to ensure the safe and stable operation of the system while reducing maintenance costs. When the incomplete maintenance threshold is set to Rp∈[0.80,0.95] and the replacement threshold is set to Rc∈[0.70,0.75], the average maintenance costs and the change in availability of the equipment under different replacement thresholds were determined by simulation analysis and the enumeration method, as shown in Tables 2 and 3, respectively. The variation trend of average maintenance cost and availability with replacement threshold selection is shown in Figs. 3 and 4.
Figure 3: The impact of changes in Rc on the average maintenance costs when Rp is 0.80 and 0.90
Figure 4: The impact of changes in Rc on the availability when Rp is 0.80 and 0.90
According to Tables 2–3 and Figs. 3–4, the average maintenance cost tends to decrease and then increase with the number of repairs when the replacement threshold is the same, and the availability of the equipment tends to increase and then decrease with the number of repairs. Therefore, for the same replacement threshold, the optimal number of pre-repairs can be selected. When both the incomplete repair reliability threshold and the number of repairs are the same, the average repair cost increases with the selected replacement threshold and the availability decreases with the selected replacement threshold. When the replacement threshold Rc is equal to the preventive maintenance threshold Rp, the average repair cost is the largest and the availability is the smallest; therefore, the replacement threshold Rc should be selected to be less than the incomplete maintenance threshold Rp. When Rp=0.80, the equipment is repaired 4 times, Rc increases from 0.70 to 0.75, the average repair cost rises from 48.63 yuan/day to 49.89 yuan/day, and the availability decreases from 99.379% to 99.363%; when Rp=0.90, the equipment is repaired 3 times, Rc increases from 0.70 to 0.75, the average repair cost rises from 58.70 yuan/day to 61.32 yuan/day, and the availability decreases from 99.239% to 99.209%.
The above analysis indicates that the average maintenance cost of the equipment is the smallest at a replacement threshold of 0.70, with the highest availability and longest running time. Therefore, the replacement threshold was chosen as Rc=0.70 in the model in this paper.
4.1.3 Calculus Optimization Analysis
For the inverter, the usage time frame was set to TL=3600⋅d, the parameters in Table 1 were substituted into the model of this paper, and the number of preventive maintenance n was set to 6 for simulation optimization. The average maintenance cost of the device Ccost(Rp,n) and the availability A(Rp,n) under the partial maintenance strategy (Rp,n) were obtained as shown in Tables 4 and 5. The trend of average maintenance cost and availability under different maintenance strategies is shown in Figs. 5 and 6.
Figure 5: The average repair costs Ccost(Rp,n) under the partial repair strategy (Rp,n)
Figure 6: Availability A(Rp,n) under the partial repair strategy (Rp,n)
According to Tables 4–5 and Figs. 5–6, the average maintenance cost of the equipment decreases and then increases as the number of pre-repairs increases, and the availability increases and then decreases; therefore, an optimal number of pre-repairs can be determined for the equipment to minimize the average maintenance cost and maximize the availability at any reliability threshold. For the same maintenance times, the average maintenance cost increases with the increase of the preventive maintenance threshold, and the availability decreases with the increase of the preventive maintenance threshold. Therefore, the smaller the preventive threshold is, the more economical it is when the normal operation of the equipment is met. Some of the best repair strategies are (0.80, 4), (0.85, 4), (0.90, 3), and (0.95, 2), such as when Rp=0.80 and the equipment is repaired 4 times, with the average repair cost of a minimum of 48.63 yuan/day and the maximum availability of 99.379%. That is, the first 3 times when the reliability of PV power generation equipment drops to Rp, it is repaired, and when the reliability of the 4th period, i.e., the last operating cycle of the equipment, drops to Rc, it is directly replaced. When the number of repairs is the same, the average repair cost gradually increases with the increase of the preventive maintenance threshold Rp, and the availability gradually decreases with the increase of the preventive maintenance threshold Rp.
To verify the economy and feasibility of this model, the simulation calculated the elastic maintenance interval, replacement interval, average maintenance cost, and availability of this component when the optimal maintenance strategy was (0.80, 4) and (0.90, 3), as shown in Table 6. From Table 6, it can be seen that the failure rate of the equipment is affected by the operation time and the service age appears to be decreasing. To increase the reliability of the PV power generation system operation, the maintenance interval decreases with the operation time, the maintenance interval is gradually shortened, the flexible maintenance interval of the system gradually decreases with the increase of the preventive maintenance threshold Rp, the replacement cycle also decreases, the availability decreases, and the average maintenance cost gradually increases.
4.2.1 Comparison between the Model in This Paper and the Equal-Cycle Maintenance Model without Considering Reliability
After simulation, the optimization results of the isocyclic maintenance model without considering the reliability at the optimal maintenance strategy (Rp,n) of (0.80, 4) are shown in Table 7.
Comparison between Tables 6 and 7 shows that when the number of component pre-repairs is the same and the optimal maintenance strategy is (0.80, 4), the replacement cycle of this model is 11.72 days less than that of the equal-cycle maintenance model without reliability consideration, but the average maintenance cost of this model is 20.3% less than that of the equal-cycle maintenance model without reliability consideration. The reason may be that the model in this paper keeps the equipment operating with high reliability by gradually shortening the flexible maintenance cycle, which results in low system failure frequency, low maintenance frequency, and low maintenance cost; however, when the equipment operates without reliability constraints, its operating cycle increases, and at the same time, the equipment may operate with low reliability, which may easily lead to component wear and tear or cause system failure and thus cause the maintenance cost to increase.
4.2.2 Comparison between the Model in This Paper and the Maintenance Model without Considering the Replacement Threshold Rc
If the component replacement threshold Rc is not considered, the component is replaced when its reliability drops to Rp in the last operating cycle. The optimization results were obtained by simulation without considering the replacement threshold Rc when the optimal maintenance strategy of the device (Rp,n) was (0.80, 4) and (0.90, 3), as shown in Table 8.
Comparison between Tables 6 and 8 indicates that when the equipment is under a certain threshold of incomplete maintenance and the number of maintenance instances is the same, the proposed model in this paper has a long operation period, lower average maintenance cost, and higher equipment availability than the maintenance model without considering the threshold of equipment replacement. When the optimal maintenance strategy of the equipment was (0.80, 4) and (0.90, 3), the model in this paper decreased the average maintenance cost by 5.54% and 25.12%, respectively, extended its service life by 215.4 days and 501.2 days, respectively, and increased the availability by 0.0337% and 0.1893%, respectively. Notably, the maintenance model developed in this paper can effectively reduce the maintenance cost while maintaining the high reliability of the PV plant and can make fuller use of the value of the components.
4.3 For Parameter Sensitivity Analysis
By analyzing the data in Table 9, it can be concluded that with the increase in component failure rate increasing factor bi, the number of preventive maintenance should be reduced and the maintenance cycle and parts replacement cycle should be shortened to ensure the high and reliable operation of the equipment. As the operating cycle of the equipment is gradually shortened, the huge replacement cost is spread out every day to increase the average maintenance cost.
From the analysis of Table 10, it can be seen that with the increase of service age decline factor ai, the non-equal maintenance cycle decreases. Therefore, the number of optimal maintenance is gradually decreasing, the replacement cycle is shortened, and the average maintenance cost is rising.
As can be seen from Table 11 the impact of maintenance cost parameters on maintenance strategies is as follows:
1) Minor repair cost Cm
With the increase of Cm, the optimal maintenance frequency decreases gradually, while the average maintenance cost increases. When the minimum maintenance cost is small, the reliability of the equipment can be maintained by frequent maintenance of the parts, so the number of maintenance is increased; When the cost of minimal repairs is higher, the maintenance activity is less worthwhile, as far as possible to replace parts after several repairs.
2) Downtime loss cost Cd
With the increase of Cd reduced. When the Cd is 500 yuan, the preventive maintenance is replaced after 3 times, and when the Cd is 50,000 yuan, the preventive maintenance is replaced after 2 times. As the Cd increases, so does the average maintenance cost.
3) Replacement cost Cf
Under the assumption of Cp<Cf, with the increase of Cf number n preventive maintenance and average cost also increase. When Cf is 2800 yuan, can be replaced after 2 times, because replacement small, are similar, you use to improve reliability system ensure operation system; 280,000 much greater than cost, so that 7 times. this shows equipment is more expensive, higher, but necessary.
4) Preventive maintenance cost Cp
The cost of preventive maintenance is increased by fixed maintenance costs and variable costs with the increase in maintenance times. Now, Cg and Cv are reduced and expanded by ten times at the same time, and the impact on maintenance strategy is obtained. With the increase of Cp, the optimal maintenance times decreased and the average maintenance cost increased. When Cp increases to a certain extent and exceeds the replacement cost, the significance of preventive maintenance is no longer important, and the equipment is replaced directly to ensure the highly reliable operation of the system.
This paper proposes a preventive maintenance and replacement strategy for photovoltaic power generation systems based on reliability as a constraint, establishes and optimizes the preventive maintenance interval of photovoltaic power generation equipment, and the following conclusions can be drawn from the arithmetic analysis:
1. By introducing the service age regression factor and failure rate increment factor to describe the degradation process of PV power generation equipment reliability and establishing a non-periodic incomplete maintenance model with the average maintenance cost of equipment and equipment availability as the objective function, the flexible maintenance cycle, the optimal number of pre-repairs and the replacement cycle of PV power generation equipment can be derived, which can effectively avoid over-repair or under-repair of equipment.
2. The model comparison shows that at the optimal maintenance strategy of (0.80, 4), the average maintenance cost of this paper’s model is decreased by 20.3% and 5.54% and the availability is increased by 0.2395% and 0.0337%, respectively, compared with the equal-cycle maintenance model without considering the reliability constraint and the maintenance model without considering the equipment replacement threshold. Therefore, this maintenance model can ensure the high reliability of PV plant operation while increasing the equipment availability to improve the system economy.
In this paper, the correlation between the components of the PV power system was not considered, and the extension to a multi-component opportunity maintenance model will be developed in the future.
Acknowledgement: None.
Funding Statement: This research was supported by the National Natural Science Foundation of China (Nos. 51767017 and 51867015), the Basic Research and Innovation Group Project of Gansu (No. 18JR3RA133), and the Natural Science Foundation of Gansu (No. 21JR7RA258).
Author Contributions: The authors confirm their contribution to the paper as follows: study conception and design: Wei Chen, Ming Li. data collection: Ming Li, Tingting Pei. Analysis and interpretation of results: Wei Chen, Ming Li, Cunyu Sun, Huan Lei. Draft manuscript preparation: Wei Chen, Ming Li, Tingting Pei. All authors reviewed the results and approved the final version of the manuscript.
Availability of Data and Materials: Data supporting this study are included within the article.
Conflicts of Interest: The authors declare that they have no conflicts of interest to report regarding the present study.
References
1. Wang, Z. H., Xu, Z. G., Liu, B., Zhang, Y., Yang, Q. M. (2022). A hybrid cleaning scheduling framework for operations and maintenance of photovoltaic systems. IEEE Transactions on Systems, Man, and Cybernetics, Systems, 52(9), 5925–5936. [Google Scholar]
2. Zhu, X. R., Liu, Y. W. (2020). Maintenance strategy for photovoltaic power plants based on component-system hierarchical optimization. Power System Automation, 44(8), 92–99. [Google Scholar]
3. Qi, X. J., Zheng, J. Y., He, W. G., Yin, D. Y. (2020). Multi-objective maintenance strategy optimization of distributed photovoltaic plants. 2020 IEEE 1st China International Youth Conference on Electrical Engineering (CIYCEE), pp. 1–6. Wuhan, China. [Google Scholar]
4. Jing, P. H., Han, C. Y., Ai, Y. L., Liu, Q. F., Ding, J. Y. (2021). Fault detection of photovoltaic array based on particle swarm optimization wavelet neural network. Engineering Journal of Wuhan University, 54(9), 860–865 (In Chinese). [Google Scholar]
5. Lu, X. Y., Lin, P. J., Cheng, S. Y., Lin, Y. H., Chen, Z. C. et al. (2019). Fault diagnosis for photovoltaic array based on convolutional neural network and electrical time series graph. Energy Conversion and Management, 196, 950–965. [Google Scholar]
6. Gao, P., Su, Y. H., Zuo, Y., Tao, F. (2022). Dynamic scheduling method of distributed photovoltaic operation and maintenance resources based on reinforcement learning. Computer Integrated Manufacturing Systems, 28(2), 552–563. [Google Scholar]
7. Gosumbonggot, J., Fujita, G. (2019). Partial shading detection and global maximum power point tracking algorithm for photovoltaic with the variation of irradiation and temperature. Energies, 12(2), 202. [Google Scholar]
8. Ning, P. G., Zhang, Q. F., Feng, D. R., Ding, X. L., Xia, X. G. et al. (2021). An optimized photovoltaic global maximum power point tracking method. Power System Protection and Control, 49(22), 152–160. [Google Scholar]
9. Ali, A. I. M., Alaas, Z. M., Sayed, M. A., Almalaq, A., Farah, A. et al. (2022). An efficient MPPT technique-based single-stage incremental conductance for integrated PV systems considering flyback central-type PV inverter. Sustainability, 14(19), 12105. [Google Scholar]
10. Eltamaly, A. M., Mohamed, M. A. (2014). A novel design and optimization software for autonomous PV/wind/battery hybrid power systems. Mathematical Problems in Engineering, 2014, 1–16. [Google Scholar]
11. Malik, M. (1979). Reliable preventive maintenance policy. AIIE Transactions, 11(3), 221–228. [Google Scholar]
12. Nakagawa, T. (1988). Sequential imperfect preventive maintenance policies. IEEE Transactions on Reliability, 37(3), 295–298. [Google Scholar]
13. Han, B. J., Fan, X. M., Ma, D. Z. (2003). Optimization of preventive maintenance strategy based on reliability constraints. Journal of Mechanical Engineering, (6), 102–105. [Google Scholar]
14. Zhou, X. J., Xi, L. F., Li, J. (2005). A reliability-based sequential preventive maintenance model for equipment. Journal of Shanghai Jiaotong University, 39(12), 2044–2047 (In Chinese). [Google Scholar]
15. Ye, Y. B., Liu, H. J., Huang, T. G., Zhao, Z. G. (2021). Research on the reliability analysis method of condition-based maintenance of relay protection equipment in substation. Power System Protection and Control, 49(10), 170–177. [Google Scholar]
16. Deng, C., Duan, C. Q., Wu, J. (2016). Economic optimization model of phased sequential maintenance based on equipment reliability. Computer Integrated Manufacturing Systems, 22(2), 568–575. [Google Scholar]
17. Xi, Q. C., Cao, J. P., Chen, G. M., Chang, L. L., Xiong, Q. et al. (2017). Research on a phased periodic preventive maintenance model based on reliability constraint. Journal of Military Engineering, 38(11), 2251–2258. [Google Scholar]
18. Wu, Y. S., Liu, Q. M., Ye, C. H. M. (2022). Optimization study of equipment phased sequential maintenance decision based on hybrid failure rate. Industrial Engineering, 25(3), 151–156. [Google Scholar]
19. Zhao, H. S., Zhang, X. K., Guo, W. (2014). Optimized maintenance strategy with imperfect repair for the gearbox of a wind turbine. Power System Protection and Control, 42(10), 15–22. [Google Scholar]
20. Huang, C. C. (2017). Intelligent maintenance scheduling system for maximum performance of the solar-energy-generating system. Sensors and Materials, 29(11), 1579–1588. [Google Scholar]
21. Perdue, M., Gottschalg, R. (2015). Energy yields of the small grid-connected photovoltaic system: Effects of component reliability and maintenance. IET Renewable Power Generation, 9(5), 432–437. [Google Scholar]
22. Baklouti, A., Mifdal, L., Dellagi, S., Chelbi, A. (2020). An optimal preventive maintenance policy for a solar photovoltaic system. Sustainability, 12(10), 4266–4279. [Google Scholar]
23. Yin, D. Y., Mei, F., Zheng, J. Y., He, W. G., Qi, X. J. (2022). Optimal operation and maintenance cycle determination method for distributed photovoltaic systems. Power Automation Equipment, 42(5), 135–141. [Google Scholar]
24. Zhang, Y. P., Yang, K. X., Shi, L. (2018). An economic optimization model for incomplete preventive maintenance under reliability constraints. Computer Integrated Manufacturing Systems, 24(12), 3019–3026. [Google Scholar]
25. Gan, J., Zeng, J. C., Zhang, X. H. (2016). A maintenance decision model considering performance reliability constraints. Computer Integrated Manufacturing Systems, 22(4), 1079–1087. [Google Scholar]
26. Li, J. H., Xu, J. S., Ren, L. N. (2022). Incomplete preventive replacement maintenance model under reliability constraints. Journal of Solar Energy, 43(4), 446–452. [Google Scholar]
27. Robert, A., Neal, D., Robert, J. (2015). Equipment failure characteristics & RCM for optimizing maintenance cost. IEEE Transactions on Industry Applications, 52(2), 1257–1264. [Google Scholar]
28. Verbert, K., de Schutter, B., Babuska, R. (2017). Timely condition-based maintenance planning for multi-component systems. Reliability Engineering & System Safety, 159(10), 310–321. [Google Scholar]
29. Nguyen, K. A., Do, P., Grall, A. (2014). Condition-based maintenance for multi-component systems using importance measure and predictive information. International Journal of Systems Science Operations & Logistics, 1(4), 228–245. [Google Scholar]
30. Hu, J. W., Jiang, Z. H., Liao, H. T. (2017). Preventive maintenance of a single machine system working under piecewise constant operating condition. Reliability Engineering & System Safety, 168(12), 105–115. [Google Scholar]
31. Lin, Z. L., Huang, Y. S., Fang, C. C. (2015). Non-periodic preventive maintenance with reliability thresholds for complex repairable systems. Reliability Engineering & System Safety, 136(2), 145–156. [Google Scholar]
32. Yang, C. J., Tong, S., Sun, C. S., Song, Z. H. (2008). A hybrid preventive maintenance model based on reliability constraints. Journal of Zhejiang University (Engineering Edition), 42(8), 1376–1379 (In Chinese). [Google Scholar]
33. Chen, W., Li, X. B., Ji, Q. C., Pei, X. P., Wang, Z. F. et al. (2022). A maintenance strategy for photovoltaic power generation system based on association set and availability. Power System Protection and Control, 50(14), 94–104. [Google Scholar]
Cite This Article
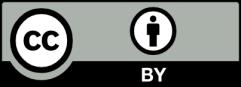
This work is licensed under a Creative Commons Attribution 4.0 International License , which permits unrestricted use, distribution, and reproduction in any medium, provided the original work is properly cited.