Open Access
ARTICLE
Evaluation of Process and Economic Feasibility of Implementing a Topping Cycle Cogeneration
Department of Industrial & Management Systems Engineering, West Virginia University, Morgantown, 26506, USA
* Corresponding Author: Unique Karki. Email:
Energy Engineering 2023, 120(2), 345-365. https://doi.org/10.32604/ee.2023.025600
Received 21 July 2022; Accepted 09 October 2022; Issue published 29 November 2022
Abstract
Industrial applications that require steam for their end-use generally utilize steam boilers that are typically oversized, citing operations flexibility. Similarly, gas turbine-based power plants corroborate a gas turbine system that may eventually relieve the usable exhaust into the atmosphere. This study explores the economic and technical feasibility of a topping cycle combined heat and power (CHP) system. It does so by leveraging a partially loaded boiler or gas turbine by increasing its unused load to generate steam and heat for subsequent usage. To this end, a decision support tool (COGENTEC) was developed, which emulates a given facility’s boiler or gas-turbine system, and its operational parameters with the application of steam turbines. The tool provides necessary insights into the most appropriate parameters that enable a CHP system to be technically and economically advantageous. Based on input variables such as boiler-rated capacity, steam pressure, steam temperature, and existing boiler load, among others, COGENTEC designs a topping cycle CHP system to inform a user whether this system is feasible in their facility or not. If applicable, the tool assists the user to realize the point of break-even (fuel cost incurred and cost savings) at the desired steam flow rate. It also conducts sensitivity analyses between energy usage, cost savings, and payback on the investment of the operating parameters to understand the relationship between relevant variables. By utilizing parameters from a pulp and paper manufacturing facility, the research determines that the fuel cost, electricity cost, and steam flow rate are the most important parameters for the feasibility of the system with a desirable payback on the investment.Graphic Abstract
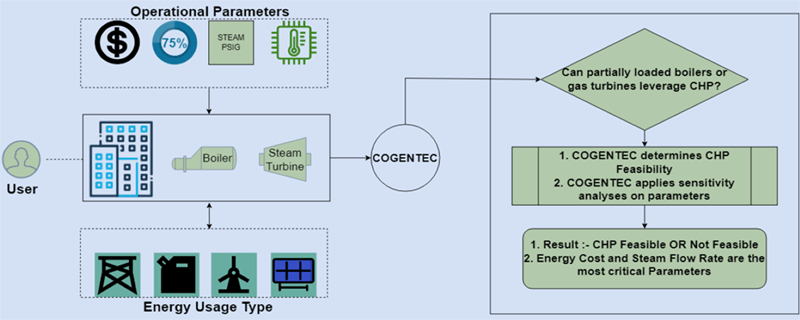
Keywords
Nomenclature
CHP | Combined Heat and Power |
CO2 | Carbon Dioxide |
COGENTEC | Cogeneration Topping Cycle Evaluation |
DSS | Decision Support System |
GT | Gas Turbine |
HRSG | Heat Recovery Steam Generator |
MWe | Megawatt Electricity |
ORC | Organic Rankine Cycle |
Cogeneration (Combined Heat and Power, CHP) is the concurrent generation of electrical and thermal energy from process heating systems such as furnaces, heaters, and kilns. A typical CHP system consists of on-site electrical generators, prime movers, and fossil fuel-fired equipment (boilers/gas turbines). CHP systems increase the plant’s efficiency, and reliability while reducing losses on the system. They increase the facility’s resiliency during power outages by maintaining runtime that leads to reliability improvement. CHP systems have higher efficiency and lower electricity and heat cost. They can often achieve total system efficiencies of 60%–80% compared to only about 45%–50% for conventional separate heat and power generation by avoiding losses and capturing heat energy wasted in power generation to provide heating and cooling [1]. These systems have great potential to offset the energy usage and cost in manufacturing facilities.
A topping cycle CHP system generates steam by utilizing more fuel for combustion; whereas, a bottoming cycle CHP system generates steam by utilizing the waste heat from the boiler/gas turbine. In short, a topping cycle uses primary fuel to generate steam and electricity, whereas a bottoming cycle uses waste heat to generate steam and electricity. Another difference between these two cycles is that the former focuses on electrical power generation, whereas the latter prioritizes heat generation. In a typical industrial setting where boilers and furnaces produce process heat, a topping cycle system is an ideal solution for offsetting energy costs. Industrial plants that do not operate boilers/gas turbines at full load are a perfect candidate for a topping cycle system. The processes in manufacturing plants generate flue gases with medium to high-grade heat content. These flue gases can be utilized to generate steam for power and heat generation.
Most industrial and manufacturing plants are also energy-intensive. They use fossil fuels and purchase electricity from the grid. It is prevalent in industrial plants that specialize in fiberglass, water and wastewater, metal fabrication, pulp and paper, and chemical manufacturing. Fossil fuels are a depleting source of energy; the worldwide reservoir for oil, coal, and gas is expected to extinguish in approximately 35, 107, and 37 years [2]. Further, fossil fuels dissipate a large number of greenhouse gases into the atmosphere, thereby increasing the global atmospheric temperature. The major pathways to decrease fossil fuel usage are energy efficiency and electrification through renewable sources. However, renewable energy has only increased its global uptake in the last decade. While the alternative sources receive more uptake, another major option to reduce the usage of fossil fuels for industries is to install CHP systems. These systems produce onsite electricity and offset electrical and thermal energy usage and cost. Moreover, the industrial plants can sell excess electricity back to the power grid, thereby reducing the load on the power plants, which produce 80% of the electricity in the world [3]. Another advantage is that it helps relieve the demand on the strained electric grid when the industrial, buildings and transportation sectors pursue electrification.
Much literature has focused on bottoming and combined cycles, where the flue gases generate steam in a Heat Recovery Steam Generator (HRSG) to drive the prime mover, and generate electricity and heat. The findings in bottoming cycles through energy and exergy analysis do not help comprehensively in the analysis of the technical and economic feasibility of a topping cycle system in industries. While the CHP systems are a mature technology with a wide array of applications, this study explores optimal working conditions for standalone topping cycles based on partially loaded industrial boilers or gas turbines. To that end, there are minimally available studies and/or programs that evaluate the feasibility of a partially loaded system based on its equipment and operating parameters. Industrial plants can make extensive use of a decision support system (DSS) that can evaluate the feasibility of such a system for their boiler operations. It can help devise the advantages and the disadvantages of monetary, power, and energy considerations based upon the demand side over time. A contradictory situation, in the absence of a DSS, would lead to a facility following the path set up by a vendor, without realizing whether it is economically viable or not. Therefore, the topping cycle-based DSS will bridge the gap between an idea and its implementation by incorporating mathematical values and measurements. The DSS termed Cogeneration Topping Cycle Evaluation (COGENTEC), enhances the decision-making capability in a topping cycle where the boiler(s) are not working at full load.
The advantages of CHP can be realized by facilities using prime movers such as reciprocating engines, steam turbines, gas turbines, microturbines, and fuel cells [4]. The authors mention the advantages of CHP systems such as elimination of transmission & distribution losses, increased reliability, reduction in greenhouse gas emission, and its versatile applicability in various industries and commercial facilities. Other authors have studied the effects of turbine inlet temperature, pressure ratio, and exhaust gas flow rate on the thermal efficiency and exergy loss of exhaust gas in a gas topping cycle and steam bottoming cycle system with an HRSG [5]. Butcher et al. conducted a study on the performance of waste heat recovery systems focusing on ambient temperatures, net-work output, and entropy generation [6]. Ahmadi et al. researched exergy losses in combined cycle power plants and concluded that the highest exergy loss occurs in the combustion chambers of turbines and boilers, thereby affecting overall efficiency [7]. Bilgen studied the exergy losses in gas turbine-based CHP plants to calculate economic parameters, such as Levelized cost and payback on the investment, concluding higher fuel utilization and exergy efficiency in CHP-based gas turbine systems [8]. Studies have also been conducted on exergy analysis in gas turbines-based bottoming cycle plants to decrease the exergy losses, subsequently concluding that energy efficiency measures in the heat exchanger (among heat exchangers, combustion chambers, steam boiler, gas turbine, and ambient air compressor) would result in the highest efficiency increase [9]. Frigo et al. studied the technical and economical feasibility of a biomass-based CHP plant to achieve a net electrical efficiency of 23.9% [10]. Research on CHP plant that utilizes black liquor and fuel oil to produce steam and electricity based on energy, exergy, and market-based method have been carried out. Varying fuel and electricity costs influence the plant’s revenue and the energy procurement cost of the mill [11]. Beyene developed the concept of eco-park which consists of various facilities employing CHP systems to highlight the reliability, flexibility, and resiliency of CHP systems, citing topping cycles as more beneficial than bottoming cycles as they can be modified to generate electricity and heat based on requirements [12]. Studies on the effect on cycle efficiency with a reduction in energy loss and irreversibility at different points of a combined cycle such as heat input point work output point, and heat rejection part conclude the outcomes are better for CHP systems concerning overall efficiency [13]. Improvements in system efficiency and savings through high-grade stack temperatures and ammonia-water turbines have been explored in [14,15]. The authors concluded that an increase in pressure ratio results in a subsequent increase in the combined cycle efficiency because lesser input fuel is required for combustion due to an increase in ambient air temperature.
Nag et al. researched the design and operation of a heat recovery steam generator in a gas and steam turbine-based topping & bottoming cycle to achieve minimum irreversibility and exergy loss by operating HRSG at its maximum capacity [16]. Theoretical studies on the improvement of operational parameters of bottoming cycle plants led to the conclusion that system design and operation schedule plays a vital role in overall efficiencies. The authors conclude that longer operating hours of absorption chillers and gas turbines would generate higher revenue. Therefore, changes in parameters such as decrement in inlet gas temperature in gas turbines and an increment in operational hours would result in higher electricity and cooling generation [17]. Valdes et al. studied the influence of different parameters such as ambient temperature and pressure, isentropic efficiency of the gas turbine, superheaters and reheaters temperature, evaporators, and economizers on the thermo-economic performances of combined cycled gas turbine power plants on full-load and partial-load. The results are significantly dependent on the type of turbine selected and the initial design parameters [18]. Optimal designs for heat recovery steam generators (HRSG) for bottoming cycles have been studied to reduce exergy losses for achieving maximum performance [19]. Effects of ambient temperature in combined cycle thermal power plants are explored in [20,21]. Oh et al. evaluated the economic feasibility of a gas turbine-based CHP for a hotel or an office building in Seoul, South Korea, citing a gas turbine-based CHP system being economically viable for a hotel, while not viable for office buildings [22]. Similarly, CHP systems have been studied for shipping applications to increase the net output of a cogeneration system through an increase in the mass flow rate of exhaust gas [23]. On the fuel side, topping cycles have been operated with wood and biomass as the primary fuel generating high-pressure steam for electricity generation, further increasing the sustainability of energy [24–27]. According to a report produced by the U.S. Department of Energy, the CHP systems in commercial facilities account for 50% of the total CHP systems in the United States [28]. The report highlights successful CHP installations in industrial and commercial facilities. Application of waste heat recovery in industrial applications for process integrating between heating and cooling loads using pinch analysis has been performed in [29]. Similarly, McBrien et al. studied the energy savings from heat recovery in an integrated steel supply chain through pinch analysis to compare the heat recovery process and an integrated heat recovery process [30]. Gambini et al. made a case study on high-efficiency CHP systems for the paper industry in Italy where the incentive scheme for selling electricity back to the grid has been modified with better rates for the unit selling price of electricity in recent years. The study indicated that gas turbines (GT) were the best CHP system for the selected paper industry [31]. Manufacturing facilities often oversize their heat-generating equipment to be more flexible for any increase in future production. Therefore, increasing loads on boilers, for example, can generate excess steam which can later be transported across steam turbines to generate electricity. This also improves their efficiency, resulting in increased cost savings. Despite copious amounts of literature on and widespread applications of CHP systems, a topping cycle-based CHP system that leverages partially loaded stationary combustion equipment in the manufacturing sector has not been performed. This paper aims to fill that gap through a techno-economic analysis of such systems by generating an MS-Excel™-based tool named COGENTEC.
This study aims to develop a system to analyze the economic and technical feasibility of a topping cycle system and sensitivity analysis of operating parameters in an industrial facility with a boiler working at partial load. The gas turbine system generates electricity in the topping cycle, and its exhaust, through a waste heat recovery boiler, generates steam for a steam turbine and end-uses. The approach is laid out on an MS-Excel™-based model that utilizes the relevant inputs from the user to advise them on the benefits and drawbacks of a topping cycle system if they choose to implement it. The tool can be requested through the authors for the usage of any kind. The general layout of the proposed CHP system is illustrated in Fig. 1.
Figure 1: Topping cycle CHP system schematics based on a partially loaded boiler
The study utilized data from a paper industry that uses high-pressure steam to dry its products before shipping them out. The selection of variables for COGENTEC was as per the requirements in a boiler/turbine-based CHP system and based on the literature survey. The facility also fitted quite well to the scope of a topping cycle as the facility’s natural gas boiler operated to about 30% of its total capacity. A combustion analyzer measured the stack temperature of the boiler and calculated the combustion efficiency of the boiler furnace. The combustion efficiency of the existing boiler was found to be 56.96%. In addition to this, it also calculated the temperature of the flue gas, the temperature of the ambient air, and the percentage of excess air during combustion. Boiler parameters such as boiler pressures and temperatures were recorded from the boiler display screen. Table 1 shows the recorded parameters.
After the procurement of the data from the paper facility, the study developed COGENTEC by referencing the reviewed literature and the parameters during the data collection. It can also evaluate gas turbine-based CHP systems. It has different input sheets (i) boiler and (ii) gas turbine. Once a user inputs all the necessary parameters, it calculates the variables such as total cost and energy savings, steam flow rate, and payback on investment, among other variables. Similarly, it also generates a spreadsheet with a block diagram for the entire CHP system (technical aspects) and displays the values of the important steam and energy parameters. Finally, it generates a result page that contains the economic aspects of the respective systems for the facility. The result sheet displays total savings, costs incurred, and payback on investment. It also generates graphs related to the sensitivity analysis for the change in output variables at different ranges of the input variables. COGENTEC has set boundaries regarding the operational pressure and temperature of the steam. They are as follows:
a) The operating temperature of the superheated steam should be between 32°F and 1,500°F.
b) The operating pressure of the superheated steam should be between −14.5949 and 1,085 psig.
c) The operating temperature of the saturated liquid/steam should be between 32°F and 705°F.
d) The operating pressure of the saturated liquid/steam should be between −14.61 and 3,185 psig.
e) Inlet mass flow rate is equal to the outlet mass flow rate in the steam turbines.
f) Steam passing through the steam turbines exhibits the isentropic process.
g) Steam flowing through the PRVs exhibits the isenthalpic process.
h) The boiler feed water leaves the deaerator and the economizer as the saturated liquid at the respective pressure.
Figs. 2 and 3 describe the design and schematics of COGENTEC. The user begins by selecting the applicable heat-generating equipment (boiler or gas turbine), followed by the input of relevant parameters based on their existing operations in the facility. The variables are identified in Table 1, and also portrayed in Fig. 3. Based on the values that the user selects, a block diagram illustrating the proposed CHP system is generated in COGENTEC. The block diagram has information regarding the steam and condensate flow rates, steam temperature and pressure at various points, losses, and power generation. On a separate worksheet, further results about respective parameters, and sensitivity analysis graphs are presented. The results include but are not limited to total energy and cost savings, capital cost, and payback on the investment. The information from this tool could be leveraged by the user to decide whether a topping cycle can be implemented in their facility or not.
Figure 2: Design of the decision support system–1
Figure 3: Design of the decision support system–2
Figs. 4–6 show the input screen of COGENTEC for a boiler-based topping cycle system. The input screen is user-friendly and easy to work with. In Fig. 5, the user starts by entering boiler rated capacity, excess air during combustion, ambient air temperature, boiler stack gas temperature, steam quantity, steam pressure, steam temperature, blowdown percentage, makeup water pressure, and temperature. COGENTEC also has options to include blowdown heat recovery, boiler controls, and combustion air pre-heat using boiler stack gas. These energy efficiency measures are beneficial for plants concerning energy and cost savings. If the plant does not have these measures, to begin with, it can implement them for a reduction in fuel consumption and CO2 emissions. Facilities can achieve a substantial leap in combustion efficiency by implementing these measures. Similarly, the user can enter operational parameters for up to four processes that require superheated or saturated steam. COGENTEC provides an option for the user to account for a backpressure turbine instead of a pressure release valve, in cases of additional electricity production. Backpressure turbines reduce the pressure of the steam while generating electricity at the same time. COGENTEC accounts for the economic aspects of installing a backpressure turbine and lets the user know if it is beneficial or not.
Figure 4: COGENTEC input screen-2
Figure 5: COGENTEC input screen-3
Figure 6: COGENTEC input screen-1
In Fig. 4, the outlet steam from the steam turbine and the processes, after accounting for the possible losses, is then used for absorption cooling during summer (yearly in cases where a facility requires cooling all the time) and comfort heating during the winter months. As the primary objective of a topping cycle is power generation, only the HVAC and chiller units can utilize excess heat in this study. Facilities may conduct an in-depth study to develop a situation for using the heat in outlet steam for district heating. Fig. 4 lets the user input their utility, fuel, and water cost. The utility and the fuel costs are recurring prices that the facilities pay to the utilities. COGENTEC does not address or include the “time of day” costs that can vary constantly and arbitrarily within the same facility. Spot trading at various times of the day is prevalent in states such as California, Massachusetts, and Ohio. However, in states such as West Virginia and Vermont, distributed generation is uncommon. The user will have to enter the constant price of electricity that they owe to the facility for electricity usage every month. COGENTEC uses these values to calculate expenditure and savings incurred through the project.
Fig. 7 illustrates the calculated parameters in a gas turbine-based CHP system. COGENTEC computes the power generated by the gas turbine, a steam turbine in a Rankine cycle, and the Organic Rankine cycle (ORC). The user selects an option to implement a condensing turbine or a backpressure turbine to generate electricity from the waste heat recovery boiler outlet steam. The waste heat boiler is powered by the flue gases from the gas turbine outlet. The electricity generation is exhibited in the gas turbine, and the subsequent steam turbines. If the ORC is applicable, COGENTEC automatically integrates an ORC based on the working fluid of the ammonia and water mixture. While it does not do calculations of an ORC in detail, the research assumes that for 1 MMBtu/hr of energy transferred from the hot water to the working fluid in the ORC, 36 kW of electrical energy is generated [32,33]. The exhaust of the steam turbines is the condensate, which has ample thermal energy for comfort heating required in the facility. The condensate is then returned to the waste heat boiler through the aid of a deaerator. Similarly, with a backpressure turbine, COGENTEC calculates savings and investment costs for an absorption chilling system as well. The study verified the gas turbine-based model in COGENTEC by computing it against a case study performed by the University of Massachusetts Amherst on a CHP system of 16 MWe capacity [34].
Figure 7: Example computation of gas turbine-based CHP parameters
Fig. 8 shows the results obtained from the parameters utilized in the pulp and paper industry in question. The payback comes out as a negative value. It means that the annual savings after implementing the topping cycle system are lesser than the annual expenditure. Thus, the CHP cycle at this facility with its respective energy, fuel, and water cost will not result in savings. COGENTEC shows negative payback as infinite, and the sensitivity analysis graphs show the negative, infeasible payback as “0” months. The most important factor for this calculation is the energy and fuel cost. Moreover, the combustion efficiency of the boiler furnace is around 50% only. It means that the boiler wastes half of the fuel in the form of stack gases. The facility can implement automatic burner controls and pre-heat combustion air to increase combustion efficiency, and produce a desirable payback on investment. COGENTEC integrates the sensitivity analysis graphs, thereby making it easier for the user to change the input values to produce as many graphs as they require. Figs. 9a and 9b show the relationship between the changes in the input variables to the power generation in (kW) and the payback on investment period on investment (months). Fig. 10 shows the overall layout for the topping cycle system.
Figure 8: Results for the boiler-based CHP cycle
Figure 9: Sensitivity analysis between input and output parameters
Figure 10: Boiler diagram with a condensing steam turbine
The relationship between the steam flow rate and power generation is linear. Despite generating more power at a higher steam flow rate, the payback on investment will not be feasible unless there is some serious revamp in the cost of natural gas and electricity usage. Steam pressure had a minimal impact on power generation; it also had a similar impact in the case of payback on investment. Steam temperature and turbine outlet pressure had an important relationship with power generation and payback during the investment period. However, for this facility, the minimum turbine outlet pressure (maximum energy transfer) is not enough for higher annual cost savings than that of the cost incurred.
Fig. 11 shows the relationship between the payback on the investment period, natural gas cost, and electricity usage cost. It can infer that a lower natural gas cost and a higher electricity usage cost are vital to achieving better savings and payback on investment. For the facility in question, the most optimal natural gas and electricity usage costs are $2.75/MMBtu and $0.14/kWh for a 4 years payback on investment. There is a better payback on investment outcomes at various energy and fuel costs; however, those costs are not in the control of the facility, therefore, the analysis is only carried out for information on the range of costs.
Figure 11: Sensitivity analysis between the payback on investment period, natural gas cost, and electricity usage cost
Table 2 shows the ranges of values for the input variables for which the facility will achieve a payback on the investment of fewer than 4 years for the boiler-based CHP system. For the current facility with its existing steam boilers, the process is infeasible at all the flow rates, steam pressure, temperature, and turbine exit pressure. However, if the price of utilities changes to the content in Table 2, then the facility will achieve a desirable payback. The optimum values of natural gas and electricity cost are less than $2.75/MMBtu and greater than >=$0.14/kWh.
As performed with the boiler-based CHP, the study carried out sensitivity analysis for a gas turbine-based CHP system as well. The graphs are readily available in the results spreadsheet, and COGENTEC modifies the graphs every time the user changes the values of the input parameters. The input parameters chosen for the analysis are inlet air mass flow rate, inlet air temperature, compressor efficiency, the pressure ratio of the compressor, excess air percentage, waste heat boiler steam quantity, waste heat boiler steam pressure, and temperature. Similarly, the output parameters in the analysis are total power generation by the system and payback on the investment period on investment. These two parameters prevail as they are at the forefront of the technical and economical capability of the system. Figs. 12 and 13a–13c show the results and the sensitivity analysis graphs for the gas turbine-based CHP.
Figure 12: Gas turbine-based CHP results
Figure 13: Sensitivity analysis for a gas-turbine-based CHP system
The Fig. 13 infers that the amount of inlet air, its temperature, the pressure ratio of the compressor, and the waste heat boiler steam quantity are the major parameters that influence power generation and payback on investment. Out of those input parameters, based on the graphs in the above figures, the waste heat boiler steam flow rate is the parameter that has the most impact on the payback during the investment period on investment. The waste heat boiler steam runs through a steam turbine that generates electricity. At present, the facility utilizes 100,000 lbs/hr of steam. By increasing the steam flow rate to 400,000 lbs/hr, the payback on the investment period reduces by half (10 months) because of increased electricity generation. The y-axis (payback on the investment) and the x-axis variables are not directly related, as they are obtained from numerous subsequent calculations. Moreover, the payback on investment also includes the capital cost for investment, annual operating costs, and energy savings costs, these trends result in a non-uniform pattern. Further, Fig. 16 shows a data table for the impact of varying electricity and natural gas costs on payback on investment of the gas turbine-based CHP system. The figure further strengthens the flexibility of electricity and natural gas costs for the CHP system in question.
In the case study, the varying cost of energy and fuel cost does play a role in changing payback on investment. However, as the impact of natural gas cost on the gas turbine-based CHP is minimal, the project has a lot of green areas even at highly varying fuel and electricity costs. Even at the high cost of natural gas ($5/MMBtu) and a low cost of electricity usage ($0.05/kWh), the payback on investment is approximately 5.5 years. Therefore, the project is viable for the case study. Figs. 14 and 15 show the block diagrams for the proposed scenario.
Figure 14: Gas turbine-based CHP system (Condensing turbine)
Figure 15: Gas turbine-based CHP system (Backpressure turbine)
Figure 16: Impact of varying electricity and natural gas costs on payback on investment
Table 3 shows the ranges of values for the input variables for which the payback will be lesser than 21 months. 21 months is the payback under the current set of input variables. Therefore, the optimum values for which the payback is less than 21 months are calculated to get a better understanding of the variables that influence the payback on the investment the most. The most important set of parameters is the electricity cost, natural gas cost, waste heat boiler steam quantity, and the compressor pressure ratio.
The study researches and verifies the effect of the operational parameters of a steam boiler and a gas turbine on the economic and technical aspects of implementing a topping cycle system. It developed an MS Excel®-based decision support system called “COGENTEC”, which lets a user enter the input parameters related to the operations of a steam turbine or a gas turbine. COGENTEC selected the operational parameters as per the CHP system’s operations and a literature survey carried out in previous studies. The study computes the results based on the input parameters and displays the results, based on savings, expenditure, and the payback on investment. Moreover, a block diagram associated with the CHP system makes it easier for the user to grasp the flow of steam/water and the energy in the system. COGENTEC lets the user select two different primary equipment. The first option is that a steam turbine utilizes the excess steam from the boiler pushed at full load. The second option is that of a gas turbine that generates electricity and utilizes turbine exhaust’s heat in the form of comfort heating, district heating, or a waste heat recovery boiler for power generation.
The study verified COGENTEC by utilizing the steam boiler operational and input parameters from the pulp and paper industry. The most important parameters for obtaining a feasible payback on investment are electricity usage and natural gas usage cost in a gas turbine and boiler-based CHP system. Power generation from a steam turbine is linearly proportional to the steam generation in a steam boiler or a waste heat recovery boiler. Steam pressure and temperature are directly proportional to the power generation; however, their impact is not as important as that of the steam quantity. The steam turbine outlet pressure is inversely proportional to the power generation and the payback on investment. Lower outlet pressure generates more power and lowers the payback on investment. To achieve a feasible payback in the paper industry, the cost of electricity must be more than $0.14/kWh. Similarly, the cost of natural gas must be less than $2.00/MMBtu for a feasible payback. For the facility under consideration in the case study, the demand cost did not influence the payback on the investment. The most optimal combined cost of electricity and natural gas for a feasible payback on investment is $0.12/kWh and $2.5/MMBtu. These costs would result in an eight-year payback. The Inlet air temperature and quantity of the gas turbine are linearly dependent on the total power generation. Inlet air temperature is directly proportional to the power generation whereas the inlet air temperature is inversely proportional to the power generation. Similarly, for a gas-turbine-based CHP system case study, the optimal cost of the natural gas and electricity should be $3.00/MMBtu ad $0.09/kWh for a 2 years payback. The Inlet air temperature and quantity of the gas turbine are linearly dependent on the total power generation. Inlet air temperature is directly proportional to the power generation whereas the inlet air temperature is inversely proportional to the power generation. The compressor pressure ratio and the waste heat boiler steam quantity are the most important parameters after the natural gas and electricity usage for a lower payback in a gas turbine-based CHP.
Future work on this research study involves the formulation of a dynamic DSS by increasing the number of parameters for the boilers and the steam turbine, and analyzing their continuous effects, if any, on the economic and technical benefits of a topping cycle system. Future works may pursue the usage of dynamic data collection through sensors to get data over time. COGENTEC deals in brief with the end-use and their characteristics. It could, further, include an enumeration of different detailed end uses. Similarly, the usage of multiple boilers, steam turbines, and dual burners was not a part of this study. Integrating multiple pieces of equipment would result in a better embodiment of a real-life process. Time-of-day rates of natural gas and electricity based on the principle of distributed generation may provide a realistic cogeneration analysis. Finally, the model could create a system based on the target power required, and subsequent derivation for the energy system attributes such as boilers and steam turbines.
Funding Statement: This research work was funded in part by the Industrial Assessment Center Project, supported by grants from the US Department of Energy and by the West Virginia Development Office.
Conflicts of Interest: The authors declare that they have no conflicts of interest to report regarding the present study.
References
1. U.S. DOE (2012). Combined heat and power: A clean energy solution. Washington DC, USA: U.S.DOE and U.S. EPA. [Google Scholar]
2. Shafiee, S., Topal, E. (2009). When will fossil fuel reserves be diminished? Energy Policy, 37(1), 181–189. DOI 10.1016/j.enpol.2008.08.016. [Google Scholar] [CrossRef]
3. Abuelnuor, A., Saqr, K. M., Mohieldein, S. A., Dafallah, K. A., Abdullah, M. M. et al. (2017). Exergy analysis of Garri “2” 180 MW combined cycle power plant. Renewable and Sustainable Energy Reviews, 79(C), 960–969. DOI 10.1016/j.rser.2017.05.077. [Google Scholar] [CrossRef]
4. Singh, V., Radermacher, R. (2009). Boost efficiency and reliability via cogeneration. Buildings, 103(6), 78–81. [Google Scholar]
5. Khan, M., Tlili, I. (2018). Innovative thermodynamic parametric investigation of gas and steam bottoming cycles with heat exchanger and heat recovery steam generator: Energy and exergy analysis. Energy Reports, 4, 497–506. DOI 10.1016/j.egyr.2018.07.007. [Google Scholar] [CrossRef]
6. Butcher, C., Reddy, B. (2007). Second law analysis of a waste heat recovery based power generation system. International Journal of Heat and Mass Transfer, 50(11–12), 2355–2363. DOI 10.1016/j.ijheatmasstransfer.2006.10.047. [Google Scholar] [CrossRef]
7. Ahmadi, M. H., Nazari, M. A., Sadeghzadeh, M., Pourfayaz, F., Ghazvini, M. et al. (2019). Thermodynamic and economic analysis of performance evaluation of all the thermal power plants: A review. Energy Science & Engineering, 7(1), 30–65. [Google Scholar]
8. Bilgen, E. (2000). Exergetic and engineering analyses of gas turbine based cogeneration systems. Energy, 25(12), 1215–1229. [Google Scholar]
9. Ozkan, D. B., Kiziler, O., Bilge, D. (2012). Exergy analysis of a cogeneration plant. International Journal of Mechanical and Aerospance Engineering, 6(1), 235–239. [Google Scholar]
10. Frigo, S., Gabbrielli, R., Linari, L. (2018). Feasibility study of a CHP plant with steam turbine and biomass gasification for tissue paper production. Energy Procedia, 146, 751–757. [Google Scholar]
11. Holmberg, H., Tuomaala, M., Haikonen, T., Ahtila, P. (2012). Allocation of fuel costs and CO2-emissions to heat and power in an industrial CHP plant: Case integrated pulp and paper mill. Applied Energy, 93, 614–623. [Google Scholar]
12. Beyene, A. (2005). Combined heat and power as a feature of energypark. Journal of Energy Engineering, 131(3), 173–188. DOI 10.1061/(ASCE)0733-9402(2005)131:3(173). [Google Scholar] [CrossRef]
13. Murugan R. S., Subbarao P. (2008). Efficiency enhancement in a rankine cycle power plant: Combined cycle approach. Proceedings of the Institution of Mechanical Engineers, Part A: Journal of Power and Energy, 222(8), 753–760. DOI 10.1243/09576509JPE613. [Google Scholar] [CrossRef]
14. Ferreira, V. R., Augusto, C. M., Ribeiro, J. B., Gaspar, A. R., Costa, J. J. (2015). Increasing the efficiency of high temperature furnaces through a topping cycle cogeneration—A case study. Energy Efficiency, 8(1), 85–95. DOI 10.1007/s12053-014-9278-2. [Google Scholar] [CrossRef]
15. Maheshwari, M., Singh, O. (2019). Comparative evaluation of different cycle configurations having simple gas turbine, steam turbine and ammonia water turbine. Energy, 168(7), 1217–1236. DOI 10.1016/j.energy.2018.12.008. [Google Scholar] [CrossRef]
16. Nag, P., De, S. (1997). Design and operation of a heat recovery steam generator with minimum irreversibility. Applied Thermal Engineering, 17(4), 385–391. DOI 10.1016/S1359-4311(96)00033-6. [Google Scholar] [CrossRef]
17. Somcharoenwattana, W., Menke, C., Kamolpus, D., Gvozdenac, D. (2011). Study of operational parameters improvement of natural-gas cogeneration. Energy and Buildings, 43(4), 925–934. DOI 10.1016/j.enbuild.2010.12.016. [Google Scholar] [CrossRef]
18. Valdes, M., Rovira, A., Duran, M. D. (2004). Influence of the heat recovery steam generator design parameters on the thermoeconomic performances of combined cycle gas turbine power plants. International Journal of Energy Research, 28(14), 1243–1254. DOI 10.1002/er.1026. [Google Scholar] [CrossRef]
19. Franco, A., Giannini, N. (2006). A general method for the optimum design of heat recovery steam generators. Energy, 31(15), 3342–3361. DOI 10.1016/j.energy.2006.03.005. [Google Scholar] [CrossRef]
20. Arrieta, F. R., Lora, E. E. (2005). Influence of ambient temperature on combined-cycle power-plant performance. Applied Energy, 80(3), 261–272. DOI 10.1016/j.apenergy.2004.04.007. [Google Scholar] [CrossRef]
21. Şen, G., Nil, M., Mamur, H., Doğan, H., Karamolla, M. et al. (2018). The effect of ambient temperature on electric power generation in natural gas combined cycle power plant—A case study. Energy Reports, 4(12), 682–690. DOI 10.1016/j.egyr.2018.10.009. [Google Scholar] [CrossRef]
22. Oh, S. D., Oh, H. S., Kwak, H. Y. (2007). Economic evaluation for adoption of cogeneration system. Applied Energy, 84(3), 266–278. DOI 10.1016/j.apenergy.2006.08.002. [Google Scholar] [CrossRef]
23. Tien, W. K., Yeh, R. H., Hong, J. M. (2007). Theoretical analysis of cogeneration system for ships. Energy Conversion and Management, 48(7), 1965–1974. DOI 10.1016/j.enconman.2007.01.032. [Google Scholar] [CrossRef]
24. Tillman, D., Jamison, R. (1982). Cogeneration with wood fuels: A review. Fuel Processing Technology, 5(3), 169–181. DOI 10.1016/0378-3820(82)90013-3. [Google Scholar] [CrossRef]
25. Oliveira, T. L., Assis, P. S., Leal, E. M., Ilidio, J. R. (2015). Study of biomass applied to a cogeneration system: A steelmaking industry case. Applied Thermal Engineering, 80(5), 269–278. DOI 10.1016/j.applthermaleng.2015.01.002. [Google Scholar] [CrossRef]
26. Çakir, U., Çomakli, K., Yüksel, F. (2012). The role of cogeneration systems in sustainability of energy. Energy Conversion and Management, 63(4), 196–202. DOI 10.1016/j.enconman.2012.01.041. [Google Scholar] [CrossRef]
27. Demirbas, A. (2005). New opportunities resulting from cogeneration systems based on biomass gasification. Energy Sources, 27(10), 941–948. DOI 10.1080/00908310490449063. [Google Scholar] [CrossRef]
28. Hampson, A., Tidball, R., Fucci, M., Weston, R. (2016). Combined heat and power (CHP) technical potential in the United States. Washington DC, USA: U.S. DOE. [Google Scholar]
29. Arzbaecher, C., Fouche, E., Parmenter, K., Global Energy Partners (2007). Industrial waste-heat recovery: Benefits and recent advancements in technology and applications. In: ACEEE summer study on energy efficiency in industry. Washington DC, USA: ACEEE. [Google Scholar]
30. McBrien, M., Serrenho, A. C., Allwood, J. M. (2016). Potential for energy savings by heat recovery in an integrated steel supply chain. Applied Thermal Engineering, 103(1), 592–606. DOI 10.1016/j.applthermaleng.2016.04.099. [Google Scholar] [CrossRef]
31. Gambini, M., Vellini, M., Stile, T., Manno, M., Bellochi, S. (2019). High-efficiency cogeneration systems: The case of the paper industry in Italy. Energies, 12(3), 335–355. DOI 10.3390/en12030335. [Google Scholar] [CrossRef]
32. Ogriseck, S. (2009). Integration of kalina cycle in a combined heat and power plant, a case study. Applied Thermal Engineering, 29(14–15), 2843–2848. DOI 10.1016/j.applthermaleng.2009.02.006. [Google Scholar] [CrossRef]
33. Bai, L. (2012). Life cycle assessment of electricity generation from low temperature waste heat: The influence of working fluid (Master Thesis). Norwegian University of Science and Technology, Norway. [Google Scholar]
34. Burbank, J. (2013). Case study: 16 MW combined cycle cogeneration plant for a university campus. Amherst, USA: UMass Amherst. [Google Scholar]
Cite This Article
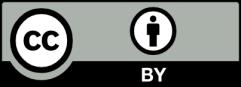
This work is licensed under a Creative Commons Attribution 4.0 International License , which permits unrestricted use, distribution, and reproduction in any medium, provided the original work is properly cited.