Open Access
ARTICLE
Optimization of Blade Geometry of Savonius Hydrokinetic Turbine Based on Genetic Algorithm
1 College of Water Resources and Civil Engineering, China Agricultural University, Beijing, 100083, China
2 Beijing Engineering Research Center of Safety and Energy Saving Technology for Water Supply Network System, China Agricultural University, Beijing, 100083, China
* Corresponding Author: Ran Tao. Email:
Energy Engineering 2023, 120(12), 2819-2837. https://doi.org/10.32604/ee.2023.042287
Received 25 May 2023; Accepted 03 August 2023; Issue published 29 November 2023
Abstract
Savonius hydrokinetic turbine is a kind of turbine set which is suitable for low-velocity conditions. Unlike conventional turbines, Savonius turbines employ S-shaped blades and have simple internal structures. Therefore, there is a large space for optimizing the blade geometry. In this study, computational fluid dynamics (CFD) numerical simulation and genetic algorithm (GA) were used for the optimal design. The optimization strategies and methods were determined by comparing the results calculated by CFD with the experimental results. The weighted objective function was constructed with the maximum power coefficient Cp and the high-power coefficient range R under multiple working conditions. GA helps to find the optimal individual of the objective function. Compared the optimal scheme with the initial scheme, the overlap ratio β increased from 0.2 to 0.202, and the clearance ratio ε increased from 0 to 0.179, the blade circumferential angle γ increased from 0° to 27°, the blade shape extended more towards the spindle. The overall power of Savonius turbines was maintained at a high level over 22%, R also increased from 0.73 to 1.02. In comparison with the initial scheme, the energy loss of the optimal scheme at high blade tip speed is greatly reduced, and this reduction is closely related to the optimization of blade geometry. As R becomes larger, Savonius turbines can adapt to the overall working conditions and meet the needs of its work in low flow rate conditions. The results of this paper can be used as a reference for the hydrodynamic optimization of Savonius turbine runners.Keywords
Nomenclature
λ | Blade tip velocity ratio |
β | Blade tip ratio |
ε | Blade clearance ratio |
δ | Arc radius ratio |
e | Overlap distance |
a | Clearance distance |
Rb | Blade radius |
γ | Circumferential angle of blade |
D | The diameter of runner |
ω | The angular velocity of runner |
Cp | The turbine power coefficient |
ρ | The fluid density |
T1 | The temperature |
ω1 | Is the turbulent eddy frequency |
π | Circumference ratio |
H | The runner height |
U0 | The steady inlet velocity |
T | The torque |
Cpmax | The optimal power coefficient |
W | The performance weighting functions |
w1 | The weight of Cpmax of 0.5 |
c1 | The maximum experimental power coefficient value of 0.3 |
w2 | The weight of R of 0.5 |
c2 | The range of the maximum tip speed ratio of 2 |
Ep | The entropy production rate |
β1 | The model closure constant, β1 = 0.09 |
k | The turbulent energy |
T* | The moment of motion of the runner blades |
i | The number of segments in a π cycle |
nt | The number of segments through which the blade passes |
In recent years, with the increase of the world’s population, countries around the world are facing different degrees of energy crisis. As a result, countries began to switch from fossil energy to renewable energy, hydropower is a kind of power generation technology that can alleviate the pressure of fossil energy demand to a certain extent [1–3]. Large hydropower stations need to utilize the potential energy generated by the water level difference between upstream and downstream to generate electricity. People have different reviews of such behavior. The small hydropower station appeared, with a preference for gaining energy directly from low-velocity water [4,5]. Savonius hydrokinetic turbine is a kind of turbine which works under the condition of small velocity. Under the condition that velocity is greater than 0.5 m/s, the Savonius turbine can work well and produce certain efficiency, this kind of turbine is suitable for hydropower generation and transmission in remote areas and poor geographical environments [6–8].
The Savonius turbine is characterized by its ability to work harmoniously at low velocity without causing significant damage to fish populations and the work environment [9,10]. The early Savonius turbine was designed with an S-blade runner, which has stable working performance but low working efficiency, and some people have studied the blade shape optimization of the Savonius turbine. The work characteristics of the Savonius turbine are analyzed under steady inlet velocity conditions, and the effects of blade overlap ratio, clearance ratio, blade chord length, blade number and tip speed ratio on turbine performance are figured out. Thiyagaraj et al. [11] studied how to improve the power coefficient of the Savonius turbine by changing the number of blades, overlap ratio and increasing overturning. The power coefficients under different blade numbers and overlap ratios are analyzed. Bian et al. [12] analyzed the flow field performances of the Savonius turbine based on CFD and explored the influence of tip speed ratio and overlap ratio on the power coefficient. Kumar et al. [13] concentrated on the study of the Savonius turbine runner. Compared with the two-blade and three-blade runner, the four-blade Savonius runner performance is worse. Mosbahi et al. [14] studied how to improve the efficiency of the Savonius runner by changing the blade shape, and used CFD to simulate the different blade shapes, and optimized the power coefficient according to the tip speed ratio and the blade shape. Hashem et al. [15] took a pair of swimming koi carp as inspiration and carried out a CFD-based optimization design for the Savonius turbine, mainly aiming at the blade overlap ratio and clearance ratio to enhance the power coefficient on the meta-model. Wang et al. [16] optimized the design of the Savonius wind turbine with a double-sided contour, using sliding network technology to build CFD models, and optimized the double-sided shape of the runner based on the Kriging-PSO optimization model. Finally, the turbine performance was significantly improved. Shashikumar et al. [17] studied the performance of conventional and tapered turbine blades in hydroelectric power generation was investigated and it was found that the loss of energy measured at the outlet of the advancing blade of the tapered turbine resulted in a 5% reduction in performance. Additionally, Shashikumar et al. [18] also studied the Savonius turbine with different tip speed ratios using the dynamic grid technique and showed that the maximum torque coefficient and power coefficient for tip speed ratios of 0.22 and 0.17 were 0.7 and 0.9. Khani et al. [19] first used different software calculation methods such as Catboost, artificial neural networks, and random forests to predict the power coefficients of the Savonius hydrodynamic turbine, and the results showed that the Catboost method was more accurate. Wu et al. [20] combined the fast Fourier transform and dynamic modal decomposition to provide an in-depth analysis of the frequency distribution and dynamic patterns of velocity fluctuations in the near wake region, comparing the advantages and disadvantages of the two methods and providing a new approach to flow analysis.
It is found that the blade geometry is the key to the power coefficient performance of the Savonius turbine. When evaluating the performance of the Savonius turbine, the value of the maximum power coefficient and the value of the high-power coefficient range should also be considered. This is a typical bi-objective optimization study [21,22]. Using an algorithm to optimize design is a method often used in engineering work. It is not only widely used in water turbines, but also widely used in air turbines, pumps and so on. Based on the genetic algorithm, Chan et al. [23] optimized the blade shape of the Savonius wind turbine with conventional semi-circular blades to further improve the power coefficient. Jia et al. [24] optimized the Savonius wind turbine blade shape based on a support vector regression agent model and an improved flower pollination algorithm. The optimized wind turbine has a better ability to catch wind than the conventional semicircular blade turbine. Mohamad et al. [25] optimized the design of centrifugal pumps based on the Particle swarm optimization, optimizing the shape of the centrifugal pump runner to increase efficiency and head. Oyama et al. [26] optimized the design of a rocket engine pump based on an evolutionary algorithm, using the concept of a single-stage centrifugal pump to enhance the design. After optimization, the total head of the unit is superior to the original design, and the input power is reduced by 1%. Wu et al. [27] used the discrete particle swarm optimization algorithm to optimize the array of tidal turbines, by redefining the particle velocity to optimize the position of each tidal turbine. Based on the genetic algorithm, Han et al. [28] optimized the design of wind turbine blades by using induced iterative initialization. Lu et al. [29] optimized the design of the rotor blade and guide vane shape of the OWC device based on a genetic algorithm and artificial neural network, and the results showed that the energy loss of the optimal blade shape was greatly reduced and there was a significant widening of the efficient range of the OWC device.
In the process of optimization design, the flow characteristics in the runner blade region and the energy loss at the blade can be analyzed by means of computational fluid dynamics (CFD). Based on the entropy production theory, Chang et al. [30] analyzed the energy loss of the self-priming pump, and analyzed the type, magnitude and location of hydraulic loss under different blade thickness distributions. Su et al. [31] analyzed the performance and energy loss of the high-speed centrifugal pump with straight blades, combined with the flow stability analysis, and introduced the entropy production method to evaluate the mechanical loss. Ghorani et al. [32] utilized the theory of entropy production, and a pump was used as a turbine in the numerical study of the mechanism of energy dissipation. In this paper, entropy production theory and the second law of thermodynamics are used to study the problem of energy loss inside the pump. Based on entropy production, Wang et al. [33] optimized the geometric parameters of the pump as the impeller of a steam turbine under three different typical flow conditions. An entropy production rate analysis can effectively explain the energy loss phenomenon.
The main research object of this paper is the Savonius turbine with an S-shaped blade, in which the geometric shape of the runner blade is the key point of the optimization design. The optimization will consider dual performance parameters as the objective function, and the genetic algorithm will be utilized as the foundational technique for achieving this objective. The relationship between the blade overlap ratio, clearance ratio, blade circumferential angle and the maximum power coefficient and high-power coefficient range of the Savonius turbine will be deeply analyzed and expounded. The influence of runner blade geometry on turbine performance will be thoroughly studied, which will provide technical support for hydropower generation in conditions of small flow velocity.
2 Model and Parameters Profiles of Savonius Turbine
Fig. 1 below shows a two-dimensional model of the Savonius turbine, serving as the key point of this paper. As the computational domain of the Savonius turbine is very wide compared to the runner computational domain and the results near the edges do not affect the runner computational domain, we saved both computational resources and time costs by reducing the three-dimensional model to two dimensions [34,35]. The turbine is composed of four key components: inlet, outlet, interface and runner blade. At low velocity, water flows from the inlet through the runner and blade, producing torque under the combined action of the two blades, and then flows out of the outlet.
Figure 1: Multi-block computational domains showing dimensions and boundary conditions
The relationship between the power coefficient of the Savonius turbine and the blade geometry is studied. Therefore, we define the control parameters of blade clearance, such as the blade overlap ratio
In the design of runner blades, the shape and parameter values of the turbine model used in this study are shown in Fig. 2 and Table 1. The blade tip velocity ratio
where
The blade clearance ratio
The arc radius ratio
Figure 2: Geometric parameters of turbine
Parameters
3 Performance Evaluation of Baseline Model
In this study, the commercial software ANSYS CFX was used for CFD simulation. The fluid medium was water at 25°C, and the pressure was 1 Atm. The turbulence model utilized was the SST k-ω model, which is more accurate and reliable and widely applied. In CFD simulation, one side of the domain was taken as the inlet and the other side was taken as the outlet. The condition of the velocity inlet type was set at the inlet side, while the static pressure type outlet boundary was set at the outlet side. All wall boundaries use the no-slip wall conditions. The Multiple Reference Frame (MRF) is used. The computational domain consists of the stationary domain and the rotational domain, and the boundary between the stationary and the rotational domain is given as the interface. Steady state iterative simulation is performed first. The steady results are used as the basis for the unsteady state simulation. The convergent criterion is that the RMS residual of the continuity equation and momentum equation was less than 0.0001.
3.2 Grid Preparation and Check
To conduct CFD simulation, grid preparation and grid-independent checking should be carried out. The grid of the computational domain is shown in Fig. 3. In order to ensure the accuracy of CFD, four sets of different grids (N1, N2, N3 and N4) are prepared with the number of grids of 10 thousand, 20 thousand, 40 thousand, 80 thousand, respectively. The performance of the Savonius turbine under the same operating condition is tested by using these four sets of grids. The grid check results are shown in Fig. 4. From the different grid of turbine performance variation curves, the error is within the permissible range. Finally, the grid of 20 thousand nodes is selected for CFD simulation.
Figure 3: Grid of computational domain
Figure 4: Grid independence check details
3.3 Performance Evaluation and Comparison
In Fig. 5, we performed CFD numerical simulations of the model and compared the CFD prediction results with Nakajima’s experimental results [36]. It is found that the fitting is good from the trend of power coefficient, but the value of power coefficient
Figure 5: Comparison of power coefficients
4 Runner Blade Geometry Optimization
4.1 Parameterization and Coding
In this paper, the key optimization parameters are blade overlap ratio
In this paper, the optimal power coefficient and maximum power coefficient area width of the Savonius turbine are analyzed and optimized, so define the dimensionless number power coefficient
where
Define the optimal power coefficient is
where
The optimization parameters had previously been binary coded, followed by genetic algorithm (GA) operations that set the probability of crossover at 20%, the probability of variation at 5%, and the probability of copying/eliminating the best/worst individuals at 100%. The flow chart illustrating this process is drawn in Fig. 6 below. On the basis of this configuration in place, the optimization design is carried out combined with CFD simulation.
Figure 6: Flow chart of genetic algorithm operation
Compare the blade geometry of the initial scheme with the optimal scheme, as shown in Fig. 7 below. The initial scheme has the following parameters:
Figure 7: Comparison of blade geometry before and after optimization
The performance of the turbine with the optimized blade is compared with the that of the turbine with the initial blade, as shown in Fig. 8. The overall performance of the optimal Savonius turbine is superior to the initial turbine. In the initial scheme, the power coefficient
Figure 8: Comparison of Savonius turbine’s performance of initial and optimal scheme
The fluctuation curves of the power coefficient
Figure 9: The comparison of the
In this paper, the energy loss analysis based on the entropy production rate of the Savonius turbine is carried out. The entropy production rate
where
The initial scheme and optimal scheme of blade rotation are examined at different locations under various working conditions. Conditions like blade tip velocity ratio
where π is circumference ratio,
Figure 10: The position of the runner blades at five moments
Fig. 11 shows the condition of
Figure 11: The comparison of the entropy production rate of initial and optimal schemes at five moments when
When
When
When
When
Fig. 12 shows the condition of
Figure 12: The comparison of the entropy production rate of initial and optimal schemes at five moments when
When
When
When
When
Fig. 13 shows the condition of
Figure 13: The comparison of the entropy production rate of initial and optimal schemes at five moments when
When
When
When
When
The main conclusions of this study are as follows:
(1) In this paper, before optimization, the power coefficient of the turbine in the original scheme increases slightly with the increase of the blade tip speed ratio from 0.7 to 1.1, then it decreases slowly, and finally decreases sharply to 10% at
(2) In this paper, a Genetic Algorithm (GA) was used to optimize the blade overlap ratio
(3) In this paper, the energy loss of the optimized turbine, especially around the runner blades, is obviously reduced. The five moments (
Acknowledgement: We acknowledge the financial support of National Natural Science Foundation of China to support the research.
Funding Statement: This research was funded by National Natural Science Foundation of China, Grant Number 52079142.
Author Contributions: The authors confirm contribution to the paper as follows: study conception and design: Zhang F. F., Guang W. L.; data collection: Wu Y. Z.; analysis and interpretation of results: Tao R., Li X. Q.; draft manuscript preparation: Lu J. H., Tao R. All authors reviewed the results and approved the final version of the manuscript.
Availability of Data and Materials: Data supporting this study are included within the article.
Conflicts of Interest: The authors declare that they have no conflicts of interest to report regarding the present study.
References
1. Fabre, A., Fodha, M., Ricci, F. (2020). Mineral resources for renewable energy: Optimal timing of energy production. Resource and Energy Economics, 59, 101131. [Google Scholar]
2. Holechek, J. L., Geli, H. M. E., Sawalhah, M. N., Valdez, R. (2022). A global assessment: Can renewable energy replace fossil fuels by 2050. Sustainability, 14(8), 4792. [Google Scholar]
3. Chamberland, A., Levesque, S. (1996). Hydroelectricity, an option to reduce greenhouse gas emissions from thermal power plants. Energy Conversion and Management, 37(6–8), 885–890. [Google Scholar]
4. Schwartz, F. H., Shahidehpour, M. (2006). Small hydro as green power. 2006 IEEE EIC Climate Change Conference, pp. 1–6. Ottawa, Canada. [Google Scholar]
5. Tapia, A., Millan, P., Gomez-Estern, E. (2018). Integer programming to optimize micro-hydro power plants for generic river profiles. Renewable Energy, 126, 905–914. [Google Scholar]
6. Rengma, T. S., Sengupta, A. R., Basumatary, M., Biswas, A., Bhanja, D. (2021). Performance analysis of a two bladed Savonius water turbine cluster for perennial river-stream application at low water speeds. Journal of the Brazilian Society of Mechanical Sciences and Engineering, 43(5), 1–21. [Google Scholar]
7. Güney, M. S., Kaygusuz, K. (2010). Hydrokinetic energy conversion systems: A technology status review. Renewable & Sustainable Energy Reviews, 14(9), 2996–3004. [Google Scholar]
8. Khan, A. A., Shahzad, A., Hayat, I., Miah, M. S. (2016). Recovery of flow conditions for optimum electricity generation through micro hydro turbines. Renewable Energy, 96, 940–948. [Google Scholar]
9. Song, L., Liu, H. Z., Yang, Z. X., Dong, G. Q. (2016). Simulation analysis based performance comparison for vertical axis wind turbines. 2016 International Conference on Advanced Mechatronic Systems (ICAMechS), pp. 334–339. Melbourne, Australia. [Google Scholar]
10. Song, L., Liu, H. X., Yang, Z. X. (2015). Performance comparison for Savonius type wind turbines by numerical analysis approaches. 2015 International Conference on Advanced Mechatronic Systems (ICAMechS), pp. 402–407. Beijing, China. [Google Scholar]
11. Thiyagaraj, J., Rahamathullah, I., Anbuchezhiyan, G., Barathiraja, R., Ponshanmugakumar, A. (2021). Influence of blade numbers, overlap ratio and modified blades on performance characteristics of the Savonius hydro-kinetic turbine. Materials Today: Proceedings, 46, 4047–4053. [Google Scholar]
12. Bian, P. X., Yang, Z. H., Wang, Y., Ma, P. L., Wang, S. Y. (2018). Hydrodynamic performance of Savonius water turbine. Journal of Zhejiang University Engineering Science, 52(2), 268–272. [Google Scholar]
13. Kumar, R. S., Premkumar, T. M., Seralathan, S., Xavier, D. D., Elumalai, E. S. et al. (2020). Simulation studies on influence of shape and number of blades on the performance of vertical axis wind turbine. Materials Today: Proceedings, 33(3), 3616–3620. [Google Scholar]
14. Mosbahi, M., Lajnef, M., Derbel, M., Mosbahi, B., Driss, Z. et al. (2021). Performance improvement of a Savonius water rotor with novel blade shapes. Ocean Engineering, 237(1), 109611. [Google Scholar]
15. Hashem, I., Zhu, B. S. (2021). Metamodeling-based parametric optimization of a bio-inspired Savonius-type hydrokinetic turbine. Renewable Energy, 180(6), 560–576. [Google Scholar]
16. Wang, W., Song, B. W., Mao, Z. Y., Tian, W. L. (2019). Optimization of Savonius wind turbine impeller with bilateral contour. Journal of Harbin Engineering University, 40(2), 254–259. [Google Scholar]
17. Shashikumar, C. M., Vijaykumar, H., Vasudeva, M. (2021). Numerical investigation of conventional and tapered Savonius hydrokinetic turbines for low-velocity hydropower application in an irrigation channel. Sustainable Energy Technologies and Assessment, 43, 100871. [Google Scholar]
18. Shashikumar, C. M., Honnasiddaiah, R., Hindasageri, V., Madav, V. (2021). Studies on application of vertical axis hydro turbine for sustainable power generation in irrigation channels with different bed slopes. Renewable Energy, 163, 845–857. [Google Scholar]
19. Khani, M. S., Shahsavani, Y., Mehraein, M., Kisi, O. (2023). Performance evaluation of the Savonius hydrokinetic turbine using soft computing techniques. Renewable Energy, 215, 118906. [Google Scholar]
20. Wu, Y. Z., Guang, W. L., Tao, R., L, J., Xiao, R.F. (2023). Dynamic mode structure analysis of the near-wake region of a Savonius-type hydrokinetic turbine. Ocean Engineering, 282(1), 114965. [Google Scholar]
21. Wang, X. L., Zhu, Z. Q., Liu, Z., Wu, Z. C. (2006). Bi-point/bi-objective optimization design of ailfoil using N-S equations. Journal of Beijing University of Aeronautics and Astronautics, 32(5), 503–507. [Google Scholar]
22. Dong, X., Liu, X. M. (2019). Bi-objective topology optimization of asymmetrical fixed-geometry microvalve for non-Newtonian flow. Microsystem Technologies Micro and Nanosystems-Information Storage and Processing Systems, 25(6), 2471–2479. [Google Scholar]
23. Chan, C. M., Bai, H. L., He, D. Q. (2018). Blade shape optimization of the Savonius wind turbine using a genetic algorithm. Applied Energy, 213(6), 148–157. [Google Scholar]
24. Jia, R. Y., Xia, H. J., Zhang, S., Su, W. G., Xu, S. H. (2022). Optimal design of Savonius wind turbine blade based on support vector regression surrogate model and modified flower pollination algorithm. Energy Conversion and Management, 270(5), 116247. [Google Scholar]
25. Mohamad, B., Shahram, D., Jamal, S. (2019). Design optimization of a centrifugal pump using particle swarm optimization algorithm. International Journal of Fluid Machinery and Systems, 12(4), 322–331. [Google Scholar]
26. Oyama, A., Liou, M. S. (2002). Multiobjective optimization of rocket engine pumps using evolutionary algorithm. Journal of Propulsion and Power, 18(3), 528–535. [Google Scholar]
27. Wu, G. W., Wu, H., Wang, X. Y., Zhou, Q. W., Liu, X. M. (2018). Tidal turbine array optimization based on the discrete particle swarm algorithm. China Ocean Engineering, 32(3), 358–364. [Google Scholar]
28. Han, Z., Wu, T. (2008). Optimal design of wind turbine blades based on genetic algorithm. Journal of Power Engineering, 28(6), 955–958. [Google Scholar]
29. Lu, J. H., Zhang, F. F., Tao, R., Li, X. Q., Zhu, D. et al. (2023). Optimization of runner and vane blade angle of an oscillating water column based on genetic algorithm and neural network. Ocean Engineering, 284(4), 115257. [Google Scholar]
30. Chang, H., Shi, W. W., Li, W., Liu, J. R. (2019). Energy loss analysis of novel self-priming pump based on the entropy production theory. Journal of Thermal Science, 28(2), 306–318. [Google Scholar]
31. Su, X., Jin, W., Zu, Z., Li, Z., Jia, H. (2021). Performance characteristics and energy loss analyses of a high-speed centrifugal pump with straight blades. Journal of Applied Fluid Mechanics, 14(5), 1377–1388. [Google Scholar]
32. Ghorani, M. M., Haghighi, M. H. S., Maleki, A. (2020). A numerical study on mechanisms of energy dissipation in a pump as turbine (PAT) using entropy generation theory. Renewable Energy, 162(1), 1036–1053. [Google Scholar]
33. Wang, Z. L., Luo, W., Zhang, B. W., Asomani, S. N., Xu, J. et al. (2022). Performance analysis of geometrically optimized PaT at turbine mode: A perspective of entropy production evaluation. Proceedings of the Institution of Mechanical Engineers, Part C: Journal of Mechanical Engineering Science, 236(24), 11446–11463. [Google Scholar]
34. Sakamoto, S., Murakami, S., Mochida, A. (1993). Numerical study on flow past 2D square cylinder by large eddy simulation: Comparison between 2D and 3D computations. Journal of Wind Engineering and Industrial Aerodynamics, 50, 61–68. [Google Scholar]
35. Franchina, N., Persico, G., Savini, M. (2019). 2D-3D computations of a vertical axis wind turbine flow field: Modeling issues and physical interpretations. Renewable Energy, 136(8), 1170–1189. [Google Scholar]
36. Nakajima, M., Iio, S., Ikeda, T. (2008). Performance of Savonius rotor for environmentally friendly hydraulic turbine. Journal of Fluid Science and Technology, 3(3), 420–429. [Google Scholar]
Cite This Article
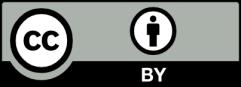
This work is licensed under a Creative Commons Attribution 4.0 International License , which permits unrestricted use, distribution, and reproduction in any medium, provided the original work is properly cited.