Open Access
ARTICLE
Analysis of Multiple Annular Pressure in Gas Storage Well and High-Pressure Gas Well
1
School of Petroleum Engineering, China University of Petroleum (East China), Qingdao, 266580, China
2
Tarim Oilfield Company, PetroChina, Korla, 841000, China
3
CNPC Research Institute of Safety and Environment Technology, Beijing, 102206, China
4
Research Institute of Petroleum Exploration & Development, PetroChina, Beijing, 100083, China
* Corresponding Authors: Jinsheng Sun. Email: ; Bo Zhang. Email:
(This article belongs to the Special Issue: Simulation of Flow and Transport Problems in Petroleum Engineering)
Energy Engineering 2023, 120(1), 35-48. https://doi.org/10.32604/ee.2022.022867
Received 30 March 2022; Accepted 25 May 2022; Issue published 27 October 2022
Abstract
In gas storage or high-pressure gas wells, annular pressure is an unavoidable threat to safe, long-term resource production. The more complex situation, however, is multiple annular pressure, which means annular pressure happens in not only one annulus but two or more. Such a situation brings serious challenges to the identification of well integrity. However, few researches analyze the phenomenon of multiple annular pressure. Therefore, this paper studies the mechanism of multi-annular pressure to provide a foundation for its prevention and diagnosis. Firstly, the multi-annular pressure is classified according to the mechanism and field data. Then the failure mechanism and function of the wellbore safety barriers in the process of passage formation are analyzed. Finally, some suggestions are put forward for identifying and controlling multi-annular pressure. The results show that gas storage wells and high-pressure gas wells have the conditions to generate pressure channels, which leads to the expansion of annular pressure from a single annulus to multiple annuli. The pressure channel is composed of the tubing string, casing string, and a cement mantle, and the failures among the three have causal and hierarchical relationships. According to the channel direction, it can be divided into two types: tubing-casing annulus to casing annulus and casing annulus to the tubing-casing annulus, of which the former is more harmful. Some measures can be considered to prevent pressure channeling, including improvement of cementing quality, revision of maximum allowable annular pressure, and suitable frequency of pressure relief.Keywords
Nomenclature
A | Cross section area of cement mantle, cm2 |
Hl | Height of gas column, m; Vgan is the volume of gas column, m3 |
Ke | Comprehensive permeability of cement, μm2 |
L | Length of cement mantle, cm; pe is gas reservoir pressure, MPa |
KT | Isothermal compressibility of annular liquid, MPa−1 |
Rs | Gas solubility of annular liquid, m3/m3 |
Ta | Gas temperature under standard conditions, K |
pl | Annular liquid column pressure, MPa |
pa | Gas pressure under standard conditions, MPa |
pan | Annular pressure, MPa |
panj−1 | Annular pressure in the iteration of (j − 1)th time, MPa |
Tan | Annular temperature, K |
Van | Annular volume, m3; Qjis gas rate in the iteration of j, m3/s |
Vg | Total gas volume invading into annulus under standard conditions, m3 |
Za | Gas compressibility factor under standard conditions, dimensionless |
Zan | Gas compressibility factor in annulus, dimensionless |
Gas viscosity under average pressure difference, mPa·s | |
Gas compressibility factor under average pressure difference, dimensionless | |
Δpa | Annular pressure, MPa |
ΔVa | Volume change of annulus, m3 |
ΔT | Increase of annular temperature, °C |
Annular pressure is an important issue in well quality due to its high risk and relatively wide distribution. Up to now, this phenomenon has been reported in deepwater wells [1–3], shale gas wells [4], geothermal wells [5], high-pressure and high-temperature gas wells [6,7], gas storage wells [8,9], steam injection wells [10] and gas injection wells [11]. Therefore, great effort has been devoted to related research, including mechanisms, predictions, management, and mitigation.
As shown in Fig. 1, the gas storage wells and high-pressure gas wells mainly consist of tubing, casing, cement, packer, and liner hangers. The space between tubing and casing is called the A annulus, and the space between two nearby casings are the B, C, D annulus, and so on. Regarding annular pressure, multiple-annular pressure in gas storage and high-pressure gas wells should be paid greater attention to. Multiple-annular pressure means annular pressure exits in two or more annuli simultaneously. The risks are reflected in three aspects.
Figure 1: Graph of high-pressure gas wells and gas storage wells
First is wellhead movement. According to modeling analysis [12], annular pressure can cause wellhead movement. Therefore, the wellhead movement would be higher when annular pressure exits in multiple annuli. Second, productivity and workover [13]. Generally speaking, the maximum allowable annular pressure (MAAP for short) decreases from the inner annulus to the outer annulus. Taking a high-pressure gas well, for example, the tubing-casing annulus (usually called A annulus) can bear 68.2 MPa while the annulus next to it (usually called B annulus) can only bear 35.0 MPa. If pressure channels connect A annulus and B annulus, the MAAP of the B annulus may be exceeded. As a result, the gas well has to shut-in, and workover becomes necessary, which leads to productivity loss and expensive costs; fire or groundwater pollution are such examples [14,15]. The outer annulus is usually isolated from the formation by cement mantle. Once the flammable gas enters the outer annulus through the pressure channel, the cement of the casing may lose its integrity under high annular pressure, and then the formation may be fractured. As a result, gas probably diffuses to the earth’s surface or into groundwater through fractures. So fire may happen, and groundwater may be polluted. For example [16], an explosion happened in Hutchinson Town on 17 and 18 January 2001. This was caused by gas leakage from Yaggy gas storage through casing and formation fracture.
As stated above, it is important to get a clear understanding of multiple annular pressure in gas storage wells and high-pressure gas wells, thus providing support for the indemnification and mitigation of multiple-annular pressure. However, annular pressure can be caused by different mechanisms, like thermal expansion and cement integrity failure or tubing leakage. But available research rarely studies multiple annular pressure; most studies appraise one kind of annular pressure in one annulus. For example, Maiti et al. [17] applied machine learning to study annular pressure caused by thermal expansion of drilling fluid. Zhang et al. [18] built a model to simulate the sustained pressure in A annulus caused by tubing leakage. Mainguy et al. [19] explained the annular pressure in A annulus by field data and engineering logging. Demirci et al. [20] proposed stopping annular gas migration by gravity fluid to mitigate annular pressure. Rocha-Valadez et al. [21] used annular pressure to determine the integrity of gas lift valves. Dong et al. [22] listed evaluation and control methods for annular pressure, including several annuli, but the annular pressure is caused by thermal expansion in deepwater wells.
These available researches are helpful in determining the sources of annular pressure, but it is difficult to judge multiple-annular pressure. Therefore, this paper conduct innovative work on the calcification and mechanism of multiple annular pressure. The cases are introduced to use field data to analyze multiple annular pressure. The risks are also compared and evaluated. The failure mechanism and function of wellbore safety barriers are analyzed to get the reason for the pressure channel. Combined with the conditions of gas storage, wells, and high-pressure gas wells, some suggestions are put forward for identifying and controlling multiple-annular pressure. This paper will reveal the formation mechanism of the pressure channels among multiple annuli. Theoretical and technical supports will also be provided for the identification of pressure channels and the prevention of multi-annular pressure.
Despite that the phenomena observed in the wellhead are similar, the mechanisms of annular pressure are all different and can be divided into four kinds. As shown in Table 1, the first kind is caused by the operation itself. Annular pressure would increase when the casing is compressed by pressure from an operation, like a fracture. This kind is not always considered a type because it would routinely be expected to disappear when the operation in question finishes. The other three kinds are also listed in Table 1, which also compares their characteristics.
2.1.1 Annular Pressure Caused by Thermal Expansion
Annular temperature would increase after the well is put into production because the production fluid brings heat from deeper within the formation. So the liquid in the annulus tends to expand but is then trapped by the annulus. Therefore, annular pressure increases to compress the liquid, thus keeping the volumes of liquid and annulus equal [23,24], as expressed by Eq. (1):
Annular pressure caused by thermal expansion is also called trapped annular pressure. For trapped annular pressure, there is no fluid exchange outside. It can be mitigated by many measures, including thermal-isolate fluid or pipe, releasing thermal-expanded liquid, and optimizing fluid properties. Moreover, the pressure would not rebound once it is mitigated.
2.1.2 Annular Pressure Caused by Cement Integrity Failure
One of the cement’s functions is to isolate the formation fluid. However, the cement is not exactly qualified for this function. Once the cement loses its integrity, the formation would invade the annulus along with the cement. This would be more severe for gas wells because gas is easy to channel. Many researchers use comprehensive permeability to present the failure degree of cement integrity, but it cannot reflect the complex process of fluid transportation within the cement. But comprehensive permeability can be used in the model of annular pressure caused by cement integrity. Eqs. (2) and (3) are examples of comprehensive permeability in the model [25,26].
As shown in Table 1, annular pressure caused by cement integrity failure takes cement as pressure channels. The gas is propelled by pressure differences between two ends of the cement. The pressure difference will be generated again once the annular pressure is released, so the annular pressure recovers. For this reason, it is called sustained annular pressure.
2.1.3 Annular Pressure Caused by Tubing String Leakage
According to field data, tubing leakage is the top reason for annular pressure in gas wells. The type of tubing leakage includes corrosion holes, thread leakage, packer leakage, and tubing body fractures. Sometimes, there are several leakage points in the tubing string. High-pressure gas enters the tubing-casing annulus through the leakage point(s) in the tubing string, so annular pressure increases accordingly. Usually, the small hole model is used to describe the leakage degree of tubing string leakage point, as expressed by Eq. (4) [18].
The gas leakage through the tubing string leakage point(s) is also propelled by pressure differences. Likewise, it will also recover after annular pressure is released, so it is also called sustained annular pressure. Moreover, the recovery speed is usually faster than the speed of annular pressure caused by the cement integrity failure.
2.2 Analysis of Multiple-Annular Pressure
2.2.1 Classification of Multiple-Annular Pressure
According to the analysis in Section 2.1, the gas storage well and high pressure well satisfy the conditions to generate annular pressure caused by thermal expansion, and cement integrity failure and tubing string leakage. First, annular protection liquid is injected into A-annulus to prevent tubing damage and corrosion in the gas storage and high-pressure wells. Meanwhile, the production rates of the gas storage well and high-pressure gas well are so high that the temperature of the annular liquid is increased correspondingly. For example, the maximum production rate of gas storage well can be as high as 200 × 104 m3/d. In some cases, B-annulus or C-annulus is also filled with liquid, although the cement is back to the surface. As a result, trapped annular pressure would be observed. Due to the critical downhole conditions, there is a shortage of conditions for the well barriers failure in the gas storage well and high pressure well, which will be analyzed in detail in the next section. Therefore, the multiple-annular pressure in the gas storage well and high-pressure gas well can be classified into seven types, as illustrated in Table 2. It can be found that not all types of multiple-annular pressure are caused by pressure channels among annuli.
Here, several types of multiple-annular pressure require extra explanation and analysis. Type 1, Type 2, Type 3, and Type 5 all contain annular pressure caused by thermal expansion, which the B-B test can diagnose a B-B test. B-B test is shorted for pressure bleeding-buildup test. The annular pressure caused by thermal expansion would not re-buildup after bleeding, while annular pressure caused by well integrity failure dose. Usually, the sustained annular pressure in A-annulus is caused by a tubing string leakage or leakages. Still, sometimes the integrity failures of production casing and the cement are also the potential reasons, just like Type 4. For example, sustained A-annular pressure appeared in the high-pressure wells of the Elgin and Franklin field in the UK’s North Sea [19]. The detection showed that the gas invaded into A-annulus through the production casing thread, which is caused by formation deformations and general reservoir depletion. the B-B test can diagnose Type 6. Because there is no pressure channel among annuli, the pressure in other annuli does not fluctuate remarkably when the pressure in one annulus is released. Type 7 is of the highest risk because the pressure from the tubing is high and may exceed MAAP of B-annulus.
2.2.2 Field Situation of Multiple-Annular Pressure
Two typical cases are used to illustrate the multiple-annular pressure in gas storage well and high-pressure gas wells. The first case is DZ gas storage in North China. This gas storage has 14 injection-production wells and five production wells. As shown in Table 3, multiple-annular pressure appears in 8 wells [27], which translates into 42.11% of the total wells. Annular pressure appears in the A-annulus and B-annulus of the DZ gas storage. This is mainly due to the poor cement quality and tubing leakage. Annular pressure in three annuli can also be found in gas storage well, such as Well S034-22 in S gas storage.
The other case is a high-pressure gas field in Northwest China. This gas field is faced with serious well integrity failure problems, and many advanced technologies have been previously conducted. Therefore, some gas wells are monitored in order to continue production under higher than desired annular pressure. Fig. 2 shows the annular pressure of a monitored gas well of T oilfield company. Three viewpoints can be obtained from Fig. 1. First, eight gas wells have the obvious phenomenon of multiple-annular pressure, which equals 80% of the monitored gas wells. Second, the high-pressure gas well is much more severe than the gas storage well; the pressure is high, to say the least. For example, the A-annular pressure in Well 5 is 44.56 MPa. Annular pressure exists in three annuli simultaneously in most monitored wells. Third, the A-annular pressure is usually higher than B-annular or C-annular pressure. This indicates that A-annular pressure may actually be the cause or reason for the generation of B-annular or C-annular pressure.
Figure 2: Multiple-annular pressure in monitored high-pressure gas wells
According to the above analysis, it can be noted that multiple-annular pressure is a critical issue regarding gas storage wells, as well as for high-pressure gas wells. The major kind of annular pressure is sustained annular pressure caused by a gas channel or channels. As a result, one of the reasons for the multiple-annular pressure is that pressure channels connect the annuli. Here, the pressure channel is analyzed in order to prevent multiple-annular pressure from building up.
3.1 Mechanisms of Pressure Channel and Failure
The well barriers between nearby annuli are tubing, casing, and cement, so the pressure channels also consist of them. The pressure channels can be divided into two kinds: the first consists of tubing, casings, and cement. The gas leaks from tubing through the leakage point, so A-annular pressure increases. Next, the gas invades into B-annulus through casing leakage points and through damaged cement, so B-annular pressure also increases, respectively. Likewise, the pressure can also expand to C-annulus. The other consists of just casing and cement. Gas invades into the casing annulus leading to greater, more sustained casing annular pressure. The gas then invades into the nearby annulus through casing leakage point(s), which can be either the tubing-casing annulus or nearby casing annulus. As a result, multiple-annular pressure appears in gas storage wells or high-pressure gas wells. To explain why the pressure channel generates then, it is necessary to understand how the related well barriers lose their integrity as well.
The integrity failure of tubing can be attributed to three factors, including load, environment, and tubing quality. The load includes the gravity of the tubing string, stimulation operation, tubing shock, annular pressure caused by thermal engineering, and formation deformation. The environment represents temperature and corrosive fluid. The tubing quality refers to its materials and manufacturing technology. Under the above factors or combination, the tubing may lose its integrity. Research showed that stress corrosion crack is a major type of tubing integrity failure that occurs in high-pressure gas wells. Other types are thread seal failures, tubing body deformation, etc. Fig. 3 is the tubing integrity failure in the gas well [6].
Figure 3: Leakage types of the tubing string in gas well
Casing integrity failure can also be subdivided into tubing body and thread failure. As shown in Fig. 4, the induced causes include casing strength factors and stress distribution, which also change with time and space. Among the casing strength factors, the quality parameters include the casing yield strength, elastic modulus, wall thickness, non-uniformity, and residual stress [28]. The environment also impacts casing strength, mainly including high temperature and pressure, wear, and corrosion [29,30]. The stress distribution is related to geological and engineering load [31,32], including the uncertainty of formation information, formation plastic flow, complex pressure strata, formation slip, reservoir compaction and annular pressure, high-pressure water injection, fracturing acid, etc.
Figure 4: Causes of casing integrity failure
The failure of cement integrity can be attributed to cement slurry properties, cement quality, perforation, corrosion, temperature, and pressure changes [33,34]. The typical failure types are fractures and micro-annulus [35–37]. During cement operation, the slurry may leak into formation, and the casing may be eccentric, so the cement quality may be poor. For example, from 2015 to 2016, 25 wells were completed in the aforementioned T oilfield, but the leakage of cement slurry happened in 15 of the 25 wells. Some particular types of cement slurry are not stable enough under high pressure and high temperature, so the cement rock’s strength decreases with time. The test shows that the strength of cement rock in KeS131 Well decreases to 10.8 from 36 MPa in just 28 days under temperatures of 170°C.
3.2 Case of Multiple-Annular Pressure
For gas storage, many of the wells are old wells. After years and years of production, these old wells have integrity problems to various degrees, like casing damage and cement integrity failure. Moreover, the gas storage well is serviced as an injection and production well. The production rate is usually very high, and the injection pressure is also very high. This leads to remarkable alternating loads and threatens the integrity of the tubing, casing, and cement. The high-pressure gas well is usually a deep or even ultra-deep well, so the temperature is high and the pressure system is complex. Deep wells need longer drilling times, and as a result, the casing may be quite worn. For example, the casing at a depth of 1600 m in DB301 was well worn. The reservoir contains H2S or CO2 in part of the high-pressure well, such as the Puguang gas field. Also, the tubing suffers from a rather complex load due to the combination of gravity, temperature, and the water h mer effect. All of the conditions mentioned above lead to the formation of one or more pressure channels.
Here, a deep gas well is selected as the case study to illustrate the pressure channel and multiple-annular pressure. This well is 6605 m deep. The reservoir pressure and temperature are 110 MPa and 147°C, which is a typical high-pressure and high-temperature gas well. This well was put into production on 28th, May 2016. At that time, A-annular pressure was 40.11 MPa, and B-annular pressure was 40.03 MPa. Tubing pressure was 87.30 MPa, and the highest production rate approached was 50 × 104 m3/d.
3.2.1 History of Annular Pressure
As shown in Fig. 5, A-annular pressure and B-annular pressure increased on 19th, August 2016, and flammable gas was released from A-annulus. Meanwhile, the liquid was released from B-annulus. Both A-annular pressure and B-annular pressure rebound quickly after release. On 7th, December 2016, flammable gas was also released from B-annulus. Through periodical releasing, B-annular pressure was controlled under 35 MPa. On 28th, Oct 2017, tubing pressure decreased sharply from 74.5 to 57.7 MPa. Meanwhile, A-annular pressure increased first and then decreased. This demonstrates that the tubing leakage was obviously aggravated. B-annular pressure and C-annular pressure then decreased with time. On 30th, Oct 2017, The pressures of A-annulus, B-annulus, and C-annulus were respectively 71.1, 42.6, and 16.6 MPa.
Figure 5: History of annular pressure
3.2.2 Analysis of Multiple-Annular Pressure
Multiple-annular pressure could be seen after the well was put into production. At that time, this was annular pressure caused merely by thermal expansion. Here is the analysis: first of all, no flammable gas was reported in the annulus. Secondly, the change of annular pressure was determined by the production rate; the annular pressure decreased when production stopped and then increased again after production was restarted once more. Third, the values of the annular pressure in the A-annulus and B-annulus were close, which is a characteristic of the annular pressure caused by thermal expansion. The multiple-annular pressure, therefore, was not of high risk at that time.
However, the situation changed on 19th, August 2016. The pressure channel formed, and annular pressure was sustained. The gas escaped from the tubing string and then entered B-annulus. Here is the analysis. First, the annular pressures were related to the tubing pressure. The sudden increase of A-annular pressure led to a sudden decrease in the tubing pressure. The pressure channel was tubing, casing, and cement. Second off, flammable gas was reported in A-annulus, as well as in B-annulus. The pressure channel was tubing, casing, and cement.
3.2.3 Pressure Channel and Proofs
The integrity failure of the tubing string was verified after the tubing string was lifted to the ground. Four leakage points were found in the tubing string. First is a hole at a depth of 1910 m. The second is the tubing deformation at the depth of 6093.86 m. The third is the tubing deformation at the 6381 m, which is under the packer. Forth is a longitudinal crack in the tubing body from 6381∼6391 m, which is also under the packer. However, the first two leakage points are the key for the sustained A-annular pressure. The casing cannot be lifted from the ground. However, the high pressure in A-annulus and poor cement quality create a very easy circumstance that could bring about eventual casing integrity failure. Moreover, the highest A-annular pressure was over 80 MPa, according to Fig. 5, while the lowest anti-burst strength of casing string is 79 MPa.
Cement integrity failure is also not difficult to explain. Besides the cement quality, the high pressure in A-annulus was already in the process of bringing about micro-annulus, even if the cement quality was perfect. For the pressure in C-annulus, the quality of cement behind 365.12/339.72 mm casing can be seen in Table 4. It can be seen that almost all the cement is poor or medium in quality. So the annular pressure was transferred to the C-annulus after increased B-annular pressure.
(1) Annular pressure can be divided into four particular kinds. They are each caused by operation; annular liquid thermal expansion, cement integrity failure, and tubing string leakage. Accordingly, multiple-annular pressure can be classified into seven types, but not all the types of multiple-annular pressure are caused by pressure channels. Type 7 is at the highest risk because the pressure from tubing is high and may exceed MAAP of the outer annului.
(2) The pressure channel mainly consists of the tubing string, casing, and cement. The integrity failure of the tubing can be attributed to three factors, including load, environment, and tubing quality. Casing integrity failure can also be divided into tubing body and thread failure. The failure of the cement integrity can be attributed to cement slurry properties, cement quality, perforation, corrosion, temperature, and pressure change.
(3) Field data shows that multiple-annular pressure is one of the most serious challenges for both gas storage and high-pressure wells. They have the conditions for the formation of pressure channels. This case study verified the analysis of multiple-annular pressure and pressure channels. To prevent multiple-annular pressure, however, some measures are recommended to prevent multiple-annular pressure, including improvement of cement quality, control of A-annular pressure fluctuation, and the greater enhancement of tubing string integrity.
Funding Statement: The project is supported by CNPC Forward-Looking Basic Strategic Technology Research Projects (Nos. 2021DJ6504, 2021DJ6501, 2021DJ6502 & 2021DJ0806) received by Bo Zhang, CNPC Science Technology Major Project (2021ZZ03) received by Bo Zhang.
Conflicts of Interest: The authors declare that they have no conflicts of interest to report regarding the present study.
References
1. Zhang, B., Guan, Z., Zhang, Q. (2015). Prediction and analysis on annular pressure of deepwater well in the production stage. Acta Petrolei Sinica, 33(8), 1012–1017. [Google Scholar]
2. da Veiga, A. P., Martins, I. O., Barcelos, J. G., Ferreira, M. V. D., Alves, E. B. et al. (2022). Predicting thermal expansion pressure buildup in a deepwater oil well with an annulus partially filled with nitrogen. Journal of Petroleum Science and Engineering, 208, 109275. DOI 10.1016/j.petrol.2021.109275. [Google Scholar] [CrossRef]
3. Zhang, B., Sun, B., Deng, J., Lu, N., Zhang, Z. et al. (2021). Method to optimize the volume of nitrogen gas injected into the trapped annulus to mitigate thermal-expanded pressure in oil and gas wells. Journal of Natural Gas Science and Engineering, 96, 104334. DOI 10.1016/j.jngse.2021.104334. [Google Scholar] [CrossRef]
4. Yin, F., Gao, D. (2015). Prediction of sustained production casing pressure and casing design for shale gas horizontal wells. Journal of Natural Gas Science and Engineering, 25, 159–165. DOI 10.1016/j.jngse.2015.04.038. [Google Scholar] [CrossRef]
5. Marbun, B. T. H., Ridwan, R. H., Nugraha, H. S., Sinaga, S. Z., Purbantanu, B. A. (2020). Casing setting depth and design of production well in water-dominated geothermal system with 330°C reservoir temperature. Energy Reports, 6, 582–593. DOI 10.1016/j.egyr.2020.02.013. [Google Scholar] [CrossRef]
6. Zhang, B., Xu, Z., Lu, N., Liu, H., Liu, J. et al. (2021). Characteristics of sustained annular pressure and fluid distribution in high pressure and high temperature gas wells considering multiple leakage of tubing string. Journal of Petroleum Science and Engineering, 196, 108083. DOI 10.1016/j.petrol.2020.108083. [Google Scholar] [CrossRef]
7. Li, C., Guan, Z., Zhang, B., Wang, Q., Xie, H. et al. (2021). Failure and mitigation study of packer in the deepwater HTHP gas well considering the temperature-pressure effect during well completion test. Case Studies in Thermal Engineering, 26, 101021. DOI 10.1016/j.csite.2021.101021. [Google Scholar] [CrossRef]
8. Ma, X., Zheng, D., Shen, R., Wang, C., Luo, J. et al. (2018). Key technologies and practice for gas field storage facility construction of complex geological conditions in China. Petroleum Exploration and Development, 45(3), 507–520. [Google Scholar]
9. Yan, X., Yan, H., Yan, Y. (2019). Abnormal physical characteristics of UGS annular pressure based on improved waha two-fluid model. Journal of China University of Petroleum (Edition of Natural Science), 43(5), 146–156. [Google Scholar]
10. Zhang, B., Guan, Z., Lu, N., Hasan, A. R., Wang, Q. et al. (2019). Trapped annular pressure caused by thermal expansion in oil and gas wells: A review of prediction approaches, risk assessment and mitigation strategies. Journal of Petroleum Science and Engineering, 172, 70–82. DOI 10.1016/j.petrol.2018.09.041. [Google Scholar] [CrossRef]
11. Guo, Y., Huang, Z., Yao, A., Qiu, Y., Kong, X. (2019). Analysis on tubing leakage caused by gas injection with pressure mutations when multiplephase transport. Chinese Journal of Applied Mechanics, 36(4), 920–923. [Google Scholar]
12. Aasen, J. A., Aadnoy, B. S. (2009). Multistring analysis of wellhead movement. Journal of Petroleum Science and Engineering, 66(3–4), 111–116. DOI 10.1016/j.petrol.2009.01.010. [Google Scholar] [CrossRef]
13. Lei, Q., Li, Y., Tao, L., Li, H., Gao, B. et al. (2020). Technical status and development direction of workover operation of PetroChina. Petroleum Exploration & Development, 47(1), 155–162. DOI 10.1016/S1876-3804(20)60015-5. [Google Scholar] [CrossRef]
14. Jordan, P. (2020). Chronic well leakage probability relative to basin and fluid characteristics. Proceedings of the National Academy of Sciences, 117(3), 1249–1251. DOI 10.1073/pnas.1919199116. [Google Scholar] [CrossRef]
15. Wisen, J., Chesnaux, R., Werring, J., Wendling, G., Baudron, P. et al. (2020). A portrait of wellbore leakage in northeastern British Columbia, Canada. Proceedings of the National Academy of Sciences, 117(2), 913–922. DOI 10.1073/pnas.1817929116. [Google Scholar] [CrossRef]
16. Zhao, L., Yan, Y., Wang, P., Yan, X. (2019). A risk analysis model for underground gas storage well integrity failure. Journal of Loss Prevention in the Process Industries, 62, 103951. DOI 10.1016/j.jlp.2019.103951. [Google Scholar] [CrossRef]
17. Maiti, S., Gupta, H., Vyas, A., Kulkarni, S. D. (2022). Evaluating precision of annular pressure buildup (APB) estimation using machine-learning tools. SPE Drilling & Completion, 37(1), 93–103. DOI 10.2118/196179-PA. [Google Scholar] [CrossRef]
18. Zhang, B., Lu, N., Guo, Y., Wang, Q., Cai, M. et al. (2022). Modeling and analysis of sustained annular pressure and gas accumulation caused by tubing integrity failure in the production process of deep natural gas wells. Journal of Energy Resources Technology, 144(6), 063005. DOI 10.1115/1.4051944. [Google Scholar] [CrossRef]
19. Mainguy, M., Innes, R. (2019). Explaining sustained “A”-annulus pressure in major north sea high-pressure/high-temperature fields. SPE Drilling & Completion, 34(1), 71–80. DOI 10.2118/194001-PA. [Google Scholar] [CrossRef]
20. Demirci, E., Wojtanowicz, A. K. (2016). Pilot size process visualization: Gravity fluid displacement method to stop annular gas migration. Journal of Natural Gas Science and Engineering, 29, 223–231. DOI 10.1016/j.jngse.2015.12.051. [Google Scholar] [CrossRef]
21. Rocha-Valadez, T., Hasan, A. R., Mannan, M. S., Crabtree, A., Kabir, C. S. (2015). Assessing integrity of the gas-lift valves by analyzing annular-pressure-transient response. Journal of Petroleum Science and Engineering, 133, 177–183. DOI 10.1016/j.petrol.2015.05.002. [Google Scholar] [CrossRef]
22. Dong, G., Chen, P. (2017). A review of the evaluation methods and control technologies for trapped annular pressure in deepwater oil and gas wells. Journal of Natural Gas Science and Engineering, 37, 85–105. DOI 10.1016/j.jngse.2016.11.042. [Google Scholar] [CrossRef]
23. Oudeman, P., Bacarreza, L. J. (1995). Field trial results of annular pressure behavior in a high-pressure/high-temperature well. SPE Drilling & Completion, 10(2), 84–88. DOI 10.2118/26738-PA. [Google Scholar] [CrossRef]
24. Zhang, B., Xu, Z., Guan, Z., Li, C., Liu, H. et al. (2019). Evaluation and analysis of nitrogen gas injected into deepwater wells to mitigate annular pressure caused by thermal expansion. Journal of Petroleum Science and Engineering, 180, 231–239. DOI 10.1016/j.petrol.2019.05.040. [Google Scholar] [CrossRef]
25. Zhang, B., Guan, Z., Zhang, Q., Han, D. (2015). Prediction of sustained annular pressure and the pressure control measures for high pressure gas wells. Petroleum Exploration and Development, 42(4), 616–619. DOI 10.1016/S1876-3804(15)30051-3. [Google Scholar] [CrossRef]
26. Yan, W., Zhao, X., Yan, Y., Guan, Z. (2022). Casing annular pressure prediction based on annular channeling combination model. China Petroleum Machinery, 50(1), 27–33. [Google Scholar]
27. Liu, Y., Li, J. (2020). The analysis and countermeasures of intermediate casing pressure in the injection and production wells of domestic gas storage. 32th National Natural Gas Academic Conference in Chongqing, pp. 1–6. China. [Google Scholar]
28. Lin, Y., Deng, K., Sun, Y., Xia, T. (2016). Through-wall yield collapse pressure of casing based on unified strength theory. Petroleum Exploration and Development, 43(3), 506–513. DOI 10.1016/S1876-3804(16)30059-3. [Google Scholar] [CrossRef]
29. Mao, L., Cai, M., Wang, G. (2018). Effect of rotation speed on the abrasive–erosive–corrosive wear of steel pipes against steel casings used in drilling for petroleum. Wear, 410, 1–10. DOI 10.1016/j.wear.2018.06.002. [Google Scholar] [CrossRef]
30. Liu, S., Zheng, H., Zhu, X., Tong, H. (2014). Equations to calculate collapse strength of defective casing for steam injection wells. Engineering Failure Analysis, 42, 240–251. DOI 10.1016/j.engfailanal.2014.03.010. [Google Scholar] [CrossRef]
31. Xi, Y., Li, J., Liu, G., Cha, C., Fu, Y. (2018). Numerical investigation for different casing deformation reasons in weiyuan-changning shale gas field during multistage hydraulic fracturing. Journal of Petroleum Science and Engineering, 163, 691–702. DOI 10.1016/j.petrol.2017.11.020. [Google Scholar] [CrossRef]
32. Li, X., Gu, C., Feng, Y., Ding, Z. (2021). Numerical study of shear deformation of casings during hydraulic fracturing considering wellbore loading history. Petroleum Science Bulletin, 6(2), 245–261. [Google Scholar]
33. Zhao, C., Li, J., Liu, G., Zhang, X. (2019). Analysis of the influence of cement sheath failure on sustained casing pressure in shale gas wells. Journal of Natural Gas Science and Engineering, 66, 244–254. DOI 10.1016/j.jngse.2019.04.003. [Google Scholar] [CrossRef]
34. Xi, Y., Li, J., Liu, G., Tao, Q., Lian, W. (2019). Research into cement sheath integrity during multistage hydraulic fracturing in shale gas wells. Petroleum Science Bulletin, 4(1), 57–68. [Google Scholar]
35. Dong, X., Duan, Z., Qu, Z., Gao, D. (2019). Failure analysis for the cement with radial cracking in HPHT wells based on stress intensity factors. Journal of Petroleum Science and Engineering, 179, 558–564. DOI 10.1016/j.petrol.2019.04.062. [Google Scholar] [CrossRef]
36. Zhang, B., Guan, Z., Lu, N., Hasan, A. R., Xu, S. et al. (2018). Control and analysis of sustained casing pressure caused by cement sealed integrity failure. Offshore Technology Conference Asia in Kuala Lumpur, pp. 1–14. Malaysia. [Google Scholar]
37. Qu, L., Yang, H., Huang, Z., Wu, J., Huang, P. et al. (2020). Effect of trapped annular pressure on failure of cement sheath sealing. China Petroleum Machinery, 48(2), 80–84. [Google Scholar]
Cite This Article
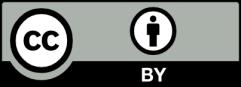
This work is licensed under a Creative Commons Attribution 4.0 International License , which permits unrestricted use, distribution, and reproduction in any medium, provided the original work is properly cited.