Open Access
ARTICLE
Microstructure and Hot Tearing Sensitivity Simulation and Parameters Optimization for the Centrifugal Casting of Al-Cu Alloy
1 School of Energy and Environmental Engineering (SEEE), University of Science and Technology Beijing (USTB), Beijing, 100083, China
2 Advanced Research Institute of Multidisciplinary Science (ARIM), Beijing Institute of Technology (BIT), Beijing, 100081, China
* Corresponding Author: Ruifeng Dou. Email:
(This article belongs to the Special Issue: Advanced Computer Technology for Materials Characterization, Properties Prediction, Design and Discovery)
Computers, Materials & Continua 2024, 80(2), 2873-2895. https://doi.org/10.32604/cmc.2024.052571
Received 07 April 2024; Accepted 14 July 2024; Issue published 15 August 2024
Abstract
Four typical theories on the formation of thermal tears: strength, liquid film, intergranular bridging, and solidification shrinkage compensation theories. From these theories, a number of criteria have been derived for predicting the formation of thermal cracks, such as the stress-based Niyama, Clyne, and RDG (Rapaz-Dreiser-Grimaud) criteria. In this paper, a mathematical model of horizontal centrifugal casting was established, and numerical simulation analysis was conducted for the centrifugal casting process of cylindrical Al-Cu alloy castings to investigate the effect of the centrifugal casting process conditions on the microstructure and hot tearing sensitivity of alloy castings by using the modified RDG hot tearing criterion. Results show that increasing the centrifugal rotation and pouring speeds can refine the microstructure of the alloy but increasing the pouring and mold preheating temperatures can lead to an increase in grain size. The grain size gradually transitions from fine grain on the outer layer to coarse grain on the inner layer. Meanwhile, combined with the modified RDG hot tearing criterion, the overall distribution of the castings’ hot tearing sensitivity was analyzed. The analysis results indicate that the porosity in the middle region of the casting was large, and hot tearing defects were prone to occur. The hot tearing tendency on the inner side of the casting was greater than that on the outer side. The effects of centrifugal rotation speed, pouring temperature, and preheating temperature on the thermal sensitivity of Al-Cu alloy castings are summarized in this paper. This study revealed that the tendency of alloy hot cracking decreases with the increase of the centrifugal speed, and the maximum porosity of castings decreases first and then increases with the pouring temperature. As the preheating temperature increases, the overall maximum porosity of castings shows a decreasing trend.Keywords
Cite This Article
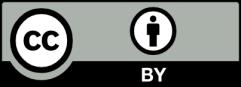
This work is licensed under a Creative Commons Attribution 4.0 International License , which permits unrestricted use, distribution, and reproduction in any medium, provided the original work is properly cited.