Open Access
ARTICLE
A Multi-Objective Optimization for Locating Maintenance Stations and Operator Dispatching of Corrective Maintenance
1 Department of Industrial Management, National Taiwan University of Science and Technology, Taipie, 106, Taiwan
2 Department of Industrial Engineering University of Gondar, Institute of Technology, Gondar, 196, Ethiopia
* Corresponding Author: Chao-Lung Yang. Email:
(This article belongs to the Special Issue: Metaheuristic-Driven Optimization Algorithms: Methods and Applications)
Computers, Materials & Continua 2024, 79(3), 3519-3547. https://doi.org/10.32604/cmc.2024.048462
Received 08 December 2023; Accepted 08 March 2024; Issue published 20 June 2024
Abstract
In this study, we introduce a novel multi-objective optimization model tailored for modern manufacturing, aiming to mitigate the cost impacts of operational disruptions through optimized corrective maintenance. Central to our approach is the strategic placement of maintenance stations and the efficient allocation of personnel, addressing a crucial gap in the integration of maintenance personnel dispatching and station selection. Our model uniquely combines the spatial distribution of machinery with the expertise of operators to achieve a harmonious balance between maintenance efficiency and cost-effectiveness. The core of our methodology is the NSGA III+ Dispatch, an advanced adaptation of the Non-Dominated Sorting Genetic Algorithm III (NSGA-III), meticulously designed for the selection of maintenance stations and effective operator dispatching. This method integrates a comprehensive coding process, crossover operator, and mutation operator to efficiently manage multiple objectives. Rigorous empirical testing, including a detailed analysis from a Taiwanese electronic equipment manufacturer, validated the effectiveness of our approach across various scenarios of machine failure frequencies and operator configurations. The findings reveal that the proposed model significantly outperforms current practices by reducing response times by up to 23% in low-frequency and 28.23% in high-frequency machine failure scenarios, leading to notable improvements in efficiency and cost reduction. Additionally, it demonstrates significant improvements in operational efficiency, particularly in selective high-frequency failure contexts, while ensuring substantial manpower cost savings without compromising on operational effectiveness. This research significantly advances maintenance strategies in production environments, providing the manufacturing industry with practical, optimized solutions for diverse machine malfunction situations. Furthermore, the methodologies and principles developed in this study have potential applications in various other sectors, including healthcare, transportation, and energy, where maintenance efficiency and resource optimization are equally critical.Keywords
Cite This Article
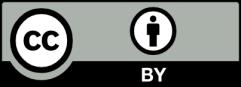
This work is licensed under a Creative Commons Attribution 4.0 International License , which permits unrestricted use, distribution, and reproduction in any medium, provided the original work is properly cited.