Open Access
ARTICLE
An IoT-Based Aquaculture Monitoring System Using Firebase
1 Department of Electrical Engineering, National Chin-Yi University of Technology, Taichung, 411030, Taiwan
2 Department of Informatics Management, Politeknik Negeri Sriwijaya, Palembang, 30139, Indonesia
3 Department of Information Technology, Takming University of Science and Technology, Taipei City, 11451, Taiwan
* Corresponding Author: Sung-Jung Hsiao. Email:
(This article belongs to the Special Issue: Development and Industrial Application of AI Technologies)
Computers, Materials & Continua 2023, 76(2), 2179-2200. https://doi.org/10.32604/cmc.2023.041022
Received 07 April 2023; Accepted 13 June 2023; Issue published 30 August 2023
Abstract
Indonesia is a producer in the fisheries sector, with production reaching 14.8 million tons in 2022. The production potential of the fisheries sector can be optimally optimized through aquaculture management. One of the most important issues in aquaculture management is how to efficiently control the fish pond water conditions. IoT technology can be applied to support a fish pond aquaculture monitoring system, especially for catfish species (Siluriformes), in real-time and remotely. One of the technologies that can provide this convenience is the IoT. The problem of this study is how to integrate IoT devices with Firebase’s cloud data system to provide reliable and precise data, which makes it easy for fish cultivators to monitor fishpond conditions in real time and remotely. The IoT aquaculture fishpond monitoring use 3 parameters: (1) water temperature; (2) pH water level; and (3) turbidity level of pond water. IoT devices use temperature sensors, pH sensors, and turbidity sensors, which are integrated with a microcontroller and Wi-Fi module. Data from sensor readings are sent to the Firebase cloud via the Wi-Fi module so that it can be accessed in real time by end users with an Android-based mobile app. The findings are (1) the IoT-based aquaculture monitoring system device has a low error rate in measuring temprature, pH, and turbidity with a percentage of 1.75%, 1.94% and 9.78%, respectively. Overall, the total average error of the three components is 4.49%; (2) in cost analysis, IoT-based has a cost-effectiveness of 94.21% compared to labor costs. An IoT-based aquaculture monitoring system using Firebase can be effectively used as a technology for monitoring fish pond conditions in real-time and remotely for fish cultivators that contribute to providing an IoT-based aquaculture monitoring system that produces valid data, is precise, is easy to implement, and is a low-cost system.Keywords
Indonesia is an archipelagic country, and one of its economic supports is the fisheries sector. Statistics Indonesia (BPS) stated that the production of the fisheries sector in Indonesia in 2022 reached 14.8 million tons [1]. This potential could be further increased with good management of aquaculture, which starts with selecting seeds, monitoring pond water, providing good fish feed, and the fish harvesting process [2]. The implementation of IoT technology could be an option in assisting the management of aquaculture, especially in monitoring fish pond water. There are many fish species in aquaculture of fresh water, including catfish (Siluriformes), which is a commodity in the fisheries sector that has high economic value. The condition of pond water for catfish is an important issue because catfish can grow optimally with the conditions of pond water temperature of 25°C~30°C, turbidity levels at 0~50 Nephelometric Turbidity Unit (NTU), and pH levels between 6~9 [3]. The IoT control system can be implemented to monitor the condition of fish pond water so that fish cultivators can find out as early as possible the quality of fish pond water. IoT integrates physical devices such as sensors and actuators that are connected to the internet to produce data that becomes valuable information for the users [4]. The process of processing data through the internet network provides convenience for humans without the need for human-to-human or human-to-computer interaction [5]. The IoT technology applied in this research is to build catfish pond water monitoring through 3 parameters: (1) pool water temperature; (2) pH pool water level; and (3) turbidity level of pond water. IoT devices use temperature sensors, pH sensors, and turbidity sensors, which are integrated with a microcontroller and Wi-Fi module.
In this study, the data from sensor readings are connected to real-time cloud data so that users can directly access the current conditions of the fishpond. The IoT device, which consists of a pH sensor, temperature sensor, and turbidity sensor that is integrated with a microcontroller and a Wi-Fi module, sends sensor data to the cloud continuously. The gateway acts as a connector between the IoT device and the real-time database so that data transmission occurs [6]. Real-time database hosted on a cloud-based platform that uses Firebase. The data contained in Firebase is then distributed to users to be accessible and provide the latest information about fishponds through an Android-based mobile application. Fig. 1 visualizes the interconnection between IoT devices and Firebase real-time databases.
Figure 1: IoT device and Firebase workflow
The related work in this study was conducted by Al-Mutairi et al. [7] who developed a smart monitoring and management system in fish farming. The system uses a set of sensors with real-time information from a mobile phone that is embedded in the tilapia fishpond. Javvaji et al. [8] integrate a microcontroller with a set of sensors for monitoring aquaculture by detecting temperature, dissolved oxygen, and pH sensors. Information from sensor readings is carried out in real time via the Thingspeak server connected to an Android-based mobile device. While Tamim et al. [9] use the ESP-12E as a microcontroller connector with a wireless network on an aquaculture system. The system is carried out in real-time using the MIT Inventor app to see the condition of the fishpond, which consists of the level of oxygen, temperature, and pH. In summary, Table 1 shows the analysis of the research carried out with the previous study.
In this study, we used Firebase cloud system data, which can be accessed directly by fish cultivators, to monitor real-time conditions of pH level, temperature, and turbidity. The system is built on Android with a user-friendly interface. This study also measures the accuracy of the sensors implemented and conducts a cost analysis of the efficiency of using the device. So this study contributes to developing an aquaculture monitoring system that delivers data that is valid, precise, easy to implement, and low-cost.
The development of Internet of Things (IoT) technology has increasingly become an interesting topic for discussion by researchers and in the industrial world. Fortino et al. [10] define IoT as a concept that integrates “smart objects” with the internet so that it is possible for them to communicate with one another. The IoT research field has been widely carried out in various aspects, Niaraki [11] categorizes it into four categories: infrastructure applications, environmental applications, consumer applications, and community applications. Meanwhile, the agriculture, plantation, and aquaculture sectors are included in the industry category, which is part of infrastructure applications. In his paper, Niaraki describes that IoT research implemented in the industry (agriculture, plantation, and aquaculture) has experienced a rapid increase since 2019. IoT is part of the industrial revolution 4.0 where researchers and practitioners collaborate with machine learning, big data and cloud computing, and Artificial Intelligence/Machine Learning [12]. The IoT domain has expanded, and there is now the term Internet of Underwater Things, which is a concept that integrates underwater autonomous vehicles (AUVs) and underwater wireless sensor networks (UWSNs) supported by Internet services. In general, there are 3 main layers in IoUT, i.e., the application and service layer, the networking layer, and the physical layer [13]. In the healthcare sector, IoT could be implemented in patient monitoring, increasing the efficiency with real-time data and improving service performance through remote monitoring [14]. IoT can also be implemented in remote health monitoring, which is integrated into a wireless body area network (WBAN) for monitoring critical patients [15]. The IoT development is combined with machine learning (ML) as implemented by Bhoi et al. [16] for an environmental monitoring system with features of carbon dioxide (CO2), humidity, temperature, and carbon monoxide (CO). In the field of agrotechnology, IoT plays a role in monitoring and increasing food production by integrating various sensors, actuators, and protocols as a tool of communication between the user and the system [17]. The main focus of IoT research in agrotechnology is on sensors used in IoT, IoT controllers, IoT communication standards, and IoT-based smart machinery [18]. While in the field of aquaculture, which is also related to this study in IoT, in general, there are two challenges: the first is common challenges that relate to how IoT devices interact with waters, while the second is specific challenges that relate to species and accessibility with water aquaculture objects [19]. In this study, IoT is the basic foundation of a system of communicating with users that has an impact on increasing fish productivity through an aquaculture monitoring system.
2.2 Aquaculture Monitoring Water System
The production from aquaculture is increasing, so innovation and technology are needed to support market needs. One of the technological implementations is the IoT in the Aquaculture Monitoring Water System. Chiu et al. [20] integrate sensor devices and Wi-Fi modules to control water quality, which is combined with deep learning random forest modeling to predict fish production potential, with the result being a smart aquaculture monitoring device. The implementation of temperature and pH sensors in the water monitoring system is carried out to see the actual conditions that have an impact on fish growth, using an Arduino Mega 2560 and Wi-Fi Module ESP8266 [21]. IoT-based Smart Aquaculture System (ISAS) has been developed by Tsai et al. [22] to control water quality automatically and replenish water to keep the growth of fish and shrimp stable. ISAS can provide automatic feeding through fuzzy rules, and the result is a shrimp survival rate that has increased by 33.3%. An AI buoy system combined with IoT has been developed to measure real-time data on salinity, water temperature, dissolved oxygen, and velocity in a low-cost and easy-to-build system [23]. The implementation of IoT in aquaculture provides benefits for fish cultivators to get environmental conditions in real-time, remotely, and accurately [24]. Hawari et al. [25] developed an IoT monitoring water system device with a background of climate and weather changes locally in Malaysia, which have caused a decrease in fish production levels. A communication system built on cloud portals and mobile devices that provide accurate and real-time information.
A microcontroller is a component with a minimalist size that serves as a system controller [26]. Microcontrollers are an integral part of helping humans work; there are 250 billion microcontrollers in electronic devices that are used daily [27]. Davis innovates the microcontroller as a low-cost dual-polarity high-voltage controller, which provides a stable high-voltage output in both positive and negative modes [28]. In the field of aquaculture technological innovation, microcontrollers are widely used as part of system development [29]. In its development, the microcontroller not only integrates sensors and actuators but furthermore can be integrated with cloud data and machine learning or deep learning [30]. Saha et al. [31] describe in their paper a microcontroller that can be integrated with deep learning to become an intelligent system. Whereas in this study, the role of the microcontroller is to control data transfer and monitoring from sensor devices to an output that can be accessed by end users.
The architectural system used in this study is represented in Fig. 2 below, where there are three main layers: (1) the physical layer, which consists of sensors and microcontroller devices; (2) the network layer, in the form of a Wi-Fi module that connects the physical layer with internet services; and (3) the application layer, in the form of a mobile-based application that can be accessed by end users to monitor the current conditions of the observed environment.
Figure 2: System architecture proposed
In Fig. 2 above, several sensors, i.e., a turbidity sensor, a pH sensor, and a temperature sensor, read the environmental conditions of catfish pond water. The reading data from the sensors is received by the microcontroller device and then sent to the data cloud via the Wi-Fi module as an accessibility connection that connects physical layer devices with internet services. Real-time data is uploaded to the cloud system and then accessed by end users via an Android-based application. End users can see the current condition of catfish pond water in the form of temperature conditions, level of turbidity, and level of pH (acidity or alkalinity). In Fig. 3, can be seen in detail the system flow of the Firebase cloud data as a real-time data storage medium from sensors that can be accessed by end users. IoT devices via Wi-Fi modules, communicate with cloud systems via the Message Queuing Telemetry Transport (MQTT) protocol. The MQTT protocol is one of the communication protocols that are commonly used for the IoT and uses standard ISO subscription publishing-based messages that work in the Transmission Control Protocol/Internet Protocol (TCP/IP), which does not have a special address either between the servers or with other connected devices. The MQTT protocol was specifically designed for machine-to-machine communication [32].
Figure 3: System of data cloud Firebase
MQTT works as a broker or server that has the function of filtering incoming messages and distributing them to clients who are interested in receiving them. Each client can be a publisher (message sender) or subscriber (recipient of messages). In this study, IoT devices work as clients that publish data from sensors that are received and sent to brokers. The MQTT protocol forwards real-time data to Firebase via a cloud gateway. Mobile applications for end users are developed based on Android, which requires the Rest API as a link between cloud Firebase data and end users. Rest stands for Representational State Transfer and is a type of software architecture. Rest represents a set of constraints that must be followed when developing applications on the internet. Application Programming Interface, or API, is a set of standards and protocols that integrate users with applications so that users can access and use the application software functions. Through the Rest API, developed applications can have well-organized interfaces and standardized procedures that are easy to represent. This also facilitates communication between devices and users.
Arduino UNO R3 is the latest variant of the Arduino UNO and a microcontroller device based on the IC ATMega 328. Fig. 4 represented the Arduino UNO that has 14 input and output pins, of which 6 can be used for pulse width modulation (PWM) output and 6 other pins for analog input. The 14 digital pins can be used as input or output via the pinMode(), digitalWrite(), and digitalRead() commands. Arduino is very popular because of its ease of communicating with computers through the Arduino Integrated Development Environment (IDE). The operating voltage in the pin is 5 volts and it can work with input voltages between 7 and 12 volts. The DC on each input or output pin is 40 mA, while the DC for the 3.3 V pin is 50 mA. The Arduino has 32 kB of flash memory on the ATMega328, of which 2 kB is for SRAM and 1 kB is for EPROM. The reset button on the Arduino can be used to reset the software running on the connected computer.
Figure 4: Arduno UNO R3
ESP8266 is a microchip device that functions as a Wi-Fi module and can be connected to an Arduino. It has embedded TCP/IP networking software. Memory capacity on the ESP8266 consists of 32 kB for instruction RAM, 32 kB for instruction cache RAM, 16 kB for ETS system-data RAM, and 80 kB for user-data RAM. There are 8 pins in the ESP8266 consisting of Ground (GND), Transmit data out (TX), which is also GPIO1, General purpose input/output No. 2 (GPIO2), chip power-down (CH_PD), General purpose input/output No. 0 (GPIO0), reset (RST), receive data in (RX), which is also GPIO3, and voltage 3.3 V as shown by Fig. 5.
Figure 5: ESP 8266
The turbidity sensor is SEN 0189 and works on the principle of using light to detect suspended particles in water. SEN 0189 is widely used to measure the quality of water, such as drinking water, tap water, water in ponds, and river water. SEN 0189 can operate at a voltage of 5 VDC with a maximum power of 40 mA. The operating temperature range of the SEN 0189 is 5°C~90°C and it can detect turbidity in water from 0~1000 NTU [33]. SEN 0189 has 8 pinouts, as represented by Fig. 6.
Figure 6: SEN 0189
The type of pH sensor used is SEN 0161 as represented in Fig. 7, which is an analog pH meter. SEN 0161 has a module power specification of 5 VDC and a pH measuring range of 0~14 pH. SEN 0161 can operate at a temperature of 0°C~60°C. The accuracy level of this device is +/− 0.1 pH (in 25°C) and has a response time of less than or equal to 1 min [34]. There are three pins: ground (GND), VCC, and output (OUT). The use of SEN 0161 is generally used to determine water quality in the field of aquaculture.
Figure 7: SEN 0161
The type of sensor used to measure temperature is the RTD PT100. RTD stands for resistance temperature detector. The RTD PT100 is made of platinum (PT) and can measure temperatures from 0°C to 100°C. RTD PT100 is made of water-resistant material, so it is very safe to use to measure water temperature. Fig. 8 represents the RTD PT100 sensor which has 3 pins, consisting of VCC, output (OUT), and ground (GND).
Figure 8: RTD PT100
Firebase is becoming a trend for software developers because of its reliability with “not only structured query language” or “NoSQL” data structures that can accommodate a variety of data with high volume characteristics, different sources, and multi-format data processing [35]. The data presented in Firebase is real-time data with a very fast response time. Developers generally use Firebase for authentication, cloud messaging, application programming interface (API) integration, and database management [36]. Firebase is widely used by researchers as a data transfer medium for IoT devices with user systems, such as in production natural parameter monitoring, which uses Firebase for data processing [37]. Currently, Firebase has 6 main services: (1) Cloud messaging and notifications; (2) Firebase authentication; (3) Firebase analytics; (4) Firebase real-time database; (5) Firebase hosting, and (6) Firebase cloud. This study uses the Firebase real-time database service as a communication tool between IoT devices and end users. Fig. 9 illustrated how Firebase connects the IoT device to the end user.
Figure 9: IoT Device is connected to end user through Firebase
Android Studio is a software developed by Google as an integrated development environment (IDE) for Android-based applications. The Android Studio programming language uses Java or Kotlin for the logic structure and extensive mark-up language (XML) for the user interface display. Android Studio is widely used by developers and researchers because it is an open-source platform based on the stability of the Gradle feature used during the build system, the Android Virtual Device (emulator) to execute run and debug applications, and support with several other software such as Google Cloud Messaging and Google App Engine. Android Studio has three main modules: the Android App Module, Library Module, and Google App Engine Module as shown in Fig. 10.
Figure 10: Android studio module
Fig. 11 shows a flowchart of a system built with several processes. The first stage begins with reading the data from the sensor in the fish pond. The data read is the value of temperature, the value of pH, and the value of turbidity. The microcontroller receives data from the sensor device, and then the Wi-Fi module connects the data to be stored on Firebase via the MQTT protocol. Next, the MQTT protocol distributes data into Firebase as real-time data that can be accessed directly by end users through Android-based applications.
Figure 11: System flowchart
Data collection was carried out by testing IoT devices in catfish ponds with a time range of 06.00 a.m. to 08.00 p.m. and a break every 2 h. The data that appears on the mobile app is real-time data from sensor readings accessed via Firebase. The dimensions of the fish pond are 5 m long, 3 m wide, and 1.5 m deep. Fish pond environmental temperatures range from 25°C to 30°C with occasional light rain. Data collection was carried out in as many as 8 categories of data collection time, as shown in Table 2 below.
Fig. 12 is a configuration of data collection where the sensor interacts directly with the fish pond. Turbidity sensors, pH sensors, and temperature sensors are connected directly to the microcontroller via a connector so that the data can be read by the microcontroller. The microcontroller is connected to the Wi-Fi module device, and data can be uploaded to Firebase.
Figure 12: Configuration of data collection environment
Fig. 13 is the actual condition of the catfish ponds, where there are several fish ponds. However, this study only focused on 1 fish pond, the orange line is the data collection area.
Figure 13: Actual catfish pond environment
To test the accuracy of the data generated by the sensor in an IoT device, a test is needed by comparing the output data from the sensor with data based on measurements of turbidity, pH, and temperature measuring instruments. This study used a temperature measuring pen to measure temperature, a portable turbidity meter to measure turbidity, and a digital pH meter to measure the pH level, as shown in Table 3 below.
Sensor measurement results are presented in the mobile app as illustrated in Fig. 14, where there is a main menu and a menu displaying sensor measurement results of real-time temperature, turbidity level, and pH level values. Fig. 14a is the main menu display of the water monitoring system app, and Fig. 14b is the sensor measurement results menu in real-time conditions. In the main menu, there are two buttons: water control and settings. The water button opens the control menu page, which contains the results of the real-time condition of fishpond monitoring, which consists of temperature, pH level, and turbidity level. On the result menu page, apart from displaying the real-time conditions of the fishpond, there is also a “back” button to return to the main menu.
Figure 14: Mobile application user interface
The implementation of the fishpond real-time condition measurement can be seen in Fig. 15, with data collection times at 06.00 a.m. and noon. In each figure, there is a change in the condition of the pH level, temperature, and turbidity; at 06.00 a.m., the pH level was 7.0, the temperature was 25.3°C, and the turbidity was 19.9. Whereas at noon, the three parameters experienced an increase with values of 7.0, 27.9°C, and 21.1, respectively. Likewise, in Fig. 16, the data was taken at 02.00 p.m. and 06.00 p.m., with real-time data at 02.00 p.m. pH level of 7.00, temperature of 27.7°C, and turbidity of 21.1, while at 06.00 p.m. it decreased with values of 6.8, 25.2°C, and 20.5, respectively. Conditions read by IoT devices are real-time data with dynamic data conditions. This provides convenience and economic impact for users, especially fish cultivators. To provide solutions in aquaculture monitoring systems that are efficient, precise, and remotely accessible.
Figure 15: Condition results at 06.00 a.m (left side) and noon (right side)
Figure 16: Condition results at 02.00 p.m (left side) and 06.00 p.m (right side)
Real-time data is processed in the system using Firebase cloud data, as represented in Fig. 17. The results of sensor readings on the fishpond are uploaded to Firebase to become real-time data with conditions of pH, temperature, and turbidity.
Figure 17: Firebase real-time data condition
5.1 Temperature Measurement Results Analysis
Table 4 shows the measurement results of IoT devices and measurement tools, which consist of 8 specific time categories and are measured in Celsius (C). The highest measurement results for both IoT devices and measurement tools are at noon. When compared between the results of these two devices, the gap is not too high, while the highest measurement gap is in the time range at 06.00 am, where there is a 1.1°C difference between the results of measurements using measurement tools (24.2°C) and the results of IoT device measurements (25.3°C). As for the gap measurements at other specific times are less than 1°C, and if it is averaged, the gap between IoT devices and measurement tools is 0.4°C.
Visually, in Fig. 18, it can be seen that the gap between the IoT device (blue line) and the measurement results (red line) is not that significant. Between 10.00 a.m. and 12.00 p.m., both devices detected an increase in temperature and a decrease in temperature between 02.00 p.m. to 08.00 p.m.
Figure 18: Graphic of the temperature measurement result
5.2 pH Measurement Result Analysis
The measurement results of IoT devices and measurement tools for pH levels show a gap less than or equal to 0.3, as shown in Table 5. The highest gap at noon was 0.3, where IoT devices showed a pH value of 7.0, and measurement tools showed a pH value of 7.3. The highest accuracy in data collection was at 04.00 PM and 08.00 PM where both devices show a pH value of 7.0.
Fig. 19 is a graphic of the pH measurement result where at noon there was an increase in the pH level based on the measurement tool result. This was because at that hour it was time for fish feeding, so it increased the pH level in the pond. While the measurement results of IoT devices at 12.00 p.m. and 02.00 p.m. did not change, and had a gap of 0.3 lower than the results of the measurement tool.
Figure 19: Graphic of the pH measurement result
5.3 Analysis Turbidity Measurement Result
Turbidity level measurements were carried out using the Nephelometric Turbidity Unit (NTU). In Table 6, it can be seen that the turbidity measurement results through the IoT device produce the measurement values below through the measuring instrument. The highest gap between the two devices occurred between 08.00 a.m. and 10.00 a.m. with a value of 2.8 NTU. In aggregate, the average gap between IoT Devices and Measurement Tools is 2.2 NTU.
The graphical visualization is shown in Fig. 20 where the blue line shows the data generated by the IoT device and the red line shows the data generated by the measurement tool. In both devices there was an increase in turbidity at 12.00 p.m. and 02.00 p.m, this was because at that time it was the fish feeding schedule that increased the turbidity level in fish ponds.
Figure 20: Graphic of the turbidity measurement result
5.4 Analysis of Error Percentage
The error percentage calculation is performed by finding the absolute difference between the expected value (νE) which is the value resulting from the measurement tool result and the actual value observed (νA) which is the result of IoT devices, Eq. (1) is the percentage error formulation
Based on the results of calculating the error percentage which refers to the measurement results of IoT devices and measurement tools in Tables 3–5, the resulting average error percentage is represented in Table 7.
Table 7 above results in an average temperature error percentage of 1.75%; this indicates that the accuracy value of the temperature data generated by the IoT device is 98.25% (which is taken from 100% minus 1.75%). The pH error percentage shows 1.94%, which indicates an accuracy percentage of 98.06%. Meanwhile, the turbidity error percentage shows 9.78% or an accurate value of 90.22%. Of the three error percentage results above, the overall average error between temperature error percentage, pH error percentage, and turbidity error results in a percentage of 4.49%. From the percentage error, the level of accuracy can be measured with the Eq. (2):
where A is the percentage of accuracy with a 100% formulation minus
Cost analysis is carried out by conducting a comparative analysis using a labor-based. The elements that are calculated in the IoT device consist of (a) the use of electric power in units of watts and (b) the prediction of maintenance costs in one month. The electricity cost charged is standard in Indonesia at Indonesian Rupiah (IDR) 1,352 kilowatt-hours (kWh). Based on the conditions of the IoT device, the maximum consumption of electric power is 20 watts with full-day or 24-h usage. The consumption of electric power is 20 watts, so it is necessary to convert the unit cost of electricity into watts per hour (Wh). So the parameters used in the calculation is IDR 1.352 Wh. The formula used to calculate the daily electricity load is maximum power consumption multiplied by the number of hours of use, multiplied by the cost of electricity (IDR 1.352 Wh). In this case, 20 watts × 24 h × IDR 1.352 Wh results in a daily cost of IDR 648.96 for device usage. If calculated for a month (30 days), it generates IDR 19,468.8 for costs charged to IoT devices. However, using an IoT device requires additional maintenance costs; in this case, the maintenance charge for the device is IDR 50,000 per month. Meanwhile, for the use of daily labor, the standard cost in Indonesia is IDR 40,000 per day with a work duration of 1 to 2 h. If calculated for one month (30 days), it will generate a cost of IDR 1,200,000. Table 8 shows a comparison of the monthly costs incurred between the IoT device and the daily labor-based one.
In Table 8 above, it can be seen that there is a significant difference between aquaculture monitoring using IoT devices and labor-based, wherein monthly usage for IoT devices, taking into account maintenance costs, results in a cost of IDR 69,468.8. While labor-based, the total monthly fee is IDR 1,200,000. In terms of monthly cost effectiveness, IoT device-based aquaculture has a very high advantage when compared to labor-based. This can be calculated by the difference between labor-based and IoT devices which results in IDR 1,130,531. This means that the effective cost of IDR 69,468.8 (IoT device) is IDR 1,130,531 (labor-based), which is less than IDR 1,200,000. In terms of percentage, the effective value formula is divided by the original value (labor-based = IDR 1,200,000) and multiplied by 100% to produce 94.21%. So, the effective cost of IoT devices is 94.21% when compared to labor-based costs.
The application of IoT technology in the aquaculture area can make it beneficial for fish cultivators to monitor real-time conditions where several fish species are highly dependent on water conditions, including catfish (Siluriformes). This research has implemented an IoT device to monitor the condition of fish ponds with three parameters: temperature, pH level, and turbidity level. The technology is integrated with Firebase cloud data, which can be accessed directly in real-time via Android-based mobile apps for end users. From the results of IoT-based aquaculture monitoring system testing compared to measurement tools, through data collection that is divided into 8-time categories, it produces an average error for the temperature of 1.75%, the average error for pH level of 1.94%, and an average error for turbidity level of 9.78%. Overall the total average error of the three components is 4.49%, and at this level, the accuracy can be calculated as 100% minus 4.49%, resulting in an accuracy level of 95.51%. Meanwhile in cost analysis, where a comparative analysis was carried out between IoT device-based and labor-based aquaculture monitoring, the percentage of IoT device cost-effectiveness was 94.21% compared to labor-based. This shows that IoT devices are a low-cost technology to be implemented in an aquaculture monitoring system. So that this IoT-based aquaculture monitoring system can be effectively used as a technology in monitoring fish pond conditions in real-time and remotely for fish cultivators that contribute to providing an IoT-based aquaculture monitoring system that produces data that is valid, precise, easy to implement, and low-cost. As a further development, the integration of aquaculture can be carried out with several physical sensors that can observe fish activities, such as hungry fish conditions, as well as water conditions with other parameters such as dissolved oxygen (DO) or water conductivity sensors. In addition, this study can be combined with machine learning to produce not only real-time conditions but also recommendations for fish pond conditions, whether normal or not, whether fish are hungry or not, as well as other possible parameters that can be processed to provide decision recommendations.
Acknowledgement: This research was supported by the Department of Electrical Engineering at the National Chin-Yi University of Technology. The authors would like to thank the National Chin-Yi University of Technology, Takming University of Science and Technology, Taiwan, for supporting this research.
Funding Statement: The authors received no specific funding for this study.
Conflicts of Interest: The authors declare that they have no conflicts of interest to report regarding the present study.
References
1. BPS Statistics Indonesia, Statistical Yearbook of Indonesia 2022. Jakarta, Indonesia: BPS-Statistics Indonesia, 2022. [Online]. Available: https://www.bps.go.id/publication/2020/04/29/e9011b3155d45d70823c141f/statistik-indonesia-2020.html [Google Scholar]
2. S. Jaiswal, K. D. Rasal, T. Chandra, R. Praba, M. A. Iquebal et al., “Proteomics in fish health and aquaculture productivity management: Status and future perspectives,” Aquaculture, vol. 566, no. 739159, pp. 1–22, 2023. [Google Scholar]
3. H. Kartikaningsih, Y. Yahya, D. Setijawati and H. I. Fathoni, “The behavior of catfish traders on the food safety perspective in Malang markets, Indonesia,” Biodiversitas, vol. 23, no. 5, pp. 2270–2275, 2022. [Google Scholar]
4. Q. F. Hasan, “Internet of Things concept,” in Internet of Things A—Z: Technologies and Application, 1st ed. New Jersey, USA: John Wiley & Sons, pp. 7, 2018. [Google Scholar]
5. W. T. Sung and F. N. Fadillah, “Water quality monitoring using physiochemical sensors,” in Proc. Int. Symp. on Computer, Consumer and Control (IS3C), Taichung, Taiwan, pp. 440–443, 2020. [Google Scholar]
6. G. J. R. Kumar and K. Zaki, “IoT based system for monitoring and control of industrial process using real-time firebase database,” in Proc. 3rd Int. Conf. in Cimputational and Experimental Method in Mechanical Engineering, Greater Noida, India, pp. 020110-1–020110-6, 2021. [Google Scholar]
7. A. W. Al-Mutairi and K. M. Al-Aubidy, “IoT-based smart monitoring and management system for fish farming,” Bulletin of Electrical Engineering and Informatics, vol. 12, no. 3, pp. 1435–1446, 2023. [Google Scholar]
8. K. S. S. Javvaji and Md. A. Hussain, “Prototype of aquaculture using IoT technologies,” in Proc. 11th Int. Conf. on Computing and Networking Technology (ICCNT), Kharagpur, India, pp. 1–4, 2020. [Google Scholar]
9. A. T. Tamim, H. Begum, S. A. Shachcho, M. M. Khan, B. Yeboah-Akowuah et al., “Development of IoT based fish monitoring system for aquaculture,” Intelligent Automation & Soft Computing, vol. 32, no. 1, pp. 55–71, 2022. [Google Scholar]
10. G. Fortino and P. Trunfio, Internet of Things Based on Smart Objects: Technology, Middleware, and Applications. Switzerland: Springer, 2014. [Online]. Available: https://link.springer.com/book/10.1007/978-3-319-00491-4 [Google Scholar]
11. A. S. Niaraki, “Internet of Thing (IoT) review of review: Bibliometric overview since its foundation,” Future Generation Computer System, vol. 143, no. 5, pp. 361–377, 2023. [Google Scholar]
12. Z. Jan, F. Ahamed, W. Mayer, N. Patel and G. Grossman, “Artificial intelligence for industry 4.0: Systematic review of applications, challenges, and opportunities,” Expert System With Application, vol. 216, no. 119456, pp. 1–21, 2023. [Google Scholar]
13. E. S. Ali, R. A. Saeed, I. K. Eltahir and O. O. Khalifa, “A systematic review on energy efficiency in the Internet of Underwater Things (IoUTRecent approaches and research gaps,” Journal of Network and Computer Applications, vol. 213, no. 103594, pp. 1–22, 2023. [Google Scholar]
14. A. Rejeb, K. Rejeb, H. Treiblmaier, A. Appolloni, S. Alghamdi et al., “The Internet of Things (IoT) in healthcare: Taking stock and moving forward,” Internet of Things, vol. 22, no. 100721, pp. 1–23, 2023. [Google Scholar]
15. F. Aadil, B. Mehmood, N. Ul Hasan, S. Lim, S. Ejaz et al., “Remote health monitoring using IoT-based smart wireless body area network,” Computers, Materials & Continua, vol. 68, no. 2, pp. 2499–2513, 2021. [Google Scholar]
16. S. K. Bhoi, S. K. Panda, K. K. Jena, K. S. Sahoo, N. Z. Jhanjhi et al., “IoT-EMS: An Internet of Things based environment monitoring system in volunteer computing environment,” Intelligent Automation & Soft Computing, vol. 32, no. 3, pp. 1493–1507, 2022. [Google Scholar]
17. A. N. Fajar, R. Jayadi, J. Halim and B. Robertson, “Mobile application for agrotechnology systems using Internet of Things (IoT),” Journal of System and Management Science, vol. 12, no. 3, pp. 104–116, 2022. [Google Scholar]
18. V. R. Pathmudi, N. Khatri, S. Kumar, A. S. H. Abdul-Qawy and A. K. Vyas, “A systematic review of IoT technologies and their constituents for smart and sustainable agriculture applications,” Scientific African, vol. 19, no. e01577, pp. 1–14, 2023. [Google Scholar]
19. H. Rastegari, F. Nadi, S. S. Lam, M. Ikhwanuddin, N. A. Kasan et al., “Internet of Things in aquaculture: A review of the challenges and potential solutions based on current and future trends,” Smart Agriculture Technology, vol. 4, no. 100187, pp. 1–11, 2023. [Google Scholar]
20. M. C. Chiu, W. M. Yan, S. A. Bhat and N. F. Huang, “Development of smart aquaculture farm management system using IoT and AI-based surrogate models,” Journal of Agriculture and Food Research, vol. 9, no. 100357, pp. 1–11, 2022. [Google Scholar]
21. L. P. Rahayu, B. A. Kindhi, C. D. Pradika, F. I. Adhim, C. W. Priananda et al., “Design of pH control system and water recirculation in aquaponic cultivation using mamdani fuzzy logic control,” in Proc. ICAMIMIA, Surabaya, Indonesia, pp. 287–292, 2021. [Google Scholar]
22. K. L. Tsai, L. W. Chen, L. J. Yang, H. Shiu and H. W. Chen, “IoT based smart aquaculture system with automatic aerating and water quality monitoring,” Journal of Internet Technology, vol. 23, no. 1, pp. 177–184, 2022. [Google Scholar]
23. H. Y. Lu, C. Y. Cheng, S. C. Cheng, Y. H. Cheng, W. C. Lo et al., “A low-cost AI buoy system for monitoring water quality at offshore aquaculture cages,” Sensors, vol. 22, no. 4078, pp. 1–15, 2022. [Google Scholar]
24. L. B. Chen, Y. H. Liu, X. R. Huang, W. H. Chen and W. C. Wang, “Design and implementation of a smart seawater aquarium system based on Artificial Intelligence of Things technology,” IEEE Sensors Journal, vol. 22, no. 20, pp. 19908–19918, 2022. [Google Scholar]
25. H. F. Hawari and M. A. Hazwan, “Development of Iot monitoring system for aquaculture application,” in Proc. GEOCOST, Sarawak, Malaysia, pp. 330–334, 2022. [Google Scholar]
26. S. R. Rizvi, “Using CMOS integrated-circuit,” in Microcontroller Programming—An Introduction, 1st ed. Boca Raton, US: CRC Press Taylor & Francis Group, pp. 204–207, 2012. [Google Scholar]
27. R. Immonen and T. Hämäläinen, “Tiny machine learning for resource-constrained microcontrollers,” Journal of Sensors, vol. 2022, no. 7437023, pp. 1–11, 2022. [Google Scholar]
28. E. J. Davis and B. H. Clowers, “Low-cost arduino controlled dual-polarity high voltage power supply,” HardwareX, vol. 13, no. e00382, pp. 1–14, 2023. [Google Scholar]
29. A. Kamboj, P. Garg, D. Bansal, A. Sankar and M. Bukya, “Development of android app-based portable water quality testing device using arduino,” in Proc. ICRITO, Noida, India, pp. 1–4, 2021. [Google Scholar]
30. N. Elbeheiry and R. S. Balog, “Technologies driving the shift to smart farming: A review,” IEEE Sensor Journal, vol. 23, no. 3, pp. 1752–1769, 2022. [Google Scholar]
31. S. S. Saha, S. S. Sandha and M. Srivastava, “Machine learning for microcontroller-class hardware: A review,” IEEE Sensor Journal, vol. 22, no. 22, pp. 21362–21390, 2022. [Google Scholar]
32. T. K. Boppana and P. Bagade, “GAN-AE: An unsupervised intrusion detection system for MQTT networks,” Engineering Applications of Artificial Intelligence, vol. 119, no. 105805, pp. 1–12, 2023. [Google Scholar]
33. W. L. Hakim, L. Hasanah, B. Mulyanti and A. Aminudin, “Characterization of turbidity water sensor SEN0189 on the changes of total suspended solids in the water,” Journal of Physics: Conference Series, vol. 1280, no. 2, pp. 1–8, 2019. [Google Scholar]
34. R. Seetharaman, N. Nivetha, S. V. Dakshin, K. Anandan and R. R. Sreeja, “Arduino based system for domestic waste water management using pH sensor,” in Proc. I-SMAC, Dharan, Nepal, pp. 352–355, 2022. [Google Scholar]
35. A. B. Semma, M. Ali, M. Saerozi, M. Mansur and K. Kusrini, “Cloud computing: Google firebase firestore optimization analysis,” Indonesian Journal of Electrical Engineering and Computer Science, vol. 29, no. 3, pp. 1719–1728, 2023. [Google Scholar]
36. M. S. Aman Khan, A. R. Farabi and A. Iqbal, “What do firebase developers discuss about? An empirical study on stack overflow posts,” in Proc. NSysS, Cox’s Bazar, Bangladesh, pp. 65–74, 2022. [Google Scholar]
37. U. Ramani, R. Binisha, P. Rajasekaran, M. Vignesh, P. Malini et al., “Enhancement of embedded controller firebase database labview interactive IoT based production natural parameters monitoring,” in Proc. ICAISS, Trichy, India, pp. 1192–1197, 2023. [Google Scholar]
Cite This Article
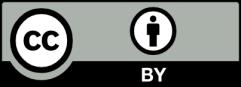
This work is licensed under a Creative Commons Attribution 4.0 International License , which permits unrestricted use, distribution, and reproduction in any medium, provided the original work is properly cited.