Open Access
ARTICLE
Industrial Recycling Process of Batteries for EVs
1 School of Engineering Technology, Al Hussein Technical University (HTU), Amman, 11831, Jordan
2 Department of Medical Instrumentation Techniques Engineering, Dijlah University College, Baghdad, Iraq
3 Department of Mechanical Engineering, College of Engineering, Taif University, Taif, 21944, Saudi Arabia
4 Department of Electrical Engineering, University of Engineering and Technology, Peshawar, 814, Pakistan
5 University of South-Eastern Norway, Bredalsveien 14, 3511 Hønefoss, Norway
* Corresponding Author: Dag Øivind Madsen. Email:
Computers, Materials & Continua 2023, 74(2), 4571-4586. https://doi.org/10.32604/cmc.2023.032995
Received 03 June 2022; Accepted 05 July 2022; Issue published 31 October 2022
Abstract
The growing number of decarbonization standards in the transportation sector has resulted in an increase in demand for electric cars. Renewable energy sources have the ability to bring the fossil fuel age to an end. Electrochemical storage devices, particularly lithium-ion batteries, are critical for this transition’s success. This is owing to a combination of favorable characteristics such as high energy density and minimal self-discharge. Given the environmental degradation caused by hazardous wastes and the scarcity of some resources, recycling used lithium-ion batteries has significant economic and practical importance. Many efforts have been undertaken in recent years to recover cathode materials (such as high-value metals like cobalt, nickel, and lithium). Regrettably, the regeneration of lower-value-added anode materials (mostly graphite) has received little attention. However, given the widespread use of carbon-based materials and the higher concentration of lithium in the anode than in the environment, anode recycling has gotten a lot of attention. As a result, this article provides the most recent research progress in the recovery of graphite anode materials from spent lithium ion batteries, analyzing the strengths and weaknesses of various recovery routes such as direct physical recovery, heat treatment recovery, hydrometallurgy recovery, heat treatment-hydrometallurgy recovery, extraction, and electrochemical methods from the perspectives of energy, environment, and economy; additionally, the reuse of recycled anode mats is discussed. Finally, the problems and future possibilities of anode recycling are discussed. To enable the green recycling of wasted lithium ion batteries, a low energy-consuming and ecologically friendly solution should be investigated.Keywords
The electric vehicle (EV) market has boomed in recent years. In 2017, global EV sales exceeded 1 million for the first time [1], and according to EV30@30 according to the plan, by 2030, the annual sales of electric vehicles will reach 44 million [2]. As shown in Fig. 1, the EV batteries that will be phased out in 2030 will reach 100–120 Giga-Watt-Hour (GW⋅h), and their capacity is roughly equivalent to the current annual battery output [3]. Lithium-ion batteries usually contain high-risk substances such as Ni, Co, and phosphide. If ordinary garbage disposal methods (such as landfill, incineration, etc.) are adopted, it will cause serious pollution to the environment. In addition, most of the metal elements contained in waste lithium-ion batteries are relatively scarce in my country, and imports rely on high resources, so the recycling of battery materials has extremely high environmental protection and economic value.
Figure 1: Evolution of the batteries in EVs [3]
Compared with cathode materials (LiCoO2 [4–6], LiFePO4 [7–9], LiNixCoyMnzO2 [10–12]) recycling, anode materials (mainly graphite) are rarely used due to their relatively low added value received attention [13–17]. It is worth noting that waste lithium-ion batteries contain 12% to 21% graphite [18], and countries that do not produce graphite or have low graphite reserves, such as the United States and the European Union, regard flake graphite as a key material [19,20]. The cost of preparing ordered graphite is high and requires calcination at high temperature (2500°C∼3000°C) in an inert atmosphere, which makes graphite as expensive as some metals in the positive electrode [21]. In addition, in traditional lithium-ion battery recycling methods, the anode is burned at high temperature or discarded as filter residue, which will lead to particulate pollution and aggravate the greenhouse effect [22,23]. Moreover, the toxicity of electrolytes and additives, the lithium content in the anode that is much higher than the environmental abundance [24], and the increase in the demand for graphite (the increase in graphite demand is estimated to be 250,000 tons per year) [25] have prompted the recycling of anode materials became an inevitable trend.
Although there are many review articles on lithium-ion battery recycling, the research on anode materials is rarely mentioned [26–28]. In this review, combined with the literature in recent years, a comprehensive summary of the graphite anode regeneration methods and their applications for lithium-ion batteries is carried out, and a comprehensive evaluation of the energy, environment, resource cost and performance involved in various graphite recycling methods is carried out which pointed out the current recycling process of graphite anode material reuse challenges and solutions, with a view to providing a reference for researchers working in this field.
2 Recycling Method of Negative Electrode Material
The main components of the graphite anode materials for commercial waste lithium-ion batteries include graphitic carbon materials, lithium salts, and a small amount of electrolytes, binders and conductive agents. As shown in Fig. 2, the current industrial waste lithium-ion battery recycling methods mainly include pyrometallurgy, hydrometallurgy, and a combination of pyrometallurgy and hydrometallurgy. However, the recovered products are mainly positive precious metals and their alloys, and the recycling of graphite negative electrodes is not considered. For example, graphite is directly burned in the pyrometallurgical process, and the hydrometallurgical process is discarded as filter residues [29]. Therefore, researchers have developed new routes for the recovery of graphite anode materials, including direct physical recovery, heat treatment, hydrometallurgy, combination of heat treatment and hydrometallurgy, extraction and electrochemical recovery. The development route of various recovery methods is shown in Fig. 3.
Figure 2: Industrial recycling process
Figure 3: Evolution of recovery methods
There was research on the use of hammer crushing, vibrating screening and air separation combined process to achieve direct recovery of copper and carbon powder [30]. Subsequently, reference [31] used diesel as the collector and methyl isobutyl methanol as the foaming agent to conduct an experimental study on the flotation of graphite anode, and the recovery rate could reach 98.56%. Then, they reported a series of studies on the recovery of LiCoO2 and graphite by flotation. First, the Fenton additive flotation method was used, and the H2O2/Fe2+ was 40/280 and the liquid-solid ratio was 99% [32]. The electrode material was modified under the optimum parameters of 25/100, and then separated by flotation, the recovery rate of LiCoO2 reached 98.99%. The team then studied grinding flotation technology. The wettability of LiCoO2 and graphite was different by grinding. The concentrate grades of LiCoO2 and graphite after flotation were 97.13% and 73.56%, respectively, and the recoveries were 49.32% and 73.56%, respectively [33]. In addition, the organic binder can be removed by the pyrolysis-ultrasonic-assisted method, which increases the recovery rate of LiCoO2 from 74.62% to 93.89% [34]. A schematic diagram of the recovery of this method is shown in Fig. 4. The flotation method realizes the simultaneous recovery of LiCoO2 positive electrode and graphite negative electrode material, which simplifies the recovery process, is simple to operate, efficient, and has little pollution. However, the graphite recovered by this method contains many impurities, and the purity is difficult to meet the requirements of commercial graphite negative electrode materials (battery 9% and grade graphite mass fraction higher than 99.9%).
Figure 4: Graphical representation of recovery process using pyrolysis-ultrasonic-assisted method
The prelithiated graphite was obtained by removing the organic electrolyte and the binder polyvinylidene fluoride (PVDF) with pyrrolidone (NMP), respectively. The first cycle capacity loss of the prelithiated graphite anode is reduced by about 10% (compared to the unused graphite anode) due to the retention of lithium-containing species that reduces the consumption of Li+ during the formation of the solid electrolyte interface (SEI) film. This method opens up a new avenue for the recycling of graphite anode materials [35].
To reduce the consumption of chemicals and energy, reference [36] proposed a simple, green water treatment method to recover graphite from spent LiFePO4/graphite batteries. Due to the self-discharge during battery cycling, the corrosion of hydrofluoric acid, the dissolution of transition metal elements in the positive electrode and the deposition on the negative electrode material, the composition of the SEI film on the waste graphite negative electrode is very complicated [37,38]. Through water treatment, the residual Li in graphite reacts with water to generate H2, which can separate the complex SEI film from graphite. Removal of the impurity results in the opening of Li+ transport channels, thereby restoring the electrochemical activity of graphite (345 mAhg−1 capacity after 100 cycles). Water treatment technology does not require high-temperature operation, nor does it consume harmful chemicals, which is economical and environmentally friendly. In addition, the filtrate of water treatment can be recycled until the dissolved lithium salt is saturated, and then the lithium salt is recovered by precipitation method. However, this technique does not consider the removal of toxic binders such as polyvinylidene fluoride (PVDF).
Since the surface morphology and composition of graphite anodes change with the number of cycles, reference [39] prepared reconstituted graphite with sp2 + sp3 carbon surface by microwave exfoliation and reconstituted graphite on carbon surface (RG) method and neural network-like amorphous sp2 + sp3 carbon-coated graphite (AC@G). The results show that surface reforming is beneficial to improve the capacity of modified graphite, and the reversible capacities of RG and AC@G after 100 cycles at 0.1 C are 409.7 and 420.0 mA⋅h⋅g−1, respectively. However, it is worth mentioning that due to the presence of surface activated carbon, the voltage plateau of AC@G increases sharply when the capacity is close to 300 mAhg−1, resulting in a higher average discharge potential. Moreover, the porous structure will prevent a part of the intercalated lithium from being extracted, resulting in a decrease in the Coulombic efficiency in the first week.
Reference [40] took a novel, green approach to efficiently regenerate graphite, which consists of two key steps. The recovered anode material was first heat-treated in air for 1 h to remove the residual conductive agent acetylene black (AB), binder styrene-butadiene rubber (SBR) and thickener sodium carboxymethyl cellulose (CMC), and then used phenolic resin The graphite surface was coated with 6.885% pyrolytic carbon at 950°C under N2 atmosphere. The graphite coated with pyrolytic carbon exhibited an initial charge capacity of 347.2 mAhg−1 and a coulombic efficiency of 92.07%, and all technical indicators exceeded those of the same type of mid-grade graphite, satisfying requirements for reuse. In addition, the method has simple equipment and high quality of recovered graphite, which is expected to realize large-scale application.
Reference [41] successfully regenerated pure graphite from waste lithium-ion batteries through a simple high-temperature smelting and screening process, as shown in Fig. 5. First, the negative electrode sheet was reacted at 1400°C for 4 h under N2 atmosphere to melt the copper foil into spherical particles and separate from graphite. Then the copper and graphite are separated from each other by ultrasonic vibration and sieving, and 80.00% copper larger than 200 mesh and 77.53% graphite smaller than 300 mesh can be recovered. The purity of the recovered graphite is higher than 99.5%, and it has a higher specific capacity and a stable low-voltage discharge platform. However, this method consumes a lot of energy, and at a temperature of 1400°C, all the lithium salts are volatilized, resulting in a waste of precious lithium resources.
Figure 5: Smelting and serving based industrial recycling process
High-temperature heat treatment can effectively repair the structure of graphite and remove impurities, but this method has high energy costs, and the decomposition of polymers will produce toxic gases, and the recovered materials are single.
2.3 Hydrometallurgical Recovery
Studies have shown that the waste anode also contains lithium (30.07 mg g−1), which is much higher than the environmental abundance, and most of them are composed of inorganic substances Li2O, LiF, Li2CO3 and organic substances ROCO2Li, CH3OLi, (the form of ROCO2Li)2 exists in the SEI film. A small part exists in the graphite voids in the form of Li elemental substance. Among them, Li2O, ROCO2Li and CH3OLi are water-soluble, while other substances are almost insoluble in water [42]. Based on this behavior, the research developed a hydrochloric acid leaching process to recover lithium in the anode. The results show that under the experimental conditions of 3 mol.L−1 hydrochloric acid, 80°C temperature, 20 g.L−1 solid-liquid ratio, and 90 min reaction time, the leaching efficiency of lithium is as high as 99.4%. Recently, Reference [43] used sulfuric acid solution as the leaching agent to study the effect of sulfuric acid concentration, leaching time, and leaching temperature on the leaching of lithium from the anode sheet and the separation of graphite and copper foil. The results show that when the leaching time is 5 min and the sulfuric acid concentration is 0.9 mol.L−1, the copper foil and graphite can be completely separated. When the leaching temperature is 40°C, the sulfuric acid concentration is 1.8 mol.L−1, the leaching time was 50 min and the solid-liquid ratio was 60 g.L−1, and almost all the lithium in the graphite entered the solution.
The hydrometallurgical process has a low operating temperature and can effectively recover lithium salts in the negative electrode. However, due to the presence of insoluble lithium salts such as LiF, the process consumes a large amount of strong acids (sulfuric acid, hydrochloric acid) and produces more toxic hydrofluoric acid. Therefore, an effective solution for hydrometallurgical recycling is to combine the recycling of positive and negative electrodes, which can greatly simplify the recycling process and reduce secondary pollution caused by waste acid.
2.4 Combined Heat Treatment and Hydrometallurgical Recovery
Reference [44] removed all residual cathode material, other metal impurities, most binders and alumina through sulfuric acid leaching and molten NaOH calcination steps, and regenerated high-quality graphite powder, which could reach 377.3 at 0.1 C The reversible specific capacity of mA⋅h⋅g−1. This process merges the negative electrode recycling into the positive electrode recycling process, which greatly reduces the cost of battery separation and simplifies the recycling process. In addition, reference [45] adopted a two-step calcination and acid leaching method to achieve the recovery of graphite, Cu, Li and Al. Under 1.5 mol⋅L−1 hydrochloric acid, S/L atomic ratio of 100 g⋅L−1 and 1 h leaching time, 100% Cu, Li and Al can be leached out. By adjusting the pH value from 7 to 9, 99.9% Cu and Al can be extracted. After that, more than 99% of Li was recovered by adding Na2CO3 by precipitation method. The regenerated graphite also has excellent electrochemical properties. This technology is a sustainable method to achieve anode graphite regeneration and recovery of Li and Cu. Reference [46] removed the impurities by two-step sulfuric acid leaching and then calcined at 1500°C to obtain regenerated graphite. The schematic diagram of recovery is shown in Fig. 6. At high temperature, graphite is reduced to its original structure with a mass fraction of up to 99.6%, and exhibits an initial charge capacity of 349 mA h g−1. The generated waste acid filtrate can be fed into the process of hydrometallurgical recovery of cathode materials, reducing secondary pollution and realizing lithium resource recovery.
Figure 6: Industrial recycling process using sulfuric acid curing-leaching combined with high-temperature calcination
The combination of heat treatment and hydrometallurgy is an economical and feasible technology to realize the efficient regeneration of graphite and recovery of lithium, and on the basis of solving the problem of waste acid pollution, this technology has great potential for commercialization in the future.
Another challenge for anode recycling is the disposal of the electrolyte. For digital waste lithium-ion batteries, most of the electrolyte is not recycled, and it is usually burned by fire. As a power source of lithium-ion batteries, the electrolyte accounts for about 15% of the battery cost, is rich in lithium ions, and has a high recovery value. Moreover, the commonly used electrolytes are generally carbonated organic solutions of LiPF6. In humid air, LiPF6 will react with water to generate harmful gas HF. Therefore, effective recovery of electrolyte not only has certain economic benefits, but also reduces harmful gas emissions.
Reference [47] used three different methods to remove electrolytes, namely direct thermal treatment, subcritical CO2 and acetonitrile extraction, and supercritical CO2 extraction. The results show that 90% of the electrolyte (including conductive salts) can be recovered by extraction with subcritical CO2 and acetonitrile. However, the crystallinity of graphite decreases after extraction, which adversely affects its electrochemical performance as a negative electrode.
Reference [48] proposed a clean electrochemical method to “kill two birds with one stone” to recover graphite and copper foils from Li-ion batteries, and studied the effects of various parameters (voltage, inter-electrode distance and electrolyte concentration) on the electrolysis process. The schematic diagram of the recovery is shown in Fig. 7. The results show that under the optimum conditions of a pole distance of 10 cm, a concentration of Na2SO4 electrolyte of 1.5 g⋅L−1 and a voltage of 30 V, the complete separation of copper foil and graphite can be achieved within 25 min of electrolysis. Li+ in the electrolyte can be further recovered by precipitation. In addition, the authors conducted an economic evaluation of this method, estimating a profit of approximately $10 per kg of lithium-ion battery anode material processed. However, due to the presence of binder PVDF and conductive agent, the mass fraction of recovered graphite (∼95%) needs to be improved.
Figure 7: Electrolysis based recovery of graphite
3 Reuse of Recycled Anode Materials
3.1 Anode Materials for Lithium Ion Energy Storage Devices
Most of the recovered graphite is recycled as a negative electrode material for lithium-ion batteries. Table 1 shows the electrochemical properties of the recovered graphite in the literature reported in the past. The research shows that the recovered graphite maintains a good crystal structure, and the initial capacity can basically meet the requirements of reuse, but whether the recovered graphite meets the commercial standards depends on the particle size, density, specific surface area, purity, and the first week Coulomb efficiency, charge and discharge of the material, voltage platform, cycle stability and other aspects are comprehensively evaluated.
Reference [49] used mechanical treatment and sulfuric acid leaching process to recover anode materials and applied them to Li-ion batteries/capacitors. The results show that the recovered carbonaceous materials can achieve energy densities of 313 and 112 W⋅h⋅kg−1 in Li-ion full batteries and Li-ion capacitors, respectively. However, due to the existence of disordered structure, the Coulombic efficiency of the recovered carbonaceous materials in the first week of Li-ion half cells is only 50%. Residual conductive agents, binders and thickeners can be removed by heat treatment in air, and the surface of graphite can be coated with pyrolytic carbon to improve the coulombic efficiency of the first week. The authors adopted this method to recover the coulombic efficiency of graphite. increased to 92.1%. In addition, Reference [50] proposed a water treatment-high-temperature calcination method to use the recovered graphite as the anode material for double carbon-lithium ion capacitors. It is calculated that the maximum energy density of recycled graphite reaches 185.54 W⋅h⋅kg−1 under the power density of 0.319 kW⋅kg−1 and the capacity retention rate is 75% after 2000 continuous cycles at 10°C and 25°C. This work opens up the possibility of recycling graphite as an electrode material for high-energy storage devices.
3.2 Anode Materials for Sodium/Potassium Ion Batteries
Reference [51] recovered the graphite anode material by a simple heat treatment method and reused it as a sodium/potassium ion battery anode. Under the current density of 0.2 A⋅g−1, the reversible sodium storage capacity of the recovered graphite is 162 mA⋅h⋅g−1, and even at 2 A⋅g−1, the capacity retention rate after 1000 cycles is still as high as 94%. .6%. At a current density of 0.05 A⋅g−1, a potassium storage capacity of 320 mA⋅h⋅g−1 can be achieved. Recently, Reference [52] reported the application of graphite recovered by one-step acid treatment in Na-ion batteries. At the current density of 0.05 A⋅g−1, the recovered graphite has a high reversible capacity of 127 mA⋅h⋅g−1. In addition, it has an excellent long cycle life, with a reversible capacity of 106.8 mA⋅h⋅g−1 maintained after 500 cycles at a current density of 2 A⋅g−1. Applying recycled graphite to sodium/potassium-ion batteries not only solves the problems caused by waste lithium-ion batteries. The problem of waste pollution can also promote the development of next-generation batteries.
3.3 Aluminum Ion Battery Cathode Material
Reference [53] recovered graphite from spent lithium-ion batteries and explored its potential as a cathode for aluminum-ion batteries. Due to the large interlayer spacing of the recycled graphite, the intercalation/extraction of Al ions is effectively promoted during the charging and discharging process, so at a current density of 50 mA⋅g−1, the Al ion storage capacity reaches 124 mA⋅h⋅g−1, even after 6700 cycles at a high rate of 300 mA⋅g−1, the capacity retained 81% of its initial capacity. This excellent aluminum ion storage property makes recycled graphite a promising cathode material, providing a feasible solution for the recycling of large amounts of graphite anode waste.
Due to the excellent properties of graphene in many aspects such as optics, electricity, mechanics, and heat, recycled graphite is often used to prepare graphene. Reference [54] prepared graphene by oxidizing graphite by Hummers method. Since the oxygen groups between the waste graphite layers can promote the oxidation reaction, the consumption of H2SO4 and KMnO4 is reduced by 40% and 28.6%, respectively, but a large amount of toxic N2H4⋅H2O is still required as a reducing agent. Therefore, Reference [55] used waste lithium-ion battery packaging materials (i.e., Al and stainless steel) as reducing agents to prepare reduced graphene oxide (rGO) in the presence of HCl, and studied the application of graphene in supercapacitors. At 0.5 A⋅g−1, the material exhibits a specific capacitance as high as 112 F⋅g−1. In another study, they also used Al reduction to prepare rGO, and transformed the separator into carbon hollow spheres (CHS). Under the conditions of 1.5 MPa and −196°C, the absorption of H2 by rGO and CHS were 1.78% and 1.22% (mass fraction, the same below), respectively. The CO2 uptake was 12% and 33%, respectively [56]. This study confirms the possibility of transforming the recycled separator and graphite anode into materials for efficient storage of H2 and CO2, providing a new idea for full-component recovery of Li-ion batteries.
Although the redox method is very effective, it consumes a large amount of strong oxidants (H2SO4, KMnO4) and reducing agents (N2H4⋅H2O), which not only causes environmental pollution, but also severely damages the crystal structure of graphene. Therefore, Reference [57] prepared graphene by exfoliating graphite in sodium cholate aqueous solution by ultrasonic-assisted liquid-phase exfoliation. Due to the weakening of the interlayer force after graphite cycling, the exfoliation efficiency of waste graphite is 3 to 11 times that of natural graphite, and more than 60% of the graphene flakes are larger than 1 mm in size and less than 1.5 nm in thickness. The conductivity of graphene is as high as 9100 Sm−1, which can be applied to conductive ink. Reference [58] prepared graphene by combining H2SO4 leaching and shear mixing. The results show that battery cycling and acid treatment can expand the graphite lattice, thereby increasing the graphene yield to 10 times that of pristine graphite. This process can be seamlessly embedded into the current cathode recycling process. In addition, the authors further explored the effect of graphene on the mechanical properties of epoxy resins. Compared with the original epoxy resin, the flexural strength (122.5 MPa), elastic modulus (3.6 GPa) and toughness (2269.9 kJ⋅m−3) of the graphene/epoxy composites were improved, respectively 26.0%, 38.5% and 13.0%. This is mainly attributed to the functional groups generated on the graphite surface during battery cycling, resulting in better dispersion and stronger bonding between graphene and epoxy resin.
3.5 Preparation of Graphite Composites
Recycled graphite also shows good prospects in the preparation of composite materials. The authors recovered and used graphite and separator materials (polyethylene, polypropylene) to synthesize polymer-graphite nanocomposite films. Compared with pure polymer films, the resulting nanocomposite films exhibited a 10-fold increase in tensile strength and a 5–6 orders of magnitude increase in conductance. In addition, they conducted a series of studies using waste anode carbon materials as adsorbents for wastewater treatment. They decorated the surface of waste graphite with nanostructured Mg(OH)2 and explored its ability to adsorb phosphate in water. The obtained material exhibited a high phosphate adsorption capacity of 588.4 mg⋅g−1 [59]. Similarly, the team fabricated Mg-rich carbon nanocomposites from waste graphite. The maximum phosphate adsorption capacity of the material reached 406.3 mg⋅g−1. The adsorption mechanism is to remove phosphate through phosphorus precipitation on the surface to form MgHPO4⋅1.2H2O and Mg3(PO4)2⋅8H2O nanocrystals [60]. The team also prepared MnO2-modified graphite adsorbents for the adsorption of heavy metal ions Pb2+, Cd2+ and Ag+ in wastewater. The results showed that the removal rates of Pb2+, Cd2+ and Ag+ were 99.9%, 79.7% and 99.8%, respectively [61]. The above research provides an economical and environmentally friendly method for waste recycling and heavy metal pollution treatment.
At present, the recovery methods of graphite anodes for lithium-ion batteries mainly include direct physical recovery, heat treatment, hydrometallurgy, the combination of heat treatment and hydrometallurgy, extraction and electrochemical methods. Among them, the flotation method aims to recover the cathode and anode at the same time, which improves the efficiency of recovery, but the purity of the recovered product is not enough for commercial application. The heat treatment recovery route can effectively regenerate graphite, but the energy cost of this process is high, and the decomposition of the polymer will produce toxic gas, which requires the installation of an exhaust gas absorption device. In addition, this process cannot achieve the recovery of high value-added lithium resources, and alternative methods are urgently needed if the complete recyclability of graphite anodes and lithium is to be achieved. Hydrometallurgy is a common method to extract high-value transition metals such as cobalt and nickel for positive electrodes, and it is also applicable to the extraction of high-value lithium from negative electrodes. However, due to the existence of insoluble lithium salts such as Lithium fluoride (LiF), this process consumes a large amount of strong acid (sulfuric acid, hydrochloric acid) and produces more toxic hydrofluoric acid. The discharge of waste acid will cause serious pollution to the environment. In addition, this process usually requires pre-heat treatment to separate copper foil and graphite, which further increases energy consumption. Therefore, an effective solution for hydrometallurgical recycling is to combine the recycling of positive and negative electrodes, which can greatly simplify the process and save labor and costs. The CO2 extraction method can effectively recover the electrolyte, avoiding the harm caused by the volatilization and decomposition of the electrolyte, but this method is uneconomical for the recycling of laptop and mobile phone batteries. The electrochemical method can combine the separation of graphite and copper foil and the recovery of lithium resources, which simplifies the recovery process and cost, but because the removal of binders and conductive agents is not considered, the purity of the recovered graphite is insufficient, and the electrochemical method has still many hurdles to overcome for large-scale adoption.
In addition, recycled graphite has shown good prospects in the fields of energy storage and preparation of graphene and graphite composites, especially in the preparation of graphene. Since the interlayer spacing of the anode graphite increases during the repeated charge/discharge process, the van der Waals force between the graphite layers is weakened, making it easier for the graphite to exfoliate into graphene. The presence of oxygen-containing groups can prevent graphene agglomeration, thereby improving its dispersibility. More importantly, the ultrasonic-assisted liquid phase exfoliation method and shear mixing method can be combined with the cathode precious metal recovery process, making the waste battery recycling technology more environmentally friendly, efficient and high value-added.
In recent years, initial progress has been made in the recycling of graphite anode materials for lithium-ion batteries, such as efficient direct physical recycling methods, simple but energy-intensive heat treatment methods, and hydrometallurgical methods that can be incorporated into the cathode recycling process. Realize the combination of industrialized heat treatment and hydrometallurgy, the extraction method that can recover toxic electrolytes, and the economical and environmentally friendly electrochemical method. In addition, recycled anode materials are used in other energy storage batteries, the preparation of graphene and graphite composites, etc. for satisfactory performance in all aspects, realizing the high value-added utilization of anode materials. Nevertheless, the recycling of graphite anodes is still in the laboratory stage and still faces many challenges.
1) Recycling the negative electrode can alleviate the cost pressure of battery recycling to a certain extent. The negative electrode can be regarded as the “waste” of the positive electrode recycling. Therefore, recycling the negative electrode is a process of turning waste into treasure.
In addition, graphite ore can only produce 90% to 98% flake graphite, and requires very complex (crushing classification-modification or granulation-graphitization, etc.) process and high temperature (2500°C∼3000°C) conditions to be able to flake graphite. Graphite is upgraded to battery grade spherical graphite. Therefore, considering the complicated and expensive techniques experienced to obtain battery-grade graphite from graphite ores, regenerating graphite from spent batteries is a more economical option.
However, the current car battery packs used for recycling are all disassembled manually, which greatly increases the cost of recycling waste power batteries, and toxic components such as electrolytes can also endanger human health. Therefore, the research and development of automatic disassembly and intelligent separation of different batteries will greatly improve the recycling efficiency of batteries, reduce costs, increase the value of recycled materials, and eliminate injuries to workers.
2) The removal method of fluoride binder is usually pyrolysis (PVDF pyrolysis will produce harmful by-products such as HF) or use highly toxic N-methylpyrrolidone (NMP) to dissolve, which is very unfavorable to the environment. Recent battery disassembly suggests that many newer batteries are moving to alternative binders on the anode, such as water-soluble CMC and emulsion-like SBR, which may be easier to remove at end-of-life.
3) The leaching agent selected for the recovery of insoluble lithium salts such as LiF in the negative electrode is mainly strong acid (sulfuric acid, hydrochloric acid), which makes the treatment of waste acid another challenge. Therefore, when considering the recovery of lithium by acid leaching, the recovery of the negative electrode can be incorporated into the process of recycling the positive electrode, which can save the recycling cost and reduce the pollution to the environment. In addition, finding a more environmentally friendly leaching agent is a more suitable solution. In addition to strong acid leaching, the electrochemical method can also realize the recovery of lithium-containing substances, and this process only consumes electricity, which is economical and environmentally friendly, and does not produce harmful by-products, which is a feasible strategy.
4) The existence of the conductive agent in the negative electrode will make the capacity of graphite when reused exceed the theoretical capacity, so the removal of the conductive agent is also inevitable. Previously, most conductive agents were burned by heat treatment. From a long-term point of view, this method is not desirable. Therefore, it is a better choice to develop a recovery or conversion route for conductive agents;
5) The preparation of waste graphite into other functional materials effectively improves the added value of waste utilization, but the impact and mechanism of the gap between recycled graphite and natural graphite on material preparation need to be further explored.
The recycling of waste lithium-ion batteries will become an urgent and arduous task in the near future. Starting from the concept of green chemistry, designing a short process, low energy consumption, and an environmentally friendly recycling route is an urgent need to achieve sustainable development of lithium-ion batteries.
Acknowledgement: The authors would like to thanks the editors and reviewers for their review and recommendations.
Funding Statement: The authors would like to thank the Deanship of Scientific Research at Taif University for the grant received for this research. This research was supported by Taif University with research grant (TURSP-2020/77).
Conflicts of Interest: The authors declare that they have no conflicts of interest to report regarding the present study.
References
1. A. Fakhri, S. Mohammed, I. Khan, A. Sadiq, B. Alkazemi et al., “Industry 4.0: Architecture and equipment revolution,” Computers, Materials & Continua, vol. 66, no. 2, pp. 1175–1194, 2021. [Google Scholar]
2. J. Yao, S. Xiong and X. Ma, “Comparative analysis of national policies for electric vehicle uptake using econometric models,” Energies, vol. 13, no. 14, pp. 1–24, 2020. [Google Scholar]
3. C. Vrabie, “Electric vehicles optimism versus the energy market reality,” Sustainability, vol. 14, no. 9, pp. 1–18, 2022. [Google Scholar]
4. B. Zhang, H. Xie and B. Lu, “A green electrochemical process to recover co and li from spent LiCoO2-based batteries in molten salts,” ACS Sustainable Chemistry & Engineering, vol. 7, no. 15, pp. 13391–13399, 2019. [Google Scholar]
5. X. Qu, H. Xie and X. Chen, “Recovery of LiCoO2 from spent li-ion batteries through a low-temperature ammonium chloride roasting approach: Thermodynamics and reaction mechanisms,” ACS Sustainable Chemistry & Engineering, vol. 8, no. 16, pp. 6524–6532, 2020. [Google Scholar]
6. J. Zhao, B. Zhang and H. Xie, “Hydrometallurgical recovery of spent cobalt-based lithium-ion battery cathodes using ethanol as the reducing agent,” Environmental Research, vol. 181, no. 4, pp. 1088–1105, 2020. [Google Scholar]
7. F. Larouche, F. Tedjar, K. Amouzega, G. Houlachi, P. Bouchard et al., “Progress and status of hydrometallurgical and direct recycling of li-ion batteries and beyond,” Materials, vol. 13, no. 3, pp. 1–17, 2020. [Google Scholar]
8. W. Lv, X. Zheng, L. Li, H. Cao, Y. Zhang et al., “Highly selective metal recovery from spent lithium-ion batteries through stoichiometric hydrogen ion replacement,” Frontiers of Chemical Science and Engineering, vol. 15, no. 3, pp. 1243–1256, 2021. [Google Scholar]
9. J. Zhang, J. Hu and Y. Liu, “Sustainable and facile method for the selective recovery of lithium from cathode scrap of spent LiFePO4 batteries,” ACS Sustainable Chemistry & Engineering, vol. 7, no. 6, pp. 5626–5631, 2019. [Google Scholar]
10. P. Liu, L. Xiao and Y. Chen, “Recovering valuable metals from LiNixCoyMn1−x−yO2 cathode materials of spent lithium ion batteries via a combination of reduction roasting and stepwise leaching,” Journal of Alloys and Compounds, vol. 783, no. 2, pp. 743–752, 2019. [Google Scholar]
11. Y. Tang, X. Qu, B. Zhang, Y. Zhao, H. Xie et al., “Recycling of spent lithium nickel cobalt manganese oxides via a low-temperature ammonium sulfation roasting approach,” Journal of Cleaner Production, vol. 279, no. 4, pp. 1233–1243, 2021. [Google Scholar]
12. W. Zhang, C. Xu and W. He, “A review on management of spent lithium ion batteries and strategy for resource recycling of all components from them,” Waste Management & Research: The Journal for a Sustainable Circular Economy, vol. 36, no. 2, pp. 99–112, 2021. [Google Scholar]
13. G. Harper, R. Sommerville and E. Kendrick, “Recycling lithium-ion batteries from electric vehicles,” Nature Journal, vol. 575, no. 7781, pp. 75–86, 2019. [Google Scholar]
14. E. Prasetyo, W. Muryanta, A. Gesta, S. Sudibyo, M. Amin et al., “Tannic acid as a novel and green leaching reagent for cobalt and lithium recycling from spent lithium-ion batteries,” Journal of Material Cycles and Waste Management, vol. 24, pp. 927–938, 2022. [Google Scholar]
15. Z. Zheng, M. Chen and Q. Wang, “High performance cathode recovery from different electric vehicle recycling streams,” ACS Sustainable Chemistry & Engineering, vol. 6, no. 11, pp. 13977–13982, 2018. [Google Scholar]
16. R. Xu, W. Xu, J. Wang, F. Liu, W. Sun et al., “A review on regenerating materials from spent lithium-ion batteries,” Molecules Journal, vol. 27, no. 7, pp. 1–18, 2022. [Google Scholar]
17. A. Holzer, S. Kern, C. Ponak and H. Raupenstrauch, “A novel pyrometallurgical recycling process for lithium-ion batteries and its application to the recycling of lco and lfp,” Metals Journal, vol. 11, no. 1, pp. 1–17, 2020. [Google Scholar]
18. S. Natarajan and V. Aravindan, “An urgent call to spent lib recycling: Whys and wherefores for graphite recovery,” Advanced Energy Materials, vol. 10, no. 37, pp. 1–21, 2020. [Google Scholar]
19. L. Zhang, W. Wang, S. Lu and Y. Xiang, “Carbon anode materials: A detailed comparison between na-ion and k-ion batteries,” Advanced Energy Materials, vol. 11, no. 11, pp. 1743–1752, 2021. [Google Scholar]
20. F. Arshad, L. Li and K. Amin, “A comprehensive review of the advancement in recycling the anode and electrolyte from spent lithium ion batteries,” ACS Sustainable Chemistry & Engineering, vol. 8, no. 36, pp. 13527–13554, 2020. [Google Scholar]
21. M. Mngomezulu, A. Luyt, S. Chapple and M. John, “Poly (lactic acid)-starch/expandable graphite (PLA-starch/EG) flame retardant composites,” Journal of Renewable Materials, vol. 6, no. 1, pp. 26–37, 2018. [Google Scholar]
22. D. Muller, A. Fill and K. Birke, “Cycling of double-layered graphite anodes in pouch-cells,” Batteries Journal, vol. 8, no. 3, pp. 1–18, 2022. [Google Scholar]
23. C. Liu, J. Lin, H. Cao, Y. Zhang and Z. Sun, “Recycling of spent lithium-ion batteries in view of lithium recovery: A critical review,” Journal of Cleaner Production, vol. 228, no. 3, pp. 801–813, 2019. [Google Scholar]
24. W. Urbanska, “Recovery of co li, and ni from spent li-ion batteries by the inorganic and/or reducer assisted leaching method,” Minerals Journal, vol. 10, no. 6, pp. 1–19, 2020. [Google Scholar]
25. W. Lee, Y. Wu, Y. Liao and Y. Liu, “Graphite felt modified by atomic layer deposition with TiO2 nanocoating exhibits super-hydrophilicity, low charge-transform resistance, and high electrochemical activity,” Nanomaterials Journal, vol. 10, no. 9, pp. 1–23, 2020. [Google Scholar]
26. W. Lv, Z. Wang and H. Cao, “A critical review and analysis on the recycling of spent lithium-ion batteries,” ACS Sustainable Chemistry & Engineering, vol. 6, no. 2, pp. 1504–1521, 2018. [Google Scholar]
27. X. Zhang, L. Cai, E. Fan, J. Lin, F. Wu et al., “Recovery valuable metals from spent lithium-ion batteries via a low-temperature roasting approach: Thermodynamics and conversion mechanism,” Journal of Hazardous Advances, vol. 1, no. 5, pp. 1003–1015, 2021. [Google Scholar]
28. E. Fan, L. Li and Z. Wang, “Sustainable recycling technology for li-ion batteries and beyond: Challenges and future prospects,” Chemical Reviews, vol. 120, no. 14, pp. 7020–7063, 2020. [Google Scholar]
29. X. Zhang, L. Li, E. Fan and C. Shen, “Toward sustainable and systematic recycling of spent rechargeable batteries,” Chemical Society Reviews, vol. 47, no. 19, pp. 7239–7302, 2018. [Google Scholar]
30. H. Qiu, C. Peschel, M. Winter, S. Nowak, J. Kothe et al., “Recovery of graphite and cathode active materials from spent lithium-ion batteries by applying two pretreatment methods and flotation combined with a rapid analysis technique,” Metals Journal, vol. 12, no. 4, pp. 1–19, 2022. [Google Scholar]
31. R. Zhan, Z. Oldenburg and L. Pan, “Recovery of active cathode materials from lithium-ion batteries using froth flotation,” Sustainable Materials and Technologies, vol. 17, no. 3, pp. 1764–1773, 2018. [Google Scholar]
32. G. Zhang, Z. Du, Y. He, H. Wang, W. Xie et al., “A sustainable process for the recovery of anode and cathode materials derived from spent lithium-ion batteries,” Sustainability Journal, vol. 11, no. 8, pp. 1–15, 2019. [Google Scholar]
33. J. Yu, Y. He and Z. Ge, “A promising physical method for recovery of LiCoO2 and graphite from spent lithium-ion batteries: Grinding floatation,” Separation and Purification Technology, vol. 190, no. 4, pp. 45–52, 2018. [Google Scholar]
34. G. Zhang, Y. He and Y. Feng, “Pyrolysis-ultrasonic-assisted floatation technology for recovering graphite and LiCoO2 from spent lithium-ion batteries,” ACS Sustainable Chemistry & Engineering, vol. 6, no. 8, pp. 10896–10904, 2018. [Google Scholar]
35. J. Sabisch, A. Anapolsky and G. Liu, “Evaluation of using pre-lithiated graphite from recycled li-ion batteries from new lib anodes,” Resources, Conservation and Recycling, vol. 129, no. 8, pp. 129–134, 2018. [Google Scholar]
36. H. Wang, Y. Huang and C. Huang, “Reclaiming graphite from spent lithium ion batteries ecologically and economically,” Electrochimica Acta, vol. 313, no. 5, pp. 423–431, 2019. [Google Scholar]
37. C. Ye, W. Tu and L. Yin, “Converting detrimental HF in electrolytes into a highly fluorinated interphase on cathodes,” Journal of Materials Chemistry A, vol. 6, no. 36, pp. 17642–17652, 2018. [Google Scholar]
38. Z. Ma, H. Chen, H. Zhou, L. Xing and W. Li, “Cost-efficient film-forming additive for high-voltage lithium-nickel-manganese oxide cathodes,” ACS Omega, vol. 6, no. 46, pp. 31330–31338, 2021. [Google Scholar]
39. Z. Ma, Y. Zhuang and Y. Deng, “From spent graphite to atmosphere sp2 + sp3 carbon-coated sp2 graphite for high-performance lithium ion batteries,” Journal of Power Sources, vol. 376, no. 3, pp. 91–99, 2018. [Google Scholar]
40. J. Zhang, X. Li and D. Song, “Effective regeneration of anode material recycled from scrapped li-ion batteries,” Journal of Power Sources, vol. 390, no. 5, pp. 38–44, 2018. [Google Scholar]
41. C. Yi, Y. Yang, T. Zhang and X. Wang, “A green and facile approach for regeneration of graphite from spent lithium ion battery,” Journal of Cleaner Production, vol. 277, no. 3, pp. 1877–1889, 2020. [Google Scholar]
42. A. Ibrahim, A. Klopocinska, K. Horvat and Z. Hamid, “Graphene-based nanocomposites: Synthesis, mechanical properties and characterization,” Polymers Journal, vol. 13, no. 17, pp. 1–19, 2021. [Google Scholar]
43. O. Tyler, W. Storm, K. Karthikeyan, A. Yu and Z. Chen, “Recycling of mixed cathode lithium-ion batteries for electric vehicles: Current status and future outlook,” Carbon Energy Journal, vol. 2, no. 1, pp. 6–43, 2020. [Google Scholar]
44. X. Ma, M. Chen and B. Chen, “High-performance graphite recovered from spent lithium-ion batteries,” ACS Sustainable Chemistry & Engineering, vol. 7, no. 3, pp. 19732–19738, 2019. [Google Scholar]
45. Y. Yang, S. Song and S. Lei, “A process for combination of recycling lithium and regenerating graphite from spent lithium-ion battery,” Waste Management, vol. 85, no. 7, pp. 529–537, 2019. [Google Scholar]
46. Y. Gao, C. Wang and J. Zhang, “Graphite recycling from the spent lithium-ion batteries by sulfuric acid curing-leaching combined with high-temperature calculation,” ACS Sustainable Chemistry & Engineering, vol. 8, no. 25, pp. 9447–9455, 2020. [Google Scholar]
47. J. Liu, H. Shi, X. Hu, Y. Geng, L. Yang et al., “Critical strategies for recycling process of graphite from spent lithium-ion batteries: A review,” Science of the Total Environment, vol. 816, no. 3, pp. 1521–1539, 2022. [Google Scholar]
48. N. Cao, Y. Zhang and L. Chen, “An innovative approach to recover anode from spent lithium-ion battery,” Journal of Power Sources, vol. 483, no. 3, pp. 2293–2307, 2021. [Google Scholar]
49. K. Liu, S. Yang, L. Luo and K. Zhang, “From spent graphite to recycle graphite anode for high-performance lithium ion batteries and sodium ion batteries,” Electrochimica Acta, vol. 356, no. 3, pp. 1387–1398, 2020. [Google Scholar]
50. V. Aravindan, S. Jayaraman and F. Tedjar, “From electrodes to electrodes: Building high-performance li-ion capacitors and batteries from spent lithium-ion battery carbonaceous materials,” ChemElectroChem Journal, vol. 6, no. 5, pp. 1407–1412, 2019. [Google Scholar]
51. M. Divya, S. Natarajan and Y. Lee, “Achieving high-energy dual carbon li-ion capacitors with unique low-and high-temperature performance from spent li-ion batteries,” Journal of Materials Chemistry A, vol. 8, no. 9, pp. 4950–4959, 2020. [Google Scholar]
52. H. Liang, B. Hou and W. Li, “Staging na/k-ion de-/intercalation of graphite retrieved from spent li-ion batteries: In operando x-ray diffraction studies and an advanced anode material for na/k-ion batteries,” Energy & Environmental Sciences, vol. 12, no. 12, pp. 3575–3584, 2019. [Google Scholar]
53. H. Pham, M. Horn and J. Fernando, “Spent graphite from end-of-life li-ion batteries as a potential electrode for aluminum ion battery,” Sustainable Materials and Technologies, vol. 26, no. 3, pp. 959–978, 2020. [Google Scholar]
54. Y. Lei, J. Zhang, X. Chen, W. Min, R. Wang et al., “From spent lithium-ion batteries to high performance sodium-ion batteries: A case study,” Materials Today Energy Journal, vol. 26, no. 4, pp. 3315–3324, 2022. [Google Scholar]
55. S. Natarajan, S. Rao and H. Bajaj, “Environmental benign synthesis of reduced graphene oxide (rGO) from spent lithium-ion batteries (libs) graphite and its application in supercapacitor,” Colloids and Surfaces A: Physicochemical and Engineering Aspects, vol. 543, no. 5, pp. 98–108, 2018. [Google Scholar]
56. S. Natarajan, H. Bajaj and V. Aravindan, “Template-free synthesis of carbon hollow speheres and reduced graphene oxide from spent lithium-ion batteries towards efficient gas storage,” Journal of Materials Chemistry A, vol. 7, no. 7, pp. 3244–3252, 2019. [Google Scholar]
57. X. Chen, Y. Zhu and W. Peng, “Direct exfoliation of the anode graphite of used li-ion batteries into few-layer graphene sheets: A green and high yield route to high quality graphene preparation,” Journal of Materials Chemistry A, vol. 8, no. 12, pp. 5880–5885, 2020. [Google Scholar]
58. Y. Zhang, N. Song and J. He, “Lithium-aided conversion of end-of-life lithium-ion battery anoes to high-quality graphene and graphene oxide,” Nano Letters, vol. 19, no. 1, pp. 512–519, 2021. [Google Scholar]
59. Y. Zhang, X. Guo and F. Wu, “Mesocarbon microbead carbon-supported magnesium hydroxide nanoparticles: Turning spent li-ion battery anode into a highly efficient phosphate adsorbent for wastewater treatment,” ACS Applied Materials & Interfaces, vol. 8, no. 33, pp. 21315–21325, 2019. [Google Scholar]
60. Y. Zhang, X. Guo, Y. Yao and K. Zhang, “Synthesis of mg-decorated carbon nanocmposites from mesocarbon microbeads (MCMB) graphite: Application for wastewater treatment,” ACS Omega, vol. 1, no. 3, pp. 417–423, 2020. [Google Scholar]
61. T. Zhao, Y. Yao and M. Wang, “Preparation of MnO2-modified graphite sorbents from spent li-ion batteries for the treatment of water contaminated by lead, cadmium, and silver,” ACS Applied Materials & Interfaces, vol. 9, no. 30, pp. 25369–25376, 2021. [Google Scholar]
Cite This Article
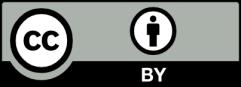
This work is licensed under a Creative Commons Attribution 4.0 International License , which permits unrestricted use, distribution, and reproduction in any medium, provided the original work is properly cited.