Open Access
ARTICLE
Information-Centric IoT-Based Smart Farming with Dynamic Data Optimization
1 Department of Computer Science and Engineering, Sister Nivedita University, Kolkata, India
2 Post Doctoral Researcher, Sambalpur University, Sambalpur, India
3 Department of Computer Science, Anna Adarsh College for Women, Chennai, India
4 Department of Information Technology, Vels Institute of Science, Technology and Advanced Studies, Chennai, India
5 School of Computer Science and Engineering, SCE, Taylor’s University, Subang Jaya, 47500, Selangor, Malaysia
6 Center for Smart Society 5.0, [CSS5], FIT, Taylor’s University, Subang Jaya, 47500, Selangor, Malaysia
7 Department of Information Security and Applied Computing, Eastern Michigan University, USA
8 School of Information Security and Applied Computing, Eastern Michigan University, USA
* Corresponding Author: Souvik Pal. Email:
Computers, Materials & Continua 2023, 74(2), 3865-3880. https://doi.org/10.32604/cmc.2023.029038
Received 23 February 2022; Accepted 21 June 2022; Issue published 31 October 2022
Abstract
Smart farming has become a strategic approach of sustainable agriculture management and monitoring with the infrastructure to exploit modern technologies, including big data, the cloud, and the Internet of Things (IoT). Many researchers try to integrate IoT-based smart farming on cloud platforms effectively. They define various frameworks on smart farming and monitoring system and still lacks to define effective data management schemes. Since IoT-cloud systems involve massive structured and unstructured data, data optimization comes into the picture. Hence, this research designs an Information-Centric IoT-based Smart Farming with Dynamic Data Optimization (ICISF-DDO), which enhances the performance of the smart farming infrastructure with minimal energy consumption and improved lifetime. Here, a conceptual framework of the proposed scheme and statistical design model has been well defined. The information storage and management with DDO has been expanded individually to show the effective use of membership parameters in data optimization. The simulation outcomes state that the proposed ICISF-DDO can surpass existing smart farming systems with a data optimization ratio of 97.71%, reliability ratio of 98.63%, a coverage ratio of 99.67%, least sensor error rate of 8.96%, and efficient energy consumption ratio of 4.84%.Keywords
1 Prologue Study to Smart Farming and Information Management
Due to technological advances in recent years, the working environment in the agriculture industry has undergone significant changes [1]. The agricultural industry has entered a new age when fast and complex decision-making becomes the key to success [2]. Technological developments such as big data, IoT, artificial intelligence, neural networks, cloud computing, etc., equip farmers with tools and expertise to improve decision-making during their particular phases of production and yielding [3–6]. The existing facts such as population expansion, climate change, and workforce scarcity have led to developing intelligent farming systems from planting and watering to crop health care and harvests [7]. Environmental and remote automation and surveillance using IoT are expanding fast in agriculture to produce more competent and effective agricultural tools and services [8]. Smart farming can supply farmers with valuable intimate environmental information obtained from wireless IoT sensors in the growing fields to increase competition and profitability [9].
The recent emergence in smart farming involves several agricultural domains, as seen in Fig. 1. The smart farming system or infrastructure integrates plant disease diagnosis, fertility ratio analysis, crop monitoring, soil profile monitoring, water spreading, field surveillance, and water stress analysis [10,11]. Disease diagnosis and crop monitoring can be improved through video and image classification. Water spreading and field monitoring are employed using wireless devices such as drones and UAVs [12]. Soil profile monitoring can be done by collecting the soil profile using sensors. The water stress analysis manages the availability and distribution of the smart farming system. Finally, the fertility rate analysis can aid in effective decision-making in production planning and marketing [13]. All these services are available only if there is an effective information management system.
Figure 1: Smart farming through IoT-Cloud
1.2 Agricultural Information Management
Data from sensors can be communicated with stakeholders in sensor-oriented precision agriculture via either the local server or the cloud according to communication network stability and internet connectivity [14]. Smart farming’s Information management has grown from basic farm recording systems into big, comprehensive farm management systems to fulfill the requirements of the many stakeholders for communication and data transfer between databases [15]. The primary responsibility of such information management is the management of the large volume of data covered by different agricultural parameters, such as information from farmers, soil physical and chemical parameters, nutrients available, crops, weather, precipitation, seasons, fertilizers, pest control, irrigation procedures, crop yield predictions, and environmental factors [16]. During the past 60 years, terabytes of unstructured data in the database have been produced from the processes involved in gathering the various agricultural data [17]. Conversely, large-scale data cleansing and preprocessing have been tedious due to unstructured data types and a single database instance [18].
To address these challenges, data optimization can be effectively used in this domain. Often including errors, inconsistencies, redundancies, or other abnormalities unnecessarily make access to essential information in a timely and complete manner difficult. The data optimization uses extensive quality by the availability of precise data, better access, organization, and cleaning, irrespective of the source, for maximizing the speed and comprehensivity of the collection, analysis, and application of relevant information [19]. Data optimization has been aimed at reducing the lifespan of information in IoT-cloud systems. Reduction in energy consumption seems to be the major advantage of data optimization [20]. Multiple access mechanisms are frequently used to accommodate this non-orthogonal system [21]. The efficient collection of data is another benefit of data optimization. For compressing collected data, compressive sensing can even be used to reduce the volume of information transmission [22]. The optimized data can be retrieved with appropriate retrieval techniques if necessary [23].
For this reason, Information-Centric IoT-based Smart Farming with Dynamic Data Optimization (ICISF-DDO) has been proposed to improve the smart farming system by efficient information management with minimal energy consumption and improved lifetime. The DDO approach with membership parameter initialization has been integrated into an information-centric smart farming system with an IoT-cloud platform.
Section-wise categorization is implemented as follows: Section 1 discussed smart farming and agricultural information management to introduce the entire research. Section 2 summarizes the relevant works on smart farming and agricultural information management by various researchers. The following section elaborates the proposed system design, and Section 4 validates the proposed system’s significance compared to the existing smart farming system. The entire research is concluded with the future scope in Section 5.
2 Relevant Research Works on Smart Farming and Information Management
As discussed in the above introductory section, there exist several research studies on smart farming. Agriculture and automation providers are increasingly researching ways to use IoT and digital technologies to increase yields, profitability, and agricultural practices. This section thus summarizes the recent works on IoT-based smart farming frameworks and farming information management schemes for the comparative analysis, which can effectively validate the significance of the proposed ICISF-DDO framework.
Dahane and the joint authors (2020) in [24] established and experimented with a smart farming platform with artificial intelligence (SFP-AI) technology to provide forecasting potential. In [25], Gaikwad and others (2021) implemented a real-time monitoring farming system using IoT (RMFS-IoT) in high-resolution soil humidity, temperature, humidity, and temperature data at the agribusiness level. Opensource platforms were used in the development of the system. They employed three components in RMFS-IoT such as Arduino IoT, smartphone, and a cloud-based web server. To evaluate the collected farming data, the IoT-based device instantaneously transferred the sent parameters to a cloud server.
To meet information monitoring needs for current big farms, a low cost, low power, and low data rate communication (LP-LDC) solution were presented by Saqib with his co-authors (2020) in [26]. In LP-LDC, they met the problems of monitoring information over long distances with a serial module for low power, long-range and low-cost communication. It could increase the communication range by adding intermediary nodes to a tree-based mechanism of communications. Field data were gathered automatically, stored, analyzed, and accessible in real-time by farmers using a combination of IoT and Farm Management Information Systems (FMIS) as per the authors in [27]. An IoT circuit and FMIS web interface for smart farming with proof of concept (PoC) were designed. The proposed FMIS-POC web interface was assessed its performance in real-time intelligent agriculture.
In [28] Re- Iedentification model utilises the complimentary expression benefits of middle features in a CNN to improve feature expression. None of them addressed data optimization to improve the lifespan and energy consumption of their IoT-cloud systems [29,30].
This fact has led to the hypothesis to enhance the smart farming system through efficient information management, with low energy consumption and better lifetime. Thereby proposes the Information-Centric IoT-based Smart Farming with Dynamic Data Optimization (ICISF-DDO) incorporating DDO into a smart farming system with an IoT-cloud platform that uses activation of the membership parameter.
3 Information-Centric Iot-Based Smart Farming with Dynamic Data Optimization (ICISF-DDO)
In this section, the elaborated discussion of the proposed ICISF-DDO has been included. To minimize inefficiencies and enhance performance in all sectors, the IoT is beginning to influence various industries, from the industrial, healthcare, communications, and energy sectors, to agriculture. IoT provides a basic communication infrastructure that enables intelligent objects from sensors, vehicles, and mobile devices that use the Internet, including local or remote data acquisition, cloud-based intelligent analysis, decision-making, user interfacing, and agricultural management. This is the reason why this research aims to improve the performance of IoT-cloud systems in smart farming. As defined in the previous sections, the proposed ICISF-DDO has been implemented effective information management with data optimization to ensure improved energy consumption and lifetime. This aim can be achieved through the DDO scheme presentation, which defines and initializes membership parameters in its effective data handling. The following gives the conceptual framework of the proposed model that can be effectively implemented in real-time.
As seen in Fig. 2, the conceptual framework of the proposed ICISF-DDO for a real-time smart farming environment. For the above scenario, the IoT-based smart farming environment has been created with IoT sensors such as fruit sensors for yield analysis, leaf sensors for leaf disease monitoring, soil sensors for water level monitoring, root sensors for soil moisture, and root growth dynamics analysis, and environmental sensors for air quality monitoring, etc. These sensors continually collect a large amount of data and pass it to the cloud platform through internet gateways for sustainable management and analysis. The massive data collection can lead to the highest energy consumption and thus limits the lifetime of the sensor network. The data optimization under the data processing module has been addressed this challenge effectively. The data monitoring, analysis, and forecasting processes are then ensure reliable and efficient performance. The expert groups, farmers, and supervisors involved in smart farming can access the outcomes and information through their smartphones, desktops, tablets, etc., from anywhere at any time. The following gives the architectural design of the proposed model.
Figure 2: Conceptual framework for ICISF-DDO
Fig. 3 depicts the layered architecture with three finite layers such as front-end layer, gateway layer, and back-end layer. The first layer of the proposed ICISF-DDO (front-end layer) consists of four elements, including the IoT sensors or nodes, a microcontroller, environment sensors and actuators, interface circuits, and a module for the wireless connection. In the front-end layer, there are multiple node-set (NS) from 1 to M, where M is the maximum number of trees in the smart farming environment (as seen in Fig. 2). The microcontroller in this layer gathers and transfers the various sensors to the next architectural layer through the Internet. The microcontroller can be battery-powered, automatically powered using solar panels, and automatically powered by backup batteries, depending on the application. The sensors such as leaf sensor, fruit sensor, environment sensor, root sensor, and the foot sensor in this layer transform the detected events into a voltage or power equivalent. Such electrical signal, however, remains in analog form. To convert these analog signals from the sensors into the correct digital format and conduct further signal conditioning capabilities, it is necessary to have a sensor interface circuit with actuators and controllers to assure compatibility with the microcontroller in use. The main components of these interfacing circuits are analog to digital converters (ADC). The wireless communication module provides the means to send the information to the nearest gateway for the sensor nodes. This research design suggests the ultra-low energy transceiver NRF 24L01 working on the ISM 2.4 GHz range, which greatly decreases the power consumption of our design unit, as opposed to the vast majority of comparable works using high power Bluetooth or cellular technologies. The gateways in the second layer send the gathered information to the cloud server in the back-end layer for storage and thorough analysis after data optimization by the proposed DDO induced with the membership parameters. The gateway layer also transmits requests from the back-end to the node actuators. The back-end layer of the proposed ICISF-DDO facilitates the functionality of end-users to obtain sensed data with significant processing results. In addition to providing suitable application programming interfaces (APIs) and software tools to enable end-users to access the data, various services including data storage, data analytics (forecasting and analysis), and data visualization. Since this research aimed at tackling the information storage and management in smart farming efficiency to attain the lowest energy consumption and the highest lifetime, this paper concentrates on the specific design of the DDO scheme, the essential module for optimizing the resource allocation to various components of the cloud system. The following sub-section gives the theoretical background and the statistical design of the DDO scheme in detail.
Figure 3: Layered architecture of ICISF-DDO
Mass transit across the agricultural infrastructure is produced in a huge volume by the IoT-based intelligent farming environment sensors. The exposure of huge data in the smart agricultural system communication network makes statistical and computational data analysis, processing, and optimization crucial. In this proposed ICISF-DDO approach, data optimization is achieved by efficient data acquisition. Two enhancements have been made, in particular in the area of data redundancy and energy usage. Optimized sensing has been used to compact the obtained data to decrease the amount of data transfer. Furthermore, the optimized data from the IoT-assisted smart farming systems can even be retrieved using appropriate recovery solutions. Therefore, DDO in the proposed ICISF-DDO contributes to a minimum delay for energy-efficient, reliable IoT data transmission. In addition, these strategies decrease overall cost needs.
3.2 Dynamic Data Optimization Algorithm
This section deals with Dynamic Data Optimization algorithm. Since the data acquisition and processing in IoT-based smart farming systems involve dynamic variables whose values change in time, this research aims at designing the DDO algorithm as follows:
Algorithm 1 defines the various computation steps and flow of the proposed DDO algorithm in the research model ICISF-DDO. As seen in the above algorithm, for all the nodes set NS in the smart farming environment, the sub-optimized data is computed for the optimal node selected using S′ij based on the data flow volume DFVij(p→q), energy Eij(p→q), and cost cij(p→q). Then, membership parameter induction has been performed by computing the initial membership parameter Fij(p,q) and final membership parameter F′ij(p,q). The centroid for the state p and q in the data transit have been then computed as Gqij and Gqij. By then, sub-optimized data, OiD is aggregated for the final optimized data allocation, OD. Each step of the proposed algorithm is explained as follows:
In the large space-smart farming system, it is assumed that multiple nodes set in a single, smart farming infrastructure, for example, as assumed in Fig. 2, a large-scale cherry farming environment with each tree is individually observed with multiple sensors including, fruit sensor, leaf sensor, root sensor, and soil sensor along with an environmental sensor. Let us assume in general and there is M number of such nodes set (indexed with i=1,2,3,…,M) with N number of nodes in each (indexed with j=1,2,3,…,N). For the statistical design model, the cloud resource storage variable is initialized as follows:
R0=∑M{IMN∑Mi=1∑Nj=1I0}(1)
Eq. (1) depicts the cloud resource R0 for the entire smart farming system, which is initialized with the incidence ratio IMN of the Nth node in the Mth nodes set over an arithmetic summation of the I0 initial incidence ratios of each N node in the M nodes set. If the cloud resource is not enough or equal to the required sensor data storage, the data processing through cloud retrievel fails by missing data. After initializing the maximum enough of cloud resources for the entire smart farming system, the cloud resource for the individual nodes in each node-set is computed as follows:
Rij=argargmaxsij∂(sij)+∅(2)
In Eq. (2), the variable Rij is the individual cloud resource value for each jth node in the ith node-set. The sij represents the state vector of the jth node in the ith node-set. This resource variable finds the arg argmax of the overall state momentum ∂(sij) for each state vector sij. The argargmax sometimes called the argument of the maximum computes the elements of the state vectors of state momentum at which the momentum values are maximized, which helps in finding the maximum cloud resource available for each N node. The variable ∅ is the constant cloud resource value reserved for the garbage collection. After reserving the cloud resource, the steps for optimal data allocation have been calculated. For this, the optimization criteria are then fixed for each node in every node-set, as follows:
Yipq=Ki,where0≤Kij≤Rij(3)
The optimization criterion for the state transition p→q as denoted in Eq. (3) uses the variable Yipq in value storage and the Ki is the constant randomly chosen from the range of 0≤Kij≤Rij. The p and q are used to represent the states of the non-repeatable data selection criteria of nodes set i. Based on the selected optimization criteria, sensor node selection at the selected location is performed by evaluating the data flow volume, sensor energy, and sensor cost as follows:
DFVij(p→q)=DFVi0−∑Pp=1∑Qq=1Aij(p,q)(4)
Eij(p→q)=Ei0+R0Aij(p,q)(5)
cij(p→q)=ci0−∑Pp=1∑Qq=1Aij(p,q)∗Cj(Aij)(6)
As seen in Eqs. (4)–(6), the node selection criteria such as data flow volume DFVij(p→q), sensor energy Eij(p→q), and sensor cost cij(p→q) are computed for the state transition p→q. In Eq. (4), the variable DFVi0 denotes the initial data flow volume for the node-set i, and variable Aij(p,q) describes the server space or the ranging area of the node j in the node-set i for the states p and q, which are included in the state group of maximum P and Q, respectively. In Eq. (5), the variable Ei0 is the initial sensor energy for the node-set i, which is measured with ∑Nj=1Ej0. The variable Ej0 is the sensor energy of the individual node j in the node-set i. In Eq. (6), the sensor cost is computed with the initial cost ci0 of the node-set i, with the sensor coverage area Cj(Aij) in the state space Aij. The following gives the pictorial view of these three basic criteria of optimal node selection.
Fig. 4 pictorizes the statistical derivations of the three basic optimal node selection criteria. The data flow volume must have been the minimum at the transition from p to q with the total server space for all the states computed as ∑Pp=1∑Qq=1Aij(p,q), depicted in Fig. 4a. In Fig. 4b, the sensor energy criterion should be minimum for the state transition from p to q with the minimal ratio of energy coefficient to the server space. As seen in Fig. 4c, the minimal criteria for node selection in terms of sensor cost is computed based on the total coverage volume of all the sensors, ∑Pp=1∑Qq=1Aij(p,q)∗Cj(Aij). Under these above criteria, the optimal node is selected and represented as follows:
Sij(x)=Cj(Aij)β∗Ypq→(0,Cj(Aij))+DFVij(p→q)+Eij(p→q)=S′ij(x)(7)
Figure 4: Optimal node selection criteria (a) Data flow volume, (b) Sensor energy, and (c) Sensor cost
In Eq. (7), the sensor node positioned at x, that represented as Sij(x) has been chosen as the optimal sensor node for the optimized data allocation that further transmits to the cloud data resource reserved for the smart farming system. The optimal sensor node S′ij(x) selection satisfies the condition (0,Cj(Aij))+DFVij(p→q)+Eij(p→q) from Sij(x). Since the proposed DDO algorithm induces the membership parameter, it is to be initialized as:
Fij(p,q)=eDFVij(p→q)∂(sij)∗P∗Q(8)
Eq. (8) defines the initial membership parameter for the state transition from p to q, and represented by Fij(p,q). The membership parameters help identify the association among the states and quantifies it. In this equation, the eDFVij(p→q) measures the exponential value of the data flow volume for the state transition from p to q. The parameter ∂(sij), which is the state momentum has been considered as the state value. The initial membership parameter depends on the total area of node placement in the node-set and is denoted by P∗Q.
(p,q)=eDFVij(p→q)∂(sij)+(P+Q)(9)
In Eq. (9), the final membership parameter for the dynamic data optimization is denoted by F′ij(p,q). In this case, the final membership parameter depends only on the total number of optimal sensor nodes selected in the node-set, denoted by P+Q. To compute the optimized data, the centroid of the state p and state q have been found and computed using the following equations.
Gpij=∑Pp=1Aij(p,q)∑Pp=1∑Qq=1Aij(p,q)(10)
Gqij=∑Qq=1Aij(p,q)∑Pp=1∑Qq=1Aij(p,q)(11)
Eqs. (10) and (11) find the centroids, where Gpij is the centroid for the state p, and Gqij is the centroid for the state q in the ith node-set. In Eq. (10), the numerator ∑Pp=1Aij(p,q) finds the server space for every p states with the area Aij(p,q), whereas the denominator ∑Pp=1∑Qq=1Aij(p,q) computes the total server space. Similarly, for Eq. (11), the computation expression ∑Qq=1Aij(p,q) has been used for finding the server space for every q states with the area Aij(p,q). The centroids are the datapoint used for the optimal data allocation in cloud resources. For every node-set i, the optimal data allocation has been performed and termed as sub-optimal data allocation. This sub-optimal data allocation can be expressed as follows:
OiD=Gpij−GqijFij(p,q)+F′ij(p,q)(12)
OD=∑Mi=1OiD(13)
As seen in Eq. (12), the sub-optimized data can be computed by finding the argument minimum argargGpij−GqijFij(p,q)+F′ij(p,q), of the relation among centroids and the membership parameters. The d0 is the initial data in the optimal cloud resource, and the final optimized data allocation OD can be obtained by aggregating all the sub-optimized data, as seen in Eq. (13).
In summary, this elaborated section included the proposed ICISF-DDO framework and the layered architecture having three significant layers such as front-end layer, the back-end layer, and the gateway layer. After designing these, the DDO algorithm is presented, and the steps in the proposed algorithm are detailed. The entire research model is designed to ensure the IoT-assisted smart farming system with intelligent information handling for reliable performance. The following section includes the validation details in terms of many significant evaluation parameters. It compares the results from the simulation with existing smart farming models.
The experimental validation is performed on a ThingsBoard platform installed on a system with specifications as CPU of Intel CoreTM i5-3470 3.2 GHz, storage of RAM 8 GB, and the operating system Ubuntu 16.04.03 LTS. The simulation scenario and its parameters are set as follows:
Tab. 1 gives the simulation parameters set for the experimental validation. Based on these parameters, the research model is evaluated on a dataset from GitHub (https://github.com/sb-cloudscience/smart-farming-poc-data). The number of sensor nodes is selected in varying numbers from 5 to 50 to perform an iterated assessment. The data optimization with optimized data allocation in varying times is implemented for the efficiency of the proposed ICISF-DDO in dynamic nature is illustrated in Tab. 2. The following results observed the optimal data allocation rate, efficient energy consumption ratio, lifetime, reliability ratio, coverage ratio, and sensor error rate compared with that of existing models. These metrics are evaluated in two different cases: the varying number of sensor nodes and varying time slots of observation (2 h of observation classified into five-time slots of equal division).
As seen in Fig. 5, the optimization rate over a number of sensor nodes and the time slots shows the highest performance by giving a minimum allocation rate compared to existing models. The optimization ratio is computed by analyzing the optimal data allocation rate over available memory resources. The highest optimization ratio with optimal data allocation or minimal data allocation rate for the proposed ICISF is about 97.71% when the number of nodes is fixed at 25, as seen in Fig. 5a. For Fig. 5b, the number of nodes is fixed to 25, which gives the best optimization results and observes the optimization ratio over five different time slots. The optimization ratio of data allocation is significant in the evaluation since it validates the optimized energy consumption and thus improves the lifetime and the data optimization rate for each sensor node calculation is obtained from Eq. (8). The following shows the experimental outcomes of the energy consumption ratio.
Figure 5: Optimization ratio (a) Over number of sensor nodes and (b) Time slots
Fig. 6 evaluates the energy consumption ratio of the proposed ICISF-DDO compared with existing smart farming frameworks. Each transition through sensors consumes some amount of energy as shown in Tab. 2. Data transmission from sensor nodes to sink nodes and gateway takes a crucial amount of overall energy in traditional IoT-cloud systems. In Algorithm 1, for all sensor nodes pair in the smart farming environment the optimized data is computed based on the data flow volume. According to the data flow and data optimization energy consumption rate of the propsed ICISF-DDO explained in Fig. 6.
Figure 6: Energy consumption ratio (a) Over number of sensor nodes and (b) Time slots
In this novel approach of ICISF-DDO, the optimized data allocation ensures the lowest average energy consumption ratio of 4.84%. Figs. 6a and 6b validates the energy consumption ratio of the proposed ICISF-DDO at the number of sensor nodes is 5 and at the time slot of 5, respectively.
Fig. 7 depicts the comparative evaluation of the reliability ratio of the proposed ICISF-DDO. In the proposed IoT-assisted smart farming system, quantifying their reliability is crucial. The IoT-cloud system lifespan diminishes as the data is continually sent to the sink nodes and gateways without data optimization. The optimal allocation of data can enhance the durability and, therefore, network reliability. When the optimization ratio of the IoT-cloud systems improves, the reliability of the system thus increases. In the above figure, it is obvious that the proposed ICISF-DDO can ensure the highest reliability ratio compared to existing models in real-time implementation. The highest reliability ratio of 98.63% is observed for the proposed ICISF-DDO while choosing 45 sensor nodes. The highest reliability ratio is achieved when the highest data optimization is achieved with lesser energy consumption among the utilized sensor nodes.
Figure 7: Reliability ratio (%) Over varying number of sensor nodes
Tab. 3 includes the network coverage ratio and the sensor error rate of the proposed ICISF-DDO compared to existing models. As seen in the above table, the proposed ICISF-DDO results in the highest coverage ratio of 99.67%, with the least sensor error rate of 8.96%. The above results on network coverage ratio are measured as the average coverage ratios of the sensor nodes. The highest average coverage ratio gives lesser sensor error rate and highest reliability rate as shown in Tab. 3. The highest coverage ratio over the least ratio of 78%, 54% is observed when 35 sensor nodes are selected for the simulation. The highest data optimization ratio achieves greater average coverage ratio with lesser sensor error rate and the result stage in shown in Tab. 3. The simulation analysis observed the major limitation of the proposal as the network and data security of IoT-assisted smart farming system over the highest reliability.
In this research, a novel Information-Centric IoT-based Smart Farming with Dynamic Data Optimization (ICISF-DDO) was designed with the conceptual framework. The proposed approach concentrated on the design of the DDO algorithm and its statistical explanation. Since many researchers failed to ensure the lowest energy consumption and improved lifetime by ensuring the optimal data allocation, this research model can outperform the existing models. The simulation analysis found that the ICISF-DDO could ensure the highest data optimization ratio of 97.71%, reliability ratio of 98.63%, a coverage ratio of 99.67%, least sensor error rate of 8.96%, and efficient energy consumption ratio of 4.84% in the real-time implementation. Since this research found the limitation in network security and data security, the future scope of this research is planned to integrate intrusion detection model using deep learning and data security model through blockchain technology integration.
Funding Statement: The authors received no specific funding for this study.
Conflicts of Interest: The authors declare that they have no conflicts of interest to report regarding the present study.
References
1. I. Charania and X. Li, “Smart farming: Agriculture’s shift from a labor intensive to technology native industry,” Internet of Things, vol. 9, pp. 100142, 2020. [Google Scholar]
2. M. Mahbub, “A smart farming concept based on smart embedded electronics, internet of things and wireless sensor network,” Internet of Things, vol. 9, pp. 100161, 2020. [Google Scholar]
3. R. Alfred, J. H. Obit, C. C. P. Yee, H. Haviluddin and Y. Lim, “Towards paddy rice smart farming: A review on big data, machine learning and rice production tasks,” IEEE Access, vol. 9, pp. 50358–50380, 2021. [Google Scholar]
4. K. Demestichas, N. Peppes and T. Alexakis,“Survey on security threats in agricultural IoT and smart farming,” Sensors, vol. 20, no. 22, pp. 6458, 2020. [Google Scholar]
5. A. W. Malik, A. U. Rahman, T. Qayyum and S. D. Ravana, “Leveraging fog computing for sustainable smart farming using distributed simulation,” IEEE Internet of Things Journal, vol. 7, no. 4, pp. 3300–3309, 2020. [Google Scholar]
6. Y. Adhitya, S. W. Prakosa, M. Köppen and J. S. Leu, “Feature extraction for cocoa bean digital image classification prediction for smart farming application,” Agronomy, vol. 10, no. 11, pp. 1642, 2020. [Google Scholar]
7. A. Khan, T. Ilyas, M. Umraiz, Z. I. Mannan and H. Kim, “Ced-net: Crops and weeds segmentation for smart farming using a small cascaded encoder-decoder architecture,” Electronics, vol. 9, no. 10, pp. 1602, 2020. [Google Scholar]
8. N. Islam, M. M. Rashid, F. Pasandideh, B. Ray, S. Moore et al., “A review of applications and communication technologies for internet of things (IoT) and unmanned aerial vehicle (UAV) based sustainable smart farming,” Sustainability, vol. 13, no. 4, pp. 1821, 2021. [Google Scholar]
9. E. Skotadis, A. Kanaris, E. Aslanidis, P. Michalis, P. Kalatzis et al., “A sensing approach for automated and real-time pesticide detection in the scope of smart-farming,” Computers and Electronics in Agriculture, vol. 178, pp. 105759, 2020. [Google Scholar]
10. F. Shamrat, M. Asaduzzaman, P. Ghosh, M. D. Sultan and Z. Tasnim, “A web based application for agriculture:Smart farming system,” International Journal of Emerging Trends in Engineering Research, vol. 8, no. 6, pp. 2309–2320, 2020. [Google Scholar]
11. A. Rehman, J. Liu, L. Keqiu, A. Mateen and M. Q. Yasin, “Machine learning prediction analysis using IoT for smart farming,” International Journal of Emerging Trends in Engineering Research, vol. 8, no. 9, pp. 6482–6487, 2020. [Google Scholar]
12. S. Lieder and C. Schröter-Schlaack, “Smart farming technologies in arable farming: Towards a holistic assessment of opportunities and risks,” Sustainability, vol. 13, no. 12, pp. 6783, 2021. [Google Scholar]
13. S. Duangsuwan, C. Teekapakvisit and M. M. Maw, “Development of soil moisture monitoring by using IoT and UAV-SC for smart farming application,” Advances in Science, Technology and Engineering Systems Journal (ASTESJ), vol. 5, no. 4, pp. 381–387, 2020. [Google Scholar]
14. F. N. Fote, S. Mahmoudi, A. Roukh and S. A. Mahmoudi, “Big data storage and analysis for smart farming,” in 2020 5th Int. Conf. on Cloud Computing and Artificial Intelligence: Technologies and Applications (CloudTech), Morocco, IEEE, pp. 1–8, 2020. [Google Scholar]
15. A. Roukh, F. N. Fote, S. A. Mahmoudi and S. Mahmoudi, “Big data processing architecture for smart farming,” Procedia Computer Science, vol. 177, pp. 78–85, 2020. [Google Scholar]
16. D. S. Paraforos, V. Vassiliadis, D. Kortenbruck, K. Stamkopoulos, V. Ziogas et al., “A farm management information system using future internet technologies,” IFAC-PapersOnLine, vol. 49, no. 16, pp. 324–329, 2016. [Google Scholar]
17. A. Almomani, A. Al-Nawasrah, M. Al-Abweh and B. B. Gupta, “Building safety and security smart home and farm system, based on information management and IoT technology,” Journal of Global Information Management (JGIM), vol. 29, no. 6, pp. 1–23, 2021. [Google Scholar]
18. E. M. Ouafiq, A. Elrharras, A. Mehdary, A. Chehri, R. Saadane et al., “IoT in smart farming analytics, big data based architecture,” in Human Centred Intelligent Systems, Singapore, Springer, pp. 269–279. 2021. [Google Scholar]
19. D. Siddharth, D. K. Saini and A. Kumar, “Precision agriculture with technologies for smart farming towards agriculture 5.0,” in Unmanned Aerial Vehicles for Internet of Things (IoTConcepts, Techniques, and Applications, Scrivener Publishing, Beverly, USA, pp. 247–273, 2021. [Online]. Available: https://onlinelibrary.wiley.com/doi/abs/10.1002/9781119769170.ch14. [Google Scholar]
20. L. Tang and Y. Meng, “Data analytics and optimization for smart industry,” Frontiers of Engineering Management, vol. 8, no. 2, pp. 157–171, 2021. [Google Scholar]
21. L. Abualigah, A. H. Gandomi, M. A. Elaziz, H. A. Hamad, M. Omari et al., “Advances in meta-heuristic optimization algorithms in big data text clustering,” Electronics, vol. 10, no.2, pp. 101, 2021. [Google Scholar]
22. P. Buneman, S. Davidson, G. Hillebrand and D. Suciu, “A query language and optimization techniques for unstructured data,” in Proc. of the 1996 ACM SIGMOD Int. Conf. on Management of Data, ACM, Montreal, Canada, pp. 505–516, 1996. [Google Scholar]
23. A. Schwarte, P. Haase, K. Hose, R. Schenkel and M. Schmidt, “Fedx: Optimization techniques for federated query processing on linked data,” in Int. Semantic web Conf., Berlin, Heidelberg, Springer, pp. 601–616, 2011. [Google Scholar]
24. A. Dahane, R. Benameur, B. Kechar and A. Benyamina, “An IoT based smart farming system using machine learning,” in Proc. of the Int. Symp. on Networks, Computers and Communications (ISNCC), Montreal, Canada, IEEE, pp. 1–6, 2020. [Google Scholar]
25. S. V. Gaikwad, A. D. Vibhute, K. V. Kale and S. C. Mehrotra, “An innovative IoT based system for precision farming,” Computers and Electronics in Agriculture, vol. 187, pp. 106291, 2021. [Google Scholar]
26. M. Saqib, T. A. Almohamad and R. M. Mehmood, “A Low-cost information monitoring system for smart farming applications,” Sensors, vol. 20, no. 8, pp. 2367, 2020. [Google Scholar]
27. E. Adetiba, C. F. Olumba, A. H. Ifijeh, E. Noma-Osaghae, J. N. Adetiba et al., “Internet of things and farm management information system for precision agriculture: A proof of concept circuit, simulation and web app,” Preprints 2021, 2021030457, 2021. [Google Scholar]
28. X. R. Zhang, X. Chen, W. Sun, and X. Z. He, “Vehicle re-identification model based on optimized DenseNet121 with joint loss,” Computers, Materials & Continua, vol. 67, no. 3, pp. 3933–3948, 2021. [Google Scholar]
29. S. Doss, J. Paranthaman, S. Gopalakrishnan, D. Akila, S. Pal et al., “Memetic optimization with cryptographic encryption for secure medical data transmission in IoT-based distributed systems,” Computers, Material & Continua, vol. 66, No no. 2, pp. 1577–1594, 2020. [Google Scholar]
30. S. Sahana, D. Singh, S. Pal and D. Sarddar, “A design of IoT-based agricultural system for optimal management,” in Pattnaik P., Kumar R., Pal S., Panda S. (eds) IoT and Analytics for Agriculture. Studies in Big Data, Singapore, Springer, vol. 63, pp. 211–227, 2020. https://doi.org/10.1007/978-981-13-9177-4_10. [Google Scholar]
Cite This Article
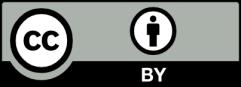
This work is licensed under a Creative Commons Attribution 4.0 International License , which permits unrestricted use, distribution, and reproduction in any medium, provided the original work is properly cited.