Open Access
ARTICLE
Thermomechanical Behavior of Brake Drums Under Extreme Braking Conditions
1 Institute of Science and Technology, University Center Salhi Ahmed Naama, Algeria
2 Laboratory of Gas Combustion and Environment, University of Sciences and Technology of Oran, L.P 1505 El-Menaouer, Oran, USTO 31000, Algeria
3 High School of Aeronautic Techniques Dar El Beida, Algeria
4 Ho Chi Minh City Open University, Ho Chi Minh City, Viet Nam
5 Faculty of Engineering, Van Lang University, Ho Chi Minh City, Vietnam
6 Soete Laboratory, Faculty of Engineering and Architecture, Ghent University, TechnologieparkZwijnaarde 903, B-9052 Zwijnaarde, Belgium
* Corresponding Author: M. Abdel Wahab. Email:
Computers, Materials & Continua 2022, 72(2), 2259-2273. https://doi.org/10.32604/cmc.2022.020879
Received 12 June 2021; Accepted 30 December 2021; Issue published 29 March 2022
Abstract
Braking efficiency is characterized by reduced braking time and distance, and therefore passenger safety depends on the design of the braking system. During the braking of a vehicle, the braking system must dissipate the kinetic energy by transforming it into heat energy. A too high temperature can lead to an almost total loss of braking efficiency. An excessive rise in brake temperature can also cause surface cracks extending to the outside edge of the drum friction surface. Heat transfer and temperature gradient, not to forget the vehicle's travel environment (high speed, heavy load, and steeply sloping road conditions), must thus be the essential criteria for any brake system design. The aim of the present investigation is to analyze the thermal behavior of different brake drum designs during the single emergency braking of a heavy-duty vehicle on a steeply sloping road. The calculation of the temperature field is performed in transient mode using a three-dimensional finite element model assuming a constant coefficient of friction. In this study, the influence of geometrical brake drum configurations on the thermal behavior of brake drums with two different materials in grey cast iron FG200 and aluminum alloy 356.0 reinforced with silicon carbide (SiC) particles is analyzed under extreme vehicle braking conditions. The numerical simulation results obtained using FE software ANSYS are qualitatively compared with the results already published in the literature.Keywords
Cite This Article
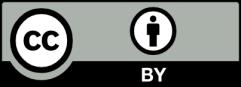
This work is licensed under a Creative Commons Attribution 4.0 International License , which permits unrestricted use, distribution, and reproduction in any medium, provided the original work is properly cited.