Open Access
ARTICLE
Modeling and Optimization of Surface Roughness of Epoxy/Nanoparticles Composite Coating
1 Department of Mechanical Engineering, College of Engineering & Islamic Arch., Umm Alqura University, Makkah, Saudi Arabia
2 Department of Mechanical Engineering, Faculty of Engineering, Sohag University, Sohag, Egypt
3 Department of Systems Engineering, King Fahd University of Petroleum & Minerals, Dhahran, 31261, KSA
4 College of Engineering at Wadi Addawaser, Prince Sattam Bin Abdulaziz University, Al-Kharj, 11911, Saudi Arabia
5 Department of Electrical Engineering, Faculty of Engineering, Minia University, Minia, 61517, Egypt
6 Department of Production Engineering and Design, Faculty of Engineering, Minia University, Minia, 61517, Egypt
* Corresponding Author: Mujahed Al-Dhaifallah. Email:
Computers, Materials & Continua 2022, 71(1), 71-83. https://doi.org/10.32604/cmc.2022.019257
Received 08 April 2021; Accepted 10 May 2021; Issue published 03 November 2021
Abstract
In power plants, flue gases can cause severe corrosion damage in metallic parts such as flue ducts, heat exchangers, and boilers. Coating is an effective technique to prevent this damage. A robust fuzzy model of the surface roughness (Ra and Rz) of flue gas ducts coated by protective composite coating from epoxy and nanoparticles was constructed based on the experimental dataset. The proposed model consists of four nanoparticles (ZnO, ZrO2, SiO2, and NiO) with 2%, 4%, 6%, and 8%, respectively. Response surface methodology (RSM) was used to optimize the process parameters and identify the optimal conditions for minimum surface roughness of this coated duct. To prove the superiority of the proposed fuzzy model, the model results were compared with those obtained by ANOVA, with the coefficient of determination and the root-mean-square error (RMSE) used as metrics. For Ra, for the first output response, using ANOVA, the coefficient-of-determination values were 0.9137 and 0.4037, respectively, for training and prediction. Similarly, for Rz, the second output response, the coefficient-of-determination results were 0.9695 and 0.4037, respectively, for training and prediction. In the fuzzy modeling of Ra, for the first output response, the RMSE values were 0.0 and 0.1455, respectively, for training and testing. The values for the coefficient of determination were 1.00 and 0.9807, respectively, for training and testing. The results prove the superiority of fuzzy modeling. For modeling the second output response Rz, the RMSE values were 0.0 and 0.0421, respectively, for training and testing, and the coefficient-of-determination values were 1.00 and 0.9959, respectively, for training and testing.Keywords
Cite This Article
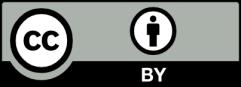
This work is licensed under a Creative Commons Attribution 4.0 International License , which permits unrestricted use, distribution, and reproduction in any medium, provided the original work is properly cited.