Open Access
ARTICLE
Simulation of Non-Isothermal Turbulent Flows Through Circular Rings of Steel
1 Department of Mathematics and Social Sciences, Sukkur IBA University, Sukkur, 65200, Sindh, Pakistan
2 Department of Mathematics, Faculty of Science, Khon Kaen University, Khon Kaen, 40002, Thailand
3 Department of Mathematics, College of Science Al-Zulfi, Majmaah University, Al-Majmaah, 11952, Saudi Arabia
* Corresponding Author: Kamsing Nonlaopon. Email:
(This article belongs to the Special Issue: Role of Computer in Modelling & Solving Real-World Problems)
Computers, Materials & Continua 2022, 70(3), 4341-4355. https://doi.org/10.32604/cmc.2022.019407
Received 12 April 2021; Accepted 15 June 2021; Issue published 11 October 2021
Abstract
This article is intended to examine the fluid flow patterns and heat transfer in a rectangular channel embedded with three semi-circular cylinders comprised of steel at the boundaries. Such an organization is used to generate the heat exchangers with tube and shell because of the production of more turbulence due to zigzag path which is in favor of rapid heat transformation. Because of little maintenance, the heat exchanger of such type is extensively used. Here, we generate simulation of flow and heat transfer using non-isothermal flow interface in the Comsol multiphysics 5.4 which executes the Reynolds averaged Navier stokes equation (RANS) model of the turbulent flow together with heat equation. Simulation is tested with Prandtl number (Pr = 0.7) with inlet velocity magnitude in the range from 1 to 2 m/sec which generates the Reynolds number in the range of 2.2 × 105 to 4.4 × 105 with turbulence kinetic energy and the dissipation rate in ranges (3.75 × 10−3 to 1.5 × 10−2) and (3.73 × 10−3−3 × 10−2) respectively. Two correlations available in the literature are used in order to check validity. The results are displayed through streamlines, surface plots, contour plots, isothermal lines, and graphs. It is concluded that by retaining such an arrangement a quick distribution of the temperature over the domain can be seen and also the velocity magnitude is increasing from 333.15% to a maximum of 514%. The temperature at the middle shows the consistency in value but declines immediately at the end. This process becomes faster with the decrease in inlet velocity magnitude.Keywords
Cite This Article
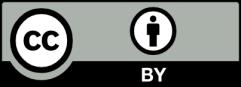
This work is licensed under a Creative Commons Attribution 4.0 International License , which permits unrestricted use, distribution, and reproduction in any medium, provided the original work is properly cited.