Open Access
ARTICLE
Thermodynamic Simulation on the Change in Phase for Carburizing Process
1 Ho Chi Minh city University of Technology (HUTECH), Ho, Vietnam
2 Ho Chi Minh city University of Transport, Ho Chi Minh city, Vietnam
3 Al-Nahrain University, Al-Nahrain Nanorenewable Energy Research Center, Baghdad, Iraq
4 Hanoi University of Science and Technology, Hanoi, Vietnam
5 Industrial University of Ho Chi Minh City (IUH), Ho Chi Minh city, Vietnam
6 Vietnam Maritime University, Haiphong, Vietnam
* Corresponding Author: Duong Nam Nguyen. Email:
(This article belongs to the Special Issue: Application of Big Data Analytics in the Management of Business)
Computers, Materials & Continua 2021, 68(1), 1129-1145. https://doi.org/10.32604/cmc.2021.015349
Received 16 November 2020; Accepted 03 January 2021; Issue published 22 March 2021
Abstract
The type of technology used to strengthen the surface structure of machine parts, typically by carbon-permeation, has made a great contribution to the mechanical engineering industry because of its outstanding advantages in corrosion resistance and enhanced mechanical and physical properties. Furthermore, carbon permeation is considered as an optimal method of heat treatment through the diffusion of carbon atoms into the surface of alloy steel. This study presented research results on the thermodynamic calculation and simulation of the carbon permeability process. Applying Fick’s law, the paper calculated the distribution of carbon concentration in the alloy steel after it is absorbed from the surface into the internal of the sample. Using the SYSWELD software, an analysis was performed on the carbon permeability process to determine the distribution of carbon concentrations in 20CrMo steel that was then followed by a detailed analysis of the microstructure of the sample post the carburizing process. According to the calculation results, the surface carbon content was 0.9% and steadily decreased into the core. After 3 hours, the depth of the absorbent layer was measured at 0.5 mm for both the cylindrical and cubic samples. By analyzing the phase, the distribution of martensite phases such as ferrite/pearlite and residual austenite was also determined after the carburizing process.Keywords
Cite This Article
Citations
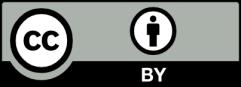
This work is licensed under a Creative Commons Attribution 4.0 International License , which permits unrestricted use, distribution, and reproduction in any medium, provided the original work is properly cited.