Open Access
ARTICLE
A New Metaheuristic Optimization Algorithms for Brushless Direct Current Wheel Motor Design Problem
1 Department of Electrical and Electronics Engineering, GMR Institute of Technology, Rajam, 532127, India
2 Department of Electrical and Electronics Engineering, National Institute of Technology, Tiruchirappalli, 620015, India
3 Rajasthan Rajya Vidyut Prasaran Nigam, Sikar, 305001, India
4 Department of Mathematics, College of Arts and Sciences, Prince Sattam bin Abdulaziz University, Wadi Aldawaser, 11991, Saudi Arabia
5 Systems Engineering Department, King Fahd University of Petroleum & Minerals, Dhahran, Saudi Arabia
* Corresponding Author: Kottakkaran Sooppy Nisar. Email:
(This article belongs to the Special Issue: Role of Computer in Modelling & Solving Real-World Problems)
Computers, Materials & Continua 2021, 67(2), 2227-2242. https://doi.org/10.32604/cmc.2021.015565
Received 08 November 2020; Accepted 18 December 2020; Issue published 05 February 2021
Abstract
The Equilibrium Optimizer (EO), Grey Wolf Optimizer (GWO), and Whale Optimizer (WO) algorithms are being recently developed for engineering optimization problems. In this paper, the EO, GWO, and WO algorithms are applied individually for a brushless direct current (BLDC) design optimization problem. The EO algorithm is inspired by the models utilized to find the system’s dynamic state and equilibrium state. The GWO and WO algorithms are inspired by the hunting behavior of the wolf and the whale, respectively. The primary purpose of any optimization technique is to find the optimal configuration by maximizing motor efficiency and/or minimizing the total mass. Therefore, two objective functions are being used to achieve these objectives. The first refers to a design with high power output and efficiency. The second is a constraint imposed by the reality that the motor is built into the wheel of the vehicle and, therefore, a lightweight is needed. The EO, GWO, and WOA algorithms are then utilized to optimize the BLDC motor’s design variables to minimize the motor’s total mass or maximize the motor efficiency by simultaneously satisfying the six inequality constraints. The simulation is carried out using MATLAB simulation software, and the simulation results prove the dominance of the proposed algorithms. This paper also suggests an efficient method from the proposed three methods for the BLDC motor design optimization problem.Keywords
Cite This Article
Citations
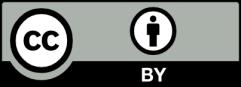
This work is licensed under a Creative Commons Attribution 4.0 International License , which permits unrestricted use, distribution, and reproduction in any medium, provided the original work is properly cited.