Open Access
ARTICLE
Prediction of Melt Pool Dimension and Residual Stress Evolution with Thermodynamically-Consistent Phase Field and Consolidation Models during Re-Melting Process of SLM
1 Department of Aerospace Engineering, Seoul National University, Seoul, 08826, South Korea
2 Institute of Advanced Aerospace Technology, Seoul National University, Seoul, 08826, South Korea
* Corresponding Author: Gun Jin Yun. Email:
Computers, Materials & Continua 2021, 66(1), 87-112. https://doi.org/10.32604/cmc.2020.012688
Received 09 July 2020; Accepted 17 August 2020; Issue published 30 October 2020
Abstract
Re-melting process has been utilized to mitigate the residual stress level in the selective laser melting (SLM) process in recent years. However, the complex consolidation mechanism of powder and the different material behavior after the first laser melting hinder the direct implementation of the re-melting process. In this work, the effects of re-melting on the temperature and residual stress evolution in the SLM process are investigated using a thermo-mechanically coupled finite element model. The degree of consolidation is incorporated in the energy balance equation based on the thermodynamically-consistent phase-field approach. The drastic change of material properties due to the variation of temperature and material state is also considered. Using the proposed simulation framework, the single-track scanning is simulated first to predict the melt pool dimension and validate the proposed model with the existing experimental data. The obtained thermal histories reveal that the highest cooling rate is observed at the end of the local solidification time which acts as an important indicator for the alleviation of temperature gradient. Then, the scanning of a whole single layer that consists of multiple tracks is simulated to observe the stress evolution with several re-melting processes. After the full melting of powder material in the first scanning process, the increase of residual stress level is observed with one remelting cycle. Moreover, the predicted stress level with the re-melting process shows the variation trend attributable to the accumulated heat in the tracks. The numerical issues and the detailed implementation process are also introduced in this paper.Keywords
Cite This Article
Citations
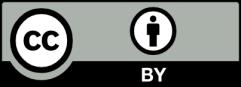
This work is licensed under a Creative Commons Attribution 4.0 International License , which permits unrestricted use, distribution, and reproduction in any medium, provided the original work is properly cited.