Open Access
REVIEW
Review on the Prediction of Residual Stress in Welded Steel Components
1 Soete Laboratory, Faculty of Engineering and Architecture, Ghent University, Ghent, Belgium.
2 Institute of Forming Technology and Equipment, School of Materials Science and Engineering, Shanghai Jiao Tong University, Shanghai, China.
3 National Engineering Research Center of Die & Mold CAD, Shanghai Jiao Tong University, Shanghai, China.
4 Division of Computational Mechanics, Ton Duc Thang University, Ho Chi Minh, Vietnam.
5 Faculty of Civil Engineering, Ton Duc Thang University, Ho Chi Minh, Vietnam.
* Corresponding Author: Magd Abdel Wahab. Email: .
Computers, Materials & Continua 2020, 62(2), 495-523. https://doi.org/10.32604/cmc.2020.08448
Abstract
Residual stress after welding has negative effects on the service life of welded steel components or structures. This work reviews three most commonly used methods for predicting residual stress, namely, empirical, semi-empirical and process simulation methods. Basic principles adopted by these methods are introduced. The features and limitations of each method are discussed as well. The empirical method is the most practical but its accuracy relies heavily on experiments. Mechanical theories are employed in the semi-empirical method, while other aspects, such as temperature variation and phase transformation, are simply ignored. The process simulation method has been widely used due to its capability of handling with large and complex components. To improve its accuracy and efficiency, several improvements need to be done for each simulation aspect of this method.Keywords
Cite This Article
Citations
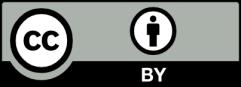
This work is licensed under a Creative Commons Attribution 4.0 International License , which permits unrestricted use, distribution, and reproduction in any medium, provided the original work is properly cited.