Open Access
ARTICLE
SGBEM Voronoi Cells (SVCs), with Embedded Arbitrary-Shaped Inclusions, Voids, and/or Cracks, for Micromechanical Modeling of Heterogeneous Materials
Center for Aerospace Research & Education, University of California, Irvine
Department of Engineering Mechanics, Hohai University
Distinguished Adjunct-Professor of Multi-Disciplinary Engineering and Computer Science, King Abdulaziz University, Saudi Arabia
Computers, Materials & Continua 2013, 33(2), 111-154. https://doi.org/10.3970/cmc.2013.033.111
Abstract
In this study, SGBEM Voronoi Cells (SVCs), with each cell representing a grain of the material at the micro-level, are developed for direct micromechanical numerical modeling of heterogeneous composites. Each SVC can consist of either a (each with a different) homogenous isotropic matrix, and can include micro-inhomogeneities such as inclusions, voids of a different material, and cracks. These inclusions and voids in each SVC can be arbitrarily-shaped, such as circular, elliptical, polygonal, etc., for 2D problems. Further, the cracks in each SVC can be fully-embedded, edge, branching, or intersecting types, with arbitrary curved shapes. By rearranging the weakly-singular boundary integral equations, a stiffness matrix and a force vector are developed for each SVC with inclusions, voids, and micro-cracks. The stiffness matrix of each SVC is symmetric, positive semidefinite, and has the correct number of rigid-body modes. The stiffness matrix of each SVC and the force vector can also be interpreted to have the same physical meaning as in traditional displacement finite elements, and related to strain energy and the work done. Therefore, the direct coupling of different SVCs (each with a different isotropic material property, and each with heterogeneities of a different material), or the coupling of SVCs with other traditional or special elements, can be achieved by the usual assembly procedure. Moreover, because the heterogeneous micro-structures are modeled directly in the most natural way, as in the present work, by using an SVC to model each grain, one not only saves the labor of meshing and re-meshing, but also reduces the computational burden by several orders of magnitude as compared to the usual FEM. Through several numerical examples, we demonstrate that the SVCs are useful in not only estimating the overall stiffness properties of heterogeneous composite materials, but they are most useful in capturing the local stress concentrations and singularities in each grain, which act as damage precursors, efficiently. Several examples of interaction of cracks with inclusions and voids within each SVC (or material grain) are also presented. Accurate results are obtained for stress intensity factors. Non-collinear fatigue growth of micro-cracks in heterogeneous materialis also modeled very efficiently, with these SVCs, without a need for the complicated re-meshing as is common when using the traditional displacement-based finite element methods.Keywords
Cite This Article
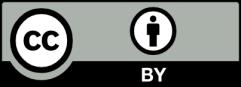
This work is licensed under a Creative Commons Attribution 4.0 International License , which permits unrestricted use, distribution, and reproduction in any medium, provided the original work is properly cited.