Open Access
ARTICLE
Analysis and Experiment on Incremental Forming Process for the Spiral Plate of Continuous Screw Conveyer
Iwaki Meisei University, Iwaki, Fukushima, Japan
Hiroshima Kokusai Gakuin University, Aki, Hiroshima, Japan
Worm Japan Co. Ltd., Iwaki, Fukushima, Japan
AUT, School of Engineering Reception, Auckland Central, New Zealand
Computers, Materials & Continua 2011, 22(1), 39-54. https://doi.org/10.3970/cmc.2011.022.039
Abstract
An incremental press-forming method was newly developed for the fabrication of spiral plates of a continuous screw conveyer, boring screw, screw pump and so on. In this method, a pair of V-shaped punches and dies with two opposite inclined edges are used instead of punch and die with spiral surfaces. The experiments on incremental forming were carried out on aluminum alloy and steel disks with a hole and a slit, and the deformation process of the plate during and after the press-forming was simulated by a finite element method (FEM). The press-forming shows that the spiral plate has a correct shape and smooth surface, i. e. the gradient of the surface along the internal, central, and external spiral curves of the deformed disk is constant. In addition, the spiral pitch and the amount of spring back obtained by the FEM simulation agree well with the experimental values for the different die or punch angles, the disk thicknesses and the disk materials. The FEM calculation also indicates that the equivalent stress during the press forming as well as the residual stress after the spring back takes a maximum value at an internal diameter position where the die or punch makes first contact to the disk.Keywords
Cite This Article
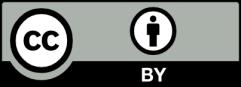
This work is licensed under a Creative Commons Attribution 4.0 International License , which permits unrestricted use, distribution, and reproduction in any medium, provided the original work is properly cited.