Open Access
ARTICLE
3-D Modeling of a composite material reinforced with multiple thickly coated particles using the infinite element method
Computer Modeling in Engineering & Sciences 2005, 9(2), 179-192. https://doi.org/10.3970/cmes.2005.009.179
Abstract
A three-dimensional heterogeneous infinite element method (HIEM) for modeling inclusions with interphases in composite materials is presented. This special element is formulated based on the conventional finite element method (FEM) using the similarity stiffness property and matrix condensation operations. An HIE-FE coupling scheme is also developed and implemented using the commercial software ABAQUS to conduct the elastostatic analysis. The proposed approach was validated first to study heterogeneous material containing one spherical inclusion. The displacement and stress variations around the inclusion vicinity are verified against conventional FEM. The proposed approach was next applied to analyze the effective modulus of single-particle and 2×2×2-particles cubic models with the presence of interphases. The effects of varying the modulus and thickness of the interphase are also examined. The influences of multiple inclusion orientation arrangements are investigated. The results show that different model orientation arrangements can have marked influences on the effective elastic modulus evaluation for particulate-reinforced composites.Keywords
Cite This Article
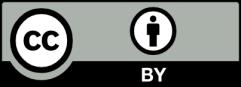
This work is licensed under a Creative Commons Attribution 4.0 International License , which permits unrestricted use, distribution, and reproduction in any medium, provided the original work is properly cited.