Open Access
ARTICLE
Numerical Investigation on Dynamical Response of Aluminum Foam Subject to Hypervelocity Impact With Material Point Method
Computer Modeling in Engineering & Sciences 2012, 83(5), 527-546. https://doi.org/10.3970/cmes.2012.083.527
Abstract
Owing to its low density and good energy absorption capability, aluminum foam is an excellent protective material for spacecraft against debris impact. However, because of its complicated microstructure, it is very difficult to generate a FEM mesh accounting for the real microstructure of the alluminum foam. On the contrary, it is very easy to model three-dimensional problems with very complicated geometry with meshfree/meshless methods. Furthermore, the material point method has obvious advantages in modeling problems involving extreme large deformation problems like hypervelocity impact problem. In this paper, a three-dimensional material point model accounting for the real microsctructure of aluminum foam is created based on the scanned CT images, and is used to study the protective capacity of aluminum foam in different Whipple shield structures using our three-dimensional material point method code, MPM3D. The simulation results agree well with the experimental data.Keywords
whipple shield structure, aluminum foam, debris impact, material point method, hypervelocity impact
Cite This Article
APA Style
Gong, W., Liu, Y., Zhang, X., Ma, H. (2012). Numerical Investigation on Dynamical Response of Aluminum Foam Subject to Hypervelocity Impact With Material Point Method. Computer Modeling in Engineering & Sciences, 83(5), 527–546. https://doi.org/10.3970/cmes.2012.083.527
Vancouver Style
Gong W, Liu Y, Zhang X, Ma H. Numerical Investigation on Dynamical Response of Aluminum Foam Subject to Hypervelocity Impact With Material Point Method. Comput Model Eng Sci. 2012;83(5):527–546. https://doi.org/10.3970/cmes.2012.083.527
IEEE Style
W. Gong, Y. Liu, X. Zhang, and H. Ma, “Numerical Investigation on Dynamical Response of Aluminum Foam Subject to Hypervelocity Impact With Material Point Method,” Comput. Model. Eng. Sci., vol. 83, no. 5, pp. 527–546, 2012. https://doi.org/10.3970/cmes.2012.083.527
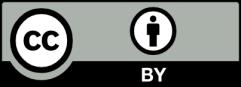
This work is licensed under a Creative Commons Attribution 4.0 International License , which permits unrestricted use, distribution, and reproduction in any medium, provided the original work is properly cited.