Open Access
ARTICLE
Creation of Imperfections for Welding Simulations
Faculty of mechanical engineering, Technical university in Košice, Letná 9, 04200 Košice, Slovakia, e-mail: ladislav.novotny@gmail.com
Structure and Strength Department, Research Laboratory, IHI corporation 1, Shin-Nakahara-cho, Isogo-ku, Yokohama, JAPAN, 235-8501, mitsuyoshi_tsunori@ihi.co.jp
Computer Modeling in Engineering & Sciences 2011, 82(3&4), 253-264. https://doi.org/10.32604/cmes.2011.082.253
Abstract
The welding simulation is carried out by an uncoupled thermal and mechanical analysis or by a coupled thermo-mechanical analysis. For weld-induced distortion and residual stress simulation, nonlinear mechanical analysis is required. Nonlinearities are caused by both nonlinear behaviour of the material and geometrical nonlinearity. Usually, the element birth technique is used to incorporate the filler material in the model. The ideal straight geometry may be altered by imperfections to enable buckling behaviour. Real component shapes contain various imperfections (e.g. geometrical, material). The finite element mesh may contain geometrical imperfections too. When a simple weld model is used, the mode of the end-distortion is predictable. The imperfections are created in the same shape as predicted. The sufficient magnitude of an imperfection is approximately 1/100 of end-distortion. In case that complex weld model shapes are used, it is not easy to predict the correct imperfection shape. For general purpose as well, the common procedure for calculation of correct imperfections shapes is required. In these article a new approach to create imperfections was adopted. The results obtained in the course of this work allowed to calculate resultant welding distorsion more accurate.Keywords
Cite This Article
Citations
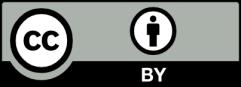
This work is licensed under a Creative Commons Attribution 4.0 International License , which permits unrestricted use, distribution, and reproduction in any medium, provided the original work is properly cited.