Open Access
ARTICLE
Numerical Study of Dynamic Compression Process of Aluminum Foam with Material Point Method
School of Aerospace, Tsinghua University, Beijing 100084, P. R. China.
Corresponding author: xzhang@tsinghua.edu.cn.
Computer Modeling in Engineering & Sciences 2011, 82(3&4), 195-214. https://doi.org/10.32604/cmes.2011.082.195
Abstract
Due to its high strength, low weight and strong anti impact capability, aluminum foam has great potential in the fields of transportation, aerospace and building structures as energy absorbing materials. Due to its complicated microstructures, it is desirable to develop an efficient numerical method to study the dynamic response of the aluminum foam under impact loading. In this paper, the material point method (MPM) is extended to the numerical simulation of the dynamic response of the aluminum foam under impact loading by incorporating the Deshpande Fleck's model and a volumetric strain failure model into our three-dimensional explicit material point method code, MPM3D. The developed method is first validated by comparing the numerical results obtained by MPM3D for a Taylor bar test with those obtained by LS-DYNA, and then is used to simulate the dynamic compression process of aluminum foam material. The numerical results show that the MPM has significant advantages in analyzing the high-speed dynamic characteristics of aluminum foam materials, and can be used in the practical applications of aluminum foam materials.Keywords
Cite This Article
Citations
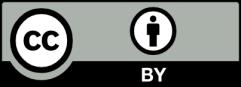
This work is licensed under a Creative Commons Attribution 4.0 International License , which permits unrestricted use, distribution, and reproduction in any medium, provided the original work is properly cited.