Open Access
ARTICLE
An Effective Thermal-mechanical Modeling Methodology for Large-scale Area Array Typed Packages
Associate Professor, Department of Aerospace and Systems Engineering, Feng Chia University, Taichung, Taiwan 407, R.O.C., hccheng@fcu.edu.tw
Graduate Student, Department of Power Mechanical Engineering, National Tsing Hua University, Hsinchu, Taiwan 300, R.O.C.
Professor, Department of Power Mechanical Engineering, National Tsing Hua University, Hsinchu, Taiwan 300, R.O.C., whchen@pme.nthu.edu.tw
Computer Modeling in Engineering & Sciences 2005, 7(1), 1-18. https://doi.org/10.3970/cmes.2005.007.001
Abstract
In this study, a simple but effective solution methodology that integrates a modified global/local finite element (GLFE) modeling technique and a two-staged constitutive modeling strategy is presented for the thermal-mechanical modeling of solder joints in an area array typed electronic package for characterizing the associated solder joint fatigue life under the JEDEC temperature cycling specification. The effectiveness and applicability of the proposed technique are demonstrated through two case studies, each of which is associated with an area array typed test vehicle. The geometry profile of solder joints in the test vehicle is determined by the Surface Evolver [Brakke (1996)]. For benchmark, a baseline finite element (FE) modeling is attempted by a conventional direct FE analysis (DFEA) approach. The DFEA approach employs a 3-D, fine-mesh FE model and a full constitutive law that takes both elastoplasticity and viscoelastic into account. The validity of the proposed thermal-mechanical modeling methodology is confirmed through existing experimental fatigue life data in literature as well as optical, interferometric measurement of the in-plane displacement field performed in this work. It turns out that the proposed methodology can efficiently and accurately deal with solder joint fatigue life prediction for large-scale area array typed electronic packages consisting of a large number of solder joints. In addition, results show that in terms of computational performance and solution accuracy, the methodology incorporating with the simplified constitutive law-Dwell Creep (DC) model could be a very ideal choice.Keywords
Cite This Article
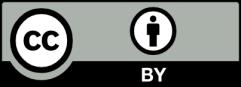
This work is licensed under a Creative Commons Attribution 4.0 International License , which permits unrestricted use, distribution, and reproduction in any medium, provided the original work is properly cited.