Open Access
ARTICLE
Experimental and Numerical Investigation of Instructions for Hyperelastic Membrane Inflation Using Fluid Structure Coupling
Universite de Lille1, LML UMR CNRS 8107 France
Universite du Quebec en Abitibi-Temiscamingue Canada
Computer Modeling in Engineering & Sciences 2011, 77(3&4), 183-200. https://doi.org/10.3970/cmes.2011.077.183
Abstract
During the design process of membrane structure to resist to high pressure loading, and the characterization of hyperelastic material, a structure made up of thin rubber undergoes large deformation and rotation under high pressure loading out of high pressurized gas. Until recently, to simulate the inflation of the hyperelastic membrane, a uniform pressure based on thermodynamic model or experimental tests is applied to the structure, as boundary conditions. From a computational time point of view, this approach is very fast, since no computational fluid dynamics is involved in the simulation. However, at the late stage of the membrane inflation, uniform pressure simulations lead to numerical instability due to the lack of fluid that generates damping effects and prevent numerical instability. Thus the uniform pressure assumption is unstable at the end phase of the inflation for long time duration. To simulate accurately the inflation process, computational fluid dynamics in a moving fluid domain as well as fluid structure interaction (FSI) algorithms need to be performed for accurate pressure prediction and fluid structure interface coupling. For the simulation of gas dynamic in a moving domain, Arbitrary Lagrangian Eulerian (ALE) formulation is used. Both simulations, uniform pressure and ALE simulation for computational gas dynamics, were compared to test data, indicating satisfactory results in terms of correlation for earlier stage of the inflation. However for late stage inflation, simulation using uniform pressure show numerical instability leading to the blow up of the structure. With the more recently developed procedure, ALE theory, shows the greatest accuracy, both in terms of graphical and schematic comparison, especially at the late stage of the inflation process. As a result, the new simulation procedure model can be utilised to research into the effects of changing the designs of the membrane structure to resist to highly pressure loading on soft rubber material.Keywords
Cite This Article
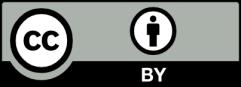
This work is licensed under a Creative Commons Attribution 4.0 International License , which permits unrestricted use, distribution, and reproduction in any medium, provided the original work is properly cited.