Open Access
ARTICLE
Solid Element with Four-Point Integration in Plane for Bulk Forming
State Key Laboratory of Material Processing and Die & Mould Technology, Huazhong University of Science & Technology, Wuhan Hubei 430074
Corresponding author at: State Key Laboratory of Material Processing and Die & Mould Technology, Huazhong University of Science & Technology, 1037 Luoyu Road, Wuhan Hubei 430074, PR China. Tel.: +86 27 87558193; fax: +86 27 87554405. Email: fastamp@vip.sina.com
Computer Modeling in Engineering & Sciences 2009, 51(2), 93-114. https://doi.org/10.3970/cmes.2009.051.093
Abstract
An eight-node hexahedral element with four-point quadrature in plane is developed using the assumed strain method, which can eliminate volumetric locking of incompressible material and absence of the portion of shear velocity strain related with hourglass mode to suppress hourglass mode and shear locking. In this approach, the radial return algorithm is adopted for more precise calculation of internal forces, stress and strain. In addition, a co-rotational coordinates system is established to make bending simulation much more effective, and the system is applicable to arbitrary 3D anisotropic yield criteria. A large elastic-plastic deformation of unconstrained thick plate bending example is then carried out with the comparison between ASQBI and ADS solid element. Numerical results of thick metal plate ironing and cylindrical piece embossing are remarkably identical to experimental results and less computation (only one hours is needed using new element in this examples while 5.5 hours using DEFORM 3D software) and higher accuracy are obtained using this new solid element by comparing with DEFORM 3D's result, which meets the demand of Shenyang Mint.Keywords
Cite This Article
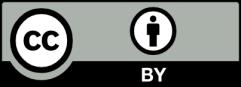
This work is licensed under a Creative Commons Attribution 4.0 International License , which permits unrestricted use, distribution, and reproduction in any medium, provided the original work is properly cited.