Open Access
ARTICLE
Development of a Numerical Toolbox for the Computer Aided Design of Composite Over-Wrapped Pressure Vessels
Dept. Mechanics, Politecnico di Torino, Corso Duca degli Abruzzi, 24; 10129 Torino, Italy; email: eugenio.brusa@polito.it
Former student, nowadays Engineer at Danieli Officine Meccaniche, Buttrio (Ud), Italy; e-mail: m.nobile@danieli.it
Computer Modeling in Engineering & Sciences 2009, 48(2), 155-190. https://doi.org/10.3970/cmes.2009.048.155
Abstract
Lightness of high pressure vessels is currently assured by composite materials. Construction of over-wrapped composite pressure vessels with inner metallic liner is for instance compatible with standards requirements of the hydrogen technology of energy storage. Therefore a typical layout manufactured by some industries consists of a cylindrical vessel with covering of carbon-epoxy laminates and metallic impermeable liner. To allow the filament winding of the composite fibres are used hoop and helical layers, respectively. A single nozzle is usually built. It requires that the vessel material is reinforced. This need imposes to have a variable thickness in the composite layer. In practice, fibres orientation angle and thickness are both variable. These aspects make hard a straight design operation by means of analytical approaches. In this paper a numerical design toolbox is developed. It includes a preliminary definition of the fibres network, found by the so-called netting analysis, the theory of composite laminates and the structural optimisation through the Finite Element Method. An industrial prototype was used as a test case to validate the proposed approach. Burst and auto-frettage pressures for the liner were predicted and a preliminary analysis of the fatigue life was performed.Keywords
Cite This Article
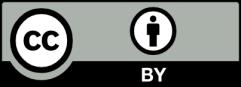
This work is licensed under a Creative Commons Attribution 4.0 International License , which permits unrestricted use, distribution, and reproduction in any medium, provided the original work is properly cited.