Open Access
ARTICLE
Coupled Atomistic/Continuum Simulation based on Extended Space-Time Finite Element Method
Department of Mechanical Engineering, University of Cincinnati, Cincinnati, OH 45221.
Corresponding Author. Department of Mechanical Engineering, University of Cincinnati, Cincinnati, OH 45221. Email dong.qian@uc.edu
Computer Modeling in Engineering & Sciences 2008, 24(2&3), 185-202. https://doi.org/10.3970/cmes.2008.024.185
Abstract
A multiscale method based on the extended space-time finite element method is developed for the coupled atomistic/continuum simulation of nanoscale material systems. Existing single scale approach such as the finite element method has limited capability of representing the fine scale physics in both the spatial and temporal domains. This is a major disadvantage for directly incorporating FEM in coupled atomistic/continuum simulations as it results in errors such as spurious wave reflections at the atomistic/continuum interface. While numerous efforts have been devoted to eliminating the interfacial mismatch effects, less attention has been paid to developing fine scale, atomistic level representations within the FEM framework. In this paper, we show that multiscale space-time approximations can be established within the context of FEM. By augmenting the regular space-time finite element shape function basis with the enrichment function, we demonstrate that the continuum and atomistic representations can be consistently linked and this naturally leads to a reflectionless interfacial boundary condition. In addition, a unique feature of this approach is its ability to achieve wave transmitting condition that is energy conservative. Realization of these properties is illustrated through both harmonic and nonlinear lattices in 1D.Keywords
Cite This Article
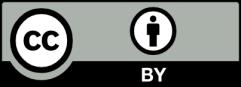
This work is licensed under a Creative Commons Attribution 4.0 International License , which permits unrestricted use, distribution, and reproduction in any medium, provided the original work is properly cited.