Open Access
ARTICLE
A Novel Model for Describing Rail Weld Irregularities and Predicting Wheel-Rail Forces Using a Machine Learning Approach
1 State Key Laboratory of High-Speed Railway Track System, China Academy of Railway Sciences Corporation Limited, Beijing, 100081, China
2 Railway Engineering Research Institute, China Academy of Railway Sciences Corporation Limited, Beijing, 100081, China
3 School of Aeronautic Science and Engineering, Beihang University, Beijing, 100191, China
* Corresponding Author: Ziquan Yan. Email:
(This article belongs to the Special Issue: Machine Learning Based Computational Mechanics)
Computer Modeling in Engineering & Sciences 2025, 142(1), 555-577. https://doi.org/10.32604/cmes.2024.056023
Received 12 July 2024; Accepted 16 October 2024; Issue published 17 December 2024
Abstract
Rail weld irregularities are one of the primary excitation sources for vehicle-track interaction dynamics in modern high-speed railways. They can cause significant wheel-rail dynamic interactions, leading to wheel-rail noise, component damage, and deterioration. Few researchers have employed the vehicle-track interaction dynamic model to study the dynamic interactions between wheel and rail induced by rail weld geometry irregularities. However, the cosine wave model used to simulate rail weld irregularities mainly focuses on the maximum value and neglects the geometric shape. In this study, novel theoretical models were developed for three categories of rail weld irregularities, based on measurements of the high-speed railway from Beijing to Shanghai. The vertical dynamic forces in the time and frequency domains were compared under different running speeds. These forces generated by the rail weld irregularities that were measured and modeled, respectively, were compared to validate the accuracy of the proposed model. Finally, based on the numerical study, the impact force due to rail weld irrregularity is modeled using an Artificial Neural Network (ANN), and the optimum combination of parameters for this model is found. The results showed that the proposed model provided a more accurate wheel/rail dynamic evaluation caused by rail weld irregularities than that established in the literature. The ANN model used in this paper can effectively predict the impact force due to rail weld irrregularity while reducing the computation time.Keywords
Cite This Article
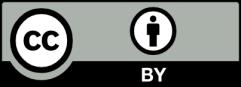
This work is licensed under a Creative Commons Attribution 4.0 International License , which permits unrestricted use, distribution, and reproduction in any medium, provided the original work is properly cited.