Open Access
ARTICLE
Shear Deformation of DLC Based on Molecular Dynamics Simulation and Machine Learning
Key Laboratory of Traffic Safety on Track (Central South University), Ministry of Education, School of Traffic & Transportation Engineering, Central South University, Changsha, 410075, China
* Corresponding Authors: Zhanyuan Xu. Email: ; Lichun Bai. Email:
Computer Modeling in Engineering & Sciences 2024, 141(3), 2107-2119. https://doi.org/10.32604/cmes.2024.055743
Received 05 July 2024; Accepted 11 September 2024; Issue published 31 October 2024
Abstract
Shear deformation mechanisms of diamond-like carbon (DLC) are commonly unclear since its thickness of several micrometers limits the detailed analysis of its microstructural evolution and mechanical performance, which further influences the improvement of the friction and wear performance of DLC. This study aims to investigate this issue utilizing molecular dynamics simulation and machine learning (ML) techniques. It is indicated that the changes in the mechanical properties of DLC are mainly due to the expansion and reduction of sp3 networks, causing the stick-slip patterns in shear force. In addition, cluster analysis showed that the sp2-sp3 transitions arise in the stick stage, while the sp3-sp2 transitions occur in the slip stage. In order to analyze the mechanisms governing the bond breaking/re-formation in these transitions, the Random Forest (RF) model in ML identifies that the kinetic energies of sp3 atoms and their velocities along the loading direction have the highest influence. This is because high kinetic energies of atoms can exacerbate the instability of the bonding state and increase the probability of bond breaking/re-formation. Finally, the RF model finds that the shear force of DLC is highly correlated to its potential energy, with less correlation to its content of sp3 atoms. Since the changes in potential energy are caused by the variances in the content of sp3 atoms and localized strains, potential energy is an ideal parameter to evaluate the shear deformation of DLC. The results can enhance the understanding of the shear deformation of DLC and support the improvement of its frictional and wear performance.Keywords
Diamond-like carbon (DLC) films have garnered significant attention in material science due to their high hardness, similar to diamond, and good lubricity of graphite [1,2]. These films exhibit excellent properties, including high wear resistance, low coefficient of friction, and good chemical stability, which make them promising for potential applications in mechanics, electronics, optics, and biomedicine [2,3]. Meanwhile, the DLC has proven to be a key material for improving the performance and lifetime of devices, particularly in protective coatings, micromechanical devices, and energy storage devices. For instance, Wroblewski et al. [1,4,5] investigated the influence of a change in the tribological parameters of DLC anti-wear coatings on the moment of resistance to the piston movement of an aircraft engine.
Understanding the deformation mechanisms of DLC under different conditions is essential to optimize their application procedure and predict their working lifetime and reliability. However, due to the microscale thickness of these films, it is challenging to conduct detailed analyses of their microstructural evolutions during deformation in the lab.
In recent years, molecular dynamics (MD) simulation has become a powerful tool for understanding the properties and behaviors of materials at the microscale. MD simulations can observe the structural changes of DLC during deformations at the microscale [6–8]. For example, Bai et al. [9] conducted a fatigue behavior analysis in the tensile testing of DLC films and determined that their interfacial fatigue is primarily caused by sp3-sp2 transition. Yu et al. [10] also conducted a uniaxial compressive simulation of DLC films and indicated that their deformation behavior results from the competition between relative slip and diffusion relaxation. However, the microstructural evolution and mechanical behaviors of DLC under shearing deformation conditions are still unclear, so their systematic deformation mechanism is still not obtained.
In order to perform more detailed simulation experiments, machine learning (ML) has been widely used in recent literature [11–13]. Deringer et al. [12] presented a methodology based on an ML representation of the density-functional theory (DFT) potential energy surface, enabling materials simulations with close-to-DFT accuracy but at a much lower cost. Xiong et al. [13] proposed a coarse-grained molecular dynamics approach to modify Tersoff’s potential and reduce high-throughput computational cost by 86%. Daru et al. [11] introduced an automated strategy to perform high-quality coupled cluster molecular dynamics. The strategy can systematically improve the efficiency and accuracy of complex systems. These studies prove ML can improve simulation efficiency by extracting valuable information from plenty of data [14].
This study aims to comprehensively analyze the microstructural evolution of DLC under shear deformation conditions and their mechanical properties through MD simulations combined with ML methods. Considerations are given to the factors such as shear velocity, temperature, and loading. The investigations will emphasize the changes in bonding ratio, the relationship between shear force and various physical parameters, and the bonding breaking/re-forming mechanisms. The outcomes can improve the understanding of the mechanical behaviors of DLC under shear conditions.
The atomistic model for shear deformations of DLC has the dimensions of 50 × 15 × 80 Å3, as shown in Fig. 1. The model was divided into three layers along the z-direction. The layers on both boundaries were defined as rigid bodies to avoid deformation. The middle one was regarded as a thermostatic layer in which atoms can move based on the forces given by their surrounding neighbors. During the shear simulation, the lower rigid layer was fixed with zero velocity along all three directions, but the upper layer was applied with certain x-directional velocity and y-directional loading. In order to ensure that the shear sliding happens in the middle region of the thermostatic layer, the void defects in the middle region were created by removing the C atoms. The structure of DLC was acquired using the melting-quenching method [10]; more details are provided in the literature [9]. In the shear simulation, periodic boundary conditions were applied on the x-and y-axes, while non-periodic boundary conditions were applied on the z-axis. The timestep was set to 0.1 fs. The temperature of the thermostatic layer was controlled using the Nose-Hoover thermostat.
Figure 1: MD model for the shear deformation of DLC
The simulations were conducted using the open-sourced LAMMPS coding [15], and the results were visualized using OVITO software [16]. The interactions among C atoms were described using the AIREBO potential, which can accurately represent atomic interactions between C atoms [17].
The shear simulations investigated the effect of three factors, including temperature T (T = 100, 200, 300, 500, 700, 900, and 1100 K), shear velocity Vx (Vx = 0.5, 1, 1.5, and 2 Å/ps) and vertical loading Fn (Fn = 0.3, 1.2, 2.4, 3, 6, and 9 GPa). A base case was defined with T = 300 K, Vx = 0.5 Å/ps, Fn = 0.3 GPa. Only one factor was changed from the base case during the simulation, but the others were kept unchanged. The shear force FL undertaken by DLC was calculated in the simulation by summing up all the x-directional forces of atoms in the upper rigid layer. In addition, the atomic potential energy Pe was also determined. The coordination number (CN) of each C atom was calculated using a cut-off distance of 1.9 Å. The atoms with CN = 3 and 4 were regarded to have sp2 and sp3 hybridized bonding states [18], respectively. In addition, the same cut-off distance was utilized to analyze the cluster formed by C atoms in shear deformation [10].
3.1 Effect of Different Factors on the Shear Performance of DLC
Fig. 2a shows the FL vs. displacement (dx) at different T. The FL-dx curves can be divided into three stages: elastic deformation, elastic-plastic transition, and plastic deformation. The FL increases linearly in the first stage while showing fluctuations with stick-slip patterns in the last stage [19]. The maximum FL (Table 1) and the amplitude of stick-slip patterns decreases with T. The change of Pe with dx remains consistent with that of FL, as depicted in Fig. 2b. The initial value of Pe at the beginning of shear deformation increases with T, which seems to converse with the reported results [10]. This is because an additional Fn is applied to the DLC in the current work, which can cause the C networks to undertake compressive strain along the z-direction, which is the main difference between the current and previous models. In addition, when the DLC stays in the plastic deformation stage, the Pe decreases with the T.
Figure 2: Dependence of (a) FL, (b) Pe, and (c) fsp3 on dx under different temperatures
The changes of both FL and Pe can be well explained by the microstructural changes of DLC that are described by the ratio of sp3 bonding atoms fsp3, as shown in Fig. 2c. The fsp3 generally decreases with the shear deformation, indicating the occurrence of graphitization of DLC, corresponding to the decrease of FL with dx. In addition, a high T induces a decrease in the fsp3 because the high temperature can enhance the graphitization of DLC. This is further verified by the increased height of the model along the z-direction with a high T since sp2 atoms have a small density, and the increase of their fraction can cause the expansion of the model. The decreased fsp3 also agrees well with the small FL and Pe at a high T since the C networks with less sp3 bonding have a low Pe and hardly undertake a high shear force. In addition, an interesting phenomenon is that the fsp3 with a low T (T < 700 K) shows a peak in the elastic-plastic transition stage. This demonstrates that the shear strain can induce the sp2-sp3 transition at low temperatures, which is consistent with the observation under compressive deformation [10]. The absence of such a peak at high T can be attributed to the enhanced graphitization eliminating sp2-sp3 transition, corresponding to the decreased maximum FL at a high T.
Fig. 3 illustrates the mechanical performance of DLC under various Fn. It indicates that the maximum FL increases with the Fn. This trend is also evident in the Pe change of the DLC. In addition, the fsp3 is higher under a high Fn condition than standard test conditions, as given in Fig. 3c, which can be due to the atom re-distribution induced by elastically shear deformation [20]. The above results indicate that the increase in the fsp3 causes the increases in the maximum FL and Pe, as the shear force is mainly undertaken by the network formed by the sp3C clusters [19,21,22].
Figure 3: Dependence of (a) FL, (b) Pe, and (c) fsp3 on dx under different loadings
Fig. 4 shows the mechanical performance of DLC under different Vx. It indicates that the DLC can withstand a larger maximum FL and possess a higher Pe under a greater Vx condition. This can be due to the dynamic effect that occurs when higher Vx is applied externally, causing the network formed by the sp3C-atoms to have insufficient time to rearrange atoms. In addition, the maximum fsp3 present in the elastic stage slightly increases with the Vx, which is attributed to the fact that under the high deformation rate, the sp2 atoms can become sp3 bonding with their surrounding sp3 networks, which also keeps consistent with the change of maximum FL and Pe with Vx. In addition, in the plastic deformation stage, the FL, Pe, and fsp3 have little changes with the Vx, indicating that the Vx only influences the elastic deformation and has less effect on the mechanical performance of DLC than T.
Figure 4: Dependence of (a) FL, (b) Pe, and (c) fsp3 on dx with different shear velocities
3.2 Microstructural Evolution in the Shear Deformation
The slight increase of fsp3 in the elastic stage is an exciting phenomenon governing the elastic deformation of DLC. Further analysis of the distribution of atomic force (Fig. 5a) shows that such an increase mainly happens in the middle region of the model (40 < x < 60 Å). The force on the C atoms increases during the elastic deformation process in such a region, which is the stick stage. However, the increased stress cannot be released due to the absence of stick-slip transitions. As a result, the sp2 atoms near the sp3 networks become sp3 bonding and are merged into such networks, increasing their size until slip occurs [10]. When the stress in the localized region is beyond the mechanical strength of DLC, the slip phenomenon happens in such region (Fig. 5b), making the sp3 networks break and their size decrease. The stress release resulting from the slip phenomenon increases the absolute atomic velocity as atoms respond to the sudden change in stress conditions. This remains consistent with the change of cluster size distribution around the shear force wave induced by the stick-slip phenomenon, as given in Table 2. The largest ssp3 is small before the shearing deformation but becomes significant when the stick occurs, decreasing in the slipping stage. Such a change pattern of fsp3 is similar for every stick-slip phenomenon.
Figure 5: (a) The distribution of stress σxz in the sticking stage, and (b) the distribution of absolute atomic velocity in the slipping stage
The change pattern of fsp3 is sensitive to different influence factors. As T increases, the sp3 networks are easy to deform to relax the localized stress and experience the sp3-sp2 transition accompanied by the high T, resulting in that increasing tendency of fsp3 in the elastic phase degrades gradually (Fig. 2). For high Fn and Vx, the localization level of atomic stresses increases and promotes the increasing of the size of sp3 networks, contributing to the higher peaks in fsp3 during shearing (Figs. 3 and 4).
Since the sp3C network is the primary carrier of the shear force in DLC, the evolution of the size of such networks induced by the bond breaking/re-formations is essential to understanding the shear deformation of DLC, which have been rarely analyzed in the previous studies [23–26]. The relation between the bond breaking/re-formations of sp3 atoms and their surrounding environment is investigated by conducting an ML analysis. Random Forest (RF) is an ML integration method that makes predictions by constructing multiple decision trees and combining them, capable of assessing the relative importance of features [27]. In the analysis based on the RF model, the data of the properties of sp3 atoms include their velocity, CN, kinetic energy, Pe, and stresses in different directions. These data are divided into 70% training and 30% test sets. The RF model is trained using an RF classifier based on the training set and subsequently utilized to analyze new data verified by the test set. The model performance, including confusion matrices, Receiver Operating Characteristic (ROC) curves, and feature importance maps, are depicted in Fig. 6.
Figure 6: (a) Confusion matrix, (b) ROC matrix, and (c) eigen importance analysis obtained by the RF model for the effect of different parameters on the bond breaking/re-formation
Fig. 6a shows that 81% of the total test set consists of true and true-negative cases (i.e., correctly predicted), showing the acceptable accuracy of the trained RF model. The ROC diagram in Fig. 6b demonstrates that the model achieves an ROC Area Under the Curve (AUC) of 0.93. Since a ROC AUC close to 1 indicates the significant model balance between true and false positive cases, the current ROC AUC proves the ability of the model to classify positive and negative samples under different thresholds.
The impact of various factors on bond breaking/re-formation between sp3 atoms can be observed through the characteristic importance plot (Fig. 6c). The kinetic energy has the maximum feature importance, indicating the greatest influence on bond breaking/re-formation. This is probably because the high kinetic energy of atoms can exacerbate the instability of the bonding state and increase the probability of bond breaking/re-formation. As the kinetic energy consists of the atomic velocities along different directions, further analysis of the impact of these velocities shows that the velocity in the z-direction (Vz) has the main contribution. This is different from the common sense that the velocity along the shear direction (x-direction in this work) dominates the changes in bonding evolution between C atoms. The influence of Vz can be attributed to the fact that the shear deformation happens in the x-z plane, and the atomic movements along the x-direction are confined due to the periodic boundary condition but have high freedom along the z-direction since the Fn applied along the z-direction is much lower than the strength of DLC and thus insufficient to confine all the atomic movement.
Regarding the influence of different types of atomic stresses, the τxz has the highest influence among them, agreeing well with the shear deformation in the x-z plane. In addition, the σxx also has a high influence, which is slightly lower than τxz. This can be due to that in the shearing regions (Fig. 5) induced by the x-z shearing deformation, the atoms entirely move along the x-direction and promote the high σxx of atoms nearby such regions, finally contributing to the bond breaking/re-formation between these atoms. In addition, Pe has a significant influence since Pe always correlates closely with the stability of the bonding state of materials, i.e., an increase in Pe caused by shear deformation and atomic movements signals a tendency for bonds to break. Hence, the impact of Pe can be regarded as a combination of the effects of stresses of atoms and the changes in their spatial positions. This is the reason why the Pe has the capability of correlating the change of fsp3 in Figs. 2–4 and also in literature [6,20,28].
3.3 Relation between Shear Force and Influencing Parameters
The relation between the FL and influencing parameters is significant to understanding the mechanical properties of DLC. The results in Section 3.1 indicate a strong relation between the FL and fsp3. In addition, since the sp3C networks are the primary carrier of the shear force in DLC, the factors, including the Ke (constituted by the influence of Vz) and Pe should also correlate with the FL, due to Section 3.2, which shows that these factors have the top influence in influencing the bond breaking/re-formation between sp3C atoms [29].
Based on the above analysis, the ML technique is employed to construct the correlation analysis for the FL with fsp3, Ke, and Pe. The RF model, using the following parameters: ‘n_estimators = 100’ (number of trees), ‘max_depth = None’ (unlimited depth of trees), ‘min_samples_split = 2’ (minimum samples required to split an internal node), ‘min_samples_leaf = 1’ (minimum samples required to be at a leaf node), and ‘random_state = 42’ (ensuring reproducibility), is employed to predict FL, as illustrated in Fig. 7. The predictions obtained from Pe in both models possess a high degree of accuracy. However, the accuracy of the prediction from fsp3 decreases, and the prediction from Ke has the worst performance.
Figure 7: Relation between the actual and predicted FL by RF model in terms of (a) Pe, (b) Ke, and (c) fsp3
The performance of the RF model is assessed by calculating the Pearson correlation coefficient, mean square error (MSE), and coefficient of determination (R2), given in Fig. 8 and Table 3. The correlation coefficient of 0.96 and R2 = 0.902 for the predictions from Pe indicate a strong positive relationship with FL. For the predictions from fsp3, the correlation coefficient and R2 decrease to 0.17 and 0.752, respectively, showing the decreased correlation between fsp3 and FL. These two parameters decrease further for the predictions from Ke. These results agree well with those in Fig. 7.
Figure 8: Correlation matrix between different parameters with FL obtained by the RF model
The ranking on the correlation of different parameters to FL is quite different from the common sense of the mechanical properties of DLC. Many previous studies by both experimental and theoretical approaches have demonstrated that its deformation and easy-shear properties are dominated by the content of sp3 and sp2 atoms [6,30,31]. This is because the sp3 networks are backbones in amorphous carbon structures, and the sp2 clusters can contribute to the low shear force due to the properties of their localized π bonds, which is consistent with the observation of microstructural evolution in this study.
However, the significant influence of Pe demonstrated by the current analysis indicates that the localization strains of atoms and their bonding transition between sp3 and sp2 dominate the mechanical performances of DLC since the temperature (that can also affect the Pe) remains constant in this study. This exhibits that the influence of Pe includes that of fsp3. The localized contribution strains can contribute to the FL by increasing the barrier for the mobility of atoms under shear deformation, thus improving the shear resistance of the local structure.
This study utilizes MD simulation and ML techniques to investigate the microstructural evolution and mechanical performance of DLC under shearing deformation. The findings indicated that the top ranking of different factors in terms of their influences on shear force are T, Fn, and Vx. The changes in the mechanical properties of DLC are mainly due to the expansion and reduction of sp3 networks.
In addition, cluster analysis showed that for the stick-slip patterns observed for the shear force, the sp2-sp3 transitions happen in the stick stage, while the sp3-sp2 transitions occur in the slip stage. The RF model in ML identifies that the Ke of sp3 atoms and their Vz has the highest influence to analyze the influence of factors on the bond breaking/re-formation in these transitions. This is because a high Ke of atoms can exacerbate the instability of the bonding state and increase the probability of bond breaking/re-formation.
Finally, the RF model finds that the FL is highly correlated to Pe, with less correlation with fsp3. Since the changes in Pe are caused by the variances in fsp3 and localized strains in this work, it is evident that Pe is an ideal parameter to evaluate the shear deformation of DLC instead of its fsp3, which is conventionally regarded as a direct parameter representing the mechanical performance of DLC. It should be noted that the MD simulations and ML models in this work are only focused on shearing conditions. The applicability of current findings on the other loading types (such as tensile and compressive deformations) should be examined in future.
Acknowledgement: The simulations in this work are supported by the High-Performance Computing Center of Central South University.
Funding Statement: The authors received no specific funding for this study.
Author Contributions: The authors confirm contribution to the paper as follows: study conception and design, Chaofan Yao; data collection, Chaofan Yao; analysis and interpretation of results, Chaofan Yao, Lichun Bai, and Huanhuan Cao; writing—original draft preparation, Chaofan Yao; writing—review and editing, Huanhuan Cao and Zhanyuan Xu; supervision, Lichun Bai and Zhanyuan Xu. All authors reviewed the results and approved the final version of the manuscript.
Availability of Data and Materials: The data that support the findings of this study are available on request from the corresponding author upon reasonable request.
Conflicts of Interest: The authors declare that they have no conflicts of interest to report regarding the present study.
References
1. Komori K, Umehara N. Effect of surface morphology of diamond-like carbon coating on friction, wear behavior and tribo-chemical reactions under engine-oil lubricated condition. Tribol Int. 2015;84:100–9. doi:10.1016/j.triboint.2014.11.010. [Google Scholar] [CrossRef]
2. Ohgoe Y, Takada S, Hirakuri KK, Tsuchimoto K, Homma A, Miyamatsu T, et al. Investigating the functionality of diamond-like carbon films on an artificial heart diaphragm. Asaio J. 2003;49(6):701–7. doi:10.1097/01.MAT.0000093970.59796.40 [Google Scholar] [PubMed] [CrossRef]
3. Fu ZQ, Sun J, Wang CB, Zhang W, Yue W, Peng ZJ, et al. Tribological performance of DLC coatings deposited by ion beam deposition under dry friction and oil lubricated conditions. Vacuum. 2013;94:14–8. doi:10.1016/j.vacuum.2013.01.006. [Google Scholar] [CrossRef]
4. Kapsiz M, Geffroy S, Holzer A, Schmitz K. Tribological performances of diamond-like carbon coatings for hydraulic applications. Chem Eng Technol. 2023;46(1):118–27. doi:10.1002/ceat.202200459. [Google Scholar] [CrossRef]
5. Wroblewski P, Rogolski R. Experimental analysis of the influence of the application of TiN, TiAlN, CrN and DLC1 coatings on the friction losses in an aviation internal combustion engine intended for the propulsion of ultralight aircraft. Materials. 2021;14(22):6839. doi:10.3390/ma14226839 [Google Scholar] [PubMed] [CrossRef]
6. Bai LC, Srikanth N, Wu H, Liu Y, Liu B, Zhou K. Investigation on tensile behaviors of diamond-like carbon films. J Non-Cryst Solids. 2016;443:8–16. doi:10.1016/j.jnoncrysol.2016.03.025. [Google Scholar] [CrossRef]
7. Li JH, Peng Y, Tang XQ, Xu Q, Liu B, Bai LC. Lubrication performance of hydrogenated graphene on diamond-like carbon films based on molecular dynamics simulation. Tribol Lett. 2021;69(1):1–13. doi:10.1007/s11249-020-01382-x. [Google Scholar] [CrossRef]
8. Baimova JA. An overview of mechanical properties of diamond-like phases under tension. Nanomater. 2024;14(2):129. doi:10.3390/nano14020129 [Google Scholar] [PubMed] [CrossRef]
9. Bai L, Yu Y. Fatigue behaviors of diamond-like carbon films. Diam Relat Mater. 2022;124. doi:10.1016/j.diamond.2022.108892. [Google Scholar] [CrossRef]
10. Yu YF, Zhang X, Yin SW, Bai LC, Liu ZS. The sp2-sp3 transition and shear slipping dominating the compressive deformation of diamond-like carbon. J Non-Cryst Solids. 2022;577:121318. doi:10.1016/j.jnoncrysol.2021.121318. [Google Scholar] [CrossRef]
11. Daru J, Forbert H, Behler J, Marx D. Coupled cluster molecular dynamics of condensed phase systems enabled by machine learning potentials: liquid water benchmark. Phys Rev Lett. 2022;129(22). doi:10.1103/PhysRevLett.129.226001 [Google Scholar] [PubMed] [CrossRef]
12. Deringer VL, Csanyi G. Machine learning based interatomic potential for amorphous carbon. Phys Rev B. 2017;95(9). doi:10.1103/PhysRevB.95.094203. [Google Scholar] [CrossRef]
13. Xiong Z, Yu Y, Chen H, Bai L. A coarse-grained study on mechanical behaviors of diamond-like carbon based on machine learning. Nanotechnology. 2023;34:385702. doi:10.1088/1361-6528/acde5a [Google Scholar] [PubMed] [CrossRef]
14. daFonseca BG, Thind SS, Booth I, Brolo AG. A machine learning approach for the automated classification of bulk sp2-sp3 carbon materials. J Raman Spectrosc. 2024;55(1):15–25. doi:10.1002/jrs.6608. [Google Scholar] [CrossRef]
15. Humphrey W, Dalke A, Schulten K. VMD: visual molecular dynamics. J Mol Graph Model. 1996;14(1):33–8, 27–8. doi:10.1016/0263-7855(96)00018-5 [Google Scholar] [PubMed] [CrossRef]
16. Stukowski A. Visualization and analysis of atomistic simulation data with OVITO-the open visualization tool. Model Simul Mater Sc. 2010;18(1). doi:10.1088/0965-0393/18/1/015012. [Google Scholar] [CrossRef]
17. Hoehnerbach M, Bientinesi P. Accelerating AIREBO: navigating the journey from legacy to high-performance code. J Comput Chem. 2019;40(14):1471–82. doi:10.1002/jcc.25796 [Google Scholar] [PubMed] [CrossRef]
18. Ma TB, Wang LF, Hu YZ, Li X, Wang H. A shear localization mechanism for lubricity of amorphous carbon materials. Sci Rep. 2014;4. doi:10.1038/srep03662 [Google Scholar] [PubMed] [CrossRef]
19. Rysaeva LK, Lisovenko DS, Gorodtsov VA, Baimova JA. Stability, elastic properties and deformation behavior of graphene-based diamond-like phases. Comput Mater Sci. 2020;172. doi:10.1016/j.commatsci.2019.109355. [Google Scholar] [CrossRef]
20. Wang JX, Wang LJ, Chen H, Wang HY. Molecular dynamics simulation of friction in DLC films with different sp3 contents. Tribol Int. 2023;190. doi:10.1016/j.triboint.2023.109050. [Google Scholar] [CrossRef]
21. Huang J, Peng J, Qiu X, Li X. Evolution of the microstructure, hybridization, and internal stress of Al-doped diamond-like carbon coatings: a molecular dynamics simulation. Langmuir. 2023;39(11):3895–904. doi:10.1021/acs.langmuir.2c03200 [Google Scholar] [PubMed] [CrossRef]
22. Jarratt M, Stallard J, Renevier NM, Teer DG. An improved diamond-like carbon coating with exceptional wear properties. Diam Relat Mater. 2003;12(3–7):1003–7. doi:10.1016/s0925-9635(02)00296-0. [Google Scholar] [CrossRef]
23. Baimova JA, Galiakhmetova LK, Mulyukov RR. Diamond-like structures under hydrostatic loading: atomistic simulation. Comp Mater Sci. 2021;192:110301. doi:10.1016/j.commatsci.2021.110301. [Google Scholar] [CrossRef]
24. Muniz AR, Machado AS, Maroudas D. Mechanical behavior of interlayer-bonded nanostructures obtained from bilayer graphene. Carbon. 2015;81:663–77. doi:10.1016/j.carbon.2014.10.003. [Google Scholar] [CrossRef]
25. Rahman SM, Song J, Yeo C-D. Computational study on surface energy of amorphous DLC with respect to hybridization state of carbon and potential functions. Diam Relat Mater. 2019;95:127–34. doi:10.1016/j.diamond.2019.04.015. [Google Scholar] [CrossRef]
26. Shen B, Chen SL, Sun FH. Investigation on the long-duration tribological performance of bilayered diamond/diamond-like carbon films. P I Mech Eng J-J Eng. 2014;228(6):628–41. doi:10.1177/1350650114522611. [Google Scholar] [CrossRef]
27. Breiman L. Random forests. Mach Learn. 2001;45(1):5–32. doi:10.1023/a:1010933404324. [Google Scholar] [CrossRef]
28. Yue ZF, Wang H, Fan XQ, Li H, Zhang JY, Zhu MH. Regulating the fretting behavior of diamond-like carbon films by changing the composition and structure. Carbon. 2023;212:118097. doi:10.1016/j.carbon.2023.118097. [Google Scholar] [CrossRef]
29. Dankesreiter B, Song JG, Rahman SM, Shah NMR, Yeo CD. Effects of diffused hydrogen atoms on thermomechanical properties and contact behavior of a diamond-like carbon film. J Appl Phys. 2021;130(2):9. doi:10.1063/5.0051339. [Google Scholar] [CrossRef]
30. Wang LP, Bai LC, Lu ZB, Zhang GA, Wu ZG. Influence of load on the tribological behavior of a-C films: experiment and calculation coupling. Tribol Lett. 2013;52(3):469–75. doi:10.1007/s11249-013-0230-y. [Google Scholar] [CrossRef]
31. Gershman I, Mironov A, Mezrin A, Torskaya E, Kuznetsova T, Lapitskaya V, et al. Effect of sp3-sp2 transformation on the wear rate of the DLC coating. Lubricants. 2022;10(5):85. doi:10.3390/lubricants10050085. [Google Scholar] [CrossRef]
Cite This Article
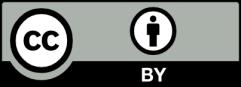
This work is licensed under a Creative Commons Attribution 4.0 International License , which permits unrestricted use, distribution, and reproduction in any medium, provided the original work is properly cited.