Open Access
REVIEW
Analysing Recent Breakthroughs in Fault Diagnosis through Sensor: A Comprehensive Overview
Faculty of Geoengineering, Mining and Geology, Wroclaw University of Science and Technology, Wroclaw, 50-421, Poland
* Corresponding Author: Govind Vashishtha. Email:
Computer Modeling in Engineering & Sciences 2024, 141(3), 1983-2020. https://doi.org/10.32604/cmes.2024.055633
Received 03 July 2024; Accepted 26 September 2024; Issue published 31 October 2024
Abstract
Sensors, vital elements in data acquisition systems, play a crucial role in various industries. However, their exposure to harsh operating conditions makes them vulnerable to faults that can compromise system performance. Early fault detection is therefore critical for minimizing downtime and ensuring system reliability. This paper delves into the contemporary landscape of fault diagnosis techniques for sensors, offering valuable insights for researchers and academicians. The papers begin by exploring the different types and causes of sensor faults, followed by a discussion of the various fault diagnosis methods employed in industrial sectors. The advantages and limitations of these methods are carefully examined, paving the way for highlighting current challenges and outlining potential future research directions. This comprehensive review aims to provide a thorough understanding of current advancements in sensor fault diagnosis, enabling readers to stay abreast of the latest developments in this rapidly evolving field. By addressing the challenges and exploring promising research avenues, this paper seeks to contribute to the development of more robust and effective sensor fault diagnosis methods, ultimately improving the reliability and safety of industrial and agricultural systems.Keywords
In today’s increasingly automated and data-driven world, sensors play a pivotal role across various industries, from manufacturing and healthcare to transportation and environmental monitoring. These devices, integral to the functioning of modern systems, provide crucial data that inform decision-making, control processes, and ensure safety and efficiency [1,2]. However, the reliability of these systems is heavily dependent on the accuracy and functionality of the sensors themselves. Sensor faults, whether due to hardware malfunctions, environmental conditions, or aging, can lead to significant errors, costly downtime, and even hazardous situations [3,4].
Sensor systems are crucial components in a wide range of industries, from automotive and aerospace to process control and manufacturing [5,6]. Reliable and accurate sensor data is essential for the proper functioning of these systems, making sensor fault diagnosis a critical area of research and development [7,8]. In recent years, there have been significant advancements in sensor fault diagnosis methods, driven by the increasing complexity of sensor systems and the need for more robust and efficient fault detection and isolation techniques [9].
To address these challenges, recent advancements in sensor fault diagnosis have become a focal point of research and development. These innovations aim to detect, isolate, and rectify sensor faults in real-time, thereby maintaining system integrity and performance [10]. Leveraging cutting-edge technologies such as artificial intelligence (AI), machine learning (ML), and advanced signal processing techniques, contemporary methods of sensor fault diagnosis offer unprecedented accuracy and reliability [11–13].
This comprehensive overview explores the latest trends and breakthroughs in the field, highlighting key methodologies, tools, and applications. It delves into AI-driven diagnostic algorithms, model-based and data-driven approaches, and the integration of the Internet of Things (IoT) for enhanced fault detection. Additionally, the overview examines the practical implementation of these innovations in various sectors, illustrating how they contribute to more resilient and adaptive systems.
By understanding the recent innovations in sensor fault diagnosis, researchers and academicians can better navigate the complexities of modern sensor networks, ensuring optimal performance and minimizing the risks associated with sensor failures [14–16]. This exploration not only underscores the importance of continued research and development but also sets the stage for future advancements that will further enhance the robustness and dependability of sensor-driven systems. The steps in fault diagnosis of industrial components through sensor technology are shown in Fig. 1.
Figure 1: Steps in fault diagnosis
This paper contributes to the field of fault diagnosis through sensors in the following ways:
• It provides a thorough exploration of various sensor fault types and their underlying causes, offering a valuable foundation for understanding the challenges associated with sensor malfunction.
• The paper presents a comprehensive analysis of the diverse methods employed for sensor fault diagnosis in industrial settings, highlighting their strengths and weaknesses.
• The authors identify key challenges and limitations within the existing landscape of fault diagnosis techniques through sensors, emphasizing the need for further research and development.
• By outlining potential future research avenues, the paper provides valuable guidance for researchers seeking to develop more robust and effective sensor fault diagnosis methods.
Sensor faults can significantly impact the reliability and accuracy of systems that depend on sensor data. These faults can arise from various sources and manifest in different ways, affecting the performance of the sensor and, consequently, the entire system [17,18]. Understanding the types of sensor faults is crucial for developing effective diagnosis and mitigation strategies. Here are the main types of sensor faults.
An offset or bias occurs when a sensor consistently reads a value that is systematically higher or lower than the actual value as shown in Fig. 2. This can be due to calibration errors, sensor aging, or environmental changes [19]. Offset faults can significantly impact the accuracy of sensor measurements, leading to inaccurate control decisions and potential system malfunctions [20].
Figure 2: Representation of bias faults
Kuruppu et al. [21] provided a comprehensive understanding of the impact of static offset errors in rotor position sensors on permanent magnet synchronous machine drives and proposed a reliable diagnostic strategy for detecting this critical failure mode. Liu et al. [22] proposed an improved time-dependent displacement excitation (TDDE) model to analyse the vibrations of ball bearings with different local defects in the outer race. The study investigates the effects of defect size, defect offset distance, and defect bias angle on the vibrations of the ball bearing, providing valuable insights into the influence of different defect types and severities.
Gain faults happen when there is a proportional error in the sensor’s output as shown in Fig. 3. Instead of maintaining a consistent ratio between the input and output, the sensor’s output is multiplied by an incorrect factor, leading to scaled readings [23]. Gain faults alter the sensor’s sensitivity, affecting its ability to detect small changes in the input signal. Gain faults can significantly distort the measured values, leading to inaccurate interpretations and potentially flawed control decisions.
Figure 3: Representation of gain faults
Badihi et al. [24] presented a comprehensive solution for enhancing the reliability and efficiency of wind turbines by integrating advanced fault detection and accommodation techniques. The proposed approach utilizes fuzzy modelling, identification, and control methods to develop a robust gain-scheduled PI control system and an active fault-tolerant control system. Xu et al. [25] contributed to the field of robust fault detection by providing a systematic approach for designing observer gains that optimize the trade-off between uncertainty confinement and fault sensitivity. This can lead to improved fault detection performance in various dynamical systems, ensuring system safety and reliability. Dong et al. [26] addressed the challenge of imbalanced gearbox fault data in deep learning-based diagnostics by proposing a novel Dynamic Normalization Supervised Contrastive Network (DNSCN) with a multiscale compound attention mechanism.
Drift faults are characterized by a gradual change in sensor readings over time as shown in Fig. 4. This can result from component wear, temperature variations, or environmental influences. Drift can cause the sensor to deviate slowly from its correct measurements, complicating fault detection [27]. Wang et al. [28] proposed a novel sensor fault estimator for the dynamic point-the-bit rotary steerable system (DPRSS) based on ellipsoid bundles. The DPRSS is described by a descriptor system with uncertainties, and the estimator utilizes decoupling techniques and interval analysis to handle these uncertainties. He et al. [29] contributed to advancing the adaptability and learning capabilities of fault diagnosis models for rotating machinery under changing operating conditions. The proposed feature-boosting approach provides a promising solution for tackling catastrophic forgetting and enhancing model plasticity in the face of new fault types. Peng et al. [30] proposed an adaptive fleet-based fault detection method for reliable and efficient fault detection in EV battery packs under changing operating conditions.
Figure 4: Representation of drift faults
In a stuck-at-fault, the sensor output gets stuck at a particular value, regardless of changes in the actual measured parameter as shown in Fig. 5. This type of fault can be caused by mechanical failure, software bugs, or hardware issues. Jo et al. [31] proposed a method to diagnose stuck actuators and implement fault-tolerant control in an anti-lock brake system (ABS). Liu et al. [32] addressed fault-tolerant attitude tracking control for aircraft with actuator faults. The proposed controller utilizes nonlinear dynamic inversion (NDI) for fault-free attitude tracking. Rivas et al. [33] proposed a predictive maintenance (PdM) framework using machine learning models (MLM) developed to optimize component maintenance operations and support safe electricity generation with high capacity factors. The framework utilizes sensor measurements to predict the remaining useful life (RUL) of components, enabling maintenance only when necessary and optimizing costs.
Figure 5: Representation of struck at faults
Noisy signals occur when there is an abnormal amount of random fluctuations or spikes in the sensor output as shown in Fig. 6. Noise can be caused by electrical interference, poor sensor quality, or environmental factors. This type of fault can obscure true measurements and complicate data analysis. Xu et al. [34] established a probability detection model combining singular value decomposition (SVD) and adaptive wavelet denoising for laser radar, analysing the influence of noise on detection accuracy. Mitra et al. [35] proposed a novel approach for automatic target recognition in autonomous weapons by matching connected graphs of feature pixels. The proposed model utilizes speeded-up robust features (SURF) for feature extraction and graph generation.
Figure 6: Representation of noisy signal
Complete sensor failure results in no output signal at all as shown in Fig. 7. This can be due to severe hardware damage, power supply issues, or disconnection. A sensor experiencing complete failure is unable to provide any useful data [36]. Kim et al. [37] analysed the failure of a rail grinder car’s rotating shaft, using fractography, chemical analysis, metal lography, hardness measurement, and finite element analysis. Xu et al. [38] investigated the vibration mechanism of a rotate vector (RV) reducer with needle roller bearing (NRB) failures using a dynamic model based on contact multibody dynamics. Venturini et al. [39] proposed a digital twin (DT) approach to predict failure in automotive steel wheels during experimental fatigue tests.
Figure 7: Representation of complete failure
Cross-sensitivity faults occur when a sensor intended to measure one parameter is affected by changes in another parameter. For example, a temperature sensor might also be sensitive to humidity, leading to erroneous readings if both parameters change simultaneously [40]. Fu et al. [41] presented a novel multi-mode flexible nanofiber membrane sensor based on interpenetrating networks of magnetic particles. The sensor utilizes a controllable electrospinning technology to create nanofiber membranes with adjustable morphology. Carmona-Cejas et al. [42] proposed a method to discriminate humidity variations from other environmental factors in solidly mounted resonators (SMRs) by utilizing a dual-mode SMR. Wang et al. [43] suggested that cross-sensitivity among sensors hinders accurate identification of mixed gasses. To address this issue the authors proposed an improved deep Bidirectional Recurrent Neural Network (BRNN) model to address the cross-sensitivity issue in chemical gas sensor arrays, leading to improved recognition accuracy of mixed gas analytes.
Hysteresis faults are characterized by a lag in the sensor’s response when the measured parameter changes direction as represented in Fig. 8. This can result in different sensor outputs for the same measured value, depending on whether the parameter is increasing or decreasing [44]. Wang et al. [45] proposed a double normalization fault diagnosis (DNFD) method for dealing with open-circuit faults in Permanent Magnet Synchronous Motor (PMSM) drives that incorporates several innovative components aimed at enhancing fault detection and diagnosis reliability. Ding et al. [46] proposed an evolvable system-level fault diagnosis framework for train transmission systems to address challenges such as separate networks for each component and dependency on incremental samples.
Figure 8: Representation of hysteresis
This section provides a comprehensive overview of different types of sensor faults, crucial for understanding sensor behaviour and developing effective fault detection and mitigation strategies. Each fault is explained with examples and relevant research, highlighting the impact of each fault type on system performance and the importance of addressing them through robust fault detection and accommodation techniques.
3 Fault Diagnosis Through Sensor
Fault diagnosis through sensors is a crucial process in maintaining the reliability and efficiency of various systems. It involves detecting, isolating, and identifying faults within a system using sensor data [47,48]. Effective sensor fault diagnosis helps prevent system failures, reduces maintenance costs, and ensures the safety and performance of the system. Recent advances in sensor technologies, signal processing methods, and machine learning have enabled the development of more robust and efficient fault diagnosis techniques. For instance, Kibrete et al. [49] comprehensively reviewed multi-sensor data fusion techniques for the intelligent fault diagnosis of rotating machines. Given the critical role that rotating machines play across various industries, their malfunction can lead to significant financial losses and safety risks. As a result, there is increasing interest in leveraging multi-sensor condition monitoring data for more effective fault diagnosis. Tan et al. [50] suggested that sensor data often suffer from quality issues such as missing or damaged data, which can arise due to communication delays, environmental noise, and sensor faults. These data quality issues can significantly reduce the accuracy of fault diagnostic models (FDMs). In response to this challenge, the authors proposed a robust fault diagnostic scheme capable of maintaining stability and accuracy even under non-ideal sensor data conditions. Tang et al. [51] proposed a minimum unscented Kalman filter-aided deep belief network to address the challenges presented by environmental noise and internal bearing degradation. Li et al. [52] presented an intelligent diagnostic framework leveraging multi-source information and advanced machine learning techniques to address the existing diagnostic methods that often rely on single signals, struggle with noise interference and fail to capture the interdependence between data samples, limiting their accuracy.
Model-based methods for fault diagnosis rely on creating mathematical models that represent the normal operating behaviour of a system. By comparing the actual behaviour of the system with these models, deviations can be detected, isolated, and identified as faults. Xu et al. [53] proposed an interval-valued evidence (IVE) fusion method via a cloud model to address the issues of single-valued belief degrees (SVB). Wang et al. [54] presented an approach to fault detection and diagnosis in Liquid Rocket Engines (LREs) that leverages several advanced techniques to address the inherent challenges. Tang et al. [55] proposed an adaptive deep framework that represents a significant advancement in the automatic diagnosis of hydraulic axial piston pumps. By leveraging multi-sensor data, converting it into rich two-dimensional representations, optimizing model parameters automatically, and achieving very high diagnostic accuracy, this approach holds great promise for enhancing the safety and reliability of hydraulic transmission systems. This method not only reduces the reliance on traditional expert-driven diagnosis but also addresses the challenges faced by current deep learning models in parameter tuning, making it a robust and efficient solution for fault detection. Wang et al. [56] proposed a domain adaptation method for bearing fault diagnosis that utilizes innovative techniques to address the common issues of incomplete datasets and domain mismatches. By generating missing category data with Cycle GAN, leveraging domain invariant knowledge through anchor adapters, and employing an ensemble of classifiers, your approach offers a robust and effective solution for fault diagnosis. Kumar et al. [57] described the approach that provides a novel and robust solution to fault isolation in systems where temporal information and mathematical constraints are crucial. By integrating analytical redundancy relations, formulating a time-dependent function for fault isolation, and applying genetic algorithms for optimization, the method offers high accuracy and reliability. Zhang et al. [58] proposed a pruned-optimized weighted graph convolutional network (POWGCN) that leverages hydrophone-collected underwater acoustic signals to diagnose faults in axial flow pumps effectively. By constructing an optimized graph representation of the signals and using a GCN for fault detection, this method provides an accurate and robust solution capable of handling noisy environments. Here are the key model-based methods used for fault diagnosis.
Analytical redundancy involves comparing the outputs of redundant mathematical models or equations with the actual sensor outputs. Any discrepancy between the expected and actual outputs can indicate a fault.
• Residual Generation: Residuals are the differences between the measured and estimated values from the model. Significant residuals suggest a fault.
• Residual Evaluation: Statistical methods, thresholds, or decision functions evaluate the residuals to determine if they indicate a fault.
Yu et al. [59] presented a comprehensive approach to fault detection, isolation, and estimation in a nonlinear electromechanical system, effectively addressing both parametric and nonparametric faults. By introducing the concept of extended analytical redundancy relations (EARRs), it allows for the clear distinction between different types of nonparametric faults, facilitating more efficient fault isolation through the integration of dependent and independent EARRs. Amrane et al. [60] introduced a novel approach to the design of fault detection and isolation (FDI) for sensors in induction machines using nonlinear analytical redundancy (NLAR). By focusing on the elimination of unknown system variables and states, the study addresses the complexities associated with detecting and isolating faults in nonlinear, multivariable, and time-varying systems like induction machines.
However, analytical redundancy relies heavily on the accuracy of the mathematical models used. If the model does not accurately represent the real system due to simplifications or incorrect assumptions, it may lead to false conclusions about the presence or absence of faults. For complex, nonlinear, or time-varying systems, developing accurate models can be extremely challenging. In such cases, analytical redundancy methods may struggle to perform effectively, leading to difficulties in fault detection and isolation.
3.1.2 Observer-Based Techniques
Observer-based techniques use state observers to estimate the internal states of a system. Differences between the estimated and actual states indicate potential faults.
• Luenberger Observer: Estimates system states using a linear model and compares them with actual measurements to generate residuals.
• Kalman Filter: An optimal estimator for linear systems with Gaussian noise, it predicts the system state and updates the prediction based on sensor measurements, with discrepancies indicating faults.
• Extended Kalman Filter (EKF): An extension of the Kalman filter for nonlinear systems, linearizing around the current estimate to handle nonlinearities.
Jeong et al. [61] introduced a model-based fault detection and isolation (FDI) technique within the framework of prognostics and health management (PHM) to emphasize the importance of accurately diagnosing machine health conditions. This approach addressed the growing complexity of manufacturing machinery and the critical need for effective maintenance strategies to mitigate both efficiency losses and safety hazards caused by machinery breakdowns. Campos-Delgado et al. [62] introduced a novel approach for the detection and isolation of open-switch faults in induction motor drives based on model-based residual generation and directional characterization. By exploiting the inherent decoupled structure of the induction motor, the proposed method effectively mitigates the influence of load torque and operating conditions on residual generation.
Parameter estimation methods involve identifying and tracking the parameters of the system model. Deviations from known parameter values indicate faults.
• Least Squares Estimation: Estimates the parameters of the system model by minimizing the sum of the squared differences between the measured and predicted outputs.
• Recursive Least Squares (RLS): An adaptive version of least squares that updates parameter estimates in real-time as new data becomes available.
• Maximum Likelihood Estimation (MLE): Estimates parameters by maximizing the likelihood function, which represents the probability of observed data given the parameters.
Bouchikhi et al. [63] presented a novel parametric spectral estimator based on the maximum likelihood estimator (MLE) for fault diagnosis in electrical machines. This approach offers high-resolution capabilities, overcoming the limitations of classical techniques like the periodogram. Souza et al. [64] presented a robust adaptive parameter estimation procedure for detecting stator inter-turn short-circuit (ITSC) faults in induction motors. By employing a fault state space model and an adaptive parameter estimation methodology, the proposed approach effectively identifies a parameter directly related to the fault severity.
Parity space methods generate residuals by projecting sensor measurements onto a parity space, where inconsistencies can be detected as faults.
• Parity Equations: Formulate consistency relations (parity equations) among sensor measurements. Any inconsistency indicates a fault.
• Geometric Parity Space: Uses geometric properties of the parity space to detect and isolate faults by analysing the direction and magnitude of residual vectors.
Zhong et al. [65] introduced a novel robust fault detection (FD) approach called Parity Space Vector Machine (PSVM) for linear discrete-time systems. By integrating residual generation and residual evaluation within a parity space framework, PSVM effectively addresses the trade-off between false alarm rate (FAR) and fault detection rate (FDR). Cho and Jiang presented a novel framework that effectively integrates a Support Vector Machine (SVM) with parity equation-based residual generation for fault detection and isolation (FDI) in process systems. This approach addresses the challenges associated with identifying multivariate probability distribution functions for residuals, especially in the presence of complex noise characteristics and modelling errors.
3.1.5 Dynamic Model-Based Methods
Dynamic models capture the time-dependent behaviour of systems. Fault diagnosis is performed by analysing the dynamic response of the system.
• State-Space Models: Represent the system dynamics using state variables and equations. Faults are detected by comparing predicted and actual state trajectories.
• Frequency Domain Methods: Analyse the system’s response in the frequency domain to identify anomalies that indicate faults.
Li et al. [66] presented a novel fault diagnosis method for planetary gearboxes in wind turbines, combining transfer learning with a dynamic model to address the challenge of limited labelled data. The proposed approach leverages a modified lumped-parameter dynamic model to simulate vibration signals, capturing key features relevant to real gearbox faults. Zhang et al. [67] proposed the improved EMD method, utilizing wavelet packet decomposition, effectively extracting time-frequency characteristics and statistical parameters, and providing robust fault features. The integration of fuzzy SVM (FSVM) optimized by a multi-population genetic algorithm enables automatic fault classification with high accuracy and strong robustness.
Bond graphs provide a unified graphical representation of physical systems, capturing the energy exchange between components. Faults are diagnosed by analysing deviations in the energy flow.
• Causality Analysis: Determines the cause-and-effect relationships in the bond graph. Faults are identified by detecting inconsistencies in these relationships.
• Power Flow Analysis: Monitors the power flow in the system. Discrepancies between expected and actual power flow indicate faults.
Mishra et al. [68] proposed a scheme that leverages a combination of signal processing techniques, including uniform resampling based on angular position, empirical mode decomposition (EMD) for intrinsic mode function (IMF) extraction, thresholding and signal reconstruction for noise reduction, and envelope order tracking for fault diagnosis. The scheme’s effectiveness is validated using data generated from a comprehensive bond graph model of the bearing system, capturing intricate dynamics and fault geometries. Dash et al. [69] proposed a novel hybrid fault diagnosis method, that combines the strengths of bond-graph (BG) modeling and CNN for improved fault isolation in complex systems. By leveraging the inherent structure and physical insights provided by BG, the method generates informative residuals that are then effectively analyzed by a CNN for accurate fault classification.
Model-based methods for fault diagnosis offer a systematic and reliable approach to detecting, isolating, and identifying faults in complex systems. By leveraging mathematical models, state observers, parameter estimation techniques, parity space methods, dynamic models, and bond graphs, these methods provide accurate and timely fault detection. This not only enhances system reliability and performance but also reduces maintenance costs and prevents unexpected failures. As systems become more complex and interconnected, model-based fault diagnosis will continue to play a crucial role in ensuring their safe and efficient operation.
Knowledge-based methods for fault diagnosis involve using existing knowledge about a system and its components to detect, identify, and isolate faults. These methods typically rely on a deep understanding of the system’s behaviour under normal and faulty conditions. Zhang et al. [70] proposed the deep adaptive sparse residual network (DASRN) represents a significant advancement in the fault diagnosis of rotating machinery, particularly in addressing the challenges posed by continuous operation, varying conditions, fault domain increments, and catastrophic forgetting. Maurya et al. [71] underscored the critical importance of transitioning from single-fault to multi-fault diagnosis in rotating machinery, particularly rolling element bearings, given their susceptibility to defects and the consequential risks of system failures. By leveraging cutting-edge technologies such as IoT, cloud computing, and AI, the development of intelligent, comprehensive, and predictive maintenance systems is achievable. These advancements hold the potential to significantly mitigate the risks of catastrophic failures and optimize maintenance strategies, ensuring the efficient and reliable operation of industrial machinery. Sarwar et al. [72] proposed a hybrid model for fault detection and diagnosis of industrial gas turbine engines that leverages the strengths of PCA for data fusion and ANN for pattern recognition. Zhang et al. [73] proposed a methodology for industrial fault diagnosis, combining nonlinear graph-based predictable feature analysis (GPFA) with explanatory reasoning, presenting a novel approach to addressing the complexities of fault detection in industrial systems. Vo et al. [74] introduced a novel deep-learning model for fault detection and diagnosis in induction motors, addressing the limitations of traditional approaches and utilizing the strengths of convolutional neural networks (CNNs) and recursive neural networks (RNNs). Fu et al. [75] proposed a semi-supervised prototype network with the two-stream wavelet scattering convolutional encoder (TWSCE-SSPN) that offers a novel approach to main bearing fault diagnosis in tunnel boring machines, overcoming challenges related to data quality and quantity in industrial scenarios. Zhao et al. [76] introduced a federated distillation domain generalization (FDDG) framework for enhancing machinery fault diagnosis using federated learning. The FDDG framework aims to improve the generalization of diagnostic models beyond the federated environment, addressing issues related to performance drops on unseen clients. Zhao et al. [77] introduced a novel self-paced decentralized federated transfer framework for fault diagnosis in rotating machinery, addressing data privacy concerns while leveraging distributed data from diverse clients. This framework aims to improve efficiency, enhance security in data privacy protection, and enable fault diagnosis across a range of domains. Yang et al. [78] introduced a novel federated semi-supervised transfer fault diagnosis method called Targeted Transfer Learning through Distribution Barycenter Medium (TTL-DBM). This method is designed to address the challenges of data decentralization in fault diagnosis of machines, where transferring faults between source and target domains requires a different approach due to data privacy concerns and the impracticality of centralized data processing. Here are some common knowledge-based approaches:
The knowledge-based system is briefly explained in the following sub-sections and presented in Fig. 9.
Figure 9: Schematic of knowledge-based system
These systems use a set of if-then rules to represent expert knowledge and diagnose faults. Rules are created based on the experience of human experts. The inference engine applies logical rules to the knowledge base to derive conclusions about the state of the system.
Wu et al. [79] demonstrated the effectiveness of a novel fault diagnosis system for internal combustion engines utilizing wavelet packet transform (WPT) and artificial neural network (ANN) techniques. The system effectively leverages the signal processing capabilities of WPT, specifically its ability to decompose engine sound emission signals into informative frequency bands and extract entropy features, enabling accurate fault identification. Yang et al. [80] presented VIBEX, an expert system designed to assist plant operators in diagnosing the causes of abnormal vibration in rotating machinery. The system utilizes a probabilistic decision table based on a cause-symptom matrix, enabling automated diagnosis.
These models use mathematical equations to represent the normal behaviour of the system. Deviations from the expected behaviour indicate potential faults. These models use qualitative descriptions and relationships between components to detect inconsistencies and diagnose faults.
Isermann [81] contrasted traditional limit/trend checking approaches with model-based fault-detection methods that utilize input and output signals and dynamic process models, offering a deeper understanding of system behaviour and enabling more accurate fault diagnosis. Atoui et al. [82] presented a hybrid method for fault diagnosis in complex systems, addressing the challenges of unknown operating conditions and the need to identify single and multiple simultaneous faults.
In case-based reasoning, a library of past fault cases with their symptoms and solutions is maintained. When a new fault occurs, the system searches for similar cases in the library to find potential solutions. This involves comparing the current situation with past cases to find the best match.
Boral et al. [83] integrated case-based reasoning (CBR) with historical fault data, the framework enables automated analysis and identification of potential issues, leading to more efficient and proactive maintenance strategies. Yang et al. [84] presented a novel hybrid approach for fault diagnosis, integrating case-based reasoning (CBR) with an ART-Kohonen neural network (ART-KNN). This synergistic combination leverages the strengths of both techniques, enabling more accurate and robust fault diagnosis.
3.2.4 Fault Trees and FMECA (Failure Mode, Effects, and Criticality Analysis)
This method uses a tree structure to represent the logic leading to system failures. Each branch represents different fault events leading to the top event (failure). This systematic approach identifies potential failure modes, their effects on system performance, and the criticality of their impacts.
Mzougui et al. [85] proposed an enhanced FMECA approach that addresses the limitations of traditional methods by integrating fault tree analysis (FTA) and incorporating two additional factors, security and pollution, into the risk assessment process. The modified FMECA utilizes a five-factor RPN formula and employs the analytical hierarchy process (AHP) to determine the weight of each factor, leading to a more comprehensive and accurate risk prioritization. Du et al. [86] presented a tailored approach for conducting FMECA on remanufactured machine tools, focusing on the unique characteristics of these machines and emphasizing the importance of analyzing failure modes during service. The proposed method utilizes the RPN method for assessing the criticality of each identified failure mode.
Bayesian networks represent the probabilistic relationships between different system variables. They help in diagnosing faults by calculating the probabilities of different faults given observed symptoms.
Gao et al. [87] integrated the Haystack data model and a Bayesian network framework, the proposed methodology enables automatic identification of the most probable root cause of comfort and energy issues, considering interdependencies within the energy distribution chain. Zhou [88] addressed the critical challenges of imbalanced sample sizes and unlabeled data in fault diagnosis, proposing a novel Bayesian Graph Balanced Learning (BGBL) method. By combining a balancing strategy for imbalanced data, graph theory for unlabeled data, and Bayesian neural networks, BGBL effectively tackles these challenges.
A combination of the above methods is used to leverage their strengths and provide a more robust fault diagnosis.
These methods are widely used in various industries, including manufacturing, aerospace, automotive, and telecommunications, to ensure system reliability and maintain optimal performance. The choice of method depends on the complexity of the system, the availability of expert knowledge, and the specific requirements of the diagnostic process.
The brief summary application of traditional methods in the fault diagnosis through sensor is tabulated in Table 1.
4 Artificial Intelligence-Based Fault Diagnosis
Artificial intelligence (AI)-based fault diagnosis methods use advanced AI techniques to detect, identify, and predict faults in systems and processes as shown in Fig. 10. These methods leverage machine learning, pattern recognition, and data analytics to provide more accurate and efficient fault diagnosis compared to traditional approaches.
Figure 10: Application of ANN in fault diagnosis
Xia et al. [93] suggested that the integration of AI techniques seems promising in overcoming the challenges associated with obtaining high-quality labeled datasets in industrial settings. That Huang et al. [94] utilized a multi-scale competitive network for bearing fault diagnosis seems to address the challenges associated with detecting faults, particularly in the early stages where fault components are less prominent in the vibration signal. The use of an improved multi-scale feature fusion residual network (IMSFFRN) to extract deep features from vibration signals and efficiently fuse them at different scales sounds like a promising method to capture comprehensive fault information. Guo et al. [95] proposed the causal explaining guided domain generalization (CXDG) method to address this limitation by incorporating human decision-making into the process. By training an explaining model with conditional mutual information to identify causal features in the input data and translating these attributions into understandable insights, the method aims not only to explain the diagnostic model’s decisions but also to guide it towards focusing on causal features for improved generalization across unseen domains. Akcan et al. [96] employed 18 distinct entropy methods for feature extraction and fed these features into an extreme learning machine (ELM) model for effectively diagnosing bearing faults. Here are some of the most common AI techniques used for fault diagnosis which are also presented through Fig. 11.
Figure 11: Categorization of AI techniques
• Classification algorithms: Algorithms such as support vector machines (SVM) as shown in Fig. 12, decision trees, random forests, and neural networks are trained on labeled data (features and their corresponding fault types) to classify new observations into fault categories.
• Regression models: These models predict the severity or progression of a fault based on historical data.
Figure 12: Concept of SVM
• Clustering: Techniques such as K-means, density-based spatial clustering of applications with noise (DBSCAN), and hierarchical clustering group similar data points together. These clusters can reveal patterns that indicate normal or faulty states without prior labels.
• Anomaly detection: Algorithms like autoencoders, isolation forests, or one-class SVMs identify outliers or anomalies in the data that could signify potential faults.
Combines labelled and unlabeled data for training, which is useful when obtaining labelled data is expensive or time-consuming. Techniques include semi-supervised SVMs and semi-supervised deep learning.
The brief summary application of AI in the fault diagnosis through sensor is tabulated in Table 2.
5 Deep Learning-Based Fault Diagnosis
Deep learning-based fault diagnosis is an advanced approach that leverages deep learning techniques to detect, identify, and predict faults in complex systems. Deep learning models, can capture intricate patterns and relationships in large datasets, making them highly effective for fault diagnosis. Here’s a detailed look at how deep learning can be applied to fault diagnosis as shown in Fig. 13 and through the following steps:
Step 1: Data collection and pre-processing
• Collect large volumes of data from sensors, logs, and other monitoring tools.
• Pre-process data by normalizing, filtering, and segmenting to remove noise and irrelevant information.
Step 2: Feature extraction (Optional)
Although deep learning models can automatically learn features, sometimes domain-specific features may be manually extracted to enhance model performance.
Step 3: Model selection and training
• Choose an appropriate deep learning architecture based on the nature of the data (e.g., CNNs for images, LSTMs for time-series data).
• Split data into training, validation, and test sets.
• Train the model using labelled data, optimizing parameters using techniques like gradient descent.
Step 4: Model evaluation
• Assess the trained model using metrics like accuracy, precision, recall, and F1-score.
• Use cross-validation to ensure the model’s robustness and generalization capability.
Step 5: Deployment and monitoring
• Deploy the trained model in the operational environment.
• Continuously monitor model performance and update it as needed with new data to maintain accuracy.
Figure 13: Deep learning theories
5.1 Convolutional Neural Networks (CNNs)
CNNs are a type of deep learning algorithm particularly well-suited for image and signal processing tasks as shown in Fig. 14. Inspired by the human visual cortex, CNNs excel at recognizing complex patterns and features in data, making them highly effective for various applications [105].
Figure 14: Procedure of fault diagnosis through CNN
A CNN typically consists of multiple layers, each performing specific tasks. For instance, the Convolutional layer applies filters (kernels) to the input data to extract features. Each filter detects specific patterns or edges in the data. The pooling layer reduces the dimensionality of the data by summarizing information from smaller regions. This helps to control overfitting and improve computational efficiency [106,107]. The activation layer introduces non-linearity into the network, allowing it to learn more complex relationships between features. A fully connected layer combines the features extracted by the convolutional and pooling layers to make predictions [108,109].
CNNs learn by adjusting their weights and biases through a process called backpropagation. This involves comparing the network’s predictions to the actual labels of the training data and adjusting the weights to minimize the error.
5.2 Long Short-Term Memory (LSTM) Networks
LSTM networks are a special type of recurrent neural network (RNN) capable of learning long-term dependencies in data as shown in Fig. 15. Unlike traditional RNNs, which struggle to remember information over extended periods, LSTMs can effectively capture and process information over long sequences. The LSTMs maintain an internal memory called the cell state, which stores information over time [110]. The LSTMs employ three gates to control the flow of information. Forget gate decides which information to discard from the cell state. The input gate determines which new information to add to the cell state [111]. Whereas the output gate decides which information from the cell state to output. LSTM uses backpropagation through time (BPTT) to train their weights and biases, allowing them to learn long-term dependencies [112].
Figure 15: Architecture of LSTM
LSTMs are powerful tools for processing sequential data and capturing long-term dependencies. Their ability to remember information over extended periods makes them suitable for various applications, including NLP, time series analysis, and speech recognition.
Autoencoders are a type of artificial neural network (ANN) deigned to learn compressed representations of data as shown in Fig. 16. They work by encoding input data into a lower-dimensional latent representation and then decoding this representation back to the original input space [113]. This process forces the autoencoder to capture the most salient features of the data while discarding irrelevant information. The autoencoder consists of an encoding phase and a decoding phase. In the encoding phase, the encoder network receives the input data and compresses it into a lower-dimensional representation in the latent space [114]. This representation typically captures the essential features of the data, discarding noise and redundancy. Whereas in the decoding phase, the decoder network takes the latent representation as input and attempts to reconstruct the original input data [115]. This process ensures that the encoder has captured the most important information in the data.
Figure 16: Architecture of autoencoder
Autoencoders are a powerful tool for data representation, compression, and feature extraction, with applications in various domains. Their ability to learn compressed representations of data while preserving essential features makes them valuable for tasks such as data compression, dimensionality reduction, and generative modelling [116]. As research in autoencoders continues to advance, we can expect even more innovative applications and advancements in the future.
5.4 Generative Adversarial Networks (GANs)
GANs are a fascinating class of deep-learning algorithms that have revolutionized the field of generative modelling. By pitting two neural networks against each other a generator and a discriminator. GANs enable the creation of incredibly realistic and diverse data, from images and videos to music and text [117]. The generator of GAN takes a random noise vector as input and generates new data samples that resemble the training data. Whereas the discriminator takes both real data and generated data as input and tries to distinguish between the two [118]. The generator and discriminator are trained in an adversarial manner. The generator tries to fool the discriminator by producing increasingly realistic data, while the discriminator tries to improve its ability to distinguish real from generated data [119]. This competition drives both networks to improve their performance.
GANs are a powerful tool for creative data generation, with applications in various fields. Their ability to produce highly realistic and diverse data makes them a valuable asset for artists, researchers, and businesses [120]. As research in GANs continues to advance, we can expect even more innovative applications and advancements in the future. The architecture of GAN is shown in Fig. 17. For instance, Shao et al. [121] presented a novel auxiliary classifier GAN (ACGAN) based framework for generating realistic one-dimensional raw data from mechanical sensor signals, addressing the challenge of limited data availability in machine fault diagnosis. The proposed architecture, built upon stacked one-dimensional convolutional layers, effectively learns hierarchical representations and generates synthetic signals with labels. In conclusion, this research addresses the critical issue of imbalanced datasets in data-driven fault diagnosis for rotating machinery, a common challenge that hinders the effectiveness of existing methods [122]. By leveraging the power of generative adversarial networks (GANs), the proposed approach effectively addresses this imbalance by generating realistic synthetic data and expanding and balancing the available training dataset.
Figure 17: Architecture of GANs
Challenges
The deep learning models offer lots of advantages however they also have certain limitations. Some of them are elaborated here:
• High-quality, labelled data is essential for training deep learning models. Obtaining labelled fault data can be challenging and time-consuming.
• Deep learning models, particularly complex ones, can act as black boxes. Understanding and explaining their decisions is crucial for gaining user trust.
• Training deep learning models can be computationally intensive, requiring significant hardware resources.
• Implementing models that can process data and diagnose faults in real-time is critical for many applications, requiring optimization for speed and efficiency.
• Ensuring the model remains accurate over time requires regular updates with new data and ongoing validation.
Fault diagnosis in mechanical systems is crucial for ensuring safety, reliability, and optimal performance. Recent breakthroughs in sensor fault diagnosis have leveraged the power of attention mechanisms, a key concept in deep learning, to revolutionize how we understand and address these issues [123]. Attention mechanisms, inspired by human cognitive processes, allow models to selectively focus on relevant information within complex data [124]. This is particularly beneficial in mechanical systems where multiple sensors collect diverse data streams, each contributing a piece to the overall system’s health.
Attention mechanisms effectively integrate data from multiple sensors, prioritizing crucial information based on its relevance to the diagnosis. Attention mechanisms excel at capturing temporal dependencies, highlighting critical points in the time series that signal impending failure [125]. Attention mechanisms offer interpretability by revealing which features contribute most to the diagnosis. Attention mechanisms can efficiently reduce the dimensionality of high-dimensional data by focusing on the most informative features. Han et al. [126] introduced a novel squeeze-excitation attention-guided sparse filtering (SESF) method. Combining the benefits of attention mechanisms and unsupervised learning, SESF effectively extracts discriminative features from multi-scale inputs of variable speed signals. The embedded squeeze-excitation attention mechanism guides model training, focusing on regions with the highest classification potential. Li et al. [127] addressed the challenges of traditional fault diagnosis methods for mechanical components by proposing a novel Attention Improved CNN (AT-ICNN) model. By integrating an improved convolutional layer and a hybrid attention mechanism, AT-ICNN effectively extracts relevant fault features, enhances feature representation, and captures global information, leading to significantly improved diagnostic accuracy.
Despite these advancements, the accuracy of attention-based models relies heavily on the quality and availability of sensor data. Selecting the optimal hyperparameters for these models requires careful experimentation and can be computationally expensive. While attention mechanisms enhance interpretability, further research is needed to enhance their explainability, making them more accessible to non-experts.
5.6 Graph Neural Network (GNN)
GNNs have emerged as a powerful tool for fault diagnosis in mechanical components, leveraging the inherent structure and relationships within complex systems. GNNs excel at analysing data represented as graphs, where nodes represent components and edges signify their interactions [128,129]. This allows GNNs to capture intricate dependencies and propagate information across the entire system, leading to more accurate and insightful fault diagnoses [130].
The researchers have also proposed advancements in GNNs such as deep graph convolutional networks (DGCNNs) which apply the convolution operations on the graph, effectively capturing local patterns and dependencies between neighbouring nodes. This enhances the ability to identify subtle changes within the system, leading to more sensitive fault detection. Graph attention networks (GATs) are another advancement which incorporates attention mechanisms, allowing the network to focus on the most informative relationships between components. This improves the efficiency and accuracy of fault diagnosis by selectively prioritizing relevant connections. Spatio-temporal GNNs integrate spatial and temporal information, enabling them to analyze time-series data while considering the system’s spatial structure. This is particularly useful for diagnosing dynamic faults that evolve over time. Zhang et al. [131] addressed the critical challenge of multisensor fault diagnosis under noisy signals by introducing a novel multiscale channel attention-driven graph dynamic fusion network. This approach effectively tackles the inconsistent signal quality across different channels. By strategically incorporating channel attention weights and a graph dynamic fusion framework, the method excels at mining feature differences, achieving deep-level feature fusion, and dynamically adapting to real-time data. Furthermore, the graph dynamic reconstruction module enhances the reliability of the fusion process. Zhang et al. [132] proposed a novel multi-sensor multi-head graph attention network (MMHGAT) model. By leveraging the power of multi-head attention, MMHGAT dynamically fuses and extracts high-level fault characteristics from multiple sensor subgraphs, overcoming the limitations of manual feature selection and single-sensor analysis.
GNNs offer several advantages, however, some challenges are associated with it such as GNNs often require large datasets of labelled data to train effectively, which can be a challenge in the context of rare and complex faults. Training and deploying GNNs can be computationally expensive, particularly for large, complex systems. While GNNs provide powerful insights, understanding their decision-making process can be challenging due to the complexity of the graph structure and the message-passing mechanism.
5.7 Kolmogorov Arnold Network (KAN)
KAN offer a novel approach to fault diagnosis in mechanical components, leveraging their ability to model complex, nonlinear systems with remarkable accuracy. These networks, inspired by the Kolmogorov-Arnold representation theorem, provide a powerful framework for capturing intricate relationships within sensor data and predicting potential failures.
KAN by design, excel at capturing complex nonlinear relationships within the data, providing a more realistic representation of system behaviour. KAN possess the remarkable property of being universal approximators. This means they can approximate any continuous function to arbitrary accuracy, making them highly adaptable to the diverse range of fault signatures encountered in mechanical components. KAN can learn directly from data, eliminating the need for extensive prior knowledge or complex mathematical models. This makes them particularly suitable for systems with limited understanding or those exhibiting unpredictable behaviour. Polar et al. [133] delved into the practical construction of Kolmogorov-Arnold representations, demonstrating its equivalence to a specific type of Urysohn tree. This insight leads to the development of a novel, computationally stable algorithm for constructing such trees, offering significant improvements in efficiency and speed.
However, training KAN can be computationally expensive, particularly for complex systems with large datasets. Selecting optimal hyperparameters for KAN requires careful experimentation and can be challenging. While KAN offers some level of interpretability, understanding their internal workings and decision-making processes can be difficult.
Deep learning-based fault diagnosis offers powerful tools for enhancing the reliability and efficiency of various systems. By leveraging the capabilities of deep learning, industries can achieve more accurate, timely, and predictive fault diagnosis, leading to improved operational performance and reduced downtime.
The brief summary application of deep learning methods in the fault diagnosis through sensor is tabulated in Table 3.
6 Future of Sensor Technology in Fault Diagnosis
Transfer learning has emerged as a powerful technique in fault diagnosis, enabling the transfer of knowledge from one domain to another, as illustrated in Fig. 16. This approach leverages pre-trained models or knowledge from related tasks to enhance the performance of fault diagnosis models, particularly when dealing with limited data or computational resources [143].
6.1.1 Benefits and Applications of Transfer Learning in Fault Diagnosis
Transfer learning significantly accelerates model development by utilizing pre-trained models that have already learned from vast datasets. Models trained on one domain can be adapted to new domains with similar characteristics, reducing the need for extensive domain-specific training data [144]. This capability leads to notable improvements in the accuracy and efficiency of fault diagnosis models, especially when handling complex tasks or limited data availability.
Recent research showcases the effectiveness of transfer learning in fault diagnosis:
• Deep transfer learning architecture: Zhang et al. [145] proposed a deep transfer learning architecture employing a wide convolution kernel convolutional long short-term memory neural network (WCL) to enhance feature extraction. A multiple transfer learning scheme enables knowledge transfer from a large-scale source domain to a target domain with limited data.
• Domain adaptation fault diagnosis model: Yu et al. [146] introduced a domain adaptation fault diagnosis model based on ResNet and Transformer (DAFDMRT), combining time-frequency analysis with deep feature extraction and domain adaptation techniques. The model utilizes wavelet packet transforms to capture multi-scale time-frequency information, employs a deep fusion network based on ResNet and Transformer to extract local and global features, and utilizes multi-kernel maximum mean discrepancy to minimize distribution differences between source and target domains.
6.1.2 Challenges and Strategies for Effective Transfer Learning
Despite its potential, transfer learning presents certain challenges:
• Domain differences: Transferring knowledge between domains can be complex due to variations in data distribution, sensor characteristics, and operating conditions [147,148].
• Performance impact: In some cases, transferring knowledge from a different domain may negatively affect the performance of the target model [149,150].
• Model selection: Choosing the appropriate pre-trained model or knowledge source is crucial for successful transfer learning.
To mitigate these challenges, the following strategies can be employed for effective transfer learning:
• Fine-tuning: Adjusting the parameters of a pre-trained model on the target domain data can improve its performance.
• Feature transfer: Transferring features learned from a pre-trained model can be beneficial for developing new fault diagnosis models [151].
• Model simplification: Transferring knowledge from a complex model to a simpler model can enhance efficiency and reduce computational requirements.
6.1.3 A Step-by-Step Guide to Applying Transfer Learning in Fault Diagnosis
The procedure for applying transfer learning in fault diagnosis of industrial components can be summarized as follows:
1. Problem definition: Identify the component, its faults, and the desired output (classification, regression, anomaly detection). Determine the available data.
2. Model selection: Select a model architecture (CNN, RNN, etc.) and a domain (similar to industrial equipment, if possible) with strong performance on comparable tasks.
3. Fine-tuning and optimization: Freeze initial layers, gradually unfreeze later layers, adjust the learning rate, optimize the output layer, and select an appropriate loss function.
4. Evaluation and analysis: Use a hold-out dataset or cross-validation to assess model performance. Compare to relevant baselines. Analyze the impact of different transfer learning strategies.
5. Deployment and monitoring: Integrate the trained model into the monitoring system. Track performance over time and retrain the model periodically to ensure continued effectiveness.
By adopting these strategies and following this structured approach, practitioners can effectively leverage transfer learning to create more efficient and accurate fault diagnosis models. This advancement contributes to the development of robust and intelligent industrial systems, ultimately leading to improved performance, reduced downtime, and enhanced operational efficiency.
The emergence of Explainable Artificial Intelligence (XAI) has brought a crucial dimension to the field of fault diagnosis. XAI addresses the critical need for transparency and trust in AI-based models, ensuring users can comprehend the underlying decision-making processes [152].
6.2.1 The Importance of XAI in Fault Diagnosis
XAI techniques aim to provide insights into the reasoning behind AI model predictions, allowing users to understand “how” and “why” these predictions are made as shown in Fig. 18. This enhanced interpretability fosters trust in AI models by making their predictions more understandable and accountable [153]. Furthermore, XAI facilitates the identification of the root causes of faults, guiding the development of effective troubleshooting strategies. A deeper understanding of the reasoning behind AI-based fault diagnosis contributes to more informed and reliable decision-making [154].
Figure 18: Explainable AI in fault diagnosis
6.2.2 Key Contributions and Challenges
Researchers have made significant progress in applying XAI principles to fault diagnosis. For instance, Cohen et al. [155] proposed a novel clustering framework based on Shapley values, designed to work effectively with semi-supervised learning problems often characterized by class imbalance and weakly labeled datasets. Kobayashi et al. [156] emphasized the critical role of XAI and interpretable machine learning (IML) in ensuring that AI models not only accurately predict remaining useful life (RUL) but also maintain transparency in their decision-making processes.
Despite these advancements, deep neural networks, renowned for their high accuracy in fault diagnosis, often present challenges in interpretability due to their complex decision-making processes. Balancing the need for interpretability with the desire for high accuracy remains a crucial consideration in XAI development. The pursuit of higher interpretability sometimes necessitates compromises in model accuracy, highlighting the importance of a nuanced approach.
6.2.3 Navigating the Balance between Accuracy and Interpretability
The ideal balance between interpretability and accuracy in XAI is heavily dependent on the specific application and user requirements. A one-size-fits-all solution does not exist. By thoroughly understanding user needs and the context of the application, it becomes possible to select or develop XAI techniques that effectively strike this balance and promote the adoption of trustworthy AI in the industry [157,158].
6.2.4 A practical Framework for Applying XAI in Fault Diagnosis
The following steps outline a procedure for effectively applying XAI in the fault diagnosis of industrial components:
1. Method selection: Choose an XAI method that aligns with your model and desired level of explainability. Popular examples include LIME, SHapley Additive exPlanations (SHAP), and decision trees.
2. Implementation: Apply the chosen XAI method to the fault diagnosis model. This process may involve generating explanations during model training or after deployment.
3. Explanation analysis: Analyze the generated explanations to gain a comprehensive understanding of:
• Feature importance: Identify the features most critical for the diagnosis.
• Feature contribution: Determine how different feature values influence the model’s prediction.
• Bias detection: Identify any unexpected patterns or biases in the model’s decisions.
4. Actionable insights: Utilize the insights gained from XAI to:
• Bias mitigation: Identify and address biases or feature dependencies.
• Trust enhancement: Ensure that the model’s decisions are understandable and trustworthy.
• Root cause identification: Quickly identify the root causes of faults and facilitate effective maintenance strategies.
By diligently following these steps, practitioners can leverage XAI to enhance the interpretability, reliability, and actionability of fault diagnosis models. This approach ultimately leads to improved system performance and reduced downtime, solidifying the value of XAI in the advancement of trustworthy and effective fault diagnosis systems.
Recent advancements in Artificial Intelligence (AI) and sensor technology have significantly enhanced sensor fault diagnosis capabilities, driving progress in various industrial and technological domains. AI-powered methods offer improved accuracy and efficiency, while cutting-edge sensor technologies enable real-time monitoring and remote diagnosis. These innovations have resulted in enhanced system reliability, safety, and efficiency. As research and development continue, we anticipate further progress in sensor fault diagnosis, leading to even more sophisticated and robust systems. This paper provides a comprehensive review of the current state of sensor fault diagnosis technologies and their significance in various industries. It outlines common sensor fault types found in monitoring and control systems. The review highlights how recent fault diagnosis methods incorporate advanced technologies to address the key challenge of reducing computational complexity in diagnosis systems.
Future sensor development must prioritize not only higher efficiency but also greater reliability. To achieve this, the following key aspects require focused attention:
• Enhanced Manufacturing Technology: Improved sensor manufacturing techniques are crucial for reducing fault susceptibility and enhancing adaptability to complex environments. This includes the development of sensors with greater robustness to environmental factors, such as temperature, humidity, and vibration.
• Comprehensive Fault Diagnosis Systems: Building comprehensive sensor fault diagnosis systems that can detect faults at their earliest stages is critical for preventing complete sensor failure. These systems should be designed to identify a wide range of fault types, including both known and novel faults, and provide early warnings before significant system disruptions occur.
The review highlights how recent fault diagnosis methods incorporate advanced technologies. Diagnostic algorithms should be lightweight, capable of immediate fault detection and diagnosis, and able to differentiate between various fault types. Additionally, they should identify novel faults without misclassifying them as known faults or standard operations. Deep learning and big data analytics emerge as the most promising methods for achieving these objectives. Furthermore, incorporating advanced fault detection and isolation (FDI) technologies from other domains, such as system process fault diagnosis methods, can contribute to effective sensor fault detection. The future research should concentrate on:
• Fault-Tolerant Control Strategies: Developing fault-tolerant control strategies for sensors is essential to mitigate the effects of sudden sensor failures. This could involve employing redundant sensors, implementing adaptive control algorithms, or utilizing sensor fusion techniques.
• Compensation Measures: Exploring compensation measures to mitigate sudden sensor failures is crucial for maintaining system stability and performance. This could involve using data from other sensors to estimate the faulty sensor’s output or applying model-based compensation techniques.
The rapid advancements in AI and sensor technology have revolutionized sensor fault diagnosis, significantly enhancing system reliability, safety, and efficiency. Continued research focusing on developing comprehensive fault diagnosis systems, incorporating advanced technologies, and addressing challenges related to computational complexity and novel fault identification will pave the way for even more sophisticated and robust sensor fault diagnosis systems in the future.
Acknowledgement: None.
Funding Statement: No funding has been received for this work. However, this work is supported by the National Center of Science, Poland under Sheng2 project No. UMO-2021/40/Q/ST8/00024: NonGauMech—New Methods of Processing Non-Stationary Signals (Identification, Segmentation, Extraction, Modeling) with Non-Gaussian Characteristics for the Purpose of Monitoring Complex Mechanical Structures.
Author Contributions: Sumika Chauhan: Conceptualization, Investigation, Data curation, Writing original draft. Govind Vashishtha: Conceptualization, Investigation, Writing original draft. Radoslaw Zimroz: Conceptualization, Investigation, Supervision, Writing original draft & review & editing. All authors reviewed the results and approved the final version of the manuscript.
Availability of Data and Materials: No data is attached to this work.
Ethics Approval: Not applicable.
Conflicts of Interest: The authors declare that they have no conflicts of interest to report regarding the present study.
References
1. Vashishtha G, Chauhan S, Singh M, Kumar R. Bearing defect identification by swarm decomposition considering permutation entropy measure and opposition-based slime mould algorithm. Measurement. 2021;178:109389. doi:10.1016/j.measurement.2021.109389. [Google Scholar] [CrossRef]
2. Kumar R, Kumar P, Vashishtha G, Chauhan S, Zimroz R. Fault identification of direct-shift gearbox using variational mode decomposition and convolutional neural network. Machines. 2024;12(7):428. doi:10.3390/machines12070428. [Google Scholar] [CrossRef]
3. Chauhan S, Singh M, Kumar Aggarwal A. Bearing defect identification via evolutionary algorithm with adaptive wavelet mutation strategy. Measurement. 2021;179:109445. doi:10.1016/j.measurement.2021.109445. [Google Scholar] [CrossRef]
4. Chauhan S, Singh M, Kumar Aggarwal A. An effective health indicator for bearing using corrected conditional entropy through diversity-driven multi-parent evolutionary algorithm. Struct Health Monit. 2021;20(5):2525–39. doi:10.1177/1475921720962419. [Google Scholar] [CrossRef]
5. Gawde S, Patil S, Kumar S, Kotecha K. A scoping review on multi-fault diagnosis of industrial rotating machines using multi-sensor data fusion. Artif Intell Rev. 2022;56(5):4711–64. doi:10.1007/S10462-022-10243-Z. [Google Scholar] [CrossRef]
6. Argawal R, Kalel D, Harshit M, Domnic AD, Singh RR. Sensor fault detection using machine learning technique for automobile drive applications. In: 2021 National Power Electronics Conference (NPEC), 2021; Bhubaneswar, India; p. 1–6. doi:10.1109/NPEC52100.2021.9672546. [Google Scholar] [CrossRef]
7. Bilal H, Obaidat MS, Aslam MS, Zhang J, Yin B, Mahmood K. Online fault diagnosis of industrial robot using IoRT and hybrid deep learning techniques: an experimental approach. IEEE Internet Things J. 2024;11(19):31422–37. doi:10.1109/JIOT.2024.3418352. [Google Scholar] [CrossRef]
8. Yousuf M, Alsuwian T, Amin AA, Fareed S, Hamza M. IoT-based health monitoring and fault detection of industrial AC induction motor for efficient predictive maintenance. Meas Control. 2024;57(8):1146–60. [Google Scholar]
9. Zhang Y, Ding J, Li Y, Ren Z, Feng K. Multi-modal data cross-domain fusion network for gearbox fault diagnosis under variable operating conditions. Eng Appl Artif Intell. 2024;133(21):108236. doi:10.1016/J.ENGAPPAI.2024.108236. [Google Scholar] [CrossRef]
10. Vashishtha G, Chauhan S, Kumar S, Kumar R, Zimroz R, Kumar A. Intelligent fault diagnosis of worm gearbox based on adaptive CNN using amended gorilla troop optimization with quantum gate mutation strategy. Knowl-Based Syst. 2023;280:110984. doi:10.1016/j.knosys.2023.110984. [Google Scholar] [CrossRef]
11. Chauhan S, Vashishtha G, Kumar R, Zimroz R, Gupta MK, Kundu P. An adaptive feature mode decomposition based on a novel health indicator for bearing fault diagnosis. Measurement. 2024;226:114191. [Google Scholar]
12. Vashishtha G, Kumar R. Autocorrelation energy and aquila optimizer for MED filtering of sound signal to detect bearing defect in Francis turbine. Meas Sci Technol. 2021;33(1):15006. doi:10.1088/1361-6501/ac2cf2. [Google Scholar] [CrossRef]
13. Vashishtha G, Chauhan S, Yadav N, Kumar A, Kumar R. A two-level adaptive chirp mode decomposition and tangent entropy in estimation of single-valued neutrosophic cross-entropy for detecting impeller defects in centrifugal pump. Appl Acoust. 2022;197(3):108905. doi:10.1016/j.apacoust.2022.108905. [Google Scholar] [CrossRef]
14. Xu S, Chen X, Yang W, Liu F, Chai Y. Current sensor incipient fault diagnosis in PMSM drive systems using novel interval sliding mode observer. IEEE Trans Instrum Meas. 2024;73:1–11. doi:10.1109/TIM.2024.3351232. [Google Scholar] [CrossRef]
15. Langarica S, Ruffelmacher C, Nunez F. An industrial internet application for real-time fault diagnosis in industrial motors. IEEE Trans Autom Sci Eng. 2020;17(1):284–95. doi:10.1109/TASE.2019.2913628. [Google Scholar] [CrossRef]
16. Li X, Zhang W, Xu NX, Ding Q. Deep learning-based machinery fault diagnostics with domain adaptation across sensors at different places. IEEE Trans Ind Electron. 2020;67(8):6785–94. doi:10.1109/TIE.2019.2935987. [Google Scholar] [CrossRef]
17. Min H, Fang Y, Wu X, Lei X, Chen S, Teixeira R, et al. A fault diagnosis framework for autonomous vehicles with sensor self-diagnosis. Expert Syst Appl. 2023;224(9):120002. doi:10.1016/j.eswa.2023.120002. [Google Scholar] [CrossRef]
18. Jan SU, Lee Y-D, Shin J, Koo I. Sensor fault classification based on support vector machine and statistical time-domain features. IEEE Access. 2017;5:8682–90. doi:10.1109/ACCESS.2017.2705644. [Google Scholar] [CrossRef]
19. Mian T, Choudhary A, Fatima S. Multi-sensor fault diagnosis for misalignment and unbalance detection using machine learning. In: 2022 IEEE International Conference on Power Electronics, Smart Grid, and Renewable Energy (PESGRE), 2022; Trivandrum, India; p. 1–6. doi:10.1109/PESGRE52268.2022.9715938. [Google Scholar] [CrossRef]
20. Zhang X, Zhao J, Bajrić R, Wang L. Application of the DC offset cancellation method and S transform to gearbox fault diagnosis. Appl Sci. 2017;7(2):207. doi:10.3390/app7020207. [Google Scholar] [CrossRef]
21. Kuruppu SS, Zou Y. Static position sensor bias fault diagnosis in permanent magnet synchronous machines via current estimation. IEEE/ASME Trans Mechatron. 2021;26(2):888–96. doi:10.1109/TMECH.2020.3010898. [Google Scholar] [CrossRef]
22. Liu J, Xu Z, Xu Y, Liang X, Pang R. An analytical method for dynamic analysis of a ball bearing with offset and bias local defects in the outer race. J Sound Vib. 2019;461(4):114919. doi:10.1016/j.jsv.2019.114919. [Google Scholar] [CrossRef]
23. Hou L, Yang L. Machine fault diagnosis using industrial wireless sensor networks and on-sensor wavelet transform. In: IECON, 2017—43rd Annual Conference of the IEEE Industrial Electronics Society, 2017; Beijing, China; p. 6045–50. [Google Scholar]
24. Badihi H, Zhang Y, Hong H. Fuzzy gain-scheduled active fault-tolerant control of a wind turbine. J Frankl Inst. 2014;351(7):3677–706. doi:10.1016/j.jfranklin.2013.05.007. [Google Scholar] [CrossRef]
25. Xu F, Olaru S, Seron MM. Observer gain optimization for minimization of minimal robust positively invariant set and invariant set-based fault detection. Automatica. 2024;160(6):111413. doi:10.1016/j.automatica.2023.111413. [Google Scholar] [CrossRef]
26. Dong Y, Jiang H, Jiang W, Xie L. Dynamic normalization supervised contrastive network with multiscale compound attention mechanism for gearbox imbalanced fault diagnosis. Eng Appl Artif Intell. 2024;133(4):108098. doi:10.1016/j.engappai.2024.108098. [Google Scholar] [CrossRef]
27. Chen YD, Du R, Qu LS. Fault features of large rotating machinery and diagnosis using sensor fusion. J Sound Vib. 1995;188(2):227–42. doi:10.1006/jsvi.1995.0588. [Google Scholar] [CrossRef]
28. Wang W, Geng Y, Huang S, Yu Y, Yang Y. Sensor fault estimation based on ellipsoid bundles for dynamic point-the-bit rotary steerable systems. Measurement. 2024;235(5):114973. doi:10.1016/j.measurement.2024.114973. [Google Scholar] [CrossRef]
29. He Z, Shen C, Chen B, Shi J, Huang W, Zhu Z, et al. A new feature boosting based continual learning method for bearing fault diagnosis with incremental fault types. Adv Eng Inform. 2024;61(22):102469. doi:10.1016/j.aei.2024.102469. [Google Scholar] [CrossRef]
30. Peng X, Duan S, Sankavaram C, Jin X. Unsupervised adaptive fleet battery pack fault detection with concept drift under evolving environment. IEEE Trans Autom Sci Eng. 2024;21(3):2276–88. doi:10.1109/TASE.2024.3363002. [Google Scholar] [CrossRef]
31. Jo T, Park I, Lee J, Yoon J, Lee J, Kim H. A fault diagnosis and fault-tolerant anti-lock brake system control for actuator stuck failures in braking system in autonomous vehicles. IEEE Trans Transp Electrification. 2024. doi:10.1109/TTE.2024.3389044. [Google Scholar] [CrossRef]
32. Liu S, Zheng Z, Zhu B, Guan Z. Adaptive fault-tolerant control for attitude tracking of a carrier-based aircraft subject to actuator faults. IEEE Trans Aerosp Electron Syst. 2024;1–13. doi:10.1109/TAES.2024.3401672. [Google Scholar] [CrossRef]
33. Rivas A, Delipei GK, Davis I, Bhongale S, Yang J, Hou J. A component diagnostic and prognostic framework for pump bearings based on deep learning with data augmentation. Reliab Eng Syst Saf. 2024;247(8):110121. doi:10.1016/j.ress.2024.110121. [Google Scholar] [CrossRef]
34. Xu X, Luo M, Tan Z, Pei R. Echo signal extraction method of laser radar based on improved singular value decomposition and wavelet threshold denoising. Infrared Phys Technol. 2018;92:327–35. doi:10.1016/j.infrared.2018.06.028. [Google Scholar] [CrossRef]
35. Mitra B, Deshmukh M, Kumar A. A novel approach for single-shot target recognition by matching graph of feature pixels. Procedia Comput Sci. 2024;235(2):530–8. doi:10.1016/j.procs.2024.04.052. [Google Scholar] [CrossRef]
36. Raman S, De Silva CW. Sensor-fault tolerant condition monitoring of an industrial machine. Int J Inf Acquis. 2013;9:1350001. doi:10.1142/S0219878913500010. [Google Scholar] [CrossRef]
37. Kim D, Park Y, Kang B, Huh NS. Failure analysis of the rotating shaft in the rail grinding car. Eng Fail Anal. 2024;159(2):108100. doi:10.1016/j.engfailanal.2024.108100. [Google Scholar] [CrossRef]
38. Xu L, Xia C, Chang L. Dynamic modeling and vibration analysis of an RV reducer with defective needle roller bearings. Eng Fail Anal. 2024;157(11):107884. doi:10.1016/j.engfailanal.2023.107884. [Google Scholar] [CrossRef]
39. Venturini S, Rosso C, Velardocchia M. An automotive steel wheel digital twin for failure identification under accelerated fatigue tests. Eng Fail Anal. 2024;158(9):107979. doi:10.1016/j.engfailanal.2024.107979. [Google Scholar] [CrossRef]
40. Maseda FJ, López I, Martija I, Alkorta P, Garrido AJ, Garrido I. Sensors data analysis in supervisory control and data acquisition (SCADA) systems to foresee failures with an undetermined origin. Sensors. 2021;21(8):2762. doi:10.3390/s21082762 [Google Scholar] [PubMed] [CrossRef]
41. Fu Y, Zhao S, Zhang B, Tian Y, Wang D, Ban X, et al. Multifunctional cross-sensitive magnetic alginate-chitosan-polyethylene oxide nanofiber sensor for human-machine interaction. Int J Biol Macromol. 2024;264(1):130482. doi:10.1016/j.ijbiomac.2024.130482 [Google Scholar] [PubMed] [CrossRef]
42. Carmona-Cejas JM, Mirea T, Hervás-García R, Olivares J, Clement M. Dual-mode solidly mounted resonator-based sensor for temperature and humidity detection and discrimination. Sensors. 2024;24(9):2877. doi:10.3390/s24092877 [Google Scholar] [PubMed] [CrossRef]
43. Wang Z, Li Y, He X, Yan R, Li Z, Jiang Y, et al. Improved deep bidirectional recurrent neural network for learning the cross-sensitivity rules of gas sensor array. Sens Actuators B: Chem. 2024;401:134996. doi:10.1016/j.snb.2023.134996. [Google Scholar] [CrossRef]
44. Zamudio-Ramírez I, Osornio-Rios RA, Antonino-Daviu JA. Smart sensor for fault detection in induction motors based on the combined analysis of stray-flux and current signals: a flexible, robust approach. IEEE Ind Appl Mag. 2022;28(2):56–66. [Google Scholar]
45. Wang W, Mao Y, Cui P, Fu J, Hua W, Cheng M. Double normalization fault diagnosis method for open-circuit faults of PMSM drives. IEEE Trans Power Electron. 2024;39(9):11613–24. doi:10.1109/TPEL.2024.3404402. [Google Scholar] [CrossRef]
46. Ding A, Qin Y, Wang B, Guo L, Jia L, Cheng X. Evolvable graph neural network for system-level incremental fault diagnosis of train transmission systems. Mech Syst Signal Process. 2024;210:111175. doi:10.1016/J.YMSSP.2024.111175. [Google Scholar] [CrossRef]
47. Gao Z, Cecati C, Ding SX. A survey of fault diagnosis and fault-tolerant techniques—part I: fault diagnosis with model-based and signal-based approaches. IEEE Trans Ind Electron. 2015;62(6):3757–67. doi:10.1109/TIE.2015.2417501. [Google Scholar] [CrossRef]
48. Gao Z, Cecati C, Ding SX. A survey of fault diagnosis and fault-tolerant techniques—part II: fault diagnosis with knowledge-based and hybrid/active approaches. IEEE Trans Ind Electron. 2015;62:3768–74. doi:10.1109/TIE.2015.2419013. [Google Scholar] [CrossRef]
49. Kibrete F, Engida Woldemichael D, Shimels Gebremedhen H. Multi-sensor data fusion in intelligent fault diagnosis of rotating machines: a comprehensive review. Measurement. 2024;232(4):114658. doi:10.1016/J.MEASUREMENT.2024.114658. [Google Scholar] [CrossRef]
50. Tan J, Wan J, Chen B, Safran M, Alqahtani SA, Zhang R. Selective feature reinforcement network for robust remote fault diagnosis of wind turbine bearing under non-ideal sensor data. IEEE Trans Instrum Meas. 2024;73:1–11. doi:10.1109/TIM.2024.3375958. [Google Scholar] [CrossRef]
51. Tang H, Tang Y, Su Y, Feng W, Wang B, Chen P, et al. Feature extraction of multi-sensors for early bearing fault diagnosis using deep learning based on minimum unscented kalman filter. Eng Appl Artif Intell. 2024;127(5):107138. doi:10.1016/J.ENGAPPAI.2023.107138. [Google Scholar] [CrossRef]
52. Li X, Wang Y, Yao J, Li M, Gao Z. Multi-sensor fusion fault diagnosis method of wind turbine bearing based on adaptive convergent viewable neural networks. Reliab Eng Syst Saf. 2024;245(1):109980. doi:10.1016/J.RESS.2024.109980. [Google Scholar] [CrossRef]
53. Xu X, Guo H, Zhang Z, Yu S, Chang L, Steyskal F, et al. A cloud model-based interval-valued evidence fusion method and its application in fault diagnosis. Inf Sci. 2024;658(9):119995. doi:10.1016/J.INS.2023.119995. [Google Scholar] [CrossRef]
54. Wang C, Zhang Y, Zhao Z, Chen X, Hu J. Dynamic model-assisted transferable network for liquid rocket engine fault diagnosis using limited fault samples. Reliab Eng Syst Saf. 2024;243:109837. doi:10.1016/J.RESS.2023.109837. [Google Scholar] [CrossRef]
55. Tang S, Cheong Khoo B, Zhu Y, Meng Lim K, Yuan S. A light deep adaptive framework toward fault diagnosis of a hydraulic piston pump. Appl Acoust. 2024;217(1):109807. doi:10.1016/J.APACOUST.2023.109807. [Google Scholar] [CrossRef]
56. Wang Q, Xu Y, Yang S, Chang J, Zhang J, Kong X. A domain adaptation method for bearing fault diagnosis using multiple incomplete source data. J Intell Manuf. 2024;35:777–91. doi:10.1007/S10845-023-02075-7/FIGURES/12. [Google Scholar] [CrossRef]
57. Kumar S, Ghoshal SK, Das J. Model-based single-fault disambiguation using temporal information and genetic algorithm: a case study on hydraulic drive system. Arab J Sci Eng. 2024;1–19. doi:10.1007/S13369-023-08667-Y/TABLES/10. [Google Scholar] [CrossRef]
58. Zhang X, Jiang L, Wang L, Zhang T, Zhang F. A pruned-optimized weighted graph convolutional network for axial flow pump fault diagnosis with hydrophone signals. Adv Eng Inform. 2024;60:102365. doi:10.1016/J.AEI.2024.102365. [Google Scholar] [CrossRef]
59. Yu M, Xiao C, Jiang W, Yang S, Wang H. Fault diagnosis for electromechanical system via extended analytical redundancy relations. IEEE Trans Ind Inform. 2018;14(12):5233–44. doi:10.1109/TII.2018.2842255. [Google Scholar] [CrossRef]
60. Amrane A, Larabi A, Aitouche A. Fault detection and isolation based on nonlinear analytical redundancy applied to an induction machine. In: 2017 6th International Conference on Systems and Control (ICSC), 2017; Batna, Algeria; p. 255–60. doi:10.1109/ICoSC.2017.7958716. [Google Scholar] [CrossRef]
61. Jeong H, Park B, Park S, Min H, Lee S. Fault detection and identification method using observer-based residuals. Reliab Eng Syst Saf. 2019;184(4):27–40. doi:10.1016/j.ress.2018.02.007. [Google Scholar] [CrossRef]
62. Campos-Delgado DU, Espinoza-Trejo DR. An observer-based diagnosis scheme for single and simultaneous open-switch faults in induction motor drives. IEEE Trans Ind Electron. 2011;58(2):671–9. doi:10.1109/TIE.2010.2047829. [Google Scholar] [CrossRef]
63. El Bouchikhi EH, Choqueuse V, Benbouzid M. Induction machine faults detection using stator current parametric spectral estimation. Mech Syst Signal Process. 2015;52–53:447–64. doi:10.1016/j.ymssp.2014.06.015. [Google Scholar] [CrossRef]
64. de Souza RPP, Agulhari CM, Goedtel A, Castoldi MF. Inter-turn short-circuit fault diagnosis using robust adaptive parameter estimation. Int J Electr Power Energy Syst. 2022;139(2):107999. doi:10.1016/j.ijepes.2022.107999. [Google Scholar] [CrossRef]
65. Zhong M, Xue T, Song Y, Ding SX, Ding EL. Parity space vector machine approach to robust fault detection for linear discrete-time systems. IEEE Trans Syst Man Cybern Syst. 2021;51(7):4251–61. doi:10.1109/TSMC.2019.2930805. [Google Scholar] [CrossRef]
66. Li D, Zhao Y, Zhao Y. A dynamic-model-based fault diagnosis method for a wind turbine planetary gearbox using a deep learning network. IEEE Prot Control Mod Power Syst. 2022;7(1):1–14. doi:10.1186/s41601-022-00244-z. [Google Scholar] [CrossRef]
67. Zhang J, Ma W, Lin J, Ma L, Jia X. Fault diagnosis approach for rotating machinery based on dynamic model and computational intelligence. Measurement. 2015;59(9):73–87. doi:10.1016/j.measurement.2014.09.045. [Google Scholar] [CrossRef]
68. Mishra C, Samantaray AK, Chakraborty G. Bond graph modeling and experimental verification of a novel scheme for fault diagnosis of rolling element bearings in special operating conditions. J Sound Vib. 2016;377(6):302–30. doi:10.1016/j.jsv.2016.05.021. [Google Scholar] [CrossRef]
69. Dash MB, Bouamama BO, Boukerdja M, Pekpe KM. Bond Graph-CNN based hybrid fault diagnosis with minimum labeled data. Eng Appl Artif Intell. 2024;131:107734. [Google Scholar]
70. Zhang Y, Shen C, Shi J, Li C, Lin X, Zhu Z, et al. Deep adaptive sparse residual networks: a lifelong learning framework for rotating machinery fault diagnosis with domain increments. Knowl-Based Syst. 2024;293(3):111679. doi:10.1016/J.KNOSYS.2024.111679. [Google Scholar] [CrossRef]
71. Maurya M, Panigrahi I, Dash D, Malla C. Intelligent fault diagnostic system for rotating machinery based on IoT with cloud computing and artificial intelligence techniques: a review. Soft Comput. 2024;28:477–94. doi:10.1007/S00500-023-08255-0/TABLES/1. [Google Scholar] [CrossRef]
72. Sarwar U, Muhammad M, Mokhtar AA, Khan R, Behrani P, Kaka S. Hybrid intelligence for enhanced fault detection and diagnosis for industrial gas turbine engine. Results Eng. 2024;21(10):101841. doi:10.1016/J.RINENG.2024.101841. [Google Scholar] [CrossRef]
73. Zhang X, Deng X, Cao Y, Xiao L. Nonlinear predictable feature learning with explanatory reasoning for complicated industrial system fault diagnosis. Knowl-Based Syst. 2024;286(3):111404. doi:10.1016/J.KNOSYS.2024.111404. [Google Scholar] [CrossRef]
74. Vo TT, Liu MK, Tran MQ. Harnessing attention mechanisms in a comprehensive deep learning approach for induction motor fault diagnosis using raw electrical signals. Eng Appl Artif Intell. 2024;129(4):107643. doi:10.1016/j.engappai.2023.107643. [Google Scholar] [CrossRef]
75. Fu X, Tao J, Jiao K, Liu C. A novel semi-supervised prototype network with two-stream wavelet scattering convolutional encoder for TBM main bearing few-shot fault diagnosis. Knowl-Based Syst. 2024;286(1):111408. doi:10.1016/j.knosys.2024.111408. [Google Scholar] [CrossRef]
76. Zhao C, Shen W. A federated distillation domain generalization framework for machinery fault diagnosis with data privacy. Eng Appl Artif Intell. 2024;130:107765. doi:10.1016/j.engappai.2023.107765. [Google Scholar] [CrossRef]
77. Zhao K, Liu Z, Li J, Zhao B, Jia Z, Shao H. Self-paced decentralized federated transfer framework for rotating machinery fault diagnosis with multiple domains. Mech Syst Signal Process. 2024;211(109565):111258. doi:10.1016/j.ymssp.2024.111258. [Google Scholar] [CrossRef]
78. Yang B, Lei Y, Li X, Li N. Targeted transfer learning through distribution barycenter medium for intelligent fault diagnosis of machines with data decentralization. Expert Syst Appl. 2024;244(1):122997. doi:10.1016/j.eswa.2023.122997. [Google Scholar] [CrossRef]
79. Wu J-D, Liu C-H. An expert system for fault diagnosis in internal combustion engines using wavelet packet transform and neural network. Expert Syst Appl. 2009;36(3):4278–86. doi:10.1016/j.eswa.2008.03.008. [Google Scholar] [CrossRef]
80. Yang B-S, Lim D-S, Tan ACC. VIBEX: an expert system for vibration fault diagnosis of rotating machinery using decision tree and decision table. Expert Syst Appl. 2005;28(4):735–42. doi:10.1016/j.eswa.2004.12.030. [Google Scholar] [CrossRef]
81. Isermann R. Model-based fault-detection and diagnosis—status and applications. Annu Rev Control. 2005;29(1):71–85. doi:10.1016/j.arcontrol.2004.12.002. [Google Scholar] [CrossRef]
82. Atoui MA, Cohen A. Coupling data-driven and model-based methods to improve fault diagnosis. Comput Ind. 2021;128(4):103401. doi:10.1016/j.compind.2021.103401. [Google Scholar] [CrossRef]
83. Boral S, Chaturvedi SK, Naikan VNA. A case-based reasoning system for fault detection and isolation: a case study on complex gearboxes. J Qual Maint Eng. 2019;25(2):213–35. doi:10.1108/JQME-05-2018-0039. [Google Scholar] [CrossRef]
84. Yang BS, Han T, Kim YS. Integration of ART-Kohonen neural network and case-based reasoning for intelligent fault diagnosis. Expert Syst Appl. 2004;26(3):387–95. doi:10.1016/j.eswa.2003.09.009. [Google Scholar] [CrossRef]
85. Mzougui I, Elfelsoufi Z. Improvement of failure mode, effects, and criticality analysis by using fault tree analysis and analytical hierarchy process. J Fail Anal Prev. 2019;19(4):942–9. doi:10.1007/s11668-019-00681-3. [Google Scholar] [CrossRef]
86. Du Y, Liao L, Wang L. Failure mode, effects and criticality analysis of remanufactured machine tools in service. Int J Precis Eng Manuf. 2017;18(3):425–34. doi:10.1007/s12541-017-0051-2. [Google Scholar] [CrossRef]
87. Gao T, Marié S, Béguery P, Thebault S, Lecoeuche S. Integrated building fault detection and diagnosis using data modeling and Bayesian networks. Energy Build. 2024;306:113889. doi:10.1016/j.enbuild.2024.113889. [Google Scholar] [CrossRef]
88. Zhou Z. Fault diagnosis method for imbalanced and unlabeled data based on bayesian graph balanced learning. Meas Sci Technol. 2024;35(9):096131. doi:10.1088/1361-6501/ad5905. [Google Scholar] [CrossRef]
89. Slimani A, Ribot P, Chanthery E, Rachedi N. Fusion of model-based and data-based fault diagnosis approaches. IFAC-PapersOnLine. 2018;51(24):1205–11. doi:10.1016/j.ifacol.2018.09.698. [Google Scholar] [CrossRef]
90. Xiao P, Wang C, Lin Z, Hao Y, Chen G, Xie L. Knowledge-based clustering federated learning for fault diagnosis in robotic assembly. Knowl-Based Syst. 2024;294(2):111792. doi:10.1016/j.knosys.2024.111792. [Google Scholar] [CrossRef]
91. Wang X, Liu M, Liu C, Ling L, Zhang X. Data-driven and Knowledge-based predictive maintenance method for industrial robots for the production stability of intelligent manufacturing. Expert Syst Appl. 2023;234(1):121136. doi:10.1016/j.eswa.2023.121136. [Google Scholar] [CrossRef]
92. Zhou A, Yu D, Zhang W. A research on intelligent fault diagnosis of wind turbines based on ontology and FMECA. Adv Eng Inform. 2015;29(1):115–25. doi:10.1016/j.aei.2014.10.001. [Google Scholar] [CrossRef]
93. Xia J, Chen Z, Chen J, He G, Huang R, Li W. A digital twin-driven approach for partial domain fault diagnosis of rotating machinery. Eng Appl Artif Intell. 2024;131(7775):107848. doi:10.1016/j.engappai.2024.107848. [Google Scholar] [CrossRef]
94. Huang Z, Zhao X. A novel multi-scale competitive network for fault diagnosis in rotating machinery. Eng Appl Artif Intell. 2024;128:107441. doi:10.1016/j.engappai.2023.107441. [Google Scholar] [CrossRef]
95. Guo C, Zhao Z, Ren J, Wang S, Liu Y, Chen X. Causal explaining guided domain generalization for rotating machinery intelligent fault diagnosis. Expert Syst Appl. 2024;243(7):122806. doi:10.1016/j.eswa.2023.122806. [Google Scholar] [CrossRef]
96. Akcan E, Kuncan M, Kaplan K, Kaya Y. Diagnosing bearing fault location, size, and rotational speed with entropy variables using extreme learning machine. J Braz Soc Mech Sci Eng. 2024;46(1):1–16. doi:10.1007/s40430-023-04567-2. [Google Scholar] [CrossRef]
97. Gültekin Ö, Cinar E, Özkan K, Yazıcı A. Real-time fault detection and condition monitoring for industrial autonomous transfer vehicles utilizing edge artificial intelligence. Sensors. 2022;22(9):3208. doi:10.3390/s22093208 [Google Scholar] [PubMed] [CrossRef]
98. Filippetti F, Franceschini G, Tassoni C, Vas P. Recent developments of induction motor drives fault diagnosis using AI techniques. IEEE Trans Ind Electron. 2000;47(5):994–1004. doi:10.1109/41.873207. [Google Scholar] [CrossRef]
99. Verma AK, Nagpal S, Desai A, Sudha R. An efficient neural-network model for real-time fault detection in industrial machine. Neural Comput Appl. 2021;33(4):1297–310. doi:10.1007/s00521-020-05033-z. [Google Scholar] [CrossRef]
100. Kumar V, Mukherjee S, Verma AK, Sarangi S. An AI-based nonparametric filter approach for gearbox fault diagnosis. IEEE Trans Instrum Meas. 2022;71:1–11. doi:10.1109/TIM.2022.3186700. [Google Scholar] [CrossRef]
101. Mazzoleni M, Sarda K, Acernese A, Russo L, Manfredi L, Glielmo L, et al. A fuzzy logic-based approach for fault diagnosis and condition monitoring of Industry 4.0 manufacturing processes. Eng Appl Artif Intell. 2022;115(5):105317. doi:10.1016/j.engappai.2022.105317. [Google Scholar] [CrossRef]
102. Xu X, Cao D, Zhou Y, Gao J. Application of neural network algorithm in fault diagnosis of mechanical intelligence. Mech Syst Signal Process. 2020;141(6):106625. doi:10.1016/j.ymssp.2020.106625. [Google Scholar] [CrossRef]
103. Sharma A, Bhardwaj S, Kankar PK. Fault diagnosis of rolling element bearings using fractional linear prediction and AI techniques. Life Cycle Reliab Saf Eng. 2019;8(1):11–9. doi:10.1007/s41872-018-0062-8. [Google Scholar] [CrossRef]
104. Zhou Z, Liu Q, Ai Q, Xu C. Intelligent monitoring and diagnosis for modern mechanical equipment based on the integration of embedded technology and FBGS technology. Measurement. 2011;44(9):1499–511. doi:10.1016/j.measurement.2011.05.018. [Google Scholar] [CrossRef]
105. Mao W, Łuczak D. Machine fault diagnosis through vibration analysis: time series conversion to grayscale and RGB images for recognition via convolutional neural networks. Energies. 2024;17(9):1998. doi:10.3390/EN17091998. [Google Scholar] [CrossRef]
106. Chen Z, Gryllias K, Li W. Mechanical fault diagnosis using convolutional neural networks and extreme learning machine. Mech Syst Signal Process. 2019;133:106272. doi:10.1016/j.ymssp.2019.106272. [Google Scholar] [CrossRef]
107. Wu C, Jiang P, Ding C, Feng F, Chen T. Intelligent fault diagnosis of rotating machinery based on one-dimensional convolutional neural network. Comput Ind. 2019;108(1):53–61. doi:10.1016/j.compind.2018.12.001. [Google Scholar] [CrossRef]
108. Zhang W, Zhang T, Cui G, Pan Y. Intelligent machine fault diagnosis using convolutional neural networks and transfer learning. IEEE Access. 2022;10:50959–73. [Google Scholar]
109. Li Y, Du X, Wan F, Wang X, Yu H. Rotating machinery fault diagnosis based on convolutional neural network and infrared thermal imaging. Chin J Aeronaut. 2020;33(2):427–38. doi:10.1016/j.cja.2019.08.014. [Google Scholar] [CrossRef]
110. Wang Y, Cheng L. A combination of residual and long-short-term memory networks for bearing fault diagnosis based on time-series model analysis. Meas Sci Technol. 2020;32(1):015904. doi:10.1088/1361-6501/abaa1e. [Google Scholar] [CrossRef]
111. Lei J, Liu C, Jiang D. Fault diagnosis of wind turbine based on long short-term memory networks. Renew Energy. 2019;133(6):422–32. doi:10.1016/j.renene.2018.10.031. [Google Scholar] [CrossRef]
112. Hao S, Ge F-X, Li Y, Jiang J. Multisensor bearing fault diagnosis based on one-dimensional convolutional long short-term memory networks. Measurement. 2020;159(5786):107802. doi:10.1016/j.measurement.2020.107802. [Google Scholar] [CrossRef]
113. Khalid Fahmi A-TW, Reza Kashyzadeh K, Ghorbani S. Fault detection in the gas turbine of the Kirkuk power plant: an anomaly detection approach using DLSTM-Autoencoder. Eng Fail Anal. 2024;160(3):108213. doi:10.1016/j.engfailanal.2024.108213. [Google Scholar] [CrossRef]
114. Chen H, Wang X-B, Yang Z-X, Li J. Privacy-preserving intelligent fault diagnostics for wind turbine clusters using federated stacked capsule autoencoder. Expert Syst Appl. 2024;254(7):124256. doi:10.1016/j.eswa.2024.124256. [Google Scholar] [CrossRef]
115. Yue B, Wang K, Zhu H, Yuan X, Yang C. Spiking autoencoder for nonlinear industrial process fault detection. Inf Sci. 2024;665(1):120389. doi:10.1016/j.ins.2024.120389. [Google Scholar] [CrossRef]
116. Chen Z, Liu S, Li C, Chang Y, Chen J, Feng G, et al. Enhancing equipment safeguarding in IIoT: a self-supervised fault diagnosis paradigm based on asymmetric graph autoencoder. Knowl-Based Syst. 2024;296(15):111922. doi:10.1016/j.knosys.2024.111922. [Google Scholar] [CrossRef]
117. Wang L, Li Y, Liu J, Peng J, Zhang Q, Fu W. Research on fault diagnosis of industrial robots based on generative adversarial network. Phys Commun. 2024;64:102355. doi:10.1016/j.phycom.2024.102355. [Google Scholar] [CrossRef]
118. Wang Y, Bernat S, Vinogradov A. BC-GAN: a threshold-free framework for unsupervised early fault detection in rotating machinery. Expert Syst Appl. 2024;258(6):124832. doi:10.1016/j.eswa.2024.124832. [Google Scholar] [CrossRef]
119. Li Q, Tang Y, Chu L. Generative adversarial networks for prognostic and health management of industrial systems: a review. Expert Syst Appl. 2024;253(2):124341. doi:10.1016/j.eswa.2024.124341. [Google Scholar] [CrossRef]
120. Liao W, Yang K, Fu W, Tan C, Chen B, Shan Y. A review: the application of generative adversarial network for mechanical fault diagnosis. Meas Sci Technol. 2024;35(6):062002. doi:10.1088/1361-6501/ad356d. [Google Scholar] [CrossRef]
121. Shao S, Wang P, Yan R. Generative adversarial networks for data augmentation in machine fault diagnosis. Comput Ind. 2019;106(3):85–93. doi:10.1016/J.COMPIND.2019.01.001. [Google Scholar] [CrossRef]
122. Zhang W, Li X, Jia X-D, Ma H, Luo Z, Li X. Machinery fault diagnosis with imbalanced data using deep generative adversarial networks. Measurement. 2020;152(3):107377. doi:10.1016/j.measurement.2019.107377. [Google Scholar] [CrossRef]
123. Ding L, Li Q. Fault diagnosis of rotating machinery using novel self-attention mechanism TCN with soft thresholding method. Meas Sci Technol. 2024;35(4):047001. doi:10.1088/1361-6501/ad1eb3. [Google Scholar] [CrossRef]
124. Liu H, Xu Q, Han X, Wang B, Yi X. Attention on the key modes: machinery fault diagnosis transformers through variational mode decomposition. Knowl-Based Syst. 2024;289(7):111479. doi:10.1016/j.knosys.2024.111479. [Google Scholar] [CrossRef]
125. Shao X, Kim C-S. Adaptive multi-scale attention convolution neural network for cross-domain fault diagnosis. Expert Syst Appl. 2024;236(2022):121216. doi:10.1016/j.eswa.2023.121216. [Google Scholar] [CrossRef]
126. Han R, Wang J, Wan Y, Bao J, Jiang X, Zhang Z, et al. Attention mechanism guided sparse filtering for mechanical intelligent fault diagnosis under variable speed condition. Meas Sci Technol. 2024;35(4):042001. doi:10.1088/1361-6501/ad197a. [Google Scholar] [CrossRef]
127. Li X, Xiao S, Zhang F, Huang J, Xie Z, Kong X. A fault diagnosis method with AT-ICNN based on a hybrid attention mechanism and improved convolutional layers. Appl Acoust. 2024;225(3):110191. doi:10.1016/j.apacoust.2024.110191. [Google Scholar] [CrossRef]
128. Liu R, Zhang Q, Lin D, Zhang W, Ding SX. Causal intervention graph neural network for fault diagnosis of complex industrial processes. Reliab Eng Syst Saf. 2024;251(9):110328. doi:10.1016/j.ress.2024.110328. [Google Scholar] [CrossRef]
129. Yin M, Li J, Shi Y, Qi C, Li H. Fusing logic rule-based hybrid variable graph neural network approaches to fault diagnosis of industrial processes. Expert Syst Appl. 2024;238(1):121753. doi:10.1016/j.eswa.2023.121753. [Google Scholar] [CrossRef]
130. Wang L, Xie F, Zhang X, Jiang L, Huang B. Spatial-temporal graph feature learning driven by time-frequency similarity assessment for robust fault diagnosis of rotating machinery. Adv Eng Inform. 2024;62(17):102711. doi:10.1016/j.aei.2024.102711. [Google Scholar] [CrossRef]
131. Zhang X, Liu J, Zhang X, Lu Y. Multiscale channel attention-driven graph dynamic fusion learning method for robust fault diagnosis. IEEE Trans Ind Inform. 2024;(9):1–12. doi:10.1109/TII.2024.3397401. [Google Scholar] [CrossRef]
132. Zhang X, Zhang X, Liu J, Wu B, Hu Y. Graph features dynamic fusion learning driven by multi-head attention for large rotating machinery fault diagnosis with multi-sensor data. Eng Appl Artif Intell. 2023;125(6):106601. doi:10.1016/j.engappai.2023.106601. [Google Scholar] [CrossRef]
133. Polar A, Poluektov M. A deep machine learning algorithm for construction of the Kolmogorov-Arnold representation. Eng Appl Artif Intell. 2021;99(1):104137. doi:10.1016/j.engappai.2020.104137. [Google Scholar] [CrossRef]
134. Wang C, Sun Y, Wang X. Image deep learning in fault diagnosis of mechanical equipment. J Intell Manuf. 2024;35(6):2475–515. doi:10.1007/s10845-023-02176-3. [Google Scholar] [CrossRef]
135. Li Z, Wang Y, Wang K. A deep learning driven method for fault classification and degradation assessment in mechanical equipment. Comput Ind. 2019;104:1–10. doi:10.1016/j.compind.2018.07.002. [Google Scholar] [CrossRef]
136. Chen X, Zhang L, Liu T, Kamruzzaman MM. Research on deep learning in the field of mechanical equipment fault diagnosis image quality. J Vis Commun Image Represent. 2019;62(7553):402–9. doi:10.1016/j.jvcir.2019.06.007. [Google Scholar] [CrossRef]
137. Ma S, Chu F. Ensemble deep learning-based fault diagnosis of rotor bearing systems. Comput Ind. 2019;105(4):143–52. doi:10.1016/j.compind.2018.12.012. [Google Scholar] [CrossRef]
138. Wang J, Mo Z, Zhang H, Miao Q. A deep learning method for bearing fault diagnosis based on time-frequency image. IEEE Access. 2019;7:42373–83. doi:10.1109/ACCESS.2019.2907131. [Google Scholar] [CrossRef]
139. Li X, Zhang W, Ding Q, Sun J-Q. Intelligent rotating machinery fault diagnosis based on deep learning using data augmentation. J Intell Manuf. 2020;31(2):433–52. doi:10.1007/s10845-018-1456-1. [Google Scholar] [CrossRef]
140. Tayyab SM, Asghar E, Pennacchi P, Chatterton S. Intelligent fault diagnosis of rotating machine elements using machine learning through optimal features extraction and selection. Procedia Manuf. 2020;51(1):266–73. doi:10.1016/j.promfg.2020.10.038. [Google Scholar] [CrossRef]
141. Han D, Liang K, Shi P. Intelligent fault diagnosis of rotating machinery based on deep learning with feature selection. J Low Freq Noise Vib Act Control. 2020;39(4):939–53. doi:10.1177/1461348419849279. [Google Scholar] [CrossRef]
142. Liu H, Ma R, Li D, Yan L, Ma Z. Machinery fault diagnosis based on deep learning for time series analysis and knowledge graphs. J Signal Process Syst. 2021;93(12):1433–55. doi:10.1007/s11265-021-01718-3. [Google Scholar] [CrossRef]
143. Li C, Zhang S, Qin Y, Estupinan E. A systematic review of deep transfer learning for machinery fault diagnosis. Neurocomputing. 2020;407(2018):121–35. doi:10.1016/j.neucom.2020.04.045. [Google Scholar] [CrossRef]
144. Tang S, Ma J, Yan Z, Zhu Y, Khoo BC. Deep transfer learning strategy in intelligent fault diagnosis of rotating machinery. Eng Appl Artif Intell. 2024;134(5):108678. doi:10.1016/j.engappai.2024.108678. [Google Scholar] [CrossRef]
145. Zhang J, Pei G, Zhu X, Gou X, Deng L, Gao L, et al. Diesel engine fault diagnosis for multiple industrial scenarios based on transfer learning. Measurement. 2024;228:114338. doi:10.1016/j.measurement.2024.114338. [Google Scholar] [CrossRef]
146. Yu X, Wang S, Xu H, Yu K, Feng K, Zhang Y, et al. Intelligent fault diagnosis of rotating machinery under variable working conditions based on deep transfer learning with fusion of local and global time-frequency features. Struct Health Monit. 2024;23(4):2238–54. doi:10.1177/14759217231199427. [Google Scholar] [CrossRef]
147. Feng B, Zhou Q, Xing J, Yang Q, Chen Y, Deng Z. Attention-empowered transfer learning method for HVAC sensor fault diagnosis in dynamic building environments. Build Environ. 2024;250(6):111148. doi:10.1016/j.buildenv.2023.111148. [Google Scholar] [CrossRef]
148. Zheng B, Huang J, Ma X, Zhang X, Zhang Q. An unsupervised transfer learning method based on SOCNN and FBNN and its application on bearing fault diagnosis. Mech Syst Signal Process. 2024;208(7):111047. doi:10.1016/j.ymssp.2023.111047. [Google Scholar] [CrossRef]
149. Li W, Huang R, Li J, Liao Y, Chen Z, He G, et al. A perspective survey on deep transfer learning for fault diagnosis in industrial scenarios: theories, applications and challenges. Mech Syst Signal Process. 2022;167(12):108487. doi:10.1016/j.ymssp.2021.108487. [Google Scholar] [CrossRef]
150. Yang D, Zhang W, Jiang Y. Mechanical fault diagnosis based on deep transfer learning: a review. Meas Sci Technol. 2023;34(11):112001. doi:10.1088/1361-6501/ace7e6. [Google Scholar] [CrossRef]
151. Li ZN, Li ZD, Gu FS. Intelligent diagnosis method for machine faults based on federated transfer learning. Appl Soft Comput. 2024;163(5):111922. doi:10.1016/J.ASOC.2024.111922. [Google Scholar] [CrossRef]
152. Brusa E, Cibrario L, Delprete C, Di Maggio LG. Explainable AI for machine fault diagnosis: understanding features’ contribution in machine learning models for industrial condition monitoring. Appl Sci. 2023;13(4):2038. doi:10.3390/APP13042038. [Google Scholar] [CrossRef]
153. Gawde S, Patil S, Kumar S, Kamat P, Kotecha K. An explainable predictive maintenance strategy for multi-fault diagnosis of rotating machines using multi-sensor data fusion. Decis Anal J. 2024;10(6):100425. doi:10.1016/J.DAJOUR.2024.100425. [Google Scholar] [CrossRef]
154. Brito LC, Susto GA, Brito JN, Duarte MAV. Fault diagnosis using eXplainable AI: a transfer learning-based approach for rotating machinery exploiting augmented synthetic data. Expert Syst Appl. 2023;232(4):120860. doi:10.1016/J.ESWA.2023.120860. [Google Scholar] [CrossRef]
155. Cohen J, Huan X, Ni J. Shapley-based explainable AI for clustering applications in fault diagnosis and prognosis. J Intell Manuf. 2024;18(22):5031. doi:10.1007/s10845-024-02468-2. [Google Scholar] [CrossRef]
156. Kobayashi K, Alam SB. Explainable, interpretable, and trustworthy AI for an intelligent digital twin: a case study on remaining useful life. Eng Appl Artif Intell. 2024;129(3):107620. doi:10.1016/j.engappai.2023.107620. [Google Scholar] [CrossRef]
157. Bhakte A, Pakkiriswamy V, Srinivasan R. An explainable artificial intelligence based approach for interpretation of fault classification results from deep neural networks. Chem Eng Sci. 2022;250(2):117373. doi:10.1016/J.CES.2021.117373. [Google Scholar] [CrossRef]
158. Mey O, Neufeld D. Explainable AI algorithms for vibration data-based fault detection: use case-adadpted methods and critical evaluation. Sensors. 2022;22(23):9037. doi:10.3390/S22239037 [Google Scholar] [PubMed] [CrossRef]
Cite This Article
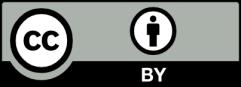
This work is licensed under a Creative Commons Attribution 4.0 International License , which permits unrestricted use, distribution, and reproduction in any medium, provided the original work is properly cited.