Open Access
ARTICLE
Reliability Prediction of Wrought Carbon Steel Castings under Fatigue Loading Using Coupled Mold Optimization and Finite Element Simulation
1 Mechanical Engineering Department, Prince Mohammad Bin Fahd University, Alkhobar, 34754, Saudi Arabia
2 Mechanical Engineering Department, King Fahd University of Petroleum and Minerals, Dhahran, 31261, Saudi Arabia
3 Interdisciplinary Research Center for Intelligent Manufacturing and Robotics, King Fahd University of Petroleum and Minerals, Dhahran, 31261, Saudi Arabia
4 Interdisciplinary Research Center for Advanced Materials, King Fahd University of Petroleum and Minerals, Dhahran, 31261, Saudi Arabia
5 Interdisciplinary Research Center for Industrial Nuclear Energy, King Fahd University of Petroleum & Minerals, Dhahran, 31261, Saudi Arabia
* Corresponding Author: Syed Sohail Akhtar. Email:
(This article belongs to the Special Issue: Recent Advances in Computational Methods for Performance Assessment of Engineering Structures and Materials against Dynamic Loadings)
Computer Modeling in Engineering & Sciences 2024, 141(3), 2325-2350. https://doi.org/10.32604/cmes.2024.054741
Received 06 June 2024; Accepted 20 September 2024; Issue published 31 October 2024
Abstract
The fatigue life and reliability of wrought carbon steel castings produced with an optimized mold design are predicted using a finite element method integrated with reliability calculations. The optimization of the mold is carried out using MAGMASoft mainly based on porosity reduction as a response. After validating the initial mold design with experimental data, a spring flap, a common component of an automotive suspension system is designed and optimized followed by fatigue life prediction based on simulation using Fe-safe. By taking into consideration the variation in both stress and strength, the stress-strength model is used to predict the reliability of the component under fatigue loading. Under typical loading conditions of 70 kN, the analysis showed that 95% of the steel spring flaps achieve infinite life. However, under maximum loading conditions of 90 kN, reliability declined significantly, with only 65% of the spring flaps expected to withstand the stress without failure. The study also identified a safe load-induced stress of 95 MPa on the spring flap. The findings suggest that transitioning from forged to cast spring flaps is a promising option, particularly if further improvements in casting design reduce porosity to negligible levels, potentially achieving 100% reliability under typical loading conditions. This integrated approach of mold optimization coupled with reliability estimation under realistic service loading conditions offers significant potential for the casting industry to produce robust, cost-effective products.Keywords
Cite This Article
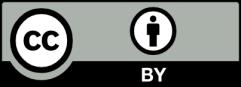
This work is licensed under a Creative Commons Attribution 4.0 International License , which permits unrestricted use, distribution, and reproduction in any medium, provided the original work is properly cited.