Open Access
REVIEW
Artificial Intelligence-Driven Vehicle Fault Diagnosis to Revolutionize Automotive Maintenance: A Review
1 Faculty of Mechanical and Automotive Engineering Technology, Universiti Malaysia Pahang Al-Sultan Abdullah, Pekan, 26600, Malaysia
2 Automotive Engineering Center, Universiti Malaysia Pahang Al-Sultan Abdullah, Pekan, 26600, Malaysia
* Corresponding Author: Md Mustafizur Rahman. Email:
Computer Modeling in Engineering & Sciences 2024, 141(2), 951-996. https://doi.org/10.32604/cmes.2024.056022
Received 12 July 2024; Accepted 23 August 2024; Issue published 27 September 2024
Abstract
Conventional fault diagnosis systems have constrained the automotive industry to damage vehicle maintenance and component longevity critically. Hence, there is a growing demand for advanced fault diagnosis technologies to mitigate the impact of these limitations on unplanned vehicular downtime caused by unanticipated vehicle breakdowns. Due to vehicles’ increasingly complex and autonomous nature, there is a growing urgency to investigate novel diagnosis methodologies for improving safety, reliability, and maintainability. While Artificial Intelligence (AI) has provided a great opportunity in this area, a systematic review of the feasibility and application of AI for Vehicle Fault Diagnosis (VFD) systems is unavailable. Therefore, this review brings new insights into the potential of AI in VFD methodologies and offers a broad analysis using multiple techniques. We focus on reviewing relevant literature in the field of machine learning as well as deep learning algorithms for fault diagnosis in engines, lifting systems (suspensions and tires), gearboxes, and brakes, among other vehicular subsystems. We then delve into some examples of the use of AI in fault diagnosis and maintenance for electric vehicles and autonomous cars. The review elucidates the transformation of VFD systems that consequently increase accuracy, economization, and prediction in most vehicular sub-systems due to AI applications. Indeed, the limited performance of systems based on only one of these AI techniques is likely to be addressed by combinations: The integration shows that a single technique or method fails its expectations, which can lead to more reliable and versatile diagnostic support. By synthesizing current information and distinguishing forthcoming patterns, this work aims to accelerate advancement in smart automotive innovations, conforming with the requests of Industry 4.0 and adding to the progression of more secure, more dependable vehicles. The findings underscored the necessity for cross-disciplinary cooperation and examined the total potential of AI in vehicle default analysis.Graphic Abstract
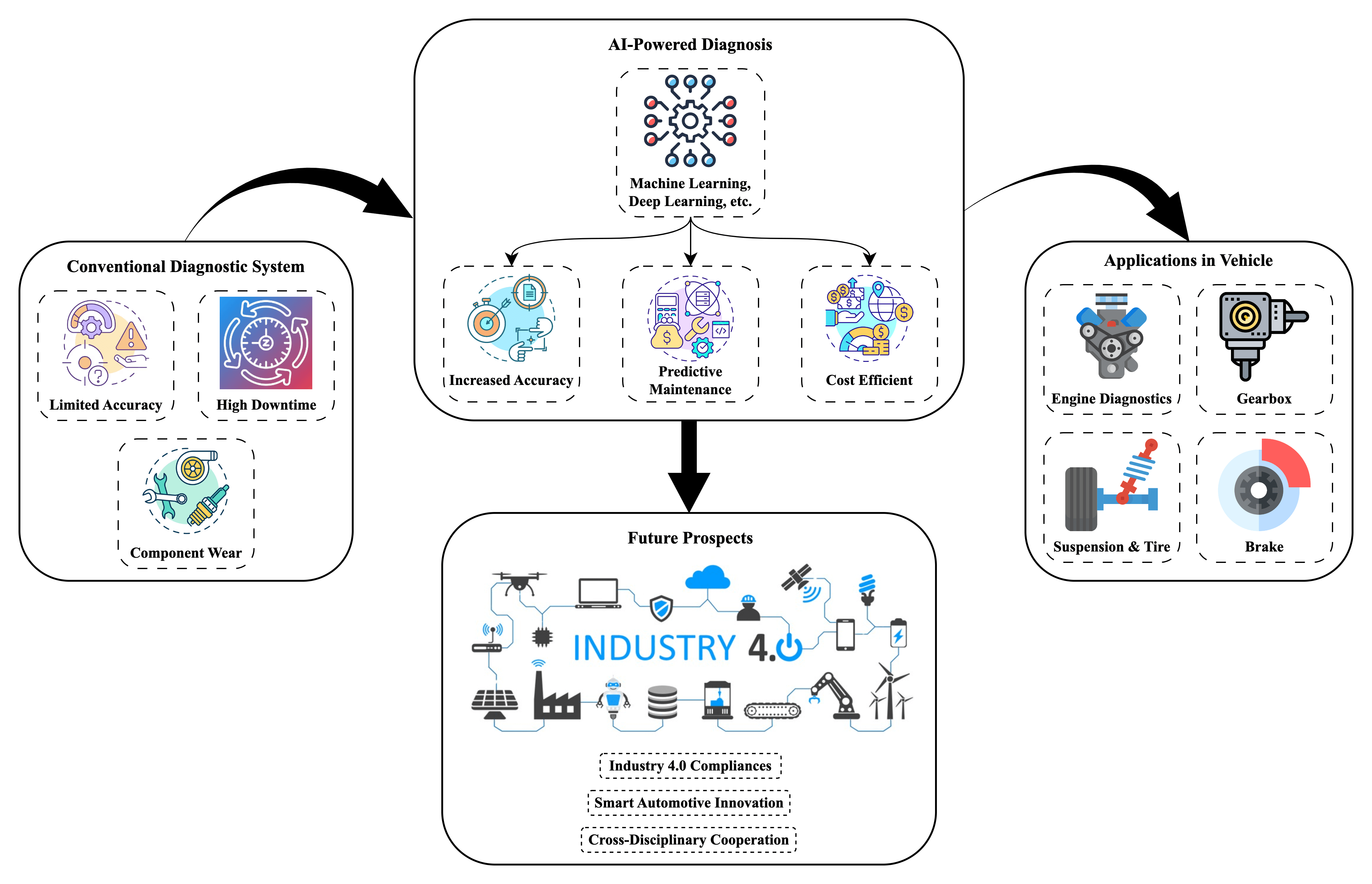
Keywords
Artificial intelligence (AI) has become ubiquitous in contemporary daily existence. The most prevalent instances include smartphones, Google’s search engine, promotional activities, and social media platforms [1]. The networks interpret such observations and provide recommendations relevant to their interests. To enhance efficiency and intelligence, numerous industries, including Tesla, are investing in novel AI technologies [2]. AI is commonly defined as the capacity of a system to comprehend external information accurately, appropriately interpret external data, and utilize this knowledge to achieve specific objectives and tasks through a flexible adaptation [3,4]. AI techniques are used in fields like predictive maintenance (PdM), predictive quality, safety analytics, and warranty analytics [5]. Several terminologies have been used to explain the evolution of AI capabilities in ensuring that components, products, and systems are healthy: E-maintenance [6], prognostics and health management [7], Maintenance 4.0 [8], or smart maintenance [9]. Significant changes are sweeping through the worldwide automotive industry, which can largely be attributed to developments in AI applied to vehicle maintenance. Vehicle fault diagnosis (VFD), also known as vehicle diagnostics, is an essential yet challenging part of automotive maintenance that involves capturing and analyzing signals from different vehicle systems to find causes or failures [10]. Sensors and software monitor vehicle state, detect performance deviations in need of attention, predict or identify problems associated with those disturbances earlier than would be possible otherwise, and give recommendations on what service measures are needed to decisively allow for capturing costs through problem identification/resolution [11]. The system creates valuable insights from the data generated on these vehicles to help us predict and prevent failures. This technology can predict the remaining useful life (RUL) and detect failures or degradation in performance at an early stage [12]. As modern vehicles get increasingly complex, this leads to issues with existing rule-based systems and onboard diagnostics (OBD) being accurate while being cost-efficient and timely [13,14]. Therefore, new solutions must be found at the key ignition. Rule-based systems, despite being simple to implement and easy to read/interpret, are generally weak in practice (especially when handling complicated use cases or a large rule base). These shortcomings reveal themselves when dealing with the need to explain complex custom conditions or accommodate hundreds of regulations, and as such, they can underperform in these circumstances. On the other hand, how OBD systems operate is primarily based on diagnostic trouble codes, making them reactive and allowing them to recognize a problem only after it has happened [15]. Additionally, they provide limited data service, increasing technicians’ workload to find the root cause of the problem [16]. By addressing these challenges, we can lower maintenance costs, improve vehicle performance and longevity, increase vehicle safety/reliability, and reduce environmental impact by optimizing the preventive maintenance schedule.
Advances in artificial intelligence have paved the way for the emergence of automotive maintenance specialists. Various AI approaches, including machine learning (ML) and deep learning (DL), present promising solutions to enhance diagnostic accuracy, enable predictive maintenance, and adapt to evolving vehicle complexities [17,18]. Gong et al. [19] presented a comprehensive review of various ML algorithms to predict and warn about failures in in-vehicle systems such as the transmission, engine, and tires. The study identifies the main limitation in evaluating the effectiveness of developed methods using real-world datasets, as it is often only partially labeled and requires significant efforts to annotate. It suggests that future research could explore using meta-learning and combining different AI models to optimize existing technologies. Moreover, Jain et al. [20] provided a literature review that focused on ML techniques as a viable solution for predictive maintenance and diagnosis of vehicle health in the automotive industry despite limited sensor access and data availability challenges. Furthermore, Rasheed et al. [21] summarized ML approaches for in-vehicle failure prognosis in automobiles, focusing on methodologies, theories, and applications in data measurement and analysis systems for vehicle on-board health monitoring systems. The review concludes that OBD systems may not adequately distinguish between minor and major vehicle failures, and there is a need for improved methods and techniques to better track and identify the failures. The latest DL algorithms and other AI methods are continuously being developed by the researchers to overcome the inherent ML limitations in the VFD context. Recent research has focused on applying deep learning techniques for fault diagnosis in various components of electric vehicles [22,23]. Machlev et al. reviewed the potential of using DL techniques for EV battery fault detection, diagnostics, and prognostics, but their potential is not yet covered. However, the above-mentioned reviews only emphasize the ML or DL application for fault diagnosis of specific vehicle systems or components. Hence, there is a pressing need to integrate and synthesize diverse AI techniques to create comprehensive and robust diagnostic frameworks for entire vehicular systems. This comprehensive review highlights the significant influences of numerous ML and DL algorithms over the model and signal-oriented approaches, which have been utilized for the fault analysis of engine, suspension, tire, gearbox, and brake. Furthermore, the review aims to analyze the current state of AI applications in VFD and predictive maintenance of electric and autonomous cars, evaluating various AI techniques’ efficacy, identifying implementation barriers, and assessing the economic, ethical, and workforce impacts. By providing a nuanced understanding of AI’s role in revolutionizing vehicle maintenance, this article seeks to offer valuable insights for researchers, industry professionals, and policymakers, paving the way for future advancements in automotive diagnostics and maintenance strategies. However, the remaining portions of this literature are organized as presented in Fig. 1. Section 2 provides a comprehensive overview of AI-based vehicle fault diagnosis about various subsystems of vehicles. Section 3 of the article delineates the prevalent AI methodologies and their contemporary implementations in VFD. Additionally, Section 4 illustrates the maintenance methodologies implemented in the automotive industry and the latest AI applications of automotive predictive maintenance. Furthermore, Section 5 examines the potential avenues for future research in this field. Finally, Section 6 culminates this review by demonstrating key findings and insights.
Figure 1: Taxonomical framework of the review
Over the years, various fault analysis and interpretation techniques have been used for vehicle fault analysis, such as model-based, signal-based, and knowledge-based, presented in Fig. 2. The model-based approach involves using mathematical equations to establish a relationship between the input and output of a system. The fundamental concept consists of calculating a residual by contrasting the model’s outputs with the actual real-time outputs of the system. When a component changes, the computed residual is also expected to change. This is because the real-time system tends to deviate from the constructed model as the system degrades over time [24]. In contrast, signal-based techniques rely solely on the observed output signals for fault detection. Subsequently, diverse techniques for extracting features are employed to analyze the signals [25]. Finally, the knowledge-based methods exhibit similarities to those signal-based [26]. Both approaches employ feature extraction to gather data on the system’s condition. The primary difference between these two methods is how the comparative database is formulated. Signal-based techniques involve the construction of a pattern or correlation between features and system state using a dataset subject to human intervention. This process is informed by understanding the components’ state concerning the output variables, and the resulting pattern is typically obtained relatively straightforwardly. Prior knowledge of signal patterns is necessary, even without any generated examples. This implies that establishing a correlation between the extracted feature and the faulty condition is accomplished through a comprehensive understanding of the system and the association of signal values with the condition in question [27]. In contrast, knowledge-based approaches independently establish the connection between features and conditions. Hence, the classifier acquires knowledge by analyzing many instances and autonomously identifying the essential patterns required for fault categorization. As Dai et al. have explained, this approach necessitates a larger corpus of data as it employs the data for learning. However, signal-based and model-based techniques require a smaller dataset for validity checks [28]. The amount of data produced by automobiles and their mechanical systems’ complexity has recently increased significantly. Therefore, AI-driven knowledge-based data analysis systems are superior to those powered by model-based and signal-based traditional techniques [29].
Figure 2: Methods for VFD
2.2 Artificial Intelligence-Driven VFD
Artificial intelligence involves using machine learning and deep learning techniques to analyze real-time data collected from various sensors installed in the vehicle [30]. The sensors collect data on multiple parameters of the different vehicle systems, which are subsequently analyzed by AI algorithms to detect any faults, anomalies, or deviations from expected performance levels [31]. Traditional ML and DL have been extensively used for fault detection and diagnosis in electric vehicle (EV) motors, with a focus on feature extraction and fault classification [32,33]. These methods have demonstrated significant potential in advancing predictive maintenance strategies by automating feature engineering and enhancing fault diagnosis accuracy. However, the AI techniques employed vary significantly, demonstrating their robust hybrid nature in Fig. 3. The diagnosis of in-wheel motor fault employs a novel artificial hydrocarbon network that does not fall into the traditional scope of either ML or DL [34]. The diversity in AI applications further shows the combination of AI with signal processing and clustering algorithms for sensorless fault diagnosis in EV propulsion systems [35]. However, concerns emerge around the effectiveness and implementability of these methods for different vehicle components under varying operational conditions. Some studies have shown the strength of AI methods in operating under variable conditions and in response to external disturbances [34]. In contrast, others pointed out their limitations when dealing with multiple concurrent faults, highlighting gaps towards more detailed datasets for testing those capabilities [33,36]. The adoption of edge-AI with real-time fault detection in industrial autonomous transfer vehicles shows both the practical necessity and technical ability to provide sub-second time delay and data transmission efficiency. These factors may be of lesser significance in alternative AI-based fault diagnosis systems [37], highlighting the context-specific requirements of fault diagnosis implementations. In summary, while AI-driven vehicle fault diagnosis and maintenance systems share the common goals of improving reliability and reducing downtime, the diversity in AI techniques and their specific applications reveals complementary strengths and areas requiring further research and development. This variability underscores the need for continued exploration and refinement of AI approaches in automotive maintenance.
Figure 3: AI algorithms for vehicle subsystems’ fault diagnosis
2.2.1 Troubleshooting of Vehicle Sensors
Diagnosing and fixing sensor issues in modern vehicles is crucial for maintaining their safety and reliability. Numerous studies have investigated diverse techniques and instruments for identifying and resolving vehicle sensor problems. A key issue in vehicle sensor maintenance is identifying and correcting faulty signals utilizing the processes shown in Fig. 4. Research by Byun et al. [38] introduced a system for diagnosing faults and restoring signals in vehicle motion sensors to address safety issues caused by sensor defects. Their method converts wheel speed data into information about the vehicle’s central axis, which is then used to calculate estimated speeds for all wheels for maintaining valid path tracking performance. By comparing these estimates to actual measurements, the system can detect faults and reconstruct faulty signals. Off-line testing has shown this approach effectively maintains vehicle control during sensor malfunctions. The analysis assumes only one sensor can fail at a given instant, which limits diagnostic methods for multiple sensors.
Figure 4: Flowchart of sensor troubleshooting
Therefore, researchers proposed a sensitivity-based fault detection and isolation algorithm to diagnose various sensor faults in commercial vehicle chassis sensors, and it was verified using hardware-in-the-loop simulation [39]. Though uncertainties were present in the model, especially during vehicle acceleration, but did not substantially affect the assessment of failures. For electric vehicles, a study by Xiong et al. [40] introduced a model-based approach that aims to detect and isolate issues in the current and voltage sensors of lithium-ion battery packs. It compares the actual state of charge (SoC) with an estimated SoC to identify faults. The method’s effectiveness is confirmed through both experimental and simulated tests. However, it might require extensive calibration and validation for different battery configurations. Beyond individual vehicle sensors, diagnosing issues in distributed sensor networks is also crucial. A study presents SNTS (Sensor Network Troubleshooting Suite), an automated tool for identifying failures in sensor networks. SNTS employs data mining methods to link network conditions with failure states, helping to uncover the underlying causes of malfunctions [41]. This tool has proven effective in troubleshooting a tracking system, showing its potential to offer valuable information for enhancing overall system performance. However, the tool’s effectiveness may depend on the quality and quantity of data collected. To overcome the limitations of the above-established methods, Khalid et al. [42] presented an autonomous data-driven surveillance and rectification system using in-vehicle sensors for intelligent transportation systems that can monitor, report, and autonomously recover vehicle sensors using AI-based techniques. Subsequently, proper sensor calibration is essential for any self-driving system and its component sensors. This crucial step must be completed accurately before implementing sensor fusion and obstacle detection processes [43].
A vehicle engine is a complex system of components that generate the power needed to propel the vehicle forward. The engine plays an essential role in the power generation of the vehicle. The assurance of combustion stability is cosntingent upon fulfilling necessary conditions that facilitate complete combustion during each cycle, thereby preventing any misfire or partial burn.
So, identifying engine misfire limits is crucial in enhancing the stability of combustion. Also, detecting misfires is vital for the engines in achieving the desired engine output torque while ensuring the protection of the engine after-treatment system [60]. Therefore, proper monitoring and optimal control of vehicular engines are critical to improving their performance and efficiency. Table 1 illustrates a significant evolution in AI-driven vehicle fault diagnosis, showcasing various techniques applied to different engine-related issues. There’s a clear trend towards more sophisticated and hybrid models, combining methods like RF, CNN, and LSTM. Applications range from emission monitoring and misfire detection to comprehensive engine health assessments, indicating a broadening scope of AI in automotive diagnostics. The shift from single-method approaches to multi-method strategies suggests an increasing recognition of the complexity of engine diagnostics and the need for more nuanced, multi-faceted analysis. However, the diversity of methods and specific applications also highlights a potential lack of standardization in the field, which could pose challenges for widespread implementation. AI offers several critical advantages in engine fault diagnosis, including high accuracy, real-time diagnostics, and resource optimization, while also acknowledging limitations such as complexity, data dependency, and integration challenges. Future directions focus on enhancing model robustness, developing efficient hybrid models, and improving integration with the Internet of Things (IoT) infrastructure.
Vehicle suspension refers to the system of springs or shock absorbers and other components that connect the vehicle body or chassis to the wheels. The primary purpose of a suspension system is to provide a smooth ride for the vehicle’s occupants while maintaining traction and control of the wheels on the road surface [61].
The most common suspension systems found in vehicles are independent and dependent suspensions. Independent suspension allows each wheel to move independently of the other wheels. It provides better handling, comfort, and traction, especially on rough roads. Examples include double wishbone and multi-link suspensions [73]. On the contrary, dependent suspension connects both wheels on the same axle to a single beam or solid axle. It provides better durability and towing capability but may result in a rougher ride and less handling performance. Leaf spring and torsion beam suspensions are dependent suspensions [74]. Traditional methods of diagnosing suspension faults often rely on specialized setups and vibration analysis, which can be time-consuming and less accurate. Recent advancements have introduced AI approaches for diagnosing faults and remaining life prediction of vehicle suspension, as shown in Table 2. Random forest classifiers have demonstrated high accuracy (up to 95.88%) in identifying suspension issues across various load conditions [62]. Moreover, advanced DL techniques, such as vision transformers, have achieved even higher accuracy (99.39%) by analyzing vibration spectrograms [75]. Transfer learning approaches, like VGG16 models examining radar plots of vibration data, have also proven effective (96.70% accuracy) [76]. However, the complexities include developing explainable AI models to enhance user trust and using AI to compensate for the lack of real fault examples. These challenges can be minimized by exploring the potential of hybrid models that combine multiple AI techniques for even more robust fault diagnosis systems.
A vehicle tire is a complex and essential component of automobiles that provides contact between the vehicle and the road surface. Tires are designed to provide maximum grip, stability, and durability while absorbing road surface impacts. The main components of a vehicle tire are tread, sidewall, beads, casing, etc. [77]. In addition to these components, modern tires may also include various technologies and features, such as run-flat technology, self-sealing materials, and low-rolling-resistance designs [78]. According to whether or not they require air to keep their shape, tires are either pneumatic or non-pneumatic. Non-pneumatic tires rely on a thick polymer to keep their shape instead of using air. When working in hazardous environments, such as demolition sites, pneumatic tires are not an option. Conversely, the compressed gas inside the pneumatic tires works as a spring and dampens much of the vibration, making these tires a popular choice for automobiles [79]. It is important to remember that various kinds of tire construction, including diagonal, radial, and bias belts, accommodate the wide range of available stability, comfort, and fuel efficiency ratings [80].
Proper maintenance of vehicle tires is essential for ensuring safe and efficient vehicle operation. Regular inspections and monitoring of tire pressure, tread wear, and overall condition can help prevent accidents, extend tire lifespan, and improve fuel efficiency. Two tire monitoring systems exist: direct tire pressure monitoring system (TPMS) and indirect TPMS. A direct TPMS uses sensors mounted inside the tire to monitor tire pressure and temperature. These sensors transmit data to a central control unit that alerts the driver when necessary (when tire pressure and temperature go outside user-defined limits). Indirect TPMS uses wheel speed sensors to estimate tire pressure, while direct TPMS is more precise [90]. The application of different AI methods for tire defect inspection, wear particle detection, and pressure loss verification are shown in Table 3. The AI techniques have been applied to various data streams, ranging from vibration signals and wheel speed measurements through camera pictures and laser sensor readings. This trend is a move toward more advanced ways of monitoring tire safety and performance in vehicles. Further, a combination of ML algorithms also aids in the design of more intelligent tire systems. Such systems are suitable for real-time data processing and accurate tire force prediction in various driving conditions [91]. The improvement is essential for a more complete and timely tire monitoring system.
A vehicle gearbox, also known as a transmission, is an essential component of a vehicle’s drivetrain that transfers power from the engine to the wheels. The gearbox allows the engine to operate within an optimal range of speeds while providing various gear ratios to match the vehicle’s speed and driving conditions [92]. Different types of vehicle gearboxes include manual, automatic, continuously variable, and dual-clutch transmissions. Each type of gearbox has its advantages and disadvantages in terms of performance, fuel efficiency, and ease of use [93]. Transmission errors or sudden failures within the gearbox have been observed to increase the noise and vibration levels of the entire system [94]. Moreover, to handle the highly imbalanced datasets, Dong et al. [95] developed a dynamic normalization supervised contrastive network with a multiscale compound attention mechanism to effectively diagnose gearbox faults. The method demonstrated superior performance in achieving high accuracies of over 90% but limited the diagnostic performance for a larger number of fault samples. Hence, the examination and establishment of condition monitoring and fault diagnosis techniques for gearboxes have been investigated and progressed during the past few decades. Table 4 presents various AI techniques, such as CNN, fuzzy logic, DT, RF, SVM, hybrid intelligence systems, etc., that can be employed for automated fault detection in the gearbox. However, CNNs are widely utilized in this case [96]. One contributing factor is their aptitude for acquiring knowledge and assimilating new concepts. The flexibility of CNNs allows for the potential identification of novel conditions or faults through the analysis of pre-existing data. Furthermore, CNNs exhibit high efficacy in modeling intricate nonlinear phenomena manifesting in various rotating machinery faults [97]. AI uses vibration data under variable speeds to predict gearbox failure. The creation of AI models that provide probability-based confidence levels has allowed for identifying both familiar and unfamiliar types of faults, enhancing the ability of AI diagnostic systems to learn and adapt on their own [98].
The vehicle brake is a crucial component of a vehicle’s safety system that slows down or stops the vehicle’s movement by converting kinetic energy into heat energy. Brakes use friction to slow down or stop the vehicle’s motion by applying force to the wheels or axle [116]. Different types of vehicle brakes include disc brakes, drum brakes, and anti-lock brakes [117]. A brake system must be efficient, reliable, and effective to ensure safety. Inadequate monitoring may result in significant adverse consequences, such as accidents, frequent equipment failures, and other catastrophic events. Therefore, it is critical to maintain constant monitoring of the brake system. The findings from Table 5 demonstrated the significance of AI methods that could efficiently enhance VFD, allowing for feedback to the driver on the operational status of the brake system, the detection and localization of faults, and the reduction of wasteful expenditures of time, money, and other resources. A correlation exists between the brake constituents’ state and the vibration indications. In the event of the failure advancing, there will be a corresponding increase in the magnitude of vibration. The fault diagnosis process heavily relies on analyzing vibration signals across different fault conditions [118]. In numerous fault diagnosis studies conducted in recent decades, AI-based wavelets have garnered significant attention due to their ability to decompose complex information into simpler forms with high precision, facilitating further analysis.
Recently, numerous AI techniques have been used for vehicle anomaly detection systems. Among those, the most used methods are depicted in Fig. 5.
Figure 5: AI techniques for VFD
In machine learning, data input initiates a pattern recognition process whereby the system identifies concealed patterns and subsequently generates predictions for future data. It can be categorized into three distinct types: supervised, unsupervised, and reinforcement learning [127]. Supervised learning refers to the process of utilizing labeled data for learning purposes. A model is generated via a training procedure subsequently employed in making predictions. If predictions prove to be inaccurate, corrective measures are implemented. The training process continues until the model achieves the required level of precision on the training data. On the contrary, extracting summaries from datasets that lack labeled responses using ML algorithms is unsupervised learning [128]. In the case of reinforcement learning, the principles are rooted in the concept of feedback-based learning. The learning process receives specific inputs and produces an output as its final result. If the result is found to be correct, it is considered acceptable. However, feedback is incorporated into the learning process if the output is inaccurate. The machine is designed to take note of this feedback for future reference [129].
Supervised and unsupervised algorithms quickly process vast amounts of data, enabling early and precise fault identification and classification in-vehicle power transmission systems–key for predictive maintenance and averting significant incidents. These methods can also adjust to various operating conditions and minimize manual data processing, boosting efficiency [130]. However, supervised models often need extensive labeled data for training, which can be costly and time-consuming to gather [131]. Also, the complexity of real-time data processing and the variability of operational conditions are significant challenges in implementing ML for vehicle fault diagnosis. Although promising for developing maintenance strategies, reinforcement learning is less commonly used due to its complexity and resource demands. In summary, specialized techniques are potentially required to perform consistently across different settings to adjust to changing work environments. Some commonly employed ML algorithms for VFD are described as follows.
Decision trees (DTs) are supervised learning algorithms employed for classification and regression, utilizing a hierarchical structure that resembles a tree composed of nodes and branches. Internal nodes represent decision points based on specific feature values. In contrast, leaf nodes at the ends of branches indicate the final output-either a class label for classification tasks or a continuous value for regression problems (Fig. 6). The DT algorithm operates by iteratively splitting the dataset into increasingly specific subsets, guided by the values of input features. For each node in the tree, the algorithm chooses the most informative feature that offers the most significant information gain or optimal division to categorize the input data into distinct classes or values effectively. Information gain is determined by calculating the entropy difference between the initial dataset and the resulting subsets after division. In this context, entropy represents the measure of randomness or unpredictability in the datasets, which has a reverse relationship with the information gain. The algorithm continues constructing the tree until it meets a predetermined stopping condition. This could be reaching a specified maximum tree depth or having a certain minimum number of data points in each leaf node. Once constructed, the DT can predict outcomes for new data by following a path from the top (root node) to the bottom (leaf node) [132,133]. DTs are frequently employed in VFD due to their user-friendly nature, easily interpretable results, and versatility in handling both categorical and continuous data. However, they are susceptible to overfitting, mainly when dealing with noisy data, and their performance can fluctuate significantly based on how the splitting criteria are selected. This can be mitigated using techniques such as pruning or ensembling, while criteria such as information gain or gain ratio help choose attributes. DT models were implemented in real-world cases by Kang et al. [134], who developed the software to predict vehicle faults. This implementation proves the algorithm’s ability to predict and interpret future failures, thus reinforcing preventive maintenance with precision and efficiency. In addition, DTs have proven to be effective in detecting faults within vehicle suspension systems. Such models have accurately detected and classified faults under various vehicular weight loads [62]. This application underscores the versatility of DT algorithms in addressing complex automotive diagnostic challenges. The utilization of DTs in these contexts exemplifies the potential of ML techniques to augment traditional fault detection and prediction methodologies in the automotive sector. These applications contribute to the broader trend of data-driven decision-making in vehicle maintenance and diagnostics.
Figure 6: Decision tree architecture, adapted from [135]; Reprinted from Decision Analytics Journal, Bansal M, Goyal A, Choudhary A, A comparative analysis of K-nearest neighbor, genetic, support vector machine, decision tree, and long short term memory algorithms in machine learning, 100071, Copyright (2022), with permission from Elsevier
Random Forest (RF) is one of the ensemble learning approaches for classification and regression tasks in supervised machine learning. This ensemble of many decision trees is grown on a bootstrapped sample from the training data with an automatically selected subset of input features [136]. The complex workflow of the algorithm includes bootstrap aggregation (bagging), feature subsamples, decision tree build process, iterative forest building, and predictions chained together. This process greatly improves the accuracy of predictions and reduces overfitting, combining large numbers of varied trees to generate an overall prediction. When new data points are presented, RF aggregates the predictions made by all of its constituent trees (usually using majority voting for classification tasks or mean prediction for regression problems) [137]. The algorithm is naturally parallelizable and capable of handling high-dimensional datasets with complex interactions, ideally suited to the automotive diagnostics and prognostics application where it can effectively handle the multi-faceted nature of vehicle system data in a manner that generates reliably generalizable predictions across varying operational conditions. RF is commonly used in ML practice, such as classification problems within VFDs. This is frequently used as a benchmark algorithm to compare with the other algorithms and often combined with ensemble methods (voting, bagging, boosting, etc.) for better predictive performance. Raveendran et al. [120] mainly directed at detecting brake problems in heavy vehicles by the RF method had a better performance, achieving 92% accuracy. This efficiency has outperformed features of popular ML algorithms such as Naïve Bayes, KNN, SVM, and DT. Additionally, RF can handle high-dimensional inputs (as would be the case with a vehicle fault diagnosis application that contains many variables, such as sensors and different data sources). Some works have shown that one can parallelize optimized RF models using Spark, improving diagnosis time and accuracy [138]. A significant strength of RF is its resilience against noise and overfitting, making it particularly suitable for diagnosing faults in the dynamic and noisy conditions typical of vehicle systems. This resilience is further improved by feature extraction and selection methods, which help identify the most essential characteristics for categorizing faults. Despite its strengths, RF algorithms face several challenges in VFD, such as complexity and computation time, dependence on balanced datasets, etc., which can be tackled by incorporating adaptive and transfer learning techniques to changing conditions and new fault types in vehicle systems.
The support vector machine (SVM) is a robust and adaptable supervised learning method applicable to various tasks, including classification, regression, and outlier identification. SVM functions by identifying the best possible dividing line (hyperplane) to categorize input data into distinct classes or groups (Fig. 7). The input features’ linear function defines the hyperplane; the optimal hyperplane is the one that maximizes the margin, which is the gap between the hyperplane and the nearest data points of each class [139]. In cases where a linear function cannot effectively separate the classes, SVM uses a kernel trick to transform the input features into a higher-dimensional feature space where the classes become more separable. The kernel function transforms the input features into a space of higher dimensions without explicitly calculating the data points’ new coordinates in that expanded space. Popular kernel functions include linear, polynomial, radial basis functions, and sigmoid [140,141]. Researchers use SVM algorithms to implement automatic fault diagnosis, which has become increasingly imperative as automotive applications advance toward greater autonomy. For example, Biddle et al. [142] used SVM algorithms to identify and detect sensor malfunctions in autonomous vehicle control systems. The findings demonstrated detection and identification rates of 94.94% and 97.01%, respectively. Furthermore, SVM is well-suited for intricate fault diagnosis due to its capacity to manage data with many dimensions and its robustness against overfitting. For instance, an SVM optimized through grid search in electric vehicle lithium battery systems has demonstrated high accuracy and efficiency in detecting safety states and fault degrees, providing a basis for future battery management strategies [143]. Nevertheless, the performance of SVM heavily depends on the selection of parameters (e.g., penalty factor and kernel function) and unbalanced datasets. To address this problem, methods such as undersampling and adjusting thresholds with algorithms like Grey Wolf Optimizer are essential, as demonstrated in diagnosing faults in the steering actuators of autonomous vehicles [144].
Figure 7: Illustration of SVM for two features of data, adapted from [135]; Reprinted from Decision Analytics Journal, Bansal M, Goyal A, Choudhary A, A comparative analysis of K-nearest neighbor, genetic, support vector machine, decision tree, and long short term memory algorithms in machine learning, 100071, Copyright (2022), with permission from Elsevier. X1 and X2 denote two features of the data
The K-nearest neighbor (KNN) algorithm is a supervised ML technique for classification and regression problems. As a non-parametric method, KNN generates predictions by evaluating the resemblance between new data points and those already present in the training set. The basic idea behind KNN is to identify the K nearest data points to the latest data point (where K is a hyperparameter that needs to be specified) and then use the labels of these K data points to predict the label of the new data point [145]. Various methods can be employed to gauge the similarity between data points, with popular choices including Euclidean distance, Manhattan distance, and cosine similarity. In classification scenarios, the KNN algorithm categorizes a new data point by assigning it the most frequent class found among its K closest neighbors [146]. For regression problems, KNN forecasts the value for a new data point by computing either the average or the middle value of the target variables belonging to its K closest neighbors [147]. The KNN algorithm is valued for its simplicity and effectiveness in dealing with nonlinear and multi-modal data, which are common in vehicle fault diagnosis. A study by Wang and coworkers [148] emphasizes KNN’s capability to handle the nonlinearity and multimodality often found in process data, making it well-suited for complex vehicle systems. Integrating feature extraction techniques such as ANN in the AKNN (combination of ANN and KNN classifier) method enhances the ability of the KNN algorithm to predict the accuracy of the VFD system. The KNN model with K = 3 achieved an accuracy of 85%, while the ANN model yielded a lower accuracy of 78%. In contrast, the ensemble method produced a significantly higher accuracy of 98.7% [149]. However, some limitations of KNN are sensitivity to outliers and distance metrics dependency. To mitigate these, an improved version of KNN, like the Enhanced KNN (EKNN) introduced in a study by Lu et al. [150], shows better flexibility by incorporating dimension-reduction techniques and case-based reconstruction algorithms. This increased adaptability is vital for handling vehicle faults’ wide range and changing nature.
K-means clustering, a widely used unsupervised learning method, groups data into K separate clusters based on their features’ similarity. The process starts by setting up K initial cluster centers, which can be chosen randomly or through specific techniques for better results. Each data point is assigned to the nearest center, creating K clusters. Subsequently, the centers are recalculated as the average of all points in each cluster. This process of assigning and recalculating repeats until convergence, usually when point assignments stop changing. The goal is to minimize the total squared distance between data points and their cluster centers, ensuring that points in the same cluster are as similar as possible [151–153]. K-means clustering has proven valuable for fault diagnosis across various vehicle types, including large trucks, electric cars, and trains. In heavy truck applications, it has been used to examine fault data from diverse driving conditions, facilitating the integration, categorization, and analysis of vehicle issues [154]. The findings can offer robust empirical evidence to strengthen comprehensive scientific assessment and forecasting of vehicles. The algorithm has helped choose reference cells for battery fault detection for EVs, leading to fewer false alarms and more effective early warning systems [155]. Moreover, Yang et al. [156] proposed an improved K-means clustering algorithm called IDBO-Kmeans that aims to improve the accuracy of anomaly data identification in VFD. It addresses the limitations of traditional K-means clustering, such as sensitivity to initial cluster centroids and tendency to fall into local optima, by introducing three optimization strategies.
Artificial neural networks (ANNs) are a family of ML algorithms that draw loose inspiration from the structures and operations of biological neural networks in the brain. ANNs consist of interconnected nodes (neurons) that process and transmit information, where each node computes a linear transformation on its input [157]. This structure of an artificial neuron processes the input it receives and then decides to pass its output as further input in Fig. 8. It is known as a bias or, more precisely, deciding when to transmit data is controlled by an activation function within the system [158]. During the training of the ANN, weights and bias values of neurons are tuned based on changes between the predicted output & actual one. Usually, the method involves an optimization algorithm to repeatedly correct weights and biases (ever so slightly) to minimize loss function that calculates misprediction between predicted/actual outputs [159].
Figure 8: Illustration of an artificial neuron, adapted from [160]; Reprinted from neural computing and applications, 32(16), Asteris PG, Mokos VG, Concrete compressive strength using artificial neural networks, 11807–11826, Copyright (2020), with permission from Springer Nature
The ANNs have demonstrated high accuracy and reliability in diagnosing many types of vehicle faults. A model by Wang et al. [161] that integrates sound intensity analysis and wavelet packet pre-processing with the ANN has turned out to be effective in recognizing engine wear faults from both stationary as well as non-stationary signals [150]. The method uses wavelet packet analysis to extract useful information from noise signals, which can be detected highly through the ANNs approach. Additionally, an ANN technology was proposed to recognize the failures of a single or multiple sensors in gasoline-powered vehicles [162]. This system allows the engine to keep running even when several sensors fail. Although ANNs might be very good at predicting a result, they are typically described as “black boxes,” making the results difficult to understand and trust. The lack of transparency behind such a black box might deter ANN-driven diagnostic systems in these vital vehicle parts. In addition to that, ANNs find it challenging to adjust to changes in system structures and states. Concerning power systems, the ANN inaccuracy demonstrates limited adaptability since it would need to be reconstructed and retrained for every new system architecture [163]. Operating conditions are also vast in systems designed for automotive applications. Researchers are working on various neural network structures or deep learning algorithms that can cater to more complicated diagnostic situations containing multi-factors in automotive-related scenarios.
Deep learning (DL), a cutting-edge subset of machine learning, employs sophisticated multi-layered artificial neural networks to extract hierarchical feature representations from complex data sets autonomously. These networks can be tailored in architecture to suit specific tasks and data types, progressively learning more abstract and intricate features at each successive layer, mimicking the hierarchical processing observed in biological neural systems. In the domain of VFD, DL algorithms-including CNNs for spatial data analysis, LSTM networks for temporal sequence processing, autoencoders for unsupervised feature learning and anomaly detection, and deep belief networks for handling high-dimensional input spaces have demonstrated remarkable efficacy [164]. The new algorithms provide better results using diverse input modalities such as high-frequency sensor data, multispectral images, and multi-variate time series for more accurate detection of vehicle faults. The decision-making process includes the detection objectives, data properties of the cases in question, and complexities inherent to fault patterns and limitations imposed by computational infrastructure when choosing algorithms for a particular application. The following subpart describes a few DL algorithms for VFD generally used in practice.
Multilayer perceptron (MLP) is a feedforward ANN commonly employed in supervised learning tasks comprising multiple layers of interconnected neurons that sequentially transform input data to generate the final output [165]. Fig. 9 depicts the fundamental structure of an MLP consisting of an input layer, one or more hidden layers, and the output layer.
Figure 9: Multilayer perceptron approach with two hidden layers
The input layer accepts the initial data, like the feature set of vehicle components. Hidden layers apply multiple nonlinear transformations to this data, where each layer contains neurons connected to all neurons in the preceding layer. A neuron’s output in the hidden layer is computed by passing a weighted sum of inputs through a nonlinear activation function, such as ReLU [166]. ReLU, as an activation function, is typically defined as the positive portion of its input (0 to infinity):
f(x)=x+=max(0,x)
Also, the Softmax activation function is used for multi-class classification, which can be defined as follows:
σ(→z)=ezi∑Kj=1ezj
Here, σ is Softmax, →z is the input vector, ezi is a standard exponential function for the input vector, K is the number of classes in the muti-class classifier, and ezj is a standard exponential function for the output vector [167]. The output layer generates the final result at the network’s end, usually comprising multiple neurons. This result is a category label in classification tasks and a continuous value in regression tasks. MLP can diagnose complex mechanical parts of vehicles based on their modal information, extracting natural frequencies and creating fault signatures to locate and characterize faults. The method was able to estimate the location of an under-surface mechanical fault on an automobile cylinder block and has the potential to solve more sophisticated fault diagnosis problems [168]. This is because MLP demonstrates the capacity to represent intricate input-output relationships, due to their utilization of non-linear activation functions. Additionally, MLP classifiers can explore the type of faults occurring from the chosen features. Vinayagam et al. [169] applied MLP to monitor the condition of vehicle suspension systems through vibration signal analysis, achieving 98% accuracy with a 0.016 error rate in fault classification. Vibration signals were captured by mounting an accelerometer near the suspension system of a Ford EcoSport vehicle, and then the J48 DT algorithm was used to select the most important features from the vibration data. Moreover, from the study of Khoualdia et al. [170], the optimized MLP was able to successfully detect various types of faults in EV induction motors, including broken rotor bars, bearing faults, and misalignment, under various operating conditions. The crest factor, kurtosis, and variance of the vibration signals were important features that contributed to the effectiveness of the fault diagnosis system. The researchers used the Taguchi design method and the Lavenberg-Marquardt learning algorithm to optimize the architecture of the MLP neural network to improve diagnostic accuracy. These developments showcase MLP’s potential to adapt and tackle new challenges in vehicle fault detection. Recent innovations have broadened MLP’s applications in sensitive areas, such as combining it with encryption for private vehicle congestion detection [171]. The study utilizes proxy re-encryption and additive homomorphic encryption to preserve the confidentiality of raw sensing data and learning models while maintaining secure computation efficiency. However, MLP faces the challenge of dealing with heterogeneous encrypted data from different vehicle manufacturers.
3.3.2 Convolutional Neural Network
This network is a class of ANN most commonly used for image analysis in deep learning. A typical convolutional neural network (CNN) comprises several layers, each playing a specific role in the network’s ability to learn and extract features from input images [172]. The main layers of a CNN structure are shown in Fig. 10.
Figure 10: Basic architecture of CNN, adapted from [177]
i) Input layer: This layer is where the input image is fed into the network. The image is usually represented as a 3-dimensional tensor of height, width, and depth, where the depth corresponds to the number of color channels (e.g., RGB or grayscale).
ii) Convolutional layer: The feature extraction happens in this layer. It consists of multiple filters (kernels or weights), each performing a convolution operation on the input image [173]. Each filter produces a feature map representing a particular feature the filter is sensitive to, such as edges or corners. Most commonly, ReLU works as an activation function to the output of this layer [174].
iii) Pooling layer: The pooling layer downsizes the output feature maps and reduces their dimensionality, making the network more computationally efficient. The most common pooling operation is max pooling, which takes the maximum value in each pooling window [175].
iv) Fully connected layer: The fully connected layer is where the output of the convolutional and pooling layers is flattened into a 1-dimensional vector and passed through a traditional neural network layer with fully connected neurons. This layer is used to learn the high-level representation of the input features and make a prediction about the input image’s class [176].
v) Output layer: This produces the network’s final output, usually a probability distribution over the possible output classes. The most common activation function used in the output layer is the Softmax function.
Empirical evidence has demonstrated the efficacy of CNNs in the realm of automated feature extraction, as well as their superior generalization capabilities. Therefore, using CNNs in mechanical system condition monitoring is an appealing and promising prospect, owing to their exceptional aptitude for pattern recognition. For instance, a one-dimensional CNN-based pattern recognition model was used by Du et al. [178] to perform end-to-end fault diagnosis of automobile engines by processing vibration signals, achieving higher diagnostic accuracy than traditional methods. Convolutional and pooling were applied to extract features from the original vibration signals eliminating the need for manual feature extraction, and output to a new feature space for fault diagnosis. Researchers have also explored enhancements to the basic 1D-CNN architecture, such as incorporating self-normalizing neural networks to improve stability and convergence [179], and combining 1D-CNN with generative adversarial networks to address imbalanced datasets [180]. Moreover, to ensure the reliability of autonomous driving technology, Lee et al. [181] utilized CNN to diagnose the state of the image sensor in-vehicle cameras through images without the need for sensor attachment. The model achieved high performance, with an average of 92.6% in precision, recall, F1 score, and accuracy. However, the study was limited by the small number of samples. An accurate life prediction of the image sensor may be possible if a larger dataset is collected through an accelerated life test. In summary, despite CNNs demonstrating superior accuracy in VFD, current CNN-based fault diagnosis studies only consider features or images from a single domain, which may not reflect fault patterns comprehensively and can lead to low modeling accuracy and inaccurate diagnostic results. Also, CNNs cannot effectively identify and classify based on the importance of multi-channel features.
Long short-term memory (LSTM) networks, a specialized variant of recurrent neural networks (RNNs), are optimized for processing sequential data with long-term dependencies, such as speech, text, or time-series data [182]. While traditional RNNs propagate hidden states and produce outputs sequentially through the network [183], they often struggle with vanishing or exploding gradients in extended sequences, impeding the learning of long-term dependencies. This is alleviated in LSTM architecture, which consists of “memory cells” that can remember or forget according to selective information forging mechanisms. Fig. 11 presents the workflow of the LSTM algorithm for VFD where each LSTM cell comprises three main gates: forget gate, input gate, and output gate (parameterized to modulate information flow).
Figure 11: LSTM Structure for VFD
Based on current input, the model decides whether to update with new information (input gate), keep old information based on the importance of past states in solving this problem before (forget gate), and compute a predicted next state as output [184]. An LSTM cell’s output is a function of current memory and past hidden states attenuated by the gate. This architecture can update only some parts of past information while generating arbitrary output using states from large extended sequences, and it solves several problems associated with gradients. The ability of LSTM to learn complex temporal dynamics makes it particularly suitable for processing time-series data from vehicle sensors. In vibration-based fault diagnosis, the LSTM networks are used for spatiotemporal feature extraction from multi-sensor vibration signals. Reducing time steps within LSTM layers can substantially decrease computational complexity [185]. Kaplan et al. [186] proposed an LSTM-based fault diagnosis method for detecting short-circuit and open-circuit faults in EV induction motors, outperforming conventional ANNs in terms of accuracy for a large dataset of 600,000 samples, with 80% used for training. The authors also suggest applying the model in vehicle-to-grid technology for smart city implementations. Moreover, a novel LSTM-based method was proposed by Li et al. [187] to accurately diagnose potential battery cell failures and precisely locate thermal runway cells. By considering the influence of driver behavior. The method was tested using a large volume of real-world data to examine its robustness, reliability, and superiority. In modern automotive applications, LSTM-based intrusion detection systems achieved 99.995% accuracy in detecting and mitigating controller area network bus attacks, surpassing previous survival analysis methods [188]. LSTM implementations often incorporate modified adaptive boosting and prejudging models to enhance diagnostic accuracy, reduce computational time, and improve reliability. While LSTM-driven methods excel in rapid fault detection, challenges persist regarding extended training periods and limited generalization capabilities, necessitating further research and optimization.
Autoencoders, a class of self-supervised neural networks, are instrumental in unsupervised learning and dimensionality reduction tasks. Fig. 12 illustrates their architecture which comprises an encoder, which compresses high-dimensional input data into a compact latent representation, and a decoder, which reconstructs the original input from this compressed form [189]. These networks are optimized to minimize reconstruction error, typically quantified by loss functions such as mean squared error or binary cross-entropy, with parameters tuned via backpropagation algorithms [190]. In fault diagnosis, autoencoders excel in dimensionality reduction [191], signal denoising [192], and efficient data compression [193], demonstrating particular efficacy in anomaly detection within complex, multi-variate time-series sensor data. State-of-the-art implementations include convolutional autoencoders for detecting anomalies in hybrid EVs powertrain sensor data that correspond to powertrain faults [194].
Figure 12: Formation of autoencoder, adapted from [195]
The autoencoder’s ability was tested to identify abnormal sequences in the multivariate time-series data and it outperformed other unsupervised methods, such as outlier detectors and other DL techniques. Additionally, denoising shrinkage autoencoders (DSAE) coupled with residual consistency checking algorithm for anomaly detection in autonomous vehicles [196]. The DSAE used a shrinkage block and soft thresholding for feature representation enhancement and showed superior performance than traditional ML-based anomaly detectors in terms of ROC and F1 score. Autoencoders are frequently integrated with complementary neural architectures, such as generative adversarial networks and variational autoencoders, to enhance data generation quality and learn more robust latent representations [197]. However, current autoencoder designs face challenges simultaneously processing multiple sensor sequences and effectively extracting spatial neighborhood features from one-dimensional vibration signals, potentially limiting diagnostic accuracy in specific applications. Ongoing research is focused on developing sophisticated multi-variate, multi-sequence autoencoder architectures to address these limitations, aiming to improve feature extraction capabilities and overall diagnostic performance in increasingly complex and data-rich industrial systems.
4 AI-Based Vehicle Maintenance
Maintenance strategies can be subdivided in the following ways, as shown in Fig. 13.
Figure 13: Maintenance strategies
i) Corrective maintenance: Corrective maintenance is also known as breakdown maintenance. It is a type of maintenance that involves repairing components of a vehicle after it has failed. This type of maintenance is typically reactive, as it is performed in response to an unexpected failure or malfunction. Corrective maintenance can be costly in terms of downtime and repair costs, as immediate attention is required to restore the equipment or machinery to a functional state [198,199].
ii) Preventive maintenance: It is based on planned maintenance intervals that primarily depend on predetermined time intervals, occasionally also taking into account a system’s usage, for example, the mileage of automobiles. Preventive maintenance aims to maintain a system before it breaks down, ignoring the system’s actual state of health [200].
iii) Predictive Maintenance: This type of maintenance seeks to forecast the ideal time point for maintenance activities using knowledge of the system’s health status and previous maintenance data. It aims to ensure prompt repair before a failure while attempting to prevent a system’s premature and expensive repair [201]. Predictive maintenance (PdM) can be subdivided into statistical PdM and condition-based PdM. Statistical PdM focuses on information not directly related to the condition of a specific vehicle, such as previous maintenance information or information from the vehicle’s fleet or the larger population. In comparison, condition-based PdM involves using real-time data to monitor a system’s health and make informed maintenance decisions [202]. Jardine et al. [203] outlined three steps for condition-based maintenance programs: data collection, data processing, and maintenance decisions. The system’s condition is recorded using various sensor types in the data collection stage. The gathered data may encompass vibrational data, acoustic data, or images, among other possibilities. After data is collected, it needs to be processed to remove irrelevant information. This may include contributions from well-established error sources and less obvious ones, such as noise or incorrect signals. Following the collection and processing of data, the information derived from the processed data must be effectively applied to devise a maintenance plan based on the data gathered regarding the system’s condition. Maintenance decision support can be categorized into diagnostics and prognostics [204]. Diagnostics refers to detecting and identifying faults, which may be present or absent, and subsequently isolating the faulty component. Prognostics is a technique that facilitates the prediction of faults. It involves the assessment of the RUL of an element by identifying an impending fault and its likelihood within a particular operational timeframe before the actual occurrence of the fault [205].
4.2 AI-Based Predictive Maintenance Applications
Artificial intelligence methods provide a non-invasive approach with minimal computational demands and high accuracy. This is especially valuable when considering the scaling difficulties and the time-dependent nature of vehicle parts’ wear and tear. AI-driven vehicle predictive maintenance forecasts equipment breakdowns, which helps minimize operational interruptions, improve performance, and decrease maintenance expenses. Table 6 shows various AI algorithms offering substantial potential for maintenance development, prognostics, and health management in the modern automotive sector.
5 Prospects, Future Directions, and Solutions
The imperative for interpretability in vehicular fault diagnosis has become increasingly pronounced as automotive systems evolve in complexity, incorporating sophisticated electronic components and software architectures. Conventional diagnostic methodologies, which predominantly rely on domain expertise and empirical heuristics, are proving inadequate in addressing the multifaceted challenges presented by contemporary vehicles. As a result, there has been a paradigm shift towards ML and DL algorithms and other data-driven analytical frameworks, which offer superior diagnostic efficacy. These advanced computational approaches demonstrate enhanced capabilities in deciphering the intricate interplay of factors contributing to vehicle malfunctions, thereby facilitating more accurate and efficient fault identification and resolution strategies. For instance, using an adversarial learned denoising shrinkage autoencoder has shown promise in interpreting sensor data anomalies in autonomous vehicles, achieving high accuracy and reduced response time [221]. However, the opaque algorithmic structures inherent in numerous DL models present substantial obstacles with respect to their interpretability and explicability. Contemporary research endeavors are primarily focused on developing and implementing explainable artificial intelligence methodologies, which aim to elucidate the internal mechanisms of these complex models while maintaining their operational efficacy [222]. Such approaches encompass a diverse array of techniques, including feature significance analysis, proxy model construction, and advanced data visualization strategies. The future trajectory of interpretability in vehicular fault diagnosis appears auspicious, with current scholarly investigations centered on the formulation of hybrid frameworks. These innovative models seek to synthesize the inherent transparency of rule-based systems with the robust predictive capabilities afforded by ML and DL algorithms, thereby potentially offering a synergistic solution to the interpretability dilemma. Following are described some current key issues and their future research direction to interpret the vehicle fault diagnosis. Fig. 14 summarizes the major ongoing challenges and potential research paths for improving the interpretation of vehicle fault diagnosis systems.
Figure 14: Future research framework for AI-driven VFD
5.1 Integration of AI with Vehicle-to-Everything (V2X) Communication
AI algorithms can analyze vast amounts of data collected from various sensors and detect potential vehicle faults at an early stage. It can be further enhanced by integrating with V2X communication systems to enable more sophisticated data processing and decision-making processes. This integration would facilitate vehicles to share real-time health information with other vehicles, infrastructures, pedestrians, clouds, and service centers, enabling predictive maintenance and efficient repairs [223,224]. For instance, Raihan and coworkers [225] proposed a system that combines AI with fog computing in V2X networks to assist autonomous driving and enhance traffic flow. This setup uses AI to handle data processing near the network edge, which reduces delays and improves system reliability. A significant challenge is developing communication systems that are robust enough to manage the highly mobile and ever-changing nature of vehicle networks. To tackle this, researchers have proposed integrated sensing and communication systems to combine sensing and communication functions into a single system, aiming to boost performance and efficiency [226].
5.2 Insufficient Availability of Labeled Data
Using authentic data provides an opportunity to assess the efficacy of established methodologies in practical settings. One of the limitations of using real-world data is the absence or incomplete nature of labeling, as annotating a vast quantity of data is a time-intensive task that necessitates specialized expertise. Although unsupervised methods exist that do not require labels, it is generally acknowledged that semi-supervised or supervised methods tend to produce more reliable outcomes in vehicle fault diagnosis. At a minimum, labeled data is a prerequisite for model testing, even if the models have been trained on unlabeled data. Hence, future researchers can focus on optimized labeling procedures [227]. Although there exist uncomplicated statistical techniques for identifying outliers in a statistical context, it is only through the discernment of a human specialist that a determination can be made as to whether a particular subset of data should be classified as a genuine anomaly, such as a malfunction or an indication of deterioration. Therefore, it seems reasonable to integrate specialized expertise into the labeling procedure to surpass the costly method of manually labeling the complete dataset. Using active learning in conjunction with expert knowledge to selectively designate subsets of data for labeling is a promising strategy known as visual interactive labeling [228].
5.3 Edge Computing and Cloud Connectivity
With the advancement of edge computing capabilities, AI-driven VFD systems can perform data analysis and decision-making directly within the vehicle. Edge computing combined with cloud connectivity offers a revolutionary approach to vehicle fault diagnosis, blending local processing power with cloud resources to improve seamless data transfer, remote diagnostics, and centralized management of vehicle fleets [229]. This involves designing efficient data flow and workload distribution mechanisms between the edge and the cloud. Techniques such as task offloading, load balancing, and dynamic resource allocation can be explored to optimize data processing and decision-making in a distributed manner [230]. However, the significant intricacies include the diverse infrastructure and high vehicle mobility, which make smooth integration of edge and cloud systems difficult [231]. Another crucial concern is maintaining data privacy and security in open environments, particularly when using parked vehicles for mobile edge computing [232]. To mitigate these issues, future research should develop robust resource management systems and create adaptive learning techniques that can adjust to different conditions and fault types. For instance, lightweight multiscale convolutional networks with adaptive pruning have shown potential for improving fault diagnosis accuracy while managing complexity across various operating conditions [233]. Additionally, implementing blockchain technology in vehicular networks could enhance fault tolerance and reduce communication delays while ensuring secure service delivery [234].
As AI-driven fault diagnosis depends on data transmission and connectivity, it requires robust cybersecurity measures to secure sensitive vehicle information from being accessed by unauthorized agents and protect against malicious attacks. Therefore, future works should be oriented towards the establishment of robust security mechanisms such as encryption, authentication protocols and intrusion detection systems, and secure communication channels to guarantee that all exchanged data among vehicles or between vehicular nodes in some aspects are transmitted with confidentiality (protecting information contents from unauthorized access), integrity (change resistance for incoming message against modifications by unknown entities), authenticity (determined whether data was sent from a valid source) [235]. Vehicles need intrusion detection systems to help resolve cyber threats within vehicle networks on time. To work with the constraints of in-vehicle systems, which have limited computing power and make fast detections, novel solutions were created. One of them is an entropy-based analysis with sliding windows. It is a technique that makes high detection accuracy and efficiency of threats do not necessitate state-of-the-art cryptanalysis systems; this can be applied in real-time for automotive environments [236]. Additionally, the security of hardware components - utilized in VFD systems is paramount. This protects control units, sensors, and critical components against physical attacks and reverse engineering or unauthorized changes. A secure boot can be used for this purpose, as well as those measures and tamper-proof hardware and encryption mechanisms [237]. Dealing with the wide range of cybersecurity risks facing the automotive industry requires a systematic method for risk assessment. These usually contain steps like risk identification, analysis, and models for quantifying risks (e.g., STRIDE, attack trees). This systematic process helps determine the cybersecurity requirements to protect all potential attack routes [238,239]. Furthermore, while information about a vehicle is invaluable for maintenance and safety purposes, the adapters used to gather such telemetry also represent considerable cybersecurity risks, especially since so many come with wireless capabilities like WiFi or Bluetooth. Studies have covered methods to disable these radio functions, leaving the hardware undisturbed, to reduce potential exploit points. This research highlights the demand for organizations to have a thorough cybersecurity strategy when working with automotive accessories, especially those capable of getting into vital vehicle systems [240].
5.5 Integration with Existing Maintenance Systems
Integrating AI-based VFD solutions with existing vehicle maintenance systems represents a paradigm shift in automotive diagnostics and predictive maintenance strategies. This sophisticated integration requires the creation of next-generation algorithms and decision support systems that use real-time fault diagnosis input to prioritize maintenance tasks dynamically, optimize resource allocation, and schedule service activities with unrivaled efficiency. With historical data-rich applications, adaptive maintenance schedules and cutting-edge diagnostic tools seamlessly integrated into all of the critical systems help in enabling AI-driven intelligent collaboration with human technicians that reduce overhead costs associated with reliance on humans for diagnosing issues or making necessary corrections, leading to much quicker response times and hence improving operational efficiency across the entire lifecycle. A broad study on armored vehicle transmissions demonstrated a prime example of this synergy: high-precision oil sensors with an expert system of unprecedentedly elevated fault detection and predictive maintenance. Unrivaled in cost-effective reliability, this state-of-the-art holistic method uses machine learning methods to evaluate properties such as temperature changes, water level fluctuations, contamination quantities, and oil viscosity adjustments. Speedy discovery of fault origins and AI-powered analytics leads to the assessment in exacting circumstances. As this domain continues to permeate, future research directions will involve more advanced integration frameworks that can simultaneously support multiple types of sensors and concurrently process multi-modal data in real-time using context-aware diagnostic results at a higher accuracy. Furthermore, exploring edge computing paradigms and advanced IoT technologies holds promise for further enhancing these integrated maintenance systems’ real-time capabilities, scalability, and overall efficiency, potentially revolutionizing the landscape of VFD and maintenance optimization. This helps maintenance staff make informed decisions about necessary actions [241]. The approach is flexible enough to work with different vehicle types and can be tailored to specific user requirements, suggesting it could be widely implemented in current maintenance systems. Research can focus on developing user-friendly interfaces and visualization techniques, which include designing dashboards, alerts, and notifications that present health data in a clear and actionable manner for maintenance personnel. User-friendly interfaces can enhance the usability and adoption of integrated VFD and maintenance systems [242].
The escalation in fatal road accidents is considerable due to the failure of crucial vehicle components. The smooth operation of the engine, transmission, and adjustment systems for suspension and tire inflation pressure plays a vital role in maintaining the balance and safety of automobiles and ensuring individuals’ safety. As a result, various AI technologies have been devised to mitigate dangerous vehicular accidents and mechanical malfunctions. The current review analyzes various patented machine learning and deep learning methodologies for implementing the VFD system to enhance predictive maintenance efficiency. The discourse has revealed that ML and DL algorithms are highly advantageous in VFD as they facilitate the user’s ability to oversee their vehicle and respond accordingly to projected data, thereby promoting optimal vehicle maintenance. Additionally, it reduces maintenance expenses by predicting significant equipment failures. However, the following findings have been summarized from this review:
i) Knowledge-based AI-powered methods are likely more capable of diagnosing vehicle faults than traditional model-based and signal-based methods.
ii) SVM consistently outperforms other ML algorithms regarding fault classification accuracy and reliability with small sample sizes and imbalanced datasets across different vehicle components, including engines, power transmission systems, and other rotating elements.
iii) CNNs have demonstrated superior capabilities in automatically extracting features and categorizing faults, particularly when combined with domain-specific data preprocessing methods. Additionally, CNN-based methods demonstrate higher diagnostic accuracy than conventional ML-based approaches in handling complex and multi-channel data.
iv) LSTM networks have shown exceptional performance in diagnosing vehicle faults by effectively analyzing time-series data, resulting in high accuracy. These also effectively model spatiotemporal sequences of high-dimensional multi-variate features to tackle complex scenarios.
Moreover, there is a need for advanced research and development of economic and adaptable technology that can be applied to luxury and non-luxury automobiles. The utilization of AI in the diagnosis system of automobiles is extensive and is expected to progress and enhance with further technological advancements following the resolution of existing research gaps. There is potential for further development in multiple research areas, such as uneven data distribution, compound fault types, multi-modal data fusion, and edge device implementation, as the VFD system necessitates a high degree of precision to identify faults accurately. In general, the research conducted in this field is emerging and holds promise for substantially improving the performance and safety of vehicles. While this review focused on commonly used supervised ML and DL techniques in vehicle fault diagnosis, it didn’t cover many unsupervised methods that warrant further analysis. Additionally, emerging technologies such as digital twins, blockchain, and deep transfer learning are becoming increasingly relevant in this field, indicating the need for future reviews to examine their impact and potential. However, the review’s insights can assist scholars and professionals in the automotive sector in making well-informed judgments concerning the choice and integration of AI technologies for proper fault diagnosis.
Acknowledgement: The authors would like to express their heartful gratitude to the journal editor and anonymous reviewers for their valuable feedback, which helped us improve the content and quality of our paper.
Funding Statement: The authors are grateful to the Universiti Malaysia Pahang Al-Sultan Abdullah and the Malaysian Ministry of Higher Education for their generous support and funding provided through University Distinguished Research Grants (Project No. RDU223016), as well as financial assistance provided through the Fundamental Research Grant Scheme (No. FRGS/1/2022/TK10/ UMP/02/35).
Author Contributions: Study conception and design: Md Naeem Hossain, Md Mustafizur Rahman; data collection: Md Naeem Hossain; analysis and interpretation of results: Md Naeem Hossain, Md Mustafizur Rahman, Devarajan Ramasamy; draft manuscript preparation: Md Naeem Hossain. All authors reviewed the results and approved the final version of the manuscript.
Availability of Data and Materials: The data supporting this study’s findings are available on request from the corresponding author.
Ethics Approval: Not applicable.
Conflicts of Interest: The authors declare that they have no conflicts of interests to report regarding the present study.
References
1. Elliott A. The culture of AI: everyday life and the digital revolution. London: Routledge; 2019. doi:10.4324/9781315387185. [Google Scholar] [CrossRef]
2. Ajitha PV, Nagra A. An overview of artificial intelligence in automobile industry—a case study on Tesla cars. Solid State Technol. 2021;64(2):503–12. [Google Scholar]
3. Haenlein M, Kaplan A. A brief history of artificial intelligence: on the past, present, and future of artificial intelligence. Calif Manage Rev. 2019;61(4):5–14. doi:10.1177/0008125619864925. [Google Scholar] [CrossRef]
4. Alexopoulos K, Nikolakis N, Chryssolouris G. Digital twin-driven supervised machine learning for the development of artificial intelligence applications in manufacturing. Int J Comput Integr Manuf. 2020;33(5):429–39. doi:10.1080/0951192X.2020.1747642. [Google Scholar] [CrossRef]
5. Taisch M, Casidsid ML, Despeisse M, Luglietti R, May G, Morin TR, et al. The 2019 world manufacturing forum report. In: Skills for the future of manufacturing. Cernobbio, Italy: World Manufacturing Foundation; 2019. [Google Scholar]
6. Ćelić J, Bronzin T, Horvat M, Jović A, Stipić A, Prole B, et al. Generative AI in E-maintenance: myth or reality? Artif Intell. 2024;7:8. doi:10.1109/MIPRO60963.2024.10569282. [Google Scholar] [CrossRef]
7. Pecht MG, Kang M. Introduction to PHM. In: Prognostics and health management of electronics: fundamentals, machine learning, and the internet of things. USA: Wiley-IEEE Press; 2018; p. 1–37. [Google Scholar]
8. Cachada A, Barbosa J, Leitño P, Gcraldcs CAS, Deusdado L, Costa J, et al. Maintenance 4.0: intelligent and predictive maintenance system architecture. In: 2018 IEEE 23rd International Conference on Emerging Technologies and Factory Automation (ETFA), 2018; Turin, Italy; p. 139–46. doi:10.1109/ETFA.2018.8502489. [Google Scholar] [CrossRef]
9. Bokrantz J, Skoogh A, Berlin C, Wuest T, Stahre J. Smart maintenance: an empirically grounded conceptualization. Int J Prod Econ. 2020;223:107534. doi:10.1016/j.ijpe.2019.107534. [Google Scholar] [CrossRef]
10. Jimenez JJM, Schwartz S, Vingerhoeds R, Grabot B, Salaün M. Towards multi-model approaches to predictive maintenance: a systematic literature survey on diagnostics and prognostics. J Manuf Syst. 2020;56:539–57. doi:10.1016/j.jmsy.2020.07.008. [Google Scholar] [CrossRef]
11. Ranasinghe K, Sabatini R, Gardi A, Bijjahalli S, Kapoor R, Fahey T, et al. Advances in integrated system health management for mission-essential and safety-critical aerospace applications. Prog Aerosp Sci. 2022;128:100758. doi:10.1016/j.paerosci.2021.100758. [Google Scholar] [CrossRef]
12. Chen Y, Peng G, Zhu Z, Li S. A novel deep learning method based on attention mechanism for bearing remaining useful life prediction. Appl Soft Comput. 2020;86:105919. doi:10.1016/j.asoc.2019.105919. [Google Scholar] [CrossRef]
13. Rahim MA, Rahman MA, Rahman MM, Asyhari AT, Bhuiyan MZA, Ramasamy D. Evolution of IoT-enabled connectivity and applications in automotive industry: a review. Veh Commun. 2021;27:100285. doi:10.1016/j.vehcom.2020.100285. [Google Scholar] [CrossRef]
14. Erkoyuncu JA, Khan S, Hussain SMF, Roy R. A framework to estimate the cost of no-fault found events. Int J Prod Econ. 2016;173(4):207–22. doi:10.1016/j.ijpe.2015.12.013. [Google Scholar] [CrossRef]
15. Holland S. Unsettled technology opportunities for vehicle health management and the role for health-ready components. USA: SAE International; 2020. SAE Technical Paper EPR2020003. doi:10.4271/EPR2020003. [Google Scholar] [CrossRef]
16. Alghassi A. Prognostics and health management of power electronics. UK: Cranfield University; 2016. [Google Scholar]
17. Becker J, Helmle M, Pink O. System architecture and safety requirements for automated driving. In: Watzenig D, Horn M, editors. Automated driving: safer and more efficient future driving. Cham: Springer International Publishing; 2017. p. 265–83. doi:10.1007/978-3-319-31895-0_11. [Google Scholar] [CrossRef]
18. Mode GR. Adversarial robustness of deep learning enabled Industry 4.0 prognostics. Columbia: University of Missouri; 2020. doi:10.32469/10355/88952. [Google Scholar] [CrossRef]
19. Gong CSA, Su CHS, Chen YH, Guu DY. How to implement automotive fault diagnosis using artificial intelligence scheme. Micromachines. 2022;13(9):1–28. doi:10.3390/mi13091380. [Google Scholar] [PubMed] [CrossRef]
20. Jain M, Vasdev D, Pal K, Sharma V. Systematic literature review on predictive maintenance of vehicles and diagnosis of vehicle’s health using machine learning techniques. Comput Intell. 2022;38(6):1990–2008. doi:10.1111/coin.12553. [Google Scholar] [CrossRef]
21. Rasheed R, Qazi F, Ahmed A, Asif A, Shams H. Machine learning approaches for in-vehicle failure prognosis in automobiles: a review. VFAST Trans Softw Eng. 2024;12(1):169–82. doi:10.21015/vtse.v12i1.1713. [Google Scholar] [CrossRef]
22. Sundaram KM, Hussain A, Sanjeevikumar P, Holm-Nielsen JB, Kaliappan VK, Santhoshi BK. Deep learning for fault diagnostics in bearings, insulators, PV panels, power lines, and electric vehicle applications—the state-of-the-art approaches. IEEE Access. 2021;9:41246–60. doi:10.1109/ACCESS.2021.3064360. [Google Scholar] [CrossRef]
23. Trivedi M, Kakkar R, Gupta R, Agrawal S, Tanwar S, Niculescu VC, et al. Blockchain and deep learning-based fault detection framework for electric vehicles. Mathematics. 2022;10(19):3626. doi:10.3390/math10193626. [Google Scholar] [CrossRef]
24. Jiang W, Cao Y, Deng X. A novel Z-network model based on Bayesian network and Z-number. IEEE Trans Fuzzy Syst. 2019;28(8):1585–99. doi:10.1109/TFUZZ.2019.2918999. [Google Scholar] [CrossRef]
25. Abid A, Khan MT, Iqbal J. A review on fault detection and diagnosis techniques: basics and beyond. Artif Intell Rev. 2021;54(5):3639–64. doi:10.1007/s10462-020-09934-2. [Google Scholar] [CrossRef]
26. Chi Y, Dong Y, Wang ZJ, Yu FR, Leung VCM. Knowledge-based fault diagnosis in industrial Internet of Things: a survey. IEEE Internet Things J. 2022;9(15):12886–900. doi:10.1109/JIOT.2022.3163606. [Google Scholar] [CrossRef]
27. Arlsson HK. Monitoring vehicle suspension elements using machine learning techniques. Sweden: KTH Royal Institute of Technology; 2019. [Google Scholar]
28. Dai X, Gao Z. From model, signal to knowledge: a data-driven perspective of fault detection and diagnosis. IEEE Trans Ind Inform. 2013;9(4):2226–38. doi:10.1109/TII.2013.2243743. [Google Scholar] [CrossRef]
29. Rahman MA, Rahim MA, Rahman MM, Moustafa N, Razzak I, Ahmad T, et al. A secure and intelligent framework for vehicle health monitoring exploiting big-data analytics. IEEE Trans Intell Transp Syst. 2022;23(10):19727–42. doi:10.1109/TITS.2021.3138255. [Google Scholar] [CrossRef]
30. Olugbade S, Ojo S, Imoize AL, Isabona J, Alaba MO. A review of artificial intelligence and machine learning for incident detectors in road transport systems. Math Comput Appl. 2022;27(5):77. doi:10.3390/mca27050077. [Google Scholar] [CrossRef]
31. Bedi P, Goyal SB, Kumar J, Choudhary S. Smart automobile health monitoring system. In: Multimedia technologies in the internet of things environment. Singapore: Springer; 2022. vol. 2, p. 127–46. doi:10.1007/978-981-16-3828-2_7. [Google Scholar] [CrossRef]
32. Lang W, Hu Y, Gong C, Zhang X, Xu H, Deng J. Artificial intelligence-based technique for fault detection and diagnosis of EV motors: a review. IEEE Trans Transp Electrif. 2021;8(1):384–406. doi:10.1109/TTE.2021.3110318. [Google Scholar] [CrossRef]
33. Drakaki M, Karnavas YL, Tziafettas IA, Linardos V, Tzionas P. Machine learning and deep learning based methods toward Industry 4.0 predictive maintenance in induction motors: state of the art survey. J Ind Eng Manag. 2022;15(1):31–57. doi:10.3926/jiem.3597. [Google Scholar] [CrossRef]
34. Xue H, Wu M, Zhang Z, Wang H. Intelligent diagnosis of mechanical faults of in-wheel motor based on improved artificial hydrocarbon networks. ISA Trans. 2022;120:360–71. doi:10.1016/j.isatra.2021.03.015. [Google Scholar] [PubMed] [CrossRef]
35. Choudhary A, Fatima S, Panigrahi BK. State of the art technologies in fault diagnosis of electric vehicles: a component-based review. IEEE Trans Transp Electrif. 2022;9(2):2324–47. doi:10.1109/TTE.2022.3209166. [Google Scholar] [CrossRef]
36. AlShorman O, Irfan M, Saad N, Zhen D, Haider N, Glowacz A, et al. A review of artificial intelligence methods for condition monitoring and fault diagnosis of rolling element bearings for induction motor. Shock Vib. 2020;2020(1):8843759. doi:10.1155/2020/8843759. [Google Scholar] [CrossRef]
37. Gültekin Ö., Cinar E, Özkan K, Yazıcı A. Real-time fault detection and condition monitoring for industrial autonomous transfer vehicles utilizing edge artificial intelligence. Sensors. 2022;22(9):3208. doi:10.3390/s22093208. [Google Scholar] [PubMed] [CrossRef]
38. Byun YS, Kim BH, Jeong RG. Sensor fault detection and signal restoration in intelligent vehicles. Sensors. 2019;19(15):3306. doi:10.3390/s19153306. [Google Scholar] [PubMed] [CrossRef]
39. Na W, Park C, Lee S, Yu S, Lee H. Sensitivity-based fault detection and isolation algorithm for road vehicle chassis sensors. Sensors. 2018;18(8):2720. doi:10.3390/s18082720. [Google Scholar] [PubMed] [CrossRef]
40. Xiong R, Yu Q, Shen W, Lin C, Sun F. A sensor fault diagnosis method for a lithium-ion battery pack in electric vehicles. IEEE Trans Power Electron. 2019;34(10):9709–18. doi:10.1109/TPEL.2019.2893622. [Google Scholar] [CrossRef]
41. Khan MMH, Luo L, Huang C, Abdelzaher T. SNTS: sensor network troubleshooting suite. In: Distributed Computing in Sensor Systems: Third IEEE International Conference, DCOSS 2007, 2007 Jun 18–20; Santa Fe, NM, USA: Springer; p. 142–57. doi:10.1007/978-3-540-73090-3_10. [Google Scholar] [CrossRef]
42. Khalid A, Umer T, Afzal MK, Anjum S, Sohail A, Asif HM. Autonomous data driven surveillance and rectification system using in-vehicle sensors for intelligent transportation systems (ITS). Comput Netw. 2018;139:109–18. doi:10.1016/j.comnet.2018.04.008. [Google Scholar] [CrossRef]
43. Yeong DJ, Velasco-Hernandez G, Barry J, Walsh J. Sensor and sensor fusion technology in autonomous vehicles: a review. Sensors. 2021;21(6):2140. doi:10.3390/s21062140. [Google Scholar] [PubMed] [CrossRef]
44. Ge Y, Hou P, Lyu T, Lai Y, Su S, Luo W, et al. Machine learning-aided remote monitoring of NOx emissions from heavy-duty diesel vehicles based on OBD data streams. Atmosphere. 2023;14(4):651. doi:10.3390/atmos14040651. [Google Scholar] [CrossRef]
45. Ma B, Li J, Liang J, Liu P, Hou L, Zhao L, et al. An intelligent fault diagnosis algorithm for vehicle internal combustion engines based on instantaneous speed for a smart city. J Test Eval. 2023;51(3):1335–46. doi:10.1520/JTE20220099. [Google Scholar] [CrossRef]
46. Liu C, Che L, Bi X. Engine fault identification method based on TWSVM algorithm. J Intern Combust Engine. 2019;37(1):84–9 (In Chinese). doi:10.16236/j.cnki.nrjxb.201901012. [Google Scholar] [CrossRef]
47. Zhang F, Jiang M, Zhang L, Ji S, Sui Q, Su C, et al. Internal combustion engine fault identification based on FBG vibration sensor and support vector machines algorithm. Math Probl Eng. 2019;2019(1):8469868. doi:10.1155/2019/8469868. [Google Scholar] [CrossRef]
48. Rahim MA, Rahman MA, Rahman MM, Zaman N, Moustafa N, Razzak I. An intelligent risk management framework for monitoring vehicular engine health. IEEE Trans Green Commun Netw. 2022;6(3):1298–306. doi:10.1109/TGCN.2022.3179350. [Google Scholar] [CrossRef]
49. Khazaee M, Banakar A, Ghobadian B, Mirsalim MA, Minaei S. Remaining useful life (RUL) prediction of internal combustion engine timing belt based on vibration signals and artificial neural network. Neural Comput Appl. 2021;33(13):7785–801. doi:10.1007/s00521-020-05520-3. [Google Scholar] [CrossRef]
50. Shahid SM, Ko S, Kwon S. Real-time abnormality detection and classification in diesel engine operations with convolutional neural network. Expert Syst Appl. 2022;192(10):116233. doi:10.1016/j.eswa.2021.116233. [Google Scholar] [CrossRef]
51. Kumar A, Gandhi CP, Zhou Y, Vashishtha G, Kumar R, Xiang J. Improved CNN for the diagnosis of engine defects of 2-wheeler vehicle using wavelet synchro-squeezed transform (WSST). Knowledge-Based Syst. 2020;208:106453. doi:10.1016/j.knosys.2020.106453. [Google Scholar] [CrossRef]
52. Naveen Venkatesh S, Chakrapani G, Senapti SB, Annamalai K, Elangovan M, Indira V, et al. Misfire detection in dpark ignition engine using transfer learning. Comput Intell Neurosci. 2022;2022(1):7606896. doi:10.1155/2022/7606896. [Google Scholar] [PubMed] [CrossRef]
53. da Silva MER, Gracioli G, de Araujo GM. Feature selection in machine learning for knocking noise detection. In: 2022 XII Brazilian Symposium on Computing Systems Engineering (SBESC), 2022; Fortaleza/CE, Brazil: IEEE; p. 1–8. doi:10.1109/SBESC56799.2022.9964726. [Google Scholar] [CrossRef]
54. Ngatiman NA, Nuawi MZ, Putra A, Qamber IS, Sutikno T, Jopri MH. Spark plug failure detection using Z-freq and machine learning. TELKOMNIKA (Telecommun Comput Electron Control). 2021;19(6):2020–9. doi:10.12928/telkomnika.v19i6.22027. [Google Scholar] [CrossRef]
55. Francis LT, Pierozan VE, Gracioli G, de Araujo GM. Data-driven anomaly detection of engine knock based on automotive ECU. In: 2022 XII Brazilian Symposium on Computing Systems Engineering (SBESC), 2022; Fortaleza/CE, Brazil: IEEE; p. 1–8. doi:10.1109/SBESC56799.2022.9965059. [Google Scholar] [CrossRef]
56. Huangfu Y, Seddik E, Habibi S, Wassyng A, Tjong J. Fault detection and diagnosis of engine spark plugs using deep learning techniques. SAE Int J Engines. 2021;15(4):515–25. doi:10.4271/03-15-04-0027. [Google Scholar] [CrossRef]
57. Qin C, Jin Y, Zhang Z, Yu H, Tao J, Sun H, et al. Anti-noise diesel engine misfire diagnosis using a multi-scale CNN-LSTM neural network with denoising module. CAAI Trans Intell Technol. 2023;8(3):963–86. doi:10.1049/cit2.12170. [Google Scholar] [CrossRef]
58. Li X, Wang N, Lyu Y, Duan Y, Zhao J. Data-driven fault early warning model of automobile engines based on soft classification. Electronics. 2023;12(3):511. doi:10.3390/electronics12030511. [Google Scholar] [CrossRef]
59. Yang M, Chen H, Guan C. Research on diesel engine fault diagnosis method based on machine learning. In: 2022 4th International Conference on Frontiers Technology of Information and Computer (ICFTIC), 2022; Qingdao, China: IEEE; p. 1078–82. doi:10.1109/ICFTIC57696.2022.10075307. [Google Scholar] [CrossRef]
60. Aliramezani M, Koch CR, Shahbakhti M. Modeling, diagnostics, optimization, and control of internal combustion engines via modern machine learning techniques: a review and future directions. Prog Energy Combust Sci. 2022;88:109–14. doi:10.1016/j.pecs.2021.100967. [Google Scholar] [CrossRef]
61. Jiregna I, Sirata G. A review of the vehicle suspension system. J Mech Energy Eng. 2020;4(2):109–14. doi:10.30464/jmee.2020.4.2.109. [Google Scholar] [CrossRef]
62. Arun Balaji P, Sugumaran V. Fault detection of automobile suspension system using decision tree algorithms: a machine learning approach. Proc Inst Mech Eng Part E J Process Mech Eng. 2024;238(3):1206–17. doi:10.1177/09544089231152698. [Google Scholar] [CrossRef]
63. Jeong K, Choi SB, Choi H. Sensor fault detection and isolation using a support vector machine for vehicle suspension systems. IEEE Trans Veh Technol. 2020;69(4):3852–63. doi:10.1109/TVT.2020.2977353. [Google Scholar] [CrossRef]
64. Jeong K, Choi S. Model-based sensor fault diagnosis of vehicle suspensions with a support vector machine. Int J Automot Technol. 2019;20(5):961–70. doi:10.1007/s12239-019-0090-z. [Google Scholar] [CrossRef]
65. Abdelfattah A, Ibrahim H. Health monitoring of automotive suspension system using machine learning. In: International Conference on Vehicle Technology and Intelligent Transport Systems, VEHITS 2021, 2021; p. 325–32. doi:10.5220/0010402503250332. [Google Scholar] [CrossRef]
66. Baicoianu A, Stanoiu P, Velea M, Husar C. A machine learning proposal for condition monitoring of vehicle suspension. In: 16th International Conference on Innovations in Intelligent Systems and Applications, INISTA 2022, 2022; Biarritz, France: IEEE. doi:10.1109/INISTA55318.2022.9894160. [Google Scholar] [CrossRef]
67. Hu H, Luo H, Deng X. Health monitoring of automotive suspensions: a LSTM network approach. Shock Vib. 2021;2021(1):6626024. doi:10.1155/2021/6626024. [Google Scholar] [CrossRef]
68. Luo H, Huang M, Zhou Z. A dual-tree complex wavelet enhanced convolutional LSTM neural network for structural health monitoring of automotive suspension. Measurement. 2019;137:14–27. doi:10.1016/j.measurement.2019.01.038. [Google Scholar] [CrossRef]
69. Zehelein T, Werk P, Lienkamp M. An evaluation of autoencoder and sparse filter as automated feature extraction process for automotive damper defect diagnosis. In: 2019 14th International Conference on Ecological Vehicles and Renewable Energies, EVER 2019, 2019; Monte-Carlo, Monaco. doi:10.1109/EVER.2019.8813630. [Google Scholar] [CrossRef]
70. Jeong K, Choi SB. Takagi-sugeno fuzzy observer-based magnetorheological damper fault diagnosis using a support vector machine. IEEE Trans Control Syst Technol. 2022;30(4):1723–35. doi:10.1109/TCST.2021.3123611. [Google Scholar] [CrossRef]
71. Shahab M, Moavenian M. A novel fault diagnosis technique based on model and computational intelligence applied to vehicle active suspension systems. Int J Numer Model Electron Netw Devices Fields. 2019;32(3):e2541. doi:10.1002/jnm.2541. [Google Scholar] [CrossRef]
72. Kokane P, Bagavathi Sivakumar P. Online model for suspension faults diagnostics using IoT and analytics. In: International Conference on Advanced Computing Networking and Informatics: ICANI-2018, 2019; India: Springer; p. 145–54. doi:10.1007/978-981-13-2673-8_17. [Google Scholar] [CrossRef]
73. Suranjan S, Selvan CP, Nair PS, Hasan T. Numerical modeling and optimization of turns in double wish bone suspension of an automotive. Mater Today Proc. 2021;45(1):7213–5. doi:10.1016/j.matpr.2021.02.419. [Google Scholar] [CrossRef]
74. Risaliti E, Tamarozzi T, Vermaut M, Cornelis B, Desmet W. Multibody model based estimation of multiple loads and strain field on a vehicle suspension system. Mech Syst Signal Process. 2019;123:1–25. doi:10.1016/j.ymssp.2018.12.024. [Google Scholar] [CrossRef]
75. Arun B, Venkatesh NS, Sugumaran V. Fault diagnosis of suspension system based on spectrogram image and vision transformer. Eksploat i Niezawodn. 2024;26(1):174860. doi:10.17531/ein/174860. [Google Scholar] [CrossRef]
76. Sai SA, Venkatesh SN, Dhanasekaran S, Balaji PA, Sugumaran V, Lakshmaiya N, et al. Transfer learning based fault detection for suspension system using vibrational analysis and radar plots. Machines. 2023;11(8):778. doi:10.3390/machines11080778. [Google Scholar] [CrossRef]
77. Rodgers B. Tire engineering: an introduction. USA: CRC Press; 2020. doi:10.1201/9781003022961. [Google Scholar] [CrossRef]
78. Schramm D, Hesse B, Maas N, Unterreiner M. Vehicle technology: technical foundations of current and future motor vehicles. Berlin/Boston: Walter de Gruyter GmbH & Co KG; 2020. doi:10.1515/9783110595703. [Google Scholar] [CrossRef]
79. Deng Y, Wang Z, Shen H, Gong J, Xiao Z. A comprehensive review on non-pneumatic tyre research. Mater Des. 2023;227(5):111742. doi:10.1016/j.matdes.2023.111742. [Google Scholar] [CrossRef]
80. Trzesniowski M. Tyres and wheels. In: Suspension system. Wiesbaden: Springer Vieweg: Springer; 2023. p. 1–76. [Google Scholar]
81. Vasan V, Sridharan NV, Prabhakaranpillai Sreelatha A, Vaithiyanathan S. Tire condition monitoring using transfer learning-based deep neural network approach. Sensors. 2023;23(4):2177. doi:10.3390/s23042177. [Google Scholar] [PubMed] [CrossRef]
82. Vasantharaj A, Karuppusamy SA, Nandhagopal N, Pillai APV. A low-cost in-tire-pressure monitoring SoC using integer/floating-point type convolutional neural network inference engine. Microprocess Microsyst. 2023;98:104771. doi:10.1016/j.micpro.2023.104771. [Google Scholar] [CrossRef]
83. Kuric I, Klarák J, Sága M, Císar M, Hajdučík A, Wiecek D. Analysis of the possibilities of tire-defect inspection based on unsupervised learning and deep learning. Sensors. 2021;21(21):7073. doi:10.3390/s21217073. [Google Scholar] [PubMed] [CrossRef]
84. Rausch J, Jaramillo-Vogel D, Perseguers S, Schnidrig N, Grobéty B, Yajan P. Automated identification and quantification of tire wear particles (TWP) in airborne dust: sEM/EDX single particle analysis coupled to a machine learning classifier. Sci Total Environ. 2022;803:149832. doi:10.1016/j.scitotenv.2021.149832. [Google Scholar] [PubMed] [CrossRef]
85. Pardeshi SS, Patange AD, Jegadeeshwaran R, Bhosale MR. Tyre pressure supervision of two wheeler using machine learning. Struct Durab Heal Monit. 2022;16(3):271–290. doi:10.32604/sdhm.2022.010622. [Google Scholar] [CrossRef]
86. Wei L, Wang X, Li L, Yu L, Liu Z. A low-cost tire pressure loss detection framework using machine learning. IEEE Trans Ind Electron. 2020;68(12):12730–8. doi:10.1109/TIE.2020.3047040. [Google Scholar] [CrossRef]
87. Wang Y, Zhang Y, Zheng L, Yin L, Chen J, Lu J. Unsupervised learning with generative adversarial network for automatic tire defect detection from X-ray images. Sensors. 2021;21(20):1–19. doi:10.3390/s21206773. [Google Scholar] [PubMed] [CrossRef]
88. Maurya D, Khaleghian S, Sriramdas R, Kumar P, Kishore RA, Kang MG, et al. 3D printed graphene-based self-powered strain sensors for smart tires in autonomous vehicles. Nat Commun. 2020;11(1):5392. doi:10.1038/s41467-020-19088-y. [Google Scholar] [PubMed] [CrossRef]
89. Anoop PS. Implementing K-star algorithm to monitor tyre pressure using extracted statistical features from vertical wheel hub vibrations. Indian J Sci Technol. 2016;9(1):1–7. doi:10.17485/ijst/2016/v9i47/107926. [Google Scholar] [CrossRef]
90. Sachan R, Iqbal S. Application of machine learning technique for development of indirect tire pressure monitoring system. SAE Int J Adv Curr Pract Mobil. 2021;4(2021–26-0016):753–61. doi:10.4271/2021-26-0016. [Google Scholar] [CrossRef]
91. Xu N, Askari H, Huang Y, Zhou J, Khajepour A. Tire force estimation in intelligent tires using machine learning. IEEE Trans Intell Transp Syst. 2020;23(4):3565–74. doi:10.1109/TITS.2020.3038155. [Google Scholar] [CrossRef]
92. Li G, Görges D. Ecological adaptive cruise control for vehicles with step-gear transmission based on reinforcement learning. IEEE Trans Intell Transp Syst. 2019;21(11):4895–905. doi:10.1109/TITS.2019.2947756. [Google Scholar] [CrossRef]
93. Milindar SD, Prasanna S, Baskar P. Comprehensive review on dual clutch transmission. Int J Veh Perform. 2022;8(1):74–108. doi:10.1504/IJVP.2022.119440. [Google Scholar] [CrossRef]
94. Koukoura S, Carroll J, McDonald A. On the use of AI based vibration condition monitoring of wind turbine gearboxes. J Phy Conf Series. 2019;1222(1):12045. doi:10.1088/1742-6596/1222/1/012045. [Google Scholar] [CrossRef]
95. Dong Y, Jiang H, Jiang W, Xie L. Dynamic normalization supervised contrastive network with multiscale compound attention mechanism for gearbox imbalanced fault diagnosis. Eng Appl Artif Intell. 2024;133(4):108098. doi:10.1016/j.engappai.2024.108098. [Google Scholar] [CrossRef]
96. Yousuf H, Zainal AY, Alshurideh M, Salloum SA. Artificial intelligence models in power system analysis. In: Artificial intelligence for sustainable development: theory, practice and future applications. Springer; 2020; p. 231–42. doi:10.1007/978-3-030-51920-9_12. [Google Scholar] [CrossRef]
97. Zuber N, Bajrić R, Šostakov R. Gearbox faults identification using vibration signal analysis and artificial intelligence methods. Eksploat i Niezawodn. 2014;16(1):61–5. [Google Scholar]
98. Ma B, Cai W, Han Y, Yu G. A novel probability confidence CNN model and its application in mechanical fault diagnosis. IEEE Trans Instrum Meas. 2021;70:1–11. doi:10.1109/TIM.2021.3077965. [Google Scholar] [CrossRef]
99. Liu S, Huang J, Ma J, Luo J. SRMANet: toward an interpretable neural network with multi-attention mechanism for gearbox fault diagnosis. Appl Sci. 2022;12(16):8388. doi:10.3390/app12168388. [Google Scholar] [CrossRef]
100. Miltenović A, Rakonjac I, Oarcea A, Perić M, Rangelov D. Detection and monitoring of pitting progression on gear tooth flank using deep learning. Appl Sci. 2022;12(11):5327. doi:10.3390/app12115327. [Google Scholar] [CrossRef]
101. Zhang M, Li D, Wang K, Li Q, Ma Y, Liu Z. An adaptive order-band energy ratio method for the fault diagnosis of planetary gearboxes. Mech Syst Signal Process. 2022;165(11):108336. doi:10.1016/j.ymssp.2021.108336. [Google Scholar] [CrossRef]
102. Zakaria M, Elias HA, Mounira D. Gearbox faut diagnosis optimization using conventional neural networks and machine learning methods. Int J Mechatronics Appl Mech. 2022;(12):41–6. doi:10.17683/ijomam/issue12.6. [Google Scholar] [CrossRef]
103. Yu J, Zhou X. One-dimensional residual convolutional autoencoder based feature learning for gearbox fault diagnosis. IEEE Trans Ind Inform. 2020;16(10):6347–58. doi:10.1109/TII.2020.2966326. [Google Scholar] [CrossRef]
104. Azamfar M, Singh J, Bravo-Imaz I, Lee J. Multisensor data fusion for gearbox fault diagnosis using 2-D convolutional neural network and motor current signature analysis. Mech Syst Signal Process. 2020;144:106861. doi:10.1016/j.ymssp.2020.106861. [Google Scholar] [CrossRef]
105. Kapanigowda NS, Krishna H, Vasanth S. Internal combustion engine gearbox bearing fault prediction using J48 and random forest classifier. Int J Electr Comput Eng. 2023;13(4):4467–76. doi:10.11591/ijece.v13i4.pp4467-4476. [Google Scholar] [CrossRef]
106. Zhang P, Chen C. A two-stage framework for time-frequency analysis and fault diagnosis of planetary gearboxes. Appl Sci. 2023;13(8):5202. doi:10.3390/app13085202. [Google Scholar] [CrossRef]
107. Elvira-ortiz DA, Saucedo-dorantes JJ, Romero-troncoso RDJ. An entropy-based condition monitoring strategy for the detection and classification of wear levels in gearboxes. Entropy. 2023;25(3):424. doi:10.3390/e25030424. [Google Scholar] [PubMed] [CrossRef]
108. Ravikumar KN, Madhusudana CK, Kumar H, Gangadharan KV. Classification of gear faults in internal combustion (IC) engine gearbox using discrete wavelet transform features and K star algorithm. Eng Sci Technol Int J. 2022;30(1):101048. doi:10.1016/j.jestch.2021.08.005. [Google Scholar] [CrossRef]
109. Shah J, Wang W. An evolving neuro-fuzzy classifier for fault diagnosis of gear systems. ISA Trans. 2022;123(1):372–80. doi:10.1016/j.isatra.2021.05.019. [Google Scholar] [PubMed] [CrossRef]
110. Inturi V, Shreyas N, Sabareesh GR. Anfis-based defect severity prediction on a multi-stage gearbox operating under fluctuating speeds. Neural Process Lett. 2021;53(5):3445–66. doi:10.1007/s11063-021-10557-z. [Google Scholar] [CrossRef]
111. Wen W, Bai Y, Cheng W. Generative adversarial learning enhanced fault diagnosis for planetary gearbox under varying working conditions. Sensors. 2020;20(6):1685. doi:10.3390/s20061685. [Google Scholar] [PubMed] [CrossRef]
112. Karamti H. Accompanying deep framework for faults in motor and gearbox with disproportion vibrational samples. Neural Comput Appl. 2023;35(10):7659–76. doi:10.1007/s00521-022-08020-8. [Google Scholar] [CrossRef]
113. Vos K, Peng Z, Jenkins C, Shahriar MR, Borghesani P, Wang W. Vibration-based anomaly detection using LSTM/SVM approaches. Mech Syst Signal Process. 2022;169(1):108752. doi:10.1016/j.ymssp.2021.108752. [Google Scholar] [CrossRef]
114. Praveen HM, Sabareesh GR. Wavelet based real-time planetary gearbox health monitoring under non-stationary operation. Exp Tech. 2022;46(5):861–75. doi:10.1007/s40799-021-00518-5. [Google Scholar] [CrossRef]
115. Handikherkar VC, Phalle VM. Gear fault detection using machine learning techniques-a simulation–driven approach. Int J Eng. 2021;34(1):212–23. doi:10.5829/ije.2021.34.01a.24. [Google Scholar] [CrossRef]
116. Fumi DE, Sultan IA. A novel in-vehicle real-time brake-monitoring system. Proc Inst Mech Eng Part D J Automob Eng. 2009;223(6):793–804. doi:10.1243/09544070JAUTO996. [Google Scholar] [CrossRef]
117. El-Fatah A, Sharkawy AN, Ghazaly NM, Moaaz A. A comparative study of different control methods for anti-lock braking system (ABS). SVU-Int J Eng Sci Appl. 2021;2(1):27–34. doi:10.21608/svusrc.2021.65855.1007. [Google Scholar] [CrossRef]
118. Hu ZX, Wang Y, Ge MF, Liu J. Data-driven fault diagnosis method based on compressed sensing and improved multiscale network. IEEE Trans Ind Electron. 2019;67(4):3216–25. doi:10.1109/TIE.2019.2912763. [Google Scholar] [CrossRef]
119. Alamelu Manghai TM, Jegadeeshwaran R. Vibration based brake health monitoring using wavelet features: a machine learning approach. JVC/J Vib Control. 2019;25(18):2534–50. doi:10.1177/10775463198597. [Google Scholar] [CrossRef]
120. Raveendran R, Devika KB, Subramanian SC. Brake fault identification and fault-tolerant directional stability control of heavy road vehicles. IEEE Access. 2020;8:169229–46. doi:10.1109/ACCESS.2020.3024251. [Google Scholar] [CrossRef]
121. Jegadeeshwaran R, Sugumaran V. Vibration based condition monitoring of a brake system using statistical features with logit boost and simple logistic algorithm. Int J Perform Eng. 2018;14(1):1–8. doi:10.23940/ijpe.18.01.p1.18. [Google Scholar] [CrossRef]
122. Kang J, Kim CS, Kang JW, Gwak J. Recurrent autoencoder ensembles for brake operating unit anomaly detection on metro vehicles. Comput Mater Contin. 2022;73(1):1–14. doi:10.32604/cmc.2022.023641. [Google Scholar] [CrossRef]
123. Stender M, Tiedemann M, Spieler D, Schoepflin D, Hoffmann N, Oberst S. Deep learning for brake squeal: brake noise detection, characterization and prediction. Mech Syst Signal Process. 2021;149:107181. doi:10.1016/j.ymssp.2020.107181. [Google Scholar] [CrossRef]
124. Xing Y, Lv C. Dynamic state estimation for the advanced brake system of electric vehicles by using deep recurrent neural networks. IEEE Trans Ind Electron. 2019;67(11):9536–47. doi:10.1109/TIE.2019.2952807. [Google Scholar] [CrossRef]
125. Raveendran R, Devika KB, Subramanian SC. Learning-based fault diagnosis of air brake system using wheel speed data. Proc Inst Mech Eng Part D J Automob Eng. 2022;236(12):2598–609. doi:10.1177/09544070211063719. [Google Scholar] [CrossRef]
126. Marimuthu AMT, Rakkiyannan J, Jakkamputi L, Vaithiyanathan S, Gnanasekaran S. Vibration-based fault diagnosis study on a hydraulic brake system using fuzzy logic with histogram features. Struct Durab Heal Monit. 2022;16(4):383–96. doi:10.32604/sdhm.2022.011396. [Google Scholar] [CrossRef]
127. Badillo S, Banfai B, Birzele F, Davydov II, Hutchinson L, Kam-Thong T, et al. An introduction to machine learning. Clin Pharmacol Ther. 2020;107(4):871–85. doi:10.1002/cpt.1796. [Google Scholar] [PubMed] [CrossRef]
128. Alloghani M, Al-Jumeily D, Mustafina J, Hussain A, Aljaaf AJ. A systematic review on supervised and unsupervised machine learning algorithms for data science. In: Supervised unsupervised learn data science. 2020; Switzerland: Springer, Cham; p. 3–21. doi:10.1007/978-3-030-22475-2_1. [Google Scholar] [CrossRef]
129. Puiutta E, Veith EMSP. Explainable reinforcement learning: a survey. In: International Cross-Domain Conference for Machine Learning and Knowledge Extraction, 2020; Dublin, Ireland: Springer; p. 77–95. doi:10.1145/3616864. [Google Scholar] [CrossRef]
130. Gong CSA, Su CHS, Tseng KH. Implementation of machine learning for fault classification on vehicle power transmission system. IEEE Sens J. 2020;20(24):15163–76. doi:10.1109/JSEN.2020.3010291. [Google Scholar] [CrossRef]
131. Sarker IH. Machine learning: algorithms, real-world applications and research directions. SN Comput Sci. 2021;2(3):160. doi:10.1007/s42979-021-00592-x. [Google Scholar] [PubMed] [CrossRef]
132. Charbuty B, Abdulazeez A. Classification based on decision tree algorithm for machine learning. J Appl Sci Technol Trends. 2021;2(1):20–8. doi:10.38094/jastt20165. [Google Scholar] [CrossRef]
133. Yang FJ. An extended idea about decision trees. In: 2019 International Conference on Computational Science and Computational Intelligence (CSCI), 2019; Las Vegas, NV, USA: IEEE; p. 349–54. doi:10.1109/CSCI49370.2019.00068. [Google Scholar] [CrossRef]
134. Kang H, Chen Y, Zhao H. Model establishment of decision tree algorithm and its application in vehicle fault prediction analysis. In: 2020 5th International Conference on Automation, Control and Robotics Engineering (CACRE), 2020; Dalian, China: IEEE; p. 647–51. doi:10.1109/CACRE50138.2020.9230017. [Google Scholar] [CrossRef]
135. Bansal M, Goyal A, Choudhary A. A comparative analysis of K-nearest neighbor, genetic, support vector machine, decision tree, and long short term memory algorithms in machine learning. Decis Anal J. 2022;3(11):100071. doi:10.1016/j.dajour.2022.100071. [Google Scholar] [CrossRef]
136. Schonlau M, Zou RY. The random forest algorithm for statistical learning. Stata J. 2020;20(1):3–29. doi:10.1177/1536867X20909688. [Google Scholar] [CrossRef]
137. Hehn TM, Kooij JFP, Hamprecht FA. End-to-end learning of decision trees and forests. Int J Comput Vis. 2020;128(4):997–1011. doi:10.1007/s11263-019-01237-6. [Google Scholar] [CrossRef]
138. Wan L, Gong K, Zhang G, Yuan X, Li C, Deng X. An efficient rolling bearing fault diagnosis method based on spark and improved random forest algorithm. IEEE Access. 2021;9:37866–82. doi:10.1109/ACCESS.2021.3063929. [Google Scholar] [CrossRef]
139. Pisner DA, Schnyer DM. Support vector machine. In: Machine learning. Netherlands: Elsevier; 2020. p. 101–21. doi:10.1016/B978-0-12-815739-8.00006-7. [Google Scholar] [CrossRef]
140. Indu R, Dimri SC. Power of kernel functions, its benefits, and limitations. In: 2023 International Conference on Intelligent Systems, Advanced Computing and Communication (ISACC), 2023; Silchar, India: IEEE; p. 1–7. doi:10.1109/ISACC56298.2023.10084201. [Google Scholar] [CrossRef]
141. Tanveer M, Rajani T, Rastogi R, Shao YH, Ganaie MA. Comprehensive review on twin support vector machines. Ann Oper Res. 2022; 1–46. doi:10.1007/s10479-022-04575-w. [Google Scholar] [CrossRef]
142. Biddle L, Fallah S. A novel fault detection, identification and prediction approach for autonomous vehicle controllers using SVM. Automot Innov. 2021;4(3):301–14. doi:10.1007/s42154-021-00138-0. [Google Scholar] [CrossRef]
143. Yao L, Fang Z, Xiao Y, Hou J, Fu Z. An intelligent fault diagnosis method for lithium battery systems based on grid search support vector machine. Energy. 2021;214:118866. doi:10.1016/j.energy.2020.118866. [Google Scholar] [CrossRef]
144. Shi Q, Zhang H. Fault diagnosis of an autonomous vehicle with an improved SVM algorithm subject to unbalanced datasets. IEEE Trans Ind Electron. 2020;68(7):6248–56. doi:10.1109/TIE.2020.2994868. [Google Scholar] [CrossRef]
145. Taunk K, De S, Verma S, Swetapadma A. A brief review of nearest neighbor algorithm for learning and classification. In: 2019 International Conference on Intelligent Computing and Control Systems (ICCS), 2019; Madurai, India: IEEE; p. 1255–60. doi:10.1109/ICCS45141.2019.9065747. [Google Scholar] [CrossRef]
146. Ullah R, Khanb AH, Emaduddina SM. ck-NN: a clustered k-nearest neighbours approach for large-scale classification. Adv Distrib Comput Artif Intell J. 2019;8(3):67–77. doi:10.14201/ADCAIJ2019836777. [Google Scholar] [CrossRef]
147. El Morr C, Jammal M, Ali-Hassan H, El-Hallak W. K-nearest neighbors. In: Machine learning for practical decision making: a multidisciplinary perspective with applications from healthcare, engineering and business analytics. Switzerland: Springer; 2022. p. 301–18. doi:10.1007/978-3-031-16990-8_10. [Google Scholar] [CrossRef]
148. Wang J, Zhou Z, Li Z, Du S. A novel fault detection scheme based on mutual k-nearest neighbor method: application on the industrial processes with outliers. Processes. 2022;10(3):497. doi:10.3390/pr10030497. [Google Scholar] [CrossRef]
149. Vasavi S, Aswarth K, Durga TS, Gokhale AA. Predictive analytics as a service for vehicle health monitoring using edge computing and AK-NN algorithm. Mater Today: Proc. 2021;46:8645–54. doi:10.1016/j.matpr.2021.03.658. [Google Scholar] [CrossRef]
150. Lu J, Qian W, Li S, Cui R. Enhanced K-nearest neighbor for intelligent fault diagnosis of rotating machinery. Appl Sci. 2021;11(3):919. doi:10.3390/app11030919. [Google Scholar] [CrossRef]
151. Sinaga KP, Yang MS. Unsupervised K-means clustering algorithm. IEEE Access. 2020;8:80716–27. doi:10.1109/ACCESS.2020.2988796. [Google Scholar] [CrossRef]
152. Huang S, Kang Z, Xu Z, Liu Q. Robust deep k-means: an effective and simple method for data clustering. Pattern Recognit. 2021;117:107996. doi:10.1016/j.patcog.2021.107996. [Google Scholar] [CrossRef]
153. Nie F, Li Z, Wang R, Li X. An effective and efficient algorithm for K-means clustering with new formulation. IEEE Trans Knowl Data Eng. 2022;35(4):3433–43. doi:10.1109/TKDE.2022.3155450. [Google Scholar] [CrossRef]
154. Kang H, Chen Y, Zhao H. K-means algorithm description and the application of cluster analysis in heavy truck vehicle fault. In: 2020 IEEE 5th Information Technology and Mechatronics Engineering Conference (ITOEC), 2020; Chongqing, China: IEEE; p. 1130–3. doi:10.1109/ITOEC49072.2020.9141676. [Google Scholar] [CrossRef]
155. Wu M, Du W, Zhang F, Zhao N, Wang J, Wang L, et al. Fault diagnosis method for lithium-ion battery packs in real-world electric vehicles based on K-means and the Fréchet algorithm. ACS Omega. 2022;7(44):40145–62. doi:10.1021/acsomega.2c04991. [Google Scholar] [PubMed] [CrossRef]
156. Yang D, Xie J, Yin Z. Improved K-means algorithm for fault diagnosis of vehicle. In: 2023 9th International Conference on Computer and Communications (ICCC), 2023; Chongqing, China: IEEE; p. 1536–40. [Google Scholar]
157. Shinde PP, Shah S. A review of machine learning and deep learning applications. In: 2018 Fourth International Conference on Computing Communication Control and Automation (ICCUBEA), 2018; Pune, India: IEEE; p. 1–6. doi:10.1109/ICCUBEA.2018.8697857. [Google Scholar] [CrossRef]
158. Ongsulee P. Artificial intelligence, machine learning and deep learning. In: 2017 15th International Conference on ICT and Knowledge Engineering (ICT&KE), 2017; Bangkok, Thailand: IEEE; p. 1–6. doi:10.1109/ICTKE.2017.8259629. [Google Scholar] [CrossRef]
159. Janiesch C, Zschech P, Heinrich K. Machine learning and deep learning. Electron Mark. 2021;31(3):685–95. doi:10.1007/s12525-021-00475-2. [Google Scholar] [CrossRef]
160. Asteris PG, Mokos VG. Concrete compressive strength using artificial neural networks. Neural Comput Appl. 2020;32(15):11807–26. doi:10.1007/s00521-019-04663-2. [Google Scholar] [CrossRef]
161. Wang YS, Liu NN, Guo H, Wang XL. An engine-fault-diagnosis system based on sound intensity analysis and wavelet packet pre-processing neural network. Eng Appl Artif Intell. 2020;94:103765. doi:10.1016/j.engappai.2020.103765. [Google Scholar] [CrossRef]
162. Cervantes-Bobadilla M, García-Morales J, Saavedra-Benítez YI, Hernández-Pérez JA, Adam-Medina M, Guerrero-Ramírez GV, et al. Multiple fault detection and isolation using artificial neural networks in sensors of an internal combustion engine. Eng Appl Artif Intell. 2023;117(9–10):105524. doi:10.1016/j.engappai.2022.105524. [Google Scholar] [CrossRef]
163. Xie X, Xiong G, Chen J, Zhang J. Universal transparent artificial neural network-based fault section diagnosis models for power systems. Adv Theory Simulations. 2022;5(4):2100402. doi:10.1002/adts.202100402. [Google Scholar] [CrossRef]
164. Arel I, Rose DC, Karnowski TP. Deep machine learning—a new frontier in artificial intelligence research [research frontier]. IEEE Comput Intell Mag. 2010;5(4):13–8. doi:10.1109/MCI.2010.938364. [Google Scholar] [CrossRef]
165. Ramchoun H, Ghanou Y, Ettaouil M, Janati Idrissi MA. Multilayer perceptron. Int J Interact Multimed Artif Intell. 2016;4(1):26–30. doi:10.9781/ijimai.2016.415. [Google Scholar] [CrossRef]
166. Szandała T. Review and comparison of commonly used activation functions for deep neural networks. In: Bio-inspired neurocomputing. Singapore: Springer; 2021. p. 203–24. doi:10.1007/978-981-15-5495-7_11. [Google Scholar] [CrossRef]
167. Sivri TT, Akman NP, Berkol A. Multiclass classification using arctangent activation function and its variations. In: 2022 14th International Conference on Electronics, Computers and Artificial Intelligence (ECAI), 2022; Ploiesti, Romania: IEEE; p. 1–6. doi:10.1109/ECAI54874.2022.9847486. [Google Scholar] [CrossRef]
168. Mohammadzaheri M, Amouzadeh A, Doustmohammadi M, Emadi M, Nasiri N, Jamshidi E, et al. Fault diagnosis of an automobile cylinder block with neural process of modal information. Int J Mech Mechatron Eng. 2021;21(2):1–8. [Google Scholar]
169. Vinayagam N, Ramaian CP, Dhanraj JA, Solomon JM, Anaimuthu S, Selvaraju N. A multilayer perceptron approach for condition monitoring of automobile suspension system through vibration signal. In: ISET International Conference on Applied Science & Engineering (CASE 2021), 2021; Chennai, India. doi:10.1063/5.0119562. [Google Scholar] [CrossRef]
170. Khoualdia T, Lakehal A, Chelli Z, Khoualdia K, Nessaib K. Optimized multi layer perceptron artificial neural network based fault diagnosis of induction motor using vibration signals. Diagnostyka. 2021;22: 65–74. doi:10.29354/diag/133091. [Google Scholar] [CrossRef]
171. Li Y, Zhou D, Li Y, Weng J, Sun M, Yang Y, et al. Privacy-preserving and real-time detection of vehicular congestion using multilayer perceptron approach for internet of vehicles. IEEE Trans Veh Technol. 2022;71(12):12530–42. doi:10.1109/TVT.2022.3199407. [Google Scholar] [CrossRef]
172. Kiranyaz S, Avci O, Abdeljaber O, Ince T, Gabbouj M, Inman DJ. 1D convolutional neural networks and applications: a survey. Mech Syst Signal Process. 2021;151:107398. doi:10.1016/j.ymssp.2020.107398. [Google Scholar] [CrossRef]
173. Ding X, Li Z, Yu J, Xie W, Li X, Jiang T. A novel lightweight human activity recognition method via L-CTCN. Sensors. 2023;23(24):9681. doi:10.3390/s23249681. [Google Scholar] [PubMed] [CrossRef]
174. Ajit A, Acharya K, Samanta A. A review of convolutional neural networks. In: 2020 International Conference on Emerging Trends in Information Technology and Engineering (ic-ETITE), 2020; Vellore, India: IEEE; p. 1–5. doi:10.1109/ic-ETITE47903.2020.049. [Google Scholar] [CrossRef]
175. Zhou DX. Theory of deep convolutional neural networks: downsampling. Neural Netw. 2020;124:319–27. [Google Scholar] [PubMed]
176. Basha SHS, Dubey SR, Pulabaigari V, Mukherjee S. Impact of fully connected layers on performance of convolutional neural networks for image classification. Neurocomputing. 2020;378(7553):112–9. doi:10.1016/j.neucom.2019.10.008. [Google Scholar] [CrossRef]
177. Hadi MU, Qureshi R, Ahmed A, Iftikhar N. A lightweight CORONA-NET for COVID-19 detection in X-ray images. Expert Syst Appl. 2023;225(1):120023. doi:10.1016/j.eswa.2023.120023. [Google Scholar] [PubMed] [CrossRef]
178. Du C, Zhong R, Zhuo Y, Zhang X, Yu F, Li F, et al. Research on fault diagnosis of automobile engines based on the deep learning 1D-CNN method. Eng Res Express. 2022;4(1):15003. doi:10.1088/2631-8695/ac4834. [Google Scholar] [CrossRef]
179. Yinghua Y, Doliang L, Xiaozhi L. Fault diagnosis based on one-dimensional deep convolution neural network. In: 2020 Chinese Control And Decision Conference (CCDC), 2020; Hefei, China: IEEE; p. 5630–5. doi:10.1109/CCDC49329.2020.9164297. [Google Scholar] [CrossRef]
180. Jiang W, Wang C, Zou J, Zhang S. Application of deep learning in fault diagnosis of rotating machinery. Processes. 2021;9(6):919. doi:10.3390/pr9060919. [Google Scholar] [CrossRef]
181. Lee JH, Kwon MG, Kim YB, Hur JW. Failure diagnostics of camera image sensor for vehicle using CNN. J Korea Acad Coop Soc. 2022;23(12):877–84. doi:10.5762/KAIS.2022.23.12.877. [Google Scholar] [CrossRef]
182. Yu Y, Si X, Hu C, Zhang J. A review of recurrent neural networks: LSTM cells and network architectures. Neural Comput. 2019;31(7):1235–70. doi:10.1162/neco_a_01199. [Google Scholar] [PubMed] [CrossRef]
183. Das S, Tariq A, Santos T, Kantareddy SS, Banerjee I. Recurrent neural networks (RNNs): architectures, training tricks, and introduction to influential research. Mach Learn Brain Disord. 2023;197:117–38. doi:10.1007/978-1-0716-3195-9_4. [Google Scholar] [PubMed] [CrossRef]
184. Smagulova K, James AP. A survey on LSTM memristive neural network architectures and applications. Eur Phys J Spec Top. 2019;228(10):2313–24. doi:10.1140/epjst/e2019-900046-x. [Google Scholar] [CrossRef]
185. Hao S, Ge FX, Li Y, Jiang J. Multisensor bearing fault diagnosis based on one-dimensional convolutional long short-term memory networks. Measurement. 2020;159:107802. doi:10.1016/j.measurement.2020.107802. [Google Scholar] [CrossRef]
186. Kaplan H, Tehrani K, Jamshidi M. A fault diagnosis design based on deep learning approach for electric vehicle applications. Energies. 2021;14(20):6599. doi:10.3390/en14206599. [Google Scholar] [CrossRef]
187. Li D, Zhang Z, Liu P, Wang Z, Zhang L. Battery fault diagnosis for electric vehicles based on voltage abnormality by combining the long short-term memory neural network and the equivalent circuit model. IEEE Trans Power Electron. 2020;36(2):1303–15. doi:10.1109/TPEL.2020.3008194. [Google Scholar] [CrossRef]
188. Hossain MD, Inoue H, Ochiai H, Fall D, Kadobayashi Y. LSTM-based intrusion detection system for in-vehicle can bus communications. IEEE Access. 2020;8:185489–502. doi:10.1109/ACCESS.2020.3029307. [Google Scholar] [CrossRef]
189. Bo C, Chen X, Zhang J. Masked autoencoders as single object tracking learners. Comput Mater Contin. 2024;80(1):1105–22. doi:10.32604/cmc.2024.052329. [Google Scholar] [CrossRef]
190. Zhao T, Jin L, Zhou X, Li S, Liu S, Zhu J. Unsupervised anomaly detection approach based on adversarial memory autoencoders for multivariate time series. Comput Mater Contin. 2023;76(1):329–46. doi:10.32604/cmc.2023.038595. [Google Scholar] [CrossRef]
191. Pawar K, Attar VZ. Assessment of autoencoder architectures for data representation. In: Deep learning: concepts and architectures. Springer; 2019. p. 101–32. doi:10.1007/978-3-030-31756-0_4. [Google Scholar] [CrossRef]
192. Tagawa T, Tadokoro Y, Yairi T. Structured denoising autoencoder for fault detection and analysis. In: Asian Conference on Machine Learning, 2015; Nha Trang City, Vietnam: PMLR; p. 96–111. [Google Scholar]
193. Wang S, Chen H, Wu L, Wang J. A novel smart meter data compression method via stacked convolutional sparse auto-encoder. Int J Electr Power Energy Syst. 2020;118:105761. doi:10.1016/j.ijepes.2019.105761. [Google Scholar] [CrossRef]
194. Geglio A, Hedayati E, Tascillo M, Anderson D, Barker J, Havens TC. Deep convolutional autoencoder for assessment of drive-cycle anomalies in connected vehicle sensor data. In: 2022 IEEE Symposium Series on Computational Intelligence (SSCI), 2022; Singapore: IEEE; p. 743–9. doi:10.1109/SSCI51031.2022.10022233. [Google Scholar] [CrossRef]
195. Chandra R, Jain M, Maharana M, Krivitsky PN. Revisiting Bayesian autoencoders with MCMC. IEEE Access. 2022;10(1):40482–95. doi:10.1109/ACCESS.2022.3163270. [Google Scholar] [CrossRef]
196. Min H, Fang Y, Wu X, Lei X, Chen S, Teixeira R, et al. A fault diagnosis framework for autonomous vehicles with sensor self-diagnosis. Expert Syst Appl. 2023;224:120002. doi:10.1016/j.eswa.2023.120002. [Google Scholar] [CrossRef]
197. Liu H, Zhao H, Wang J, Yuan S, Feng W. LSTM-GAN-AE: a promising approach for fault diagnosis in machine health monitoring. IEEE Trans Instrum Meas. 2022;71:1–13. doi:10.1109/TIM.2021.3135328. [Google Scholar] [CrossRef]
198. Gackowiec P. General overview of maintenance strategies-concepts and approaches. Multidiscip Asp Prod Eng. 2019;2(1):126–39. doi:10.2478/mape-2019-0013. [Google Scholar] [CrossRef]
199. Yepez P, Alsayyed B, Ahmad R. Intelligent assisted maintenance plan generation for corrective maintenance. Manuf Lett. 2019;21:7–11. doi:10.1016/j.mfglet.2019.06.004. [Google Scholar] [CrossRef]
200. Basri EI, Razak IHA, Ab-Samat H, Kamaruddin S. Preventive maintenance (PM) planning: a review. J Qual Maint Eng. 2017;23(2):114–43. doi:10.1108/JQME-04-2016-0014. [Google Scholar] [CrossRef]
201. Nowakowski T, Tubis A, Werbińska-Wojciechowska S. Evolution of technical systems maintenance approaches-review and a case study. In: Intelligent systems in production engineering and maintenance. Springer; 2019. p. 161–74. doi:10.1007/978-3-319-97490-3_16. [Google Scholar] [CrossRef]
202. Zhang W, Yang D, Wang H. Data-driven methods for predictive maintenance of industrial equipment: a survey. IEEE Syst J. 2019;13(3):2213–27. doi:10.1109/JSYST.2019.2905565. [Google Scholar] [CrossRef]
203. Jardine AKS, Lin D, Banjevic D. A review on machinery diagnostics and prognostics implementing condition-based maintenance. Mech Syst Signal Process. 2006;20(7):1483–510. doi:10.1016/j.ymssp.2005.09.012. [Google Scholar] [CrossRef]
204. Xu G, Liu M, Wang J, Ma Y, Wang J, Li F, et al. Data-driven fault diagnostics and prognostics for predictive maintenance: a brief overview. In: 2019 IEEE 15th International Conference on Automation Science and Engineering (CASE), 2019; Vancouver, BC, Canada: IEEE; p. 103–8. doi:10.1109/COASE.2019.8843068. [Google Scholar] [CrossRef]
205. Li X, Zhang W, Ding Q. Deep learning-based remaining useful life estimation of bearings using multi-scale feature extraction. Reliab Eng Syst Saf. 2019;182:208–18. doi:10.1016/j.ress.2018.11.011. [Google Scholar] [CrossRef]
206. Yang H, Hong J, Liang F, Xu X. Machine learning-based state of health prediction for battery systems in real-world electric vehicles. J Energy Storage. 2023;66:107426. doi:10.1016/j.est.2023.107426. [Google Scholar] [CrossRef]
207. Shahraki AF, Al-Dahidi S, Taleqani AR, Yadav OP. Using LSTM neural network to predict remaining useful life of electrolytic capacitors in dynamic operating conditions. J Risk Reliab. 2023;237(1):16–28. doi:10.1177/1748006X2210875. [Google Scholar] [CrossRef]
208. Panda C, Singh TR. ML-based vehicle downtime reduction: a case of air compressor failure detection. Eng Appl Artif Intel. 2023;122:106031. doi:10.1016/j.engappai.2023.106031. [Google Scholar] [CrossRef]
209. El Kihel B. Development process to bearing fault diagnostic and prognostic for the predictive maintenance era. In: 10th International Conference on Innovation, Modern Applied Science & Environmental Studies (ICIES’2022), 2022. doi:10.1051/e3sconf/202235101036. [Google Scholar] [CrossRef]
210. Hiwase SD, JAGTAP P, Krishna D. Engine overheating prediction with machine learning using Gaussian mixture model (GMM). 2022; USA: SAE International SAE Technical Paper 2022-28-0007. doi:10.4271/2022-28-0007. [Google Scholar] [CrossRef]
211. Chaudhuri A, Ghosh SK. Predictive maintenance of vehicle fleets using hierarchical modified fuzzy support vector machine for industrial IoT datasets. In: Hybrid Artificial Intelligent Systems: 16th International Conference, HAIS 2021, 2021 Sep 22–24; Bilbao, Spain: Springer; p. 331–42. doi:10.1007/978-3-030-86271-8_28. [Google Scholar] [CrossRef]
212. Safavi S, Safavi MA, Hamid H, Fallah S. Multi-sensor fault detection, identification, isolation and health forecasting for autonomous vehicles. Sensors. 2021;21(7):2547. doi:10.3390/s21072547. [Google Scholar] [PubMed] [CrossRef]
213. Chaudhuri A, Patil R, Ghosh SK. Predictive maintenance of vehicle fleets using LSTM autoencoders for industrial IoT datasets. In: Big data privacy and security in smart cities. Switzerland, Springer: Cham; 2022. p. 103–18. doi:10.1007/978-3-031-04424-3_6. [Google Scholar] [CrossRef]
214. Revanur V, Ayibiowu A, Rahat M, Khoshkangini R. Embeddings based parallel stacked autoencoder approach for dimensionality reduction and predictive maintenance of vehicles. In: IoT Streams for Data-Driven Predictive Maintenance and IoT, Edge, and Mobile for Embedded Machine Learning: Second International Workshop, IoT Streams 2020, and First International Workshop, ITEM 2020, Co-Located with ECML/PKDD 2020, Sep 2020; Ghent, Belgium: Springer; p. 127–41. doi:10.1007/978-3-030-66770-2_10. [Google Scholar] [CrossRef]
215. Zhou J, Qin Y, Chen D, Liu F, Qian Q. Remaining useful life prediction of bearings by a new reinforced memory GRU network. Adv Eng Inform. 2022;53:101682. doi:10.1016/j.aei.2022.101682. [Google Scholar] [CrossRef]
216. O’Donnell J, Yoon HS. Determination of time-to-failure for automotive system components using machine learning. J Comput Inf Sci Eng. 2020;20(6):61003. doi:10.1115/1.4046818. [Google Scholar] [CrossRef]
217. Vališ D, Žák L, Vintr Z. Application of fuzzy inference system for analysis of oil field data to optimize combustion engine maintenance. Proc Inst Mech Eng Part D J Automob Eng. 2019;233(14):3736–45. doi:10.1177/0954407019833521. [Google Scholar] [CrossRef]
218. Massaro A, Selicato S, Galiano A. Predictive maintenance of bus fleet by intelligent smart electronic board implementing artificial intelligence. IoT. 2020;1(2):12. doi:10.3390/iot1020012. [Google Scholar] [CrossRef]
219. Voronov S, Krysander M, Frisk E. Predictive maintenance of lead-acid batteries with sparse vehicle operational data. Int J Progn Heal Manag. 2020;11(1):1–17. doi:10.36001/ijphm.2020.v11i1.2608. [Google Scholar] [CrossRef]
220. Sharma N, Kalra M. Predictive maintenance for commercial vehicles tyres using machine learning. In: 2022 13th International Conference on Computing Communication and Networking Technologies (ICCCNT), 2022; Kharagpur, India: IEEE; p. 1–6. doi:10.1109/ICCCNT54827.2022.9984497. [Google Scholar] [CrossRef]
221. Fang Y, Min H, Wu X, Lei X, Chen S, Teixeira R, et al. Toward interpretability in fault diagnosis for autonomous vehicles: interpretation of sensor data anomalies. IEEE Sens J. 2023;23(5):5014–27. doi:10.1109/JSEN.2023.3236838. [Google Scholar] [CrossRef]
222. Chamola V, Hassija V, Sulthana AR, Ghosh D, Dhingra D, Sikdar B. A review of trustworthy and explainable artificial intelligence (XAI). IEEE Access. 2023;11:78994–9015. doi:10.1109/ACCESS.2023.3294569. [Google Scholar] [CrossRef]
223. Tong W, Hussain A. Artificial intelligence for vehicle-to-everything. IEEE Access. 2019;7:10823–43. doi:10.1109/ACCESS.2019.2891073. [Google Scholar] [CrossRef]
224. Hossain MN, Rahman MM, Ramasamy D, Kadirgama K, Noor MM. Advancements, challenges, and implications for navigating the autonomous vehicle revolution. J Mech Eng Sci. 2024;8(2):10077–93. doi:10.15282/jmes.18.2.2024.9.0796. [Google Scholar] [CrossRef]
225. Rihan M, Elwekeil M, Yang Y, Huang L, Xu C, Selim MM. Deep-VFog: when artificial intelligence meets fog computing in V2X. IEEE Syst J. 2020;15(3):3492–505. doi:10.1109/JSYST.2020.3009998. [Google Scholar] [CrossRef]
226. Zhong Y, Bi T, Wang J, Zeng J, Huang Y, Jiang T, et al. Empowering the V2X network by integrated sensing and communications: background, design, advances, and opportunities. IEEE Netw. 2022;36(4):54–60. doi:10.1109/MNET.001.2100688. [Google Scholar] [CrossRef]
227. Bernard J, Zeppelzauer M, Sedlmair M, Aigner W. VIAL: a unified process for visual interactive labeling. Vis Comput. 2018;34:1189–207. doi:10.1007/s00371-018-1500-3. [Google Scholar] [CrossRef]
228. Bernard J, Hutter M, Zeppelzauer M, Fellner D, Sedlmair M. Comparing visual-interactive labeling with active learning: an experimental study. IEEE Trans Vis Comput Graph. 2017;24(1):298–308. doi:10.1109/TVCG.2017.2744818. [Google Scholar] [PubMed] [CrossRef]
229. Vermesan O, John R, Pype P, Daalderop G, Ashwathnarayan M, Bahr R, et al. Internet of vehicles-system of systems distributed intelligence for mobility applications. In: Intelligent technologies for internet of vehicles. Switzerland: Springer, Cham; 2021. p. 93–147. doi:10.1007/978-3-030-76493-7_4. [Google Scholar] [CrossRef]
230. Zhang Z, Li C, Peng S, Pei X. A new task offloading algorithm in edge computing. EURASIP J Wirel Commun Netw. 2021;2021(1):17. doi:10.1186/s13638-021-01895-6. [Google Scholar] [CrossRef]
231. Arthurs P, Gillam L, Krause P, Wang N, Halder K, Mouzakitis A. A taxonomy and survey of edge cloud computing for intelligent transportation systems and connected vehicles. IEEE Trans Intell Transp Syst. 2021;23(7):6206–21. doi:10.1109/TITS.2021.3084396. [Google Scholar] [CrossRef]
232. Zhou A, Ma X, Gao S, Wang S. Providing reliable service for parked-vehicle-assisted mobile edge computing. ACM Trans Internet Technol. 2022;22(4):1–24. doi:10.1145/3514242. [Google Scholar] [CrossRef]
233. Ding A, Qin Y, Wang B, Jia L, Cheng X. Lightweight multiscale convolutional networks with adaptive pruning for intelligent fault diagnosis of train bogie bearings in edge computing scenarios. IEEE Trans Instrum Meas. 2022;72:1–13. doi:10.1109/TIM.2022.3231325. [Google Scholar] [CrossRef]
234. Ahmed A, Abdullah S, Iftikhar S, Ahmad I, Ajmal S, Hussain Q. A novel blockchain based secured and QoS aware IoT vehicular network in edge cloud computing. IEEE Access. 2022;10:77707–22. doi:10.1109/ACCESS.2022.3192111. [Google Scholar] [CrossRef]
235. Ashibani Y, Mahmoud QH. Cyber physical systems security: analysis, challenges and solutions. Comput Secur. 2017;68:81–97. doi:10.1016/j.cose.2017.04.005. [Google Scholar] [CrossRef]
236. Baldini G. On the application of entropy measures with sliding window for intrusion detection in automotive in-vehicle networks. Entropy. 2020;22(9):1044. doi:10.3390/e22091044. [Google Scholar] [PubMed] [CrossRef]
237. Sharma P, Jain S, Gupta S, Chamola V. Role of machine learning and deep learning in securing 5G-driven industrial IoT applications. Ad Hoc Netw. 2021;123:102685. doi:10.1016/j.adhoc.2021.102685. [Google Scholar] [CrossRef]
238. Wang Y, Wang Y, Qin H, Ji H, Zhang Y, Wang J. A systematic risk assessment framework of automotive cybersecurity. Automot Innov. 2021;4:253–61. doi:10.1007/s42154-021-00140-6. [Google Scholar] [CrossRef]
239. Kern M, Liu B, Betancourt VP, Becker J. Model-based attack tree generation for cybersecurity risk-assessments in automotive. In: 2021 IEEE International Symposium on Systems Engineering (ISSE), 2021; Vienna, Austria: IEEE; p. 1–7. doi:10.1109/ISSE51541.2021.9582462. [Google Scholar] [CrossRef]
240. Larson E, Ford W, Lerner S, Daily J. Vehicle diagnostics adapter cybersecurity concerns with wireless connectivity. SAE Technical Paper 2023-01-0034. 2023. doi:10.4271/2023-01-0034. [Google Scholar] [CrossRef]
241. Li Y, Li T, Yi X, Liu H. Expert system for comprehensive transmission fault diagnosis based on oil sensor. In: 2020 International Conference on Sensing, Diagnostics, Prognostics, and Control (SDPC), 2020; Beijing, China: IEEE; p. 49–54. doi:10.1109/SDPC49476.2020.9353188. [Google Scholar] [CrossRef]
242. Protopsaltis A, Sarigiannidis P, Margounakis D, Lytos A. Data visualization in internet of things: tools, methodologies, and challenges. In: Proceedings of the 15th International Conference on Availability, Reliability and Security, 2020; Ireland; p. 1–11. doi:10.1145/3407023.3409228. [Google Scholar] [CrossRef]
Cite This Article
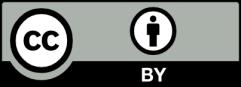
This work is licensed under a Creative Commons Attribution 4.0 International License , which permits unrestricted use, distribution, and reproduction in any medium, provided the original work is properly cited.