Open Access
ARTICLE
Computational Fluid Dynamics Approach for Predicting Pipeline Response to Various Blast Scenarios: A Numerical Modeling Study
1 Department of Mechanical Engineering, Jamia Millia Islamia (A Central University), New Delhi, 110025, India
2 Department of Civil Engineering, Jamia Millia Islamia (A Central University), New Delhi, 110025, India
* Corresponding Authors: Farman Saifi. Email: ; S. M. Anas. Email:
(This article belongs to the Special Issue: Recent Advances in Computational Methods for Performance Assessment of Engineering Structures and Materials against Dynamic Loadings)
Computer Modeling in Engineering & Sciences 2024, 140(3), 2747-2777. https://doi.org/10.32604/cmes.2024.051490
Received 06 March 2024; Accepted 11 May 2024; Issue published 08 July 2024
Abstract
Recent industrial explosions globally have intensified the focus in mechanical engineering on designing infrastructure systems and networks capable of withstanding blast loading. Initially centered on high-profile facilities such as embassies and petrochemical plants, this concern now extends to a wider array of infrastructures and facilities. Engineers and scholars increasingly prioritize structural safety against explosions, particularly to prevent disproportionate collapse and damage to nearby structures. Urbanization has further amplified the reliance on oil and gas pipelines, making them vital for urban life and prime targets for terrorist activities. Consequently, there is a growing imperative for computational engineering solutions to tackle blast loading on pipelines and mitigate associated risks to avert disasters. In this study, an empty pipe model was successfully validated under contact blast conditions using Abaqus software, a powerful tool in mechanical engineering for simulating blast effects on buried pipelines. Employing a Eulerian-Lagrangian computational fluid dynamics approach, the investigation extended to above-surface and below-surface blasts at standoff distances of 25 and 50 mm. Material descriptions in the numerical model relied on Abaqus’ default mechanical models. Comparative analysis revealed varying pipe performance, with deformation decreasing as explosion-to-pipe distance increased. The explosion’s location relative to the pipe surface notably influenced deformation levels, a key finding highlighted in the study. Moreover, quantitative findings indicated varying ratios of plastic dissipation energy (PDE) for different blast scenarios compared to the contact blast (P0). Specifically, P1 (25 mm subsurface blast) and P2 (50 mm subsurface blast) showed approximately 24.07% and 14.77% of P0’s PDE, respectively, while P3 (25 mm above-surface blast) and P4 (50 mm above-surface blast) exhibited lower PDE values, accounting for about 18.08% and 9.67% of P0’s PDE, respectively. Utilising energy-absorbing materials such as thin coatings of ultra-high-strength concrete, metallic foams, carbon fiber-reinforced polymer wraps, and others on the pipeline to effectively mitigate blast damage is recommended. This research contributes to the advancement of mechanical engineering by providing insights and solutions crucial for enhancing the resilience and safety of underground pipelines in the face of blast events.Keywords
Cite This Article
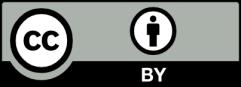
This work is licensed under a Creative Commons Attribution 4.0 International License , which permits unrestricted use, distribution, and reproduction in any medium, provided the original work is properly cited.