Open Access
ARTICLE
A High-Accuracy Curve Boundary Recognition Method Based on the Lattice Boltzmann Method and Immersed Moving Boundary Method
1 Hunan Provincial Key Laboratory of Health Maintenance for Mechanical Equipment, Hunan University of Science and Technology, Xiangtan, 411201, China
2 School of Mechanical Engineering, Hunan Chemical Vocational Technology College, Zhuzhou, 412000, China
* Corresponding Author: Yong-Zheng Jiang. Email:
Computer Modeling in Engineering & Sciences 2024, 140(3), 2533-2557. https://doi.org/10.32604/cmes.2024.051232
Received 01 March 2024; Accepted 11 May 2024; Issue published 08 July 2024
Abstract
Applying numerical simulation technology to investigate fluid-solid interaction involving complex curved boundaries is vital in aircraft design, ocean, and construction engineering. However, current methods such as Lattice Boltzmann (LBM) and the immersion boundary method based on solid ratio (IMB) have limitations in identifying custom curved boundaries. Meanwhile, IBM based on velocity correction (IBM-VC) suffers from inaccuracies and numerical instability. Therefore, this study introduces a high-accuracy curve boundary recognition method (IMB-CB), which identifies boundary nodes by moving the search box, and corrects the weighting function in LBM by calculating the solid ratio of the boundary nodes, achieving accurate recognition of custom curve boundaries. In addition, curve boundary image and dot methods are utilized to verify IMB-CB. The findings revealed that IMB-CB can accurately identify the boundary, showing an error of less than 1.8% with 500 lattices. Also, the flow in the custom curve boundary and aerodynamic characteristics of the NACA0012 airfoil are calculated and compared to IBM-VC. Results showed that IMB-CB yields lower lift and drag coefficient errors than IBM-VC, with a 1.45% drag coefficient error. In addition, the characteristic curve of IMB-CB is very stable, whereas that of IBM-VC is not. For the moving boundary problem, LBM-IMB-CB with discrete element method (DEM) is capable of accurately simulating the physical phenomena of multi-moving particle flow in complex curved pipelines. This research proposes a new curve boundary recognition method, which can significantly promote the stability and accuracy of fluid-solid interaction simulations and thus has huge applications in engineering.Graphic Abstract
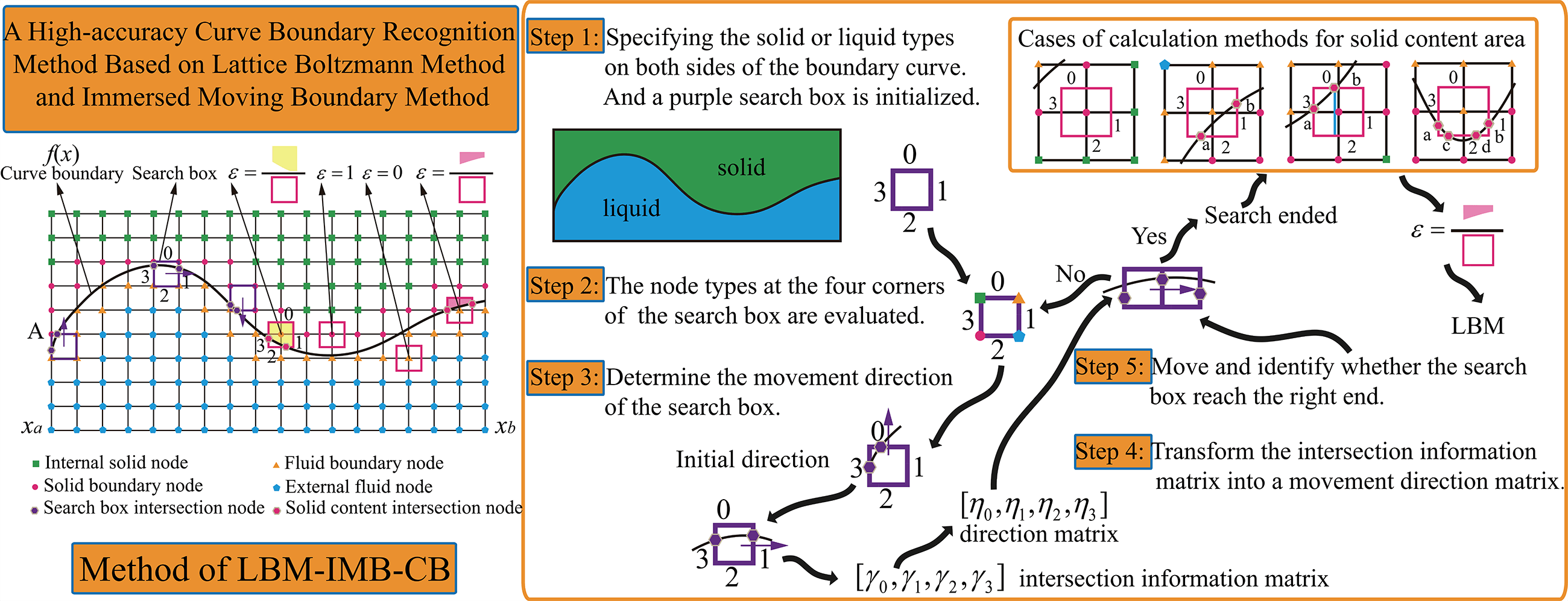
Keywords
Nomenclature
BGK | Bhatnagar-Gross-Krook model |
IBM | Immersion boundary method |
IMB | Immersed moving boundary method |
IBM-VC | IBM based on velocity correction |
IMB-CB | Curve boundary recognition method based on IMB |
LBM | Lattice Boltzmann method |
LBE | Lattice Boltzmann equation |
MRT | Multiple relaxation time |
In various fields, including aircraft engineering [1–3], ocean engineering [4–6], construction engineering [7,8], geological engineering [9,10], and others, coupled computational techniques such as the LBM and IMB are employed to simulate the impact of two-dimensional complex curved solid boundaries on the flow field and facilitates the extraction of information about the flow field within the computational domain, simplifying numerous three-dimensional fluid-structure coupling problems, which effectively diminishes a substantial amount of computational complexity. Examples of such problems include wing flow, ship flow, and bridge pier flow, among others.
There are two popular LBM fluid-solid coupling methods: one is based on the IBM [11,12], defined as IBM-VC in this study, which corrects the velocity of the solid boundary to meet the slip-free boundary condition. IBM-VC can identify complex curve boundaries through boundary node velocity interpolation. IBM-VC was gradually developed, including multiphase flow coupling, moving boundaries, computational efficiency, and others [13–16]. However, IBM-VC is prone to numerical instability [14,15]. Another alternative method is IMB [17], which introduces a solid node ratio covered by solid and weighting function in the additional collision term to calculate the solid boundary more accurately. IMB enables a smooth representation of the solid boundary contour, which many scholars have proved to be a method with high computational accuracy and stability [18–21]. However, when it comes to complex curve boundaries, the existing IMB still suffers from a significant problem related to curve boundaries. The algorithm proposed by Wang et al. [18] is not feasible for achieving custom curve boundary node detection by calculating the distance between nodes and the center of the circle or determining the area number of nodes on the circular particle. In addition, few scholars have investigated the coupling calculation of IMB at curve boundaries and multi-particle flow.
A curve boundary recognition method, IMB-CB, is introduced to promote IMB’s engineering applicability. This IMB-CB, based on IMB, uses the intersection information matrix between the search box and the curve to determine the direction of the search box movement. Then, the search box is moved to identify boundary nodes, and the solid ratio of the boundary nodes is determined to correct the weighting function in the LBM collision operator, achieving accurate recognition of custom curve boundaries. In addition, the study involves error analysis of curve boundary recognition, the influence of grid size on Poiseuille flow, numerical simulation of flow in custom curve boundaries, and flow patterns around a NACA0012 airfoil with scattered data. The calculated results are systematically compared to those obtained through IBM-VC to assess the precision and reliability of the algorithm. Considering the application of IMB-CB in moving boundaries, numerical simulations were conducted for multi-moving particle flow in curved pipelines.
In the Lattice Boltzmann Method, when the system is subjected to body forces
where
The BGK [23] model has better computational efficiency and is commonly used in lattice Boltzmann methods compared to the MRT model [24–26]. The BGK collision operator is expressed as follows:
where
where
In IMB, as proposed by Noble et al. [17], a modified LBE is derived by incorporating an additional collision operator and a weighting function into the pre-existing collision operator. The LBE augmented with additional collision operators can make it equivalent to LBE with body forces. This equivalence can be represented as follows [27]:
Eq. (4) can be understood as the body forces
The solid ratio
The hydrodynamic force and torque exerted on the solid particles, which cover
where
where
In the LBM, the lattice unit nodes are modeled with multi-dimensional and multi-velocity direction models, such as the commonly-used DnQm model, where Dn is n dimensions and Qm represents m velocity directions. This study focuses on the algorithm for recognizing two-dimensional curved boundaries, with particular emphasis on the D2Q9 model selected as the focal point for this investigation, as illustrated in Fig. 1. The fluid computational domain in this model is discretized into a grid with a grid edge length of
Figure 1: D2Q9 model
For the D2Q9 model, the macro fluid density
The theoretical knowledge of IBM-VC based on second-order Lagrangian interpolation for velocity correction can be found in the literature [14]. This study mainly focuses on IMB-CB and compares the numerical simulation results obtained by IMB-CB to IBM-VC.
As the LBM operates within its unique unit system, simulating real-world physical phenomena requires converting actual physical quantities into LBM lattice units. This conversion process is known as establishing dimensionless physical parameters.
Assuming in a computational domain of
Design with
By adhering to the dimensionless steps outlined for the parameters above, accurate numerical simulations corresponding to real physical problems can be attained, thus ensuring numerical stability.
2.2 Curve Boundary Recognition Algorithm of IMB-CB
Fig. 2 indicates that the schematic diagram of the curve boundary model encompasses internal solid nodes, solid boundary nodes, fluid boundary nodes, and external fluid nodes. For the black boundary curve
Figure 2: Schematic diagram of curve boundary recognition method model
(1) The initial step involves specifying the solid or liquid types on both sides of the boundary curve. It is assumed that the nodes in the computational domain above the function
(2) Subsequently, the node types at the four corners of the search box are evaluated. If
(3) In addition, to determine the movement direction of the search box, the first step is to establish its initial direction of movement. Firstly, it is necessary to determine whether the curve boundary
(4) To transform the intersection information matrix into a movement direction matrix
(5) Finally, the search box should be repositioned based on the direction matrix
For the schematic diagram of the curve boundary recognition method model depicted in Fig. 2, the leftmost search box corresponds to the first cycle, whose intersection information matrix is
If the boundary of the given curve is not a continuous function
where
Using search boxes to traverse curve boundaries and ascertain the solid or fluid boundary nodes can increase the algorithm’s time complexity. This study explores the computational complexity involved in identifying curve boundaries in IMB-CB and its computational efficiency. The computational complexity of this curve boundary identification algorithm is linear and is described as follows:
where
If the method proposed by Wang et al. [28] in 2017 for identifying nodes of granular fluid boundaries and solid boundaries, respectively, is improved based on the method in this study to be a customized curve boundary identification method, the time complexity is expressed as follows:
The computational method in this study will reduce the computational complexity by half compared to this kind.
After identifying the node types of the curve boundary, it is necessary to use
Figure 3: Cases of calculation methods for the solid content area of curve boundary
In Fig. 3a case 1, if the intersection matrix consists entirely of 0, and if the node is situated within the solid region,
In order to improve the calculation accuracy of the area A of a curved trapezoid, the Gauss-Legendre formula can be used, given by
where
Table 2 presents the parameters of three area algorithms. By summing up the node areas covered by all solid particles and analyzing the error in their original areas, the resulting error can be expressed as follows:
where
A solid particle with coordinates
Figure 4: Curve of solid ratio error and number
3 Numerical Simulation Results
3.1 Recognition of Custom Curve Boundary
In order to validate the feasibility and accuracy of the curve boundary recognition method and the solid ratio algorithm, an assumption is made regarding the presence of a curve boundary defined by a function
Figure 5: Solid ratio cloud map of curve boundary under different lattice numbers
Fig. 5 indicates that the upper segment of the boundary curve exhibits a solid state, with a corresponding solid ratio of
In order to further investigate the discrepancy between the identified curve boundary and the analytical solution of the curve equation, the curve information of the image is extracted through image processing of the solid ratio cloud map of the curve boundary at various grid resolutions, and the error is computed in comparison to the analytical solution. The specific procedures encompass the following:
Initially, Gaussian blur denoising is applied to the solid ratio cloud map, as derived from Fig. 5. The Sobel convolution kernel is utilized to compute the image’s gradient, and gradient amplitude and direction are determined based on the horizontal and vertical gradient components. Non-maximum suppression is subsequently employed on the gradient amplitude image. Following this, two thresholds are defined to categorize pixels into strong edges, weak edges, or non-edges. Using the connectivity of strong edge pixels, the ultimate edge line is constructed to yield a binary image of edge detection, as depicted in Fig. 5, where pixel values of 0 represent black, while 1 represents white.
Coordinate information is extracted from the white pixels in Fig. 6. Error bars are established at both ends by calculating the mean X-coordinate
Figure 6: Binary image of solid ratio cloud map under different lattice numbers
Fig. 7 indicates that the curve boundary identification points closely align with the analytical solution. In addition, as the number of lattices increases, the range of error bars diminishes. When the number of lattices reaches
Figure 7: Comparison of curve boundary identification points and analytical solutions under different grid numbers
A point method was employed to evaluate the accuracy of calculating the solid ratio on grid points [27]. As illustrated in Fig. 8, for a grid with coordinates (300, 128) at
Figure 8: Dot method for solid ratio
where
In the grid of (300, 128) depicted in Fig. 8, considering
3.2 Poiseuille Flow within Custom Curve Boundaries under Different Lattice Sizes
Different lattice sizes were established based on the curved boundary outlined in Section 3.1 to investigate the algorithm’s adaptability to various grid sizes. Hence, the Poisson blade flow was introduced, and numerical simulation results were juxtaposed with the analytical solution. Set the same computational domain and boundary conditions as in Section 3.1. The fluid density is initialized as
The entrance adopts Poiseuille flow, given by
where
The average velocity of the fluid is determined as follows:
Then, the Zou-He velocity boundary condition is employed to set the velocity at the left entrance. The average velocity of the Poiseuille flow is set to
Figure 9: Y-direction node fluid velocity under different lattices
Fig. 9 indicates that when the inlet is positioned at X = 0, the outcome of
3.3 Numerical Simulation of Flow in Custom Curve Boundary
The accuracy of the curve boundary recognition method based on IMB-CB is verified through the simulation of flow in custom curve boundary, compared to IBM-VC. Set the same computational domain and boundary conditions as in Section 3.2, when
A numerical simulation is performed to obtain the curve boundary simulation results shown in Fig. 10 using IMB-CB in this study. Figs. 10a and 10b respectively display the velocity cloud map and streamline diagram of the curved boundary. These simulation results correspond to the time
Figure 10: Simulation results at curve boundary IMB-CB
In IBM-VC, the same parameters as IMB-CB are set for numerical simulation, where
Figure 11: Simulation results at curve boundary of IBM-VC
where
Fig. 12 illustrates a comparison graph of the
Figure 12: Comparison curve of drag and lift coefficient at the curve boundary
3.4 Numerical Simulation of NACA0012 Airfoil Flow
This study conducts a flow validation using common NACA0012 airfoil data points at a Reynolds number (Re) of 500 to further validate the applicability of IMB-CB for scattered curve data. Since the Reynolds number in the fluid is determined as follows:
where
The Original data points of NACA0012 airfoil are shown in Fig. 13, in which the characteristic length is the wing’s chord length, as
Figure 13: Original data points of NACA0012 airfoil
Utilizing the algorithm outlined in this study, curve boundary identification is executed on the scattered airfoil data of NACA0012, leading to the generation of a solid ratio cloud map, as depicted in Fig. 14. The resultant numerical simulation outcomes are subsequently juxtaposed with those derived from IBM-VC and compared with
Figure 14: Solid ratio cloud map of NACA0012 airfoil
Figure 15: Calculation results of NACA0012 airfoil flow
Figure 16: Comparison chart of drag coefficient around NACA0012 airfoil
Fig. 15 indicates that the Poiseuille flow, originating from the left end of the computational domain, symmetrically bypasses the NACA0012 airfoil, and the wake progressively elongates with time. A comparative assessment of the results obtained via the two methods reveals slight disparities in maximum velocity and vorticity values, while the remainder exhibit high similarity.
Turning attention to the drag coefficient outcomes displayed in Fig. 16, the numerical simulation experienced an unstable flow state during the initial 2.0 s but gradually transitioned into a stable flow state after 2.0 s, following the Poiseuille flow. The IMB-CB and IBM-VC methods employed in this study exhibit fluctuations around the average drag coefficient of 0.1725, a value reported in Imamura et al.’s study [29]. Nevertheless, upon closer examination of the enlarged graph covering the interval from 2.0 to 3.75 s in Fig. 16, IBM-VC manifests more pronounced numerical fluctuations, whereas the calculation results of IMB-CB demonstrate enhanced stability. The average calculation result of IMB-CB from 2.0 to 3.75 s stands at 0.1750, bearing an error of 1.45%, while the average calculation result of IBM-VC is 0.1637, accompanied by an error of −5.101%. The IMB-CB method delivers more precise results than IBM-VC. Due to the airfoil’s symmetry and a 0-degree angle of attack, the average lift coefficient closely aligns with 0. Upon inspecting the average lift coefficient values in Table 2, the average value of the IMB-CB method’s calculation results in this study, ranging from 2.0 to 3.75 s, closely approximates
In summary, the IMB-CB proves proficient in accurately delineating curve boundaries for continuous functions and scattered data, yielding stable numerical calculation results of high precision.
3.5 Multi-Particle Flow in the Custom Complex Curved Pipeline
In order to verify the applicability of IMB-CB in moving boundaries, the discrete element method (DEM) is introduced in this study for calculating the motion of multiple particles within the LBM-IMB-CB framework, aiming to numerically simulate and assess the reliability of IMB-CB [30].
The coupling method flowchart of LBM-DEM-IMB is shown in Fig. 17. First, the fluid domain is discretized into a lattice domain by LBM, and the fluid and particle information are initialized. IMB recognizes custom complex curved boundaries and calculates the weighting function of solid ratio. Then, IMB recognizes particle boundaries and calculates the weighting function of the solid ratio. In addition, collision and migration of LBM distribution functions and update the grid domain’s velocity, density, and vorticity. In addition, the particle fluid force is calculated by IMB. The force of the particles, such as collision forces, gravity, buoyancy, torque, and others, is then calculated. The equations of motion of particles are calculated, and the coordinates of particles are updated accordingly. Judge whether the maximum DEM iteration step is reached. If not, return to continue calculating the particle force and equations of motion. However, if the maximum DEM iteration step is reached, the process proceeds to the next LBM iteration step. Similarly, evaluate whether the maximum LBM iteration step is reached. If not, the calculation proceeds to the IMB step for particle boundary determination. However, if the maximum LBM iteration step is reached, the calculation results are outputted, and the process concludes.
Figure 17: LBM-DEM-IMB-CB method flowchart
The discrete element soft sphere particle contact model in the DEM is equated with the discrete element spring damping dynamic model. When collisions between particles occur, the constitutive model is utilized to solve the contact force. Subsequently, the motion laws of the particles are determined by solving the Lagrange equations, which are given by
where
The normal and tangential contact forces between particles are determined by [31,32]
where
The torque received
where
where
As particle size in complex fluid particle systems often varies, this study generates a more practical and suitable particle size for engineering applications. In order to account for the different effects of particles with varying sizes on fluid flow and particle motion patterns, a random particle radius increment
where
The suitability of the algorithm for a range of customized curve boundaries and moving boundaries is ensured by incorporating more intricate curve boundaries and particles. The curve boundaries are constructed within the computational domain, which has a length of
Figure 18: The solid ratio cloud diagram with multiple particles and curved boundaries
The numerical simulation yields results for
Figure 19: Numerical simulation results of multiple same particles flow in the custom complex curved pipeline
Figure 20: Motion characteristic curve results of multiple particles flow in the custom complex curved pipeline
where
Fig. 19 indicates that along with the motion characteristic curves of multiple particles depicted in Fig. 20, at time
Based on the observations above, the IMB-CB is suitable for accurate coupling calculations of many moving and complex curve boundaries.
This study introduces IMB-CB, a high-accuracy method for recognizing custom curved boundaries, addressing the limitations of existing IMB methods based on solid ratios. IMB-CB identifies custom curved boundaries and employs image processing techniques and dot method to assess recognition errors. Then, the influence of grid size on the Poiseuille flow within the curved boundary was analyzed. Subsequent numerical simulations are conducted for flow analysis around these curved boundaries and the NACA0012 airfoil, with results compared to IBM-VC simulations using second-order Lagrangian velocity interpolation. Finally, IMB-CB is applied to the moving boundary to simulate multiple moving particles in a curved pipeline. The key findings are as follows:
(1) IMB-CB, proposed in this study, achieves minimal recognition errors for curved boundaries compared to analytical solutions. The recognition error decreases as the number of lattices increases, reaching only −1.8% to +0.8% with 500 lattices. This indicates that the method is highly accurate. Compared to the point method, IMB-CB demonstrates higher accuracy in calculating solid ratios.
(2) IMB-CB exhibits a strong fluid-structure coupling effect under different grid sizes. However, simulating LBM still necessitates the selection of an appropriate grid size. By analyzing the simulation results of flow within the custom curve using IMB-CB and IBM-VC, it can be seen that IMB-CB has more numerical stability than the IBM-VC method.
(3) IMB-CB and IBM-VC produce similar numerical simulations for flow around the NACA0012 airfoil. Both methods accurately capture curved boundary effects, which is consistent with previous research. IMB-CB's lift coefficient has an error of
(4) The particle flow in curved pipelines exhibits correct physical phenomena, including a small number of particles remaining in pits, indicating that the LBM-DEM-IMB-CB is suitable for accurate coupling calculations of a large number of moving boundaries and complex curve boundaries.
(1) The conclusions drawn in this study underscore the accuracy of the proposed IMB-CB, which effectively calculates the effects of curved boundaries on flow fields or discrete element particles. IMB-CB finds applicability in various engineering domains such as aviation engineering for aircraft airfoil design, ship engineering for ship streamline design, and construction engineering for force analysis of bridge piers in water flow. In addition, for multi-particle flow in curved pipelines, LBM-DEM-IMB-CB proves suitable for material transportation and blockage analysis, encompassing substances such as pumped concrete, seabed ore, biomass particles, and red blood cells. In short, the IMB-CB and conclusions posited in this article offer broad applicability.
(2) However, the algorithm presented in this study has shortcomings. In high Reynolds number flows with complex curved boundaries, the formation of cavities and bubbles can introduce nonlinear behavior, potentially impacting the accuracy of numerical simulations. The algorithm does not account for the influence of cavities and bubbles on boundary identification and flow. Future research directions can involve integrating bubble dynamics equations proposed by Zhang et al. [34] to simulate the generation and evolution of bubbles or incorporating LBM pseudopotential models (such as the Shan-Doolen model) [35] to simulate gas-liquid-solid three-phase coupling in IMB-CB. This will enable the effects of cavities and bubbles to be investigated using the algorithm presented in this study.
Acknowledgement: The authors are thankful to the anonymous reviewers for improving this article.
Funding Statement: WJD, JYZ, CLC, ZX, and ZGY were supported by the National Natural Science Foundation of China (Grant Number 51705143); the Education Department of Hunan Province (Grant Number 22B0464); and the Postgraduate Scientific Research Innovation Project of Hunan Province (Grant Number QL20230249).
Author Contributions: The authors confirm contribution to the paper as follows: study conception and design: WJD, JYZ; data collection: WJD, JYZ, CLC; analysis and interpretation of results: WJD, ZX; draft manuscript preparation: WJD, ZGY. All authors reviewed the results and approved the final version of the manuscript.
Availability of Data and Materials: The authors declare that the data in the article will be provided as needed.
Conflicts of Interest: The authors declare that they have no conflicts of interest to report regarding the present study.
References
1. Bin IMS, Ahmed MF, Al Saad A. Numerical investigation on the aerodynamic characteristics of a wing for various flow and geometrical parameters. Malaysian J Compos Sci Manuf. 2023;12(1):13–30. [Google Scholar]
2. Wu Z, Guo L. A new approach to aircraft ditching analysis by coupling free surface lattice Boltzmann and immersed boundary method incorporating surface tension effects. Ocean Eng. 2023;286:115559. doi:10.1016/j.oceaneng.2023.115559. [Google Scholar] [CrossRef]
3. Jo BW, Majid T. Aerodynamic analysis of camber morphing airfoils in transition via computational fluid dynamics. Biomimetics. 2022;7(2):52. doi:10.3390/biomimetics7020052. [Google Scholar] [PubMed] [CrossRef]
4. Sener MZ, Aksu E. The effects of head form on resistance performance and flow characteristics for a streamlined AUV hull design. Ocean Eng. 2022;257:111630. doi:10.1016/j.oceaneng.2022.111630. [Google Scholar] [CrossRef]
5. Ashok SG, Rauleder J. NATO generic destroyer moving-ship airwake validation and rotor–ship dynamic interface computations using immersed boundary Lattice–Boltzmann method. In: Vertical Flight Society’s 79th Annual Forum & Technology Display; 2023 May 16–18; West Palm Beach, FL, USA. [Google Scholar]
6. Huang J, Wang Z, Huang W, Yan Q, Miao H, Chen D. USRV: hydrodynamic analysis and design of a novel anti-flow underwater search and rescue vehicle with circuit control and perception system. J Mar Eng Technol. 2024;1:1–11. [Google Scholar]
7. Han K, Feng YT, Owen DRJ. Numerical simulations of irregular particle transport in turbulent flows using coupled LBM-DEM. Comput Model Eng Sci. 2007;18(2):87–100. doi:10.1016/j.chaos.2005.11.041. [Google Scholar] [CrossRef]
8. Hammid S, Naima K, Ikumapayi OM, Kezrane C, Liazid A, Asad J, et al. Overall assessment of heat transfer for a rarefied flow in a microchannel with obstacles using lattice Boltzmann method. Comput Model Eng Sci. 2024;138(1):273–99. doi:10.32604/cmes.2023.028951. [Google Scholar] [CrossRef]
9. Xia M, Zhou H, Jiang C, Cui J, Zeng Y, Chen H. Comparative study of 2D lattice Boltzmann models for simulating seismic waves. Remote Sens. 2024;16(2):285. doi:10.3390/rs16020285. [Google Scholar] [CrossRef]
10. Wang H, Liu H. A mesoscopic coupling scheme for solute transport in surface water using the lattice Boltzmann method. J Hydrol. 2020;588:125062. doi:10.1016/j.jhydrol.2020.125062. [Google Scholar] [CrossRef]
11. Feng ZG, Michaelides EE. The immersed boundary-lattice Boltzmann method for solving fluid-particles interaction problems. J Comput Phys. 2004;195(2):602–28. doi:10.1016/j.jcp.2003.10.013. [Google Scholar] [CrossRef]
12. Dash SM, Lee TS, Huang H. Particle sedimentation in a constricted passage using a flexible forcing IB-LBM scheme. Int J Comput Methods. 2015;12(1):1350095. doi:10.1142/S0219876213500953. [Google Scholar] [CrossRef]
13. Giahi M, Bergstrom D. A critical assessment of the immersed boundary method for modeling flow around fixed and moving bodies. Comput Fluids. 2023;256:105841. doi:10.1016/j.compfluid.2023.105841. [Google Scholar] [CrossRef]
14. Sikdar P, Dash SM, Sinhamahapatra KP. A flexible forcing immersed boundary scheme-based one-step simplified lattice Boltzmann method for two-dimensional fluid-solid interaction problems. Comput Fluids. 2023;265:105996. doi:10.1016/j.compfluid.2023.105996. [Google Scholar] [CrossRef]
15. Shi Y, Liu Y, Xue J, Zhao P, Li S. Study on particles sedimentation in porous media with the immersed boundary-lattice Boltzmann flux solver. Comput Math with Appl. 2023;129:1–10. doi:10.1016/j.camwa.2022.11.012. [Google Scholar] [CrossRef]
16. Xu D, Huang Y. Kinetic modeling of immersed boundary layer for accurate evaluation of local surface stresses and hydrodynamic forces with diffuse interface immersed boundary method. Phys Fluids. 2023;35(4):0436091–16. [Google Scholar]
17. Noble DR, Torczynski JR. A lattice-Boltzmann method for partially saturated computational cells. Int J Mod Phys C. 1998;9(8):1189–201. doi:10.1142/S0129183198001084. [Google Scholar] [CrossRef]
18. Wang M, Feng YT, Owen DRJ, Qu TM. A novel algorithm of immersed moving boundary scheme for fluid-particle interactions in DEM–LBM. Comput Methods Appl Mech Eng. 2019;346:109–25. doi:10.1016/j.cma.2018.12.001. [Google Scholar] [CrossRef]
19. Jiao K, Han D, Li J, Yu B. Numerical simulations of polygonal particles settling within non-Newtonian fluids. Phys Fluids. 2022;34(7):0733151–1. [Google Scholar]
20. Xia M, Deng L, Gong F, Qu T, Feng YT, Yu J. An MPI parallel DEM-IMB-LBM framework for simulating fluid-solid interaction problems. J Rock Mech Geotech Eng. 2024;1:1–14. [Google Scholar]
21. Zeng Z, Fu J, Feng YT, Wang M. Revisiting the empirical particle-fluid coupling model used in DEM-CFD by high-resolution DEM-LBM-IMB simulations: a 2D perspective. Int J Numer Anal Methods Geomech. 2023;47(5):862–79. doi:10.1002/nag.v47.5. [Google Scholar] [CrossRef]
22. McNamara GG, Zanetti G. Use of the Boltzmann equation to simulate lattice-gas automata. In: Lattice gas methods for partial differential equations. Boca Raton: CRC Press; 2019. pp. 289–96. [Google Scholar]
23. Bhatnagar PL, Gross EP, Krook M. A model for collision processes in gases. I. Small amplitude processes in charged and neutral one-component systems. Phys Rev. 1954;94(3):511. doi:10.1103/PhysRev.94.511. [Google Scholar] [CrossRef]
24. d’Humières D. Multiple–relaxation–time lattice Boltzmann models in three dimensions. Philos Trans R Soc London Ser A Math Phys Eng Sci. 2002;360(1792):437–51. doi:10.1098/rsta.2001.0955. [Google Scholar] [PubMed] [CrossRef]
25. Hosseini SA, Karlin IV. Lattice Boltzmann for non-ideal fluids: fundamentals and Practice. Phys Rep. 2023;1030:1–137. doi:10.1016/j.physrep.2023.07.003. [Google Scholar] [CrossRef]
26. Suga K, Ito T. On the multiple-relaxation-time micro-flow lattice Boltzmann method for complex flows. Comput Model Eng Sci. 2011;75(2):141–72. [Google Scholar]
27. Tao S, He Q, Yang X, Luo J, Zhao X. Numerical study on the drag and flow characteristics of porous particles at intermediate Reynolds numbers. Math Comput Simul. 2022;202:273–94. doi:10.1016/j.matcom.2022.06.001. [Google Scholar] [CrossRef]
28. Wang M, Feng YT, Wang Y, Zhao TT. Periodic boundary conditions of discrete element method-lattice Boltzmann method for fluid-particle coupling. Granul Matter. 2017;19:1–10. [Google Scholar]
29. Imamura T, Suzuki K, Nakamura T, Yoshida M. Flow simulation around an airfoil using lattice Boltzmann method on generalized coordinates. In: 42nd AIAA Aerospace Sciences Meeting and Exhibit; 2004 Jan 5–8; Reno, Nevada. pp. 244. [Google Scholar]
30. Wang M, Feng YT, Qu TM, Tao S, Zhao TT. Instability and treatments of the coupled discrete element and lattice Boltzmann method by the immersed moving boundary scheme. Int J Numer Methods Eng. 2020;121(21):4901–19. doi:10.1002/nme.v121.21. [Google Scholar] [CrossRef]
31. Cundall PA, Strack ODL. A discrete numerical model for granular assemblies. Geotechnique. 1979;29(1):47–65. doi:10.1680/geot.1979.29.1.47. [Google Scholar] [CrossRef]
32. Jiang F, Liu H, Chen X, Tsuji T. A coupled LBM-DEM method for simulating the multiphase fluid-solid interaction problem. J Comput Phys. 2022;454:110963. doi:10.1016/j.jcp.2022.110963. [Google Scholar] [CrossRef]
33. Matsumoto M, Nishimura T. Mersenne twister: a 623-dimensionally equidistributed uniform pseudo-random number generator. ACM Trans Model Comput Simul. 1998;8(1):3–30. doi:10.1145/272991.272995. [Google Scholar] [CrossRef]
34. Zhang A, Li SM, Cui P, Li S, Liu YL. A unified theory for bubble dynamics. Phys Fluids. 2023;35(3):0333231–28. [Google Scholar]
35. Shan X, Doolen G. Multicomponent lattice-Boltzmann model with interparticle interaction. J Stat Phys. 1995;81:379–93. doi:10.1007/BF02179985. [Google Scholar] [CrossRef]
Cite This Article
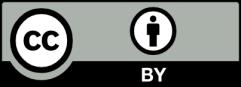
This work is licensed under a Creative Commons Attribution 4.0 International License , which permits unrestricted use, distribution, and reproduction in any medium, provided the original work is properly cited.