Open Access
ARTICLE
Film Flow of Nano-Micropolar Fluid with Dissipation Effect
1 Department of Basic Sciences & Humanities, Faculty of Engineering & Technology, Bahauddin Zakariya University, Multan, Pakistan
2 Department of Mathematics, Hacettepe University, Ankara, Türkiye
3 Department of Medical Research, China Medical University Hospital, China Medical University, Taichung, Taiwan
* Corresponding Authors: Mustafa Turkyilmazoglu. Email: ,
Computer Modeling in Engineering & Sciences 2024, 140(3), 2487-2512. https://doi.org/10.32604/cmes.2024.050525
Received 08 February 2024; Accepted 29 April 2024; Issue published 08 July 2024
Abstract
The physical problem of the thin film flow of a micropolar fluid over a dynamic and inclined substrate under the influence of gravitational and thermal forces in the presence of nanoparticles is formulated. Five different types of nanoparticle samples are accounted for in this current study, namely gold Au, silver Ag, molybdenum disulfide MoS2, aluminum oxide Al2O3, and silicon dioxide SiO2. Blood, a micropolar fluid, serves as the common base fluid. An exact closed-form solution for this problem is derived for the first time in the literature. The results are particularly validated against those for the Newtonian fluid and show excellent agreement. It was found that increasing values of the spin boundary condition and micropolarity lead to a reduction in both the thermal and momentum boundary layers. A quantitative decay in the Nusselt number for a micropolar fluid, as compared to a Newtonian one for all the tested nanoparticles, is anticipated. Gold and silver nanoparticles (i) intensify in the flow parameter as the concentration of nanoparticles increases (ii) yield a higher thermal transfer rate, whereas molybdenum disulfide, aluminum oxide, and silicon dioxide exhibit a converse attitude for both Newtonian and micropolar fluids. The reduction in film thickness for fluid comprising gold particles, as compared to the rest of the nanoparticles, is remarkable.Keywords
Nomenclature
Dimensional Quantities | |
CpCp | Thermal Capacity (JK−1)(JK−1) |
gg | Acceleration due to gravity (ms−2)(ms−2) |
hh | Thickness of the film (m)(m) |
j0j0 | Gyration parameter (m2)(m2) |
kk | Thermal conductivity (Wm−1K−1Wm−1K−1) |
˜p~p | Hydrodynamic pressure (kgm−1s−2)(kgm−1s−2) |
˜S~S | Axial component of spin vector (s−1)(s−1) |
TT | Temperature (K)(K) |
˜u~u | Horizontal component of velocity of fluid (ms−1)(ms−1) |
˜v~v | Vertical component of velocity of fluid (ms−1)(ms−1) |
˜x~x | Abscissa (m)(m) |
˜y~y | Ordinate (m)(m) |
K1K1 | Viscosity parameter |
Nu | Nusselt number |
pp | Hydrodynamic pressure |
Discharge of fluid | |
ReRe | Reynolds number |
SS | Axial component of spin vector |
uu | Horizontal component of velocity of fluid |
vv | Vertical component of velocity of fluid |
xx | Abscissa |
yy | Ordinate |
Greek Symbols | |
α1α1 | Dimensionless flow parameter |
˜β0~β0 | Dimensionless spin boundary parameter |
β1β1 | Dimensionless thermal parameter |
β2β2 | Dimensionless thermal parameter coefficient |
β3β3 | Dimensionless viscous dissipation parameter |
χχ | Vorticity Viscosity coefficient (kgm−1s−1)(kgm−1s−1) |
ϕϕ | Dimensionless Volume fraction |
γγ | Spin gradient coefficient (kgms−1)(kgms−1) |
μμ | Viscosity coefficient (kgm−1s−1)(kgm−1s−1) |
θθ | Dimensionless temperature |
θcθc | Angle of inclination of substrate |
ρρ | Density (kgm−3)(kgm−3) |
Subscripts | |
f | Fluid |
s | Nanoparticles |
nf | Nanofluid |
1.1 Thin Film Flow and Its Significance
Modern Touch of a Classical Flow Problem: Thin films of liquid are pervasive and ubiquitous across both the natural and human-made worlds. Thin film flow describes the spreading of a liquid over a solid substrate (static or dynamic) with a free surface, typically air or gas, at the interface. The flow is primarily driven by external forces, such as a translating or rotating substrate, surface tension, or gravitational force [1,2]. To further explore this, consider examples from nature and technology, including rainwater dribbling down a windowpane, blood coursing through tiny blood vessels, tears trickling down a cheek, suspensions oozing over substrates, and lubricant oil coating rotating ball bearings or other spinning objects [3–6]. Studying thin film flow has wide-ranging applications, aiding understanding of phenomena such as spin-coating, gravure printing, absorption columns, mudslides, dry processes, cooling of microelectronics devices, production of glass/wire, wettability, flow over roads/roofs, solar cells, film evaporation, food industry processes, and heat exchangers [7–11].
One application of thin film flow studies is the analysis of complex liquid flows over intricate substrates. For example, it can be utilized to model the surface-tension-driven flow of incompressible fluids, such as the lining of the lungs [12,13]. The complexity of these flows arises from two main factors:
• Substrate geometry: This can include flexible substrates like leaves [5] or the intricate lining of the lungs [13], as well as other examples like magma streams or tears on a face [14,15].
• Liquid properties: Beyond simple Newtonian fluids like pure water, the flow can involve liquids containing mud, non-Newtonian fluids, or even fluids with nanoparticles [16–20]. This study focuses specifically on micropolar fluids, which have complex molecular structures and include examples like blood, liquid crystals, and colloidal suspensions [21,22]. A deeper exploration of the fascinating properties of micropolar fluids will follow.
Currently, many literature sources exist on both theoretical and experimental studies of thin film flow for Newtonian and non-Newtonian fluids.
1.2 Literature Survey for Newtonian Fluid
The story of thin film flow began in 1916 with the work of Nusselt [23], who presented mathematical equations describing its dynamics. He derived the governing equation for thermal transfer coefficients in condensate thin films, assuming they primarily resist heat transfer. Subsequently, a significant contribution was made in 1974 by Tamir et al. [24], who extended Nusselt’s work by accounting for a constant surface resistance.
While a full historical account is beyond the scope of this discussion due to its substantial length, several noteworthy contributions have explored various aspects of thin film flow:
• Kondic et al. [25] examined thin film liquid on an inclined plane, concluding that the inclination angle significantly alters the wetting behavior.
• O’Brien et al. [26] built upon this work by detailing the implementation of the thin film lubrication approximation and presenting practical examples.
• Wang et al. [27] investigated the influence of channel shape on condensation in thin films within horizontal microchannels.
• Al-Jarrah et al. [28] described the process of film thickness development in microchannels.
• Gatapova et al. [29] analyzed the thermal effects of thin liquid film flow in a channel heated from below.
• Lin et al. [30] reported the dominant role of convective thermal transfer at high Reynolds numbers.
Applications and Experimental Verification: The applications of thin film flow extend beyond theoretical studies. For instance, Mazloomi et al. [31] utilized the lattice-Boltzmann method to investigate thin film flow with thermal sources for surface coating, while Slade [32] explored rivulet formation in thin liquid films. Experimental validation also plays a crucial role in understanding thin film flow. Several studies have focused on this aspect, including:
• Ju et al. [33] performed experiments to probe the droplet impinging on thin film flows and highlighted the characteristics of droplet evolution.
• Charogiannis et al. [34] conducted experiments on thin film flows over inclined glass planes driven by gravity, studying the relationship between the Nusselt number and Reynolds number.
• Wang et al. [35] investigated the thermal influence on thin films under a thermal source environment.
• Budakli [36] experimentally examined thin film flow generated from turbulent gas flow on heated inclined channel walls or under gravitational force.
• Markides et al. [37] conducted experiments to understand the effects of conjugate thermal transfer in thin film flow over electrically heated inclined substrates.
Micropolar Fluids with Nanoparticles: It is well known that nanoparticles in liquids can enhance thermal transfer rates and facilitate other valuable industrial phenomena, such as the instant cooling of electronic chips or rapid water heating in geysers and heat exchangers. Notably, reference [10] was the first to theoretically analyze the hydrodynamic and thermal effects of thin film flow in water containing seven different nanoparticles, even developing a closed-form solution for fluid velocity and temperature.
Contribution and Scope: Inspired by the work in [10], this study extends its analysis to explore other fluid types, such as micropolar fluids, which are relevant to blood, colloidal suspensions, and epoxies. It derives a closed-form solution for the thin film flow of a micropolar fluid containing five different nanoparticles over a thermally heated inclined plane.
1.3 Literature Survey for Non-Newtonian Fluid
In various industries, fluids such as tomato ketchup, honey, blood, colloidal suspensions, and mercury, along with other industrial fluids, do not behave ideally like water. These liquids are categorized as non-Newtonian fluids and require distinct models and constitutive equations to describe their flow behavior. The study of the thin film flow of such non-Newtonian fluids has yielded valuable insights [38–42]. To further explore it, let us examine some recent contributions from 2021 to 2023.
Recent Highlights (2021–2023):
• 2021:
○ Reference [43]: This study compared two methods, homotopy perturbation Elzaki transform and Elzaki decomposition, for analyzing the thin film flow of a third-grade fluid down an inclined plane, favoring the former for its efficacy.
○ Reference [44]: Research on Oldroyd-B ferrofluid containing nanoparticles (Cobalt Ferrite) employed the Runge-Kutta method for a numerical solution.
2022:
○ Reference [45]: Thin film flow of a Williamson fluid was numerically investigated using a homotopy-based scheme with Fractional Calculus, considering bio-convection and microorganism diffusivity.
○ Reference [46]: This study explored the thin film flow of a Casson nanofluid.
○ Reference [47]: This study analyzed viscoplastic Bingham fluid’s thin film flow behavior.
○ Reference [48]: Johnson-Segalmann fluid was the focus of this study on thin film flow.
2023:
○ Reference [49]: A third-grade fluid’s thin film flow characteristics were investigated.
○ Reference [50]: Johnson-Segalmann fluid was tackled in this study on thin film flow.
○ Reference [51]: Second-grade fluid’s thin film flow behavior was analyzed.
○ Reference [52]: Maxwell nanofluid’s thin film flow was explored.
○ Reference [53]: This study focused on Casson nanofluid, further advancing the understanding of thin film flow behavior.
Looking Forward: These examples highlight the active research landscape in non-Newtonian thin film flows. As this field continues to evolve, it offers immense potential for advancements in diverse areas such as bioengineering, microfluidics, and coating technologies.
1.4 Current Study and Micropolar Fluid
As discussed earlier, this study focuses on exploring the hydro- and thermo-dynamical effects of thin film flow in micropolar fluids containing nanoparticles. These fluids hold significant techno-scientific value and exist not only in the laboratory but also in the natural world. Blood, which represents the micropolar nature with its cellular and platelet components, is noted in [54,55]. Colloidal suspensions and liquid crystals, characterized by the presence of colloids, are also part of this category [56]. Rigid-rod epoxies, with their rod-like molecular structure and polymeric suspensions, further expand the diverse scope of micropolar fluids [22,57].
Micropolar fluids are distinguished from Newtonian and non-Newtonian fluids through their ability to sustain body couple and couple stress in addition to conventional body force and Cauchy stress. The Cauchy stress tensor in a micropolar fluid arises from the microscopic, needle-like particles it contains. While Newtonian fluids require only three degrees of freedom for analysis, micropolar fluids necessitate six, reflecting their more complex internal structure.
The literature on the thin film flow of micropolar fluids remains surprisingly sparse. A notable study from Yusuf et al. in 2021 [58] investigated this phenomenon over a static inclined porous substrate, primarily focusing on entropy analysis and employing numerical tools based on the differential transformation method. While this study is noteworthy, it leaves several intriguing questions unanswered, thus hindering a comprehensive understanding of micropolar fluid behavior in real-world situations.
Unanswered Questions and the Research Focus: These unaddressed questions become the driving force for the present research. For instance, how will the fluid respond to a heater within or near the substrate? What happens when the substrate becomes dynamic, moving at a uniform or non-uniform speed? What impact do different nanoparticles, incorporated as additive colloids, have on the flow dynamics? These and many more questions will guide this research, promising valuable insights into the world of micropolar fluids.
The Power of Nanoparticles: Nanoparticles play a vital role in shaping the landscape of modern technology [59–62]. Gold (Au) and silver (Ag) nanoparticles are extensively used in separation science, facilitating efficient separation processes [63–65]. Solutions of gold nanoparticles even reduce thermal resistance by 13% compared to pure water. These nanoparticles also hold vast potential in cancer treatment, where their heat-generating capability aids in photodynamic therapy.
Molybdenum disulfide MoS2MoS2 shines in the field of electronics and logic devices due to its tunable semi-conductive properties. It also serves as a solid lubricant additive in greases and gear oils, enhancing their performance by reducing friction and wear, lowering operating temperatures, and increasing load-carrying capacity. Additionally, MoS2MoS2 helps dampen vibration and noise, leading to reduced energy consumption. Its antioxidant and anti-corrosion properties further contribute to extending the life of lubricants [66–68].
Aluminum oxide (Al2O3Al2O3) nanoparticles are prominent in the medical field as antibacterial agents owing to their low toxicity towards eukaryotic cells [69]. Silicon dioxide (SiO2SiO2) nanoparticles, on the other hand, improve combustion efficiency and reduce emissions in dual-fuel engines. SiO2SiO2-based nanofluids, particularly those in methanol, can increase peak heat release rate and peak pressure by up to 4.3% and 8.6%, respectively, while also enhancing brake-specific fuel consumption and brake thermal efficiency under high loads [70,71].
The Current Study: This study explores the thin film flow of a micropolar fluid (base fluid) containing five distinct types of nanoparticles. This flow occurs over an inclined substrate moving with a uniform speed (U) under the influence of gravity. Section 2 meticulously formulates the governing equations for this scenario. Section 3 then tackles the derivation of a closed-form exact solution for the corresponding boundary value problem. Section 4 shows the obtained results and provides insightful commentary on their implications. Finally, Section 5 wraps up the study by summarizing the essential findings and their significance.
2 Mathematical Formulation and Analysis of the Physical Problem
The governing equations for a steady flow of an incompressible, two-dimensional nano-micropolar fluid model [10,22,56] in the presence of viscous dissipation and in the absence of Joule heating and electromagnetic influences can be written as follows:
∂˜u∂˜x+∂˜v∂˜y=0∂~u∂~x+∂~v∂~y=0(1)
˜u∂˜u∂˜x+˜v∂˜u∂˜y=−gsinθc−1ρnf∂˜p∂˜x+(μnf+χ)ρnf[∂2˜u∂˜x2+∂2˜u∂˜y2]+χρnf∂˜S∂˜y~u∂~u∂~x+~v∂~u∂~y=−gsinθc−1ρnf∂~p∂~x+(μnf+χ)ρnf[∂2~u∂~x2+∂2~u∂~y2]+χρnf∂~S∂~y(2)
˜u∂˜v∂˜x+˜v∂˜v∂˜y=−gcosθc−1ρnf∂˜p∂˜y+(μnf+χ)ρnf[∂2˜v∂˜x2+∂2˜v∂˜y2]+χρnf∂˜S∂˜x~u∂~v∂~x+~v∂~v∂~y=−gcosθc−1ρnf∂~p∂~y+(μnf+χ)ρnf[∂2~v∂~x2+∂2~v∂~y2]+χρnf∂~S∂~x(3)
˜u∂˜S∂˜x+˜v∂˜S∂˜y=γj0ρnf[∂2˜S∂˜x2+∂2˜S∂˜y2]+χj0ρnf[∂˜v∂˜x−∂˜u∂˜y−2˜S]~u∂~S∂~x+~v∂~S∂~y=γj0ρnf[∂2~S∂~x2+∂2~S∂~y2]+χj0ρnf[∂~v∂~x−∂~u∂~y−2~S](4)
(ρCp)nf[˜u∂T∂˜x+˜v∂T∂˜y]=knf[∂2T∂˜x2+∂2T∂˜y2]+μnf[(∂˜v∂˜x+∂˜u∂˜y)2+2(∂˜u∂˜x)2+2(∂˜v∂˜y)2](ρCp)nf[~u∂T∂~x+~v∂T∂~y]=knf[∂2T∂~x2+∂2T∂~y2]+μnf[(∂~v∂~x+∂~u∂~y)2+2(∂~u∂~x)2+2(∂~v∂~y)2](5)
where (˜u,˜v)(~u,~v) represents dimensional velocity components along (˜x,˜y)(~x,~y) directions; ˜p~p is the dimensional pressure; ˜S~S is axial component of the dimensional micro-rotation (spin) vector; jojo is the micro-inertia or gyration parameter; γγ is the spin-gradient coefficient. The density, thermal conductivity, and viscosity coefficient of liquid comprising nanoparticles are correlated as follows:
ρnf=(1−φ)ρf+φρsρnf=(1−φ)ρf+φρs(6a)
knf=kfks+2kf−2φ(kf−ks)ks+2kf+φ(kf−ks)knf=kfks+2kf−2φ(kf−ks)ks+2kf+φ(kf−ks)(6b)
andμnf=(1−φ)−2.5μfandμnf=(1−φ)−2.5μf(6c)
where φφ is the volume fraction or concentration of nanoparticles, whereas the subscripts f and s represent fluid and nanoparticle, respectively; χχ is the vortex viscosity coefficient such that χ+2μ≥0χ+2μ≥0 where χ≥0χ≥0 [56]. It is important to note that χχ will be zero for a Newtonian fluid.
The above equations can be written in dimensionless form as follows:
∂u∂x+∂v∂y=0∂u∂x+∂v∂y=0(7)
Re[u∂u∂x+v∂u∂y]=−γ1sinθc−Re∂p∂x+∇2u+K1∂S∂yRe[u∂u∂x+v∂u∂y]=−γ1sinθc−Re∂p∂x+∇2u+K1∂S∂y(8)
Re[u∂v∂x+v∂v∂y]=−γ1cosθc−Re∂p∂y+∇2v+K1∂S∂xRe[u∂v∂x+v∂v∂y]=−γ1cosθc−Re∂p∂y+∇2v+K1∂S∂x(9)
K3[u∂S∂x+v∂S∂y]=∇2S+K2[∂v∂x−∂u∂y−2S]K3[u∂S∂x+v∂S∂y]=∇2S+K2[∂v∂x−∂u∂y−2S](10)
andβ2[u∂θ∂x+v∂θ∂y]=∇2θ+β3[(∂v∂x+∂u∂y)2+2(∂u∂x)2+2(∂v∂y)2]β2[u∂θ∂x+v∂θ∂y]=∇2θ+β3[(∂v∂x+∂u∂y)2+2(∂u∂x)2+2(∂v∂y)2](11)
by balancing (u,v)=(˜u,˜v)/U,(x,y)=(˜x,˜y)/h,p=˜p/U2ρnf,S=h˜S/U(u,v)=(~u,~v)/U,(x,y)=(~x,~y)/h,p=~p/U2ρnf,S=h~S/U and θ=(T−T0)/ΔTθ=(T−T0)/ΔT. Here ΔTΔT is the temperature difference between the temperature of ambient flow and that of the wall T0T0; ∇2∇2 is the two-dimensional Laplacian operator.Re=Uhρnf(μnf+χ),γ1=h2ρnf(μnf+χ)U,K1=χ(μnf+χ),k2=χh2γ,andk3=j0hUρnfγ(12)
This study considers the nano-micropolar liquid flowing over an inclined substrate with an angle of inclination, as shown in Fig. 1.
Figure 1: Flow configuration
The flow is generated by a pulling roller that is sliding along the x-axis with a constant fluid speed U. Additionally, it is assumed that the thickness (h) of the liquid film is less than the boundary layer thickness. Furthermore, the shear stress exerted by the air on the air-liquid interface is neglected, which will facilitate mathematical calculations. However, due to the influence of gravity (g), the thickness of the liquid representing the air-liquid interface may not remain uniform, and reverse flow may occur. These effects are considered infinitesimal influences on the ambient flow by compensating for the pulling speed of the liquid-carrier film [10]. The liquid considered has specific characteristics: its molecules are either rod- or dumbbell-shaped, exhibiting microrotation and couple stress in addition to usual stress. Such a liquid is typically referred to as a Cosserat or micropolar fluid [56]. Nanoparticles are added to the base liquid, the micropolar liquid, to enhance the thermal transfer rate. Five different types of nanoparticles are used as a test sample. It is assumed that the nanoparticles remain stable during fluid flow. The thermodynamical properties of these elements/compounds are presented in Table 1. Moreover, it is assumed that the liquid film, adhering to the x-axis, is uniformly heated and maintains a temperature of T0 at all times and points of the film. The thermal flux at the air-liquid interface is assumed to be zero [10].
Based on the aforementioned assumptions, Eqs. (8)–(11) deform, ensuring that Eq. (7) is satisfied as follows:
d2udy2+K1dSdy=α1(13)
Redpdy=γ1cosθc(14)
d2Sdy2−2K2S=K2dudy,(15)
and∂2θ∂y2=β1u−β3(dudy)2(16)
whereα1=γ1sinθc,(17a)
andβ1=β2∂θ∂x=constant.(17b)
Furthermore, the boundary conditions can be written as follows:
u=1,θ=0,S=β0(dudy)y=0=˜β0aty=0(18a)
dudy=0,∂θ∂y=0,S=0aty=1(18b)
u=1,θ=0,S=β0(dudy)y=0=˜β0aty=0(18c)
dudy=0,∂θ∂y=0,S=0aty=1(18d)
3 Analytical Solution of the Problem
The aforementioned BVP in Eqs. (13)–(17) contains linear coupled ODE. Hence, it can be integrated exactly using standard methods. The solution for the fluid speed u(y), spin S(y), and temperature θ(y) are summarized as follows:
u(y)=1−K1A2λ1[−1−e2λ1+eλ1y+e2λ1−λ1y]+A3[y22−y](19)
S(y)=A2[eλ1y−e2λ2−λ1y]−α12−K1[y−1],(20)
andθ(y)=β1{−y+y22+A3[y3−y36+y424]}+A2K1β1λ21{2eλ1−e2yλ12}y+1λ1{[(e2λ1−1)y+y22]A2K1β1+[−1−e4λ1+e2yλ1+e2λ1(2−y)]A22K21β32}+β3{[−y3+y22+y33+y412]A23+[2−y]ye2λ1A22K21}+A2K1β1λ31{34−e2λ1−eyλ1+e2yλ14+e(2−y)λ1}+4A2A3K1β3e2λ1λ31{cosh[λ1]−cosh[(y−1)λ1]}+2A2A3K1β3e2λ1λ21{sinh[λ1]−(y−1)sinh[(y−1)λ1]}(21)
In this scenario, the expression for thermal flux is as follows:
ddyθ(y)=β1{−1+y+A3[13−y22+y364]}+A2K1β1λ21{2eλ1−12[2λ1y+1]e2yλ1}+1λ1{[e2λ1−1+y]A2K1β1+[2λ1e2yλ1+2λ1e2λ1(2−y)]A22K21β32}+β3{[−13+y+y2+y33]A23+[1−y]2e2λ1A22K21}+A2K1β1λ21{−eyλ1+e2yλ12−e(2−y)λ1}+4A2A3K1β3e2λ1λ21{sinh[(y−1)λ1]}+2A2A3K1β3e2λ1λ21{−sinh[(y−1)λ1]−λ1(y−1)cosh[(y−1)λ1]}(22)
where
A2=(−˜β0+α1/2−K1)/(e2λ1−1);A3=2α1/(2−K1);λ1=√(2−K1)K2.(23)
If K1=0 and β3=0, then Eqs. (19)–(21) can be reduced to the speed, temperature, and thermal flux for the Newtonian fluid [10].
This section is devoted to presenting some dominant results both in tabular and pictorial forms and commenting on them. The results are based on the exact closed-form solution, Eqs. (19)–(21), of the physical problem under consideration.
In order to validate the calculations herein, Fig. 2b is set for fluid speed if K1=0 in Eq. (19) particularly for the Newtonian fluid. This figure agrees well with Fig. 2b of [10]. This satisfaction provided motivation to study the fluid speed for K1≠0, micropolar fluid, which is shown in Fig. 2a for different values of flow parameter α1.
Figure 2: Fluid-speed profiles for: (a) micropolar fluid; (b) Newtonian fluid for different values of α1 when K1=0.5 with no-spin boundary condition; ˜β0=0; (c) stagnation point study of the speed of fluid; (d) separation point study of speed of fluid
As the flow is generated by moving upward the inclined substrate over it, the fluid is flowing, and the probability of reverse flow downward naturally is dominant. This fact is reflected in Fig. 2a as a negation of speed substrate-rider fluid. This reversal of fluid dominates with the rise in the flow parameter α1. This phenomenon aligns with the physical situation because α1is linearly proportional to the angle of inclination θc of substrate by virtue of Eq. (17a). However, the critical points at which the reverse flow takes place rely on various factors, in which one of the factors is flow parameter α1. The range of flow parameter is α1∈[0,2) for which rider fluid-film moves with the moving substrate for both the Newtonian fluid (K1=0) as well as the micropolar fluid (K1≠0). Nevertheless, the speed of reverse flow increases for the micropolar fluid, which is not surprising because the effects of micropolarity are enhanced, as shown in Figs. 2a and 2b. The threshold value α1=2 is common for both the Newtonian fluid (K1=0) and the micropolar fluid (K1≠0) at which the reverse flow initiates caused by the gravitational force, provided that a no-spin boundary condition ˜β0=0 is imposed. When a spin boundary condition ˜β0≠0 is encountered, then the threshold value of α1 varies such that α1=1 if ˜β0=0.6, as shown in Fig. 3. Additionally, the following facts for the flow attitude are also observed based on Eq. (18) generally and particularly in Table 2.
Figure 3: The effect of spin boundary condition on the fluid speed for micropolar fluid for different values of α1 when K1=1.5 if spin coefficient: (a) ˜β0=0.1; (b) ˜β0=0.6
where
u1=u2+K1˜β0λ1(eλ1+1)(24)
u2=1+α1K1−2+K1α1(eλ1−1)λ1(eλ1+1)(K1−2)(25)
T1=β1[2+2K1−K212+56α1−5K1α1]+α1β3Sinh2(λ1)[−α1Sinh2(λ1)3+K21α14](26)
+3K1α1[K1−2]4+4α21β3K1e2λ1λ31[1−Cosh(λ1)−Coth(λ1)+Cosh(λ1)Coth(λ1)]
+α1β1K1λ21[−12−Coth(λ1)2+2Sinh(λ1)+K14+K1Coth(λ1)4−K1Sinh(λ1)]
+2α21β3K1e2λ1λ21[Sinh(λ1)−Cosh(λ1)]+α1β1K1λ1[32+Coth(λ1)2−3K14−K1Coth(λ1)4]
T2=K21α1β3[−1+K12+˜β0−K1˜β0+K21˜β0]+3β1K1λ31[1−K1+K214]−α1β3K1[K1−2]λ1−K21˜β0β32λ1[4−4K1+K21]
+8α1β3K1e2λ12λ31[K1−2][−1+Cosh(λ1)+Coth(λ1)−Cosh(λ1)Coth(λ1)]
+β1K14λ21[4−4K1+K21][1+Coth(λ1)−4Sinh(λ1)]−2α1β3K1e2λ1λ21[(K1+2)Sinh(λ1)−(K1−2)Cosh(λ1)]
+β1K1λ1[−3−Coth(λ1)+3K1+K1Coth(λ1)−34K21−K21Coth(λ1)4](27)
T3=β1[2+2K1−K212+56α1−5K1α1]+3α1β1K14λ31[K1−2]+α1β1K1λ1[32+Coth(λ1)2−3K14−K1Coth(λ1)4]
+α1β1K1λ21[−12−Coth(λ1)2+2Sinh(λ1)+K14+K1Coth(λ1)4−K1Sinh(λ1)](28)
T4=3β1K1λ31[1−K1+K214]+β1K14λ21[4−4K1+K21][1+Coth(λ1)−4Sinh(λ1)]
+β1K1λ1[−3−Coth(λ1)+3K1+K1Coth(λ1)−34K21−K21Coth(λ1)4]
+β1K1λ1[−3−Coth(λ1)+3K1+K1Coth(λ1)−34K21−K21Coth(λ1)4](29)
F1=β1[−4+4K1−K21+43α1−23K1α1]+α21β3[−43+K21(1−Sinh(2λ1))2Sinh2(λ1)]+α1β1K1λ1[2−K1]
−2α21β3K1Cosh(λ1)λ1[1+Coth(λ1)]+α1β1K1Tanh(λ1)λ21[K1−2]+2α21β3K1eλ1λ21(30)
F2=β1{2−K1−23α1+K1α1λ21[−λ1+Tanh(λ12)]}(31)
F3=α1β3K21Sinh2(λ1)[1−Sinh(2λ1)][K1−2]+[−β1K1λ21+β1K1Tanh(λ12)λ21][4−4K1+K21]−2α21β3K1Cosh(λ1)λ1[1+Coth(λ1)]+˜β02β3K21Sinh2(λ1)[4−4K1+K21][1−Sinh(2λ1)]
+˜β02β3K21Sinh2(λ1)[4−4K1+K21][1−Sinh(2λ1)](32)
F4=K1α1β1λ21[−λ1+Tanh(λ12)][K1−2](33)
(i) For the Newtonian fluid (K1=0), Eq. (19) reduces to
u=1+α1(0.5y2−y),(34)
It coincides with [10], as attempted for the Newtonian fluid. Further if angle of inclination is zero that implies α1=0 then Eqs. (19) and (34) yield
u={1 if ˜β0=01−˜β0K1λ1(e2λ1−1)[e2λ1−λ1y+eλ1y−e2λ1−1] if ˜β0≠0(35)
where λ1=√(2−K1)K2. It can be concluded that umicropolar=uNewtonian=1 if α1=0 with ˜β0=0.
(ii) The fluid speed u decreases with the rise in the micropolarity K1 because of the increase in the colloids of micropolar fluid.
(iii) The fluid speed u also decreases with the spin boundary condition parameter ˜β0.
Since there are no aciculate particles that collide in the Newtonian fluid (K1=0), the spin S=0 for it is as depicted in Fig. 4. The spin S lives with the micropolar fluid (K1≠0) merely, and it controls the microrotation of aciculate particles as they collide about their centroids. Fig. 4 is plotted on the basis of Eq. (20). It shows that the spin S depends upon the micropolarity parameter K1, the flow parameter α1, and the spin boundary parameter ˜β0. The dominancy of rise in the spin is observed in the middle of the substrate because the spin of aciculate particles is linearly proportional to the velocity gradient.
Figure 4: Variation of spin or microrotation of aciculate particles for micropolar fluid for different values of α1 when K1=1.5 if spin coefficient: (a) ˜β0=0; and (b) ˜β0=0.5
Fig. 5 indicates that the spin rises with the micropolarity parameter K1 for all values of the flow parameter α1 and spin boundary parameter ˜β0. Further, the spin is also enhanced with the spin boundary parameter ˜β0. The increase in the spin is also observed as the flow parameter α1increases for all values of the spin boundary parameter ˜β0 and micropolarity parameter K1.
Figure 5: Variation of spin for micropolar fluid for different values of K1 when a1=3 if spin coefficient: (a) ˜β0=0; and (b) ˜β0=0.3
According to Eq. (21), the temperature θ(y) majorly depends upon the flow parameter α1, the micropolarity parameter K1, the viscous dissipation parameter β3, and the spin boundary parameter ˜β0 for the micropolar fluid. The variation of the temperature with respect to the aforementioned parameters is depicted in Fig. 6. Fig. 6c is plotted for comparison purposes for the Newtonian fluid (K1=0). The following can be derived when K1=0 is substituted in Eq. (21):
θ(y)_|(K1=0,β3=0)=[−y+y22+(13y−16y3+124y4)α1]β1(36)
Figure 6: Temperature profile for different values of a1 when K1=0.2, β3=0.0005 for: (a) micropolar fluid, with zero spin boundary condition, ˜β0=0; (b) micropolar fluid, with non-zero Spin boundary condition, ˜β0=0.5; (c) Newtonian fluid
Eq. (36) and Fig. 6c both align with Eq. (12) and Fig. 3a of [10]. Figs. 6a and 6b are plotted for micropolar fluid. These figures show that (i) the temperature increases across the channel as the micropolarity increases, due to the collides in the fluid, the thermal flux rises; (ii) the temperature for micropolar fluid is greater than the temperature for the Newtonian fluid consistently by the increase in the kinetic energy of the aciculate particles in the micropolar fluid; (iii) the temperature θ increases with spin boundary parameter ˜β0 because spin boundary condition reduces the thermal transfer rate; (iv) in contrast, the temperature θ decreases with flow parameter α1 for both micropolar and Newtonian fluids as it is expected due to the rise in the gravitational force; (v) θ_|Micropolar=θ_|Newtonian=β1[y22−y] for α1=0 with ˜β0=0=β3 for all points of the channel; (vi) If α1=0 with ˜β0≠0,β3≠0 then the expression for temperature for micropolar fluid will differ slightly as:
4θ(y,α1=0)=−2(y−2){2β1−K21˜β20β3sinh2[λ1]}−4yK1˜β0β1λ1−2K21˜β20β3(−1+e2λ1)2λ1{1+e4λ1−e−2(y−2)λ1−e2yλ1}+2(coth[λ1]−1)K1˜β0β1λ31{−1+e2λ1−e−(y−2)λ1+eyλ1−2yλ1eλ1}+2(coth[λ1]−1)K1˜β0β12λ31{1−2y2λ21+e2yλ1(−1+2yλ1)}(37)
The variation of temperature at the air-nano micropolar fluid interface is important techno-scientifically. It is examined by focusing on variation of θ(1). Its influence on flow and thermal parameters is presented in Table 3 quantitatively, while respective expressions are given in Table 2.
These tables show clearly the comparison between micropolar and Newtonian fluids. Table 3 depicts that the temperature θ(1) at air-liquid interface increases as the micropolarity effect K1 of the micropolar fluid rises for all values of fluid and geometric parameters namely β3 and ˜β0.
The thermal transfer rate is significant in engineering and technology. It is studied in terms of the Nusselt number Nu, which is defined as [10]:
Nu=2∫10udy∫10uθdy(dθdy)y=0(38)
If Eqs. (19)–(21) are substituted in Eq. (38), then one yields
Nu=R0R1R2(39)
where
R0=23(3−A3+6eλ1A2K1(−Sinh[λ1]+Cosh[λ1]λ1)λ21)(40a)
R1=13λ21(−3(−1−2e2λ1+e4λ1)A22K21β3λ21+((−3+A3)β1−A23β3)λ21+3A2K1((−1+eλ1)β1(1+eλ1(−1+λ1)+λ1)+2e2λ1A3β3(Sinh[λ1]−Cosh[λ1]λ1)))(40b)
R2=15040λ61(−16((105+A3(−84+17A3))β1+(21−8A3)A23β3)λ61)+840e3λ1A32K31β3λ21(24Sinh[λ1]+λ1(−24Cosh[λ1]−9Sinh[λ1]+7Sinh[3λ1]+4Cosh[λ1]λ1(−3Cosh[2λ1]+2λ1)))
+7A22K21λ1(20β1(77+63λ1−12λ31+36eλ1(−4+λ21)+6e2λ1(30−3λ1+λ31)+9e4λ1(7−9λ1+2λ31)7+4e3λ1(−44+3λ1(8+3λ1)))+3β3(40e2λ1λ31(3Sinh[2λ1]−6Cosh[2λ1]λ1+4λ21)+A3(−900eλ1(−1+e4λ1)+λ1(−15+15e3λ1(128+Cosh[λ1]+112Cosh[2λ1]+Sinh[λ1])−30(1−8eλ1+e4λ1+8e5λ1)λ1+40(1+e4λ1)λ31−64e2λ1λ41))))
+21A2K1(20β1λ21(21+21λ1−8λ31+12eλ1(−2+λ21)+e2λ1(3−3λ1+2λ31))+16A23β3(−15(−1+eλ1)(1+eλ1)(2+5eλ1)+λ1(15(2+5eλ1)(1+e2λ1)+λ1(15+5λ1−λ31+5e3λ1(−3+λ1)(1+λ1)−5eλ1(−1+λ1)(3+λ1)−e2λ1(15−5λ1+λ31))))+A3(240eλ1β3λ21(3+3λ1+λ21−e2λ1(3+(−3+λ1)λ1))+β1(450+435λ1−140λ31+64λ51−20eλ1(24−12λ21+5λ41)−3e2λ1(−10+λ1(5+2λ1(5−5λ1+3λ31))))))(41)
A2=˜β0+2A3e2λ1−1(42a)
A3=2α12−K1(42b)
The results related to the Nusselt number are shown quantitatively in Table 4 while qualitatively in Fig. 7a. Through Table 4 and Fig. 7a, it is observed that Nu depends upon the flow parameter α1 significantly. It varies in three intervals or stages. Nu=6 is an initial value when α1=0, which is in agreement with the literature [72] for the Newtonian fluid (K1=0). It can be seen that the commencing value of Nu=6 for micropolar fluids for all values of K1 and shown in Fig. 7b. Its justification is that: R0, R1, and R2 given as above equations, at α1=0 are identical for Newtonian and micropolar fluids. Afterward, the Nusselt number rises till its amplitude (a couple of sample data are presented in Table 4). This peak value of Nu varies with the micropolarity effects. In the second stage, Nu decays strictly till a critical value of α1 This critical point varies with the micropolarity, as shown in Fig. 7. Finally, the Nusselt number increases monotonically till α1→∞.
Figure 7: Variation of the Nusselt number Nu with flow parameter α1 f ˜β0=0.001 when: (a) without viscous dissipation β3=0; (b) with viscous dissipation β3=0.2. Note that K1=0 represents the Newtonian fluid
4.4 Influence of Nanoparticles
Let us define the following two important ratios to highlight the influences of nanoparticles [10]:
νr=μnfρfρnfμfandkr=knfkf.(43)
There are five different types of samples of nanoparticles in order to examine in this current study, namely gold Au, silver Ag, molybdenum disulfide MoS2, aluminum oxide Al2O3, and silicon dioxide SiO2 with a common base fluid in the blood, which is a micropolar fluid. The variation of relative viscosity νr and relative thermal conductivity kr with respect to the concentration of nanoparticles φ for both Newtonian and a micropolar fluids, respectively, are displayed in Figs. 8 and 9. Almost analogous trend is observed for both the fluids but a decrease in νr and an increase in kr are significant for a micropolar fluid. Furthermore, the gold and silver nanoparticles intensify in the flow parameter whereas the molybdenum disulfide, the aluminum oxide, and the silicon dioxide do decline in contribution in the flow parameter with the increase in the concentration of nanoparticles because νr relays on the kinematics viscosity of the medium for both the Newtonian and the micropolar fluids as shown in Figs. 8a and 9a. Moreover, the enhancement in thermal transfer rate due to the presence of nanoparticles is physically expected, as demonstrated in Figs. 8b and 9b for both micropolar and Newtonian fluids. Notably, gold and silver achieve a higher transfer rate compared to molybdenum disulfide, aluminum oxide, and silicon dioxide due to their thermal conductivity in both base fluids (micropolar/Newtonian). Another significant observation concerns the influence of nanoparticles on film thickness during flow on an inclined substrate, as the film thickness is inversely proportional to the relative viscosity [10]. The reduction in film thickness in a nano-liquid containing gold particles, as compared to other nanoparticles, is noticeable due to the higher density or kinematic viscosity.
Figure 8: Effects of the concentration of nanoparticles ϕ on: (a) flow parameter νr; (b) thermal parameter Kr, for the Newtonian fluid (pure water) as a base fluid
Figure 9: Effects of the concentration of nanoparticles ϕ on: (a) flow parameter νr; (b) thermal parameter Kr, for the micropolar fluid (blood) as a base fluid
The concentration of nanoparticles φ also affects the fluid speed and temperature. The fluid- speed u versus the concentration of the nanoparticles φ at the middle of the channel is examined, and sample results are displayed in Figs. 10a and 10b for Newtonian and micropolar fluids as base liquids, respectively. Consistently, an almost similar trend is observed on umid for both fluids. However, the quantitative decay of umid for a micropolar fluid is compared to a Newtonian one for all test nanoparticles. The temperature at the middle of the channel θmid exhibits analogous behavior to umid, as shown in Fig. 11.
Figure 10: Midpoint channel effects of the concentration of nanoparticles ϕ on fluid speed u if ˜β0=0.5 for the base fluid as: (a) the Micropolar fluid (blood); (b) the Newtonian fluid (water)
Figure 11: Midpoint channel effects of the concentration of nanoparticles ϕ on temperature θ for the base fluid as: (a) the Micropolar fluid (blood); (b) the Newtonian fluid (water)
In this study, the thin film flow of a micropolar fluid containing nanoparticles over an inclined substrate under the influence of viscous dissipation and gravitational force was formulated and examined theoretically. An exact solution to the formulated boundary value problem was derived for the first time. The variation of physical quantities, fluid speed, temperature, and microrotation/spin was analyzed based on the solution. The results are displayed in graphical and tabular form and compared to existing results from the literature for the Newtonian fluid as a particular case of the current study.
The results showed that the fluid velocity declines with increasing values of spin boundary condition and micropolarity due to the increase in colloids in the micropolar medium. Additionally, micropolarity with spin leads to an enhanced temperature field compared to a Newtonian fluid. Furthermore, it is observed that the Nusselt number rises until it reaches an amplitude that varies with micropolarity effects. Mid velocities eventually reveal a quantitative decay in a micropolar fluid compared to a Newtonian one for all tested nanoparticles, with similar behavior in temperature at the mid-channel. Gold and silver nanoparticles (i) intensify the flow parameters as the concentration of nanoparticles increases (ii) yield a higher thermal transfer rate, whereas molybdenum disulfide, aluminum oxide, and silicon dioxide exhibit the opposite behavior; this holds true for both Newtonian and micropolar fluids. Moreover, a reduction in film thickness for nano-liquid-containing gold particles, compared to other nanoparticles, is observed. Finally, it is important to state that this work is new and original.
Acknowledgement: The authors are extremely grateful to the editor of the journal and all four reviewers for very useful comments and suggestions.
Funding Statement: The authors did not receive any funding support from any source. It is self-financed solely.
Author Contributions: AAS: Conceptualization, Modeling, Calculations, Writing, Software; MT: Potential review, Keen validation, Proof reading, Collection of useful data, Valuable suggestions.
Availability of Data and Materials: MatLab was used to simulate the results. Upon reasonable request.
Conflicts of Interest: The authors have no conflict of interest to report regarding the present study.
References
1. Bertozzi AL, Pugh M. The lubrication approximation for thin viscous films: regularity and long-time behavior of weak solutions. Commun Pure Appl Math. 1996 Feb;49(2):85–123. doi:10.1002/(ISSN)1097-0312. [Google Scholar] [CrossRef]
2. Roy RV, Roberts AJ, Simpson ME. A lubrication model of coating flows over a curved substrate in space. J Fluid Mech. 2002 Mar;454:235–61. doi:10.1017/S0022112001007133. [Google Scholar] [CrossRef]
3. Dutta A, Som SK, Das PK. Film condensation of saturated vapor over horizontal noncircular tubes with progressively increasing radius of curvature drawn in the direction of gravity. J Heat Transfer. 2004 Dec 1;126(6):906–14. doi:10.1115/1.1798891. [Google Scholar] [CrossRef]
4. Taherzadeh D. Mechanics and substrate transport of moving biofilm structures (Ph.D. Thesis). Technische Universität München: Germany; 2011. [Google Scholar]
5. Howell PD, Robinson J, Stone HA. Gravity-driven thin-film flow on a flexible substrate. J Fluid Mech. 2013 Oct;732:190–213. doi:10.1017/jfm.2013.404. [Google Scholar] [CrossRef]
6. Liu Y, Itoh M, Kyotoh H. Flow of a falling liquid curtain onto a moving substrate. Fluid Dyn Res. 2017 Jul 27;49(5):055501. doi:10.1088/1873-7005/aa7ee8. [Google Scholar] [CrossRef]
7. Girtan M. Future solar energy devices. In: SpringerBriefs in applied sciences and technology. Cham: Springer; 2018. p. 1–104. doi:10.1007/978-3-319-67337-0. [Google Scholar] [CrossRef]
8. Thiele U. Recent advances in and future challenges for mesoscopic hydrodynamic modelling of complex wetting. Colloids Surf A: Physicochem Eng Asp. 2018 Sep 20;553:487–95. doi:10.1016/j.colsurfa.2018.05.049. [Google Scholar] [CrossRef]
9. Kreder MJ, Daniel D, Tetreault A, Cao Z, Lemaire B, Timonen JV, et al. Film dynamics and lubricant depletion by droplets moving on lubricated surfaces. Phys Rev X. 2018 Sep 4;8(3):031053. [Google Scholar]
10. Turkyilmazoglu M. Nanoliquid film flow due to a moving substrate and heat transfer. Eur Phys J Plus. 2020 Oct 6;135(10):781. doi:10.1140/epjp/s13360-020-00812-y. [Google Scholar] [CrossRef]
11. Girtan M. On the electrical and photoelectrical properties of CH3NH3PBI3 perovskites thin films. Sol Energy. 2020 Jan 1;195:446–53. doi:10.1016/j.solener.2019.11.096. [Google Scholar] [CrossRef]
12. Halpern D, Grotberg JB. Fluid-elastic instabilities of liquid-lined flexible tubes. J Fluid Mech. 1992 Nov;244:615–32. doi:10.1017/S0022112092003227. [Google Scholar] [CrossRef]
13. Heil M, White JP. Airway closure: surface-tension-driven non-axisymmetric instabilities of liquid-lined elastic rings. J Fluid Mech. 2002 Jul;462:79–109. doi:10.1017/S0022112002008613. [Google Scholar] [CrossRef]
14. Qayyum M, Ismail F, Sohail M, Imran N, Askar S, Park C. Numerical exploration of thin film flow of MHD pseudo-plastic fluid in fractional space: utilization of fractional calculus approach. Open Phys. 2021 Nov 26;19(1):710–21. doi:10.1515/phys-2021-0081. [Google Scholar] [CrossRef]
15. Adesanya SO, Onanaye AS, Adeyemi OG, Rahimi-Gorji M, Alarifi IM. Evaluation of heat irreversibility in couple stress falling liquid films along heated inclined substrate. J Clean Prod. 2019 Dec 1;239:117608. doi:10.1016/j.jclepro.2019.117608. [Google Scholar] [CrossRef]
16. Waini I, Ishak A, Pop I. Radiative and magnetohydrodynamic micropolar hybrid nanofluid flow over a shrinking sheet with Joule heating and viscous dissipation effects. Neural Comput Appl. 2022 Mar;34(5):3783–94. doi:10.1007/s00521-021-06640-0. [Google Scholar] [CrossRef]
17. Bilal M, Ramzan M, Siddique I, Sajjad A. Magneto-micropolar nanofluid flow through the convective permeable channel using Koo-Kleinstreuer–Li model. J Magn Magn Mater. 2023 Jan 1;565:170288. doi:10.1016/j.jmmm.2022.170288. [Google Scholar] [CrossRef]
18. Rajkumar D, Reddy AS, Narayana PS, Jagadeshkumar K, Chamkha AJ. Pulsating magnetohydrodynamic flow of Fe3O4-blood based micropolar nanofluid between two vertical porous walls with Cattaneo-Christov heat flux and entropy generation. J Magn Magn Mater. 2023 Apr 1;571:170564. doi:10.1016/j.jmmm.2023.170564. [Google Scholar] [CrossRef]
19. Bayareh M. An overview of non-Newtonian nanofluid flow in macro-and micro-channels using two-phase schemes. Eng Anal Bound Elem. 2023 Mar 1;148:165–75. doi:10.1016/j.enganabound.2022.12.033. [Google Scholar] [CrossRef]
20. Nabwey HA, Rahbar F, Armaghani T, Rashad AM, Chamkha AJ. A comprehensive review of non-newtonian nanofluid heat transfer. Symmetry. 2023 Jan 29;15(2):362. doi:10.3390/sym15020362. [Google Scholar] [CrossRef]
21. Siddiqui AA, Lakhtakia A. Steady electro-osmotic flow of a micropolar fluid in a microchannel. Proc R Soc A: Math, Phys Eng Sci. 2009 Feb 8;465(2102):501–22. doi:10.1098/rspa.2008.0354. [Google Scholar] [CrossRef]
22. Siddiqui AA, Turkyilmazoglu M. Slit flow and thermal analysis of micropolar fluids in a symmetric channel with dynamic and permeable. Int Commun Heat Mass Transf. 2022 Mar 1;132:105844. doi:10.1016/j.icheatmasstransfer.2021.105844. [Google Scholar] [CrossRef]
23. Nusselt W. Die oberflachenkondensation des wasserdamphes. VDI-Zs. 1916;60:541. [Google Scholar]
24. Tamir A, Taitel Y. Nusselt condensation with interfacial resistance. Chem Eng J. 1974 Jan 1;7(3):245–7. doi:10.1016/0300-9467(74)85038-0. [Google Scholar] [CrossRef]
25. Kondic L, Diez J. Pattern formation in the flow of thin films down an incline: constant flux configuration. Phys Fluids. 2001 Nov 1;13(11):3168–84. doi:10.1063/1.1409965. [Google Scholar] [CrossRef]
26. O’Brien SBG, Schwartz LW. Theory and modeling of thin film flows. 2002. Available from: https://api.semanticscholar.org/CorpusID:11512995. [Accessed 2023]. [Google Scholar]
27. Wang H, Rose JW. Film condensation in horizontal microchannels: effect of channel shape. Int Conf Nanochannels, Microchannels, Minichannels. 2005 Jan 1;41855:729–35. [Google Scholar]
28. Al-Jarrah JA, Khadrawi AF, Al-Nimr MA. Film condensation on a vertical microchannel. Int Commun Heat Mass Transf. 2008 Nov 1;35(9):1172–6. doi:10.1016/j.icheatmasstransfer.2008.07.003. [Google Scholar] [CrossRef]
29. Gatapova EY, Kabov OA. Shear-driven flows of locally heated liquid films. Int J Heat Mass Transf. 2008 Sep 1;51(19–20):4797–810. [Google Scholar]
30. Lin TS, Kondic L, Filippov A. Thin films flowing down inverted substrates: three-dimensional flow. Phys Fluids. 2012;24:022105. doi:10.1063/1.3682001. [Google Scholar] [CrossRef]
31. Mazloomi A, Moosavi A. Thin liquid film flow over substrates with two topographical features. Phys Rev E. 2013 Feb 26;87(2):022409. doi:10.1103/PhysRevE.87.022409. [Google Scholar] [CrossRef]
32. Slade DR. Gravity-driven thin liquid films: rivulets and flow dynamics. England, UK: University of Leeds; 2013. [Google Scholar]
33. Ju W, Wu Y, Lin S, Zhao F, Tan S. Visual experimental study of droplet impinging on liquid film and analysis of droplet evolution characteristics. Exp Comput Multiph Flow. 2022;4(3):212–20. doi:10.1007/s42757-020-0081-3. [Google Scholar] [CrossRef]
34. Charogiannis A, Markides CN. Spatiotemporally resolved heat transfer measurements in falling liquid-films by simultaneous application of planar laser-induced fluorescence (PLIFparticle tracking velocimetry (PTV) and infrared (IR) thermography. Exp Therm Fluid Sci. 2019 Oct 1;107:169–91. doi:10.1016/j.expthermflusci.2018.11.001. [Google Scholar] [CrossRef]
35. Wang XF, Hrnjak PS, Elbel S, Jacobi AM, He MG. Heat transfer performance for a falling-film on horizontal flat tubes. J Heat Transf. 2013 Jul 1;135(7):072901. doi:10.1115/1.4023689. [Google Scholar] [CrossRef]
36. Budakli M. Hydrodynamics and heat transfer in gas-driven liquid film flows (Ph.D. Thesis). Institute of Technical Thermodynamics, Technische Universitat Darmstadt: Germany; 2015. [Google Scholar]
37. Markides CN, Mathie R, Charogiannis A. An experimental study of spatiotemporally resolved heat transfer in thin liquid-film flows falling over an inclined heated foil. Int J Heat Mass Transf. 2016 Feb 1;93:872–88. doi:10.1016/j.ijheatmasstransfer.2015.10.062. [Google Scholar] [CrossRef]
38. Miladinova S, Lebon G, Toshev E. Thin-film flow of a power-law liquid falling down an inclined plate. J Non-Newton Fluid Mech. 2004 Sep 20;122(1–3):69–78. [Google Scholar]
39. Siddiqui AM, Mahmood R, Ghori QK. Some exact solutions for the thin film flow of a PTT fluid. Phys Lett A. 2006 Aug 14;356(4–5):353–6. [Google Scholar]
40. Siddiqui AM, Mahmood R, Ghori QK. Homotopy perturbation method for thin film flow of a fourth grade fluid down a vertical cylinder. Phys Lett A. 2006 Apr 3;352(4–5):404–10. [Google Scholar]
41. Siddiqui AM, Mahmood R, Ghori QK. Homotopy perturbation method for thin film flow of a third grade fluid down an inclined plane. Chaos, Solitons Fractals. 2008 Jan 1;35(1):140–7. doi:10.1016/j.chaos.2006.05.026. [Google Scholar] [CrossRef]
42. Alam MK, Siddiqui AM, Rahim MT, Islam S, Avital EJ, Williams JJ. Thin film flow of magnetohydrodynamic (MHD) pseudo-plastic fluid on vertical wall. Appl Math Comput. 2014 Oct 15;245:544–56. [Google Scholar]
43. Singh J, Kumar D, Baleanu D. A hybrid analytical algorithm for thin film flow problem occurring in non-Newtonian fluid mechanics. Ain Shams Eng J. 2021 Jun 1;12(2):2297–302. doi:10.1016/j.asej.2020.09.006. [Google Scholar] [CrossRef]
44. Tlili I, Samrat SP, Sandeep N, Nabwey HA. Effect of nanoparticle shape on unsteady liquid film flow of MHD Oldroyd-B ferrofluid. Ain Shams Eng J. 2021 Mar 1;12(1):935–41. doi:10.1016/j.asej.2020.06.007. [Google Scholar] [CrossRef]
45. Abdal S, Siddique I, Salamat N, Ud Din IS. Nano-bio-film flow of Williamson fluid due to a non-linearly extending/contracting surface with non-uniform physical properties. Waves Random Complex Media. 2022 Nov 16;1–9. doi:10.1080/17455030.2022.2146233. [Google Scholar] [CrossRef]
46. Alali E, Megahed AM. MHD dissipative Casson nanofluid liquid film flow due to an unsteady stretching sheet with radiation influence and slip velocity phenomenon. Nanotechnol Rev. 2022 Jan 15;11(1):463–72. doi:10.1515/ntrev-2022-0031. [Google Scholar] [CrossRef]
47. Esmaeili E, Grassia P, Ulloa CAT. Squeeze film flow of viscoplastic Bingham fluid between non-parallel plates. J Non-Newton Fluid Mech. 2022 Jul 1;305:104817. doi:10.1016/j.jnnfm.2022.104817. [Google Scholar] [CrossRef]
48. Qayyum M, Ismail F, Ali Shah SI, Sohail M, El-Zahar ER, Gokul KC. An application of homotopy perturbation method to fractional-order thin film flow of the Johnson-Segalman fluid model. Math Probl Eng. 2022 Feb 23;2022:1–7. [Google Scholar]
49. Hassan MH, Al-Saif AS. A mathematical model for the velocity of thin film flow of a third grade fluid down in an inclined plane. J Adv Res Fluid Mech Therm Sci. 2023 Feb 13;102(1):140–52. doi:10.37934/arfmts. [Google Scholar] [CrossRef]
50. Ashraf H, Sabir S, Siddiqui AM, Rehman HU, Almutairi B, Shah NA. Heat transfer analysis of temperature dependent viscosity Johnson-Segalman fluid film flow on a vertical heated belt. Case Stud Therm Eng. 2023 Sep 1;49:103362. doi:10.1016/j.csite.2023.103362. [Google Scholar] [CrossRef]
51. Mahesh T, Panda S. Longwave modeling of thin film flow of a generalized second-grade fluid down a slanted plate. Int J Non Linear Mech. 2023 Mar 1;149:104327. doi:10.1016/j.ijnonlinmec.2022.104327. [Google Scholar] [CrossRef]
52. Mandal S, Shit GC. Entropy analysis of unsteady magnetohydrodynamic thin liquid film flow of Maxwell nanofluids with variable fluid properties. Mater Chem Phys. 2023 Jan 1;293:126890. doi:10.1016/j.matchemphys.2022.126890. [Google Scholar] [CrossRef]
53. Vanitha GP, Shobha KC, Mallikarjun BP, Mahabaleshwar US, Bognár G. Casson nanoliquid film flow over an unsteady moving surface with time-varying stretching velocity. Sci Rep. 2023 Mar 11;13(1):4074. doi:10.1038/s41598-023-30886-4. [Google Scholar] [CrossRef]
54. Turk MA, Sylvester ND, Ariman T. On pulsatile blood flow. Trans Soc Rheol. 1973 Mar 1;17(1):1–21. doi:10.1122/1.549295. [Google Scholar] [CrossRef]
55. Misra JC, Ghosh SK. A mathematical model for the study of interstitial fluid movement vis-a-vis the non-Newtonian behaviour of blood in a constricted artery. Comput Math Appl. 2001 Mar 1;41(5–6):783–811. [Google Scholar]
56. Eringen AC. Microcontinuum field theories: II. fluent media. London, UK: Springer Science & Business Media; 2001 Mar 30. [Google Scholar]
57. Papautsky I, Brazzle J, Ameel T, Frazier AB. Laminar fluid behavior in microchannels using micropolar fluid theory. Sens Actuators A: Phys. 1999 Mar 9;73(1–2):101–8. [Google Scholar]
58. Yusuf TA, Kumar RN, Prasannakumara BC, Adesanya SO. Irreversibility analysis in micropolar fluid film along an incline porous substrate with slip effects. Int Commun Heat Mass Transf. 2021 Jul 1;126:105357. doi:10.1016/j.icheatmasstransfer.2021.105357. [Google Scholar] [CrossRef]
59. Ahmad S, Naveed Khan M, Ali R, Ahmad Lone S. Analysis of free bioconvective flow of hybrid nanofluid induced by convectively heated cone with entropy generation. Mod Phys Lett B. 2024 Jan 30;38(03):2450015. doi:10.1142/S0217984924500155. [Google Scholar] [CrossRef]
60. Ali L, Ali B, Iqbal T. Finite element analysis of the impact of particles aggregation on the thermal conductivity of nanofluid under chemical reaction. Waves Random Complex Media. 2023 Feb 4;1–21. [Google Scholar]
61. Shah SA, Ahammad NA, Ali B, Guedri K, Awan AU, Gamaoun F, et al. Significance of bio-convection, MHD, thermal radiation and activation energy across Prandtl nanofluid flow: a case of stretching cylinder. Int Commun Heat Mass Transf. 2022 Oct 1;137:106299. doi:10.1016/j.icheatmasstransfer.2022.106299. [Google Scholar] [CrossRef]
62. Abbas N, Rehman KU, Shatanawi W, Abodayeh K. Mathematical model of temperature-dependent flow of power-law nanofluid over a variable stretching Riga sheet. Waves Random Complex Media. 2022 Aug 18;1–8. doi:10.1080/17455030.2022.2111029. [Google Scholar] [CrossRef]
63. Stfytfkora D, Kašička V, Mikšík I, Řezanka P, Záruba K, Matějka P, et al. Application of gold nanoparticles in separation sciences. J. Sep. Sci. 2010 Feb;33(3):372–87. doi:10.1002/jssc.v33:3. [Google Scholar] [CrossRef]
64. Cabuzu D, Cirja A, Puiu R, Mihai Grumezescu A. Biomedical applications of gold nanoparticles. Curr Top Med Chem. 2015 Aug 1;15(16):1605–13. doi:10.2174/1568026615666150414144750. [Google Scholar] [CrossRef]
65. Zaaroura I, Harmand S, Carlier J, Toubal M, Fasquelle A, Nongaillard B. Thermal performance of self-rewetting gold nanofluids: application to two-phase heat transfer devices. Int J Heat Mass Transf. 2021 Aug 1;174:121322. doi:10.1016/j.ijheatmasstransfer.2021.121322. [Google Scholar] [CrossRef]
66. Hao D, Yang R, Yi N, Cheng H. Highly sensitive piezoresistive pressure sensors based on laser-induced graphene with molybdenum disulfide nanoparticles. Sci China Technol Sci. 2021 Nov;64(11):2408–14. doi:10.1007/s11431-021-1899-9. [Google Scholar] [CrossRef]
67. Luo SW, Alimujiang A, Cui J, Chen TT, Balamurugan S, Zheng JW, et al. Molybdenum disulfide nanoparticles concurrently stimulated biomass and β-carotene accumulation in Dunaliella salina. Bioresour Technol. 2021 Jan 1;320:124391. doi:10.1016/j.biortech.2020.124391. [Google Scholar] [CrossRef]
68. Gudkov SV, Burmistrov DE, Smirnova VV, Semenova AA, Lisitsyn AB. A mini review of antibacterial properties of Al2O3 nanoparticles. Nanomater. 2022 Jul 30;12(15):2635. doi:10.3390/nano12152635. [Google Scholar] [CrossRef]
69. Wei J, He C, Lv G, Zhuang Y, Qian Y, Pan S. The combustion, performance and emissions investigation of a dual-fuel diesel engine using silicon dioxide nanoparticle additives to methanol. Energy. 2021 Sep 1;230:120734. doi:10.1016/j.energy.2021.120734. [Google Scholar] [CrossRef]
70. Shuai C, Yang F, Shuai Y, Peng S, Chen S, Deng Y, et al. Silicon dioxide nanoparticles decorated on graphene oxide nanosheets and their application in poly(l-lactic acid) scaffold. J Adv Res. 2023 Jun 1;48:175–90. doi:10.1016/j.jare.2022.08.017. [Google Scholar] [CrossRef]
71. Nield DA, Kuznetsov AV. Forced convection in a parallel-plate channel occupied by a nanofluid or a porous medium saturated by a nanofluid. Int J Heat Mass Transf. 2014 Mar 1;70:430–3. doi:10.1016/j.ijheatmasstransfer.2013.11.016. [Google Scholar] [CrossRef]
72. Ilyas SU, Pendyala R, Marneni N. Stability of nanofluids. In: Engineering applications of nanotechnology: from energy to drug delivery. Springer International Publishing; 2017. p. 1–31. [Google Scholar]
73. Khan MR, Puneeth V, Alqahtani AM, Alhazmi SE, Beinane SA, Shutaywi M, et al. Numerical simulation and mathematical modeling for heat and mass transfer in MHD stagnation point flow of nanofluid consisting of entropy generation. Sci Rep. 2023 Apr 19;13(1):6423. doi:10.1038/s41598-023-33412-8. [Google Scholar] [CrossRef]
Cite This Article
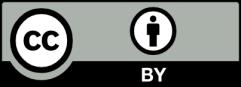
This work is licensed under a Creative Commons Attribution 4.0 International License , which permits unrestricted use, distribution, and reproduction in any medium, provided the original work is properly cited.