Open Access
ARTICLE
A Multiscale Reliability-Based Design Optimization Method for Carbon-Fiber-Reinforced Composite Drive Shafts
1 Yangtze Delta Region Institute (Huzhou), University of Electronic Science and Technology of China, Huzhou, 313001, China
2 Huzhou Key Laboratory of Green Energy Materials and Battery Cascade Utilization, Huzhou College, Huzhou, 313000, China
3 SAIC Motor Corporation Limited Passenger Vehicle Co., Shanghai, 201804, China
4 School of Mechanical and Electrical Engineering, University of Electronic Science and Technology of China,
Chengdu, 611731, China
* Corresponding Authors: Huile Zhang. Email: ; Zhonglai Wang. Email:
(This article belongs to the Special Issue: Structural Design and Optimization)
Computer Modeling in Engineering & Sciences 2024, 140(2), 1975-1996. https://doi.org/10.32604/cmes.2024.050185
Received 30 January 2024; Accepted 01 April 2024; Issue published 20 May 2024
Abstract
Carbon fiber composites, characterized by their high specific strength and low weight, are becoming increasingly crucial in automotive lightweighting. However, current research primarily emphasizes layer count and orientation, often neglecting the potential of microstructural design, constraints in the layup process, and performance reliability. This study, therefore, introduces a multiscale reliability-based design optimization method for carbon fiber-reinforced plastic (CFRP) drive shafts. Initially, parametric modeling of the microscale cell was performed, and its elastic performance parameters were predicted using two homogenization methods, examining the impact of fluctuations in microscale cell parameters on composite material performance. A finite element model of the CFRP drive shaft was then constructed, achieving parameter transfer between microscale and macroscale through Python programming. This enabled an investigation into the influence of both micro and macro design parameters on the CFRP drive shaft’s performance. The Multi-Objective Particle Swarm Optimization (MOPSO) algorithm was enhanced for particle generation and updating strategies, facilitating the resolution of multi-objective reliability optimization problems, including composite material layup process constraints. Case studies demonstrated that this approach leads to over 30% weight reduction in CFRP drive shafts compared to metallic counterparts while satisfying reliability requirements and offering insights for the lightweight design of other vehicle components.Keywords
Cite This Article
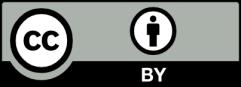
This work is licensed under a Creative Commons Attribution 4.0 International License , which permits unrestricted use, distribution, and reproduction in any medium, provided the original work is properly cited.