Open Access
ARTICLE
Numerical Analysis of Perforation during Hydraulic Fracture Initiation Based on Continuous–Discontinuous Element Method
1 School of Civil and Transportation Engineering, Hebei University of Technology, Tianjin, 300401, China
2 Key Laboratory for Mechanics in Fluid Solid Coupling Systems, Institute of Mechanics, Chinese Academy of Sciences, Beijing, 100190, China
3 School of Civil Engineering and Architecture, Zhejiang Sci-Tech University, Hangzhou, 310018, China
4 Jinyun Institute, Zhejiang Sci-Tech University, Lishui, 321400, China
* Corresponding Authors: Lixiang Wang. Email: ; Yiming Zhang. Email:
(This article belongs to the Special Issue: Multiscale, Multifield, and Continuum-Discontinuum Analysis in Geomechanics )
Computer Modeling in Engineering & Sciences 2024, 140(2), 2103-2129. https://doi.org/10.32604/cmes.2024.049885
Received 21 January 2024; Accepted 14 March 2024; Issue published 20 May 2024
Abstract
Perforation is a pivotal technique employed to establish main flow channels within the reservoir formation at the outset of hydraulic fracturing operations. Optimizing perforation designs is critical for augmenting the efficacy of hydraulic fracturing and boosting oil or gas production. In this study, we employ a hybrid finite-discrete element method, known as the continuous–discontinuous element method (CDEM), to simulate the initiation of post-perforation hydraulic fractures and to derive enhanced design parameters. The model incorporates the four most prevalent perforation geometries, as delineated in an engineering technical report. Real-world perforations deviate from the ideal cylindrical shape, exhibiting variable cross-sectional profiles that typically manifest as an initial constriction followed by an expansion, a feature consistent across all four perforation types. Our simulations take into account variations in perforation hole geometries, cross-sectional diameters, and perforation lengths. The findings show that perforations generated by the 39g DP3 HMX perforating bullet yield the lowest breakdown pressure, which inversely correlates with increases in sectional diameter and perforation length. Moreover, this study reveals the relationship between breakdown pressure and fracture degree, providing valuable insights for engineers and designers to refine perforation strategies.Keywords
Cite This Article
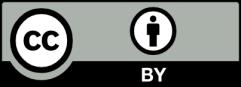
This work is licensed under a Creative Commons Attribution 4.0 International License , which permits unrestricted use, distribution, and reproduction in any medium, provided the original work is properly cited.