Open Access
ARTICLE
Effect of Modulus Heterogeneity on the Equilibrium Shape and Stress Field of α Precipitate in Ti-6Al-4V
1 Materials Genome Institute, Shanghai University, Shanghai, 200444, China
2 School of Materials Science and Engineering, Harbin Institute of Technology, Shenzhen, 518055, China
3 Shanghai Frontier Science Center of Mechanoinformatics, Shanghai University, Shanghai, 200444, China
4 Zhejiang Laboratory, Hangzhou, 311100, China
* Corresponding Author: Rongpei Shi. Email:
(This article belongs to the Special Issue: Computational Design and Modeling of Advanced Composites and Structures)
Computer Modeling in Engineering & Sciences 2024, 140(1), 1017-1028. https://doi.org/10.32604/cmes.2024.048797
Received 19 December 2023; Accepted 07 February 2024; Issue published 16 April 2024
Abstract
For media with inclusions (e.g., precipitates, voids, reinforcements, and others), the difference in lattice parameter and the elastic modulus between the matrix and inclusions cause stress concentration at the interfaces. These stress fields depend on the inclusions’ size, shape, and distribution and will respond instantly to the evolving microstructure. This study develops a phase-field model concerning modulus heterogeneity. The effect of modulus heterogeneity on the growth process and equilibrium state of the α plate in Ti-6Al-4V during precipitation is evaluated. The α precipitate exhibits strong anisotropy in shape upon cooling due to the interplay of the elastic strain and interfacial energy. The calculated orientation of the habit plane using the homogeneous modulus of α phase shows the smallest deviation from that of the habit plane observed in the experiment, compared to the case where the homogeneous modulus of β phase is adopted. In addition, the equilibrium volume of α phase within the system using homogeneous β modulus exhibits the largest dependency on the applied stresses. The stress fields across the α/β interface are further calculated under the assumption of modulus heterogeneity and compared to those using homogeneous modulus of either α or β phase. This study provides an essential theoretical basis for developing mechanics models concerning systems with heterogeneous structures.Keywords
The close correlation of microstructure with material properties makes it crucial in research and development [1]. A microstructure is usually composed of precipitates distributed in a solid matrix. The difference between the precipitates and matrix in lattice parameters and crystal structure generates elastic strain in both and, in turn, influences the morphology of the microstructure (e.g., shape and spatial distribution of the precipitates) and thermodynamic driving forces and kinetics of the precipitation process [2]. In principle, the contributions of the elastic interactions can be calculated by formulating a total elastic energy functional. A variational derivative of the total energy with respect to the microstructural variables (degrees of freedom) gives rise to the local elastic driving force for the evolution of the microstructure [3].
The elasticity solutions for a given microstructure are primarily deduced in the framework established by Eshelby for coherent precipitates [4]. A precipitate is considered coherent if the crystal lattice planes extend continuously from precipitate to matrix. Mathematically, the condition is specified as a continuation of the displacements across the precipitate-matrix boundaries. Eshelby’s approach was generalized and extended to treat multi-particle problems with realistic features in various microstructural studies [5–7]. Simplifications in numerical microstructure simulations are often made under an approximation of homogeneous elasticity, ignoring the variation in the elastic modulus among phases. The choice of the now uniform elastic modulus is taken on the major phase. Elastic assumptions using homogeneous modulus of the matrix phase (e.g., the parent phase for precipitation, the base alloys for composites, and others) have been used in systems for slip transmission across the
Since the elastic moduli generally differ between precipitates and matrix and among the precipitates (the difference also includes a rotation of the elastic modulus tensors, such as in a polycrystal), the solution for such problems can be much more complex in anisotropic solids and becomes very costly in microstructure simulations. Moulinec et al. proposed an iterative numerical method based on Fast Fourier Transforms and the Green function to investigate the effective properties of periodic composites [13], and an augmented Lagrangian method was further employed to treat elastically inhomogeneous solids, including voided materials and power-law materials [14]. The generalization of the phase-field micro elasticity theory [15] to elastically inhomogeneous systems [16–18] enables a general treatment of the elasticity problem in an elastically anisotropic and inhomogeneous solid, where coherent precipitates can take arbitrary shapes, populations, and spatial distributions. Ultimately, one can want to know how the homogeneous elasticity approximation can affect the elasticity solution (e.g., energy and stress) and the microstructure.
With the formulation, numerical calculations are performed for coherent inclusion under various approximations of elastic modulus, and the effects of the simplification on the elastic energy and stress distribution are investigated. The Ti-6Al-4V (wt.%), one of the earliest commercial titanium alloys, exhibits excellent and balanced mechanical and chemical performance [19–21] and is chosen as the working system. Ti-6Al-4V is a typical two-phase (
2.1 Phase-Field Model with Inhomogeneous Elastic Modulus for Precipitate and Matrix Phases
The current work is based on the three-dimensional multi-phase-field model for an elastically and structurally inhomogeneous system [24] of Ti-6Al-4V alloy. Within the framework of the multi-phase-field model, 12 order parameters are employed to distinguish
This study explores the equilibrium shape of
where
For a system with the assumption that the precipitate and matrix have identical elastic constants
where
where
The concurrent evolution of composition and structure follow the general form of Cahn-Hilliard diffusion equation and the Allen-Cahn equation in the multi-phase-field model by Steinbach et al. [27]. When orientations of precipitates are considered, the governing equations in this work is derived as:
where
Using
Case-I: homogeneous modulus of the matrix phase:
Case-II: homogeneous modulus of the precipitate phase:
Case-III: inhomogeneous modulus that takes the corresponding values of modulus according to the order parameter:
During the numerical process of finding the equilibrium elastic state, the elastic moduli concerning the two phases should not be set strictly equal due to the iteration of Eq. (5), where
3.1 Equilibrium Shape of
During the
Figure 1: Growth of
Figure 2: (a–c) Equilibrium shape of
Figure 3: (a) Volume development during
External stresses can also alter the equilibrium shape or size of
3.2 Stress Fields of
Due to the mismatch of lattice parameters of
Figure 4: Distribution of stress component
For titanium alloy with
Figure 5: (a–c) Evolving stress component
However, when the homogeneous modulus assumption is applied, the stress field can be distinct from that with the inhomogeneous modulus shown above due to the variation in
Figure 6: Stresses across the
The assumption of the elastic modulus for elastically and structurally inhomogeneous solids is critical to the phase transformation process and the corresponding elastic state. The effect of modulus heterogeneity on the equilibrium shape and stress field of grown
• The equilibrium shape (e.g., habit plane and size) of
• The local stresses across the
• In general, for transformation from the phase of high symmetry structure to the phase of low symmetry, using elastic modulus of the low symmetry phase would give more accurate calculation results on the equilibrium morphology of the precipitate.
Acknowledgement: The authors gratefully thank Prof. Yunzhi Wang at the Ohio State University for many useful discussions on the phase transformation model for titanium alloys.
Funding Statement: DQ would like to thank the financial support from the National Key Research and Development Program of China under Grant No. 2022YFB3707803, the Key Research Project of Zhejiang Laboratory under Grant No. 2021PE0AC02, and the National Natural Science Foundation of China under Grant No. U2230102. RS acknowledges the open research fund of Songshan Lake Materials Laboratory (2021SLABFK06) and Guangdong Basic and Applied Basic Research Foundation (2024A1515011873).
Author Contributions: The authors confirm their contribution to the paper as follows: study conception and design: R. Shi; analysis and interpretation of results: D. Qiu; draft manuscript preparation: D. Qiu. All authors reviewed the results and approved the final version of the manuscript.
Availability of Data and Materials: The raw/processed data and materials required to reproduce these findings cannot be shared at this time as the data and materials also form part of an ongoing study.
Conflicts of Interest: The authors declare that they have no conflicts of interest to report regarding the present study.
References
1. Semiatin, S. L. (2020). An overview of the thermomechanical processing of α/β titanium alloys: Current status and future research opportunities. Metallurgical and Materials Transactions A, 51(6), 2593–2625. [Google Scholar]
2. Mao, H., Zeng, C., Zhang, Z., Shuai, X., Tang, S. (2023). The effect of lattice misfits on the precipitation at dislocations: Phase-field crystal simulation. Materials, 16(18), 6307. [Google Scholar] [PubMed]
3. Chen, L. Q. (2002). Phase-field models for microstructure evolution. Annual Review of Materials Research, 32(1), 113–140. [Google Scholar]
4. Eshelby, J. D. J. (1957). The determination of the elastic field of an ellipsoidal inclusion, and related problems. Proceedings of the Royal Society of London Series A: Mathematical and Physical Sciences, 241, 376–396. [Google Scholar]
5. Yanase, K., Ju, J. W. (2012). Effective elastic moduli of spherical particle reinforced composites containing imperfect interfaces. International Journal of Damage Mechanics, 21(1), 97–127. [Google Scholar]
6. Yao, Y., Chen, J., Liu, J., Chen, S. (2022). An alternative constitutive model for elastic particle-reinforced hyperelastic matrix composites with explicitly expressed Eshelby tensor. Composites Science and Technology, 221, 109343. [Google Scholar]
7. Jiang, D. (2023). Eshelby’s inclusion and inhomogeneity problem. In: Jiang, D. (Ed.Continuum micromechanics: Theory and application to multiscale tectonics, pp. 221–243. Cham: Springer International Publishing. [Google Scholar]
8. Zhao, P., Shen, C., Savage, M. F., Li, J., Niezgoda, S. R. et al. (2019). Slip transmission assisted by Shockley partials across α/β interfaces in Ti-alloys. Acta Materialia, 171, 291–305. [Google Scholar]
9. Ke, X., Wang, D., Ren, X., Wang, Y. (2020). Polarization spinodal at ferroelectric morphotropic phase boundary. Physical Review Letters, 125(12), 127602. [Google Scholar] [PubMed]
10. Zhang, T., Wang, D., Wang, Y. (2020). Novel transformation pathway and heterogeneous precipitate microstructure in Ti-alloys. Acta Materialia, 196, 409–417. [Google Scholar]
11. Qiu, D., Zhao, P., Trinkle, D. R., Wang, Y. (2020). Stress-dependent dislocation core structures leading to non-schmid behavior. Materials Research Letters, 9(3), 134–140. [Google Scholar]
12. Qiu, D., Zhao, P., Wang, Y. (2021). A general phase-field framework for predicting the structures and micromechanical properties of crystalline defects. Materials & Design, 209, 109959. [Google Scholar]
13. Moulinec, H., Suquet, P. (1998). A numerical method for computing the overall response of nonlinear composites with complex microstructure. Computer Methods in Applied Mechanics and Engineering, 157(1–2), 69–94. [Google Scholar]
14. Michel, J. C., Moulinec, H., Suquet, P. (2000). A computational method based on augmented Lagrangians and fast Fourier transforms for composites with high contrast. Computer Modeling in Engineering & Sciences, 1(2), 79–88. [Google Scholar]
15. Khachaturyan, A. G. (1983). Theory of structural transformations in solids. New York: John Wiley & Sons. [Google Scholar]
16. Shen, Y., Li, Y., Li, Z., Wan, H., Nie, P. (2009). An improvement on the three-dimensional phase-field microelasticity theory for elastically and structurally inhomogeneous solids. Scripta Materialia, 60(10), 901–904. [Google Scholar]
17. Wang, Y. U., Jin, Y. M., Cuitiño, A. M., Khachaturyan, A. G. (2001). Phase field microelasticity theory and modeling of multiple dislocation dynamics. Applied Physics Letters, 78(16), 2324–2326. [Google Scholar]
18. Wang, Y. U., Jin, Y. M., Khachaturyan, A. G. (2002). Phase field microelasticity theory and modeling of elastically and structurally inhomogeneous solid. Journal of Applied Physics, 92(3), 1351–1360. [Google Scholar]
19. Barba, D., Alabort, C., Tang, Y. T., Viscasillas, M. J., Reed, R. C. et al. (2020). On the size and orientation effect in additive manufactured Ti-6Al-4V. Materials & Design, 186, 108235. [Google Scholar]
20. Nguyen, H. D., Pramanik, A., Basak, A. K., Dong, Y., Prakash, C. et al. (2022). A critical review on additive manufacturing of Ti-6Al-4V alloy: Microstructure and mechanical properties. Journal of Materials Research and Technology, 18, 4641–4661. [Google Scholar]
21. Zhang, Y., Ma, G. R., Zhang, X. C., Li, S., Tu, S. T. (2017). Thermal oxidation of Ti-6Al-4V alloy and pure titanium under external bending strain: Experiment and modelling. Corrosion Science, 122, 61–73. [Google Scholar]
22. Liu, J., Zhang, K., Yang, Y., Wang, H., Zhu, Y. et al. (2022). Grain boundary α-phase precipitation and coarsening: Comparing laser powder bed fusion with as-cast Ti-6Al-4V. Scripta Materialia, 207, 114261. [Google Scholar]
23. Shi, R., Choudhuri, D., Kashiwar, A., Dasari, S., Wang, Y. et al. (2022). α phase growth and branching in titanium alloys. Philosophical Magazine, 102(5), 389–412. [Google Scholar]
24. Shi, R., Wang, Y. (2013). Variant selection during α precipitation in Ti-6Al–4V under the influence of local stress—A simulation study. Acta Materialia, 61(16), 6006–6024. [Google Scholar]
25. Cahn, J. W., Hilliard, J. E. (1958). Free energy of a nonuniform system. I. Interfacial free energy. The Journal of Chemical Physics, 28(2), 258–267. [Google Scholar]
26. Zhang, F., Chen, S. L., Chang, Y., Ma, N., Wang (2007). Development of thermodynamic description of a pseudo-ternary system for multicomponent Ti64 alloy. Journal of Phase Equilibria and Diffusion, 28, 115–120. [Google Scholar]
27. Steinbach, I., Pezzolla, F., Nestler, B., Seeßelberg, M., Prieler, R. et al. (1996). A phase field concept for multiphase systems. Physica D: Nonlinear Phenomena, 94(3), 135–147. [Google Scholar]
28. Burgers, W. G. (1934). On the process of transition of the cubic-body-centered modification into the hexagonal-close-packed modification of zirconium. Physica, 1(7), 561–586. [Google Scholar]
29. Ledbetter, H., Ogi, H., Kai, S., Kim, S., Hirao, M. (2004). Elastic constants of body-centered-cubic titanium monocrystals. Journal of Applied Physics, 95(9), 4642–4644. [Google Scholar]
30. Mills, M., Hou, D., Suri, S., Viswanathan, G. (1997). Orientation relationship and structure of alpha/beta interfaces in conventional titanium alloys. Boundaries & Interfaces in Materials: The David A. Smith Symposium, pp. 295–301. [Google Scholar]
31. Lee, H. K., Ju, J. W. (2007). A three-dimensional stress analysis of a Penny-shaped crack interacting with a spherical inclusion. International Journal of Damage Mechanics, 16(3), 331–359. [Google Scholar]
Cite This Article
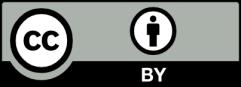
This work is licensed under a Creative Commons Attribution 4.0 International License , which permits unrestricted use, distribution, and reproduction in any medium, provided the original work is properly cited.