Open Access
ARTICLE
Dynamic Response of Foundations during Startup of High-Frequency Tunnel Equipment
1 College of Civil and Transportation Engineering, Shenzhen University, Shenzhen, 518060, China
2 State Key Laboratory of Intelligent Geotechnics and Tunnelling, Shenzhen University, Shenzhen, 518060, China
3 Key Laboratory of Coastal Urban Resilient Infrastructures of Ministry of Education, Shenzhen University, Shenzhen, 518060, China
4 Underground Polis Academy, Shenzhen University, Shenzhen, 518060, China
5 Shenzhen Key Laboratory of Green, Efficient and Intelligent Construction of Underground Metro Station, Shenzhen University, Shenzhen, 518060, China
* Corresponding Author: Mingwei Hu. Email:
(This article belongs to the Special Issue: Structural Design and Optimization)
Computer Modeling in Engineering & Sciences 2024, 140(1), 821-844. https://doi.org/10.32604/cmes.2024.048392
Received 06 December 2023; Accepted 08 February 2024; Issue published 16 April 2024
Abstract
The specialized equipment utilized in long-line tunnel engineering is evolving towards large-scale, multifunctional, and complex orientations. The vibration caused by the high-frequency units during regular operation is supported by the foundation of the units, and the magnitude of vibration and the operating frequency fluctuate in different engineering contexts, leading to variations in the dynamic response of the foundation. The high-frequency units yield significantly diverse outcomes under different startup conditions and times, resulting in failure to meet operational requirements, influencing the normal function of the tunnel, and causing harm to the foundation structure, personnel, and property in severe cases. This article formulates a finite element numerical computation model for solid elements using three-dimensional elastic body theory and integrates field measurements to substantiate and ascertain the crucial parameter configurations of the finite element model. By proposing a comprehensive startup timing function for high-frequency dynamic machines under different startup conditions, simulating the frequency and magnitude variations during the startup process, and suggesting functions for changes in frequency and magnitude, a simulated startup schedule function for high-frequency machines is created through coupling. Taking into account the selection of the transient dynamic analysis step length, the dynamic response results for the lower dynamic foundation during its fundamental frequency crossing process are obtained. The validation checks if the structural magnitude surpasses the safety threshold during the critical phase of unit startup traversing the structural resonance region. The design recommendations for high-frequency units’ dynamic foundations are provided, taking into account the startup process of the machine and ensuring the safe operation of the tunnel.Keywords
Cite This Article
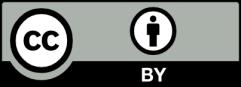
This work is licensed under a Creative Commons Attribution 4.0 International License , which permits unrestricted use, distribution, and reproduction in any medium, provided the original work is properly cited.