Open Access
ARTICLE
Probabilistic-Ellipsoid Hybrid Reliability Multi-Material Topology Optimization Method Based on Stress Constraint
1 College of Mechanical and Electrical Engineering, Qingdao University, Qingdao, 266071, China
2 National Engineering Research Center for Intelligent Electrical Vehicle Power System, Qingdao University, Qingdao, 266071, China
* Corresponding Author: Qinghai Zhao. Email:
(This article belongs to the Special Issue: Structural Design and Optimization)
Computer Modeling in Engineering & Sciences 2024, 140(1), 757-792. https://doi.org/10.32604/cmes.2024.048016
Received 25 November 2023; Accepted 11 January 2024; Issue published 16 April 2024
Abstract
This paper proposes a multi-material topology optimization method based on the hybrid reliability of the probability-ellipsoid model with stress constraint for the stochastic uncertainty and epistemic uncertainty of mechanical loads in optimization design. The probabilistic model is combined with the ellipsoidal model to describe the uncertainty of mechanical loads. The topology optimization formula is combined with the ordered solid isotropic material with penalization (ordered-SIMP) multi-material interpolation model. The stresses of all elements are integrated into a global stress measurement that approximates the maximum stress using the normalized p-norm function. Furthermore, the sequential optimization and reliability assessment (SORA) is applied to transform the original uncertainty optimization problem into an equivalent deterministic topology optimization (DTO) problem. Stochastic response surface and sparse grid technique are combined with SORA to get accurate information on the most probable failure point (MPP). In each cycle, the equivalent topology optimization formula is updated according to the MPP information obtained in the previous cycle. The adjoint variable method is used for deriving the sensitivity of the stress constraint and the moving asymptote method (MMA) is used to update design variables. Finally, the validity and feasibility of the method are verified by the numerical example of L-shape beam design, T-shape structure design, steering knuckle, and 3D T-shaped beam.Keywords
Cite This Article
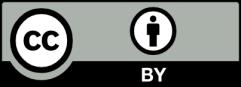
This work is licensed under a Creative Commons Attribution 4.0 International License , which permits unrestricted use, distribution, and reproduction in any medium, provided the original work is properly cited.