Open Access
ARTICLE
Reduced-Order Observer-Based LQR Controller Design for Rotary Inverted Pendulum
1 College of Engineering, China University of Petroleum-Beijing at Karamay, Karamay, 834000, China
2 School of Electrical Engineering and Information, Southwest Petroleum University, Chengdu, 610500, China
* Corresponding Author: Tianpeng Huang. Email:
Computer Modeling in Engineering & Sciences 2024, 140(1), 305-323. https://doi.org/10.32604/cmes.2024.047899
Received 21 November 2023; Accepted 06 February 2024; Issue published 16 April 2024
Abstract
The Rotary Inverted Pendulum (RIP) is a widely used underactuated mechanical system in various applications such as bipedal robots and skyscraper stabilization where attitude control presents a significant challenge. Despite the implementation of various control strategies to maintain equilibrium, optimally tuning control gains to effectively mitigate uncertain nonlinearities in system dynamics remains elusive. Existing methods frequently rely on extensive experimental data or the designer’s expertise, presenting a notable drawback. This paper proposes a novel tracking control approach for RIP, utilizing a Linear Quadratic Regulator (LQR) in combination with a reduced-order observer. Initially, the RIP system is mathematically modeled using the Newton-Euler-Lagrange method. Subsequently, a composite controller is devised that integrates an LQR for generating nominal control signals and a reduced-order observer for reconstructing unmeasured states. This approach enhances the controller’s robustness by eliminating differential terms from the observer, thereby attenuating unknown disturbances. Thorough numerical simulations and experimental evaluations demonstrate the system’s capability to maintain balance below 50 Hz and achieve precise tracking below 1.4 rad, validating the effectiveness of the proposed control scheme.Keywords
The Rotary Inverted Pendulum (RIP), also known as the Furuta Pendulum, has been extensively studied by researchers since its introduction in 1992 [1,2]. The RIP system, characterized by high instability, multivariate, nonlinear, and underactuated properties, is regarded as an ideal benchmark system for the training and validation of new control strategies in the field of engineering control. The study of dynamic modelling and equilibrium state control algorithms for the RIP systems is crucial in advanced technological sectors, especially in aerospace industry. Moreover, the progress in this field has found extensive application in daily life, as demonstrated by the steady-state control mechanisms used in Segway [3], bipedal robots [4], and skyscrapers [5]. Furthermore, the control principle of cranes [6] and offshore drilling platforms [7] share similarities with the model when the pendulum is suspended.
In fact, these mechanical systems exemplify a category of attitude control challenges that essential goal is to drive the arm in following a prescribed time-varying trajectory while keeping the pendulum balanced near a stable upright position. To achieve this, numerous linear and nonlinear controller synthesis methods have attracted significant interest and research attention. Among them, proportional-integral-derivative (PID) control or its hybrid variants are frequently used controllers [8,9], due to its simplistic structure, cost-effectiveness, and ease of implementation in hardware. Ideally, the performance of controlled dynamical systems should be optimal. However, determining the optimal control gain to efficiently suppress uncertain nonlinearities using the system dynamics model is challenging when designing a PID controller. Moreover, the PID controller is designed for linear applications without considering saturation nonlinearity, which may result in performance degradation or even instability in certain instances. In recent years, it has been found that the peculiarities of fractional calculus in mathematics provide an extension to the traditional PID method. Dwivedi et al. [10] was the first to design and test a fractional-order PID (FOPID) controller on RIP, and the saturation effect when the control input is saturated was mitigated by combining the FOPID controller with an anti-windup technique [11]. Linear quadratic regulation (LQR) is another commonly used optimal control method, which is based on minimizing a quadratic performance criterion that encapsulates state and control input variations. In references [12–14], the LQR controller was utilized to stabilize the attitude dynamics of RIP in an upright posture. Although LQR is optimal, it lacks robustness against parametric uncertainties. Therefore, hybrid versions of LQR, which incorporate additional control strategies, filters or observers, were employed to address this deficiency while ensuring robustness and optimal performance. For instance, the linear quadratic gaussian (LQG) controller, which combines a Kalman filter observer and LQR, was presented in [15,16]. Hybrid control, formulated in [17], integrates backstepping and LQR. Additionally, in [18], the combination of passivity-based control and LQR was analyzed, designed and implemented on RIP.
Recent advancements in artificial intelligence (AI) and evolutionary computational techniques, collectively referred to as intelligent computational techniques, have introduced innovative solutions for controlling RIP systems. AI has gained popularity in clustering random complex matrices [19] and graphs [20]. There has been a recent surge in the development of an intelligent optimal control approach that integrates the adaptive features of intelligent computation into traditional linear control frameworks. Rather than manually tuning LQR, the state weighting matrices in [21,22] have been dynamically adjusted based on secant hyperbolic functions (SHFs) or optimized using particle swarm optimization (PSO) algorithms. Additionally, LQR controllers with fuzzy tuning have improved robustness in practical applications [23]. Consequently, the retrofitted LQR has demonstrated superior control outcomes. To fully exploit the benefits of intelligent algorithms and optimal control, some researchers have focused on associating LQR with a neural network (NN) for improving system response. In [24,25], LQR determines the stability of the IP system around arbitrary equilibrium points, while the NN control improves transient performance when deviations occur from an intended point and suppresses system bias.
In the aforementioned works, system models and state variables are pivotal in deriving optimal control laws or strategies to achieve the desired response and performance. However, many physical states of the system are either unmeasurable or extremely difficult to measure using sensors. Moreover, sensors are susceptible to noise interference, resulting in the acquisition of inaccurate measurements. A review of the existing literature shows that although a number of well-known control strategies, including neural NN-based system identification [26,27], fuzzy control (FC) [13,23], sliding mode control (SMC) [28], model-free control (MFC) [29], and hybrids of these, can mitigate the inherent problems of model-based control, but each has its own limitations. For example, NN often requires extensive experimental datasets for effective training and testing; to ensure robustness, FC relies on intricate qualitative logic rules derived from the relevant experience of the operator or designer; while SMC accelerates system stabilization, but often leads to undesirable oscillation. Additionally, in practical control engineering systems, the simplicity of control algorithms is highly desired along with the achievement of control objectives.
Motivated by the aforementioned challenges and inspired by the observer-based control approach detailed in references [30–33], this study focuses on the stabilizing and tracking control problems for RIP systems using a reduced-order observer feedback within a LQR control framework. The contributions of this study are outlined as follows:
(1) The RIP was analyzed and modeled using Newton-Euler and Lagrange equations. Additionally, the controllability and observability of the system were determined, and the feedback gain matrix was evaluated.
(2) A reduced-order observer was proposed to reconstruct the unmeasured system states and showed excellent robustness to low-amplitude, high-frequency disturbances by eliminating the differential term.
The remainder of this paper is organized as follows: Section 2 presents the mathematical model and linearization of the RIP system. In Section 3, the design of the controller and reduced-order observer is introduced. In Section 4, simulations and experiments are given, respectively. Finally, the main conclusions are presented in Section 5.
The RIP system comprises an unactuated pendulum that freely rotates in a vertical plane, perpendicular to the tip of a horizontally rotating arm driven by a direct current (DC) motor. The system is characterized by two degrees of mechanical freedom and a single control input, as illustrated in Fig. 1. Angle sensors are employed to detect the angle at which the pendulum deviates from equilibrium. The rotary arm and a parallel Z-axis are depicted in Fig. 1, with the inertial earth-fixed reference frame labelled as O-XYZ and the arm-fixed reference frame as O′-X′Y′Z′.
Figure 1: The RIP with reference frames
It is assumed that the pendulum is homogeneous. The rotary arm and pendulum have masses
where
Figure 2: The pendulum projection into the XOY plane
From Eqs. (1) and (2), the kinetic energy
where
The kinetic energy
In this equation,
Define the plane X′O′Y′ as the reference plane. Around upright equilibrium, the potential energy
Equations describing rotary arm and pendulum motions with respect to DC motor voltage are obtained by the Euler-Lagrange equation
The Lagrangian function, L, can be inferred from Eqs. (6) and (7), which can be represented as
where
In which,
The state variables are defined as
where
where
3 Controller and Reduced-Order Observer Design
The eigenvalues of matrix
3.1 LQR-Based Controller Design
As stated in Eqs. (12) and (13), let
In a closed-loop control system, the system input
Given the parameters listed in Table 1, matrices
For the Type I RIP system, its inherent underdriven characteristics dictate that
Figure 3: State feedback control scheme
where
The
The state matrix of closed-loop control systems can be expressed as
where
Moreover, it is worthwhile to note that along with Eq. (17) we also have
The Riccati equation [14,22,24] can be solved to yield the matrix
3.2 Reduced-Order Observer Design
Due to the installation environment or other factors, there might be a need for an observer to estimate states that cannot be directly measured. In this project, a reduced-order observer is constructed specifically to estimate states
where
The unmeasurable states can be interpreted through Eqs. (24) and (25), which serve as the dynamic differential equation and output equation, respectively. By utilizing the design methodology of the Luenberger full-order state observer and using error feedback between the measured and estimated output, a reduced-order observer for
where
Define
The reduced-order observer can be derived by substituting Eq. (29) for Eq. (28)
where the transformation relation from
Eq. (30) can be further derived as
Define the observation error
It should be emphasized that the assumption of
Combining Eqs. (35) and (36), we get
By analyzing the dynamic properties of
All the parameter symbols and values used in RIP system modeling are summarized in Table 1.
Using the values given in Table 1, the system state equation is
LQR controller performance is dependent on the choice of weight matrices
where
Figure 4: Simulation results of test experiments
The results show that
At this point, the system is asymptotically stabilized for any given initial state. Combining the controller Eq. (33), the reduced-order observer Eq. (30), and the transformation relation
Figure 5: Control block diagram of the linear RIP system
The system, as shown in Figs. 6 and 7, exhibits asymptotic stability under the influence of
Figure 6: Angular response curves
Figure 7: Angular velocity response curves
Eq. (37) can be used to determine the response curve for any given initial condition. In addition, the convergence rate of
Figure 8: The observation and error dynamic of
Figure 9: The observation and error dynamic of
The desired arm angle is defined as
where
Figure 10: The desired signal and position tracking
Figure 11: Variation of
4.2 Hardware Implementation and Validation
This method is validated with the Quanser QNET 2.0 RIP Board. Fig. 12 shows the system connection and front-end panel, which serve as the user interface for displaying state variation and controlling the application. The rotary arm is driven by a direct-drive 18 V brushed DC motor housed in a solid aluminum frame. Real-time variations in
Figure 12: The system connection and front-end panel
On this platform, two distinct experiments were conducted. The first experiment focused on examining the balance and disturbance rejection capabilities of the system following the pendulum’s swing up to the upright position. The second experiment concentrated on assessing the tracking control performance.
The experimental parameters used are consistent with those employed in the numerical simulation. Due to the manual erection and stabilization of the pendulum before each experiment, the initial conditions for activating balance control are random. Consequently, the data recording starts from the 5th second, as shown in Figs. 13 to 16. The controller’s capability to withstand mechanical vibration or process noise is evaluated by injecting sinusoidal and random signals of different frequencies and low-amplitude. In Fig. 13, the disturbance
Figure 13: Disturbance
Figure 14: Disturbance
Figure 15:
Figure 16:
The desired arm angle in the tracking control experiment is set to
where
Figure 17: The tracking control results
This paper presents a reduced-order observer technique to estimate unmeasurable state variables and integrate these estimates into a full-state feedback controller for RIP. By combining estimation with measurement, a state feedback controller for RIP is designed based on the LQR technique. The conclusion is summarized as follows:
(1) Numerical simulations show that the theoretically established linear controller is able to stabilize the system rapidly.
(2) The balance control experiment confirmed that the RIP can be balanced below 50 Hz and tracked well below 1.4 rad.
In summary, the controller demonstrates proficient performance in balance stabilization and trajectory tracking, showcasing robustness against low-amplitude, high-frequency disturbances. These outcomes suggest that the proposed framework effectively contributes to both RIP balancing and tracking, offering novel theoretical insights and practical applications for industrial use.
While this study primarily addresses linear control theory, the precise control of mechanical systems warrants further exploration in the realm of nonlinear control algorithms. Consequently, future work will delve into nonlinear control algorithms for underactuated systems.
Acknowledgement: The authors wish to thank their colleagues for their suggestions to improve the quality of this article.
Funding Statement: This work is supported in part by the Youth Foundation of China University of Petroleum-Beijing at Karamay (under Grant No. XQZX20230038); the Karamay Innovative Talents Program (under Grant No. 20212022HJCXRC0005).
Author Contributions: The authors confirm contribution to the paper as follows: study conception and design: G. Gao, L. Xu; system analysis and modeling: T. Huang, X. Zhao; controller and observer design: G. Gao, T. Huang; platform construction and experimental design: X. Zhao; L. Huang; analysis and interpretation of results: L. Xu, L. Huang; draft manuscript preparation: G. Gao, T. Huang. All authors reviewed the results and approved the final version of the manuscript.
Availability of Data and Materials: The datasets generated and/or analyzed during this study are available from the corresponding author on reasonable request.
Conflicts of Interest: The authors declare that they have no conflicts of interest to report regarding the present study.
References
1. Furuta, K., Yamakita, M., Kobayashi, S. (1992). Swing-up control of inverted pendulum using pseudo-state feedback. Proceedings of the Institution of Mechanical Engineers, Part I: Journal of Systems and Control Engineering, 206(4), 263–269. [Google Scholar]
2. Hamza, M. F., Yap, H. J., Choudhury, I. A., Isa, A. I., Zimit, A. Y. et al. (2019). Current development on using rotary inverted pendulum as a benchmark for testing linear and nonlinear control algorithms. Mechanical Systems and Signal Processing, 116, 347–369. [Google Scholar]
3. Ch, R. P., Ch, R., Assaf, M., Narayan, S. V., Naicker, P. R. et al. (2022). Acceleration feedback controller processor design of a segway. 2022 IEEE 7th Southern Power Electronics Conference (SPEC), Nadi, Fiji, IEEE. [Google Scholar]
4. Li, Z., Zeng, J., Chen, S., Sreenath, K. (2023). Autonomous navigation of underactuated bipedal robots in height-constrained environments. The International Journal of Robotics Research, 42(8), 565–585. [Google Scholar]
5. Zhou, K., Zhang, J. W., Li, Q. S. (2022). Control performance of active tuned mass damper for mitigating wind-induced vibrations of a 600-m-tall skyscraper. Journal of Building Engineering, 45, 103646. [Google Scholar]
6. Sun, N., Fu, Y., Yang, T., Zhang, J., Fang, Y. et al. (2020). Nonlinear motion control of complicated dual rotary crane systems without velocity feedback: Design, analysis, and hardware experiments. IEEE Transactions on Automation Science and Engineering, 17(2), 1017–1029. [Google Scholar]
7. Wang, J., Tang, S. X., Krstic, M. (2020). Adaptive output-feedback control of torsional vibration in off-shore rotary oil drilling systems. Automatica, 111, 108640. [Google Scholar]
8. Prasad, L. B., Tyagi, B., Gupta, H. O. (2014). Optimal control of nonlinear inverted pendulum system using PID controller and LQR: Performance analysis without and with disturbance input. International Journal of Automation and Computing, 11, 661–670. [Google Scholar]
9. Galan, D., Chaos, D., De La Torre, L., Aranda-Escolastico, E., Heradio, R. (2019). Customized online laboratory experiments: A general tool and its application to the furuta inverted pendulum [focus on education]. IEEE Control Systems Magazine, 39(5), 75–87. [Google Scholar]
10. Dwivedi, P., Pandey, S., Junghare, A. (2017). Performance analysis and experimental validation of 2-DOF fractional-order controller for underactuated rotary inverted pendulum. Arabian Journal for Science and Engineering, 42, 5121–5145. [Google Scholar]
11. Dwivedi, P., Pandey, S., Junghare, A. S. (2017). Stabilization of unstable equilibrium point of rotary inverted pendulum using fractional controller. Journal of the Franklin Institute, 354(17), 7732–7766. [Google Scholar]
12. Sarkar, T. T., Dewan, L., Mahanta, C. (2020). Real time swing up and stabilization of rotary inverted pendulum system. 2020 International Conference on Computational Performance Evaluation (ComPE). Shillong, India, IEEE. [Google Scholar]
13. Abdullah, M., Amin, A. A., Iqbal, S., Mahmood-ul Hasan, K. (2021). Swing up and stabilization control of rotary inverted pendulum based on energy balance, fuzzy logic, and LQR controllers. Measurement and Control, 54(9–10), 1356–1370. [Google Scholar]
14. Shahzad, A., Munshi, S., Azam, S., Khan, M. N. (2022). Design and implementation of a state-feedback controller using LQR technique. Computers, Materials & Continua, 73(2), 2897–2911. https://doi.org/10.32604/cmc.2022.028441 [Google Scholar] [CrossRef]
15. Videcoq, E., Girault, M., Bouderbala, K., Nouira, H., Salgado, J. et al. (2015). Parametric investigation of linear quadratic gaussian and model predictive control approaches for thermal regulation of a high precision geometric measurement machine. Applied Thermal Engineering, 78, 720–730. [Google Scholar]
16. Alhinqari, A. (2022). State estimation of an inverted pendulum on cart system by kalman filtering and optimal control (LQG). 2022 IEEE 2nd International Maghreb Meeting of the Conference on Sciences and Techniques of Automatic Control and Computer Engineering (MI-STA). Sabratha, Libya, IEEE. [Google Scholar]
17. Patra, A. K., Biswal, S. S., Rout, P. K. (2022). Backstepping linear quadratic gaussian controller design for balancing an inverted pendulum. IETE Journal of Research, 68(1), 150–164. [Google Scholar]
18. Vo, M. T., Nguyen, V. D. H., Duong, H. N., Nguyen, V. H. (2023). Combining passivity-based control and linear quadratic regulator to control a rotary inverted pendulum. Journal of Robotics and Control (JRC), 4(4), 479–490. [Google Scholar]
19. Uykan, Z. (2020). Shadow-cuts minimization/maximization and complex hopfield neural networks. IEEE Transactions on Neural Networks and Learning Systems, 32(3), 1096–1109. [Google Scholar]
20. Uykan, Z. (2023). Fusion of centroid-based clustering with graph clustering: An expectation-maximization-based hybrid clustering. IEEE Transactions on Neural Networks and Learning Systems, 34(8), 4068–4082. [Google Scholar] [PubMed]
21. Saleem, O., Mahmood-Ul-Hasan, K. (2020). Indirect adaptive state-feedback control of rotary inverted pendulum using self-mutating hyperbolic-functions for online cost variation. IEEE Access, 8, 91236–91247. [Google Scholar]
22. Maghfiroh, H., Nizam, M., Anwar, M., Ma’Arif, A. (2022). Improved LQR control using PSO optimization and kalman filter estimator. IEEE Access, 10, 18330–18337. [Google Scholar]
23. Bekkar, B., Ferkous, K. (2023). Design of online fuzzy tuning LQR controller applied to rotary single inverted pendulum: Experimental validation. Arabian Journal for Science and Engineering, 48(5),6957–6972. [Google Scholar]
24. Nghi, H. V., Nhien, D. P., Ba, D. X. (2022). A LQR neural network control approach for fast stabilizing rotary inverted pendulums. International Journal of Precision Engineering and Manufacturing, 23, 45–56. [Google Scholar]
25. Juárez-Lora, J. A., Azuela, J. H. S., Ponce, V. H. P., Rubio-Espino, E., Fernández, R. B. (2022). Spiking neural network implementation of LQR control on underactuated system. International Journal of Combinatorial Optimization Problems and Informatics, 13(4), 36–46. [Google Scholar]
26. Chawla, I., Singla, A. (2020). Anfis based system identification of underactuated systems. International Journal of Nonlinear Sciences and Numerical Simulation, 21(7–8), 649–660. [Google Scholar]
27. de Carvalho, A., Justo, J. F., Angélico, B. A., de Oliveira, A. M., da Silva Filho, J. I. (2021). Rotary inverted pendulum identification for control by paraconsistent neural network. IEEE Access, 9, 74155–74167. [Google Scholar]
28. El-Sousy, F. F., Alattas, K. A., Mofid, O., Mobayen, S., Fekih, A. (2022). Robust adaptive super-twisting sliding mode stability control of underactuated rotational inverted pendulum with experimental validation. IEEE Access, 10, 100857–100866. [Google Scholar]
29. Huang, J., Zhang, T., Fan, Y., Sun, J. Q. (2019). Control of rotary inverted pendulum using model-free backstepping technique. IEEE Access, 7, 96965–96973. [Google Scholar]
30. Jmel, I., Dimassi, H., Hadj-Said, S., M’Sahli, F. (2020). An adaptive sliding mode observer for inverted pendulum under mass variation and disturbances with experimental validation. ISA Transactions, 102, 264–279. [Google Scholar] [PubMed]
31. Vu, V. P., Nguyen, M. T., Nguyen, A. V., Tran, V. D., Nguyen, T. M. N. (2021). Disturbance observer-based controller for inverted pendulum with uncertainties: Linear matrix inequality approach. International Journal of Electrical & Computer Engineering, 11(16), 4907–4921. [Google Scholar]
32. Assefa, A. (2022). Reduced order observer based pole placement design for inverted pendulum on cart. Journal of Informatics Electrical and Electronics Engineering (JIEEE), 3(2), 1–11. [Google Scholar]
33. Liu, G., Park, J. H., Xu, H., Hua, C. (2022). Reduced-order observer-based output-feedback tracking control for nonlinear time-delay systems with global prescribed performance. IEEE Transactions on Cybernetics, 53(9), 5560–5571. [Google Scholar]
34. Liu, W., Hao, B., Wang, Y. (2018). Global terminal sliding mode control based on extended state observer for rotary inverted pendulum systems. Control Engineering of China, 25(1), 106–111 (In Chinese). [Google Scholar]
Cite This Article
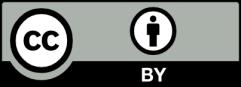
This work is licensed under a Creative Commons Attribution 4.0 International License , which permits unrestricted use, distribution, and reproduction in any medium, provided the original work is properly cited.