Open Access
ARTICLE
Contact Stress Reliability Analysis Model for Cylindrical Gear with Circular Arc Tooth Trace Based on an Improved Metamodel
1 School of Intelligent Manufacturing & Automobile, Chengdu Industrial Vocational Technical College, Chengdu, 610218, China
2 School of Intelligent Manufacturing, Panzhihua University, Panzhihua, 617000, China
3 School of Electrical Engineering, Chengdu Industry and Trade College, Chengdu, 601165, China
4 School of Mechanical Engineering, Sichuan University, Chengdu, 601165, China
5 Chengdu Technological University, Chengdu, 611730, China
* Corresponding Author: Yang Wu. Email:
(This article belongs to the Special Issue: Computer-Aided Uncertainty Modeling and Reliability Evaluation for Complex Engineering Structures)
Computer Modeling in Engineering & Sciences 2024, 140(1), 593-619. https://doi.org/10.32604/cmes.2023.046319
Received 26 September 2023; Accepted 21 November 2023; Issue published 16 April 2024
Abstract
Although there is currently no unified standard theoretical formula for calculating the contact stress of cylindrical gears with a circular arc tooth trace (referred to as CATT gear), a mathematical model for determining the contact stress of CATT gear is essential for studying how parameters affect its contact stress and building the contact stress limit state equation for contact stress reliability analysis. In this study, a mathematical relationship between design parameters and contact stress is formulated using the Kriging Metamodel. To enhance the model’s accuracy, we propose a new hybrid algorithm that merges the genetic algorithm with the Quantum Particle Swarm optimization algorithm, leveraging the strengths of each. Additionally, the “parental inheritance + self-learning” optimization model is used to fine-tune the Kriging Metamodel’s parameters. Following this, a mathematical model for calculating the contact stress of Variable Hyperbolic Circular-Arc-Tooth-Trace (VH-CATT) gears using the optimized Kriging model was developed. We then examined how different gear parameters affect the VH-CATT gears’ contact stress. Our simulation results show: (1) Improvements in R2, RMSE, and RMAE. R2 rose from 0.9852 to 0.9974 (a 1.22% increase), nearing 1, suggesting the optimized Kriging Metamodel’s global error is minimized. Meanwhile, RMSE dropped from 3.9210 to 1.6492, a decline of 57.94%. The global error of the GA-IQPSO-Kriging algorithm was also reduced, with RMAE decreasing by 58.69% from 0.1823 to 0.0753, showing the algorithm’s enhanced precision. In a comparison of ten experimental groups selected randomly, the GA-IQPSO-Kriging and FEM-based contact analysis methods were used to measure contact stress. Results revealed a maximum error of 12.11667 MPA, which represents 2.85% of the real value. (2) Several factors, including the pressure angle, tooth width, modulus, and tooth line radius, are inversely related to contact stress. The descending order of their impact on the contact stress is: tooth line radius > modulus > pressure angle > tooth width. (3) Complex interactions are noted among various parameters. Specifically, when the tooth line radius interacts with parameters such as pressure angle, tooth width, and modulus, the resulting stress contour is nonlinear, showcasing a multifaceted contour plane. However, when tooth width, modulus, and pressure angle interact, the stress contour is nearly linear, and the contour plane is simpler, indicating a weaker coupling among these factors.Keywords
Cite This Article
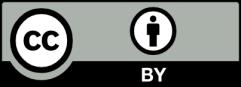
This work is licensed under a Creative Commons Attribution 4.0 International License , which permits unrestricted use, distribution, and reproduction in any medium, provided the original work is properly cited.