Open Access
ARTICLE
Buckling Optimization of Curved Grid Stiffeners through the Level Set Based Density Method
State Key Laboratory of Digital Manufacturing Equipment and Technology, Huazhong University of Science and Technology, Wuhan, 430074, China
* Corresponding Author: Qi Xia. Email:
(This article belongs to the Special Issue: Structural Design and Optimization)
Computer Modeling in Engineering & Sciences 2024, 140(1), 711-733. https://doi.org/10.32604/cmes.2024.045411
Received 25 August 2023; Accepted 15 December 2023; Issue published 16 April 2024
Abstract
Stiffened structures have great potential for improving mechanical performance, and the study of their stability is of great interest. In this paper, the optimization of the critical buckling load factor for curved grid stiffeners is solved by using the level set based density method, where the shape and cross section (including thickness and width) of the stiffeners can be optimized simultaneously. The grid stiffeners are a combination of many single stiffeners which are projected by the corresponding level set functions. The thickness and width of each stiffener are designed to be independent variables in the projection applied to each level set function. Besides, the path of each single stiffener is described by the zero iso-contour of the level set function. All the single stiffeners are combined together by using the p-norm method to obtain the stiffener grid. The proposed method is validated by several numerical examples to optimize the critical buckling load factor.Keywords
Stiffened structures are commonly used in various fields because of their efficient material utilization and superior mechanical properties [1,2], for instance, in aircraft fuselages, wing skins, and others. Correspondingly, the study of its stability has important engineering implications. It is well known that buckling failure is a common failure mode of stiffened structures under axial compression [3], and it is important for their design and applications.
The Optimal design of stiffened structures taking into account the buckling properties has attracted the attention of many researchers and much effort has been devoted to it. Kapania et al. [4,5] indicated that some curved stiffeners placed on the metal plates and composite plates with buckling-dominated load may further reduce the weight of the structure with respect to the straight stiffeners under the same load. Tamijani et al. [6] employed the Chebyshev-Ritz method to analyze the vibration and buckling of curved stiffened plates, including the influence of the plate width ratio, the number of stiffeners, and other parameters of the mechanical properties. Townsend et al. [7] adopted the level set method to optimize the structure aimed at maximizing its critical buckling load factor, where its balance between buckling load performance and compliance was discussed. Due to the effects of structural materials and geometric manufacturing on buckling bearing performance, Luo et al. [8] introduced a density-based method to optimize the stiffened structures with uncertain imperfect geometry, as an objective function of buckling load. Wang et al. [9,10] adopted the smeared model and Bloch wave theory to obtain local and global buckling loads, respectively. All the attempts led to significant progress in the buckling optimization of the stiffeners.
Commonly, the grid stiffened structures will fail under three different forms of skin instability, stiffener instability, and global instability [9], with global buckling being known as the main failure form of the stiffened structures under the axial compression [11–13] and typically viewed as an optimization objective. Further, due to the fact that buckling failure may occur much earlier than the material yielding under axial compression, the critical buckling load is one of the most important optimization criteria of stiffened panels at the design stage [14,15].
To improve the global critical buckling load factor of stiffened structures, a buckling optimization method of grid stiffeners through the level set based density method is proposed in this paper, where the grid stiffeners consist of different single stiffeners, each of which is projected by a corresponding level set function. In this way, the level sets within the projective interval are considered as the stiffeners, and the zero iso-contour of the level set functions are devoted to describe the stiffeners’ paths. Further, the level sets are parameterized by the compactly supported radial basis functions (CS-RBFs), so the paths of stiffeners are controlled by the coefficients of CS-RBFs. Different from our previous model [16], both the thickness and width of each stiffener are designed as the unrestricted variables. Specifically, the thickness variable that controls the entire thickness of each stiffener is no longer just 0/1 by penalty, and the interval of projection for each stiffener is treated as an independent width variable. Based on this transition, the material utilization will be further improved during the optimization process, as the material can be utilized more freely by enhancing or weakening the thickness or width of the different stiffeners within a specified range, depending on their contribution to the structural stability.
Simultaneously, considering the manufactured performance, the spacing between the two adjacent stiffeners should be limited to be larger than an admissible value to avoid manufacturability issue. According to the gradient constraints of the level sets, the distance in the
The rest of this paper proceeds are summarized as follow. A descriptive model of curved grid stiffeners is established in Section 2. The definition of constraints for stiffeners is listed in Section 3. Details of sensitivity analysis and optimization design are given in Section 4. There are several numerical examples discussed in Section 5.
2 Descriptive Model of Grid Stiffeners
2.1 Definition of Stiffener Density
In order to efficiently address the global buckling optimization problem of the structure, the grid-stiffened structure is modeled using an equivalent panel based on Mindlin plate theory [18–20], akin to the concept of “cast-in stiffeners,” as opposed to employing the discrete stiffener method [21,22]. Additionally, it is assumed that the material of the substrate and the stiffener are the same. Consequently, the the stiffness matrix
where
where
where
where
In our studies, to achieve more flexible optimization of each stiffener, we combine the different single stiffeners to make up grid stiffeners by the
where
Inspired by the threshold projection of three-field approach [27,28], and in order to change the width of the single stiffeners, the virtual density
where the basic threshold function
where
2.2 Definition of Level Set Functions Based on RBF
In this paper, the shape of the
where
where
where
where
Figure 1: An example of the design domain with 10 × 10 finite elements and 6 × 6 RBFs
Several figures of two single stiffeners with different thicknesses and widths are displayed in Fig. 2. Fig. 2a indicates a schematic of the projection function Eq. (10) with
Figure 2: Several diagrams of the stiffener with separate thickness and width, and the thickness constant is set as 0.5, i.e.,
3 Definition of Constraints for Stiffeners
3.1 Constraint of Uniform Width
In most cases, the width of each single stiffener is expected to be uniform. Accordingly, the constraint designed to keep the width to be uniform [33] is still used in this paper. It is realized by ensuring the gradient norm of all the level sets to be equal to 1 in each element. In such circumstances, the width of each stiffener is determined by the projection parameter
The gradient norm of the
where
To realize the value of the gradient norm to be equal to 1, the width constraint similar to those in [33,34], is designed by
Considering the issue of computational efficiency due to the large number of elements, the
where
3.2 Constraint of the Stiffener Minimum Spacing
Considering the fabrication constraint on the stiffener spacing, the minimum spacing between the adjacent stiffeners must be controlled. Based on the gradient norm constraint, the spacing distance in the
In order to find the minimum spacing between the two adjacent stiffeners, the
Further, for the two adjacent level sets as seen in Fig. 3, the spacing is calculated as
where the
Figure 3: A schematic example of the adjacent level sets when the corresponding stiffeners are just in contact
In order to make good use of the material as in most optimization problems, the constraint on the stiffening material volume is defined as
where
4 Optimization Design and Sensitivity Analysis
4.1 Definition of the Design Problem
In the present study, the maximization of the critical buckling load factor is seen as the objective to be optimized; the expansion coefficients of the CS-RBFs
where
4.2 Definition of the Sensitivity Analysis
The sensitivity of theoptimization objective J for the expansion coefficients
According to Eq. (25), the partial derivative of the critical buckling load factor
Based on Eqs. (6) and (7), we have
Based on Eqs. (8)–(12), we have
where
The sensitivity of the optimization objective J with respect to the thickness variables
According to Eq. (9), we have
The sensitivity of the optimization objective J with respect to the width variables
According to Eqs. (10) and (11), we have
where
According to Eq. (24), the sensitivity of the volume constraint V with respect to the design variable
The sensitivity of the gradient constraint
According to Eqs. (16)–(19), we have
The sensitivity of the minimum spacing constraint
where
For most gradient-based optimization algorithms, sensitivity determines their search direction. Consequently, after obtaining all sensitivities, the Method of Move Asymptote (MMA) [35] is employed by substituting the objective function value, constraint function values, and their respective sensitivities. This computation yields updated design variables, including the expansion coefficient for the parameterized level set function, as well as thickness and width variables for the stiffeners.
4.3 Optimization Process Summary
The optimization process mainly consists of several steps: defining the design domain, mesh partition, and boundary conditions; initializing the level set function and radical basis function; conducting finite element analysis; Solving the characteristic equation to obtain the eigenvalues; performing sensitivity analysis; and updating variables. Theses steps are discussed in detail one by one as follows:
Step 1: Define the design domain, partition the design domain for finite element meshing, select the nodes for RBFs, and impose the boundary conditions.
Step 2: Based on the shape requirements of the reinforcing bars, the parameters for the expansion coefficient and threshold projection interval in the level set function are defined. The initial thickness variables are all set to 1.
Step 3: Calculate the thickness of each element and determine the stiffness matrix and geometric stiffness matrix for each individual element. Combine these to form the overall stiffness matrix and overall geometric stiffness matrix.
Step 4: Solve for eigenvalues and eigenvectors based on the characteristic equation.
Step 5: Compute the sensitivity of the objective function and constraint functions with respect to the design variables.
Step 6: Based on sensitivity information, utilize the MMA (Method of Moving Asymptotes) algorithm using gradient-based optimization to update the design variables.
Step 7: Repeat steps 3 through 6 until the iteration termination criteria are met.
In this section, the effectiveness of the proposed method is validated by several examples, akin to those found in other studies [8,10,36,37]. The Poisson’s ratio is set as 0.3 and the Young’s modulus of material is set as 200 GPa. The thickness constants of the stiffeners and substructure are respectively set as
The optimization convergence criterion is given by
where convergence condition
The boundary conditions of the first example is given as Fig. 4. The substrate is a square plate (
Figure 4: Design domain and boundary conditions of the first example
In this example, the optimizations using different methods are compared, that is, whether the shape and cross section are optimized simultaneously. As shown in Fig. 5, all the designs are displayed with two-dimensional (2D) and three-dimensional (3D) modality for more details, where the color intensity depends on the thickness of the stiffener. In Figs. 5c and 5d, the optimized design with cross sections has changed the thickness and width of each stiffener, indicating that material utilization could be improved by weakening the low-intensity stiffeners and strengthening the high-intensity stiffeners. Furthermore, the optimized design with both the shape and cross section is shown in Fig. 5e, where the stiffeners are optimized not only on the section, but also the shape in unison, which has improved the critical buckling load factor by nearly 80.6%. Meanwhile, Fig. 6 illustrates the first modal shape of the structure, depicting the distribution of transverse normalized displacement in the structure corresponding to the critical eigenvalue, similar to [9,10].
Figure 5: The optimized designs with different optimization types (The intensity of the color depends on the thickness of the stiffener in 2D, and the thicknesses in 3D have been doubled for sharper display)
Figure 6: First order buckling mode of different optimization types, (a) initial design, (b) optimized design with cross section, (c) optimized design with shape and cross section
Remarkably, both the first and second order buckling load factors are shown in Fig. 7, which proves that the optimization to maximize the critical buckling load factor is reliable as such two lines do not intersect. In addition, as seen in Figs. 8 and 9, the thickness and width of the stiffeners are optimized differently if there is a simultaneous shape change, demonstrating that the optimization of shape and cross section is collaborative rather than independent.
Figure 7: Convergence history of buckling load factors and volume in the first example with different optimization types,
Figure 8: Convergence histories of thickness
Figure 9: Convergence histories of width
The boundary conditions are the same as Fig. 4. The substrate is a square plate (
Firstly, in this example, we consider the effectiveness of the minimum spacing constraint in Eq. (23). As shown in Fig. 10, the adjacent stiffeners may be interlaced when there is not any constraint of minimum spacing (i.e.,
Figure 10: The optimized designs with different minimum spacings (The intensity of the color depends on the thickness of the stiffener in 2D, and the thicknesses in 3D have been doubled for sharper display)
Secondly, to account for the impact of finite element discretization, analyses were conducted using mesh sizes of 120 × 120, 150 × 150, and 180 × 180. The optimized designs of different mesh configurations are shown in Fig. 11. It can be observed that when the number of mesh elements is too low, it may impact the results of the optimization design, with the critical buckling load factor
Figure 11: The optimized designs under various mesh element configurations. (a, b)
The essential boundary conditions of the third example is shown in Fig. 12. The size of the substrate is
Figure 12: Design domain and boundary conditions of the third example
In this example, with the same distribution of stiffeners as in Fig. 5a, the optimization is performed with different admissible volumes
Figure 13: The optimized designs with different admissible volumes, as the same initial design as in Example 1 (The intensity of the color depends on the thickness of the stiffener in 2D, and the thicknesses in 3D have been doubled for sharper display)
Figure 14: Convergence history of buckling load factors and volume in the second example with different admissible volumes,
Figure 15: Convergence histories of thickness
Figure 16: Convergence histories of width
Figure 17: First order buckling mode with different admissible volumes, (a) optimized with
Compared to the first example, the upper bound on the thickness variable is raised, and during the optimization one can see that the material is still used to reinforce several main stiffeners up to the upper limit, ensuring the strength of the structure. Further, if the material is reduced by even less, the bounds on the thickness and width can be lowered to accommodate the material variations.
A novel buckling optimization method of curved grid stiffeners is proposed in this paper, where the shape and cross section (including thickness and width) of each stiffener can be optimized in a synchronous and flexible manner to improve the critical buckling load factor of the stiffened structure.
Based on the level set based density method proposed in the previous study [16], the grid stiffeners are composed of different single stiffeners projected by the corresponding level set functions. As an enhancement, the thickness and width of each stiffener are designed as unrestricted variables. This allows the material to freely redistribute from a low-intensity stiffener to a high-intensity one. In other words, the width and thickness of the stiffener are adjusted based on their contribution to structural stability, either being enhanced or weakened. Additionally, the spacing between neighboring stiffeners is effectively controlled for manufacturing considerations. All these advancements have been successfully demonstrated in the buckling optimization.
Acknowledgement: The authors sincerely appreciate the insightful comments from the reviewers and also gratefully thank Krister Svanberg for providing the MMA codes.
Funding Statement: The present research works are supported by the National Natural Science Foundation of China (Grant Nos. 51975227 and 12272144).
Author Contributions: The authors confirm contribution to the paper as follows: study conception and design: Zhuo Huang, Qi Xia; data collection: Ye Tian; analysis and interpretation of results: Zhuo Huang, Yifan Zhang, Tielin Shi; draft manuscript preparation: Zhuo Huang, Qi Xia. All authors reviewed the results and approved the final version of the manuscript.
Availability of Data and Materials: None.
Conflicts of Interest: The authors declare that they have no conflicts of interest to report regarding the present study.
References
1. Jadhav, P., Mantena, P. R. (2007). Parametric optimization of grid-stiffened composite panels for maximizing their performance under transverse loading. Composite Structures, 77(3), 353–363. [Google Scholar]
2. Zhu, J. H., Zhang, W. H., Xia, L. (2016). Topology optimization in aircraft and aerospace structures design. Archives of Computational Methods in Engineering, 23(4), 595–622. [Google Scholar]
3. Ma, H., Jiao, P., Li, H., Cheng, Z., Chen, Z. (2023). Buckling analyses of thin-walled cylindrical shells subjected to multi-region localized axial compression: Experimental and numerical study. Thin-Walled Structures, 183, 110330. [Google Scholar]
4. Kapania, R. K., Li, J., Kapoor, H. (2005). Optimal design of unitized panels with curvilinear stiffeners. AIAA 5th ATIO and the AIAA 16th Lighter-than-Air Systems Technology Conference and Balloon Systems Conference, vol. 3, pp. 1708–1737. Arlington, Virgina. [Google Scholar]
5. Zhao, W., Kapania, R. K. (2016). Buckling analysis of unitized curvilinearly stiffened composite panels. Composite Structures, 135, 365–382. [Google Scholar]
6. Tamijani, A. Y., Kapania, R. K. (2015). Chebyshev-ritz approach to buckling and vibration of curvilinearly stiffened plate. Aiaa Journal, 50(5), 1007–1018. [Google Scholar]
7. Townsend, S., Kim, H. A. (2019). A level set topology optimization method for the buckling of shell structures. Structural and Multidisciplinary Optimization, 60(5), 1783–1800. [Google Scholar]
8. Luo, Y., Zhan, J. (2020). Linear buckling topology optimization of reinforced thin-walled structures considering uncertain geometrical imperfections. Structural and Multidisciplinary Optimization, 62(4), 3367–3382. [Google Scholar]
9. Wang, D., Abdalla, M. M. (2015). Global and local buckling analysis of grid-stiffened composite panels. Composite Structures, 119, 767–776. [Google Scholar]
10. Wang, D., Abdalla, M. M., Zhang, W. (2017). Buckling optimization design of curved stiffeners for grid-stiffened composite structures. Composite Structures, 159, 656–666. [Google Scholar]
11. Zheng, Q., Jiang, D., Huang, C., Shang, X., Ju, S. (2015). Analysis of failure loads and optimal design of composite lattice cylinder under axial compression. Composite Structures, 131, 885–894. [Google Scholar]
12. Lopatin, A. V., Morozov, E. V. (2015). Buckling of the composite sandwich cylindrical shell with clamped ends under uniform external pressure. Composite Structures, 122, 209–216. [Google Scholar]
13. Ghazijahani, T. G., Jiao, H., Holloway, D. (2015). Longitudinally stiffened corrugated cylindrical shells under uniform external pressure. Journal of Constructional Steel Research, 110, 191–199. [Google Scholar]
14. Singh, K., Kapania, R. K. (2021). Accelerated optimization of curvilinearly stiffened panels using deep learning. Thin-Walled Structures, 161(3), 107418. [Google Scholar]
15. Bostan, B., Kusbeci, M., Cetin, M., Kirca, M. (2023). Buckling performance of fuselage panels reinforced with voronoi-type stiffeners. International Journal of Mechanical Sciences, 240, 107923. [Google Scholar]
16. Huang, Z., Tian, Y., Yang, K., Shi, T., Xia, Q. (2023). Shape and generalized topology optimization of curved grid stiffeners through the level set based density method. Journal of Mechanical Design, 145(11), 111704. https://doi.org/10.1115/1.4063093 [Google Scholar] [CrossRef]
17. Le, C., Norato, J., Bruns, T., Ha, C., Tortorelli, D. (2010). Stress-based topology optimization for continua. Structural and Multidisciplinary Optimization, 41(4), 605–620. [Google Scholar]
18. Ma, H., Gao, X. L., Reddy, J. (2011). A non-classical mindlin plate model based on a modified couple stress theory. Acta Mechanica, 220(1–4), 217–235. [Google Scholar]
19. Batista, M. (2010). An elementary derivation of basic equations of the reissner and mindlin plate theories. Engineering Structures, 32(3), 906–909. [Google Scholar]
20. Liu, H., Chen, L., Shi, T., Xia, Q. (2022). M-vcut level set method for the layout and shape optimization of stiffeners in plate. Composite Structures, 293, 115614. [Google Scholar]
21. Wodesenbet, E., Kidane, S., Pang, S. S. (2003). Optimization for buckling loads of grid stiffened composite panels. Composite Structures, 60(2), 159–169. [Google Scholar]
22. Wang, J. T. S., Hsu, T. M. (1985). Discrete analysis of stiffened composite cylindrical shells. AIAA Journal, 23(11), 1753–1761. [Google Scholar]
23. Zhang, W. H., Zhou, Y., Zhu, J. H. (2017). A comprehensive study of feature definitions with solids and voids for topology optimization. Computer Methods in Applied Mechanics and Engineering, 325, 289–313. [Google Scholar]
24. Savine, F., Irisarri, F. X., Julien, C., Vincenti, A., Guerin, Y. (2021). A component-based method for the optimization of stiffener layout on large cylindrical rib-stiffened shell structures. Structural and Multidisciplinary Optimization, 64(4), 1843–1861. [Google Scholar]
25. Bendse, M. P. (1989). Optimal shape design as a material distribution problem. Structural Optimization, 1(4), 193–202. [Google Scholar]
26. Rozvany, G. I. N., Zhou, M., Birker, T. (1992). Generalized shape optimization without homogenization. Structural Optimization, 4(3), 250–254. [Google Scholar]
27. Wang, F. W., Lazarov, B. S., Sigmund, O. (2011). On projection methods, convergence and robust formulations in topology optimization. Structural and Multidisciplinary Optimization, 43(6), 767–784. [Google Scholar]
28. Clausen, A., Aage, N., Sigmund, O. (2015). Topology optimization of coated structures and material interface problems. Computer Methods in Applied Mechanics and Engineering, 290, 524–541. [Google Scholar]
29. Wang, S., Wang, M. (2006). Structural shape and topology optimization using an implicit free boundary parametrization method. Computer Modeling in Engineering & Sciences, 13(2), 119–147. [Google Scholar]
30. Luo, Z., Tong, L., Wang, M. Y., Wang, S. (2007). Shape and topology optimization of compliant mechanisms using a parameterization level set method. Journal of Computational Physics, 227(1), 680–705. [Google Scholar]
31. Wang, Y., Luo, Z., Kang, Z., Zhang, N. (2015). A multi-material level set-based topology and shape optimization method. Computer Methods in Applied Mechanics and Engineering, 283, 1570–1586. [Google Scholar]
32. Wei, P., Li, Z. Y., Li, X. P., Wang, M. Y. (2018). An 88-line matlab code for the parameterized level set method based topology optimization using radial basis functions. SStructural and Multidisciplinary Optimization, 58(2), 831–849. [Google Scholar]
33. Yang, K., Tian, Y., Shi, T., Xia, Q. (2022). A level set based density method for optimizing structures with curved grid stiffeners. Computer-Aided Design, 153, 103407. [Google Scholar]
34. Jiang, L., Chen, S. K. (2017). Parametric structural shape & topology optimization with a variational distance-regularized level set method. Computer Methods in Applied Mechanics and Engineering, 321, 316–336. [Google Scholar]
35. Svanberg, K. (1987). The method of moving asymptotes-a new method for structural optimization. International Journal for Numerical Methods in Engineering, 24(2), 359–373. [Google Scholar]
36. Wang, W., Ye, H., Li, Z., Sui, Y. (2023). Topology optimization for disc structures with buckling and displacement constraints. Engineering Optimization, 55(1), 35–52. [Google Scholar]
37. Lindgaard, E., Lund, E. (2011). Optimization formulations for the maximum nonlinear buckling load of composite structures. Structural and Multidisciplinary Optimization, 43(5), 631–646. [Google Scholar]
Cite This Article
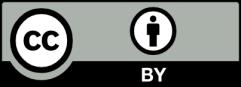
This work is licensed under a Creative Commons Attribution 4.0 International License , which permits unrestricted use, distribution, and reproduction in any medium, provided the original work is properly cited.