Open Access
ARTICLE
Research on the Generation Mechanism and Suppression Method of Aerodynamic Noise in Expansion Cavity Based on Hybrid Method
1 School of Mechanotronics and Vehicle Engineering, East China Jiaotong University, Nanchang, 330013, China
2 Suzhou Automotive Research Institue, Tsinghua University, Suzhou, 215131, China
* Corresponding Author: Haitao Liu. Email:
Computer Modeling in Engineering & Sciences 2024, 139(3), 2747-2772. https://doi.org/10.32604/cmes.2024.047129
Received 26 October 2023; Accepted 02 January 2024; Issue published 11 March 2024
Abstract
The expansion chamber serves as the primary silencing structure within the exhaust pipeline. However, it can also act as a sound-emitting structure when subjected to airflow. This article presents a hybrid method for numerically simulating and analyzing the unsteady flow and aerodynamic noise in an expansion chamber under the influence of airflow. A fluid simulation model is established, utilizing the Large Eddy Simulation (LES) method to calculate the unsteady flow within the expansion chamber. The simulation results effectively capture the development and changes of the unsteady flow and vorticity inside the cavity, exhibiting a high level of consistency with experimental observations. To calculate the aerodynamic noise sources within the cavity, the flow field results are integrated using the method of integral interpolation and inserted into the acoustic grid. The acoustic analogy method is then employed to determine the aerodynamic noise sources. An acoustic simulation model is established, and the flow noise source is imported into the sound field grid to calculate the sound pressure at the far-field response point. The calculated sound pressure levels and resonance frequencies show good agreement with the experimental results. To address the issue of airflow regeneration noise within the cavity, perforated tubes are selected as a means of noise suppression. An experimental platform for airflow regeneration noise is constructed, and experimental samples are processed to analyze and verify the noise suppression effect of perforated tube expansion cavities under different airflow velocities. The research findings indicate that the perforated tube expansion cavity can effectively suppress low-frequency aerodynamic noise within the cavity by impeding the formation of strong shear layers. Moreover, the semi-perforated tube expansion cavity demonstrates the most effective suppression of aerodynamic noise.Graphic Abstract
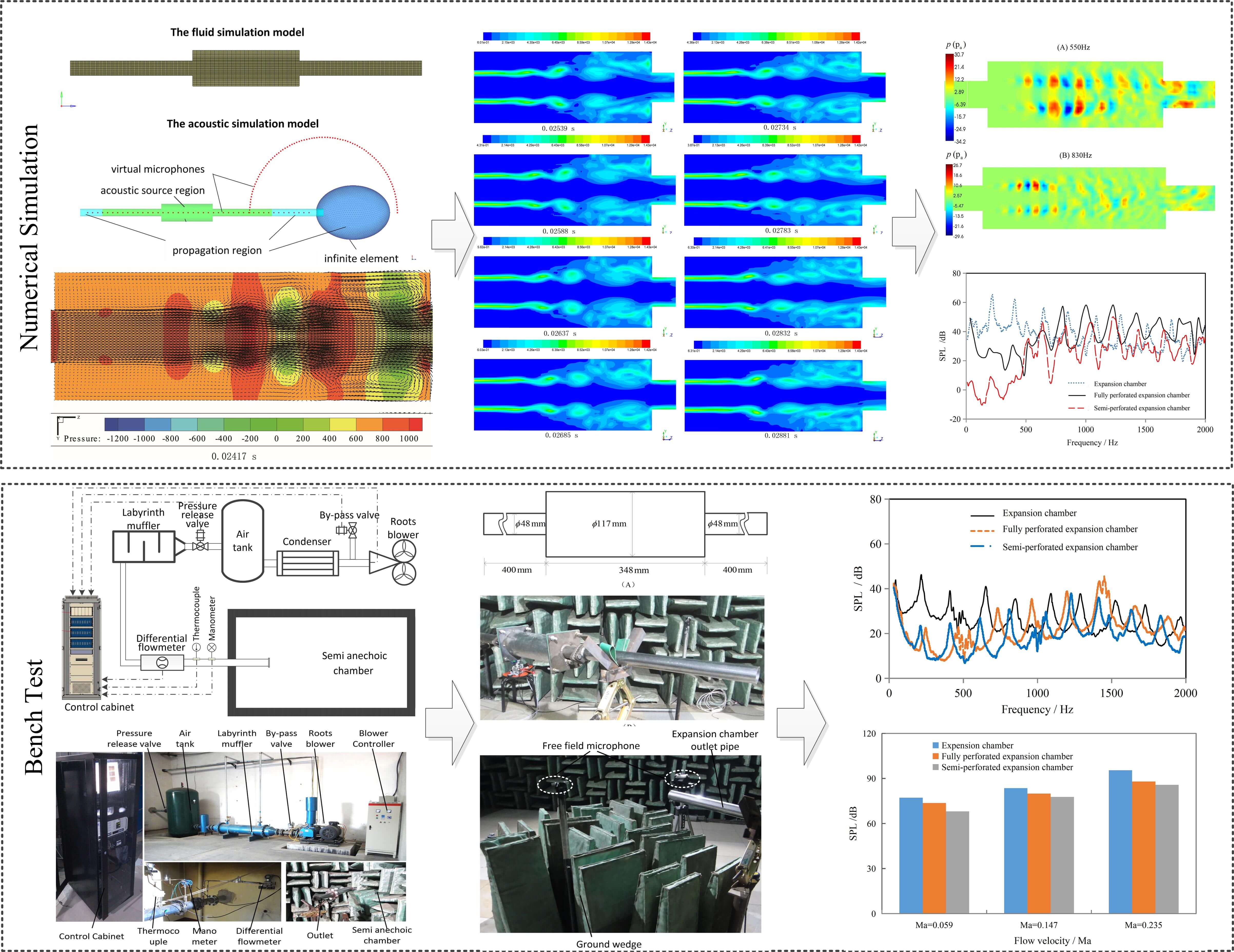
Keywords
Cite This Article
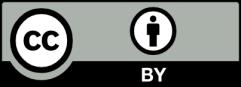
This work is licensed under a Creative Commons Attribution 4.0 International License , which permits unrestricted use, distribution, and reproduction in any medium, provided the original work is properly cited.