Open Access
ARTICLE
Study on Chaotic Characteristics of the Friction Process between High Hardness Alloy Steel and Cemented Carbide under C60 Nanoparticle Fluid Lubrication
School of Aerospace Engineering, Xiamen University, Xiamen, 361005, China
* Corresponding Author: Bin Yao. Email:
(This article belongs to the Special Issue: Vibration Control and Utilization)
Computer Modeling in Engineering & Sciences 2024, 138(1), 525-550. https://doi.org/10.32604/cmes.2023.029675
Received 02 March 2023; Accepted 11 May 2023; Issue published 22 September 2023
Abstract
Friction and wear phenomenon is a complex nonlinear system, and it is also a significant problem in the process of metal cutting. In order to systematically analyze the friction and wear process of tool material-workpiece material friction pair in the cutting process of high hardness alloy steel under different lubrication conditions, the chaotic characteristics of friction process between high hardness alloy steel and cemented carbide under the lubrication C60 nano-particles fluid are studied based on the chaos theory. Firstly, the friction and wear experiments of the friction pair between high hardness alloy steel and cemented carbide tool are carried out based on the ring-block friction and wear tester, and the results of friction force signal in time domain and wear width are obtained. Then, the friction signals in time domain are processed and transformed based on phase space reconstruction and recurrence plot theory, and the recurrence plots of different experimental groups under different lubrication conditions are generated. The evolution law of recurrence plot is further observed and studied, and the recursive quantitative index is analyzed. Finally, the cutting experiments of tool wear are carried out. The results show that the proposed method can intuitively and accurately reveal the wear evolution process and the wear feature identification law of the tool material-high hardness alloy steel pair under different lubrication conditions. Meanwhile, it is found that when the concentration of C60 nanoparticles is 200~300 ppm, the stability of the friction pair system is best. The proposed method can provide a strategy for wear prediction in cutting process, and provide a theoretical basis and technical support for antifriction lubrication methods in practical cutting applications.Keywords
Cite This Article
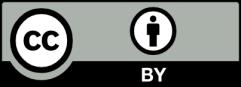
This work is licensed under a Creative Commons Attribution 4.0 International License , which permits unrestricted use, distribution, and reproduction in any medium, provided the original work is properly cited.