Open Access
ARTICLE
Technique for Multi-Pass Turning Optimization Based on Gaussian Quantum-Behaved Bat Algorithm
Computer Engineering College, Jimei University, Xiamen, 361021, China
* Corresponding Author: Xingwang Huang. Email:
(This article belongs to the Special Issue: Computational Intelligent Systems for Solving Complex Engineering Problems: Principles and Applications)
Computer Modeling in Engineering & Sciences 2023, 136(2), 1575-1602. https://doi.org/10.32604/cmes.2023.025812
Received 31 July 2022; Accepted 19 October 2022; Issue published 06 February 2023
Abstract
The multi-pass turning operation is one of the most commonly used machining methods in manufacturing field. The main objective of this operation is to minimize the unit production cost. This paper proposes a Gaussian quantum-behaved bat algorithm (GQBA) to solve the problem of multi-pass turning operation. The proposed algorithm mainly includes the following two improvements. The first improvement is to incorporate the current optimal positions of quantum bats and the global best position into the stochastic attractor to facilitate population diversification. The second improvement is to use a Gaussian distribution instead of the uniform distribution to update the positions of the quantum-behaved bats, thus performing a more accurate search and avoiding premature convergence. The performance of the presented GQBA is demonstrated through numerical benchmark functions and a multi-pass turning operation problem. Thirteen classical benchmark functions are utilized in the comparison experiments, and the experimental results for accuracy and convergence speed demonstrate that, in most cases, the GQBA can provide a better search capability than other algorithms. Furthermore, GQBA is applied to an optimization problem for multi-pass turning, which is designed to minimize the production cost while considering many practical machining constraints in the machining process. The experimental results indicate that the GQBA outperforms other comparison algorithms in terms of cost reduction, which proves the effectiveness of the GQBA.Keywords
In the manufacturing field, the technological challenge of machining operations is to produce products of the desired quality with high productivity and low cost. To reduce the machining cost for economical reasons, the optimization of the machining parameters is one of the most important issues, since these parameters have a strong impact on productivity, cost and quality [1]. Most turning processes require multi-pass turning, considering economic factors. The optimization problem for machining parameters in multi-pass turning becomes very complicated when a large number of actual machining constraints need to be considered [2]. Traditional optimization techniques, namely, dynamic programming [3] and the sequential unconstrained minimization technique [4], may be helpful in addressing some specific issues. However, these methods tend to find local optimal results. As a result, heuristic algorithms and nature-inspired swarm intelligence (SI) techniques have been introduced to solve economic machining problems because they have power in global search and robustness [5–9]. Chen proposed a scatter search to address optimization problems [10]. The genetic algorithm (GA) has been used extensively by some researchers [11–13] to optimize the process of multi-pass turning. The researchers applied varying improvements of the genetic operators to improve the GA performance to obtain better results. To solve optimization problems, ant colony optimization (ACO) [13–15], particle swarm optimization (PSO) [16–18], cuckoo optimization algorithm (COA) [9], grasshopper optimization algorithm (GOA) [19], bird swarm algorithm (BSA) [20], and the hybrid immune algorithm [21] were also developed.
In this paper, the first application of an improved version of the prevailing bat algorithm (BA) in the optimization of turning operations is presented. The BA is a recently proposed swarm intelligence optimization technique [22]. By mimicking the foraging behaviours of bats in searching for prey, the BA has incorporated the advantages of many classical techniques in a reasonable manner, including PSO, the GA [23] and simulated annealing (SA) [24]. Not only does the BA retain simplicity, it has also been shown to be more effective than its predecessors, especially in cases of lower dimensions. In addition, it is convenient to implement using a variety of programming languages. Therefore, the BA has been used to solve various engineering optimization applications [25]. However, since the population diversity of the BA is not sufficiently high, the BA may fall into a local optimum when dealing with applications of high dimensions [26]. To address this defect, many versions of the BA have been proposed, such as the CLBA [27], IBA [28], DLBA [29], and HSBA [30]. The quantum bat algorithm (QBA) [31] is a new technique based on the idea of quantum computing, which can increase the population diversity of the BA. In addition, considering the self-adaptive compensation of the Doppler effect in sound, the echolocation mechanism of bats can be simulated in the QBA. The QBA has been proven to outperform the standard BA and some well-known algorithms [31].
However, because the position of the stochastic attractor determines the central position of the quantum-behaved bat search area in the population and some critical random numbers are produced in the quantum mutation phase utilizing a uniform distribution, there is still premature convergence in the QBA to a certain extent. Motivated by these disadvantages, this paper proposes a QBA approach based on a Gaussian distribution (GQBA) to address the problem of premature convergence. The main contributions of this paper are as follows:
1. We propose an improved quantum-behaved bat algorithm using Gaussian distribution and apply it to the multi-pass turning problem.
2. We introduce a new stochastic attractor updating strategy to promote the diversification of swarms and a new quantum-behaved bat updating strategy to perform a more accurate search and avoid premature convergence.
3. Experiments on the numerical and multi-pass turning optimization indicate the efficiency of the GQBA. Comparisons with other comparative algorithms validate that the GQBA is competitive and is a good alternative approach.
The remainder of this paper is structured as follows: Section 2 briefly introduces related works. Section 3 gives the details of the GQBA proposed in this article. Section 4 presents the numerical validation and comparison. Section 5 presents an application of the GQBA to the multi-pass turning operation problem as well as the experimental results. Finally, the concluding comments and some future research directions are presented in Section 6.
When bats are foraging for food, they use echolocation to find prey and avoid obstacles. Inspired by the foraging behaviour of real bats, Yang proposed the bat algorithm in 2010 [22]. The original BA uses a frequency-tuning method to promote the diversification of the population. Additionally, it utilizes the automatic scaling technique to maintain a balance between exploration and exploitation during the optimization process by imitating the changes in pulse loudness and emission frequency during foraging. The procedures of the original BA are given below.
Each virtual bat in the swarm moves towards the global optimal position, which is the reason that all bats fly towards prey when foraging. The frequency (
where
For the exploitation stage, to generate a new candidate position for every virtual bat when a position is selected from the current optimal positions, a technique called a local random walk is adopted, which is given as Eq. (4):
where
When foraging, every virtual bat gradually adjusts its loudness value and emission frequency to locate prey. The equations for updating the value of loudness
where
The pseudo-code of the original BA is shown in Fig. 1.
Figure 1: Pseudo-code of the original BA [22]
The original BA has been used in many applications. However, since the population diversity of the BA is not sufficiently high, the BA does not perform well in multimodal cases. By analyzing the flight path of virtual bats, Meng et al. [31] developed the QBA. In the QBA, both the quantum behaviour and Doppler effect are taken into account, as well as other characteristics of the original BA. The mutation operator of quantum behaviour contributes to promoting the diversity of the swarm, which is ultimately beneficial in avoiding premature convergence.
The QBA is generally proposed on the framework of the standard BA. The exploration and exploitation procedures in the QBA are controlled by the decreasing loudness value A and increasing emission rate value r, respectively. However, the approach to generating new candidate positions in the QBA is not the same as that in the standard BA. Two more idealized rules have been introduced [32]: (1) the virtual bats have two foraging habitats instead of one foraging habitat depending on a random choice, and (2) the virtual bats self-adaptively compensate for the Doppler effect in sound. The positions of the virtual bats determined by quantum behaviour in the QBA can be described as Eq. (7):
where
Considering the self-adaptive capability of virtual bats to compensate for the Doppler effect, the equations mentioned in Eqs. (1) and (2) can be changed as Eqs. (11)–(13):
where
In the exploitation stage, in the QBA, the new candidate position of the virtual bat is produced as Eqs. (14) and (15):
where
During the search process, if the fitness of the objective function is not promoted in the Kth time step, then a simple strategy is employed to enhance the algorithm, which is to reassign the loudness value
The pseudo-code of the QBA is given in Fig. 2.
Figure 2: Pseudo-code of the QBA [31]
As mentioned above, the QBA is an improved BA variant that has good performance. However, by analyzing Eq. (7), it can be seen that due to the convergence of quantum-behaved bats to the stochastic attractor
To address the premature convergence problem of the QBA, this paper makes full use of the guiding role of the stochastic attractor and proposes a new strategy to update the position of the stochastic attractor as well as the bats in the population; this leads to the quantum-behaved bat algorithm based on a Gaussian distribution (the GQBA). In the implementation of the GQBA, some improved schemes have been substituted into the QBA, which are illustrated in the remainder of this section.
The first modification is to update the stochastic attractor with the guidance of the current optimal position value of the ith bat
where
The second change is to substitute coefficients u into Eq. (7) with the absolute value of the Gaussian distribution whose
The formula of probability density for G in one dimension can be stated as Eq. (17):
Therefore, in the GQBA, the position of the quantum-behaved bats can be described as Eq. (18):
where
In the GQBA, the stochastic attractor in terms of
The procedure of the GQBA is shown in Fig. 3.
Figure 3: Pseudo-code of the GQBA
4 Numerical Validation and Comparison
In this section, thirteen classical benchmark functions are utilized to verify the efficiency of the GQBA, which are illustrated in Tables 1 and 2. These benchmark functions have been utilized in many numerical optimization studies [36–39]. In this paper, the thirteen classical test functions can be divided into two classes. The first class consists of 7 unimodal benchmark functions with only one global best solution and effectively validates the meta-heuristic algorithms in terms of the convergence rate as well as the local search ability. The second class consists of 6 multimodal functions, the quantity of whose local optima increases exponentially. Multimodal functions are usually utilized to examine the global search ability of algorithms. All the tests on each benchmark function are repeated 30 times independently. All the tests described in this article were executed using MATLAB 2014a on a computer equipped with an Intel(R) Core(TM) i5-6500 CPU at 3.20 GHz with 8.0 GB of RAM.
Since the heuristic algorithm is a random optimization method, at least 10 independent runs need to be carried out to generate meaningful statistical results. In addition to the average value and standard deviation, statistical tests, such as the Wilcoxon rank sum test, are required to test the significance of the consequences based on each separate run. In this research, nonparametric Wilcoxon rank sum tests were carried out to examine whether the consequences of the GQBA were conspicuously different from those of comparative techniques.
To examine the efficiency of the GQBA and to obtain an exhaustive comparison, the GQBA and four other techniques, the BA [22], the QBA [31], PSO [40] and the GSA [41], are tested on the sets of benchmark instances above. In all experiments, the total number of iterations is 10000, and the number of individuals is 50. Table 3 shows the other specific parameter designs for each technique. The simulation results are illustrated in Tables 4 and 5 and Figs. 4–16. The best consequences for each test function are denoted in bold.
Figure 4: Convergence comparison of five techniques for
Figure 5: Convergence comparison of five techniques for
Figure 6: Convergence comparison of five techniques for
Figure 7: Convergence comparison of five techniques for
Figure 8: Convergence comparison of five techniques for
Figure 9: Convergence comparison of five techniques for
Figure 10: Convergence comparison of five techniques for
Figure 11: Convergence comparison of five techniques for
Figure 12: Convergence comparison of five techniques for
Figure 13: Convergence comparison of five techniques for
Figure 14: Convergence comparison of five techniques for
Figure 15: Convergence comparison of five techniques for
Figure 16: Convergence comparison of five techniques for
As shown in Table 4, the GQBA outperforms the other techniques in most cases, followed by PSO, the GSA, the QBA and the BA. To a certain extent, this is evidence that when the dimensionality of the search scope is high, the local optimal avoidance effect of the BA is insufficient.
As seen from Table 4, concerning accuracy, the GQBA has a better mean than the other techniques in eight out of 13 instances (
Figs. 4–16 show the convergence comparison of the five algorithms for the thirteen benchmark cases. The values shown in the convergence curves above them indicate the average of the objective values obtained from 30 separate runs. On the basis of the figures, the original BA and QBA converge at a faster speed with fewer iterations. However, in many cases, they are more likely to fall into local optima. It can also be seen from the figures that the convergence rate of the GQBA is similar to that of the QBA, while the GQBA can prevent premature convergence and can offer higher performance accuracy on most benchmark instances.
5 GQBA for Optimization of the Multi-Pass Turning Process
In this section, the GQBA with the pruning strategy is developed to address the constrained manufacturing optimization problem of multi-pass turning optimization. The goal of this problem is to find the optimal cutting parameters to minimize the unit production cost (UC) [8,9,42]. The minimization process is subject to many machining constraints that describe the states of the machining procedure. Machining optimization has been investigated by different techniques, such as ACO [14], PSO [16,43], the GA [5], the artificial bee colony (ABC) [44–46], the COA [9], the firefly algorithm (FA) [47], the flower pollination algorithm (FPA) [8], and differential evolution (DE) [48]. It is very convenient to compare the proposed GQBA with the methods developed previously.
5.1 Mathematical Model of Multi-Pass Turning
In this article, we adopt the mathematical model presented in [8,9,42] for optimizing the cutting parameters. The goal of the optimization model is to find the optimal cutting parameters, i.e., the depth-of-cut, feed rate and cutting speed, for both finishing and rough machining to minimize the unit production cost. A schematic representation of a turning operation is given in Fig. 17.
Figure 17: Schematic representation of a multi-pass turning operation
5.1.1 The Objective Function: Unit Production Cost (UC)
The UC of the multi-pass turning process is usually indicated by a combination of 4 basic cost factors:
(1) The cost due to the real cutting time (
(2) The machine idle cost for setup operations and tool idling motion (
(3) The cost of tool replacement (
(4) The tool cost (
Thus, the UC can be expressed as following Eq. (19) [8,9,42]:
5.1.2 Machining Condition Constraints
To minimize the UC, practical machining constraints that describe the states of the machining procedure, i.e., finishing and rough machining, are taken into account. They are described in detail as follows [8,42]:
Rough Machining
The constraints of rough machining are listed as Eqs. (20)–(27):
The chip-tool interface temperature constraint is expressed as Eq. (26):
Finish Machining
The constraints of finish machining are listed as Eqs. (28)–(36):
The chip-tool interface temperature constraint is expressed as Eq. (26):
Parameter Relations
The practical relationship between finish and rough machining can be given by Eqs. (37)–(40):
where the tool life can be formulated as Eq. (41).
It is supposed that the same tool is utilized during the whole machining operation procedure for both finishing and roughing. The wear rate of the cutter tools is commonly different between finishing and roughing due to changing machining conditions. Therefore, the life of the tool can be calculated as Eq. (42):
where
In some previous research work, a simplified formula for
5.1.3 Pruning Strategies Using the Theoretical Lower Bound of the Subproblem
The machining parameters of multi-pass turning that need to be optimized include a single finish cut and multiple rough cuts. Therefore, the available quantity of rough cuts should be restricted to certain ranges by Eq. (46):
where
Therefore, the total quantity of available values of n can be given as Eq. (47):
where m is generally a small integer.
Hence, the issue of optimizing the cutting parameters of multi-pass turns is divided into m subproblems. Therefore, the search process for the entire optimization problem is equivalent to search processes of the m subproblems, and the solution corresponding to the optimal fitness value among the m subproblems is taken as the solution of the entire optimization problem. Inspired by pruning strategies, we have found that the theoretical lower bound on the unit production cost for each subproblem can be used to reduce the total running time during the enumerative process, as reported in our previous work [49]. The theoretical lower bound on the unit production cost can be calculated according to the different quantities of rough cuts for each subproblem [49], and the theoretical lower bound on UC for the j-th subproblem is represented by
Figure 18: The flowchart of the GQBA for multi-pass turning optimization
The various notation used above is defined in Fig. 19.
Figure 19: List of symbols [48]
5.2 Experimental Verification and Comparisons
All the simulations were performed on a PC with the same characteristics as in Section 4. The numerical validation and comparisons using the machining model data [8,42] are shown in Table 6. We note that the tool life is usually defined by two different expressions (Eqs. (42) and (45)); thus, the proposed GQBA was tested using these two definitions. In each case, the GQBA was performed 50 times to obtain the average solution and optimized solution. The total number of iterations and the total number of individuals in each test were set to 7500 and 100, respectively. The remaining parameter design of the GQBA is given in Table 3.
Table 7 presents the results of the average unit production costs obtained by the GQBA using various mathematical models with different tool life expressions and cutting depths. We note that none of the solutions obtained in the experiment violate the practical machining constraints, suggesting that they are feasible. Moreover, it can be seen from this table that due to the low standard deviation, the solution obtained in each instance fluctuates within a small range, which indicates that the GQBA presented in this paper has good stability.
The optimization problem has been investigated by various approaches. To demonstrate the effectiveness of the proposed GQBA, we compare the simulation results with those reported in recent literature [5,8,9]. For a fair comparison, we select the results of other algorithms with consistent common parameters in these literatures. The detailed comparison results are summarized in Tables 8–11, where the best results are indicated by underlines.
From Table 8, it can be clearly seen that the GQBA presented in this paper outperforms many algorithms, and its performance is comparable with that of some previously best approaches such as the COA [9], hybrid particle swarm optimization (HPSO) [43] and the FPA [8]. All four methods can produce an optimal result of
As mentioned previously, different definitions have been proposed for the tool life expression in previous studies [5,8,9], i.e.,
The GQBA can find better results than the other algorithms to further cut down the unit production cost. The main reasons come from the following two aspects.
Firstly, we improve the original BA algorithm to form the novel GQBA. The first improvement is to incorporate the current optimal positions of quantum bats and the global best position into the stochastic attractor to facilitate population diversification. The second improvement is to use a Gaussian distribution instead of the uniform distribution to update the positions of the quantum-behaved bats, thus performing a more accurate search and avoiding premature convergence. All these are verified by the numerical simulation experiments in Section 4.
Secondly, to overcome the complicated optimization problems in various fields, we need to carefully consider the characteristics of the specific problem and use the specific domain knowledge to design the optimization algorithm. In this paper, for the optimization problem of multi-pass turning, because the machining process can be divided into different numbers of roughing cuts, we decompose the whole optimization problem into several simple sub-problems according to the different numbers of roughing cuts. Each sub-problem can be conquered individually, which greatly reduces the space of the problem solution.
Therefore, the performance of the combination of traditional divide-and-conquer strategy and swarm intelligence algorithm is better than other algorithms that only use traditional mathematical methods or swarm intelligence algorithms. However. the proposed GQBA may be suitable to solve the optimization problem of multi-pass turning, but it is not general as other algorithms, that is, they can also be applied to the optimization problems in other manufacturing fields. Therefore, the generality of our algorithm is insufficient, and we hope to improve it further in the future.
In this research, the GQBA is developed to promote the efficiency of the BA and QBA with respect to accuracy and stability. In the GQBA, the combination of the QBA and a Gaussian distribution can expand the search space and prevent premature convergence. The modification of the stochastic attractor can contribute to promoting swarm diversity. The GQBA also inherits the characteristics of the QBA, such as simplicity and feasibility. To conclude, the experimental results of numerical functions verify the effectiveness of the GQBA. In addition, the results of multi-pass turning operation optimization show that the GQBA is a good alternative method.
For future research directions, the proposed GQBA can be utilized with the angle modulation technique [50–52] to solve binary optimization problems. Moreover, the GQBA can be applied to other real-world problems, including artificial neural networks, task scheduling, feature selection and image segmentation.
Acknowledgement: The data that supports the findings of this study are authentic and reliable. And the authors appreciated the reviewers for their helpful suggestions which greatly improved the presentation of this paper.
Funding Statement: This research was supported by the the National Natural Science Foundation of Fujian Province of China (2020J01697, 2020J01699).
Conflicts of Interest: The authors declare that they have no conflicts of interest to report regarding the present study.
References
1. Chandrasekaran, M., Muralidhar, M., Krishna, C. M., Dixit, U. S. (2010). Application of soft computing techniques in machining performance prediction and optimization: A literature review. International Journal of Advanced Manufacturing Technology, 46(5–8), 445–464. DOI 10.1007/s00170-009-2104-x. [Google Scholar] [CrossRef]
2. Sibalija, T. V. (2019). Particle swarm optimisation in designing parameters of manufacturing processes: A review (2008–2018). Applied Soft Computing, 84, 105743. DOI 10.1016/j.asoc.2019.105743. [Google Scholar] [CrossRef]
3. Agapiou, J. S. (1992). The optimization of machining operations based on a combined criterion, Part 1: The use of combined objectives in single-pass operations. Journal of Engineering for Industry, 114(4), 500–507. DOI 10.1115/1.2900704. [Google Scholar] [CrossRef]
4. Duffuaa, S. O., Shuaib, A. N., Alam, M. (1993). Evaluation of optimization methods for machining economics models. Computers & Operations Research, 20(2), 227–237. DOI 10.1016/0305-0548(93)90077-V. [Google Scholar] [CrossRef]
5. Sofuoğlu, M. A., Çakır, F. H., Gürgen, S. (2019). An efficient approach by adjusting bounds for heuristic optimization algorithms. Soft Computing, 23(13), 5199–5212. DOI 10.1007/s00500-018-3327-2. [Google Scholar] [CrossRef]
6. Miodragovi, G. R., Orevi, V., Bulatovi, R. R., Petrovi, A. (2019). Optimization of multi-pass turning and multi-pass face milling using subpopulation firefly algorithm. Proceedings of the Institution of Mechanical Engineers, Part C: Journal of Mechanical Engineering Science, 233(5), 1520–1540. [Google Scholar]
7. Costa, A., Fichera, S. (2018). Response to cuckoo optimization algorithm for unit production cost in multi-pass turning operations [int j advmanuftechnol (2015) 76 (1647–656]. The International Journal of Advanced Manufacturing Technology, 94(1), 57–58. DOI 10.1007/s00170-017-0550-4. [Google Scholar] [CrossRef]
8. Xu, S., Wang, Y., Huang, F. (2017). Optimization of multi-pass turning parameters through an improved flower pollination algorithm. The International Journal of Advanced Manufacturing Technology, 89(1), 503–514. [Google Scholar]
9. Mellal, M. A., Williams, E. J. (2015). Cuckoo optimization algorithm for unit production cost in multi-pass turning operations. The International Journal of Advanced Manufacturing Technology, 76(1), 647–656. DOI 10.1007/s00170-014-6309-2. [Google Scholar] [CrossRef]
10. Chen, M. (2004). Optimizing machining economics models of turning operations using the scatter search approach. International Journal of Production Research, 42(13), 2611–2625. DOI 10.1080/00207540410001666251. [Google Scholar] [CrossRef]
11. Onwubolu, G. C., Kumalo, T. (2001). Optimization of multipass turning operations with genetic algorithms. International Journal of Production Research, 39(16), 3727–3745. DOI 10.1080/00207540110056153. [Google Scholar] [CrossRef]
12. Chen, M. C., Chen, K. Y. (2003). Optimization of multipass turning operations with genetic algorithms: A note. International Journal of Production Research, 41(14), 3385–3388. DOI 10.1080/0020754031000118143. [Google Scholar] [CrossRef]
13. Sankar, R. S., Asokan, P., Saravanan, R., Kumanan, S., Prabhaharan, G. (2007). Selection of machining parameters for constrained machining problem using evolutionary computation. The International Journal of Advanced Manufacturing Technology, 32(9–10), 892–901. DOI 10.1007/s00170-006-0420-y. [Google Scholar] [CrossRef]
14. Vijayakumar, K., Prabhaharan, G., Asokan, P., Saravanan, R. (2003). Optimization of multi-pass turning operations using ant colony system. International Journal of Machine Tools & Manufacture, 43(15), 1633–1639. DOI 10.1016/S0890-6955(03)00081-6. [Google Scholar] [CrossRef]
15. Wang, Y. C. (2007). A note on ‘optimization of multi-pass turning operations using ant colony system’. International Journal of Machine Tools & Manufacture, 47(12–13), 2057–2059. DOI 10.1016/j.ijmachtools.2007.03.001. [Google Scholar] [CrossRef]
16. Srinivas, J., Giri, R., Yang, S. (2009). Optimization of multi-pass turning using particle swarm intelligence. The International Journal of Advanced Manufacturing Technology, 40(1), 56–66. DOI 10.1007/s00170-007-1320-5. [Google Scholar] [CrossRef]
17. Yildiz, A. R. (2009). A novel particle swarm optimization approach for product design and manufacturing. The International Journal of Advanced Manufacturing Technology, 40(5–6), 617–628. DOI 10.1007/s00170-008-1453-1. [Google Scholar] [CrossRef]
18. Raja, S. B., Baskar, N. (2010). Optimization techniques for machining operations: A retrospective research based on various mathematical models. International Journal of Advanced Manufacturing Technology, 48(9–12), 1075–1090. DOI 10.1007/s00170-009-2351-x. [Google Scholar] [CrossRef]
19. Yan, X., Liu, Y., Xu, Y., Jia, M. (2020). Multistep forecasting for diurnal wind speed based on hybrid deep learning model with improved singular spectrum decomposition. Energy Conversion and Management, 225, 113456. DOI 10.1016/j.enconman.2020.113456. [Google Scholar] [CrossRef]
20. Yan, X., She, D., Xu, Y., Jia, M. (2021). Deep regularized variational autoencoder for intelligent fault diagnosis of rotor-bearing system within entire life-cycle process. Knowledge-Based Systems, 226, 107142. DOI 10.1016/j.knosys.2021.107142. [Google Scholar] [CrossRef]
21. Yildiz, A. R. (2009). Hybrid immune-simulated annealing algorithm for optimal design and manufacturing. International Journal of Materials & Product Technology, 34(3), 217–226. DOI 10.1504/IJMPT.2009.024655. [Google Scholar] [CrossRef]
22. Yang, X. -S. (2010). A new metaheuristic bat-inspired algorithm. In: Nature inspired cooperative strategies for optimization (NICSO 2010), pp. 65–74. Berlin, Heidelberg: Springer. [Google Scholar]
23. Mirjalili, S. (2019). Genetic algorithm. In: Evolutionary algorithms and neural networks, pp. 43–55. Cham: Springer. [Google Scholar]
24. Van Laarhoven, P. J., Aarts, E. H. (1987). Simulated annealing. In: Simulated annealing: Theory and applications, pp. 7–15. Dordrecht: Springer. [Google Scholar]
25. Jayabarathi, T., Raghunathan, T., Gandomi, A. (2018). The bat algorithm, variants and some practical engineering applications: A review. Nature-Inspired Algorithms and Applied Optimization, pp. 313–330. Cham: Springer. [Google Scholar]
26. Jordehi, A. R. (2015). Chaotic bat swarm optimisation (CBSO). Applied Soft Computing, 26, 523–530. DOI 10.1016/j.asoc.2014.10.010. [Google Scholar] [CrossRef]
27. Lin, J. H., Chou, C. W., Yang, C. H., Tsai, H. L. (2012). A chaotic levy flight bat algorithm for parameter estimation in nonlinear dynamic biological systems. Computer and Information Technology, 2(2), 56–63. [Google Scholar]
28. Yilmaz, S., Kucuksille, E. U. (2013). Improved bat algorithm (iba) on continuous optimization problems. Lecture Notes on Software Engineering, 1(3), 279. DOI 10.7763/LNSE.2013.V1.61. [Google Scholar] [CrossRef]
29. Xie, J., Zhou, Y., Chen, H. (2013). A novel bat algorithm based on differential operator and lévy flights trajectory. Computational Intelligence and Neuroscience, 2013. [Google Scholar]
30. Wang, G., Guo, L. (2013). A novel hybrid bat algorithm with harmony search for global numerical optimization. Journal of Applied Mathematics, 2013, 696491. DOI 10.1155/2013/696491. [Google Scholar] [CrossRef]
31. Meng, X. B., Gao, X. Z., Liu, Y., Zhang, H. (2015). A novel bat algorithm with habitat selection and Doppler effect in echoes for optimization. Expert Systems with Applications, 42(17–18), 6350–6364. DOI 10.1016/j.eswa.2015.04.026. [Google Scholar] [CrossRef]
32. Clerc, M., Kennedy, J. (2002). The particle swarm-explosion, stability, and convergence in a multidimensional complex space. IEEE Transactions on Evolutionary Computation, 6(1), 58–73. DOI 10.1109/4235.985692. [Google Scholar] [CrossRef]
33. Cai, X., Wang, L., Kang, Q., Wu, Q. (2014). Bat algorithm with Gaussian walk. International Journal of Bio-Inspired Computation, 6(3), 166–174. DOI 10.1504/IJBIC.2014.062637. [Google Scholar] [CrossRef]
34. dos Santos Coelho, L. (2010). Gaussian quantum-behaved particle swarm optimization approaches for constrained engineering design problems. Expert Systems with Applications, 37(2), 1676–1683. DOI 10.1016/j.eswa.2009.06.044. [Google Scholar] [CrossRef]
35. Liu, J., Xu, W., Sun, J. (2005). Quantum-behaved particle swarm optimization with mutation operator. 17th IEEE International Conference on Tools with Artificial Intelligence (ICTAI’05). Hong Kong, China, IEEE. [Google Scholar]
36. Mirjalili, S. (2015). Moth-flame optimization algorithm: A novel nature-inspired heuristic paradigm. Knowledge-Based Systems, 89, 228–249. DOI 10.1016/j.knosys.2015.07.006. [Google Scholar] [CrossRef]
37. Chen, K., Zhou, F., Liu, A. (2018). Chaotic dynamic weight particle swarm optimization for numerical function optimization. Knowledge-Based Systems, 139, 23–40. DOI 10.1016/j.knosys.2017.10.011. [Google Scholar] [CrossRef]
38. Mirjalili, S., Lewis, A. (2016). The whale optimization algorithm. Advances in Engineering Software, 95, 51–67. DOI 10.1016/j.advengsoft.2016.01.008. [Google Scholar] [CrossRef]
39. Zhu, B., Zhu, W., Liu, Z., Duan, Q., Cao, L. (2016). A novel quantum-behaved bat algorithm with mean best position directed for numerical optimization. Computational Intelligence and Neuroscience, 2016. DOI 10.1155/2016/6097484. [Google Scholar] [CrossRef]
40. James, K., Russell, E. (1995). Particle swarm optimization. Proceedings of 1995 IEEE International Conference on Neural Networks, Perth, WA, Australia. [Google Scholar]
41. Rashedi, E., Nezamabadi-Pour, H., Saryazdi, S. (2009). Gsa: A gravitational search algorithm. Information Sciences, 179(13), 2232–2248. DOI 10.1016/j.ins.2009.03.004. [Google Scholar] [CrossRef]
42. Chen, M. C., Tsai, D. (1996). A simulated annealing approach for optimization of multi-pass turning operations. International Journal of Production Research, 34(10), 2803–2825. DOI 10.1080/00207549608905060. [Google Scholar] [CrossRef]
43. Costa, A., Celano, G., Fichera, S. (2011). Optimization of multi-pass turning economies through a hybrid particle swarm optimization technique. The International Journal of Advanced Manufacturing Technology, 53(5), 421–433. DOI 10.1007/s00170-010-2861-6. [Google Scholar] [CrossRef]
44. Yildiz, A. R. (2012). A comparative study of population-based optimization algorithms for turning operations. Information Sciences, 210, 81–88. DOI 10.1016/j.ins.2012.03.005. [Google Scholar] [CrossRef]
45. Yildiz, A. R. (2013). Optimization of cutting parameters in multi-pass turning using artificial bee colony-based approach. Information Sciences, 220, 399–407. DOI 10.1016/j.ins.2012.07.012. [Google Scholar] [CrossRef]
46. Yildiz, A. R. (2013). Optimization of multi-pass turning operations using hybrid teaching learning-based approach. The International Journal of Advanced Manufacturing Technology, 66(9), 1319–1326. DOI 10.1007/s00170-012-4410-y. [Google Scholar] [CrossRef]
47. Belloufi, A., Assas, M., Rezgui, I. (2014). Intelligent selection of machining parameters in multipass turnings using firefly algorithm. Modelling and Simulation in Engineering, 2014, 592627. [Google Scholar]
48. Yildiz, A. R. (2013). Hybrid taguchi-differential evolution algorithm for optimization of multi-pass turning operations. Applied Soft Computing, 13(3), 1433–1439. DOI 10.1016/j.asoc.2012.01.012. [Google Scholar] [CrossRef]
49. Xie, S., Guo, Y. (2012). Optimisation of machining parameters in multi-pass turnings using ant colony optimisations. International Journal of Machining and Machinability of Materials, 11(2), 204–220. DOI 10.1504/IJMMM.2012.045983. [Google Scholar] [CrossRef]
50. Leonard, B. J., Engelbrecht, A. P., Cleghorn, C. W. (2015). Critical considerations on angle modulated particle swarm optimisers. Swarm Intelligence, 9(4), 291–314. DOI 10.1007/s11721-015-0114-x. [Google Scholar] [CrossRef]
51. Pampara, G. (2013). Angle modulated population based algorithms to solve binary problems (Ph.D. Thesis). University of Pretoria. [Google Scholar]
52. Huang, X., Li, P., Pu, Y. (2019). Amplitude angle modulated bat algorithm with application to zero-one knapsack problem. IEEE Access, 7, 27957–27969. DOI 10.1109/ACCESS.2019.2901988. [Google Scholar] [CrossRef]
Cite This Article
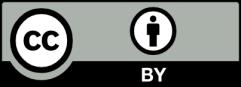
This work is licensed under a Creative Commons Attribution 4.0 International License , which permits unrestricted use, distribution, and reproduction in any medium, provided the original work is properly cited.