Open Access
ARTICLE
Multi-Objective Redundancy Optimization of Continuous-Point Robot Milling Path in Shipbuilding
College of Mechanical and Electrical Engineering, Harbin Engineering University, Harbin, 150001, China
* Corresponding Author: Jianjun Yao. Email:
(This article belongs to the Special Issue: Computer Modeling in Ocean Engineering Structure and Mechanical Equipment)
Computer Modeling in Engineering & Sciences 2023, 134(2), 1283-1303. https://doi.org/10.32604/cmes.2022.021328
Received 08 January 2022; Accepted 28 March 2022; Issue published 31 August 2022
Abstract
The 6-DOF manipulator provides a new option for traditional shipbuilding for its advantages of vast working space, low power consumption, and excellent flexibility. However, the rotation of the end effector along the tool axis is functionally redundant when using a robotic arm for five-axis machining. In the process of ship construction, the performance of the parts’ protective coating needs to be machined to meet the Performance Standard of Protective Coatings (PSPC). The arbitrary redundancy configuration in path planning will result in drastic fluctuations in the robot joint angle, greatly reducing machining quality and efficiency. There have been some studies on singleobjective optimization of redundant variables, However, the quality and efficiency of milling are not affected by a single factor, it is usually influenced by several factors, such as the manipulator stiffness, the joint motion smoothness, and the energy consumption. To solve this problem, this paper proposed a new path optimization method for the industrial robot when it is used for five-axis machining. The path smoothness performance index and the energy consumption index are established based on the joint acceleration and the joint velocity, respectively. The path planning issue is formulated as a constrained multi-objective optimization problem by taking into account the constraints of joint limits and singularity avoidance. Then, the path is split into multiple segments for optimization to avoid the slow convergence rate caused by the high dimension. An algorithm combining the non-dominated sorting genetic algorithm (NSGA-II) and the differential evolution (DE) algorithm is employed to solve the above optimization problem. The simulations validate the effectiveness of the algorithm, showing the improvement of smoothness and the reduction of energy consumption.Keywords
Cite This Article
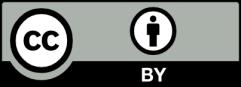
This work is licensed under a Creative Commons Attribution 4.0 International License , which permits unrestricted use, distribution, and reproduction in any medium, provided the original work is properly cited.